Mant1.ppt
Document Details
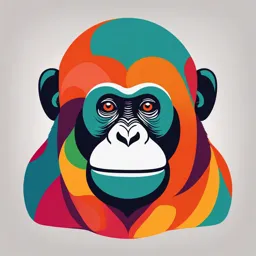
Uploaded by SustainableGallium
Tags
Related
- Safety Management Systems PDF
- On-load tap-changer Installation and Commissioning Instructions PDF
- VACUTAP® VM 300 On-load tap-changer Operating Instructions PDF
- OILTAP® R On-load Tap-Changer Installation and Commissioning Instructions PDF
- DS 1 : Concept F.M.D. PDF
- ISO 14224-Reliability and Maintenance Data for Equipment PDF
Full Transcript
CAPACIDAD INICIAL (lo que puede hacer) Mantenimiento no puede elevar la capacidad por Mantenimiento sobre este nivel debe asegurar la capacidad por sobre este nivel RENDIMIENTO DESEADO (lo se quiere q...
CAPACIDAD INICIAL (lo que puede hacer) Mantenimiento no puede elevar la capacidad por Mantenimiento sobre este nivel debe asegurar la capacidad por sobre este nivel RENDIMIENTO DESEADO (lo se quiere que haga) Maxima 1 VIEJA Al mantenimiento le compete la preservación de los bienes NUEVA Al mantenimiento le compete la preservación de la prestación requerida de los bienes En general a los responsables del mantenimiento les gustan los bienes en perfectas condiciones y sienten un cierto rechazo a que esto no ocurra. Esto puede llevar a que se mantengan las prestaciones de los bienes más allá de su uso y se realice mantenimiento por mantenimiento mismo. Se han desarrollado estrategias de mantenimiento donde se trata de preservar la confiabilidad inherente o la capacidad de diseño de todos los bienes. Cuando se profundiza en el rol de los bienes en el negocio se aprecia el hecho de que cada bien físico se pone en servicio porque alguien necesita que haga algo. Por consecuencia, cuando se mantiene un bien , el estado de prestación que debemos lograr es aquel que el usuario necesita. Las funciones y espectativas de perfomance no solo cubren la prestación sino que abarcan la calidad,el servicio al cliente, la economía y eficiencia de la operación, el confort, la protección, el medio ambiente, la integridad estructural y aún la apariencia del bien. Maxima 2 VIEJA Al mantenimiento de rutina le compete eliminar fallas NUEVA Al mantenimiento de rutina le compete evitar, reducir o eliminar las consecuencias de las fallas Cada falla afecta a la organización en algún modo, pero los efectos son diferentes. Pueden afectar la operación, la calidad del producto, el servicio al cliente o el ambiente. Si las consecuencias son importantes vamos a tratar de preveer la falla. Si el modo de falla tiene consecuencias serias trataremos de prevenirla. Si tiene pequeño o poco efecto se puede decidir tomar o no una acción preventiva. Las consecuencias de las fallas son más importantes que sus características técnicas. La principal razón para hacer cualquier mantenimiento proactivo es evitar,reducir o eliminar las consecuencias de la falla. Esto ayuda a que lo que se gasta en mantenimiento se haga donde es más efectivo. Ejemplo Falla Bomba Rotura de rodamiento de Capacidad bomba por desgaste normal nominal: 400 l/min Tiempo de recambio 4 horas Switch Parada 90.000 l 5 HORAS de Bomba Switch Arranque 45.000 l 2,5 HORAS de Bomba Proceso Requerimiento: 300 l/min Maxima 3 VIEJA La mayoría del equipamiento tiene mayor tendencia fallar con el envejecimiento NUEVA La mayoría de las fallas no tienen mayor probabilidad de ocurrencia con el envejecimiento Por décadas, se sugirió que la mejor manera de optimizar la perfomance de los bienes es el overhaul o el reemplazo de partes a intervalos fijos. Esta sugiere que la mayoría de los items tienen un período de operación confiable “X” y luego se desgastan. El pensamiento clásico sostiene que X puede ser determinado de datos históricos permitiendo tomar acciones poco tiempo antes de que falle. Esta predecible relación entre edad y falla es cierta para algunos modos de falla. Tiende a ser cierto en equipamiento en contacto directo con el producto. Por ejemplo; impulsores de bombas, refractario de hornos, asientos de válvulas, etc. Las fallas por edad de uso están asociadas con fatiga y corrosión. Con la investigación aparecen otros modos de falla AVIACION CIVIL A 4% B 2% C 5% D 7% E 14 % F 68% En ausencia de otra evidencia en contrario, es más conservativo desarrollar una estrategia de mantenimiento asumiendo que la falla puede ser aleatoria que suponer que sólo puede ocurrir después de un tiempo fijo. Maxima 4 VIEJA Datos detallados acerca de las tasas de falla deben estar disponibles para poder desarrollar un exitoso programa de mantenimiento NUEVA Las decisiones acerca del gerenciamiento de las fallas del equipamiento deben ser realizadas, casi siempre, sin disponer de datos exhaustivos de las tasas de falla Una gran cantidad de personas cree que solo se pueden formular políticas de mantenimiento efectivas sobre la base de un extenso registro histórico del información sobre fallas. El hecho que incomoda en el tema de la historia técnica es que recogemos datos acerca de fallas que ocurren porque no las prevenimos. El exitoso mantenimiento preventivo implica que no se obtengan datos históricos que necesitamos para decidir que mantenimiento preventivo debemos hacer. Esta contradicción se aplica al revés en la otra punta de la escala de consecuencias. Se tiende a permitir que las fallas con consecuencias menores ocurran porque no importan demasiado. Como resultado, se dispone gran cantidad de datos históricos que generalmente se relacionan con el tiempo de uso. Sin embargo como las fallas no interesan demasiado no es raro encontrar que el intervalo de mantenimiento previsto no es económicamente redituable. La conclusión es que el mantenimiento se debe dedicar a anticipar o prevenir fallas que importen antes que a contarlas. Para ser realmente efectivos, debemos sentirnos a gusto con la idea de cierta incertidumbre y desarrollar estrategias que permitan manejarla con seguridad Maxima 5 VIEJA Hay 3 tipos básicos de mantenimiento: - predictivo - preventivo - correctivo NUEVA Hay 4 tipos básicos de mantenimiento: - predictivo - preventivo - correctivo - detectivo Predictivo ( o basado en condición ) implica chequear si algo está fallando. Preventivo implica overhauls o reemplazo de componentes a intervalos fijos. Correctivo implica reparación de cosas que se encontraron que van a fallar o que ya fallaron. Sin embargo hay una familia de tareas de mantenimiento que no caen en ninguna de las categorías anteriores. Por ejemplo, cuando se activa períodicamente la alarma de incendio no estamos chequeando si falla, no la estamos remplazando y no la estamos reparando. Estamos simplemente viendo si todavía funciona. Son chequeos funcionales para detectar si algo ha fallado. El mantenimiento detectivo aplica solamente para las fallas ocultas que afectan elementos de protección. Se encuentra que del orden del 40% de los modos de falla caen en la categoría de ocultos, por lo cual se estima que un tercio de las tareas de una estrategia de mantenimiento deben ser detectivas. Maxima 6 VIEJA La frecuencia de las tareas del mantenimiento basado en condición deberían estar basados en la frecuencia de la falla y/o en la criticidad de la falla del elemento NUEVA La frecuencia de las tareas del mantenimiento basado en condición deberían estar basados en el período de falla (P-F interval) Cuando se habla de frecuencia de mantenimiento predictivo normalmente se escuchan cosas como: No falla demasiado seguido por lo cual no necesita ser chequeado demasiado seguido Se necesita chequear mas las plantas mas críticas que las menos críticas EL P-F interval gobierna la frecuencia con la cual se debe realizar el predictivo. El intervalo de chequeo debe ser significativamente menor que período de falla si queremos detectar la falla potencial antes que se convierta en una falla funcional. La cantidad de tiempo necesario para responder a cualquier falla potencial que se detecte también influye en el intervalo del predictivo. Esto incluye: Tomar acción para evitar la consecuencia de la falla Planificar la acción correctiva para tratar de realizarla sin interrumpir la operación y/o otras actividades de mantenimiento Organizar los recursos necesarios para reparar la falla Período de falla : 9 meses Tiempo de respuesta: 8 meses Intervalo de inspección: 1 mes Maxima 7 VIEJA Si los dos son técnicamente apropiados, los overhauls a intervalo fijo o reemplazos son por lo general tanto mas baratos y mas efectivos que el mantenimiento a condición NUEVA Si los dos son técnicamente apropiados, el mantenimiento a condición es casi siempre mas barato y mas efectivo que los overhauls a intervalo fijo o reemplazos, a través de toda la vida del bien Las tareas del mantenimiento predictivo deben ser consideradas primero, por las siguientes razones: Pueden casi siempre ser hechas sin mover el bien y usualmente en operación y rara vez interfieren con la operación. Identifican condiciones específicas de fallas potenciales por lo que las acciones correctivas pueden ser claramente definidas antes que el trabajo comience. Esto reduce la cantidad de trabajo de reparación a realizar y permite que se haga más rápido. Identificando en el equipo un punto de falla potencial se puede conocer más de su vida útil. El número de intervenciones por fallas potenciales es apenas más alta que las que resultarían por fallas funcionales, por lo que los costos de las reparaciones y requerimientos de repuestos se minimizan. Ejemplo Mantenimiento a plazo fijo: cambio cada 30.000 millas Condición: banda no menor a 2 mm Promedio de cambio: 40.000 millas Ganancia de vida útil: 33% Maxima 8 VIEJA Los incidentes importantes o catastróficos que involucran multiples fallas son usualmente el resultado de “mala suerte” y por esto son inmanejables NUEVA En una considerable cantidad de casos, la probabilidad de fallas múltiples es una variable manejable , especialmente en sistemas protejidos Recientemente se han desarrollado poderosas herramientas ( como la determinación probabilística del riesgo ) para establecer la probabilidad acumulada de falla y el riesgo total asociado en sistemas complejos. La probabilidad que se considera aceptable para cualquier falla múltiple depende de sus consecuencias. Algunos niveles de aceptación son fijados por las autoridades reguladoras, pero en la gran mayoría de los casos deben ser establecidas por los usuarios del bien. Desde que estas consecuencias varían grandemente de sistema en sistema, lo que se considera aceptable también tiene una gran variación. Esto significa que no hay standards universales de riesgo que puedan ser aplicados a todos los sistemas de un cierto tipo. Cuando alguien tomó la decisión de cual es el nivel de riesgo aceptable es posible decidir que se debe hacer en el diseño, operación y mantenimiento de sistemas protegidos. Maxima 9 VIEJA La más rápida y segura forma de mejorar las prestaciones de un bien no confiable es mejorar el diseño NUEVA Es casi siempre mas efectivo, del punto de vista de costos, tratar de mejorar las prestaciones de un bien no confiable mejorando la forma en que se opera y se mantiene y sólo revisar el diseño si no puede desarrollar las prestaciones que se le requieren El mantenimiento y la operación deberían considerarse antes del rediseño por 3 razones: 1. La mayoría de las modificaciones toma entre 6 meses a 3 años desde la concepción hasta la concreción, dependiendo del costo y la complejidad del nuevo diseño. 2. Muchas organizaciones encaran muchos mas cambios de diseño de los que son fisicamente o económicamente viables. 3. No hay una garantía automática que un nuevo diseño realmente resuelva el problema. Existen muchos proyectos de cambio que no funcionaron que avalan esto. Maxima 10 VIEJA Las políticas genéricas de mantenimiento pueden ser desarrolladas para la mayoría de los tipos de los bienes físicos NUEVA Las políticas genéricas deberían ser aplicadas a bienes idénticos cuyo contexto operativo,funciones y standards de perfomance deseados también sean idénticos Las razones son : Funciones: un elemento puede tener una expectativa de perfomance en un lugar y una diferente en otro. Los diferentes standards de este tipo requieren diferentes estrategias de mantenimiento. Modos de falla : equipamiento idéntico que es usado en aun levemente distintos lugares ( un area de de alta humedad, un area inusualmente polvorienta ) o desarrollan tareas levemente distintas ( cortar un material más duro de lo usual, operar a mayor temperatura, bombear un líquido más abrasivo o más ácido ), los modos de falla varían drásticamente. Esto significa que las estrategias para afrontar esas deben variar en forma acorde. Consecuencias de la falla: las diferentes consecuencias demandan diferentes estrategias de mantenimiento EJEMPLO A B C Condición Mantenimiento A Operando Correctivo B Stand By Detectivo C Operando Predictivo EJEMPLO A B C Condición Mantenimiento A No opera Reparación B Operando Predictivo C Operando Predictivo EJEMPLO A B C Condición Mantenimiento A Stand By Detectivo B Operando Correctivo C Operando Predictivo Maxima 11 VIEJA Los fabricantes de equipos están en la mejor posición para desarrollar los programas de mantenimiento para los nuevos equipos NUEVA Los fabricantes de equipos sólo pueden jugar un rol limitado ( pero todavía importante ) en el desarrollo de los programas de mantenimiento de los nuevos equipos Los fabricantes de equipos pueden tener otras prioridades cuando especifican programas de mantenimiento ( por ejemplo venta de repuestos ). A su vez ellos no pagan por los recursos que se utilizan en el mantenimiento por lo cual no es su interés primordial el minimizarlos o por otro lado pueden ser cotizantes para realizar mantenimiento por lo cual les puede interesar incrementarlo tanto como sea posible. Esta combinación de intereses comerciales e ignorancia acerca del contexto operativo tiende a que los programas de mantenimiento especificados por los fabricantes contengan un alto nivel de sobre mantenimiento y una sobre provisión de repuestos. Una parte de los usuarios resuelven este problema encarándolo de una forma absolutamente diferente. Estos piden a los fabricantes que suministren técnicos de campo experimentados para trabajar con la gente que operará y mantendrá los equipos y desarrollar las estrategias de mantenimiento de forma satisfactoria para todas las partes.