Materials Management PDF
Document Details
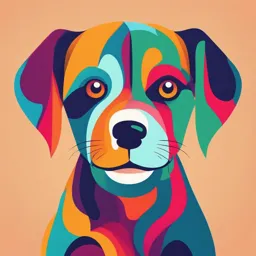
Uploaded by GlimmeringJade1431
Tags
Summary
This document covers materials management, focusing on the processes of planning, sourcing, purchasing, moving, storing, and controlling materials to provide service to the customer at a minimum cost. It includes information on material planning techniques, purchasing objectives and procedures, store management functions, inventory control, and standardization.
Full Transcript
MATERIALS MANAGEMENT SLIDESMANIA.COM Materials management -is a function, which aims for integrated approach towards the management of materials in an industrial undertaking. Its main objective is cost...
MATERIALS MANAGEMENT SLIDESMANIA.COM Materials management -is a function, which aims for integrated approach towards the management of materials in an industrial undertaking. Its main objective is cost reduction and efficient handling of materials at all stages and in all sections of the undertaking. Its function includes several important aspects connected with material, such as, purchasing, storage, inventory control, material handling, standardization etc. -is defined as “the function responsible for the coordination of planning, sourcing, purchasing, moving, storing and controlling materials in an optimum manner so as to provide a pre- SLIDESMANIA.COM decided service to the customer at a minimum cost”. SLIDESMANIA.COM Material planning -is a scientific technique of determining in advance the requirements of raw materials, ancillary parts and components, spares etc. as directed by the production programme. Two factors: 1. Macro factors: Some of the macro factors which affect material planning, are price trends, business cycles Govt. import policy etc. 2. Micro factors: Some of the micro factors that affect material planning are plant capacity utilization, rejection rates, lead times, inventory levels, working capital, delegation of powers and SLIDESMANIA.COM communication. Techniques of Material Planning SLIDESMANIA.COM Purchasing - is an important function of materials management. In any industry purchase means buying of equipments, materials, tools, parts etc. required for industry. - In small industry, this function is performed by works manager and in large manufacturing concern; this function is done by a separate department. Objectives of Purchasing - The basic objective of the purchasing function is to ensure continuity of supply of raw materials, sub-contracted items and SLIDESMANIA.COM spare parts and to reduce the ultimate cost of the finished goods. The objectives of the purchasing department can be outlined as under: 1. To avail the materials, suppliers and equipments at the minimum possible costs 2. To ensure the continuous flow of production 3. To increase the asset turnover 4. To develop an alternative source of supply 5. To establish and maintain the good relations with the suppliers 6. To achieve maximum integration with other department of the company 7. To train and develop the personnel SLIDESMANIA.COM 8. Efficient record keeping and management reporting Parameters of Purchasing - The success of any manufacturing activity is largely dependent on the procurement of raw materials of right quality, in the right quantities, from right source, at the right time and at right price popularly known as ten ‘R’s’ of the art of efficient purchasing. 1. Right Price- It is the primary concern of any manufacturing organization to get an item at the right price. But right price need not be the lowest price. 2. Right Quality- Right quality implies that quality should be available, measurable and understandable as far as SLIDESMANIA.COM practicable. 3. Right Time- For determining the right time, the purchase manager should have lead time information for all products and analyse its components for reducing the same. 4. Right Source- The source from which the material is procured should be dependable and capable of supplying items of uniform quality. 5. Right Quantity - The right quantity is the most important parameter in buying. 6. Right Attitude- Developing the right attitude, too, is necessary as one often comes across such statement: ‘Purchasing knows the price of everything and value of nothing’; ‘We buy price and not cost’; SLIDESMANIA.COM ‘When will our order placers become purchase managers?’; ‘Purchasing acts like a post box’. 7. Right Contracts- The buyer has to adopt separate policies and procedures for capital and consumer items. 8. Right Material - Right type of material required for the production is an important parameter in purchasing. 9. Right Transportation- Right mode of transportation have to be identified as this forms a critical segment in the cost profile of an item. 10. Right Place of Delivery- Specifying the right place of delivery, like head office or works, would often minimize the handling and transportation cost. Purchasing Procedure - The procedure describes the sequence of steps leading to the completion of an identified specific task SLIDESMANIA.COM 1. Recognition of the Need- The initiation of procedure starts with the recognition of the need by the needy section. 2. The Selection of Supplier- The process of selection of supplier involves two basic aspects: searching for all possible sources and short listing out of the identified sources. 3. Placing the Order-. Purchase order is a letter sent to the supplier asking to supply the said material. 4. Follow-up the Order- the follow-up procedure tries to see that the purchase order is confirmed by the supplier and the delivery is promised. 5. Receiving and Inspection of the Materials- The receiving department receives the materials supplied by the vendor. 6. Payment of the Invoice- When the goods are received in satisfactory condition, the invoice is checked before it is approved SLIDESMANIA.COM for the payment. 7. Maintenance of the Records- Maintenance of the records is an important part and parcel of the efficient purchase function. 8. Maintenance of the Vendors Relation - The quantum and frequency of the transactions with the same key suppliers provide a platform for the purchase department to establish and maintain good relations with them. SLIDESMANIA.COM SLIDESMANIA.COM Selection of Suppliers - Selection of the right supplier is the responsibility of the purchase department. It can contribute substantially to the fundamental objectives of the business enterprise. A. SOURCES OF SUPPLIER - The best buying is possible only when the decision maker is familiar with all possible sources of supply and their respective terms and conditions. 1. Specialized trade directories. 2. Assistance of professional bodies or consultants. SLIDESMANIA.COM 3. The buyer’s guide or purchase handbook. 4. The manufacturer’s or distributor’s catalogue. 5. Advertisements in dailies. 6. Advertisement in specialised trade journals. 7. Trade fair exhibitions. B. DEVELOPMENT OF APPROVED LIST OF SUPPLIERS The survey stage highlights the existence of the source. A business inquiry is made with the appropriate supplier. It is known as ‘Inquiry Stage’. SLIDESMANIA.COM Short listing is made out of the given sources of suppliers in terms of: production facilities and capacity, financial standing product quality possibility of timely supply technical competence manufacturing efficiency general business policies followed standing in the industry competitive attitude SLIDESMANIA.COM interest in buying orders C. EVALUATION AND SELECTION OF THE SUPPLIER - In the ‘purchasing handbook’ edited by Aljian, it has been described that the following variables to be considered while evaluating the quotations of the suppliers: 1. Cost Factors Price, transportation cost, installation cost if any, tooling and other operations cost, incidence of sales tax and excise duty, terms of payment and cash discount are considered in cost factor. 2. Delivery Routing and F.O.B. terms are important in determining the point at which the title to the goods passes from vendor to the buyer and SLIDESMANIA.COM the responsibility for the payment of the payment charges. 3. Design and Specification Factors Specification compliance, specification deviations, specification advantages, important dimensions and weights are considered in line with the demonstration of sample, experience of other users, after sale services etc. 4. Legal Factors Legal factors include warranty, cancellation provision, patent protection, public liability, federal laws and reputation compliance. 5. Vendor Rating The evaluation of supplier or vendor rating provides valuable information which help in improving the quality of the decision. In the SLIDESMANIA.COM vendor rating three basic aspects are considered namely quality, service and price. Special Purchasing Systems The following are some of the important purchasing systems: 1. Forward Buying- Forward buying or committing an organization far into the future, usually for a year. Depending upon the availability of the item, the financial policies, the economic order quantity, the quantitative discounts, and the staggered delivery, the future commitment is decided. 2. Tender Buying- In public, all semblance of favouritism, personal preferences should be avoided. As such, it is common for government departments and public sector undertakings to purchase through tenders. 3. Blanket Order System- This system minimizes the administrative expenses and is useful for ‘C’ type items. It is an agreement to provide a required quantity of specified items, over a period of time, usually for one year, at an agreed price. Deliveries are made depending upon the buyer’s needs. SLIDESMANIA.COM 4. Zero Stock- Some firms try to operate on the basis of zero stock and the supplier holds the stock for these firms. Usually, the firms of the buyer and seller are close to each other so that the raw material of one is the finished products of another. 5. Rate Contract- The system of rate contract is prevalent in public sector organizations and government departments. It is common for the suppliers to advertise that they are on ‘rate contract’ for the specific period. 6. Reciprocity- Reciprocal buying means purchasing from one’s customers in preference to others. It is based on the principle “if you kill my cat, I will kill your dog”, and “Do unto your customers as you would have them do unto you”. 7. Systems Contract- This is a procedure intended to help the buyer and the sellers to reduce administrative expenses and at the same time ensure suitable controls. SLIDESMANIA.COM STORES MANAGEMENT - The most important purpose served by the stores is to provide uninterrupted service to the manufacturing divisions. FUNCTIONS OF STORES The functions of stores can be classified as follows: 1. To receive raw materials, components, tools, equipment’s and other items and account for them. 2. To provide adequate and proper storage and preservation to the various items. SLIDESMANIA.COM FUNCTIONS OF STORES 3. To meet the demands of the consuming departments by proper issues and account for the consumption. 4. To minimize obsolescence, surplus and scrap through proper codification, preservation and handling. 5. To highlight stock accumulation, discrepancies and abnormal consumption and effect control measures. 6. To ensure good housekeeping so that material handling, material preservation, stocking, receipt and issue can be done adequately. 7. To assist in verification and provide supporting information for effective purchase action. SLIDESMANIA.COM Codification -It is one of the functions of stores management. Codification is a process of representing each item by aa number, the digit of which indicates the group, the sub-group, the type and the dimension of the item. -Codification should be compact, concise, consistent and flexible enough to accommodate new items. SLIDESMANIA.COM Objectives of Codification The objectives of a rationalized material coding system are: 1. Bringing all items together. 2. To enable putting up of any future item in its proper place. 3. To classify an item according to its characteristics. 4. To give an unique code number to each item to avoid duplication and ambiguity. 5. To reveal excessive variety and promote standardization and variety reduction. 6. To establish a common language for the identification of an item. 7. To fix essential parameters for specifying an item. 8. To specify item as per national and international standards. SLIDESMANIA.COM 9. To enable data processing and analysis. Advantages of Codification -Many firms have reduced the number of items. -It enables systematic grouping of similar items. -Avoids confusion caused by long description of items. -It’s serves as the starting point of simplification and standardization. -It helps in avoiding duplication of items. -Codification enables easy recognition of an item in stores. SLIDESMANIA.COM INVENTORY CONTROL OR MANAGEMENT ∙ refers to the materials in stock ∙ is also called the idle resource of an enterprise ∙ represent those items which are either stocked for sale REASONS FOR KEEPING INVENTORIES 1. To stabilize production 2. To take advantage of price discounts 3. To meet the demand during the replenishment period: 4. To prevent loss of orders (sales) SLIDESMANIA.COM 5. To keep pace with changing market conditions INVENTORY CONTROL ∙ A planned approach of determining what to order, when to order and how much to order and how much to stock so that costs associated with buying and storing are optimal without interrupting production and sales ∙ Deals with two problems: When should an order be placed? (Order level), and (ii) How much should be ordered? (Order quantity). OBJECTIVES OF INVENTORY CONTROL 1. To ensure adequate supply of products to customer and avoid shortages as far as possible. 2. To make sure that the financial investment in inventories is minimum SLIDESMANIA.COM (i.e., to see that the working capital is blocked to the minimum possible extent). OBJECTIVES OF INVENTORY CONTROL 3. Efficient purchasing, storing, consumption and accounting for materials is an important objective. 4. To maintain timely record of inventories of all the items and to maintain the stock within the desired limits. 5. To ensure timely action for replenishment. 6. To provide a reserve stock for variations in lead times of delivery of materials. 7. To provide a scientific base for both short-term and long-term planning of materials SLIDESMANIA.COM STANDARDIZATION ∙ producing maximum variety of products from the minimum variety of materials, parts, tools and processes ∙ process of establishing standards or units of measure by which extent, quality, quantity, value, performance etc., may be compared and measured SLIDESMANIA.COM ADVANTAGES OF STANDARDIZATION BENEFITS TO DESIGN DEPARTMENT 1. Fewer specifications, drawings and part list have to prepared and issued. 2. More time is available to develop new design or to improve established design. 3. Better resource allocation. 4. Less qualified personnel can handle routine design work. SLIDESMANIA.COM BENEFITS TO DESIGN DEPARTMENT 5. Increased interchangeability of parts. 6. Better utilization of manpower and equipment. 7. Accurate delivery dates. 8. Better services of production control, stock control, purchasing, etc. 9. More effective training. BENEFITS TO MARKETING DEPARTMENT 1. Better quality products of proven design at reasonable cost leads to greater sales volume. 2. Increased margin of profit. 3. Better product delivery. SLIDESMANIA.COM BENEFITS TO PRODUCTION PLANNING DEPARTMENT 1. Scope for improved methods, processes and layouts. 2. Opportunities for more efficient tool design. 3. Better resource allocation. 4. Reduction in pre-production activities. BENEFITS TO PRODUCTION CONTROL DEPARTMENT 1. Well proven design and methods improve planning and control. 2. Accurate delivery promises. 3. Fewer delays arise from waiting for materials, tools, etc. 4. Follow-up of small batches consumes less time. SLIDESMANIA.COM BENEFITS IN PURCHASE AND STOCK CONTROL DEPARTMENT 1. Holding of stock of standard items leads to less paper work and fewer requisitions and orders. 2. Storage and part location can be improved. 3. Newer techniques can be used for better control of stocks. 4. Because of large purchase quantities involved, favourable purchase contracts can be made. BENEFITS TO QUALITY CONTROL 1. Better inspection and quality control is possible. 2. Quality standards can be defined more clearly. SLIDESMANIA.COM 3. Operators become familiar with the work and produce jobs of consistent quality. ERGONOMICS (HUMAN ENGINEERING) ⮚ The word ‘Ergonomics’ has its origin in two Greek words Ergon meaning laws or “ study of the man in relation to his work”. ⮚ In USA and other countries it is called by the name ‘human engineering or human factors engineering”. ⮚ ILO defines human engineering as, “The application of human biological sciences along with engineering sciences to achieve optimum mutual adjustment of men and his work, the benefits being measured in terms of human efficiency and well-being.” SLIDESMANIA.COM Objectives of Human Engineering Human engineering (ergonomics) has two broader objectives: 1. To enhance the efficiency and effectiveness with which the activities (work) is carried out so as to increase the convenience of use, reduced errors and increase in productivity. 2. To enhance certain desirable human values including safety reduced stress and fatigue and improved quality of SLIDESMANIA.COM life. Just-In-Time (JIT) Manufacturing - is a philosophy rather than a technique. By eliminating all waste and seeking continuous improvement, it aims at creating manufacturing system that is response to the market needs. - is used to because this system operates with low WIP (Work-In- Process) inventory and often with very low finished goods inventory. SLIDESMANIA.COM Benefits of JIT The most significant benefit is to improve the responsiveness of the firm to the changes in the market place thus providing an advantage in competition. 1. Product cost—is greatly reduced due to reduction of manufacturing cycle time, reduction of waste and inventories and elimination of non-value added operation. 2. Quality—is improved because of continuous quality improvement programmes. 3. Design—Due to fast response to engineering change, alternative designs can be quickly brought on the shop floor. 4. Productivity improvement. 5. Higher production system flexibility. SLIDESMANIA.COM 6. Administrative and ease and simplicity. THANK YOU SLIDESMANIA.COM