Module 5: Construction and Project Management Engineering PDF
Document Details
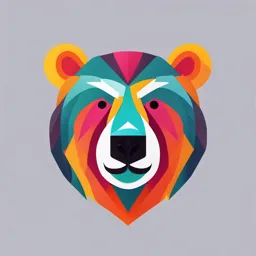
Uploaded by LavishDaisy
Tags
Related
- Silver 2017-1-5 FIDIC 2017 Conditions of Contract PDF
- The Role of Engineers in the Construction Project PDF
- Essentials of Project Procurement PDF
- Objective Civil Engineering by Gupta and Gupta PDF
- Construction Cost Engineering: Work Breakdown Structure (WBS) PDF
- Classification of Civil Engineering Services PDF
Summary
This document provides information about construction engineering, project management, and the various phases involved in construction projects. The document includes an overview of the key concepts and explores different stages of a construction project such as conceptualization, design, pre-construction, and owner occupancy, along with the typical roles and responsibilities of project personnel and teams.
Full Transcript
MODULE 5 Construction and Project Management Engineering EXPLORE Watch the following videos: StepByStep Construction.mp4 12 Steps of Construction.mp4 Foundation layout.mp4 Project phases.mp4 ENGAGE...
MODULE 5 Construction and Project Management Engineering EXPLORE Watch the following videos: StepByStep Construction.mp4 12 Steps of Construction.mp4 Foundation layout.mp4 Project phases.mp4 ENGAGE Construction engineering is a professional discipline that deals with the designing, planning, construction and management of infrastructures such as roads, tunnels, bridges, airports, railroads, facilities, buildings, dams, utilities and other projects. Growing up you probably saw several different construction projects happening even the smallest scale like the construction of a one-storey house. Who were the people you can see in the construction site? What are the different job descriptions of a typical construction worker? 1. ________________________________________ 2. ________________________________________ 3. ________________________________________ 4. ________________________________________ 5. ________________________________________ 6. ________________________________________ 7. ________________________________________ EXPLAIN Construction and Project Management, or CPM, involves the application of technical and scientific knowledge to infrastructure construction projects. While engineering focuses on design and construction management is concerned with overseeing the actual construction, CPM often represents a blend of both disciplines, bridging design and management or project execution. Construction engineering managers may have an educational background at both undergraduate and graduate levels as well as experience in construction management techniques. Their skills may be applied widely to the architecture, engineering, and construction (AEC) industry. Basically, project construction can be divided into 6 phases. 1. Conceptualization and Design 4. Construction 2. Pre-Construction 5. Testing and Commissioning 3. Procurement 6. Owner Occupancy ELABORATE As construction engineers it is basically our job to oversee construction projects from start to finish. We ensure that construction is safe, economical, and productive. PHASES OF PROJECT CONSTRUCTION 1. CONCEPTUALIZATION AND DESIGN Normally, the conception of the project starts with the client. This is where the dream begins as well as the research for the right location and the specifications/standards that should be followed. Depending on the project, the conception stage might vary. It can take anywhere from a few days to a few months or more, depending on how imminent is the need for the completion of the project. It goes without saying that construction workers usually don’t have much input during this stage, as the ball is still in the hands of the project owner. Once the project is closer to fruition, it is time to sit down and talk design. This is still a preliminary stage, which means that nothing is guaranteed at this point. Nevertheless, design is the stage where usually the bidding process begins. The team that is in charge of the design, led by an architect or an engineer, will need to make sure that each of the state regulations and codes is met while respecting the vision of the project owner as well as ensuring that the newly built structure will be usable. There are normally four different steps within the design stage and they include programming and feasibility, schematic design, design development, and contract documents. During the programming and feasibility step, each of the objectives and goals of the project has to be outlined. Numerous decisions are made at this stage, including how large the building will be, how space will be used, and how many rooms will be needed. Once the contract documents are drawn up, everything is close to being finalized, because they contain the final drawings and specifications. These documents are used in the construction field by those placing bids to work on the project. 2. PRE-CONSTRUCTION The next stage of a construction project begins when the bidding is completed and the contractor has been chosen to do the work. As soon as the contractor is chosen, the project team is put together. Typically, a project team has the task to prepare the construction site before the work begins. As a rule, it consists of the following specialties: Contract administrator Project manager Superintendent Field engineer Health and safety manager In close collaboration with the contractor, the project team is responsible for visiting the field in order to complete a site examination. The site examination will allow the project team to detect or predict any environmental challenges that might emerge during the building process. Soil testing is also an integral part of this step. When all information is collected, all plans and findings should be reviewed by the city authorities. This is usually a long procedure, as all concerns and opinions should be heard and addressed. 3. PROCUREMENT OF MATERIALS Now it’s time for the project team to order and obtain materials, equipment, and workforce. This stage of the project can be more or less complex and challenging depending on how big the project is, the available resources and the agreed start date. Many of the big construction companies have their own procurement departments. In such cases, it is common that the construction company will simultaneously order labourers, equipment and materials for a number of projects. This process might vary a lot in smaller projects. The typical heavy equipment used in large scale construction are as follows: BACKHOE— also called excavator — is a type of excavating equipment, or digger, consisting of a digging bucket on the end of a two-part articulated arm. ROAD ROLLER - compactor-type engineering vehicle used to compact soil, gravel, concrete, or asphalt in the construction of roads and foundations. Similar rollers are used also at landfills or in agriculture. Road rollers are frequently referred to as steamrollers, regardless of their method of propulsion CRANE A crane is a type of machine, generally equipped with a hoist rope, wire ropes or chains, and sheaves, that can be used both to lift and lower materials and to move them horizontally. It is mainly used for lifting heavy things and transporting them to other places The typical workforce of any construction consists of the following: 1. FOREMAN or CAPATAZ – in charge of leading the workforce 2. LEADMAN – works as the foreman’s right hand 3. CARPENTERS – works on formworks 4. STEELMEN – works with reinforcing steel bars 5. MASONS – works with concreting 6. LABORERS – works on manual labor jobs 7. ELECTRICIANS – works on providing electricity to the construction site 8. PLUMBERS – in charge of plumbing fixtures 9. HEAVY EQUIPMENT OPERATORS – operates heavy machinery 10. WAREHOUSEMAN – in charge of keeping tabs on construction materials and equipment 11. WELDERS – in charge of welding 4. CONSTRUCTION Before the construction work begins, a pre-construction meeting is done to ensure that everyone is on the same page when the construction starts. This meeting normally includes information about the following topics: how to access the job site the quality control of the project how and where to store all the materials the hours that everyone will be working Each worker may be given their own schedule. It is also important to note that the schedule of each project agent might vary depending on their role. This is especially true for subcontractors who need certain parts of the job completed before they can begin their portion. It easily becomes evident that bad planning at this point can lead to serious delays and budget overruns. Once the meeting is over and there are no lingering questions, the very first step of the project can begin. The goal at this point is to have planned everything so carefully that everything goes off without a hitch. Of course, that rarely happens, as something always goes wrong during a construction project. The typical stages of construction include: 1. Site preparation – includes the clearing of unwanted obstructions in the construction site. 2. Lay out – Noting all points of importance like boundaries and location of foundation. 3. Gravel laying – Laying of gravel bed where foundation will stand. 4. Laying steel reinforcement and batter boards for concrete pouring. 5. Concrete pouring 6. Installation of reinforcing steel bars 7. Installation of formworks 8. Concrete pouring 9. Repetition of steps 6, 7, and 8 till completion. 10. Finishing 5. TESTING AND COMMISSIONING This phase includes making sure that everything works as they should. Making sure the electricity works, plumbing works, paint is applied correctly, tiles are set properly, and everything is in place for the owner. 6. OWNER OCCUPANCY Once the tests are finished, it is now ready to be occupied by the client. Now that the training is completed, the owner can take over the building. This is when the warranty period is on. In that way, the project owner can feel safe that there is enough time to examine all the different systems, equipment, and materials that have been installed. TYPICAL TERMS USED IN WIKANG FILIPINO 1. POSTE - COLUMN 23. MULDURA - MOULDING 2. HALIGE - WALL 24. SIBE - EAVE 2. GUILILAN - GIRDER 25. BOLADA - PROJECTION 3. SULERAS - JOIST 26. BALANGKAS - FRAME WORK 4. SAHIG, SUELO - FLOORING 27. KANAL - GUTTER 5. SEPO - GIRT 28. ALULOD - CONDUCTOR d. BIGA - BEAM 29. PLANCHUELA - W. I. STRAP 7. BARAKILAN - BOTTOM CHORD 30. PIERNO - BOLT 8. REOSTRA - PURLIN 9. SENEPA - FASCIA BOARD 10. KOSTILYAHE - CEILING JOIST 11. TABIKE - SIDING (EXTERNAL) 31. PLANCHA - SCAFFOLDING 12. PILARETE - STUD (VERTICAL) 32. ESTAKA - STAKE 13. PABALAGBAG - STUD (HORIZONTAL) 33. KUSTURADA - PLASTERED COURSE 14. PASAMANO - WINDOW SILL 34. PALITADA - STUCCO OR PLASTER 15. SUMBRERO - WINDOW HEAD 35. REBOCADA - SCRATCH COAT 16. HAMBA - WINDOW JAMB / DOOR 36. PIKETA - PICKWORK (on masonry) JAMB 37. MONYEKA - VARNISH FINISH 17. SINTURON - COLLAR PLATE 38. BIENTO - SPACING OF GAP 18. HARDINERA - STRINGER (OPEN) 39. LARGA MASA - CONCRETE SLAB 19. MADRE (de escalera) - STRINGER (rough) (CLOSED) 40. ASINTADA - ALIGNMENT 20. BAYTANG - TREAD 41. HULOG - PLUMB LINE 21. TAKIP (SILIPAN) - RISER 42. BALDOSA - CEMENT TILE 22. GABAY - HANDRAIL 43. LADRILYO - CEMENT BRICK 44. BATIDORA - DOOR FILLET 45. KANAL - GROOVE 46. HASPE - GOOD GRAIN 47. PLANTILYA - PATTERN / SCHEDULE 48. BISAGRA - HINGE 49. DE BANDEHA - PANELED DOOR 50. ESCOMBRO - EARTHFILL 51. LASTILYAS - MASONRY FILL 52. LIYABE - ADOBE ANCHOR 53. HINANG - SOLDER 54. ESTANYO - NICOLITE BAR 55. SUBAN, SUBUHAL - TEMPER (metal work) 56. PIE DE GALLO - DIAGONAL BRACE 57. PUNSOL - NAIL SETTER 58. POLEYA - WIRING KNOB 59. ESPOLON - CABINET HING EVALUATE Sketch a flow diagram of the phases of construction, including the subdivisions per phase. Read on the typical construction terms in the Filipino language and draw a small picture per item.