Engineering Materials Chapter 4 PDF
Document Details
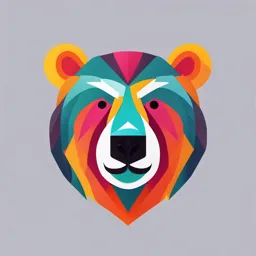
Uploaded by UnbeatableRuthenium3838
Universiti Teknologi MARA
Tags
Summary
This document provides an introduction to the classification of engineering materials, focusing on metals, polymers, and ceramics. It discusses the characteristics, bonding, and crystal structures of each material type. Specific details include classifications, bonding mechanisms, and crystal structures. It is potential lecture notes or study material for engineering students.
Full Transcript
CHAPTER 4 ENGINEERING MATERIALS MEC 481 1 CLASSIFICATION OF MATERIALS Metals: Strong, ductile high thermal & electrical conductivity opaque, reflective. Polymers/plastics: Covalent bonding → sharing of e’s Soft, ductile, low strength, low density...
CHAPTER 4 ENGINEERING MATERIALS MEC 481 1 CLASSIFICATION OF MATERIALS Metals: Strong, ductile high thermal & electrical conductivity opaque, reflective. Polymers/plastics: Covalent bonding → sharing of e’s Soft, ductile, low strength, low density thermal & electrical insulators Optically translucent or transparent. Ceramics: ionic bonding (refractory) – compounds of metallic & non-metallic elements (oxides, carbides, nitrides, sulfides) Brittle, glassy, elastic non-conducting (insulators) MEC 481 2 CERAMICS : INTRODUCTION racteristian Ceramics are inorganic and nonmetallic. Bonded by ionic or covalent bonds. metallic · non ionic/covalent · Good electrical and heat insulation property. insulator Brittle, and lesser ductility · and toughness than metals. I ductibility High chemical stability and high melting A chemical · stability temperature.(more resistance towards harsh env.), high T and corrosive medium Traditional Ceramics: Basic components (Clay and Silica and feldspar). Engineering Ceramics: Pure compounds (Al2O3, Si3N4, SiC).oxides,nitrides and carbides MEC 481 3 CERAMIC BONDING Bonding: -- Mostly ionic, some covalent. -- % ionic character increases with difference in electronegativity. Large vs small ionic bond character: CaF2: large SiC: small Adapted from Fig. 2.7, Callister 7e. (Fig. 2.7 is adapted from Linus Pauling, The Nature of the Chemical Bond, 3rd edition, Copyright 1939 and 1940, 3rd edition. Copyright 1960 by Cornell University. MEC 481 4 CERAMIC CRYSTAL STRUCTURES Oxide structures oxygen anions much larger than metal cations close packed oxygen in a lattice (usually FCC) cations in the holes of the oxygen lattice In ionic ceramic solid, the packing of the ions is determined by the following factors 1. Relative size of cations and anions 2. Magnitude of the electrical charge MEC 481 5 IONIC BONDING & STRUCTURE 1. Size - Stable structures: --maximize the # of nearest oppositely charged neighbors. - - - - - - + + + Adapted from Fig. 12.1, Callister 7e. - - - - - - unstable stable stable Charge Neutrality: --Net charge in the F- structure should CaF 2 : Ca 2+ + cation anions be zero. F- --General form: A m Xp m, p determined by charge neutrality MEC 481 6 AX CRYSTAL STRUCTURES AX–Type Crystal Structures include NaCl, CsCl, and zinc blende Cesium Chloride structure: rCs + 0.170 = = 0.939 rCl − 0.181 cubic sites preferred So each Cs+ has 8 neighboring Cl- Adapted from Fig. 12.3, Callister 7e. MEC 481 7 AX2 CRYSTAL STRUCTURES Fluorite structure Calcium Fluorite (CaF2) cations in cubic sites UO2, ThO2, ZrO2, CeO2 antifluorite structure – cations and anions reversed Adapted from Fig. 12.5, Callister 7e. MEC 481 8 ABX3 CRYSTAL STRUCTURES Perovskite Ex: complex oxide BaTiO3 Adapted from Fig. 12.6, Callister 7e. MEC 481 9 MECHANICAL PROPERTIES We know that ceramics are more brittle than metals. Why? Consider method of deformation slippage along slip planes in ionic solids this slippage is very difficult too much energy needed to move one anion past another anion (due to the presence of lattice distortion) MEC 481 10 TAXONOMY OF CERAMICS Glasses Clay Refractories Abrasives Cements Advanced products ceramics -optical -whiteware -bricks for -sandpaper -composites engine -composite -bricks high T -cutting -structural -rotors reinforce (furnaces) -polishing -valves -containers/ Adapted from Fig. 13.1 and discussion in Section -bearings household 13.2-6, Callister 7e. -sensors Properties: -- Tm for glass is moderate, but large for other ceramics. -- Small toughness, ductility; large moduli & creep resist. Applications: -- High T, wear resistant, novel uses from charge neutrality. Fabrication -- some glasses can be easily formed -- other ceramics can not be formed or cast. MEC 481 11 CLAY COMPOSITION A mixture of components used (50%) 1. Clay - Provide workability. 12 (25%) 2. Filler – e.g. quartz (finely ground)- Provide better temperature resistance and MP. (25%) 3. Fluxing agent (Feldspar) binds it together aluminosilicates + K+, Na+, Ca+ MEC 481 File:KaolinUSGOV.jpg 375px-NGruev KAOLINITE Clay is inexpensive. Kaolinite is a clay mineral with the Shear chemical composition Al2Si2O5(OH)4. It is a layered silicate mineral, with one tetrahedral sheet linked through charge oxygen atoms to one octahedral sheet neutral of alumina octahedra. When water is added to clay, water Structure of Kaolinite Clay molecules fit between layered sheets, reducing degree of van der Waals weak van bonding; (Can shear along vdW bonds der Waals more easily). bonding When external forces are applied, clay 4+ charge Si particles are free to move past one 3+ another, becoming hydroplastic. neutral Al - OH Adding water to clay enables extrusion O2- and slip casting. Kaopectate, paper, pipes (smoking). Shear CERAMIC FABRICATION METHODS-I GLASS PARTICULATE CEMENTATION FORMING FORMING MEC 481 14 Glass Forming Pressing and Blowing ❑ Some glass blowing is done by hand. ❑ The process is completely automated for the production of glass jars, bottles and light bulbs. ❑ From a raw gob of glass, a parison (temporary shape) is formed by mechanical pressing in a mold. ❑ This piece is inserted into a finishing or blow mold and forced to conform to the mold contours by the pressure created from a blast of air. plates, dishes, cheap glasses --mold is steel with graphite lining DRAWING ❑ Drawing is used to form long glass parts (sheets, rods, tubing and fibers) that have a constant cross section. Fiber drawing: wind up 1. The molten glass is contained in a platinum heating chamber. 2. Fibers are formed by drawing the molten glass through many small orifices at the chamber base. 3. The glass viscosity, which is critical, is controlled by chamber and orifice temperatures. 16 PARTICULATE FORMING Produced by compacting powder or particles into shapes and heated to bond particles together. Material preparation: Particles and binders and lubricants are (sometimes ground) and blend wet or dry. Forming: Formed in dry, plastic or liquid conditions. Cold forming process is predominant. Compaction, slipcasting and extrusion are the common forming processes. MEC 481 17 PARTICULATE FORMING Traditional Ceramic Processing Processing sequence 1. Preparing powders (milling and screening) 2. Shaping of wet clay 3.Drying 4.Firing PARTICULATE FORMING Traditional Ceramic Processing Processing sequence 1. Preparing powders (milling and screening) 2. Shaping of wet clay 3.Drying 4.Firing 1. MATERIAL PREPARATION Milling and screening: desired particle size Mixing particles & water: produces a "slip" The more water in the mixture, the easier to form. But cracking during drying and sintering The slip composition is 25% to 40% water 2.SHAPING OF WET CLAY Slip casting A suspension of ceramic powders in water, called a slip, is poured into a porous plaster of paris mold so that water from the mix is absorbed into the plaster to form a firm layer of clay at the mold surface Two principal variations: – Drain casting - the mold is inverted to drain excess slip after a semi-solid layer has been formed, thus producing a hollow product – Solid casting - to produce solid products, adequate time is allowed pour slip for entire body to become absorb water firm pour slip drain “green into mold into mold into mold mold “green ceramic” ceramic” solid component hollow component Hydroplastic forming: extrude the slip (e.g., into a pipe) Single cross sections and hollow shapes of ceramics can be produced by extrusion. Plastic ceramic material is forced through a hard steel or alloy die by a motor driven augur. Examples: Refractory brick, sewer pipe, hollow tubes. 3.DRYING Water must be removed from the clay piece before firing Shrinkage is a problem during drying because water contributes volume to the piece, and the volume is reduced when it is removed The drying process occurs in two stages: Stage 1: drying rate is rapid and constant as water evaporates from the surface into the surrounding air and water from the interior migrates by capillary action to the surface to replace it. (This is when shrinkage occurs, with the risk of warping and cracking) Stage 2: the moisture content has been reduced to where the ceramic grains are in contact Little or no further shrinkage occurs wet slip partially dry “green” ceramic 4. FIRING Firing: Heat treatment process that sinters the ceramic material performed in a furnace called a kiln Bonds are developed between the ceramic grains which leads to densification and reduction of porosity. Hence additional shrinkage occurs. T raised to (900-1400°C) --vitrification: liquid glass forms from clay and flows between SiO2 particles. Flux melts at lower T.. The temperature at which the liquid phase forms is lowered by the addition of fluxing agents such as feldspar. This fused phase flows around the remaining unmelted particles and fills in the pores as a result of surface tension forces. Upon cooling liquid phase of glass solidifies and a glass matrix that bonds the particles is formed NEW CERAMIC PROCESSING Processing sequence Material preparation Powder pressing Drying firing 1.MATERIAL PREPARATION Millingand screening to get desire size 2.powder pressing 1. uniaxial pressing, the powder is compacted in a metal die by pressure that is applied in a single direction. The formed piece takes on the configuration of die and platens through which the pressure is applied 2. isostatic pressing, the powdered material is contained in a rubber envelope and the pressure is applied by a fluid, isostatically (i.e., it has the same magnitude in all directions). For complicated shapes more time consuming and expensive. Hot pressing - pressure + heat are applied simultaneously Drying: Parts are dried before firing to remove 3. water from ceramic body. Usually carried out at or below 1000C. 4. firing During firing the formed piece shrinks, and experiences a reduction of porosity and an improvement in mechanical integrity Sintering: Small particles are bonded together by solid state diffusion producing dense coherent product. Carried out at higher temperature but below MP. Longer the sintering time, larger the particles are SINTERING - powder particles touch one another -necks form along the contact regions between adjacent particles; - a grain boundary forms within each neck, -every interstice between particles becomes a pore the pores become smaller and more spherical in shape CEMENTATION ❑ Hardening of a paste: paste formed by mixing cement material with water. ❑ Formation of rigid structures having varied and complex shapes. ❑ Hardening process: hydration (complex chemical reactions involving water and cement particles). ❑ Production of Portland cement: ❑ mix clay and lime-bearing minerals ❑ calcine (heat to 1400°C) ❑ grind into fine powder 31 ENGINEERING CERAMICS Alumina (Al2O3): Aluminum oxide is doped with magnesium oxide, cold pressed and sintered. Uniform structure. Used for electric applications. Silicon Nitride (Si3N4): Compact of silicon powder is nitrided in a flow of nitrogen gas. Moderate strength and used for parts of advanced engines. Silicon Carbide (SiC): Very hard refractory carbide, sintered at 21000C. Used as reinforcement in composite materials. Zirconia (ZrO2): Polymorphic and is subject to cracking. Combined with 9% MgO to produce ceramic with high fracture toughness. MEC 481 32 11-21 CERAMIC COMPARISON # Traditional ceramic Engineering ceramic Clay composition; Copound carbide, oxide or nitride material % component purpose Example:1 silicon carbide 50 clay Al2O3.siO2.H2 Provide O workability 2. silicon nitride 25 filler Quartz; SiO2 Provide better 3. alumina oxide temperature resistance and MP 25 Fluxing Feldspar binds it agent K2O3.al2O3. together 6SiO2 Fabrication methods D Traditional ceramic Engineering ceramic Drying Temperature: below 100 Temperature: below 100 Temperature: 800-1400 Temperature: below MP firing Process ; sintering illustration powder particles touch Process Vitrification illustration one another Formation of liquid glass from called i-necks form along the vitrification contact regions between adjacent Liquid glass flow around particles; unmelted silica ii.a grain boundary forms particles. within each neck, iii.every interstice between particles Upon cooling liquid becomes a pore phase of glass solidifies and a glass matrix that the pores become smaller bonds the particles is and more spherical in formed shape polymer Polymers What is a polymer? Poly mer many repeat unit repeat repeat repeat unit unit unit H H H H H H H H H H H H H H H H H H C C C C C C C C C C C C C C C C C C H H H H H H H Cl H Cl H Cl H CH3 H CH3 H CH3 Polyethylene (PE) Polyvinyl chloride (PVC) Polypropylene (PP) Adapted from Fig. 14.2, Callister 7e. MEC 481 36 Origin of Polymers Biopolymers Protein: horn, cartilage, hair, hide, ligaments, tusks Composite structures: bone, shells Plant materials: Cellulose (cotton, sisal, hemp) fiber lignin & cellulose (wood) Chitan (insect & crustacean exoskeletons) Synthetic Polymers Coal Petroleum Natural gas Petroleum from petra oleum (rock oil) Polymers PVC are everywhere PVC Transportation PSty Polyester PES Food Packaging Electronics PVC Polyisoprene PP Clothing Medical Supplies Nylon Construction SAN Manufactured PC Goods Bulk or Commodity Polymers MEC 481 40 MEC 481 41 MEC 481 42 MEC 481 43 Polymer Composition Most polymers are organic, and formed from hydrocarbon molecules Each C atom has four e- that participate in bonds, each H atom has one bonding e- Examples of saturated (all bonds are single ones)hydrocarbon molecules: Propane, C3H8 Methane, MEC 481 CH4 Ethane, C2H6 44 Double and triple bonds can exist between C atoms (sharing of two or three electron pairs). These bonds are called unsaturated bonds. Unsaturated molecules are more reactive Hydrocarbon molecules (II) Ethylene, C2H4 Acetylene, C2H2 Chemistry of Polymers Polymer molecules are very large: macromolecules Most polymers consist of long and flexible chains with a string of C atoms as a backbone. Side-bonding of C atoms to H atoms Double bonds are possible in both chain and side bonds A repeat unit in a polymer chain (“unit cell”) is a mer A single mer is called a monomer MEC 481 46 Molecular shape The angle between the singly bonded carbon atoms is~109o – carbon atoms form a zigzag pattern in a polymer molecule. Moreover, while maintaining the 109 angle between bonds polymer chains can rotate around single C-C bonds (double and triple bonds are very rigid) Random kinks and coils lead to entanglement, like in the spaghetti structure: Molecular chains may thus bend, coil and kink Neighboring chains may intertwine and entangle Large elastic extensions of rubbers correspond to unraveling of these coiled chains Mechanical / thermal characteristics depend on the ability of chain segments to rotate Molecular Structures Covalent chain configurations and strength: secondary bonding branched Linear Cross-Linked Network Direction of increasing strength Van der Waals Chains are connected by Chain packing bonding efficiency is covalent bonds. Often achieved 3D networks made between reduced compared to by adding atoms or molecules from chains. linear polymers - that form covalent links between trifunctional mers. Examples: lower density chains.Many rubbers have this Examples: epoxies, structure. polyethylene, Phenolformaldehyde nylon. MEC 481 48 Linear Polymer Physical Properties Stretch The chains can be stretched, which causes them to flow past each other. When released, the polymer will not return to its original form. Cross-Linked Polymer Stretch Relax The cross-links hold the chains together. When released, the polymer will return to it's original form. Polymers rarely 100% crystalline Polymer Too difficult to get all those chains aligned Crystallinity Polymer molecules are often partially crystalline (semicrystalline), with crystalline regions dispersed within amorphous material. crystalline region % Crystallinity: % of material that is crystalline. -- Annealing causes crystalline regions to grow. % crystallinity increases. As crystallinity is increased : 1.Density increases 2.Stiffness, strength, and toughness increases 3.Heat resistance increases 4.If the polymer is transparent in the amorphous state, it becomes opaque when partially crystallized amorphous region Taxonomy of Polymers Polymeric materials Plastics Elastomers Thermoplastic Thermosetting Vulcanized Unvulcanised Commodities plastic General Use plastic Commodities plastics General use plastics Polyethylene Nylon Phenolics Ureas Polyvinyl chloride Polycarbonates Polyurethane Melamines Polystyrene Acetals MEC 481 Thermoplastic linear/branched Thermoplastic polymers become soft and deformable upon heating. These processes are totally reversible and may be repeated (recyclable) This is the characteristic of linear Polymeric molecules and some branched molecules. The high temperature plasticity is due to the ability of the molecules/ chains to slide past one another. Thermoplastics gain ductility at high temperatures. Thermoplastics are normally fabricated by simultaneous application of heat and pressure. On a molecular level as the temperature is raised , secondary bonding forces are diminished so that the relative movement of adjacent chain is facilitated when stress is applied. easy Thermoplastics are relatively soft and ductile. Processing of thermoplastics products by : injection moulding, blow moulding, thermoforming and vacuum moulding. MEC 481 52 Recycling symbols O O O * O O n * Poly(ethylene terephthalate) or PETE * * n high density polyethylene * * n Cl polyvinyl chloride * * n low density polyethylene Recycling symbols * * n Me poly(propylene) * * n polystyrene Not recyclable Commodity (Amorphous) Thermoplastics Four high volume thermoplastics and applications: – Polyethylene (PE): Grocery bag, 55-gallon drum, lawn furniture – Polypropylene (PP): Washing machine agitator, carpet – Polyvinylchloride (PVC): Irrigation pipe, wire insulation – Polystyrene (PS): Toys, pipes, packing material (Styrofoam) Polystyrene Polyethylene Polypropylene Polyvinylchloride Low cost, temp. resistance and strength Good dimensional stability Bonds well Typically, but not always, transparent Thermoplastic processing Injection moulding Blown film moulding Extrusion 56 56 Thermosetting Plastics Thermosetting become hard and rigid upon heating, this phenomena is not lost upon cooling. This is characteristics of network molecular structures formed by the step growth mechanism. The chemical reaction steps are enhanced by higher temperatures and are irreversible ( non recyclable) During initial heating , covalent cross links are formed between adjacent molecular chains, these bonds anchor the chain together to resist the vibrational and rotational chain motion at high temperatures. Heating to excessive temperature will cause severance of cross link bonds and polymer will degrade. Thermosetting polymers are harder, stronger and more brittle and have better dimensional stability. Processing of thermosetting plastics : Compression moulding, Transfer molding. MEC 481 57 Thermosetting examples & applications 1.Epoxies 2. phenolic 3. polyester Thermosetting processing 1.Compression moulding 1.Transfer moulding 1.The required amount of polymer charge is weighed and inserted into the transfer pot 2. The transfer pot is heated by the heating element above the melting temp. of the polymer charge 3. The plunger is used to push the liquid polymer charge from the transfer pot into the mold cavity 4. The mold cavity is held closed until the resin gets cured. The mold cavity is opened and the molded part can be removed. Elastomers Elastomers can be deformed to very large strains when stressed and then spring back elastically to their original dimensions when the stress is removed. E.g: Natural rubber (polyisoprene). To be elastomeric, the polymer needs to meet several criteria: 1. Resistance to crystallization (elastomers are amorphous) 2. Relatively free chain rotations (unstressed elastomers have coiled/twisted structure – uncoil during deformation) 3. Certain degree of cross-linking (achieved by vulcanization) that increases resistance to plastic deformation 4. Temperature is above the glass transition temperature (below Tg, elastomer becomes brittle MEC 481 60 Key Figures in Polymer History: Invented vulcanization CH3 CH3 of rubber in 1839 HC C HC C CH2 H2C CH2 H2C CH2 H2C CH2 CH3 HC C HC C CH3 H 2C Poly-cis-isoprene IUPAC: cis-poly(1-methyl-1-butene-1,4-diyl) Charles Goodyear Elastomer: (1800 - 1860) 50% of Rubber tires in 1839) Charles Latex rubber gloves Goodyear found vulcanization by S S S S accidentally heating S S S S > 140 °C sulphur-coated rubber which he S observed became S firm and was stable under heating and cooling. Enabled commercialization of natural rubber Vulcanization (I) Croslinking is one of the requirements for elastomeric behavior. It can be achieved by vulcanization - an irreversible chemical reaction usually at high temperatures, and usually involving the addition of sulphur compounds. Sulfur atoms bond with double-bonded C in chain backbones and form the bridge cross-links –to restrict molecular movement Unvulcanized rubber suffers from softening at high ambient temperatures and hardening at low temperatures. Ways were sought to overcome this by treating the rubber with all sorts of chemicals Vulcanization (I) Because they are cross-linked, elastomeric materials are thermosetting polymers Elastic modulus, tensile strength, oxidation resistance increased by vulcanization – magnitude of E proportional to number of cross-links. Too many cross-links reduces extensibility Mechanical Properties i.e. stress-strain behavior of polymers a brittle polymer, which fractures brittle polymer plastic- the initial deformation while deforming is elastic, which is followed by yielding and elastically a region of plastic deformation plastic elastomer elastic modulus – less than metal totally elastic; this rubber-like elasticity (large recoverable strains produced at low stress levels) Strains – deformations > 1000% possible MEC 481 (for metals, maximum strain ca. 10% or less) 64 Polymers: Deformation Bond breaking (high energy) Chain sliding side group ordering (low energy) (high energy) Bond breaking (high energy Chain unfolding, unwinding (low energy at first) Tensile Response: Brittle & Plastic Near Failure (MPa) fibrillar structure x brittle failure near onset of failure necking plastic failure x Initial unload/reload aligned, networked cross- case linked crystalline case regions semi- crystalline amorphous slide crystalline case regions regions align elongate Tilting of lamellar chain folds Separation of crystalline block segments. Tensile Response: Elastomer Case (MPa) x brittle failure Stress-strain curves adapted from Fig. 15.1, Callister 7e. Inset figures along elastomer curve (green) adapted from Fig. 15.15, Callister plastic failure x 7e. (Fig. 15.15 is from Z.D. Jastrzebski, The Nature and Properties of x Engineering Materials, elastomer 3rd ed., John Wiley and Sons, 1987.) final: chains are straight, still cross-linked initial: amorphous chains are Deformation kinked, cross-linked. is reversible! Compare to responses of other polymers: -- brittle response (aligned, crosslinked & networked polymer) -- plastic response (semi-crystalline polymers) MEC 481 T and Strain Rate: Thermoplastics Decreasing T... (MPa) -- increases E 80 4°C Data for the -- increases TS semicrystalline -- decreases %EL 60 polymer: PMMA 20°C (Plexiglas) Increasing strain rate... 40 40°C ductile -- same effects as decreasing T. 20 to 1.3 60°C 0 0 0.1 0.2 0.3 Adapted from Fig. 15.3, Callister 7e. (Fig. 15.3 is from T.S. Carswell and J.K. Nason, 'Effect of Environmental Conditions on the Mechanical Properties of Organic Plastics", Symposium on Plastics, American Society for Testing and Materials, Philadelphia, PA, 1944.) MEC 481 68 Summary General drawbacks to polymers: -- E, y, Kc, Tapplication are generally small. -- Deformation is often T and time dependent. -- Result: polymers benefit from composite reinforcement. Thermoplastics (PE, PS, PP, PC): -- Smaller E, y, Tapplication -- Larger Kc -- Easier to form and recycle Table 15.3 Callister 7e: Elastomers (rubber): -- Large reversible strains! Good overview Thermosets (epoxies, polyesters): of applications -- Larger E, y, Tapplication and trade names -- Smaller Kc of polymers. MEC 481 69 Introduction to Composites Composite Materials ISSUES TO ADDRESS... What are the classes and types of composites? Why are composites used instead of metals, ceramics, or polymers? How do we estimate composite stiffness & strength? What are some typical applications? MEC 481 71 Composites ⚫ Definition- Composite is a material composed of two or more different materials, with the properties of the resultant material being superior to the properties of the materials that make up the composite. ⚫ Combine materials with the objective of getting a more desirable combination of properties – Ex: get flexibility & weight of a polymer plus the strength of a ceramic ⚫ Principle of combined action – Mixture gives “averaged” properties Uses of Composites Composite Bicycle Laminated Fiberglass Bow Graphite Snowboard 73 Composites : getting the best of all worlds heavy Lower Tm Why Composites are Important Composites can be very strong and stiff, yet very light in weight, so ratios of strength-to-weight and stiffness-to-weight are several times greater than steel or aluminum Fatigue properties are generally better than for common engineering metals Toughness is often greater too Composites can be designed that do not corrode like steel Possible to achieve combinations of properties not attainable with metals, ceramics, or polymers alone Composite in industry Engineering applications Aerospace Automobile Pressure vessel and pipes Any place where high performance materials are desired Nature of Composites Advantages: High strength to weight ratio (low density high tensile strength) or high specific strength ratio! High creep resistance High tensile strength at elevated temperatures High toughness Generally perform better than steel or aluminum in applications where cyclic loads are encountered leading to potential fatigue failure (i.e. helicopter blades). Impact loads or vibration – composites can be specially formulated with high toughness and high damping to reduce these load inputs. Some composites can have much higher wear resistance than metals. Corrosion resistance Dimensional changes due to temp changes can be much less. Anisotropic – bi-directional properties can be design advantage (i.e. helicopter blades Nature of Composites Disadvantages (or limitations): Material costs Fabrication/ manufacturing difficulties Repair can be difficult Operating temperature can be an issue for polymeric matrix (i.e. 500 F). Less an issue for metal matrix (2,700 F). Properties non-isotropic makes design difficult! Example –aligned continuous fibers 10X stronger vs fibers oriented at an angle. Inspection and testing typically more complex. A revolution in the use of composite materials for commercial aircraft has recently commenced with the advent of the Boeing 787 Dreamliner Why The Boeing 787 & Airbus A350 Are Built With Composite Materials Use of composites in the Boeing 787 Why The Boeing 787 & Airbus A350 Are Built With Composite Materials 1. Light weight: FRPs are much lighter in weight as compared to metals. The use of composite materials led to more than 30% weight reduction of aircraft structures. Additionally, lower fuel consumption will help to reduce the emission of greenhouse gases. 2. Composite materials used in aerospace structures should have high static strength. Some parts of the structures, for example aircraft wings, should be resistant to extreme forces due to wind shear and other high transient forces. 3. Good fatigue performance is another important requirement for composites used in aerospace engineering. 4. Composites for aerospace engineering should also possess high fracture toughness and damage tolerance. The cracks and flaws present in the structures should not grow quickly leading to sudden failure of the structures. 5. High-impact energy is another essential requirement of aerospace composites to resist against sudden impacts of various types (eg, bird strikes, foreign objects, etc.). 6. Aerospace composites should provide shielding of electromagnetic waves. 7. Composites should provide excellent dimensional stability under a wide range of temperatures (starting from freezing to high temperatures), resistance to lightning strikes, hail, corrosive environments (eg, fluids such as jet fuel, lubricants and paint strippers) and improved fire, smoke and toxicity performance. 8. Availability of affordable and easy designing and manufacturing techniques as well as reliable analysis and prediction tools are also highly essential, in order to compete with other materials used in aerospace engineering. Components in a Composite Material Nearly all composite materials consist of two phases: 1. Primary phase - forms the matrix within which the secondary phase is imbedded The phase which is continuous and surrounds the reinforcement materials (organic, ceramic or metallic) 2. Secondary phase - imbedded phase sometimes referred to as a reinforcing agent (reinforcement), because it usually serves to strengthen the composite The reinforcing phase may be in the form of fibers, particles, or various other geometries PMC – polymer matrix composite CMC – ceramic matrix composite MMC – metal matrix composite Components Reinforcement: fiber of composite materials Matrix materials Interface Glass Polymers Bonding Carbon Metals surface Organic Ceramics Boron Ceramic Metallic Function of the Matrix Support and protect the fibre (reinforcement) , The principal load carrying agent To provide a means of distributing the load among and transmitting it between the fibre(reinforcement) without itself fracturing. Serves as the binder to hold the reinforcement together in place. MEC 481 84 Classification based on matrix Composite matrices Polymer matrix Ceramic matrix Metal matrix composite composite composite (MMC) (PMC) (CMC) Thermoset Thermoplastic Rubber Epoxy Nylon Polyester Polyetheretherketone (PEEK) Phenolics Reinforcement A phase which is embedded in a matrix (varying amounts) Reinforcement can be in the form of fibre, particles/particulates and laminates Relative amounts, geometry (shape, particle size, distribution and orientation) affect the resultant properties The reinforcement materials can be of the ceramic , polymer, or metals. Examples of reinforcement materials:Carbon ,Silicon Carbide, Alumina, Boron MEC 481 86 Classification based on reinforcement Composites Particle-reinforced Fiber-reinforced Structural Large- Dispersion- Continuous Discontinuous Laminates Sandwich particle strengthened (aligned) (short) panels Aligned Randomly oriented MEC 481 88 Particles Reinforced A common shape of imbedded phase is particulate, ranging in size from microscopic to macroscopic Flakes are basically two-dimensional particles - small flat platelets The distribution of particles in the composite matrix is random, and therefore strength and other properties of the composite material are usually isotropic Strengthening mechanism depends on particle size Examples: - Spheroidite matrix: particles: steel ferrite () cementite (ductile) (Fe3 C) (brittle) 60 m Concrete which is a structural composite obtained by combining (through mixing) cement (the matrix, i.e., the binder, obtained by a reaction – known as hydration – between cement and water), sand (fine aggregate), gravel (coarse aggregate), and optionally other ingredients that are known as admixtures. Short fibers and silica fume (a fine SiO2 particulate) are examples of admixtures Reinforced concrete - Reinforce with steel rerod or remesh - increases strength - even if cement matrix is cracked Post tensioning – tighten nuts to put under tension threaded rod nut PRESTRESSED CONCRETE Prestressed concrete - remesh under tension during setting of concrete. Tension release puts concrete under compressive force - Concrete much stronger under compression. - Applied tension must exceed compressive force Elastic modulus, Ec, of composites: -- two approaches. For effective reinforcement, the particles should be small and evenly distributed throughout the matrix. The volume fraction of the two phases influences the behavior; mechanical properties are enhanced with increasing particulate content. Rule of mixture: equation predict that the elastic modulus should fall between an upper and lower bound as upper limit: “rule of mixtures” shown: Ec = VmEm + VpEp E(GPa) Data: 350 Cu matrix 30 0 lower limit: w/tungsten 250 1 Vm Vp = + particles 200 E c Em Ep 150 0 20 40 60 80 10 0 vol% tungsten (Cu) (W) Application to other properties: -- Electrical conductivity, e: Replace E in equations with e. -- Thermal conductivity, k: Replace E in equations with k. MEC 481 92 Fibers reinforced Filaments of reinforcing material, usually circular in cross-section Diameters range from less than 0.0025 mm to about 0.13 mm, depending on material Filaments provide greatest opportunity for strength enhancement of composites The filament form of most materials is significantly stronger than the bulk form As diameter is reduced, the material becomes oriented in the fiber axis direction and probability of defects in the structure decreases significantly Fibers very strong – Provide significant strength improvement to material – E.g.: fiber-glass Continuous glass filaments in a polymer matrix Strength due to fibers Polymer simply holds them in place Function of the Fiber Carry the load 70 to 90% of load carried by fibers Provide structural properties to the composite Stiffness Strength Thermal stability Provide electrical conductivity or insulation copyright J. Anderson, 2008 Commercial Fiber Fibers are available as Yarn – a bundle of fibers twisted together Tow - Large bundles (Carbon Fiber), several thousand fibers Roving - Large bundles (Fiber Glass) Uni-directional tape Woven fabric or mat Fiber materials Whiskers - Thin single crystals - large length to diameter ratio graphite, Si3N4, SiC high crystal perfection – extremely strong, strongest known very expensive Impractical to incorporate into the matrix – Fibers polycrystalline or amorphous generally polymers or ceramics Ex: Al2O3 , Aramid, E-glass, Boron, UHMWPE – Wires Metal – steel, Mo, W Fiber Alignment aligned aligned random continuous discontinuous Aligned continuous The fibres are longer than a critical length which is the minimum length necessary such that the entire load is transmitted from the matrix to the fibres. If they are shorter than this critical length, only some of the load is transmitted. Fibre lengths greater that 15 times the critical length are considered optimal. Aligned and continuous fibres give the most effective strengthening for fibre composites Discontinuous & Aligned The fibres are shorter than the critical length. Hence discontinuous fibres are less effective in strengthening the material, however, their composite modulus and tensile strengths can approach 50-90% of their continuous and aligned counterparts. And they are cheaper, faster and easier to fabricate into complicated shapes Random This is also called discrete, (or chopped) fibres. The strength will not be as high 97 as with aligned fibres, however, the advantage is that the material will be isotropic and cheaper. Composite Strength:Longitudinal Loading Continuous fibers - Estimate fiber-reinforced composite L strength for long continuous fibers in a matrix L L I : Longitudinal deformation - c = mVm + fVf but c = m = f Grease volume fraction isostrain Ece = Em Vm + EfVf longitudinal (extensional) modulus Ff EfVf f = fiber = Fm EmVm m = matrix MEC 481 98 Composite Strength: Transverse Loading In transverse loading the fibers carry less of the load - isostress c = m = f = c= mVm + fVf is o stress equal stress : 1 Vm Vf = + Ect Em Ef transverse modulus MEC 481 99 Example A continuous and aligned glass fiber–reinforced composite consists of 40 vol% glass fibers having a modulus of elasticity of 69 GPa and 60 vol% polyester resin that, honeycomb when hardened, displays a modulus of 3.4 GPa. shap (a) Compute the modulus of elasticity of this 2024 past year composite in the longitudinal direction. I solution Pomestea 60 % = 0. 6 I. Ecl = EmVm + EfVf -stibe VS 40 % Vm = 60 % Ecl = (3.4 GPa)(0.6) + (69 GPa)(0.4) = Pa) 9 (3 4x10 = 30 GPa. Composite Fiber Materials Common Fibers Used in Composites Glass, or fiberglass Starts as a silica sand Carbon Starts as a polyacrylonitrile fiber copyright J. Anderson, 2008 Structural Composites A structural composite consists of both homogeneous and composite material. There properties depend on, the characteristic properties of the constituent materials as well as the geometric design. Structural composite are of two types:- 1.Laminar compost 2.Sandwich panel Laminar Composite It consists of panels or sheets which are Such successively oriented layers are two dimensional. These panels possess stacked one above with preferred preferred directions to achieve high directions and then are cemented. Such an strength. arrangement or orientation ensures varying highest strength with each successive layer involved in material Sandwich panel Sandwich panel is also a kind of layered Faces:-They are formed by two strong composite. It consists of ‘faces’ outer sheets. and ‘core’ Core:-Core is layer of less dense With increase in thickness of material. core, its stiffness increases as Honeycomb:-Structure which contain seen in the most common thin foils forming interlocked hexagonal sandwich panel ‘honeycomb cells with their axes oriented at right angles in the direction of face sheet. Polymer Matrix composites Polymer matrix composites (PMC) and fiber reinforced plastics (FRP) are referred to as Reinforced Plastics. Common fibers used are glass (GFRP), graphite (CFRP), boron, and aramids (Kevlar). These fibers have high specific strength (strength-to-weight ratio) and specific stiffness (stiffness- toweight ratio) Matrix materials are usually thermoplastics or thermosets; polyester, epoxy (80% of reinforced plastics), fluorocarbon, silicon, phenolic Polymer Matrix Composites (PMCs)- Glass Fibers Matrix(plymer resin)+reinforcemet(fiber eg:glass ,carbon,aramid) Glass fiber reinforced plastic composite materials have high strength-weight ratio, good dimensional stability, good temperature and corrosion resistance and low cost. ‘E’ Glass : 52-56% SiO2, + 12-16% Al2O3, 16-25% CaO + 8-13% B2O3 ❖ Tensile strength = 3.44 GPa, E = 72.3 GPa ‘S” Glass : Used for military and aerospace application. 65% SiO2 + 25% Al2O3 + 10% MgO ❖ Tensile strength = 4.48 GPa, E = 85.4 GPa MEC 481 106 Polymer Matrix Composites (PMCs) – Carbon Fibers Light weight, very high strength and high stiffness. 7-10 micrometer in diameter. Produced from polyacrylonitrile (PAN) and pitch. Steps: Stabilization: PAN fibers are stretched and oxidised in air at about 2000C. Carbonization: Stabilized carbon fibers are heated in inert atmosphere at 1000-15000C which results in elimination of O,H and N resulting in increase of strength. Graphitization: Carried out at 18000C and increases modulus of elasticity at the expense of strength Tensile strength = 3.1-4.45 GPa, E = 193-241 GPa, density = 1-7-2.1 g/cc. MEC 481 107 Polymer Matrix Composites (PMCs)-Aramid Aramid = aromatic polyamide fibers. Trade name is Kevlar Kevlar 29:- Low density, high strength, and used for ropes and cables. Kevlar 49:- Low density, high strength and modulus and used for aerospace and auto applications. Hydrogen bonds bond fiber together. Used where resistance to fatigue, high strength and light weight is important. METAL MATRIX COMPOSITE The metal matrix composites offer higher modulus of elasticity, ductility, and resistance to elevated temperature than polymer matrix composites. But, they are heavier and more difficult to process. MEC 481 Metal Matrix Composites (MMCs) Continuous fiber reinforced MMCs: Continuous fibers are reinforced in metal matrix – used in aerospace, auto industry and sports equipments. Example:- Aluminum alloy – Boron fiber composite (driveshaft) Boron fiber is made by depositing boron vapor on tungsten substrate. Boron fibers are hot pressed between aluminum foils. Tensile strength of Al6061 increases from 310 to 1417 GPa and E increases from 69 to 231 GPa Tungsten filament Boron Figure 11.46 MEC 481 After “Engineered Materials Handbook,” vol. 1, ASM International, 1987, p.852. Ceramic Matrix COMPOSITE Ceramic matrix composites (CMC) are used in applications where resistance to high temperature and corrosive environment is desired. CMCs are strong and stiff but they lack toughness(ductility) Matrix materials are usually silicon carbide, and aluminum oxide, and mullite (compound of aluminum, silicon and oxygen). They retain their strength up to 3000 oF. Fiber materials used commonly are carbon and aluminum oxide. Applications are in jet and automobile engines, deep-see mining, cutting tools, dies and pressure vessels. Ceramic-Matrix Composites (CMCs) primary goal of the ceramic reinforcement is to provide toughness to a brittle ceramic Continuous fiber reinforced CMCs: SiC fibers are woven into mat and SiC is impregnated into fibrous mat by chemical vapor deposition. SiC fibers can be encapsulated by a glass ceramic. Used in heat exchanger tube and thermal protection system. Discontinuous and particulate reinforced CMCs: Fracture toughness is significantly increased. Fabricated by common process such as hot isolatic pressing. Composite Benefits PMCs: Increased E/ CMCs: Increased toughness ceramics 103 Force E(GPa) particle-reinf 102 PMCs 10 metal/ 1 metal alloys fiber-reinf.1 G=3E/8 polymers un-reinf.01 K=E.1.3 1 3 10 30 Density, [mg/m3] Bend displacement 10-4 ss(s-1) 6061 Al MMCs: 10-6 Adapted from T.G. Nieh, "Creep rupture Increased of a silicon-carbide reinforced aluminum composite", Metall. Trans. A creep 10-8 6061 Al Vol. 15(1), pp. 139-146, 1984. Used w/SiC with permission. resistance whiskers 10-102030 50 100 200(MPa) MEC 481 113 Summary Composites are classified according to: -- the matrix material (CMC, MMC, PMC) -- the reinforcement geometry (particles, fibers, layers). Composites enhance matrix properties: -- MMC: enhance y, TS, creep performance -- CMC: enhance Kc -- PMC: enhance E, y, TS, creep performance Particulate-reinforced: -- Elastic modulus can be estimated. -- Properties are isotropic. Fiber-reinforced: -- Elastic modulus and TS can be estimated along fiber dir. -- Properties can be isotropic or anisotropic. Structural: -- Based on build-up of sandwiches in layered form. MEC 481 114 Q4.1 An aligned and continuous fibre reinforced composite was manufacture from epoxy, E glass fibre and carbon fibre. The properties of the materials are tabulated in table. Material Elastic Density (g/cm3) modulus(GPa) Epoxy 2.41 1.14 E glass fibre 72.5 2.58 Carbon fibre 400 1.8 i. Initially, the E Glass fiber takes up 20% volume fraction. Calculate the longitudinal elastic modulus of composite ii. Calculate the density of the hybrid composite which contain 10% volume fraction of additional new fiber iii. Estimate the modulus elasticity of the composite if its contains 5 vol percent voids. State any assumption made. iv. State any 3 factors that must be considered when designing a fiber reinforced composite