Methods of Manufacture(1).pptx
Document Details
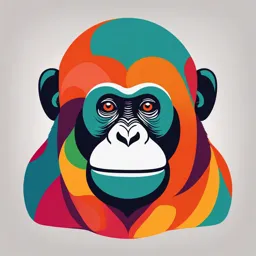
Uploaded by ThrivingSpring
Cardiff University
Full Transcript
Contact Lens Methods of Manufacture OP4101 Dr Katharine Evans Overview Regulations Soft (hydrogel) contact lens manufacture Lathing Spin casting Moulding Environmental Impact Regulations In Europe, ophthalmic products (including CLs) are regulated by the Medical Devices Directive 93/42/EED and Medic...
Contact Lens Methods of Manufacture OP4101 Dr Katharine Evans Overview Regulations Soft (hydrogel) contact lens manufacture Lathing Spin casting Moulding Environmental Impact Regulations In Europe, ophthalmic products (including CLs) are regulated by the Medical Devices Directive 93/42/EED and Medical Devices Regulations 2002 (SI 2002 No 618) Includes classification system based on perceived risk associated with device Contact lenses are Class IIa – medium risk CE marking Symbol used by manufacturers to show medical device meets relevant requirements of the Directive and is fit for intended purpose MHRA – Medicines and Healthcare Products Regulatory Agency Regulates medicines and medical devices in the UK Regulations ISO 14534:2011, Ophthalmic optics – Contact lenses and contact lens care products – fundamental requirements specifies safety and performance requirements for contact lenses and care products, such as the need for risk assessment, specifications for design, materials, clinical evaluation and manufacturing, microbiological requirements, packaging, shelf-life and discard date and labelling International Standards Organisation Soft (hydrogel)contact lens material Soft contact lenses are also known as hydrogels, HEMA, PHEMA or Poly HEMA lenses More detail in contact lens materials lecture Polymer Anhydrous material (xerogel) in rod form, sliced into buttons Button is shaped before hydrating to form the finished soft lens Liquid monomer Injected into mould before polymerisation & hydration Lathing Polymer button mounted on brass tools Lathed with diamond-tipped tool Back (concave) surface lathed, diameter cut to required size Button transferred & front (convex) surface lathed Lens polished to remove lathe marks (if necessary) Lens inspected & hydrated Inspected, packaged, autoclaved & labelled Nathan Efron Contact Lens Practice, Chapter 5 Soft Lens Manufacture Lathing + Relatively simple Wide range of parameters Relatively inexpensive to start production CNC lathes Complex designs difficult Labour intensive High cost per lens Variable surface finish Relatively slow Volume production difficult Reproducibility Lathing Spin casting Convex (male) stainless steel tool used to create disposable plastic concave (female) mould Liquid monomer introduced to rotating concave (female) mould Centrifugal forces distribute monomer across the mould Polymerisation (UV and/or heat cure) occurs at same time to produce lens Lens edge polished if necessary Lens inspected & hydrated Inspected, blister packaged & autoclaved Hydrogel Manufacture- Spin casting + Higher volume manufacture compared to lathing Automated production Low cost per lens Rapid Volume production relatively easy Expensive to start production Expense limits parameter range Lens edge may need further finishing Poorer reproducibility than moulding Lower volume than moulding Nathan Efron Contact Lens Practice, Chapter 5 Soft Lens Manufacture Moulding Stainless steel male and female tool used to create disposable plastic moulds Liquid monomer introduced between moulds and cured (UV/heat) Inspected & hydrated Inspected, blister packaged & autoclaved Hydrogel ManufactureMoulding + High volume manufacture Automated production Low cost per lens Rapid Volume production easy Good surface quality Good reproducibility Expensive to start production Expense limits parameter range Nathan Efron Contact Lens Practice, Chapter 5 Soft Lens Manufacture Watch the Panopto videos Sauflon contact lens manufacture Alcon (Ciba Vision) Lightstream The whole process Environmental impact of soft contact lenses & their manufacture Patients are becoming increasingly aware of the environmental impact of disposable lenses Less awareness about lens manufacture which includes impact of raw materials, packaging, production, transport Although lots of single-use plastic is needed for lens manufacture there are high rates of recycling Environmental impact To ensure patients can make an informed choice about what lens is the best option for them you should be able to explain: The environmental impact of lens manufacture Annualised waste of different wearing modalities Recycling options Environmental Impact of C ontact Lenses | Optical Exp ress