Theoretical and Experimental Studies on Thermal Properties of Polyester Nonwoven Fibrous Materials PDF
Document Details
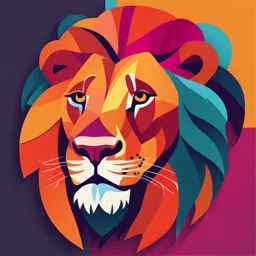
Uploaded by CharismaticCosmos9936
Northern Iloilo State University
Tao Yang, Xiaoman Xiong, Michal Petrů, Xiaodong Tan, Hiroki Kaneko, Jiří Militký, and Atsushi Sakuma
Tags
Summary
This study presents a theoretical and experimental analysis of the thermal conductivity of polyester nonwoven fibrous materials. The research focuses on the effect of fiber orientation on thermal properties and compares results with existing models for prediction. The findings suggest a modified model accurately predicts the thermal conductivity within a 0.2% margin of error.
Full Transcript
materials Article Theoretical and Experimental Studies on Thermal Properties of Polyester Nonwoven Fibrous Material Tao Yang 1, *, Xiaoman Xiong 2 , Michal Petrů 1 , Xiaodong Tan 2 , Hiroki Kaneko 3 , Jiří Militký 2 and Atsushi Sakuma 3 1 Institute for Nanomaterials, Advanced Technologies and I...
materials Article Theoretical and Experimental Studies on Thermal Properties of Polyester Nonwoven Fibrous Material Tao Yang 1, *, Xiaoman Xiong 2 , Michal Petrů 1 , Xiaodong Tan 2 , Hiroki Kaneko 3 , Jiří Militký 2 and Atsushi Sakuma 3 1 Institute for Nanomaterials, Advanced Technologies and Innovation, Technical University of Liberec, 461 17 Liberec, Czech Republic; [email protected] 2 Department of Material Engineering, Faculty of Textile Engineering, Technical University of Liberec, 46117 Liberec, Czech Republic; [email protected] (X.X.); [email protected] (X.T.); [email protected] (J.M.) 3 Department of Advanced Fibro-Science, Kyoto Institute of Technology, Matsugasaki, Sakyo-ku, Kyoto 606-8585, Japan; [email protected] (H.K.); [email protected] (A.S.) * Correspondence: [email protected] Received: 28 May 2020; Accepted: 22 June 2020; Published: 26 June 2020 Abstract: Polyester nonwoven fibrous material is widely used in construction and automobile industries for thermal insulation purposes. It is worthy and meaningful to understand the effect of structural parameters on the thermal property. Fiber orientation, as one of the most vital parameters, has a significant effect on thermal property. However, there has been little quantitative analysis focusing on this aspect. This paper theoretically and experimentally analyzes the thermal conductivity of samples with varying fiber orientation. Existing models were selected to predict the thermal conductivity of polyester nonwoven samples. Two different apparatus were applied to carry out the experimental measurements. The relative differences between the predicted and measured results were compared. One commonly used model was modified for accurate prediction. It was shown that some existing models under- or overestimate the thermal conductivity compared to the measured values. The results indicate that the modified model can accurately predict the thermal conductivity of polyester nonwoven materials within a 0.2% relative difference. Keywords: polyester; fiber orientation; thermal conductivity; models; modification 1. Introduction Recently, nonwoven fibrous materials have been extensively used in construction and automobile industries due to their high porosity, economical price, lightweight, a large thickness range, good sound absorption, etc. The most common application of nonwoven materials in industries is as a dual insulator (thermal and sound) in buildings [1–3]. The thermal property of nonwoven fibrous material has attracted considerable attention. The application in thermal insulation of some bast-fibrous materials such as flax and hemp have been verified due to their suitable insulation properties. However, bast-fibrous materials have a risk for microbial and other contaminants, and their quality should be monitored regularly because of the aging effect. The thermal properties of recycled waste clothing textiles for building application have been reported. The inverse method was adopted to study the thermal properties of a fibrous insulator due to the arbitrary distribution of fiber size in waste clothing textiles. Cerkez et al. presented the thermal insulation property of a multi-component air-laid nonwoven and stated that an increase in the amount of glass fiber resulted in lower thermal insulation. A novel approach used to apply silica aerogel into nonwoven fibrous materials for thermal insulation purpose has also been reported. It was found that an aerogel encapsulated nonwoven composite has a remarkable rise on thermal resistance compared to the sample without aerogel. Materials 2020, 13, 2882; doi:10.3390/ma13122882 www.mdpi.com/journal/materials Materials 2020, 13, 2882 2 of 18 Aside from the influence of material on the thermal properties of a nonwoven fibrous material, the effect of producing technology and structural characteristics needs to be considered. Thickness and porosity have been confirmed as the most important factors to determine the thermal properties of nonwoven fibrous materials. The thermal insulation property of perpendicular-laid and cross-laid high-loft nonwoven materials has been studied. According to the thermal conductivity results, cross-laid nonwoven has better thermal insulation than perpendicular-laid nonwoven. It was also found that the thermal conductivity decreased when the density increased in these two high-loft nonwoven structures. In addition, nonwoven fibrous materials made from coarse fibers have higher thermal resistance when the compression load is applied. A number of studies have reported on the effect of material type, structural parameter, and manufacturing technology on the thermal property of nonwoven fibrous materials. However, one important factor that researchers have not treated in much detail is fiber orientation. It has been reported that fiber orientation has a significant influence on thermal properties [10–12]. If the fibrous materials have the same fiber components, fiber orientation should be primarily considered. Some existing models can be used to estimate the thermal conductivity of nonwoven material when fibers are randomly, perpendicularly, and parallelly orientated to the direction of heat flow. However, these models do not involve the accurate effect of fiber orientation. The main objective of this paper was to study the thermal properties of a polyester nonwoven fibrous material, especially for materials with different through-plane fiber orientations. The rest of this paper is organized as follows. Thermal conductivity models for fibrous material are recalled in Section 2. Section 3 outlines the materials, methods of theoretical study, and experimental study. The results from the theoretical and experimental studies are presented and analyzed, along with modifications on an existing model in Section 4, followed by a brief conclusion. 2. Review of Thermal Conductivity Models Theoretically, thermal conduction always occurs if a temperature gradient exists between a material system and the environment or inside a material system. It is considered that no natural convection occurs in fibrous material with a density larger than 20 kg/m3 because the fibers subdivide the gas into sufficiently small pores [15,16]. Additionally, it has been stated that the convection can be eradicated due to the significant friction that is caused by constituent fibers against natural convection. Sun and Pan stated that heat transfer via radiation can be ignored when the temperature gradient is small. The heat transfer through radiation will be considered when the temperature is higher than 500 K. Furthermore, it has been stated that heat transfer modes are generally dependent on the ambient temperature and fibrous material porosity. Thus, thermal conduction is the dominant mechanism in most situations when heat is transferred through a nonwoven fibrous material. Most of the models used to analyze the heat transfer behavior of fibrous materials have been developed based on electrical network analysis, which is called thermal-electrical analogy [20,21]. Some models based on thermal-electrical analogy will be introduced, and several semiempirical models are included in this section. 2.1. Semi-Empirical Models Semi-empirical models are proposed for the quick assessment of the thermal conductivity of fibrous materials. Schuhmeister presented an empirical equation to simply calculate the thermal conductivity of a homogeneous and isotropic nonwoven material in 1877. Baxter modified Schuhmeister’s Equation to estimate the conductivity of a wool fibrous material. A semi-empirical model that applied an empirical coefficient for a different type of fiber was developed by Verschoor and Greebler. Some semi-empirical models for thermal conductivity estimation are summarized in Table 1. Materials 2020, 13, x FOR PEER REVIEW 3 of 19 and Greebler. Some semi-empirical models for thermal conductivity estimation are summarized Materials 2020, 13, 2882 3 of 18 in Table 1. Table Table 1. 1. Some Some semi-empirical semi-empirical models models for for thermal thermal conductivity conductivity estimation. estimation. No. No. Thermal Conductivity Thermal Conductivity Reference Reference 1 2 =1 + + 2 ⁄( 1 va + k f + v f k)a Schuhmeister 1 Schuhmeister 3 k = 3 v fk f + va k3a + 3 k f ka / a + 0.79 k ⁄ 2 =2 0.21k = 0.21+v f k f + v+a k0.79 f k(a / va k+ f + v f ka) Baxter Baxter 3 = 3 vmf k f + ka k =+ Verschoor and Greebler Verschoor and Greebler vf 4 = 4 k = k f kava Tavman Tavman Models Based 2.2. Models Based on on Thermal-Electrical Thermal-Electrical Analogy Analogy Electronic components Electronic components areare connected connected in in parallel parallel or or series series arrangement arrangementin in an an electrical electricalnetwork. network. Similarly, fibers in a fibrous material are assumed to be perpendicularly (serially), (serially), parallelly, parallelly, or or randomly distributed in the direction of heat flow. The The sketches sketches of of fibers fibers orientated parallel and perpendicular to perpendicular to the direction of heat flow are shown in Figure Figure 1. arrangement ((b) 1. In parallel arrangement ((b) in Figure 1), 1), the therelatively relativelyhigh conductivity high of the conductivity fibers of the contributes fibers their their contributes maximum effect on maximum the on effect overall the conductivity of the fibrous material. In contrast, the fibers contribute a minimum effect to overall conductivity of the fibrous material. In contrast, the fibers contribute a minimum effect to thethe overall thermalthermal overall conductivity of the fibrous conductivity of thematerial fibrous because materialofbecause the air layer of thebetween each air layer fiber element between in a each fiber perpendicular element arrangement.arrangement. in a perpendicular Heat Flow Heat Flow Gas Phase Solid Phase (Air) (Fiber) Solid Phase (Fibers) Gas Phase (Air) Heat Flow Heat Flow (a) (b) Figure 1. Fibers orientated Figure 1. orientated perpendicular perpendicular (a) (a) or or parallel parallel (b) (b) to to the the direction direction of of heat heat flow. flow. Bogaty et Bogaty et al. al. proposed proposed models models forfor fibrous fibrous material material with with different different fiber fiber arrangements. arrangements. Bhattacharyya Bhattacharyya presented presentedtwo two models models to predict to predict the the thermal thermal conductivity conductivity of samples of samples with with fibers fibers perpendicularly and randomly to the heat flow based on Fricke’s perpendicularly and randomly to the heat flow based on Fricke’s method for electrical method for electrical conductivity. Some conductivity. Some models models used used to to simply simply calculate calculate thethe thermal thermal property property ofof fibrous fibrous material material with with parallel, perpendicular, and random fiber orientations are summarized parallel, perpendicular, and random fiber orientations are summarized in Table 2. in Table 2. These models have been adopted to predict the thermal properties of woven, knitted, and nonwoven Table 2. fibrous Some materials [27–29]. models for fibrousMilitký materialet al. with accurately parallel, predicted and perpendicular, the thermal random resistivity fiber of wool/polyester orientations. plain woven fabric by computing the average value of models 5 and 6 in Table 2. Bogaty obtained the relative specific thermal conductivity of wool, cotton, nylon, and orlon fibrous Fiber Orientation to the materials No. by using the calculated Thermal values of the effective fraction of fibers orientated Conductivity parallel and Reference Direction of Heat Flow perpendicular to the heat flow via model 8. Nevertheless, these models provide a rough estimation of 5 = + Parallel Bogaty et al. the thermal resistivity of fibrous material. It has been proven that fiber orientation has a significant influence 6 =on thermal conductivity [10,30]. Thus, a more Perpendicular precise prediction that takes intoetaccount Bogaty al. the + specific fiber orientation angle should be considered. The mechanistic assumption that the thermal Materials 2020, 13, x FOR PEER REVIEW 3 of 19 conductivity in fiber oriented to an arbitrary angle from the heat flow direction is simply the sum of the 1− ⁄ 7 = 1− Bhattacharyya 2 ⁄ ⁄ 1+ 1+ ⁄ 8 2020, Materials = 13, 2882 + + + Bogaty et al. 4 of 18 Random 1 − in⁄the fiber axis direction and radial direction used. This assumption is contributions of conductivities 9 = 1− Bhattacharyya supported by the Debye1 +equation 5 ⁄ for the⁄prediction of the thermal conductivity. 1+ 3 1+ ⁄ Table 2. Some models for fibrous material with parallel, perpendicular, and random fiber orientations. These models have been adopted to predict the thermal properties of woven, knitted, and Fiber Orientation to the No. Thermal Conductivity nonwoven fibrous materials [27–29]. Militký et al.Direction accurately predicted the Reference thermal resistivity of of Heat Flow wool/polyester 5 plain k = v f k f + va ka woven fabric by computing the average Parallel value of models 5 and 6 in Table 2. Bogaty et al. Bogaty obtainedk the relative specific thermal conductivity of wool, cotton, nylon, and orlon f ka 6 fibrous materials k =by using the calculated values of the effective fraction ofBogaty fibers etorientated al. parallel k a v f + k f v a Perpendicular and perpendicular to the1−k heat flow via model 8. Nevertheless, these models provide a rough a /k f estimation7 of thek =thermal 1 − resistivity k off fibrous material. It has been proven Bhattacharyya that fiber orientation has 2 ( k a /k f )( v f /v a ) 1+ a significant influence on thermal (1+ka /k f )conductivity [10,30]. Thus, a more precise prediction that takes into account the specific fiber orientation angle vf −1should be considered. The mechanistic assumption that k = x v f k f + va ka + y k + vka 8 Bogaty et al. the thermal conductivity in fiber oriented f to an arbitraryRandom a angle from the heat flow direction is simply the sum of the contributions ofa /kconductivities in the fiber axis direction and radial direction used. 1−k f 9 k = 1 − k This assumption is supported 1+ ( ( a by 1 + 5 k /k f ))( thev f aDebye /v ) f equation for the prediction ofBhattacharyya the thermal conductivity 3(1+ka /k f ). The fiber orientation in nonwoven fibrous materials refers to the fiber orientation angle, as shownThein Figure fiber 2. Angles orientation in nonwoven and represent fibrous materials the through-plane and in-plane refers to the fiber orientationorientation angles, angle, as shown inrespectively. Whenθ and Figure 2. Angles δ represent is zero, the fibers theare parallel to the through-plane anddirection in-planeoforientation heat flow. If is 90°, angles, the fibers respectively. When θ is zero, the fibers are perpendicular to the aredirection parallel toof theheat flow.ofFibers direction If θthrough-plane in the heat flow. is 90◦ , the fibersorientation have a are perpendicular tosignificant effect the direction on thermal of heat flow. Fibers properties in the through-plane while the in-plane orientation orientation have ahas less effect significant. effect onThus, the thermal angle iswhile properties a critical the in-plane value inorientation the demonstrated has less situation effect.where Thus,the angle θ isofa heat thedirection flow critical is parallel value in the to the Z-axis. situation where the direction of heat flow is parallel to the Z-axis. demonstrated Figure2.2.Fiber Figure Fiberorientation orientationangle angleininthree-dimensional three-dimensionalnonwoven nonwovenfibrous fibrous material. material. Oneseries One seriesofofmodel modelthat thatcan canbe beused usedto topredict predictthe thethermal thermalconductivity conductivityof offibrous fibrousmaterial materialwith with varyingfiber varying fiberorientation orientation based based onon Bhattacharyya’s Bhattacharyya’s research research waswas developed developed by Stark by Stark and Fricke and Fricke in in 1993. 1993. TheyThey stated stated thatthat it isitnecessary is necessary to pay to pay attention attention to to thethe effect effect ofofcontact contactbetween betweenfibers fiberson on conductivity.The conductivity. Thebasic basicmodel modelof ofthermal thermalconductivity conductivityof offibrous fibrousmaterial materialbased basedononBhattacharyya’s Bhattacharyya’s assumptionsisisrepresented assumptions representedas:as: Materials 2020, 13, x FOR PEER REVIEW 4 of 19 vf va − 1 kBM = k f 1 + vf vf (1) ka 1+ k f 1 + Z va − 1 / va +1 The term Z is the fraction of fiber orientation to the macroscopic heat flow (Z = 1 when fibers are aligned perpendicular to the heat flux, Z = 0.66 when randomly arranged, and Z = 0.83 when arranged parallel to the heat flux). One critical orientation angle, ψ = cos−1 2/3 ≈ 48.19◦ , was suggested in Materials 2020, 13, 2882 5 of 18 Stark and Fricke’s work. Fibers with an orientation θ < ψ are considered parallel to the direction of heat flow, and fibers with θ > ψ are perpendicular. The final Stark-Fricke model is represented as: −1 j+1 i 1 k = (i + 1) BM + 4k f Cd (2) k j ka + jπact where act is the contact radius, and the i and j given as a function of the fiber orientation, are 1 i= s cos θ − 1 (3) 2 (0.5 sin θ)1/3 j = s2/3 2/3 − 1 (4) π 1.5 1 − µ20 pext /E where s, the geometrical parameter, is !1/2 πρ f /ρ s= (5) 0.5sin2 θ cos θ where C is the connection parameter with a suggested value of 0.611; d is the fiber diameter; act is the contact radius; µ0 is the Poisson’s number of the fibrous material; pext is the external pressure; E is the Young’s modulus; ρ f is the bulk density of fiber; and ρ is the bulk density of fibrous material. 3. Materials and Methods 3.1. Materials The polyester nonwoven fibrous material was made of 45 wt.% staple polyester, 30 wt.% hollow polyester, and 25 wt.% bi-component polyester. Low-melting polyester fiber consists of the sheath part of a bi-component fiber, which is used to thermally bond the nonwoven structure. The preparation procedure of polyester nonwoven samples was reported in our previous work. The longitudinal images of three types of polyester fibers are shown in Figure 3. The longitudinal images were captured at the Technical University of Liberec using the JENAPOL microscope (Jena, Germany) and NIS-elements software (AR 4.30.02 64-bit). Later, fifty fibers were measured for each type of fiber to ensure an accurate value. The mean diameters of the staple, hollow, and bi-component fibers were 13.19 ± 2020, Materials 0.57,13, 24.45 ± PEER x FOR and 17.94 ± 0.82 µm, respectively. 2.56, REVIEW 6 of 19 (a) Staple fiber (b) Hollow fiber (c) Bi-component fiber Figure Figure3.3.Longitudinal Longitudinalimages imagesofoffibers: fibers:(a)(a) staple staplefiber; fiber;(b) (b)hollow hollowfiber; fiber;(c)(c)bi-component bi-componentfiber. fiber. The polyester polyesternonwoven nonwovensamples samplesand andtheir theircross-sectional cross-sectionalmacroscopic macroscopicimages imagesareare illustrated in illustrated Figure 4. It can be seen that the decrease in thickness resulted in an increase in the fiber in Figure 4. It can be seen that the decrease in thickness resulted in an increase in the fiber orientation angle. One tomography orientation angle. Oneimage of sample tomography TK7 isofpresented image sample TK7in Figure 5. The x-ray is presented micro computerized in Figure 5. The x-ray tomography was performed at the Technical University of Liberec, Czech Republic micro computerized tomography was performed at the Technical University of Liberec, Czech on aRepublic Bruker SKYSCAN 1272 (Billerica, MA, USA). Software CTVOX 3.3 was used to reconstruct the tomography image. Fiber orientation TK3 TK2 TK1 TK7 (a) (b) Figure (a) 3. Longitudinal Staple fiber images of fibers: (a) fiber (b) Hollow staple fiber; (b) hollow (c)fiber; (c) bi-component Bi-component fiber fiber. Figure 3. Longitudinal images of fibers: (a) staple fiber; (b) hollow fiber; (c) bi-component fiber. The polyester nonwoven samples and their cross-sectional macroscopic images are illustrated in Figure 4. The It can be seen polyester that the samples nonwoven decreaseandin their thickness resultedmacroscopic cross-sectional in an increase in the images fiber orientation are illustrated in MaterialsOne angle. 13, 2882 2020,tomography image of sample TK7 is presented in Figure 5. The x-ray micro 6 of 18 computerized Figure 4. It can be seen that the decrease in thickness resulted in an increase in the fiber orientation tomography angle. One was performed tomography at the image Technical of sample TK7 isUniversity presented inof Liberec, Figure 5. TheCzech Republic x-ray micro on a Bruker computerized SKYSCAN on a Bruker 1272 tomography (Billerica, SKYSCAN MA, was performed 1272 USA). at the Software (Billerica,Technical CTVOX MA, USA). 3.3ofwas University Software usedCzech Liberec, CTVOX to reconstruct 3.3 wasRepublic the atomography used toonreconstruct Bruker the image.SKYSCAN 1272 (Billerica, MA, USA). Software CTVOX 3.3 was used to reconstruct the tomography tomography image. image. Fiber orientation Fiber orientation TK3 TK2 TK1 TK7 (a) TK3 TK2 TK1 (b) TK7 (a) (b)..…....….. TK2 TK2 TK7 TK7 TK6 TK6 TK5 TK5 TK4 TK4 TK1 TK1 Figure 4. Polyester nonwoven samples (a) and cross-sectional macroscopic images (b). Figure Figure Polyester nonwoven 4. Polyester nonwoven samples samples (a) (a) and and cross-sectional cross-sectional macroscopic images (b). Figure 5. Tomography image of polyester nonwoven sample TK7. The characterization of polyester nonwoven fibrous samples has been reported in our previous Figure 5. Tomography Tomography image image of of polyester polyester nonwoven nonwoven sample sample TK7. TK7. work, as listed in Figure Table 35.. From Figure 5, it can be seen that the fibers were orientated in the same direction and had a similar orientation angle. Thus, it was assumed that the fibers were generally The characterization characterization of of polyester polyester nonwoven nonwoven fibrous fibrous samples samples hashas been been reported reported in in our previous work,Materials as listed 2020,in 13,Table 3. x FOR PEER From From Figure 5, it can REVIEW can be be seen seen that that the the fibers fibers were were orientated orientated in6the of 19same the same direction and direction and had a similar orientation angle. Thus, it was assumed that the fibers were generally Thus, it was assumed that the fibers were generally orientated to the same direction with the same orientation angle. The mean fiber orientation angle Materials 2020, 13, xvia was estimated FOR PEER REVIEW ImageJ software (version 1.51). The mean fiber diameter of the polyester fibers6 of 19 was calculated by the length-weighted average method, as defined in Equation (6). X l d= di P3 i (6) i = 1 li where di is the i-th fiber type diameter obtained from the average value of 50 fibers, and li is the corresponding total fiber length in a unit volume of nonwoven fibrous material: Wi li = (7) π(di /2)2 ρi where Wi is the i-th fiber type total weight in a unit volume of nonwoven fibrous material and ρi is the corresponding fiber density. Materials 2020, 13, 2882 7 of 18 Table 3. Basic characteristics of the polyester nonwoven fibrous samples. Thickness Bulk Density Porosity Mean Fiber Orientation Angle Samples Code (mm) (kg/m3 ) (%) (◦ ) TK1 26.93 18.85 98.350 10.09 TK2 23.08 21.99 98.074 32.46 TK3 21.18 23.96 97.901 39.26 TK4 17.23 29.46 97.420 50.96 TK5 12.7 39.96 96.500 62.36 TK6 11.28 44.99 96.060 65.65 TK7 8.34 60.85 94.671 72.25 3.2. Theoretical Study The thermal conductivity of fibers is a critical parameter in the listed models. It is obliged to figure out the value of polyester fibers to carry out the theoretical study. However, it is complicated and difficult to measure single fiber thermal properties, so referring to values from the literature is a reasonable approach. Baxter estimated the thermal conductivity of polyester fiber in 1946 by measuring the thermal conductivity of pads of packed fibers with the same density. Kawabata developed a specific apparatus to measure the thermal properties of 14 types of fibers in the longitudinal and transverse directions. Militký et. al. proposed the thermal conductivity of a typical polyester fiber with 40% crystallinity. Some values of the thermal conductivity of polyester fibers are listed in Table 4. Table 4. Thermal conductivity of polyester fibers in the literature. kf (W m−1 K−1 ) Reference 0.140 Baxter 0.272 Militký et.al. 0.260 Stark et.al. The procedure for the theoretical study on thermal conductivity is illustrated in Figure 6. The fiber unity was defined as the entire solid phase (fibers) in the nonwoven fibrous material in the current study. Fiber thermal conductivities were used to estimate the values of three fiber constituents in the nonwoven samples. The conductivity of fiber unity was obtained via Botagy’s model for parallel arranged fibrous materials. Then, the thermal conductivity of the nonwoven samples was obtained by using the Materials Schuhmeister, 2020, 13, x FOR PEERBogaty, REVIEWBhattacharyya, and Stark-Fricke models. 8 of 19 1. Schuhmeister’s method 2. Bogaty’s method: Random Staple, hollow and bi-component 3. Bhattacharyya’s method polyester fiber 4. Stark & Fricke’s method Thermal conductivity k of three fiber Predicted k of k of fiber unity (k) of fiber constituents fibrous material Botagy’s method: Parallel Figure 6. Figure 6. Theoretical Theoretical study study procedures procedures according accordingto tofiber fiberthermal thermalconductivity. conductivity. Thermal conductivity of the hollow fiber should be evaluated since there was a 30 wt. % hollow fiber component in the samples. Heat transfer through the hollow fiber in the longitudinal direction is illustrated in Figure 7. The The gas phase and solid phase were parallel arranged when heat transfer occurred in the longitudinal direction. The thermal conductivity under this situation can be simply estimated via model 5, as shown in Equations (8) and (9): 1 2 = 1 + 2 (8) where , , and are volumes of the gas phase (air), the solid phase, and the hollow fiber, respectively. It was assumed that the hollow continued in the hollow fiber. Then, the thermal Botagy’s method: Parallel Figure 6. Theoretical study procedures according to fiber thermal conductivity. Materials 2020, 13, 2882 8 of 18 Thermal conductivity of the hollow fiber should be evaluated since there was a 30 wt. % hollow fiber component in the samples. Heat transfer through the hollow fiber in the longitudinal direction occurred is in the illustrated in longitudinal Figure 7. Thedirection. gas phaseTheandthermal conductivity solid phase underarranged were parallel this situation whencan betransfer heat simply estimated via model 5, as shown in Equations (8) and (9): occurred in the longitudinal direction. The thermal conductivity under this situation can be simply estimated via model 5, as shown in Equations (8)v1and (9): v2 kh− f = k1 + k2 (8) v1 v 2 = t 1+ t 2 (8) where v1 , v2 , and vt are volumes of the gas phase (air), the solid phase, and the hollow fiber, respectively. where , It was assumed , and that theare volumes hollow of theingas continued the phase hollow(air), fiber.the solid Then, thephase, thermal and the hollow of conductivities fiber, the respectively. It was assumed hollow fiber can be represented as: that the hollow continued in the hollow fiber. Then, the thermal conductivities of the hollow fiber can be represented as: 2 2 ! r r kh− f = 11 2 k1 + 1 − 1 1 k22 (9) = rt 1 + 1 − rt 2 (9) where r1 and where andrt are arethetheradius radiusofofthe thegas gasphase phase (air) (air) and and the hollow fiber, the hollow fiber, respectively; and r2 is respectively;and the is the thickness of the solid-phase wall in hollow fiber. The ratio thickness of the solid-phase wall in hollow fiber. The ratio between between r 1 and and rt was calculated based was calculated based on the on the measured measured values values viavia ImageJ ImageJ software software onon the the cross-sectional cross-sectional images images of of the the hollow hollow fiber fiber (see (see in in Figure 7). Figure 7). The The ratio ratio ((r1⁄/rt)) was was 0.433 0.433 with with aa standard standard deviation deviation of of 0.0345 0.0345 byby measuring measuring 5050 fibers. fibers. Hollow r1 r2 Heat Flow rt (a) (b) Figure7.7.Heat Figure Heattransfer transferthrough throughthe thehollow hollowfiber fiberin inthe the longitudinal longitudinal (a) (a) direction, and cross-sectional image of the hollow fiber (b). The thermal The thermal conductivity conductivity of of the the fiber fiber unity unity in in the the nonwoven nonwoven fibrous fibrous materials materials was was estimated estimated from the from the thermal thermal conductivities of the conductivities of the three three fiber fiber constituents constituents by by using using aa series series arrangement arrangement model model based on fiber volume fractions of each constituent when the solid and gas phases were in a parallel arrangement. Then, the thermal conductivity of the fiber unity can be obtained as: Materials 2020, 13, x FOR PEER REVIEW 8 of 19 k = vs− f ks− f + vh− f kh− f + vb− f kb− f (10) where vs− f , vh− f , and vb− f are the volume fractions of staple, hollow, and bi-component polyester fiber, respectively, and ks− f , kh− f , and kb− f are the thermal conductivities of staple, hollow, and bi-component polyester fibers, respectively. The thermal conductivity of the bi-component polyester fiber was assumed to be the same as the staple polyester fiber. In another situation where the two phases are perpendicularly arranged, the thermal conductivity of the fiber unity can be estimated by: !−1 vs− f vh− f vb− f k= + + (11) ks− f kh− f kb− f Materials 2020, 13, 2882 9 of 18 The thermal conductivities of the three fiber constituents and fiber unity are listed in Table 5. Some of the models require the fractions of fibers that are parallel or perpendicular to the heat flow direction. The values of fractions can be easily calculated via the trigonometric function (see Equations (12) and (13). The volume fractions of air and fiber and the fractions of fiber orientation are listed in Table 6. Next, the final results of nonwoven samples are calculated via the methods demonstrated in Figure 6. 1 x= (12) tan θ + 1 tan θ y= (13) tan θ + 1 Table 5. Thermal conductivities of three fiber constituents and fiber unity. Referred Values Staple and Hollow Fiber Fiber Unity Bogaty Models [23,26] Bi-Component Fibers (W m−1 K−1 ) (W m−1 K−1 ) (W m−1 K−1 ) (W m−1 K−1 ) 0.140 0.140 0.1187 0.1324 Parallel 0.272 0.272 0.2261 0.2556 Parallel Table 6. Volume fractions of air and fiber, and the fractions of fiber orientation to the heat flow. TK1 TK2 TK3 TK4 TK5 TK6 TK7 va 0.9835 0.9807 0.9790 0.9742 0.9650 0.9606 0.9467 vf 0.0165 0.0193 0.0210 0.0258 0.0350 0.0394 0.0533 x 0.8489 0.6112 0.5503 0.4478 0.3439 0.3116 0.2425 y 0.1511 0.3888 0.4497 0.5522 0.6561 0.6884 0.7575 3.3. Experimental Study Two different measurement methods were utilized to test the thermal conductivities of nonwoven fibrous samples. First, the samples were tested on an Alambeta device (SENSORA, Liberec, Czech Republic) at the Technical University of Liberec, Czech Republic. The measuring head of the Alambeta contains a copper block that is electrically heated to approximately 32 ◦ C to simulate the temperature of human skin. The lower part of the heated block is equipped with a direct heat flow sensor that measures the thermal drop between the surfaces of a very thin, non-metallic plate using a multiple differential micro-thermocouple [36,37]. Furthermore, a new custom-built apparatus was used to measure the thermal conductivities at the Kyoto Institute of Technology. The theory and procedure of thermal conductivity determination were adopted from the previous study (see ). As illustrated in Figure 8, the apparatus was composed of a hot plate (JUJI Field Inc. LABOPAD H, Tokyo, Japan), wind tunnel, a blower (SANYO DENKI Co. Ltd., 9SG 5724P5H61, Tokyo, Japan), a hot-wire anemometer (HARIO SCIENCE Co. Ltd., WGT-10, Tokyo, Japan), and a digital radiation temperature sensor (KEYENCE Corp. FT-H10, Osaka, Japan). Constant airflow was supplied to the wind tunnel by a blower, a specimen was placed on the heating portion of the hot plate, and the surface temperature of the specimen was measured by detecting the quantity of the infrared ray by using a digital radiation temperature sensor. Moreover, the temperature of the hot plate was set at 30, 50, and 70 ◦ C, and the emissivity set for using the digital radiation sensor was unified to 1.0. SCIENCE Co. Ltd., WGT-10, Tokyo, Japan), and a digital radiation temperature sensor (KEYENCE Corp. FT-H10, Osaka, Japan). Constant airflow was supplied to the wind tunnel by a blower, a specimen was placed on the heating portion of the hot plate, and the surface temperature of the specimen was measured by detecting the quantity of the infrared ray by using a digital radiation temperature Materials sensor. 2020, 13, 2882 Moreover, the temperature of the hot plate was set at 30, 50, and 70 °C, and 10 ofthe 18 emissivity set for using the digital radiation sensor was unified to 1.0. Anemometer Digital radiation temperature sensor Ventilator Wind tunnel Acrylic plate Flow straightening boards Hot plate Color cardboard PWMController Figure8.8.Sketch Figure Sketchofofthe thecustom-built custom-builtapparatus. apparatus. 4. 4. Results Results and and Discussion Discussion In this this section, section, the the predicted predicted thermal thermal conductivities conductivities of nonwoven nonwoven fibrous materials materials were first first compared and analyzed. Then, the comparison between between two two different test methods was carried out. The The validation validationofofthe themodels modelsbased basedonon the measured the values measured willwill values be studied at the be studied end,end, at the followed by one followed by modified model. one modified model. 4.1. 4.1. Predictions Predictions of of Thermal Thermal Conductivity Conductivity of of Nonwoven Nonwoven Samples Samples All All of of the the modeling modelingcomputations computationswerewereprocessed processedininMATLAB_R2018b MATLAB_R2018b and thethe and results areare results listed in listed Table 7. According to the four different values of fiber thermal conductivities, the values in Table 7. According to the four different values of fiber thermal conductivities, the values of of nonwoven samples nonwoven were listed in samples twolisted were groups. It cangroups. in two be seenItthat canall beofseen the that predicted all of conductivities the predicted were less than conductivities 0.2 W m −1 K−1. were less than 0.2 W m−1 K−1. Table 7. Predicted thermal conductivities of nonwoven samples based on different k f. Table 7. Predicted thermal conductivities of nonwoven samples based on different. Referred kf Predicted Thermal Conductivity of Nonwovens (W m−1 K−1 ) Referred −1 ) Models Predicted Thermal Conductivity of Nonwovens (W m−1 K−1) (W m−1−1 K Models TK1 TK2 TK3 TK4 TK5 TK6 TK7 (W m K−1) TK1 TK2 TK3 TK4 TK5 TK6 TK7 Schuhmeister Schuhmeister 0.0272 0.0274 0.0274 0.0277 0.0281 0.0272 0.0274 0.0274 0.0277 0.0281 0.0284 0.0291 0.0284 0.0291 Bogaty 0.0279 0.0278 0.0278 0.0279 0.0282 0.0283 0.0287 k f :0.140 Bogaty Bhattacharyya 0.0279 0.0280 0.0278 0.0278 0.0282 0.0278 0.0286 0.0279 0.0294 0.0282 0.0283 0.0298 0.0287 0.0310 :0.140 Bhattacharyya Stark & Fricke BM 0.0278 0.0671 0.0676 0.0280 0.0667 0.0282 0.1059 0.0286 0.0992 0.0294 0.0298 0.0964 0.0310 0.0889 Stark Stark & Fricke & Fricke BM 0.0658 0.0676 0.0610 0.0671 0.0592 0.0667 0.0769 0.1059 0.0646 0.0604 0.0992 0.0964 0.0507 0.0889 Stark & Fricke Schuhmeister 0.0658 0.0282 0.0279 0.0610 0.0283 0.0592 0.0288 0.0769 0.0296 0.0646 0.0604 0.0301 0.0507 0.0314 Bogaty Schuhmeister 0.0334 0.0279 0.0390 0.0282 0.0405 0.0283 0.0432 0.0288 0.0462 0.0473 0.0296 0.0301 0.0497 0.0314 k f :0.272 Bhattacharyya 0.0285 Bogaty 0.0334 0.0390 0.0405 0.0432 0.0462 0.0473 0.0334 0.0289 0.0291 0.0297 0.0309 0.0315 0.0497 Stark & Fricke BM 0.0906 0.0898 0.0893 0.1727 0.1561 0.1495 0.1331 :0.272 Bhattacharyya Stark & Fricke 0.0285 0.0777 0.0868 0.0289 0.0745 0.0291 0.1019 0.0297 0.0799 0.0309 0.0315 0.0730 0.0334 0.0583 Stark & Fricke BM 0.0906 0.0898 0.0893 0.1727 0.1561 0.1495 0.1331 Stark & Fricke 0.0868 0.0777 0.0745 0.1019 0.0799 0.0730 0.0583 The predicted thermal conductivities are shown in Figure 9. It is obvious that the results from StarkTheandpredicted thermal much Fricke exhibited conductivities are shown higher thermal in Figure 9. when conductivities It is obvious comparedthattotheother results from models. Stark and Fricke Meanwhile, resultsexhibited based onmuch higher thermal the Stark-Fricke modelconductivities whenwhich had a clear trend, compared to other first slightly models. decreased, then reached the highest value, followed by a decrease. Results among the seven nonwoven samples Materials 2020, 13, x FOR PEER REVIEW 10 of 19 based on the Schuhmeister and Bhattacharyya models had very small differences. When the fiber thermal conductivity was higher (i.e., 0.272 W m−1 K−1 ), the results based on the Bogaty model exhibited a clear increase. Generally, the increase in fiber thermal conductivity resulted in an increase in the thermal conductivity of the fibrous material. This can be confirmed in Figure 9. However, the increases in some predicted values (i.e., Schuhmeister and Bhattacharyya models) of nonwoven samples were relatively small, although the fiber thermal conductivity was nearly doubled. The reason behind then reached the highest value, followed by a decrease. Results among the seven nonwoven samples based on the Schuhmeister and Bhattacharyya models had very small differences. When the fiber thermal conductivity was higher (i.e., 0.272 W m−1 K−1), the results based on the Bogaty model exhibited a clear increase. Generally, the increase in fiber thermal conductivity resulted in an increase in the thermal Materials conductivity of the fibrous material. This can be confirmed in Figure 9. However, 2020, 13, 2882 11 of the 18 increases in some predicted values (i.e., Schuhmeister and Bhattacharyya models) of nonwoven samples were relatively small, although the fiber thermal conductivity was nearly doubled. The this phenomenon reason behind this can be the low fiber phenomenon can bevolume fraction the low (i.e.,