ETOS® MD-IV Motor-drive Unit Manual PDF
Document Details
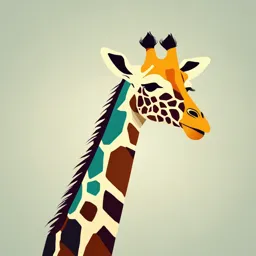
Uploaded by BestSellingBeige
null
Tags
Summary
This document provides operating instructions for the ETOS® MD-IV motor-drive unit. It covers topics such as safety, mounting, connections, commissioning, and operation. The manual is intended for professionals.
Full Transcript
THE POWER BEHIND POWER. Operating instructions ETOS® MD-IV. Motor-drive unit 10771253/01 EN © All rights reserved by Maschinenfabrik Reinhausen Dissemination and reproduction of this document and use and disclosure of its content are strictly prohibited unless expressly permitted. Infringements w...
THE POWER BEHIND POWER. Operating instructions ETOS® MD-IV. Motor-drive unit 10771253/01 EN © All rights reserved by Maschinenfabrik Reinhausen Dissemination and reproduction of this document and use and disclosure of its content are strictly prohibited unless expressly permitted. Infringements will result in liability for compensation. All rights reserved in the event of the granting of patents, utility models or designs. The product may have been altered since this document was published. We reserve the right to change the technical data, design and scope of supply. Generally the information provided and agreements made when processing the individual quotations and orders are binding. The product is delivered in accordance with MR's technical specifications, which are based on information provided by the customer. The customer has a duty of care to ensure the compatibility of the specified product with the customer's planned scope of application. The original operating instructions were written in German. Table of contents 1 Introduction................................................. 6 1.1 Manufacturer................................................................. 6 6 Mounting................................................... 49 1.2 Completeness............................................................... 6 6.1 Preparatory work........................................................ 49 1.3 Safekeeping................................................................... 6 6.1.1 Checking the neutral position of the on- 1.4 Notation conventions.................................................. 6 load tap-changer........................................... 50 1.4.1 Hazard communication system....................... 6 6.1.2 Checking the neutral position of the 1.4.2 Information system............................................ 7 motor-drive unit............................................. 51 1.4.3 Instruction system.............................................. 7 6.2 Mounting the gear motor.......................................... 52 1.4.4 Typographic conventions................................ 8 6.3 Fitting the control cabinet to the transformer........ 55 1.5 Notes on the VACUTAP® RMV-II operating 6.4 Connecting the gear motor...................................... 58 instructions................................................................ 9 6.5 Connecting the monitoring system (VIM)............... 59 1.6 Open source software.................................................. 9 6.6 Connecting the control cabinet................................ 60 6.6.1 Cable recommendation.................................. 60 2 Safety.......................................................... 10 6.6.2 Electromagnetic compatibility........................ 61 2.1 Appropriate use........................................................... 10 6.6.3 Notes on connecting to the MR sensor 2.1.1 Motor-drive unit................................................ 10 bus.................................................................. 63 2.1.2 On-load tap-changer regulation...................... 11 6.6.4 Information on connecting to the CAN 2.2 Inappropriate use........................................................ 12 bus.................................................................. 69 2.2.1 Internal power supply....................................... 12 6.6.5 Information about connecting analog 2.3 Fundamental safety instructions............................... 13 sensors........................................................... 70 2.4 Personnel qualification............................................... 15 6.6.6 Information on connecting the socket 2.5 Personal protective equipment................................. 16 circuit.............................................................. 73 6.6.7 Information on connecting the power 3 IT security................................................... 17 supply............................................................. 73 3.1 General......................................................................... 17 6.6.8 Notes on tap position indication via 3.2 Commissioning............................................................ 17 resistor contact series (optional)................. 74 3.3 Operation..................................................................... 17 6.7 Checking functional reliability................................... 76 3.4 Interfaces..................................................................... 18 3.5 Encryption standards.................................................. 18 7 Commissioning........................................... 77 7.1 Commissioning the ISM®........................................... 77 4 Product description................................... 20 7.1.1 Establishing connection to visualization........ 77 4.1 Scope of delivery........................................................ 20 7.1.2 Setting the language....................................... 78 4.2 Function description.................................................. 20 7.1.3 Commissioning wizard.................................... 78 4.3 Performance features................................................ 20 7.1.4 Downloading the operating instructions...... 79 4.4 Operating modes........................................................ 21 7.1.5 Configuring analog inputs and outputs 4.5 Design......................................................................... 22 (optional)........................................................ 79 4.5.1 Name plate...................................................... 23 7.1.6 Checking measured values and status of 4.5.2 Gear motor...................................................... 23 digital inputs and outputs............................ 82 4.5.3 Control cabinet................................................ 25 7.2 Performing tests......................................................... 83 4.6 Visualization............................................................... 38 7.2.1 Function test of the motor-drive unit............ 83 4.6.1 Main screen...................................................... 38 7.2.2 Testing monitoring system............................ 84 4.6.2 Drive overview................................................ 40 7.2.3 High-voltage tests on the transformer.......... 85 4.6.3 Operating concept.......................................... 40 7.3 Transporting transformer to the operating site...... 87 7.4 Commissioning the transformer at the 5 Packaging, transport and storage.............. 43 operating site........................................................... 87 5.1 Packaging.................................................................... 43 5.1.1 Suitability.......................................................... 43 8 Operation.................................................. 88 5.1.2 Markings........................................................... 44 8.1 System......................................................................... 88 5.2 Transportation, receipt and handling of 8.1.1 Establishing connection to visualization....... 88 shipments................................................................ 45 8.1.2 General............................................................. 89 5.3 Storage of shipments................................................. 46 8.1.3 Configuring the network.................................. 91 5.4 Unpacking shipments and checking for 8.1.4 Web visualization............................................ 93 transportation damages......................................... 46 8.1.5 Configuring serial interfaces........................... 93 8.1.6 Assigning serial interfaces.............................. 94 8.1.7 Setting the device time................................... 94 10771253/01 EN Table of contents 3 8.1.8 Configuring syslog.......................................... 96 8.5.7 Monitoring the gas volume of the 8.1.9 SCADA.............................................................. 98 Buchholz relay (OLTC)................................. 212 8.1.10 Displaying the status of the 8.5.8 Monitoring the oil pressure (on-load tap- communication services............................. 111 changer)........................................................ 212 8.1.11 Name plate.................................................... 112 8.5.9 Displaying the minimum and maximum 8.1.12 Measured value recorder............................. 113 tap position................................................... 213 8.1.13 Displaying measured value recorder 8.5.10 Messages...................................................... 213 (optional)....................................................... 113 8.5.11 Tap position message as gray code............ 213 8.1.14 Linking signals and events........................... 115 8.5.12 Tap position message as BCD code........... 216 8.1.15 MR sensor bus............................................... 119 8.5.13 Tap position message as dual code............ 218 8.1.16 Configuring analog inputs and outputs 8.5.14 Tap position message as decimal (optional)....................................................... 127 coding........................................................... 221 8.1.17 Configuring digital inputs and outputs...... 130 8.5.15 Information about the on-load tap- 8.1.18 Event management...................................... 131 changer........................................................ 224 8.1.19 User administration..................................... 134 8.6 Motor-drive unit and control cabinet..................... 225 8.1.20 Brute-force protection................................. 138 8.6.1 Actuating motor-drive unit locally............... 225 8.1.21 Hardware....................................................... 138 8.6.2 Operating the motor-drive unit with the 8.1.22 Software....................................................... 140 hand crank................................................... 225 8.1.23 Import/export manager.............................. 140 8.6.3 Selecting the operating mode..................... 227 8.1.24 Linking to the visualization of external 8.6.4 Monitoring motor-drive unit........................ 228 devices......................................................... 145 8.6.5 Drive overview............................................... 228 8.1.25 Resetting the device to factory settings... 147 8.6.6 Synchronizing the motor-drive unit............ 229 8.2 Power grid................................................................. 148 8.6.7 Control cabinet monitoring.......................... 230 8.2.1 Transformer data........................................... 148 8.6.8 Control of the motor-drive unit................... 232 8.2.2 Measurement................................................. 161 8.6.9 Motor-drive-unit monitoring........................ 234 8.2.3 Voltage monitoring........................................ 162 8.7 Protective devices.................................................... 235 8.2.4 Current monitoring........................................ 165 8.7.1 Displaying the measured values of the 8.2.5 Power monitoring.......................................... 167 Buchholz relay (optional)............................ 235 8.2.6 Power flow monitoring................................. 168 8.7.2 Displaying the measured values of the 8.2.7 Phase symmetry monitoring........................ 170 pressure relief device (optional)................ 235 8.2.8 Monitoring settings....................................... 170 8.7.3 Displaying protective device status............. 236 8.2.9 TAPCON® 2xx retrofit.................................... 171 8.8 Insulating fluids........................................................ 237 8.2.10 Displaying current measured values.......... 172 8.8.1 Displaying the measured value trend of 8.2.11 Displaying minimum and maximum the oil level and dehydrating breather measured values.......................................... 173 (optional)...................................................... 237 8.3 On-load tap-changer regulator............................... 174 8.3.1 Regulation...................................................... 174 9 Fault elimination...................................... 238 8.3.2 Voltage regulation (optional)........................ 175 9.1 Motor-drive unit........................................................ 238 8.3.3 Displaying control parameters...................... 187 9.2 Human-machine interface...................................... 239 8.3.4 Line drop compensation............................... 187 9.3 Other faults............................................................... 240 8.3.5 Parallel operation (optional)......................... 190 8.3.6 U bandwidth monitoring.............................. 199 10 Inspection and maintenance................... 241 8.3.7 Target-tap-position operation..................... 201 10.1 Cleaning motor-drive unit...................................... 241 8.4 Active part................................................................ 202 10.2 Maintaining motor-drive unit................................ 241 8.4.1 Asset intelligence.......................................... 202 10.3 Heating maintenance............................................. 242 8.4.2 Monitoring the gas volume of the Buchholz relay (transformer)..................... 203 11 Disassembly........................................... 243 8.4.3 Monitoring the oil pressure (transformer).. 203 8.4.4 Displaying transformer statistics................ 204 12 Disposal.................................................. 245 8.5 On-load tap-changer................................................ 205 12.1 SVHC information in accordance with the 8.5.1 Tap position monitoring............................... 205 REACH regulation................................................. 245 8.5.2 Switching interval monitoring...................... 206 8.5.3 Changing tap position designation............. 207 13 Technical data........................................ 246 8.5.4 Setting the tap position message 13.1 Control cabinet........................................................ 246 (optional)...................................................... 208 13.1.1 Dimensions and weight............................... 246 8.5.5 Displaying tap-change operation 13.1.2 Permissible ambient conditions................. 246 statistics....................................................... 209 13.1.3 Electrical data............................................... 246 8.5.6 OLTC data...................................................... 209 13.2 Motor-drive unit...................................................... 248 4 Table of contents 10771253/01 EN 13.3 ISM® assemblies...................................................... 249 13.3.1 Power supply PS.......................................... 249 13.3.2 CPU (central processing unit).................... 250 13.3.3 Voltage measurement U 3.......................... 252 13.3.4 Current measurement I 3........................... 253 13.3.5 Digital outputs DO 8................................... 254 13.3.6 Digital inputs DI 16-110 V............................ 256 13.3.7 Digital inputs DI 16-220 V........................... 258 13.3.8 Digital inputs DI 16-24 V............................. 259 13.3.9 Digital inputs DI 16-48 V............................. 260 13.3.10 Analog outputs AO 4................................ 262 13.3.11 Analog inputs AI 4...................................... 263 13.3.12 Analog inputs AI 4-T.................................. 264 13.3.13 System networking BES............................ 266 13.3.14 System networking COM-ETH................. 267 13.3.15 CAN gateway............................................. 267 13.3.16 IDS VLX vibroacoustic input module....... 268 13.4 Standards and directives....................................... 269 14 Drawings................................................ 270 14.1 Maßzeichnung......................................................... 271 Glossary...................................................... 272 List of key words......................................... 273 10771253/01 EN Table of contents 5 1 Introduction This technical file contains detailed descriptions on the safe and proper installa- tion, connection, commissioning and monitoring of the product. It also includes safety instructions and general information about the product. This technical file is intended solely for specially trained and authorized person- nel. 1.1 Manufacturer Reinhausen Manufacturing Inc. 2549 North 9th Avenue Humboldt, Tennessee 38343, USA +1 731 784 7681 [email protected] reinhausen.com MR Reinhausen customer portal: https://portal.reinhausen.com. Further information on the product and copies of this technical file are available from this address if required. 1.2 Completeness This technical file is incomplete without the supporting documents. The following documents also apply in addition to this technical file: – Connection diagrams – Routine test report – Supplement Also observe generally valid legislation, standards, and guidelines as well as specifications on accident prevention and environmental protection in the re- spective country of use. 1.3 Safekeeping Keep this technical file and all supporting documents ready at hand and accessi- ble for future use at all times. 1.4 Notation conventions 1.4.1 Hazard communication system Warnings in this technical file are displayed as follows. 6 Introduction 10771253/01 EN 1.4.1.1 Warning relating to section Warnings relating to sections refer to entire chapters or sections, sub-sections or several paragraphs within this technical file. Warnings relating to sections use the following format: WARNING Type of danger! Source of the danger and outcome. Action Action 1.4.1.2 Embedded warning information Embedded warnings refer to a particular part within a section. These warnings apply to smaller units of information than the warnings relating to sections. Em- bedded warnings use the following format: DANGER! Instruction for avoiding a dangerous situation. 1.4.1.3 Signal words in warning notices Signal word Meaning DANGER Indicates a hazardous situation which, if not avoided, will result in death or serious injury. WARNING Indicates a hazardous situation which, if not avoided, could result in death or serious injury. CAUTION Indicates a hazardous situation which, if not avoided, could result in mi- nor or moderate injury. NOTICE Indicates measures to be taken to prevent damage to property. Table 1: Signal words in warning notices 1.4.2 Information system Information is designed to simplify and improve understanding of particular procedures. In this technical file it is laid out as follows: Important information. i 1.4.3 Instruction system This technical file contains single-step and multi-step instructions. Single-step instructions Instructions which consist of only a single process step are structured as fol- lows: Aim of action Requirements (optional). Step 1 of 1. Result of step (optional). Result of action (optional). 10771253/01 EN Introduction 7 Multi-step instructions Instructions which consist of several process steps are structured as follows: Aim of action Requirements (optional). 1. Step 1. Result of step (optional). 2. Step 2. Result of step (optional). Result of action (optional). 1.4.4 Typographic conventions Typographic convention Purpose Example UPPERCASE Operating controls, switches ON/OFF [Brackets] PC keyboard [Ctrl] + [Alt] Bold Software operating controls Press Continue button …>…>… Menu paths Parameter > Control parameter Italics System messages, error messages, sig- Function monitoring alarm triggered nals [► Number of pages] Cross reference [► Page 41]. Dotted underscore............................................. Glossary entry, abbreviations, definitions, Glossary entry........................ etc. Table 2: Typographic conventions used in this technical file 8 Introduction 10771253/01 EN 1.5 Notes on the VACUTAP® RMV-II operating in- structions The VACUTAP® RMV-II on-load tap-changer operating instructions (document number 2159612/03) includes descriptions regarding the TAPMOTION® MD-III motor-drive unit. These descriptions no longer apply when using the ETOS® MD-IV motor-drive unit. The following table lists an overview of the content in the operating instructions 2159612/03 that is invalid and in which sections of these operating instructions (10771253/00) the corresponding descriptions can be found: Invalid sections of RMV-II (2159612/03) Comments and valid equivalent in ETOS MD-IV (this document) 3.3 Motor-drive unit 4 Product description 3.4 Monitoring system (VIM) 4.5.3.2 Monitoring system (VIM) 6 Fitting motor-drive unit 6 Mounting 14 Operating the motor-drive unit with the 8.6.2 Operating the motor-drive unit with hand crank the hand crank 16.3 Monitoring system displays and con- 4.5.3.2.3 Displays and controls trols 17.6 Maintaining the motor-drive unit 10.2 Maintaining the motor-drive unit Table 3: Invalid information in the VACUTAP® RMV-II operating instructions 1.6 Open source software This product contains open source software, which has been developed by third parties. The open source software and the corresponding license conditions can be called up in the menu via Settings > Export > Licenses. The open source software is protected by copyright. You are free to use the open source software provided that you comply with the respective license con- ditions. In the event of a conflict, these license conditions shall take precedence over other license conditions. The open source software is provided free of charge. Insofar as this is provided for by the license conditions of the open source software, you can obtain the source text of the open source software at least for three years from receipt of the product against payment of the corresponding costs from your respective contact person at Maschinenfabrik Reinhausen GmbH. 10771253/01 EN Introduction 9 2 Safety – Read this technical file through to familiarize yourself with the product. – This technical file is a part of the product. – Read and observe the safety instructions provided in this chapter. – Read and observe the warnings in this technical file in order to avoid func- tion-related dangers. – The product is manufactured on the basis of state-of-the-art technology. Nevertheless, risks to life and limb for the user or impairment of the product and other material assets due to the function may arise in the event of im- proper use. 2.1 Appropriate use The product is a modular system for controlling, regulating and monitoring a transformer. The components necessary for this are installed in a housing. De- pending on your order, the product is equipped with various function packages. The product is designed solely for use in stationary industrial large-scale electri- cal energy systems and facilities. If used as intended, in compliance with the re- quirements and conditions specified in this technical document and observing the warning notices in this technical document and attached to the product, the product does not pose a risk of injury or damage to property or the environ- ment. This applies throughout the service life of the product, from delivery, in- stallation and operation to removal and disposal. The following is considered intended use: – Operate the product in accordance with this technical document, the agreed- upon delivery conditions and the technical data. – Ensure that all necessary work is performed by qualified personnel only. – Only use the equipment and special tools included in the scope of delivery for the intended purpose and in accordance with the specifications of this technical document. – Only operate the product in industrial areas. Observe the notices in this tech- nical document regarding electromagnetic compatibility and the technical data. 2.1.1 Motor-drive unit The motor-drive unit is used to adjust the operating position of the on-load tap- changer in regulating transformers to the individual operating requirements. The following is considered appropriate use of the motor-drive unit function package: – Use the product only with the transformer and on-load tap-changer specified in the order. – You will find the standard valid for the product and the year of issue on the nameplate. – The serial numbers of on-load tap-changers and on-load tap-changer acces- sories must match if these products are supplied as a set for one order. – Electrically operate the motor-drive unit remotely during normal operation. – In special operating cases (such as during maintenance tasks), the motor- drive unit can also be operated electrically on site via control switch 43-1. 10 Safety 10771253/01 EN – Never operate the motor-drive unit electrically or with the hand crank before the transformer has been disconnected if you think there may be a fault in the transformer or the on-load tap-changer. For more information, refer to the "Troubleshooting" chapter. – The provided hand crank is for activating the motor-drive unit during installa- tion and tests in the transformer plant or during maintenance tasks if the transformer has been disconnected. – For details about using the hand crank in emergency operation when the transformer is energized, refer to the "Operation" chapter. 2.1.2 On-load tap-changer regulation The on-load tap-changer regulation function package is used to automatically adjust the tap position of an on-load tap-changer with motor-drive unit. 10771253/01 EN Safety 11 2.2 Inappropriate use Use is considered to be inappropriate if you use the product other than as de- scribed in the "Appropriate use" section. 2.2.1 Internal power supply Do not use the power supply units which are used to supply the internal assem- blies in the control cabinet to supply external circuits. 12 Safety 10771253/01 EN 2.3 Fundamental safety instructions To prevent accidents, malfunctions and damage as well as unacceptable ad- verse effects on the environment, those responsible for transport, installation, operation, maintenance and disposal of the product or parts of the product must ensure the following: Personal protective equipment Loosely worn or unsuitable clothing increases the danger of becoming trapped or caught up in rotating parts and the danger of getting caught on protruding parts. This poses a danger to life and limb. – Wear appropriate personal protective equipment such as a helmet, work gloves, etc. for the respective activity. – Never wear damaged personal protective equipment. – Never wear rings, necklaces, or other jewelry. – If you have long hair, wear a hairnet. Work area Untidy and poorly lit work areas can lead to accidents. – Keep the work area clean and tidy. – Make sure that the work area is well lit. – Observe the applicable laws for accident prevention in the relevant country. Drying the transformer Drying the product together with the transformer in an autoclave will cause damage to property and product malfunctions. – Never dry the product together with the transformer in an autoclave. Working during operation The product may only be operated in a sound, operational condition. Otherwise it poses a danger to life and limb. – Regularly check the operational reliability of safety equipment. – Comply with the inspection work, maintenance work and maintenance inter- vals described in this technical file. Invisible laser radiation Looking directly into the beam or the reflected beam can cause eye damage. The beam is emitted at the optical connections or at the end of the fiber-optic cables connected to them on the assemblies. Read the chapter "Technical Data" [►Section 13, Page 246] for further information. – Never look directly into the beam or the reflected beam. – Never look into the beam with the aid of optical instruments such as a mag- nifying glass or a microscope. – In the event that the laser beam strikes your eyes, close your eyes immedi- ately and move your head out of the path of the beam. Working with current transformers Dangerous high voltages may occur when a current transformer is operated with an open secondary circuit. This can lead to injuries and property damage. – Never operate a current transformer with an open secondary circuit; short- circuit the current transformer to prevent this. – Observe the information in the current transformer operating instructions. 10771253/01 EN Safety 13 Dangerous external voltages Depending on the product version, the control cabinet may be powered from different circuits (e.g., separate power supply circuits, measurement circuits). In this case, please note that circuits within the control cabinet can still carry dan- gerous voltages even if you have turned off the fuses and/or main switches of the control cabinet. Note the connection diagram supplied. Dangerous residual energies There are capacitors in the control cabinet that can still carry residual voltages even after the system has been completely switched off. Wait for a discharge time of at least 2 minutes after switching off the system before you start work- ing in the control cabinet. Handling electrical components Electrical components can be damaged by electrostatic discharge. – Never touch electrical components during commissioning, operation or maintenance work. – Take suitable measures (such as covers) to ensure that personnel cannot touch components. – Wear suitable personal protective equipment. Securing the motor-drive unit If you open the motor-drive unit during operation, there is a danger of electric shock due to live components behind the swing frame. – Secure the motor-drive unit against unauthorized opening during operation by using a padlock. – The motor-drive unit may only be opened by an electrically skilled person. Opening the swing frame Opening the swing frame while the motor-drive unit is in operation may result in electric shocks due to live components. – The swing frame may only be opened by an electrically skilled person. Explosion protection Highly flammable or explosive gases, vapors and dusts can cause serious explo- sions and fire. This increases the danger to life and limb. – Do not install, operate or perform maintenance work on the product in areas where a risk of explosion is present. Safety markings Warning signs and safety information plates are safety markings on the prod- uct. They are an important aspect of the safety concept. – Observe all safety markings on the product. – Make sure all safety markings on the product remain intact and legible. – Replace safety markings that are damaged or missing. Ambient conditions To ensure reliable and safe operation, the product must only be operated under the ambient conditions specified in the technical data. – Observe the specified operating conditions and requirements for the installa- tion location. Auxiliary materials and operating materials Auxiliary materials and operating materials not approved by the manufacturer can lead to personal injury, damage to property and malfunctions of the prod- uct. – Only use conductive and grounded hoses, pipes, and pump equipment that are approved for flammable liquids. 14 Safety 10771253/01 EN – Only use lubricants and auxiliary materials approved by the manufacturer. – Contact the manufacturer. Modifications and conversions Unauthorized or inappropriate changes to the product may lead to personal in- jury, material damage and operational faults. – Only modify the product after consultation with Maschinenfabrik Reinhausen GmbH. Spare parts Spare parts not approved by Maschinenfabrik Reinhausen GmbH may lead to physical injury, damage to the product and malfunctions. – Only use spare parts that have been approved by Maschinenfabrik Rein- hausen GmbH. – Contact Maschinenfabrik Reinhausen GmbH. 2.4 Personnel qualification The person responsible for assembly, commissioning, operation, maintenance and inspection must ensure that the personnel are sufficiently qualified. Electrically skilled person The electrically skilled person has a technical qualification and therefore has the required knowledge and experience, and is also conversant with the applicable standards and regulations. The electrically skilled person is also proficient in the following: – Can identify potential dangers independently and is able to avoid them. – Is able to perform work on electrical systems. – Is specially trained for the working environment in which (s)he works. – Must satisfy the requirements of the applicable statutory regulations for acci- dent prevention. Electrically trained persons An electrically trained person receives instruction and guidance from an electri- cally skilled person in relation to the tasks undertaken and the potential dangers in the event of inappropriate handling as well as the protective devices and safety measures. The electrically trained person works exclusively under the guidance and supervision of an electrically skilled person. Operator The operator uses and operates the product in line with this technical file. The operating company provides the operator with instruction and training on the specific tasks and the associated potential dangers arising from improper han- dling. Technical Service We strongly recommend having maintenance, repairs and retrofitting carried out by our Technical Service department. This ensures that all work is per- formed correctly. If maintenance is not carried out by our Technical Service de- partment, please ensure that the personnel who carry out the maintenance are trained and authorized by Maschinenfabrik Reinhausen GmbH to carry out the work. Authorized personnel Authorized personnel are trained by Maschinenfabrik Reinhausen GmbH to carry out special maintenance. 10771253/01 EN Safety 15 2.5 Personal protective equipment Personal protective equipment must be worn during work to minimize risks to health. – Always wear the personal protective equipment required for the job at hand. – Never wear damaged personal protective equipment. – Observe information about personal protective equipment provided in the work area. Protective clothing Close-fitting work clothing with a low tearing strength, with tight sleeves and with no protruding parts. It mainly serves to protect the wearer against being caught by moving machine parts. Safety shoes To protect against falling heavy objects and slipping on slip- pery surfaces. Safety glasses To protect the eyes from flying parts and splashing liquids. Visor To protect the face from flying parts and splashing liquids or other dangerous substances. Hard hat To protect against falling and flying parts and materials. Hearing protection To protect against hearing damage. Protective gloves To protect against mechanical, thermal, and electrical haz- ards. Table 4: Personal protective equipment 16 Safety 10771253/01 EN 3 IT security Observe the following recommendations to operate the product safely. 3.1 General – Ensure that only authorized personnel have access to the device. – Only use the device within an ESP (electronic security perimeter). Do not connect the device to the Internet in an unprotected state. Use mechanisms for vertical and horizontal network segmentation and security gateways (fire- walls) at the transition points. – Ensure that the device is only operated by trained personnel who are familiar with IT security. – Check regularly whether software updates are available for the device and perform the updates. 3.2 Commissioning Observe the following recommendations for device commissioning: – User IDs must be unique and assignable. Do not use a "Group account" func- tion or the "Auto login" function. – Activate the "Auto logout [►Section 8.1.2.2, Page 90]" function. – Restrict the rights of the individual user groups as much as is feasible; this helps avoid errors during operations. A user with the "Operator" role, for ex- ample, should only perform operations and should not be able to change any device settings. – Delete or disable the default "admin" user ID. This requires first creating a new user account with the "Administrator" role. You can then use it to delete or disable the default "admin" account. – Deactivate service user access [►Section 8.1.2.3, Page 90]. – Activate brute-force protection [►Section 8.1.20, Page 138]. – Enable SSL/TLS encryption [►Section 8.1.2, Page 89]; access to the device is then only possible using the SSL/TLS protocol. In addition to encrypting communication, this protocol also checks the authenticity of the server. – Integrate the device into a public key infrastructure. Create your own SSL cer- tificates for this if necessary and then import them. – Connect the device to a central log server by using the syslog interface [►Section 8.1.8, Page 96]. – Deactivate all unused interfaces [►Section 8.1.3, Page 91]. 3.3 Operation Observe the following recommendations during device operation: – Change the password at regular intervals. – Export the security log [►Section 8.1.23.1, Page 140] at regular intervals. – Check the log files regularly for unauthorized system access and other secu- rity-related events. 10771253/01 EN IT security 17 3.4 Interfaces The device uses the following interfaces for communication: CP - 8050 RS-232 X5 SICAM A8000 RS-485 X4 ETH X3 RY ER ETH X2 6 5 4 3 2 X1 1 Figure 1: CPU assembly interfaces Interface Protocol Port Description X2 TCP 102 IEC 61850 X2 TCP 502 Modbus 1 X2 TCP 20000 DNP3 1 X2 TCP 2404 IEC 60870-5-104 1 X2 UDP 123 SNTP X2 - - Bus extension (optional) X3 TCP 80 HTTP for web-based visualization 2 X3 TCP 443 HTTPS for web-based visualization X3 TCP 22 SSH (only for MR Service) 3 X3 UDP/TCP 514 Syslog X4 - - Serial interface (SCADA) X5 - - Serial interface (SCADA) Table 5: Interfaces and open ports of the CPU assembly 3.5 Encryption standards The device supports the following TLS versions: – TLS 1.2 – TLS 1.3 1 Default setting; if you have modified the port for the control system protocol, only the set port is open. 2 Port is closed if you activate the device's SSL encryption. 3 Port is closed if you deactivate the Service user access [►Section 8.1.2.3, Page 90]. 18 IT security 10771253/01 EN The device uses the following cipher suites for a TLS-secured connection: Cipher suite TLS version [►Page 93] >=1.2 >=1.3 TLS_AES_128_GCM_SHA256 TLS_AES_256_GCM_SHA384 TLS_ECDHE_ECDSA_WITH_AES_128_CBC_SHA256 - TLS_ECDHE_ECDSA_WITH_AES_128_GCM_SHA256 - TLS_ECDHE_ECDSA_WITH_AES_256_CBC_SHA384 - TLS_ECDHE_ECDSA_WITH_AES_256_GCM_SHA384 - TLS_ECDHE_RSA_WITH_AES_128_CBC_SHA256 - TLS_ECDHE_RSA_WITH_AES_128_GCM_SHA256 - TLS_ECDHE_RSA_WITH_AES_256_CBC_SHA384 - TLS_ECDHE_RSA_WITH_AES_256_GCM_SHA384 - Table 6: Cipher suite ( = available, - = not available) The device uses the SHA256 hash function to save passwords. 10771253/01 EN IT security 19 4 Product description 4.1 Scope of delivery The motor-drive unit is packaged with protection against moisture and is deliv- ered as follows: – Gear motor – Hand crank – Control cabinet – Connection cable – Product documentation Please note the following: 1. Check the shipment for completeness using the shipping documents. 2. Store the parts in a dry place until installation. 3. The product must remain in its airtight, protective wrapping and may only be removed immediately before installation. 4.2 Function description The motor-drive unit adjusts the operating position of on-load tap-changers in regulating transformers to the individual operating requirements. To do so, a gear motor that is controlled by an electronic control unit is mounted on the on-load tap-changer. The electronic control unit is located in a control cabinet and is connected to the gear motor via a connection cable. The motor-drive unit control unit can be configured and the measured values and events can be displayed using the web-based visualization. Here, the func- tional scope is based on the ordered product version. Behavior in the event of a voltage interruption On-load tap-change operations are only possible if the controller is ready for op- eration. 4.3 Performance features The motor-drive unit is characterized by the following features in particular: – On-load tap-changer driven using the gear motor – Electronic control of the gear motor with integrated protective functions – Over-run protection – End position detection – Easy connection of the gear motor and control cabinet via integrated cable plug connection – Acquiring the monitoring system (VIM) signals – Web-based visualization for configuring the motor-drive unit and displaying important data – Integrated voltage regulation (optional) 20 Product description 10771253/01 EN – SCADA – IEC 60870-5-101 – IEC 60870-5-104 – IEC 61850 (edition 1 and edition 2) – Modbus (RTU, TCP, ASCII) – DNP3 – Free digital inputs and outputs, depending on the device configuration – Free analog inputs and outputs, depending on the device configuration 4.4 Operating modes You can select the device operating mode using the rotary switch in the control cabinet (43-2). You can operate the device in the following operating modes: LOCAL (43-2 in position LOC) In the Local operating mode, you can only actuate the device using the operat- ing elements in the control cabinet. Commands via digital inputs or SCADA are not possible. There is no automatic on-load tap-changer control. REMOTE (43-2 in position REM) In the Remote operating mode, you can actuate the device, depending on the setting of the Remote behavior [►Page 89] parameter, only via external but- tons or SCADA commands. You can activate (AVR AUTO) or deactivate (AVR manual) the optional on-load tap-changer control function via digital inputs or SCADA. AUTO (43-2 in position AUTO, only with option "Automatic on-load tap-changer control") Automatic on-load tap-changer control is active only in the Auto operating mode. You cannot actuate the motor-drive unit manually in this mode. LOCAL REMOTE AUTO Control using 43-1 control switch Yes No No Control using digital inputs No Yes No Control using SCADA 4 No Yes No 5 On-load tap-changer regulation AVR MANUAL AVR MANUAL AVR AUTO AVR AUTO Table 7: Overview of operating modes 4 Optional when connecting the motor-drive unit to a control system (SCADA). 5 Only available if the device is equipped with the "On-load tap-changer control" option. 10771253/01 EN Product description 21 4.5 Design This chapter contains an overview of the design of the motor-drive unit. The en- tire system consisting of the on-load tap-changer and motor-drive unit includes the following subassemblies: Figure 2: Design 1 On-load tap-changer 3 Connecting cable 2 Gear motor 4 Control cabinet 22 Product description 10771253/01 EN 4.5.1 Name plate The nameplate is in the control cabinet. 1 Figure 3: Nameplate 1 Nameplate 4.5.2 Gear motor The gear motor is positioned below the on-load tap-changer. It is connected di- rectly to the drive shaft of the on-load tap-changer and carries out the on-load tap change operation. Figure 4: Gear motor 10771253/01 EN Product description 23 Figure 5: Connecting cable 1 Motor cable (W1) 2 Control cable (W2) 3 Motor brake cable (W3) 4 Connection cable (W4) of the moni- toring system (VIM) Figure 6: Tap position display 1 Operating position 2 Tap-change indicator 3 Tap position table for assigning the operating position to the tap position (designation) 24 Product description 10771253/01 EN 4.5.3 Control cabinet The control cabinet contains the following components: 1 2 3 4 5 6 7 Figure 7: Control cabinet 1 Hand crank 2 Monitoring system (VIM) 3 Display 4 Operating elements (control switch 43-1 RAISE/LOWER, control switch 43-2 LOC/REM or 43-2 LOC/AUTO/ REM, as an option control switch 43-3 Single/Double Step) 5 Motor protective switch 8-2 6 Service interface (J2) 7 Document pouch 10771253/01 EN Product description 25 Control cabinet door The control cabinet door is equipped with a key on the outside for activating the display when it is in sleep mode. Sleep mode is automatically reactivated after 5 minutes. If you press the button several times, you can navigate back through the menu structure until you reach the start page. Figure 8: Control cabinet door 1 Key for activating the display 4.5.3.1 ISM® assemblies 4.5.3.1.1 Power supply PS The PS assembly contains the power supply unit for supplying power to the ISM® assemblies. The RY LED signals that the assembly is ready for operation. PS - 8640 SICAM A8000 RY 4 - 3 X1 2 1 + Figure 9: PS assembly 4.5.3.1.2 CPU (central processing unit) The CPU assembly is the central processing unit for the device. It contains the following interfaces: – Serial interface RS485/422 (electrically isolated, X4) – Internal system interface RS232 (X5) – 2x Ethernet 10/100 Mbps (electrically isolated, X2, X3) 26 Product description 10771253/01 EN CP - 8050 RS-232 X5 SICAM A8000 RS-485 X4 ETH X3 RY ER ETH X2 6 5 4 3 2 X1 1 Figure 10: CPU assembly 4.5.3.1.3 Voltage measurement U 3 The U3 assembly is used for measuring 3-phase voltage. The RY LED signals that the assembly is ready for operation. AI - 8340 10 9 8 SICAM A8000 7 6 5 4 3 2 1 X2 RY 4 3 2 X1 1 Figure 11: U 3 assembly 10771253/01 EN Product description 27 4.5.3.1.4 Current measurement I 3 The I 3 assembly is used for measuring 3-phase voltage and current. The RY LED signals that the assembly is ready for operation. AI - 8330 6 I1 SICAM A8000 5 4 I2 3 2 I3 1 X1 RY Figure 12: I 3 assembly 4.5.3.1.5 Digital outputs DO 8 The DO 8 assembly provides you with 8 digital outputs (relays). The RY LED sig- nals that the assembly is ready for operation. DI - 8212 4 3 2 X4 SICAM A8000 1 4 3 2 X3 1 RY 4 3 2 X2 1 4 3 2 X1 1 Figure 13: DO 8 assembly 28 Product description 10771253/01 EN 4.5.3.1.6 Digital inputs DI 16-110 V The DI 16-110V assembly has 16 digital inputs with a nominal voltage of 110 V DC. The RY LED signals that the assembly is ready for operation. DI - 811x 10 9 8 7 SICAM A8000 6 5 4 3 2 X2 1 RY 10 9 8 7 6 5 4 3 2 X1 1 Figure 14: DI 16-110V assembly 4.5.3.1.7 Digital inputs DI 16-220 V The DI 16-220V assembly has 16 digital inputs with a nominal voltage of 220 V DC. The RY LED signals that the assembly is ready for operation. DI - 811x 10 9 8 7 SICAM A8000 6 5 4 3 2 X2 1 RY 10 9 8 7 6 5 4 3 2 X1 1 Figure 15: DI 16-220V assembly 10771253/01 EN Product description 29 4.5.3.1.8 Digital inputs DI 16-24 V The DI 16-24V assembly has 16 digital inputs with a nominal voltage of 24 V DC. The RY LED signals that the assembly is ready for operation. DI - 811x 10 9 8 7 SICAM A8000 6 5 4 3 2 X2 1 RY 10 9 8 7 6 5 4 3 2 X1 1 Figure 16: DI 16-24V assembly 4.5.3.1.9 Digital inputs DI 16-48 V The DI 16-48V assembly has 16 digital inputs with a nominal voltage of 48 V DC. The RY LED signals that the assembly is ready for operation. DI - 811x 10 9 8 7 SICAM A8000 6 5 4 3 2 X2 1 RY 10 9 8 7 6 5 4 3 2 X1 1 Figure 17: DI 16-48V assembly 30 Product description 10771253/01 EN 4.5.3.1.10 Analog outputs AO 4 The AO 4 assembly provides you with 4 analog outputs for outputting mea- sured values (0/4…20 mA, 0…10 V). The RY LED signals that the assembly is ready for operation. AI - 8380 4 3 2 X4 SICAM A8000 1 4 3 2 X3 1 RY 4 3 2 X2 1 4 3 2 X1 1 Figure 18: AO 4 assembly 4.5.3.1.11 Analog inputs AI 4 The AI 4 assembly provides you with 4 analog inputs for current measurement (0/4…20 mA) or voltage measurement (0…10 V) via analog sensors. The RY LED signals that the assembly is ready for operation. AI - 8320 4 3 2 X4 SICAM A8000 1 4 3 2 X3 1 RY 4 3 2 X2 1 4 3 2 X1 1 Figure 19: AI 4 assembly 10771253/01 EN Product description 31 4.5.3.1.12 Analog inputs AI 4-T The AI 4-T assembly provides you with 4 analog inputs for temperature mea- suring (PT100, PT1000). The RY LED signals that the assembly is ready for oper- ation. AI - 8310 10 9 8 7 SICAM A8000 6 5 4 3 2 X2 1 RY 10 9 8 7 6 5 4 3 2 X1 1 Figure 20: AI 4-T assembly 4.5.3.1.13 System networking BES The BES assembly is a bus extension module and extends the device by one ad- ditional bus rail with additional assemblies. The RY LED signals that the assem- bly is ready for operation. The ER LED signals that the device has detected an error. CI - 8530 ETH X3 SICAM A8000 ETH X2 45 23 6 I/0 789 F01 A E B CD RY ER 4 - 3 X1 2 1 + Figure 21: BES assembly 32 Product description 10771253/01 EN 4.5.3.1.14 System networking COM-ETH The COM-ETH assembly provides you with 5 Ethernet interfaces. CI - 8520 ETH X5 SICAM A8000 ETH X4 ETH X3 RY ER ETH X2 ETH X1 Figure 22: COM-ETH assembly 4.5.3.1.15 CAN gateway The CAN gateway provides you with a CAN bus connection. Use the connec- tion CAN1 for the connection to the CAN bus. Figure 23: PEAK PCAN 10771253/01 EN Product description 33 4.5.3.1.16 IDS VLX vibroacoustic input module The IDS VLX assembly records the signals of the vibration sensor via one of the IEPE interfaces. The measured signals are processed with evaluation algo- rithms. Depending on the variant, the module has 1 measuring channel (IDS VLX1) or 3 usable measuring channels (IDS VLX4). Figure 24: IDS VLX4 4.5.3.2 Monitoring system (VIM) The monitoring system is also known as the VIM module (Vacuum Interrupter Monitoring). 4.5.3.2.1 Function description The monitoring system can detect a vacuum interrupter malfunction in the fol- lowing operating modes: – Electric on-load tap-change operation resulting from manual actuation of the RAISE/LOWER control switch – Electrical on-load tap-change operation resulting from automatic activation by a voltage regulator In the event of an error, the monitoring system triggers the following actions: – The on-load tap-changer is stopped and returned to its starting position – The motor protective switch 8-2 is tripped – Further electrical on-load tap-change operations are blocked – The error indication on the monitoring circuit board lights up – Yellow LED if there are faults in the signal transmission – Red LED should a vacuum interrupter experience an error – Faults are indicated by the red Alarm indicator light (86RL) on the swing frame of the motor-drive unit lighting up. 34 Product description 10771253/01 EN 4.5.3.2.2 Monitoring system design Figure 25: Monitoring system (VIM), schematic diagram The monitoring system evaluates the current signals in the on-load tap- changer. For fail-safe transmission, the current signals are converted into opti- cal signals and transferred via fiber-optic cables. The monitoring system carries out the following checks: 1. After the by-pass switch has opened and before the vacuum interrupter opens, there must be a current signal. 2. Once the vacuum interrupter opens, there must be no current signal present. If one is present, the monitoring system generates an alarm signal. The monitoring system is also fitted with self-monitoring, which checks the in- ternal circuits. At the input, the electronics are protected by a Zener diode and an interchangeable fuse. 10771253/01 EN Product description 35 4.5.3.2.3 Displays and controls Figure 26: Monitoring system (VIM) displays and controls 1 RESET key (red) 2 TEST key (green) 3 Power LED (green) 4 1 yellow and 1 red LED per phase for signaling errors The following monitoring system (VIM) displays and controls are located in the motor-drive unit control cabinet: – The green TEST key is used to check the internal circuitry of the monitoring system.