Machinery Watchstander Study Guide PDF
Document Details
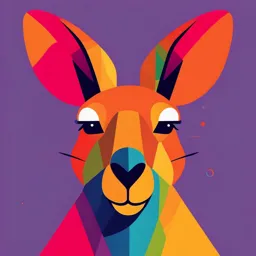
Uploaded by UnaffectedOak2839
United States Coast Guard Academy
Tags
Related
- Farm Power and Machinery Notes - Horticultural College
- Philippine Agricultural Engineering Standard PAES 101 : 2000 PDF
- Philippine Agricultural Engineering Standard PAES 101 : 2000 PDF
- Farm Machinery and Power – FMP 211 PDF
- PAES 106 : 2000 Agricultural Machinery Soil Tillage and Equipment Terminology PDF
- Mecha Power Machinery Equipment HIGHLIGHTED PDF
Summary
This study guide provides information on machinery watch rounds, restricted maneuvering doctrine (RMD), and different propulsion modes. It also includes detail questions related to different machinery spaces and equipment.
Full Transcript
UNOFFICIAL MACHINERY WATCHSTANDER STUDY GUIDE This does not replace or supersede the Machinery watch stander PQS 1 Machinery watch General Watch Practices #1: Demonstrate the ability to conduct a proper Machinery watch rounds. State...
UNOFFICIAL MACHINERY WATCHSTANDER STUDY GUIDE This does not replace or supersede the Machinery watch stander PQS 1 Machinery watch General Watch Practices #1: Demonstrate the ability to conduct a proper Machinery watch rounds. State what machinery spaces are to be checked and how to check them: There are two types of rounds conducted during the Machinery watch. On the even hours, a machinery round is conducted. This round includes taking readings from the MPDEs, and GT if running. It also includes examination of and readings taken from any running generators. It also includes examination and readings from the steering gear rooms and shaft alleys. Once during a four hour watch, an Auxillary round is conducted. Which includes taking readings from and examining the spaces: AC flats, VCHT and lift stations, the S/W cooling pumps, the air compressors, the refers, and the ROs if running. A visual inspection is also made of the watermist stations. #3 Know the initial actions per Causality Control Manual: Read the manual. #4 Outline the important parts of the Restricted Maneuvering Doctrine (RMD) - Is set during the following conditions: - General Quarters I and III - Special Sea Detail/Nav and Anchor Detail - Underway replenishment/fueling at sea - Towing - Flight Quarters condition 1 - Law enforcement phases I, II, IV - Maintain constant communication with the OOD. #5: Read the EO’s standing orders Read and sign #6: Be familiar with the different Propulsion modes - Harbor Mode (emergency mode) – 2 lever control, each shaft controlled independently.  One main runs at a constant speed and turns both shafts. The one main is clutched in at low speed, (60 and 66s engaged clutches) and no mode can be selected on the other main. 75 SRPM max  Used in the event of a MPDE casualty or whenever the OOD wants it - Cruising Mode – single lever control  One main runs at variable speeds and turns both shafts. Control lever of the selected side controls engine speed and propeller pitch of both shafts. Engine is engaged in Low speed, (60 clutch and 66 clutches) and no other mode can be selected on the other main. - Maneuvering Mode – single or dual lever control based on number of MPDEs online  Each main drives it’s own shaft, engine speed and pitch are controlled variably by each control lever.  Only the 60 clutches are engaged on each RED Gear  When maneuvering mode is selected on one side, it may be selected on the other, or no mode may be selected at all. 2 - Gas Turbine Mode – one lever control of both shafts  The GT drives both shafts exclusively.  Speed and propeller pitch are controlled variably by one control lever.  SSS and 66 clutches are engaged - CODAG mode – one lever control of both shafts  Both mains and the GT simultaneously turn both shafts. SSS, 66, and 47 clutches are engaged  The speed of the gas turbine, the speeds of both engines and the pitch of both propellers are adjusted via one control lever. #7: What are the 5 forms of communication in ECR? - the 1 MC - Phones - Hydra radios - SPP - telegraph system #8: Reset a MCMS console: Open panel below console, press small reset button. De-energize and re-energize if necessary #9: Know the locations of Fire Extinguishers and EEBD’s in machinery spaces. AMR Extinguishers - upper level: AFFF left of base of entrance ladder, AFFF left of entrance to VCHT room, PKP and CO2 left of entrance ladder after descending - lower level: AFFF behind ladder to lower level, AFFF FWD amidships in front of GEN 1, PKP and CO2 port side lower level near ‘escape’ ladder to VCHT room AMR EEBDs - upper level: 5 behind entrance ladder, 2 in VCHT room - lower level: 2 behind Auxiliary F/O service pump control panel, 2 on the port side near ladder to VCHT FMMR Extinguishers: - upper level: AFFF at bottom of STBD entrance ladder under GT fan control panel, CO2 and PKP behind STBD entrance ladder, AFFF left of base of PORT entrance ladder. - lower level: AFFF, PKP and CO2 all in front of Gen 2 LOP on STBD side. AFFF, PKP, and CO2 inboard of fire plug on port side. ` FMMR EEBDs: - upper level: 4 next to GT cooling fan at the base of the STBD entrance ladder, 4 at base of PORT entrance ladder, 2 FWD of FOWK stateroom -lower level: 3 on top of phone left of PORT decent ladder, 3 near STBD aft escape trunk AMMR Extinguishers: - upper level: AFFF, PKP, and CO2 behind PORT entrance ladder, AFFF left of base of STBD entrance ladder. - lower level: AFFF, PKP, CO2 all near STBD decent ladder, AFFF next to fire pump four at the base of the port decent ladder. AMMR EEBDs: -upper level: 6 aft of air receiver #2 on the port side -lower level: 2 above S/W pump 3 on STBD side, 2 at the base of the PORT decent ladder. 3 Gen 3 Room Extinguishers: - lower level: 2 AFFF, one by entrance, one outboard by Gen. LOP. 1 PKP and 1 CO2 on AFT Bulkhead, inboard side - upper level: PKP, CO2, AFFF near entrance Gen 3 Room EEBDs: - lower level: 2 near entrance - upper level: none #10: Know the locations of all main emergency shut downs for all machinery spaces - AMR  Generator 1 E-Stop inside VCHT room  Gen 1 E-stop outside entrance to AMR  Gen 1 E-stop on LOP - FMMR  Generator 2 E-stop buttons outside both port and stbd entrances  Gen 2 E-stop on LOP  E-stop for GT on woodward panel - AMMR  E-stop buttons for mains 1 & 2 in both PORT and STBD entrances  E-stop buttons for each main engine at the LOP in the ‘phone booth’ - GEN 3 Room  E- stop button outside each lower and upper entrances.  E-stop button on the Gen 3 LOP #11: know how to properly shift and inspect a s/w strainer; Turn the handle to the other strainer to shift. To inspect, loosen any wingnuts, bolts, ect, and look at the strainer. LOP / MCMS / MCU #1: How to pass MPDEs from remote to local control: On LOP in AMMR, press button labeled ‘local control’ to gain local control of the MPDE. A green light will illuminate next to the button. To return the MPDE to remote control, depress the same button (de-illuminating the light). The main must be idled (speed reduced to below 500 rpm) and de-clutched to pass from local to remote. #2: How to take proper readings from local control screens and navigate through each. Use touch screen at LOP in AMMR on the port side ‘phone booth’. Familiarity gained through multiple machinery rounds. #3: How to place MPDEs in’ready for operation’ mode IAW EOSS Line up s/w cooling and fuel service, and make sure safety interlocks ( Jacking Gear not engaged, Air flaps open, Ready for ops light illuminated, Turning gear secured,) are not engaged, complete blow downs #4: How to locate all MOVs for fuel oil, sea water, and compressed air for machinery equipment via MCMS: all MOVs for fuel oil, sea water, and compressed air are viewable in their respective sections within MCMS. There is only one MOV for the compressed air system controlled by MCMS. 4 #5: How to check alarms and reset on all above control panels: Check and reset alarms via MCMS, although some require acknowledgement at LOP Main Diesel Engines #1: What is the oil capacity of the lube oil service tanks? 100 gallons. #2: What are the locations to secure the MPDEs? - the local operating panel (LOP) - outside the main space (emergency secure) o trips the air flap handles, also sends signal to LOP - in ECR on the control panel - on the bridge and bridge wings - #3: What is the location of the fuel guillotine valves for the MPDEs? Across from the aft AFFF station. They are yellow handles and serve to cut off the fuel supply to each. #4: The safety interlocks for the MPDE: 1) air flaps – small red painted handles on each side of each MPDE, found forward on the MPDE 2) jacking gear cover – jacking gear facilitates the manual turnover of each engine. The gear and cover are on the centerline, aft end, of each MPDE. If the cover is missing, the MPDE will not start. 3) ready for operation on LOP 4) RED Gears on, and ready for operation 5) Locking pins on the RED gears not engaged. #5: Know components of MPDE (fuel filters, oil filters, coolers) Fuel filters: - 2 primary SEPAR coalescers on each MPDE (separates water from the fuel) - 8 secondary filters that separate any contaminates or particulate matter. - Fuel filter handles are yellow L/O filters: 4 ratcheting knife edge filters per MPDE - red handle - facilitates cleaning Lube Oil Centrifigual L/O filter for each main Piston coolers (3) for each main - fuel oil that cools the pistons Air coolers, next to the turbos Dispack filter for govenor #6: What purposes do the jacket water coolers serve?: 1) to allow salt water to cool the jacket water 2) to cool un-burnt fuel that is returning to the tank #7: What are air flaps and how are they reset after activation? Air flaps are emergency stop mechanisms that shut the air intake to the MPDE’s following activation of the emergency stop switch. They are reset by lifting the pin (which makes the red handle fall) then returning the handle to the horizontal position and releasing the pin. Releasing the pin locks the handle in place once again and the air flap is reset. #8: What is the location of the Jacket Water Head tanks? The jacket water head tanks are located in the AMMR uptake space. 5 #9: The air pressure required to start a MDE? 234-290 psi. #10: What is the location of the fuel and S/W MOVs? Aft of the mains in AMMR #11: What do the three indicator lights on the MTU ECS-UNI mean: 1) blinking green/yellow: system is communicating 2) solid green/yellow: operating/on 3) red (normally not lit): if lit indicates error. #12: What is the function and modes of the secondary fuel filters? The function of the secondary filter is to remove particulate matter. The modes of each are to utilize both, or turn the handle to isolate one for removal of the other for cleaning. #13: How to shift a fuel filter and sea strainer: for primary filter, shift 3-way directional handle to point towards filter desired for use. For secondary filter, handle points straight up to utilize both, or turned to point towards one or the other. To shift a sea strainer, unscrew locking wheel, then move selecting arm, and re-fasten locking wheel. #14: What are blow-in doors, location and purpose? blow-in doors are doors that open when the engines are not receiving enough intake air. They will open and allow unfiltered air to the mains. They are located in the uptake space of AMMR for the mains. #15: How and why to rotate knife edge filters on MPDEs: Rotating of the knife edge oil filters on the MPDE’s facilitates cleaning. It is done once every watch or every day, and occurs by a ratcheting motion. #16: How to fill a MPDE oil service tank: Open the feed valve on the head tank for the desired main to fill (located STBD aft of AMMR on the upper level), open valves next to L/O service tanks and fill via hand pump. Main Reduction Gears / Cross Connect Gear #1: Locations to disengage/engage clutches: 1) MCS5 in ECR 2) Port side AMMR ‘phone booth’ 3) In emergency – ‘control panel’ next to MRG/CCG LOP that facilitates manual clutching/de-clutching 4) On LOP #2: Locations of Sea water valves: MRGs: S/W valves on outboard sides, one inlet valve, one discharge valve, and a throttling valve after the discharge valve. CCG: Forward port side of AMMR (port side of CCG) #3: Know function and location of electric pumps and attached pumps associated with gears: Electric pumps: SERVICE pump – lubes gears/clutches – LARGER OF THE TWO PUMPS CONTROL pump – applies pressure when engaging *one of each for each R/G* 6 Attached pumps: one SERVICE (LARGEST PUMP) and one CONTROL pump that take over for electric pumps at certain shaft RPM (75-80 shaft RPM) Also an attached CPP pump CCG – Has one attached and one electric service pump. Control panel is lower level STBD AMMR bilge #4: Know the clutches and purposes for each: RED gear: - 60 clutch: low speed -47 clutch: high speed (CODAG mode) -66 clutch: connects output from BMDE’s together, or allows 1 engine to turn both shafts CCG: -SSS Clutch: engages with Gas Turbine #5: Four modes of the Synchronizing self-shifting (SSS) clutch 1) Baulked: safety mode, won’t engage, when clutch fails to engage 2) Ratcheting: not engaged, trying to match speed 3) Engaged: speeds have to match for this to occur 4) Locked: off, not engaged. #6: When and how to operate the air brakes on gears When performing PMS and shaft is desired not to move at all, HOW: press air brake buttons on the LOP for MRGs and LOP for CCG. There is also a manual operation valve to engage the air brakes. #7: What is the location and purpose of the bulkhead seal tank: The bulkhead seal tank is located forward of the CCG, on the bulkhead between AMMR and FMMR. The tank serves two purposes: lubricate/surround the GT shaft, and to maintain isolation between AMMR/FMMR during causalities. Practical Factors: #1: Align and place MRGs in remote operation: Ensure s/w cooling supply and return are open and active, ensure electric pumps are in remote, ensure that the LOP is ready for operation. #2: Navigate through the LOPs on the MRGs and CCG: Through the course of machinery rounds, gain familiarity through practice Controllable Pitch Propeller (CPP) #1: Explain how the CPP system works: Hydraulic pressure forces oil into one tube of a double tube (tube within a tube) and differential pressure of the hydraulic oil moves the blades in forward or reverse. #2: How do you manually control pitch: Depends on whether the OD box is functioning. If yes, secure all pumps locally except p3. Then, local control is available at each CPP unit by switching to local and selecting and holding over the emergency control I on the V12 switch. Once the pressure moves the blades on the propeller to forward propulsion, return v12 to ‘normal’ and toggle v9 switch to ‘increased’ position. Then use the V9 switch to change the hydraulic pressure. If OD box is not operational, select emergency control II on the V12 switch. V12 cannot be used as the manually connected hoses required are not present on board. #3: What is the location of the sea water valves: 7 Near each CPP, overhead, follow pipes from oil cooling if not sure. #4: What is the function and location of electric pumps and gear pumps associated with CPP? Large p1.1 and p1.2 pumps - service pressure pumps that provide all work until certain RPM reached - 70-80 shaft RPM reached, service pumps disengage, attached pumps on MRG take over. Small p3 static pump keep pressure on the prop hub #5: At what RPM do the electric pumps engage/disengage? Between 75-80 shaft RPM, #6: How do you check the oil level (Head Tanks and HOPM) The HOPM has a dipstick to check oil levels The head tank has a sight glass. #7: What is the location of the CPP head tanks? CPP head tanks are located in the AMMR uptake space #8: What are the modes for Emergency pitch and what is the purpose of the of the V9 static valve: Mode I: OD box intact, hold V12 on mode one until pressure increased to all ahead full. Then switch V-9 to ‘increased pressure’. Secure all pumps except for p3. Mode II: OD box not-intact, connect emergency hoses (not actually on board) #9: How do you manually operate boost pressure? There is a small twist knob outboard of the directional valve control assembly on each CPP. It must be twisted to manually operate boost pressure. Gas Turbine #1: What is the start sequence for the MPGT? #2: The safety interlocks for the MPGT: 1) the hydraulic starter – Aligned, ready for operation 2) cooling fan 3) Fuel Oil Conditioning Module (FOCM) 4) The Cross Connect Gear online (ensures LOSCA is operating) 5) CO2 suppression system active #3. How many pounds is the CO2 depression system for the MPGT and how is it activated? 200 lbs of CO2 and is activated several ways (additional 200lbs tanked present also for second blast): 1) MCMS 2) activation valves in red boxes next to sink in FMMR 3) activation directly from CO2 bottles 4) activation valves in red boxes in port p-way outside FMMR that are same as next to sink #4: What do the local gages on the FOCM indicate? pressure of fuel going to FOCM via the prefilters and coalescer #5: What are the reasons to motor the MPGT? 1) to do a water wash 8 2) to purge GT of fuel – after E-stop 3) to cool down the GT 4) purge smoke from the enclosure #6: How do you line up the cooling fan for startup? make sure the power is on and the system is in remote. #7: What are the steps required to line up the MPGT hydraulic start unit. 1) open S/W input and discharge valves 2) make sure panel is on, and in remote #8: How do you reset the FOCM? Reset FOCM by hitting the reset button on the LOP. #9: How do you respond to and clear alarms on the MPGT local panel? to respond to alarms and clear them in the MPGT local panel, hit the acknowledge button to silence it, and reset to reset it. Generators/Electrical Equipment: # 1: Where are the battery chargers located on each SSDG? The battery chargers for each SSDG are located under the aft generator side of each generator, and are blue or yellow in color. #2: Locations of shutdowns for each generator: Gen 1 – outside the entrance to AMR o in the VCHT room o on the LOP o the guillotine valves for each service tank. – in 36 passageway near MKCs room o MCMS – includes 5 min cooldown Gen 2 – outside both entrances to FMMR o in escape trunks o on the LOP o service tank guillotine valves – in 36 passageway near MKCs room o MCMS Gen 3 – outside lower and upper entrances to GEN 3 room - in the escape trunks - on the LOP - service tank guillotine valves – located outside upper entrance to Gen3 room, next to hatch leading to the fantail. - MCMS #3: How do you cross connect the #3SSDG with the firemain: Gen 3 is cross connected with the firemain by opening the emergency cross connect valve in gen 3 room #4: When placing the #3 SSDG online from local, what else needs to be placed online? #3 gen S/W cooling pump must also be placed online, it is located in #5 pump room #5: How do you acknowledge and reset alarms on the SSDG LOPs? 9 done by locating the digital display (to the right of the display normally used for taking round readings) and the button with a bell image on it. Press the bell once to silence the alarm, and twice to clear it. #6: The air pressure required to start a SSDG? 125 psi. #7: How often do the pre-lube pumps on the SSDG energize Automatically every 12 hours. They can be programmed for whatever the operator wants. #8: Know the alignment of the #3 SSDG Fuel system Gen3 has its own day tanks, so to properly align the system for running; both the supply and return valves must be opened. #9: How do you check for grounds on ground detection panels? To check for grounds on a ground detection panel, examine the lights displayed. There should be three green lights, if one is red, a ground is present. #10: How do you reset the fire alarm panel in ECR? Reset the fire alarm panel in ECR by opening the panel, pressing the acknowledge button followed by the reset button. #11: How do you check for a tripped breaker and how do you reset them? To check for a tripped breaker, use MCMS, or visually examine breakers at switchboard, if a breaker has any play in it, it has been tripped and needs to be reset. Turn it off, and then back on. #12: What is start block? is a display in MCMS that warns that another generator is needed in parallel in order to produce enough power to operate that piece of equipment. ( Bowthruster, and all three A/C units are on the start block system) #13: How do you reset fire alarm pull stations? To reset a fire alarm pull station, use the attached allen wrench to open the unit, then mechanically reset it. #12: What is the purpose of CAPAC, and what are you looking for when making a round of CAPAC? CAPAC is Cathodic Protection, it protects the ship from electrolysis. When making a round, make sure the metal brushes on the shaft are contacting the shaft just forward of the FWD Shaft bearing. #13: What is the location of fuel and S/W MOVs? For the gens, there is a supply and return mov for each ( 5-36-1&2-F), as well as 1 mov for the sea-chests #17: What is the max shore power AMPs? 2800 amps, 7 shore ties at 400 AMPS each. #18: How do you conduct a reset after load shed? The EOW will begin resets in MCMS, then the Machinery watchstander will work through a 3 page reset round checklist. #19: What is required to be reset after a power loss? Follow the steps on the reset check list. 10 Auxiliary Equipment: #1: How do you check the oil in the air compressor? Using the red handled dipstick, but switch to local operation and off first, lest oil be sprayed in thou face. #2: How do you blow-down an air compressor receiver? by opening two valves on the bottom of the receiver for only a few seconds, to remove any moisture. #3: At what pressure does The air service priority valve close? when the system air drops below 370 (325?) psi. Non-vital air systems are cut off. #4: How do you reset the AC units and what else needs to be online prior to reset? To reset the AC units, open the control panel, flip the top two toggle switches, secure the power handles, reset the top two toggle switches, turn the power handles back on, and close the panels. Prior to resetting, chill water, S/W cooling, and power need to be online. #5: What are the 2 different selector switches on a MOV? The different selector switches on an MOV designate between: local, remote, off, and the other switch selects between open and close. #6: How to Operate MOV locally: place selector switch in local, and depress open or close buttons. Without power, clutch-in the hand crank, then spin the wheel. #7: How many fuel oil service tanks are there and what equipment do they serve? - Service tanks 4-36-1 and 4-36-2 serve gens 1&2 as well as the gas turbine, the 80/81s, the 47s aux tanks for incinerator, and the boat fueling reels on the boat deck and fantail. - service tanks 4-64-1 and 4-64-2 serve the MPDEs - service tanks 1-81-1 and 1-80-0 serve GEN 3 #8: Where is the emergency firemain cross connect located for seawater? In AMR at the bottom of the entrance ladder #9 At what height does the fuel dump into the fuel OVFL tank? In the space FWD of the crew’s lounge, there is a common overflow pipe that fills after numerous other tanks overflow…This pipe extends vertically, and when the overflow fuel reaches a height of 15.4 feet, the high alarm goes off. At 15.7 feet, the high high alarm goes off. At ~16.4 feet, the overflow tanks begin to fill. Each overflow tank holds about 1500 gallons, so when both are full, the fuel will discharge overboard. #10: How do you reset the dump valve on the RO? Hold down the button on the RO LOPs touch screen. #11: How is the RO feed flow adjusted? By backing out the valve ( V-1) all the way (turn CCW) then slowly turning clockwise, being careful not to exceed 850psi. #12: What is the importance of insuring the crankcase heaters are on for the A/C compressors? They prevent the condensation from forming Practical factors: 11 #1: Demonstrate how to align and pump sewage for overboard discharge: Ensure that shore connection valve in VCHT room is closed, and that overboard valve is open. Ensure that overboard valve is open in void space within berthing. May be worth checking that the shore connection valve in the engraving room is also closed. Make sure that OVBD discharge is enabled in MCMS, otherwise it will not pump. #2: Align sea water and place steering gear in local and remote: Open the S/W supply valve, and the OVBD discharge valves. Turn to remote on the LOP #3: Place an RO unit online, and be able to switch potable water tanks: Activate 1 or both RO feed water pumps in lower level, port side aft AMMR. Use the touch screen to start the RO at the LOP, follow on screen instructions. To switch potable water tanks, find valves near potable water pumps. Open the closed valve first so that both are open, then close the desired one, leaving the tank desired to suck from open. General Knowledge:  Where are the activation points for GT CO2 fire suppression o outside port entrance, o at the CO2 bottles, stbd side upper level FMMR o Upper level port side next to deep sink.  Where are the last chance C/O valves for GT CO2 fire suppression o Upper FMMR STBD side near tanks on the overhead.  Where are the F/O service tanks, and what equipment do they serve? o 5-36-1 & 5-36-2 (36s) : Generators 1 and 2, Gas Turbine service, Gen 3 Daytanks, boat deck/fantail hose reel for small boat fueling. o 5-64-1 & 5-64-2 (64s) : Mains 1 and 2 service o 1-80-0 & 1-81-1 (80/81s) : Generator 3 day tanks o 1-47-1 & 1-47-3 (47s) : Incinerator  Where are the 10 guillotine valves located and what equipment do they connect to? o 2 on bulkhead aft of AFFF station 2: for the Mains o 2 on deck one, outside upper gen3 room entrance, next to fantail: for Gen 3 o 2 outside incinerator room on deck 1: for the 47s, service to the incinerator o 2 for STBD 36 tank in STBD 36-passageway next MKC’s room: service for gens 1,2 and GT o 2 for PORT 36 tank in PORT 36-passageway next to ‘HYDRUS’: service for gens 1,2 and GT  Where are the 5 remote activation boxes for the fire-pumps located? o #1 – outside hatch to bow thruster room o #2 – inside AMR vestibule o #3 – in passageway inboard of crew’s lounge. ~ 30 feet aft of port side FMMR entrance o #4 - outside port side AMMR entrance o #5 – on DC deck above scuttle leading down to scuttle entrance to #5 pump room  Where are the escape trunks located in AMR and where do they lead to? o 12  Where is the escape trunk located in FMMR and where does it lead to?  Where are the escape trunks located in AMMR and where do they lead to?  What installed system activation button is outside the entrance to each escape trunk? o Water-mist activation only o No emergency machinery securing buttons o AFFF activation button (only at GEN1)  What is the location of the fuel oil leak off tank control panel? o Port side lower AMMR near RO Feed-water pumps.  If you were a drop of fuel in the 64 service tanks for the MPDEs, where would you go in your path to the engine? o Leave 64 service tank o Through supply MOV o To SEPAR filter o To primary fuel pump o To secondary filters o To individual injector pumps (20 per main, 21 total fuel pumps per main, one is the low pressure gear driven feed pump) o To injectors o Into cylinder o Unburned/excess goes to the leakoff tank o Leaves leakoff tank by way of the leakoff pump o Passes through PCHE (jacket water coolers) o Passes through return MOV o Returns to 64 service tank.  At what vacuum pressure do the blow-in doors activate for the gens, mains, and GT? o Mains: 4.5 psi o GT: 8.5 psi o SSDGs: 2.5 psi  What are the stern tube cooling parameters o Maintain a pressure of 7psi o Differential pressure of 1 psi  Where is the hydraulic oil head tank for the bow thruster? o In the bos’n hole  Were are the segregation valves for deck connections for VCHT and Gray Water? o FMMR, and in engraver room  What button on the A/C unit shows what compressor is running? o System status 13  On MPDE LOP, what buttons must be lit before starting up or blowing down o Ready for operation o Local control o Turn engine (for blow down) o Start to start engine  Where are the four S/W cooling pumps located? o AMR o FMMR o AMMR o #5 Pump room (gen 3 s/w cooling pump, it is independent of others)  Where are the 4 OWT pumps located? o #2 – AMR STBD lower o #3 – FMMR STBD lower o #4 – AMMR STBD lower o #1 – stbd shaft alley  Where are the ballast / de-watering pumps and Main drainage eductor located? o Pump 1 – AMR o Main Drainage eductor – FMMR o Pump 2 – AMMR  How many air flaps are there on each main and each generator? o 2 on each.  When do MPDEs need to be blown down o After 24 hours offline, when off in high humidity, after E-Stop  What are the normal operating parameters for the S/W cooling pumps? 1025 gpm @50 psi  How many electric and gear pumps (attached) do the MRGs have? o Each RED gear has an electric service pump and electric control pump, as well as an attached service pump and attached control pump.  How many electric and attached pumps does the CCG have and what are their purpose? o There is one electric service pump and one attached service pump  Where are the grey water lift stations o Un-assigned space o AMR ( also has grey water transfer pumps 1 and 2) o #5 pump room (also has grey water transfer pumps 3 and 4)  How can you turn the shafts to lock them in place? o Use the turning gear. The turning gears are located on the forward end of each RED gear visible from catwalk looking at CCG LOP. The power control panels for each are in the bilges of AMMR. There is a smaller controller on the bulkhead next to the tiny hole leading to the escape trunks in AMMR. 14 This smaller controller allows FWD, REV selection, and holding down of a button to slowly rotate the shaft.  What tanks are located in the AMMR uptake space? o Jacket water head tanks o CPP head tanks  Where is the oil flow meter for the MRGs located? o Directly above where the shaft leaves the MRG and moves aft.  How do the MPDEs get pre-lubed? o Via the pre-lube pumps  What is the normal parameter range of the control oil and servo oil pressure for the REDgears? o Control oil – 300-390 psi o Service oil pressure – 16-84 psi  What jacket water temperature is considered uncontrollable on the Mains? o 194 Hi, 203 HiHi  Where is the air priority shut off valve located? o AMR, in front of the #1 switchboard on the overhead  What is the run time for a full Gen 3 day tank? o Depends on the load required. But in general, approximately 1% of the load burns about 1 gallon per hour. Each day tank is about 800 gallons.  Where are the stern Door HPU and controller located? o Port side steering gear room  What does DUF stand for? o Distilled unit feedwater  What does DUD stand for? o Distilled unit Discharge  What does GLO stand for? o GT lube oil  What does RLO stand for? o RED/CCG lube oil  What machinery does vital air supply? o CCG and RED gear brakes o All three generators start air o GT blow in doors o MPDE start and control air o GT shaft seal supply o Stern tubes o Blow in doors 15 o Boat wench o Rudder post seals  What does vital chill water serve? o LAN room o CIC o ECR o COM-MEES o ET/IT SHOP o 57 GUN CONTROL ROOM o CWIS  If the EOW wants to ‘top off’ GEN 3 diesel in the day tanks (80/81s), what does that mean and what needs to be done? o The 80/81 day tanks for gen 3 are supplied by the 36s, and there is one manually operated COV that needs to be opened prior to and after securing from fuel transfer. o This valve is located in the RO room on the starboard side forward, outboard of RO unit 1 on the ship’s hull.  What direction do the propulsion shafts turn? o They both turn inboard  What are the various uses for the Firemain besides the F/M? o Supply the AFFF system o Supply watermist system in an emergency o Charge main drainage eductor o Supply CMWD o Operate the chain locker eductor o Flush out the chain locker o Flush VCHT o Emergency S/W connection o Emergency GEN 3 S/W connection o CIWS and 57 Mag sprinklers o Trash compactor sprinklers o Decontamination shower  What do you do if you enter shaft alley and the shaft seal has failed and is flooding o Stop and lock propulsion shaft. o Connect hose from CO2 to shaft seal connection and activate CO2 o If CO2 fails, connect the hose to the ships service air on the aft bulkhead next to the seal o If ships air fails, the last chance option is to install the stern tube seal emergency packing gland  Located in metal box on the port side of R/O unit #2  Where is the zebra segregation valve for the fire main system? o Located in HYDRUS berthing ( first berthing area on port side fwd of the DC shop) it segragates fwd/aft F/M system  Where is the AFFF zebra segregation valve located? o It is an MOV directly above AFFF station 2 at about eye level. 16  What temperature does the jacket water have to be above for the Mains to start? o Above 40 deg. F, otherwise mains wont start.  When start air starts the mains, which bank on the engines does it compress to start? o B-bank of each main, or starboard side of each.  What equipment does the S/W Cooling system serve? o AC units 1,2,3 o GT HSU cooler o PORT and STBD RED gear coolers o Cross Connect Gear cooler o PORT and STBD CPP HOPM cooler o Line shaft bearings o Shaft seals o Steering Gear coolers o Reefers  Where are the 4 load transformers and load centers located? o L/C #1 – AMR, L/C upper level, transformer lower level, inboard of generator o L/C #2 – FMMR L/C upper level port side, aft of deep sink, transformer lower level STBD side near escape trunk o L/C #3 (VITAL L/C) – in passageway near ET/IT shop. L/C STBD side, transformer Port side next to HSCs state room. o L/C #4 (VITAL L/C) – both L/C and transformer in passageway area near ship’s office.  What are the parameters for the Generators o Rated max amperage: 2181 amps o Rated volts: 450 V o KW: 1360 o Frequency 60Hz o KV-Amps – 1700 NOTES 17