Lecture 7 Transducers and Sensors PDF
Document Details
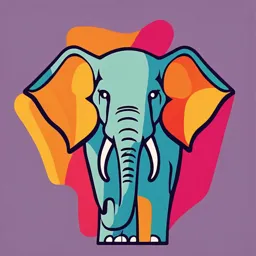
Uploaded by SnappyTopology7034
Cavite State University
Engr. Rhodonelle S. Duatin
Tags
Summary
This lecture covers transducers and sensors, including their classifications, working principles, and various types. It discusses examples and parameters of different transducer types, emphasizing their applications in diverse fields.
Full Transcript
LESSON 6. TRANSDUCERS Intended Learning Outcomes After the completion of the chapter, students will be able to: 1. Discuss basic working principle and building blocks of transducers. 2. Familiarize different classification of transducers and their area of functionality. Introduction to Tra...
LESSON 6. TRANSDUCERS Intended Learning Outcomes After the completion of the chapter, students will be able to: 1. Discuss basic working principle and building blocks of transducers. 2. Familiarize different classification of transducers and their area of functionality. Introduction to Transducers and Sensors A transducer is a device which transforms a non-electrical physical quantity (i.e. temperature, sound, or light) into an electrical signal (i.e. voltage, current, capacity…) A transducer is made of three blocks: Input, Sensor, Output Sensor is a device that converts a physical parameter to an electrical output Sensor normally senses position, forces, distance, strain, vibration, temperature, temperature, acceleration, etc. COURSE: ECEN85 – ELECTRONIC SYSTEMS AND DESIGN PREPARED BY: ENGR. RHODONELLE S. DUATIN The difference between sensors and transducers is: Sensors are devices which mainly sense anything and give output in any desired form; whereas transducers are devices that transform one form of energy in to another form, yielding a detectable output. Example of Sensor: A thermal sensor is a device which senses heat energy and a photo sensor is a device which senses light. Example of Transducer: A TV Antenna is a transducer where electromagnetic energy is transformed and reproduce in to electrical energy. Important Parameters of Transducer Static Response: how does it respond to slowly variable signals is it precise and accurate Dynamic Response: how does it respond to quickly variable signals Environmental factors: how these factors are affecting transducer performance Reliability Classification of Transducers a. PASSIVE This transducer requires an external power, and their output is measure of some variation, such as resistance or capacitance. Example of passive transducer: LDR, speaker, microphone, thermistor b. ACTIVE OR SELF-GENERATING These transducers do not require an external power, and they produce electrical output (such as voltage) when triggered by some form of non-electrical energy. The physical quantity like velocity, temperature, force and the intensity of light is induced with the help of the transducer. The piezoelectric crystal, photo-voltaic cell, tacho generator, thermocouples, photovoltaic cell are the examples of the active transducers. Displacement Transducer Passive type transducer Convert certain movement into some electrical signal variation It is concerned with the measurement of the amount by which some object has been moved. Example is rotating the control knob of potentiometer, varies its equivalent resistance. Inductive Transducer Self-generating type transducer Utilize the basic electrical generator principle that when there is relative motion between conductor and magnetic field, a voltage is induced in the conduction (generator action) Example: tachometer (inductive transducer that directly converts speed or velocity into an electrical signal) COURSE: ECEN85 – ELECTRONIC SYSTEMS AND DESIGN PREPARED BY: ENGR. RHODONELLE S. DUATIN Piezoelectric Transducer Self-generating type transducer A device that uses the piezoelectric effect to measure changes in acceleration, pressure, strain, temperature or force by converting this energy into an electrical charge. When we squeeze this piezoelectric material or apply any force or pressure, the transducer converts this energy into voltage. This voltage is a function of the force or pressure applied to it. In this way, physical quantities like mechanical stress or force can be measured directly by using a piezoelectric transducer. The only disadvantage of this transducer is that a voltage will be generated only as long as the pressure applied to the piezoelectric element is changing. Advantage of Piezoelectric transducer No need for an external force Easy to handle and use as it has small dimensions High-frequency response it means the parameters change very rapidly Disadvantage of Piezoelectric transducer It is not suitable for measurement in static condition It is affected by temperatures The output is low so some external circuit is attached to it It is very difficult to give the desired shape to this material and also desired strength Temperature Transducer Passive and Self-generating type transducer A device that converts the thermal quantity into any physical quantity such as mechanical energy, pressure and electrical signals etc. COURSE: ECEN85 – ELECTRONIC SYSTEMS AND DESIGN PREPARED BY: ENGR. RHODONELLE S. DUATIN For example, in a thermocouple the electrical potential difference is produced due to temperature difference across its terminals. So, thermocouple is a temperature transducer. Main Features of Temperature Transducer The input to them are always the thermal quantities They generally convert the thermal quantity into electrical quantity They are usually used for the measurement of the temperature and heat flow Four main categories of Temperature Transducer a. Resistance Temperature Detector (RTD) – passive type b. Thermocouples – self-generating type c. Thermistors – passive type d. Ultrasonic Transducers – passive type Resistance Temperature Detector (RTD) An electronic device used to determine the temperature by measuring the resistance of an electrical wire. This wire is referred to as a temperature sensor. If we want to measure temperature with high accuracy, an RTD is the ideal solution, as it has good linear characteristics over a wide range of temperatures. In RTD devices; Copper, Nickel and Platinum are widely used metals. These three metals are having different resistance variations with respective to the temperature variations. Platinum has the temperature range of 650 °𝐶, and then the Copper and Nickel have 120 °𝐶 and 300 °𝐶 respectively. The construction is typically such that the wire is wound on a form (in a coil) on notched mica cross frame to achieve small size, improving the thermal conductivity to decrease the response time and a high rate of heat transfer is obtained. In the industrial RTD’s, the coil is protected by a stainless-steel sheath or a protective tube. Thermocouples In the year 1821, a physicist namely “Thomas Seebeck” revealed that when two different metal wires were linked at both ends of one junction in a circuit when the temperature applied to the junction, there will be a flow of current through the circuit which is known as electromagnetic field (EMF). The energy which is produced by the circuit is named the Seebeck Effect. One of the most commonly used methods of measuring temperature in science and industry depends on the thermocouple effect. COURSE: ECEN85 – ELECTRONIC SYSTEMS AND DESIGN PREPARED BY: ENGR. RHODONELLE S. DUATIN Usually constructed of two different wire metals that are joined together at one end, a temperature difference between the wires. o Seebeck Effect: “The voltage produced in a thermocouple is proportional to the temperature between the two junctions.” The junction of the two wires of the thermocouple is called the sensing junction (hot junction). In practice, one metal is kept at a constant temperature, and it is called reference junction or the cold junction. Because the other metal is exposed to a higher temperature, thus thermocouple is frequently used for measuring high temperatures. Thermocouples are made from a number of difference metals or metal alloys covering a wide range of temperatures from as low as 270 °𝐶 (−418 °𝐹) to as high as 2700℃ (𝑎𝑏𝑜𝑢𝑡 5000℉) Thermocouples are based on the Seebeck effect, i.e. a small thermoelectric current is generated when two different metal wires are put into contact at both ends with their junctions having a different temperature. Thermopile – it is characterized by a number of thermocouples connected in series, intended to increase the sensitivity and accuracy of the sensor especially in measuring very low temperature. Applications: o Engineering – to monitor the operating temperatures of electrical and mechanical equipment o Industrial processes – to monitor temperatures of liquids and gases in storage and flowing in pipes and ducts o Medical work – to measure internal body temperatures. Thermistors A thermistor (or thermal resistor) is defined as a type of resistor whose electrical resistance varies with changes in temperature. Although all resistors’ resistance will fluctuate slightly with temperature, a thermistor is particularly sensitive to temperature changes. Thermistors act as a passive component in a circuit. They are an accurate, cheap, and robust way to measure temperature. While they do not work well in extremely hot or cold temperatures, they are the sensor of choice for many different applications. They are ideal when a precise temperature reading is required. COURSE: ECEN85 – ELECTRONIC SYSTEMS AND DESIGN PREPARED BY: ENGR. RHODONELLE S. DUATIN This device has negative temperature coefficient. o Their resistance decreases as their temperature rises The working principle of a thermistor is that its resistance is dependent on its temperature. We can measure the resistance of a thermistor using an ohmmeter. If we know the exact relationship between how changes in the temperature will affect the resistance of the thermistor – then by measuring the thermistor’s resistance we can derive its temperature. Applications: Digital Thermometers (Thermostats), Circuit Protection, Rechargeable Batteries (ensure battery temperature is maintained), wheatstone bridge circuits Ultrasonic Transducer Ultrasonics, which is sound vibrations above 20, 000 Hz, can be useful when we are concerned with: o Rapid temperature fluctuations o Temperature extremes o Limited access, nuclear o And other sever environmental conditions o And when we must measure the temperature distribution inside solid bodies These transducers send the electrical signals to the object and once the signal strikes the object then it reverts to the transducer. These transducers use ultrasonic waves for the measurement of a few parameters. These are mainly used in measuring distance applications. Working Principle of Ultrasonic Transducer: When an electrical signal is applied to this transducer, it vibrates around the specific frequency range and generates a sound wave. These sound waves travel and whenever any obstacle comes, these sound waves will reflect the transducer inform of echo. And at the end of the transducer, this echo converts into an electrical signal. Here, the transducer calculates the time interval between the sending of the sound wave to the receiving the echo signal. These transducers are better than the infrared sensors because these ultrasonic transducer/sensors are not affected by the smoke, black materials, etc. Ultrasonic sensors exhibit excellence in suppressing background interference. Ultrasonic transducers are mainly used for finding the distance by using ultrasonic waves. The distance can be measured by the following formula. 1 𝐷 = ∗ 𝑇 ∗ 𝐶 𝑤ℎ𝑒𝑟𝑒 2 D (distance), T(time difference between sending & reception of ultrasonic waves), C (sonic speed) COURSE: ECEN85 – ELECTRONIC SYSTEMS AND DESIGN PREPARED BY: ENGR. RHODONELLE S. DUATIN Photoelectric Transducer Passive and Self-generating type transducer The photoelectric transducer can be defined as, a transducer which changes the energy from the light to electrical. It can be designed with the semiconductor material. This transducer utilizes an element like photosensitive which can be used for ejecting the electrons as the light beam soak ups through it. The electron discharges can change the photosensitive element’s property. Therefore, the flowing current stimulates within the devices. The flow of the current’s magnitude can be equivalent to the whole light absorbed with the photosensitive element. This transducer soak ups the light radiation which drops over the semiconductor material. The light absorption can boost the electrons in the material, & therefore the electrons begin to move. The electron mobility can generate three effects like o The material resistance will be changed. o The semiconductor’s output current will be changed. o The semiconductor’s output voltage will be changed. Three main categories: o Photoemissive – passive type o Photoconductive – passive type o Photovoltaic – self generating type Photoemissive Transducer Radiation falling on a cathode causes electrons to be emitted from the cathode surface. Example: LED and LASER Photoconductive Transducer Resistance of a material is changed when it is illuminated. Example: Photodiode and LDR Photovoltaic Transducer Can generate an output voltage proportional to radiation intensity The photovoltaic cell, or “solar cell”, as it sometimes called, will produce an electric current when connected to a load. Both silicon (Si) and selenium (Se) types are known. Factors in Selecting a Transducer Operating Range Sensitivity Frequency Response and Resonant Frequency Environmental Compatibility COURSE: ECEN85 – ELECTRONIC SYSTEMS AND DESIGN PREPARED BY: ENGR. RHODONELLE S. DUATIN Minimum Sensitivity Accuracy Usage and Ruggedness Electrical Position/Proximity Sensor Passive type transducer Usually used to determine when an object has moved to within some particular distance of the sensor. Application: o Collision detection o Detection of presence/absence of an object o Metal or non-metal detection o Industrial manufacturing applications: packaging, parts sorting, etc. Ultrasonic Sensor In industrial applications, ultrasonic sensors are characterized by their reliability and outstanding versatility. Ultrasonic sensors can be used to solve even the most complex tasks involving object detection or level measurement with millimeter precision, because their measuring method works reliably under almost all conditions. Passive Infrared Sensor (PIR Sensor) A passive infrared sensor (PIR sensor) is an electronic sensor that measures infrared (IR) light radiating from objects in its field of view. They are most often used in PIR-based motion detectors Temperature Sensor It provides a voltage output that is linearly proportional to the Celsius temperature. The output voltage can be converted to temperature easily using the scale factor of 10 𝑚𝑉/℃ COURSE: ECEN85 – ELECTRONIC SYSTEMS AND DESIGN PREPARED BY: ENGR. RHODONELLE S. DUATIN Speed Sensor Speed sensors are machines used to detect the speed of an object, usually a transport vehicle. Blind Spot Monitor A blind spot monitor is a vehicle-based senso device that detects other vehicles located to the driver’s side and rear. Warnings can be visual, audible, vibrating. It can also include “cross traffic alerts”. Radar Gun A radar speed gun is a device used to measure the speed of moving objects. It is used in law-enforcement to measure the speed of moving vehicles and is often used in professional spectator sport, for things such as the measurement of bowling speeds in cricket, speed of pitched baseballs, athletes and tennis serves. A radar speed gun is a doppler radar unit that may be hand-held, vehicle-mounted or static. It measures the speed of the objects at which it is pointed by detecting a change in frequency of the returned radar signal caused by the Doppler effect, whereby the frequency of the returned signal is increased in proportion to the object’s speed of approach if the object is approaching, and lowered if the object is receding. Water Sensor The Water in Fuel Sensor or WiF sensor indicates the presence of water in the fuel. It is installed in the fuel filter and when the water level in the water separator reaches the warning level, the WiF sends an electrical signal to the ECU or to dashboard (lamp). COURSE: ECEN85 – ELECTRONIC SYSTEMS AND DESIGN PREPARED BY: ENGR. RHODONELLE S. DUATIN Oxygen Sensor An oxygen sensor (or lambda sensor) is an electronic device that measures the proportion of oxygen (𝑂2 ) in the gas or liquid being analysed. Other Sensors Vision and Imaging Sensors - electronic devices that detect the presence of objects or colors within their fields of view and convert this information into a visual image for display Radiation Sensors - electronic devices that sense the presence of alpha, beta, or gamma particles and provide signals to counters and display device Particle Sensors - electronic devices used to sense dust and other airborne particulates and supply signals to the inputs of control or display devices Motion Sensors - electronic devices that can sense the movement or stoppage of parts, people, etc. and supply signals to the inputs of control or display devices. Metal Sensors - electronic or electro-mechanical devices used to sense the presence of metal in a variety of situations ranging from packages to people Level Sensors - electronic or electro-mechanical devices used for determining the height of gases, liquids, or solids in tanks or bins and providing signals to the inputs of control or display devices Leak Sensors - electronic devices used for identifying or monitoring the unwanted discharge of liquids or gases Humidity Sensors - electronic devices that measure the amount of water in the air and convert these measurements into signals that can be used as inputs to control or display devices Gas and Chemical Sensors - fixed or portable electronic devices used to sense the presence and properties of various gases or chemicals and relay signals to the inputs of controllers or visual displays Force Sensors - electronic devices that measure various parameters related to forces such as weight, torque, load, etc. and provide signals to the inputs of control or display devices Flow Sensors - electronic or electro-mechanical devices used to sense the movement of gases, liquids, or solids and provide signals to the inputs of control or display devices Flaw Sensors - electronic devices used in a variety of manufacturing processes to uncover inconsistencies on surfaces or in underlying materials such as welds Flame Sensors - optoelectronic devices used to sense the presence and quality of fire and provide signals to the inputs of control devices COURSE: ECEN85 – ELECTRONIC SYSTEMS AND DESIGN PREPARED BY: ENGR. RHODONELLE S. DUATIN Electrical Sensors - electronic devices that sense current, voltage, etc. and provide signals to the inputs of control devices or visual displays Contact Sensors - any type of sensing device that functions to detect a condition by relying on physical touch or contact between the sensor and the object being observed or monitored Non-Contact Sensors - devices that do not require a physical touch between the sensor and the object being monitored in order to function COURSE: ECEN85 – ELECTRONIC SYSTEMS AND DESIGN PREPARED BY: ENGR. RHODONELLE S. DUATIN