Lube Oil System Of GM Locomotive PDF
Document Details
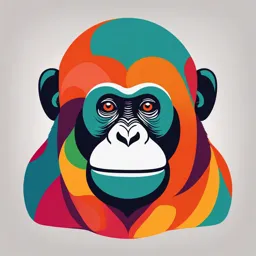
Uploaded by ImaginativePeachTree
STC/JHS
N.L.Sahu
Tags
Summary
This presentation details the Lube Oil System of a General Motors Locomotive. It covers topics such as the need for lubrication, various system components, and troubleshooting procedures, providing valuable insights into the mechanics of the system.
Full Transcript
By – N.L.Sahu /SI /STC/JHS. Content Need of lubrication Lube oil system of GM Locomotive Main Parts of lube oil system Scavenging and Soak Back system Main lubricating system Piston cooling oil system Engine protection devices Trouble shooting Need of Lubrication For free and smooth opera...
By – N.L.Sahu /SI /STC/JHS. Content Need of lubrication Lube oil system of GM Locomotive Main Parts of lube oil system Scavenging and Soak Back system Main lubricating system Piston cooling oil system Engine protection devices Trouble shooting Need of Lubrication For free and smooth operation of moving parts of engine Cooling of Bearings, Pistons, etc.. Protection of Metal surfaces from corrosion, rust, damage and wear. Keeps components clean and carbon free and prevents damage due to carbon deposition. Safety of engine, its components and their life span will largely depend on correct quality of oil at correct quantity and correct pressure which is maintained by the lube oil system. Lube Oil System of GM LOCO It is a combination of four separate systems – Scavenging system Soak back system Main lubricating system Piston cooling oil system Each system has its own oil pump. The main lubricating oil pump and piston cooling oil pump are both contained in same housing. The scavenging and soak back pumps are separate PUMP DISCHARGES MAIN: 867 LPM(7-8 KG AT 8TH NOTCH) PISTON COOLING: 413 LPM(5-6 KG AT 8TH NOTCH) SCAVENGING-1703 LPM SOAK BACK-11 LPM Soak – Back System To ensure lubrication of the turbocharger bearings prior to engine start, and the removal of residual heat from the turbo after engine shutdown, a separate lube oil pressure source is provided. This source is soak-back system. This pressure source is controlled automatically through the engine “start” and “stop” controls. A pressure relief valve, set at 32 psi, is located in the head of the soak back filter assembly. When the engine starts, and the motor driven soak back pump is still running, main lube oil pressure from the engine driven pump becomes greater than the motor driven soak back pump pressure. As there is no outlet for the lower pressure oil, the relief valve will open when the pressure builds up to 32 psi, and the oil will return to the engine oil pan through a passage in the filter head mounting flange. Also located in the filter head is a bypass valve, set at 70 psi. This valve will open to permit motor driven soak back pump pressure to bypass a plugged soak back filter element so that lubrication can continue to be supplied to the turbocharger (through the turbocharger filter) in order to prevent turbo damage. Scavenging System The scavenging oil pump takes oil through scavenging oil strainer from the oil sump. The pump then forces the oil through the michiana oil filters and oil cooler which are located near the engine. A by-pass valve is also provided parallel to michiana oil filter which is set at 40 psi differential pressure. Then oil passed to strainer housing from where it is supplied to Main Lube oil pump and Piston Cooling pump through a common suction pipe. Main Lubricating Oil System The main lubricating oil system supplies lube oil to most of the moving parts of the engine. The main pump takes oil from the strainer housing. Oil from the pump goes into the main oil manifold which is located above the crankshaft and extends the length of the engine. A relief valve is provided between pump and main manifold to limit maximum oil pressure. From main manifold oil then distributed with the help of branch pipe lines for lubrication at various parts of engine like main bearing, connecting rod bearing, vibration damper, crankshaft thrust bearings, governor, gear train at rear of the engine, turbocharger bearing and so on.. The minimum oil pressure is approximately 8-12 psi at idle and 25-29 psi at full speed. In the event of insufficient oil pressure, either a shutdown built into the governor or an EMDEC sensor will automatically protect the engine by shutting it down. Maximum pressure is determined by the relief valve setting. Accessory end Gear train Piston Cooling Oil System The piston cooling oil pump takes oil from a common suction with main lube oil pump. Then delivers oil to the two piston cooling oil manifolds extending the length of the engine, one on each side. A pipe at each cylinder directs oil through carrier to cool the underside of piston crown. Some oil enters into the oil grooves in the piston pin bearing and remaining oil drains to sump. Piston Cooling Oil System Engine Protection Devices (EPD) Crank – Case Pressure Shutdown switch When pressure inside the crank case reaches to a particular value , LW then CCPS switch S operates which CCP drains the governor S oil from governor to shutdown the engine. Low Lube Oil switch It is attached to governor and operates when the lube oil pressure drops to a particular value to shut down the engine. Hot Oil Detector It operates when the lube oil temperature reaches to 126°c to prevent engine from damage. Located on outlet elbow from the main lube oil pump HOD Trouble - Shooting When an engine is reported as having low oil pressure the following steps should be taken - : Check the engine lube oil level, add if low. Check lube oil viscosity. Note down water and oil temperature. Check and clean strainer of strainer housing. Check for suction leaks. Check and change the turbocharger oil filter element. Remove all crankcase covers inspect the piston pin and external surfaces of connecting rod for sign of overheating or loose components.