Mining Machinery 3rd Year PDF
Document Details
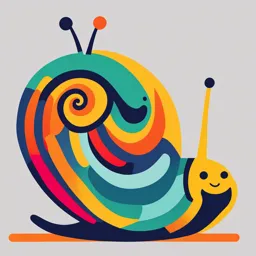
Uploaded by AwedOcarina
Tags
Summary
This document covers different types of haulage systems used in mining, including rope haulage, endless haulage, and gravity haulage. It details various aspects of each system, such as applicability, safety features, and advantages/disadvantages. The focus is on practical aspects and technical details of the equipment.
Full Transcript
## Lining Machinery - II ### Ch-1 Transport of ore #### Different types of Haulages: * Haulage Roadway: A roadway from which materials are transported. (eg coal/ore, bricks, cement, leggings etc). * The different types of haulages are: * Rope haulage * Locomotive haulage * Conveyor ha...
## Lining Machinery - II ### Ch-1 Transport of ore #### Different types of Haulages: * Haulage Roadway: A roadway from which materials are transported. (eg coal/ore, bricks, cement, leggings etc). * The different types of haulages are: * Rope haulage * Locomotive haulage * Conveyor haulage * Aerial ropeway haulage * Cage/ skip system haulage. #### Description of Rope Haulage System: A system of transportation of ore/materials by the means of tubs moving in tracks connected with wire rope to drums attached with a driving motor. #### Different types of rope haulages are: 1. Direct rope haulage 2. Endless Rope haulage 3. Main and tail rope haulage 4. Gravity haulage #### Direct Rope Haulage: * **Applicability**: * Suitable for incline working. * Suitable for hauling coal from dip heading. * Suitable for the main haulage to work between fixed points. #### Gradient: * Steeper than 1in12 * 8-10 km/h #### Safety devices: * Backstay, stop block, drop marwick, buffer, jass rail, tubs rerailer, combined stop block and run away switch, manhole * Motor: Slip ring motor used with a drum * Controller * Brakes: Caliper break * Track gauge: 0.6m #### Types of Direct rope haulage: * Single drum direct rope haulage * Double Drum direct rope haulage #### Single Drum direct rope haulage: * It is a simplest type of rope haulage system. * It consists of: * One track for running of tubs * One wire rope of standard type for holding the tubs to a drum. * One drum connected with motors & gears and situated at the top of the incline. For upward journey, the drum rotates with the help of gear and motors and for downward journey, the tubs are lowered down by the action of gravity and power required only for controlling the speed. #### Advantages of single Drum Direct Rope Haulage: 1. simple in operation 2. only one brakes is required 3. Extension is easy: 4. Branched roads can also be served, if the gradient is suitable 5. can be used in narrow roads. #### Disadvantages of single Drum Direct Rope Haulage: 1. High power demands for upper journey of loaded tubs. 2. Efficient breaking system required for downward journey. 3. High speed haulage demands more mainenane of track 4. cannot be used for less incline roadways. 5. A derailment is associated with heavy damages. #### Double Drum Direct rope haulage: * It consists of: * Separate tracks for running of empty tubs and loaded tubs * One track for lowering empty tubs. * Another track for hauling loaded tubs * Two wire ropes of standard type for holding the loaded and empty tubs with their respective drum. This separate drums (one each for loaded & empty tubs) connected with one motor & gears and situated at the top of the incline. #### Advantages: 1. higher output 2. Lower power demand 3. Branched reads can also be served, if the gradient is suitable. #### Disadvantages: 1. Wider reads required 2. Efficient breaking system required for downward journey. 3. High speed haulage demands more maininance of track 4. Cannot be used for less incline roadways. 5. A derailment is associated with heavy damages 6. Due to high speed more dust, more wear & tear takes place. #### Endless Haulage: * **Applicability**: * Flat gradient * Uniform roadway * Wider roadway In this system, there are two parallel tracks side by side. One for the loaded tubs and the other for the empties tubs. Endless rope passes from the driving drum /pulley located at the outbye end of the haulage road to the inbye end and back again via a tension pullly (return pully). The tubs, loaded as well as empties, are attached to the rope at regulars intervals with the help of clips so that the entire rope length has tubs on it at intervals. #### Endless rope haulage important points: * Gradient: 1 in 6 * Speed: 3-7 km/hs * Motor: Squirrel cage motor generally used * Brakes: Caliper brake * Clips: Screw clip, smallman clip, cam clip * Rope movers: Directionally * Track type: Required double track or under rope #### Endless repe haulage safety sevices: * Backstay * Stop block * Run auray Switch * Man hole * Tus recrailer #### Jazz rail #### Monkey Catch #### Types of Endless haulage: * Under rope endless haulage * Over rope endless haulage #### Under Rope Endless Haulage: 1. If the rope passes below the tub, it is known as under rope endless haulage. 2. In this system, there is more wear & tear of the rope but also there is an advantage that there is more direct pull on the tubs. #### Over Rope Endless Haulage: 1. If the rope passes above the tubs, it is known as over rope endless haulage. 2. In this system, rope is unaffected by wet floor & liable to less wear & tear. The rope is at better working height & a system generally used for undulating roadways. #### Advantage of Endless Haulage: * Because of slow speed less wear & tear to the tus wheel & track * Less maintenane is required * Accidents do not cause much damage * Less motor power is med * Continuous flow of mineral or coal is attained. #### Disadvantages of Endless Haulage: 1. It require wider roads 2. Not suitable for steeper gradient 3. Load on the rope is large hence a rope of large cross section require 4. Large number of tubs & clips are required. 5. It cannot traverse a branch road. #### Main and Tail Rope Haulage In this system the hauling engine is provided with two separate drums, one for the main rope which hauls the empty tubs in. When one drum is in gear, the other drums rends freely on the shaft, but controlled, when necessary, by the brake to keep the ropes taut. The main rope is approximately equal to the length of the plane, and the tail rope service this length. #### Only one track is required. #### Applicability condition: * Suitable for undulating roadways where it is impossible or undesirable to maintain the double track required for endless rope haulage. * Flat to gentle gradient * Narrow roadways * Convenient for working branches #### Advantages: * Suitable for undulating roadways * Suitable for curves and conventional ways * Fast speed * Suitable in bad roof problem. * Work in single track #### Disadvantages: * Chances of accident * More power required than endless haulage * Wear and tear due to high speed. * Serailment chances more results in more costs #### Gravity Rope Haulage: This is a haulage without any motor or external sources of power and consists of a cast iron pully (jig pully), 1.3-2.3m diameter, having a brake path on one side and a strap brake. It is located at the top of an inclined roadway and is employed to lower by gravity loads attached to one end of the rope while simultaneously hoisting empties attached to another end of the rope which passes round the jig pulley. The jig pulley is mechanical. Only single track is required for its operation, but at the mid-way of the road where the loads and empties meet, double track or a bye-pass is essential. #### Safety senvices in Haulage * Stop Block: This consists of a wooden beam of black lying across the rails, pivored at one end and held against pivoted side block at the other. It is a good plan to have two stop-blocks cone distance apart, the one forming a reserve for the other. * Position: It is situated top of the incline and mouth of incline. #### Monkey Catch: This consists of: 1. A pivoted pieces of steel rail placed between the rack rails so as to catch the axle of a backward runaway tub. #### Runaway tub: 1. A wooden block pivoted at one end and pressed over the rail by a strong spring. It is used for endless haulage track for tubs moving up gradient. #### Backstay: This is used behind an ascending set of tubs on a direct haulage road on an endless haulage. It is attached to the tub axle (at the back of tubs set) and in the event of runaway of tubs. The pointed end of the backstay stops against sleeper of the track and thus tubs get reversed. It is used for arresting backward runaway. #### Buffer: It is a safety device that maybe mechanical or horizontal wooden or steel beam depends on where it is used and placed across the track in underground to stops the running tubs near the working end and avoid accidents. #### Drop warwick: This is intended for arresting forward runaway being placed below the brow of an incline and also near the bottom and below intermediate levels. It consists of: 1. A heavy bulk or girder hinged at one end to a specially set roof girder and held up at the other by an eye-bolt and fin. The warwick is released when required in emergency by a haulage worker pulling the wire to withdraw the pin. #### Runaway Switch: The basic principle of the runaway switch is that the tubs breaking from the loosed rope are diverted by the means of an open track switch. The runaway points are closed by the tub wheels as the train ascends to incline but they are immediately open again automatically by the action of spring and the runaway tubs are then guided into the side preparre by the sand head. #### SAGE craft Device: This is designed to arrest forward runaway automatically. It works on the same principle of position of axle with movement of tubs, as the axle of tubs depresses the forked end to the axle height to stop the running tubs. When the tubs passing in normal speed, the forks drops doion before the back axle reaches to it. If the tubs moving fast, the back axle is held by the fork and the tub is stopped. #### Locomotive Haulage: It is rail transport system in which locomotives (train) were used for transportation of minerals from underground to the top surface and yields better production than rope system. #### Types of locomotives: * Diesel locomotive (runs on diesel power) * Battery locomotive (runs on D.C battery power supply) * Compressed air locomotive (runs on compressed air). * Electric locomotives (runs on electric power supply through trailing cables) etc #### Every loco's consists of: * A chasis * Driving wheels on axle, springs & brakes blocks underneath the chassis * Power unit * Operator's Cabin * Powered brakes on medium-Large size locos * Lights at both ends * A hand screw brake for emergency (as required by law) #### Applicability of Locomoti've Haulage: * Mild gradient, generally employed in gradient milder than 1 in 25. * Limiting gradient: 1 in 15. * Where reads are wide & high * In intake airway: so as to dilule firedamp and emitted diesel product. ##### Where loco track in settled ground not subject to movement by mining operation * Light type: 2-4.5 tonne * Heavy type: 8-13 tonne #### Diesel Locomotives * It is commonly used in number of mines. * Wt. varies from 3-15 tonnes, Power 50-75 KW * The locomotive used in 4/8 coal mines have a power unit in a flameproof enclosure as a safeguard against ignition of fire damp. * In coal mines the diesel locomotives are not allowed with the percentage of inflammable gas is more than 1.25%. in the General body of air, hence these are generally used in intake readways. * The Exhaust of the diesel engine includes oxygen, nitrogen, carbon dioxide and a small quantities of oxides of sulphur and Nitrogen and other aldehydes which smells badly and causes irritation to nose, throat and eyes and to prevent this exhaust conditioner use Din in locomotives. #### Advantages: * Cheaper * Completely self controlled #### Disadvantages: * Danger of fire in handling of diesel * Production of poisonous gases * Add heals to the atmosphere * Mould mainenane required * More employees required #### Electric Locomotives * It is equipped with electric motor which draws the current from the overhead wires through a pentograph or through a long pole which is kept preessed against the overhead conductor by spring tension. * DC supply to overhead wires: 250V * Locomotive main used in deep gassy mines, the overhead wires are suspended through insulators over the track at a height more than 2m. #### Advantages: * More reliable * Light weight * Less maintenance * Good control. * Small size * No exhaust gases #### Disadvantages: * High initial Investment * Danger of shock and Fire * Derailment is a major problem. #### Electric Battery locomotive: * The power unit of electric battery locomotive is a DC electric motor which receives current from a storage battery carried in locomotive itself. * This type of locomotives used for light and medium duties * The batteries are of lead acid type and each battery consists of a numbers of 2volt cells and their numbers vary from 40 to 70. * The capacity of the battery to work is showed and its charging time is also showed. #### Advantages:: * Less maίπμηαηG * No poisonous gases * NO overhead's wire problem * Quite easy in operation #### Dis advantages: * Hydrogen gas is liberated. * Flame proofing is not possible * Overheating of cell may cause sparking of fire * Expensive batteries and less life. #### Compressed Air Locomotive: * The locomotive in which compressed air used as a source of power, equipped in compressed cylinder, installed over the locomotive. * The cylinder supplies the required quantity of compressed air to the locomotive * These locomotive are very safe, reliable & very useful in hot & deep mines. * Due to their high installation cost & emission of poisonous gas (CO), it were not used in ULG coal mines. * It is only used for light duty work only. #### Advantages: * Very safe * Very reliable * Less maintenang required * Cooling effect of air #### Disadvantages: * High initial cost * Danger of Pipe leakage * Efficency is less #### Definations: * **Tractive Effort:** This is the force generated by the loco to move and accelerate the loco. * **Drawbar pull**: This is the part of the tractive effort which remains available for pulling the connected load of mine cars after deducting the force required to move the loco. * **Super Elevation**: It is the raising of outer edge or outer rail above the inner one around a curve to prevent from derail of locos or tubs from the track due to centrifugal action acquired around a curve that have tendency to leave the track & proceed along a colvese tangential to curve. * **Ideal Gradient:** If the tractive force required to move the loaded train down the gradient is same as force required to haul the empty train in upward direction of the gradient with the same velocity, this gradient is known as ideal gradient. * **Conveyor**: It is the system of transportation of ore in which are is transported continuously from one point to another with the help of closed belt, chain or plates operated by the driving and driven drums or pulley. #### Types of conveyor: 1. Belt conveyor 2. Chain conveyor 3. Plate conveyor #### Belt conveyor: * A flat endless belt which moves continuously and carries at its top surface the materials to be conveyed * The idlers which support the belt * The structure of channel iron on which idlers are mounted * The tensioning arrangement for keeping the belt is proper tension * The drums at the discharge and tail end over which the belt passes. * The drive head comprises the electric motor, coupling, gearing and snub pulley... #### Factors that Decides the selection of Belt conveyor: * Amount of materials to be conveyed * Continuity of operation needed * Size of lumps * Distance of transportation * Environment allowance * Gradient * Method of coal wining ie longwall / B&P mithal #### Capital available #### Advantages of Belt conveyor: * A continuous supply of material * Low operating cost then road transportation system * High rate and speed of supply * More efficiency and low cost. #### Limitation/Disadvantages of Belt conveyor: * It cannot be used for long distance * It requires high one time capital investment * It cannot handle the lumps of big size. * Place should be dry enough that where it will install and have velocity should not be high. * It cannot be operates at high inclination. #### Chain conveyor: * It is mostly used in longwall fall. * Speed: 30-40 tonnes per hour on a well roadway, nearly 50m long * Driving motor power: 12-15KW #### Applications: * Transportation at the face & adjoining short workings * Used to haul the coal along the gate roads. * Transporting on inclines having an angle of inclination exceeding 18° or where belt conveyors are not used. * Used on the surface for conveying coal from shaft to bunker as well as in screening & washing plants. #### Types of chain conveyor: * On the basis of Flexibility: * Rigid chain conveyor * Flexible armored chain conveyor * On the basis of no. of chains used: * Single chain conveyor * Double chain conveyor * Tripple chain conveyor #### Advantages: 1. Can convey uphill against steep (1 in 3 or more gradient) as well as downhill gradient. 2. Much stronger and can be roughly handled. 3. Flexible type can be dismantled, extended or shorted. #### Disadvantages: 1. High initial cost 2. High power consumption 3. Wear & tear more 4. Highly noisy 5. Producing high percentage of fine dust #### Plate conveyor: It carries series of steel plates, each in the form of short, tough, joint together with a slight overlap to form articulated band. The plates are either attached to one centre chain or to two side chains. These chains are connected to rollers running on an angle iron framework and transmit the drive from the drive heads. Available width: 400; 500 & 640mm Running speed: 0.8-1.2 m/s Carrying Capacity: 10-40 t/hr #### Aerial Ropeways An aerial ropeways is an installation in which transportation of material and men is done by moving carriers pulled by ropes suspended above the ground. #### Types: * Mono-cable ropeway: Single running endless rope which both support and move the carriers. * Bi-cable ropeway: two fixed track ropes along which the carriers are hauled by an endless track rope. * Twin-Cable ropeway: the rope has two pairs of track rope to support the carriers and one endless track rope. #### UNIT-2 WINDING IN SHAFT #### Propose of winding: 1. To hoist the coal or mineral from underground to surface. 2. Lowering & raising of men 3. Transport the material from the surface to underground 4. For shaft sinking NOTE: where the depth of shaft exceeds 30m; winding arrangement shall be installed & maintained constantly available for rescue. #### Main Equipment of winding: * **Headgear**: A steel or concrete framework on the mouth of the shaft, known as headgear. #### Purpose of Headgear: * To support the headgear pulley, the weight of cage, ropes and rope guides. * Guide the case at banking levels. * **Construction**: It consists of relatively vertical columns girders braced with horizontal girders. The members narrow at the top and battered at base to 1 in 10 for a lever width at the foundations. * It includes: * Six legs * Four nearly vertical * Two inclined towards winding engine room * Steel platform or plate and the bush bearing of the winding pulley at the top. * Delaching bell plate #### Headgear Pulley: * It is a large diameter pulley mounted freely at the top of the headgear with the help of bush bearings. * Its diameter should be atleast 100 times the rope diameter * The pulley generally constructed in two halves and bolted together * The pulley ensures 1/3rd of the circumference of the rope is in contact with the groove. * Dia of groove: 110% of rope dia for stranded wire rope or 105% of locked coil rope #### Cage: * The cage is a lift suspended from the winding rope, opens at both ends, where gates can be positioned during man riding. * Rails fitted to the flade for mine cars or tubs. * Catches are provided on the floor which act against the axles of the mine car / tubs * Hand bar near the roof for the men to hold. * Collapsible gates, which can be opened or closed by manually or compressed air * Removable door at roof for accommodating long timbers or rails whenever necessary. #### Skip: * It is a case of larger size that is used of minerals from underground to surface. * Sometimes it can also accomodate mine cars * It has a smaller payload usually strong or more compared to cage #### Winding Rope A rope which is used for winding is generally a stranded wire rope with fiber core & lang's lay construction. #### Guide * A system of arrangement in a vertical shaft that ensures smooth travel of cage without oscillation. #### Keps: * A platform arrangements at the pit top for the positioning of case. #### Suspension Gear: It is an attachment between winding rope and cage to avoid restation in it to transmit the load equally from each corner of cage and to hold with extra safety. #### Winding System * A system by which cage ascends & descends in shaft as per direction defined by using drum/sheave connected by driving motor, pulley, winding rope, rail rope etc * Types of winding System: * Drum Winding * Koepe / Friction winding #### Drum wirding: * The winding system, in which a driving motor connected to a large dia. of drums coiled by winding rope as per length required that operates or closed according to lowering/raising to connected cage operated in shaft. #### Types of Drum Winding 1. Cylinderical drum 2. Conical drum 3. Cylindro-conical drum 4. Bi-Cylindro-conical drum #### Cylinderical Drum: * It is a simplest and robust construction cylindrical drum, in which winding rope are attached at each end of drum barrel, and arranged to coil on the drum in opposite direction in such a way that when drum rotates, one end will be lowered and other raised. * Keep coiling underneath the drum called underlap. * Keep coiling over the top of the drum called overlap. * Drawbacks: It can be used shallow shaft only. * Reasons: In deep shaft the weight of one winding rope exceeds the weight of coal. * Raised rope wind, causing heavy brake wear, however this may be reduced by using rail rope. #### Conical Drum: * It is provided with flanges on two sides of the conical portion for even coiling of rope. * At the commencement of wind, rope supporting the full cage in small radius & holding the empty cage is descending rope follows small dia and ascending rope is on large dia. #### Advantages: * No rail rope req, wired. * Torque balancing is uses by its variable cross-section. #### Disadvantages: * Only half portion of drum. #### An improved upon the conical drum in which part of the conicas portion provided with cylinders ie combination of one & cylinder. * The rope coiled in drum in such a way that ascending cage follows smaller dia. of cone first and as the engine reaсhes the full speed after the period of acceleration, the rope is wound in larger part during hoisting period and vice-versa #### Advantages: * Decrease in length of drums as compared in conical drum & improve the weight balances in begining. #### Disadvantages: * Design not so simple & operation will not so smooth. #### Bi-Cylindra concial Drum: * It is composed of two cylindrical, two conical section. One of small dia. and the other of large dia., joined by conical section * At the begining of the hoisting the loaded cage wound over the smaller dia until the full speed attained, when the rope is transferred by the care of scroll to large dia. Near the end of hoist but just before the retardation, the descending rope is transferred from larger to smaller dia. * Advantages: It reduces the peak load on motor and loads itself better them any other type of drum. * Disadvantages: Heavier, expensive & for deep mines size becomes more excessive. #### Koepe / Friction Winding: * It consists of a steam/Electrically driven sheave (wheel/pulley) fitted with renewable friction lining which is grooved to suit the main winding rope. * Arc of contact b/w sheave & winding rope is 185-230°. * Cage/skip is suspended at each end of rope. * Rail rope is attached to the underside of the cages & is arranged hang freely in shaft. * Cages raised / lowered by the power transmitted through friction between winding rope & lining. * The pulley used shall be friction less. The driven pulley is provided with frictional lining. * More costly due to requirement of large dia. of drums. Less costly as there is no operation of drum. * Complicated in construction. Simple in construction and operation. * The rope life is reduced due multiple layering coil of rope. No over layering of rope take place, therefore the rope life is more. * Less suitable for winding heavy payloads from larger depth Suitable for winding heavy payloads from larger depth. * More power is required comparatively very less weight is required to run light weight friction pulley. * Operating cost is more. Operating cost is less. * It can be used during shaft sinking. It can't be used during shaft sinking. * The main rope of the cage & tail rope of skip may or may not be connected. The main rope of the cage & tail rope of skip are interconnected. * Separate run with one cage is possible. Separate run with one is not possible. #### Provisions on Winding Drum * **Flanges**: Provided on each side of winding drum to prevent the rope from leaving the drum from sides due to slip or slack in the rope. Depth: 10-15 com with drum. * **Depth Indicator**: An indicator used to indicate position of cage in shaft & fitted with winding drum. * **Mechanical Brakes**: A brake which directly acts on winding drum to hold it when it is stationary. Operated by oil pressure or air compressor. Sufficient to hold max torque. #### Types: 1. Anchored post brake (pressure max at top & minimum at 0. 2. Centre suspended calipers post (uniform pressure) #### Automatic contrivance * It is a safety device connected to winding system used to prevent: * Over winding * Over speeding * Ensure slow banking #### Fleet angle * Angle made between winding rope connected to winding drum and normal to headgear pulley, when cage is either at pit top or pit bottom. * Fleet angle (θ) Shall not exceed 1.5° #### Suspension Gear It is a typical arrangement of attaching cage to winding rope: * Four cage chains in case of single cage, or cage chains in case of tendom cage (multi cages) attach the ledge to a triangular distribution plate which is connected to safety detaching hook through D-links or Bull Chains. * The detaching hook is attached to the rope capel. * Triangular distribution plate, chain shackles & bolts are made up of wrought iron or mild steel. * As per CMR-2017, all chains must be annealed atleast once in every 6 months. #### Rope capel: To prepare hook in wire rope. #### Reliance capping: In this capel there are two wedges which grips the wire rope near the required end where the white metal block is prepared, over which u-shape steel strap placed to holds the wedges and prepared metal block with making hook positioning, tightened and fixed by 4-105 iron clamps by hammering. #### Safety hook: It consists of: * Four wrought iron plates: 2 inner movable plates & 2 fixed outer plates * Opposite ways 2 inner plates are placed together in a way so that the hook "m" that of secured hole: * A main bolt or center pin passes thereought the holes "F" in all 4 plates & serves: to bind the plates together & to transmit the tension of winding rope from the hooks & to provide a piver on which 2 inner plates move. * A copper pin is placed through the holes "c" in all 4 plates, to prevent inadvertent movement of inner plates. During overwind: The ascending cage goes up the hook is partially withdrawn through the circular hole in such plate "e" securely attached to a horizontal member of headgear... Thus the lower wing plate "d" forced inwards, the copper pin sheared and the hooks "m" forcibly opens, releasing the D-link of winding rope capel. Simultaneously the catches "g" of the inner plates are forced outwards, so that they rest on upper side of catches plate and the cage is safely held. #### D-link & Bull chain: These are used to attach rope capel to safety hook and triangular distribution plate. Also used in cage chains. With the help of bull chain we can adjust the height of suspension gear. #### Triangular Distribution plate: It is a triangular plate with 4 to six grooves in it for connecting the case with the top of case chains. This is done for dissipating the load pressure uniformly. The upper groove of the plate is connected with safety hook via D-link and bull chains. #### Cage chains: 4 to 6 cage chains are attached to the all corner of the case from grooves of triangular distribution plate. It is used to dissipate the load and also resist rotating in its axis. #### Guides: Guide ropes are used to ensure that the conveyance travel of cage along a fixed part from shaft top to shaft bottom safely, without falling or causing any damage. It provides minimal frictional resistance to travel of the conveyance with lesser fatigue and tensile stresses. #### Types of Guides: * Rigid Guides * Flexible Guides #### Rigid Guide: * Rigid guides are of hard wood or steel rail (section) * These are of rectangular cross-section, usually 10cm x 2000mm, and are fixed by countersunk screws in positions placed across the shaft at intervals of 1.8-3m. They suffer from risk of jure. * Steel rigid guides are flat-bottomed or T-section rails weighing from 20-55kgf/m, length: 13m. * They need only be placed at one side of each case and only one line of buttons required in the middle of shafts. #### Flexible guides; * These guides are made up of steel wire ropes * Type of Rope: Locked coil type. * These ropes are suspended in a vertical shaft from the headgears by using reliance rope capel which is screwed on the class member of headgear. * At the pit bottom the rope passes through the holes provide in the pit bottom deck are tensioned by required amount. * Tensioning weight: 10 KN per 100m depth. #### Causes of oscillation: 1. Depth of shaft 2. Winding speed 3. Rate of acceleration 4. Rate of retardation 5. Tension in cage 6. Rubbing of guide shoe 7. Sudden power failwes #### Criteria of selection of guide rope: 1. Rope should be locked type. Generally for guide ropes half locked coil ropes are used. 2. It should have high tensile strength of about 1140/10 - 1570N/mm. 3. High Factor of safety so that ropes has long life. 4. Non-rotating or non spinning type of ropes is used. 5. Stationary type rope suitability (as guides ropes remain in the same position to support the Cage/skip) 6. The wires of rope should be of galvanised type so that it prevent from corrosion and rusting. 7. The wire of the rope should not be too loose or too tight. 8. Well lubricated. 9. Geometric construction is of best arrangement to withstand shock loads. 10. Ability to withstand on high temperatures and rubbing friction. #### Keps: * Keps are retractable support platform for cages and used at pit top under our mining regulations. * Their use is not necessary at pit bottom as the cages rest on rigid platform and mid set landing shaft served by Koepe winding * Keps ensures: * Support the case at pit top * Their use in proper alignment of cage-floor and decking level. * Keps are manually operated by the banksman at pit top. #### Upward Journey: * The ascending case pushes the keps back and as it raised slightly higher than the decking level. * The keps fall back in position by gravity as the banksman releases the operating lever & the cage, after it comes to a halt, is covered by winding engine man to rest on keps. #### Downwards Journey: * The winding Engine man raises the Cages slightly for clearance to keps. * The banksman withdraws the keps by manual operasion of a lever which is held by him till the cage is lowered past the keps. #### Disadvantages: * Accumulation of slack rope on the pit bottom cage when the top cage is raised (etc for withdrawl of keps). * Loss of time and power of lifting the rope cage before its downward pauses. #### The keps which can be withdrawn without lifting it. * The gear consists essentially of shafts "s" to which is keyed the hand lever, a pair of arms "A" with a steel roller "R" mounted on pin between arms. * The roller presses against a renewable roller path on a swing-lever "z" which is pivoted at "p" and carries a pallet mounted on a steel pin at its other end. * Pallet is free to move upward and around the pin (as shown in dotted) which permits the report passage of cage, But it prevents them moving downwards. * Thus the cage is securely supported on the upper surface of pallet. * The gear may be withdrawn without first raising the cage! * As the hand lever is mounted to the left, the roller R moves backwards along the roller path on that allows the lever downwards by gravity around the Pin. P. * until the pallet is clear of the cage. #### List of safety sevices used in winding: 1. **Electrical brakes:** It is a safety device used to reduce the speed of the case until the cage comes in rest position ie. wither at decking level or bottom level and after attining rest position of cage mechanical brakes were used to hold the case. 2. **Mechanical Brakes:** It is a safety device used to hold the case when it is in rest position, but it should be in OFF mode when the cage is in motion. * In case of power failure, the mechanical brakes work automatically to hold the cage. * **Types of mechanical brake** * Anchored post brakes * Centre suspended caliper post brake 3. **Automatic Contrivance:** It is a safety device used to prevent over speeding, over winding and to ensure slow banking. 4. **Safety hook:** It is a safety device which acts when over winding takes place and it is installed below the rope capel. Its main purpose to suspend the cage / skip on the members of the headgear (bell set) and at the same time releases the rope capel to go over the headgear pully and prevent over-winding. 5. **Recovery of over-winding Cage:** After over winding, the cage/skip which held over the members of the headgear, recovery of cage from those members is to be done, for this purpose rails is provided to the pit top so that they would not fall accidently. To remove the safety hook from bell set, the rope is attached to the hole of inner plate of safety hook with the help of D-Link and slightly pulled out, due to which the plates of safety hook comes in original position and hence allow to pass down through the bell set and the Cage can be sent down. 6. **Reverse direction prevention switch:** It is a safety device which cuts the power automatically if the winding engine man operates the motor in wrong direction. 7. **Tachometer Generator:** It is connected to the winding drum for normal rpm it generates normal amount of current to run the drum but if the gear box is faulty, the tachometer generator will not generate the normal current and cut the power of motor. 8. **Safety Catches:** These type of safety device are over mounted on the headgear at an interval of 0.3-2m above normal decking level. * In case of over-winding, the Cage is allowed to pass through these safety devices which have pivoted levers, But if cage fails to stand with the support of bell set of safety hook, the cage falls over these safety catches and hence damage is reduced. 9. **Depth Indicator:** It is used to indicate the depth of the Cage in the shaft and it is mounted on the drum winden. 10. **Warning Bell:** When the cage is at a distance of two revolutions before reaching the decking