Managerial Accounting: Cost Classification, Job Order & Process Costing PDF
Document Details
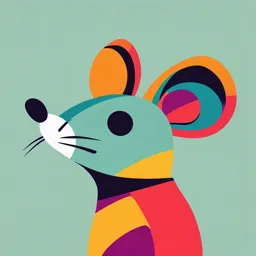
Uploaded by ChasteEducation990
EADA Business School Barcelona
Tags
Related
Summary
This document provides an introduction to managerial accounting, covering essential concepts such as cost classification, cost behavior. It also explores job order costing and process costing methods and includes various examples and exercises. Keywords: managerial accounting, cost classification, job order costing, process costing.
Full Transcript
managerial accounting introduction importance of accounting According to the U.S. Bureau of Labor statistics, 20% of small businesses fail in their first year, and 50% fail within the first five years → poor financial management often due to a lack of accounting knowledge is a leading cause 29%...
managerial accounting introduction importance of accounting According to the U.S. Bureau of Labor statistics, 20% of small businesses fail in their first year, and 50% fail within the first five years → poor financial management often due to a lack of accounting knowledge is a leading cause 29% of startups fail because they run out of cash managerial accounting → focuses on providing information and analysis to support internal decision-making within an organization → the primary purpose of managerial accounting is to assist management in planning, controlling and optimizing business operations users of accounting: main financial statements CAPEX - Capital investment → funds used by a company to acquire, upgrade, and maintain physical assets such as property, plants, buildings, technology, or equipment OPEX - Operating expenses → costs incurred by your business via the production of goods and services (inventory, labor, insurance, water, electricity, wifi, mobile…) EBIT - Earnings before income taxes: revenue - expenses (excluding tax and interest) EBITDA - earnings before interest taxes depreciation and amortization→ measures a company’s overall financial performance IRR - internal rate of return → used to evaluate the profitability of potential investments or projects, compare the attractiveness of different investment opportunities, estimate the annual growth rate of return work in capital → money you need everyday to run your business = > WC = CA-CL session 1: cost classification direct cost: it’s a cost that can be traced in full to the product, service or department that is being costed indirect cost (overheads): it’s a cost which cannot be traced directly to the product, service or department Cost behavior production cost (product): costs identified with a finished product and are part of the inventory value → known as manufacturing costs When the goods are sold these costs become expenses (COGS) non-production cost (period): costs that are deducted as expenses during a period known as manufacturing costs these costs are never part of the inventory value examples: en résumé : 1) Direct Material Direct materials are the raw materials that can be directly traced to the production of specific finished goods. These are essential components of the final product. ex: - For a car manufacturer: Steel, tires, glass for windows. - For a furniture maker: Wood, screws, nails, fabric for upholstery. - For a bakery: Flour, sugar, eggs. 2) Direct Labor Direct labor refers to the wages and benefits paid to workers who are directly involved in manufacturing or producing goods. ex: - For a car manufacturer: Assembly line workers who install engines or doors. - For a furniture maker: Carpenters cutting and assembling wood. - For a bakery: Bakers mixing ingredients and baking cakes. 3) Overhead Overhead includes all indirect costs of production that cannot be directly traced to specific products but are necessary for the production process. This is further categorized into: - Fixed Overhead: Costs that do not vary with production levels (e.g., rent, salaries for supervisors). - Variable Overhead: Costs that fluctuate with production levels (e.g., utility bills, machine maintenance). ex: - For a car manufacturer: Factory utilities, equipment depreciation, and quality control costs. - For a furniture maker: Sanding machine electricity cost, supervisor salaries, and factory rent. - For a bakery: Oven maintenance, lighting, and cleaning supplies. 4) Non-Production Cost Non-production costs are expenses not directly tied to the manufacturing of products but are still essential to the business, often classified as administrative, marketing, or distribution costs. Examples: - Administrative: Office rent, salaries for administrative staff, software subscriptions. - Marketing: Advertising expenses, promotional campaigns, sales team salaries. - Distribution: Delivery truck costs, shipping expenses, packaging for transportation. exercise on starbucks session 2: cost classification part 2 cost flow process COGS = beginning inventory + purchases - ending inventory MANUFACTURING PRODUCT COSTS inventory : refers to the assortment of goods, raw materials, work-in-progress, or finished products that a company holds for the purpose of resale, production or use in its day-to-day operations inventories are classified as follows: - raw materials: these are the basic materials that a company uses to produce its its products - work-in-process (WIP): This represents goods that are in the process of being manufactured but are not yet completed - finished goods: these are fully manufactured products ready for sale to customers Initially, costs are accumulated in the raw materials accounts → includes costs of materials and components that will be used in the manufacturing process As materials are used in the production process, they are used from the raw materials inventory to the production department (WIP) → track the materials consumed Direct labor and manufacturing overhead cost are incurred as workers contribute to the manufacturing process → added to WIP Once the production process is complete, the total costs (direct materials, direct labor, and overhead) → WIP are transferred to the finished goods inventory => completion of the manufacturing process. When the finished goods are sold → cost associated are transferred from the finished goods inventory to the COGS on the IS COST OF GOODS MANUFACTURED Total Manufacturing costs = Direct Materials Used + Direct Labor + Manufacturing Overhead Applied to Work-in-Process total costs of WIP = Beginning work in process inventory + total manufacturing costs Cost of goods manufactured = total costs of WIP - ending WIP inventory COST OF GOODS SOLD DIRECT LABOR COST It refers to the work done by employees that can be easily traced and attributed directly to the production of a specific product or service Examples: - Manufacturing: In a car manufacturing plant, the assembly line workers who directly assemble the parts of the car contribute to direct labor. - Construction: In construction projects, the workers who are involved in physically building the structure, such as carpenters and bricklayers, are considered direct labor. - Bakery: In a bakery, the bakers who are directly involved in preparing and baking the goods are part of the direct labor force INDIRECT LABOR COST It refers to the work done by employees that is not directly tied to the production of a specific product or service. It supports the overall functioning of the business but cannot be easily traced to a specific unit of production Examples: - Supervision: The salary of a production supervisor who oversees the entire manufacturing process is considered indirect labor because they contribute to the overall efficiency rather than working directly on the product. - Maintenance: Workers responsible for maintaining machinery or cleaning the production area are considered indirect labor as their work supports the production process but is not directly involved in the creation of the product. MANUFACTURING OVERHEAD It refers to indirect costs associated with the production of goods that cannot be easily traced to specific units of output. These costs are essential for the production process but do not directly contribute to the creation of a particular product. Components : - Indirect materials - indirect labor - utilities - factory rent & depreciation - property taxes & insurance example: Bike Riders Co. had the following manufacturing activities during the year: -Direct Materials: $400,000 on materials -Direct Labor: $250,000 in labor costs -Manufacturing Overhead: Incurred $300,000 in overhead expenses -Beginning Work in Process (WIP): $40,000 in Work in Process -Units Transferred to Finished Goods: units costing $700,000 from Work in Process to Finished Goods What’s the Ending Work In Process balance? cf exercises COST BEHAVIOR variable cost: expenses that fluctuate in direct proportion to changes in production or sales (raw materials, direct labor, and sales commissions) fixed costs: costs that remain constant regardless of variations in production or sales (rent, salaries of permanent staff, and insurance premiums) mixed costs: costs that combine both a fixed components that stays constant and a variable component that varies with production or sales activity (utility bills with a fixed service change and a variable component based on usage) example: cost behavior mixed cost What’s the expected monthly utility bill if … - fixed utility cost per month is 120$ - Variable cost per kw/h is 0.85$ - expected monthly consumption is 5,600 kwh solution: bill amount = 120+ (0,85*5600) = 4880$ session 3: Job order costing job order costing: cost accounting system used by manufacturing businesses to allocate and trace costs to individual units or group of custom products or services This method is particularly used for industries where each unit produced is unique or where production occurs in small quantities key components: - Direct Materials - Direct Labor - Manufacturing overhead JOB COSTING VS PROCESS COSTING job costing: Used for industries where products or services are customized, unique, or produced in small groups. process costing: applied when products are homogeneous, standardized and produced in large quantities through a continuous or repetitive process ex: bottles, milk, mobiles, oil, chemical manufacturing, food processing and automobile assembly Job order cost flow Using a job cost sheet Measuring direct materials costs Materials requisition example 1: Provide the Journal entry for each of the following transactions: Raw materials totaling 25,000 EUR are purchased on account. Direct materials totaling 7,000 EUR are requisitioned and placed into production. Timesheets submitted by employees reflect direct labor costs of 1,800 EUR to be paid the next week. solution: MEASURING DIRECT LABOR COSTS MEASURING OVERHEAD how to allocate overhead costs to this job ?? Assigning manufacturing overhead costs to jobs The goal is to allocate manufacturing overhead costs to jobs based on some common activity, such as direct labor hours, machine hours, or direct labor costs. A predetermined overhead rate is used to allocate these costs to jobs step 1- identify cost drivers - Direct labor hours : number of hours worked by employees involved in production - direct labor cost : wages paid to workers who are involved in the production - machine hours : number of hours machines are used in the production process step 2- determine the estimated overhead cost determine for a specific period of time → e.g. a week, a month or a year Overhead costs are initially recorded in a general ledger account called the “manufacturing overhead” account. The account accumulates all indirect manufacturing costs step 3 - calculate the predetermined overhead rate calculate the predetermined overhead rate by dividing the estimated overhead costs by a relevant cost driver, often the estimated direct labor hours or machine hours denominator → e.g. direct labor hours, direct labor costs, machine hours or cost of materials step 4 – allocate overhead to jobs Once the predetermined overhead rate is established, it is used to allocate overhead costs to jobs based on the actual usage of the cost driver. At the end of a specific period, allocate the overhead costs to individual jobs based on the actual usage of the predetermined cost driver. For each job, multiply the actual number of hours for the cost driver (e.g., actual direct labor hours) by the predetermined overhead rate. Overhead Allocated to Job= Actual Hours of Cost Driver x Predetermined Overhead Rate For example, if the predetermined overhead rate is 5 EUR per direct labor hour, and Job A requires 10 hours of direct labor, 50 EUR of overhead costs would be allocated to Job A. step 5 – Adjust for overhead under or overapplied compare the total overhead costs allocated to jobs with the ACTUAL overhead costs incurred → if there is a difference (underapplied or overapplied), adjust the overhead allocated to jobs underapplied : actual overhead costs (debits) > overhead applied to jobs (credits) overapplied: actual overhead costs (debits) < overhead applied to jobs (credits) step 6 – Record in job costs sheets Allocate the overhead costs to each job on the job cost sheet, along with direct materials and direct labor costs. The total cost on the job cost sheet is now complete, incorporating direct materials, direct labor, and allocated overhead Example 3. A company that produce custom sport shoes has provided the following information: -For the year, manufacturing overhead costs are expected to be €400,000 -Expected machine usage is 60,500 hours -The company assigns overhead based on machine hours -Job No. 1 used 3,000 machine hours Calculate the Predetermined overhead rate and the overhead amount to be allocated to Job N° 1 example 4: Activity-based costing (ABC costing) step 1: Identify costly activities required to complete product Purchasing materials setting up machines running machines assembling products inspecting finished products step 2: Assign estimated overhead costs to the activities step 3: Identify the cost driver for each activity step 4: Calculate a predetermined overhead rate for each activity The numerator requires an estimate of all overhead costs for the year, such as indirect materials, indirect labor and other indirect costs associated with the factory step 5: Allocate overhead costs to products Determine the activities requirement for each product Step 6. Adjust for Overhead Under or Overapplied Compare the total overhead costs allocated to jobs with the actual overhead costs incurred. If there is a difference (underapplied or overapplied overhead), adjust the overhead allocated to jobs accordingly. Underapplied overhead occurs when actual overhead costs (debits) are higher than overhead applied to jobs (credits). Overapplied overhead occurs when actual overhead costs (debits) are lower than overhead applied to jobs (credits) Step 7. Record in Job Cost Sheets Allocate the overhead costs to each job on the job cost sheet, along with direct materials and direct labor costs. The total cost on the job cost sheet is now complete, incorporating direct materials, direct labor, and allocated overhead. underapplied overhead When the overhead applied to jobs < actual overhead incurred => transfer underapplied to COGS (it decreases net operating income) overapplied overhead overhead applied to jobs > actual overhead incurred during the period => reduce the COGS for the overapplied overhead (it increases net operating income) Disposition of underapplied and overapplied overhead Adjustment to Cost of Goods Sold (COGS): The overapplied amount can be credited to the Cost of Goods Sold account. This reduces the COGS and increases the company's reported net income, leading to higher profitability. Proration Among Accounts: Companies may choose to prorate the overapplied overhead among WIP, Finished goods and COGS JOB ORDER COSTING DIFFERENCES BETWEEN JOB ORDER COSTING AND PROCESS COSTING PROCESS COSTING : EQUIVALENT UNITS When units of work-in-process (WIP) inventory exist at the end of the reporting period, process costing requires that these partially completed units be converted to the equivalent completed units (called equivalent units). The equation used to calculate equivalent completed units is as follows: Equivalent units = Number of physical (actual) units × Percentage of completion Because direct materials, direct labor, and manufacturing overhead typically enter the production process at different stages, equivalent units must be calculated separately for each of these production costs