Measuring Instruments PDF
Document Details
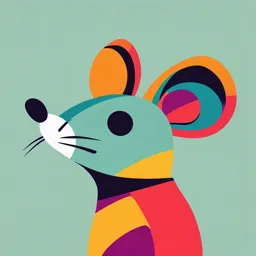
Uploaded by TrustworthyChalcedony3185
Department of Electrical Engineering
Tags
Related
Summary
This document provides an introduction to measuring instruments, covering classifications, absolute and secondary instruments, and different types based on operational characteristics, such as indicating, recording, and integrating instruments. It also details the importance of deflecting torque, controlling torque, and damping torque in these instruments.
Full Transcript
DEPARTMENT OF ELECTRICAL ENGINEERING EEM MEASURING INSTRUMENTS Introduction Measurement: It is the act or result of quantitative comparison between a predefined standard an...
DEPARTMENT OF ELECTRICAL ENGINEERING EEM MEASURING INSTRUMENTS Introduction Measurement: It is the act or result of quantitative comparison between a predefined standard and an unknown quantity. Instrument: It is a device or mechanism used to determine the present value of a quantity under observation. Classification of Instruments Instruments can be classified as: 1. Absolute instruments 2. Secondary instruments Absolute instruments: Give the magnitude of the quantity in terms of the constants of the instruments and its deflection. No comparison with standard instrument is necessary. Example: tangent galvanometer, used for measuring electric current Secondary instruments: The secondary instruments need calibration with respect to the absolute instruments. The secondary instruments determine the value of the quantity being measured from the deflection of the instruments. Calibration is a must for secondary instrument, without calibration the deflection obtained is meaningless. Example: Ammeter, voltmeter, wattmeter etc. Based on the nature of operation: 1. Indicating 2. Recording 3. Integrating Indicating instruments indicate the instantaneous value of quantity under measurement. e.g. Ordinary voltmeters, ammeters & wattmeter's Recording instruments give a continuous record of variation of quantity being measured (such as voltage, frequency, power etc.). Recorders are commonly used in power plants, process industries. e.g. ECG (Electro- Cardio-Gram). An integrating instrument is one which takes into consideration the period or the time over which the quantity is supplied. e.g. ampere-hour meter, energy meter. 1/5 DEPARTMENT OF ELECTRICAL ENGINEERING EEM Electrical instruments can also be classified as: 1. A.C. instruments 2. D.C. instruments 3. A.C./D.C. instruments Some electrical instruments can measure only A.C. quantity, e.g. induction type instruments, some can measure only D.C. quantity, e.g. P.M.M.C. instruments. Some can work on both a.c. and d.c. e.g. moving iron instruments, dynamometer instruments etc. Another way of classifying instrument is: 1. Analog instruments 2. Digital instruments Analog information is continuous and stepless function of time. Analog instruments are easy to understand, calibrate and maintain. Digital information is in form of discrete pulses or steps. Digital instruments have higher resolution, high readability. Operation of Indicating Instruments For satisfactory operation of any indicating instrument, following three torques must act together appropriately: 1. Deflecting torque 2. Controlling torque 3. Damping torque 1. Deflecting Torque: It causes the moving system of the instrument to move from its position of rest. Deflecting torque is produced by using any one of the following effects of electric current: a. Magnetic effect b. Electromagnetic induction effect c. Heating effect d. Chemical effect e. Electrostatic effect (Types of instruments where these effects are used) 2. Controlling Torque: It limits the movement of moving systems. It also ensures that magnitude of deflection is always the same for the given value of input quantity under measurement. Controlling torque acts in the opposite direction to that of the deflecting torque. The controlling torque serves two functions : The pointer stops moving beyond the final deflection The pointer comes back to its zero position when the instrument is disconnected. At steady state, Deflecting torque = Controlling torque 2/5 DEPARTMENT OF ELECTRICAL ENGINEERING EEM 3. Damping Torque: Due to deflecting torque, pointer moves in one direction while due to controlling torque pointer moves in opposite direction. Due to these opposite torques, the pointer may oscillate in the forward and backward direction if the damping torque is not present. Damping torque brings the moving system to rest quickly in its final position. Damping torque acts only when the moving system is actually moving. If moving system is at rest, damping torque is zero. Critical Damping: Depending on the magnitude of torque, damping may be classified as underdamped, overdamped or critically damped. Effect of damping on the deflection of the instrument is shown in fig. If the instrument is underdamped, the pointer will come to rest after some oscillations. If the instrument is overdamped, pointer takes considerable time to obtain its final deflected position. If the damping is critical, without oscillation and in short time the pointer reaches its final steady position. Fig.: Effect of damping on the deflection of instrument (i) Spring Control Most commonly used. One or two hairsprings made of phosphor bronze are used. The outer end of this spring is fixed and the inner end is attached with the spindle. When the pointer is at zero of the scale, the spring is normal. As the pointer moves, the spring winds and produces an opposing torque. The balance-weight balances the moving system so that its centre of gravity coincides with the axis of rotation, thereby reducing the friction between the pivot and bearings. 3/5 DEPARTMENT OF ELECTRICAL ENGINEERING EEM Double Springs Two springs A and B are wound in opposite directions. On deflection, one spring winds while the other unwinds. To make the controlling torque directly proportional to the angle of deflection, the springs should have fairly large number of turns. Advantages: Since c and d I ; at final position, c d Hence, I These instruments have uniform scale. Disadvantages: The stiffness of the spring is a function of temperature. Hence, the readings given by the instruments are temperature dependent. Furthermore, with the usage the spring develops an inelastic yield which affects the zero position of the moving system. It is simple, rigid but costlier. 4/5 DEPARTMENT OF ELECTRICAL ENGINEERING EEM (ii) Gravity Control A small control weight is attached to the moving system. In addition, an adjustable balance weight is also attached to make the centre of gravity pass through the spindle. In zero position of the pointer, this control weight is vertical. When deflected by an angle θ, the weight exerts a force, W sin The restraining or controlling torque is thus developed is given as c W sin L WL sin Since d I , and c d or WL sin kI WL I sin k or I sin Disadvantages: 1. These do not have uniform scale. 2. These must be used in vertical position so that the control may operate properly. 3. As delicate and proper levelling required, in general it is not used for indicating instruments and portable instruments. Advantages: 1. Less expensive. Errors & classification 2. Unaffected by changes in temperature. 3. Free from fatigue or deterioration with time. 5/5