Turbine Cooling Methods PDF
Document Details
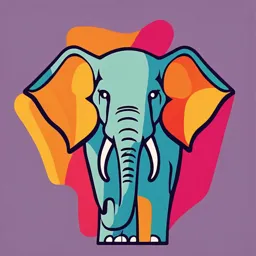
Uploaded by RazorSharpPeach9159
Shoubra Faculty of Engineering
Tags
Summary
This document provides an overview of turbine cooling methods. It explores different approaches for cooling turbine blades and components, including external and internal cooling techniques. The document also examines the design considerations and factors affecting the effectiveness of these cooling methods.
Full Transcript
Axial turbine blade cooling Methods of blade cooling First-stage nozzle vane of an advanced gas turbine First-stage blade of a typical high temperature first-stage blade. Liquid cooling:- Apart from the use of spray cooling for thrust boosting in turbojet engines, the liquid systems have...
Axial turbine blade cooling Methods of blade cooling First-stage nozzle vane of an advanced gas turbine First-stage blade of a typical high temperature first-stage blade. Liquid cooling:- Apart from the use of spray cooling for thrust boosting in turbojet engines, the liquid systems have not proved to be practicable in modern turbofan engines. There are difficulties associated with channeling the liquid to and from the blades. Air cooling:- only method used successfully in production engines has been internal, forced convection, air cooling. With 1.5-2 per cent of the air mass flow used for cooling per blade row, the blade temperature can be reduced by between 200 and 300°C. Using current alloys, this permits turbine inlet temperatures of more than 1650 K Cooled turbine rotor blade A typical distribution of cooling air required for a turbine stage designed to operate at 1500 K might be as follows; the values are expressed as fractions The cooled turbine of the entry gas mass flow: Distribution required for operation at 1500 K The cooled turbine - methods Air cooling is divided into the following methods Techniques to cool rotor blade – external cooling Film cooling Transpiration cooling – internal cooling The cooled turbine - methods Stator cooling – Jet impingement cools the hot leading edge surface Techniques to cool stator blade of the blade. – Spent air leave through slots in the blade surface or in the trailing edge Cooling performance parameter in common use is the blade relative temperature defined by:- The coolant temperature, Tcr, will usually be the compressor delivery temperature, and will increase significantly as pressure ratio is raised to reduce specific fuel consumption. The effect on the cycle efficiency of losses incurred by the cooling process: (a)There is a direct loss of turbine work due to the reduction in turbine mass flow ” can be incorporated directly into any cycle calculation”. (b) The expansion is no longer adiabatic; and furthermore there will be a negative reheat effect in multi-stage turbines. (c) There is a pressure loss, and a reduction in enthalpy, due to the mixing of spent cooling air with the main gas stream at the blade tips. (This has been found to be partially offset by a reduction in the normal tip leakage loss.) (d) Some ‘pumping’ work is done by the blades on the cooling air as it passes radially outwards through the cooling passages. (e) When considering cooled turbines for cycles with heat-exchange, account must be taken of the reduced temperature of the gas leaving the turbine which makes the heat-exchanger less effective ” can be incorporated directly into any cycle calculation”. Film Cooling Film cooling is the process of bleeding relatively cool air from the compressor, ducting the cooling air to the turbine blades, and discharging the air through small holes in the blade walls. Film cooling is employed on all surfaces of the airfoil, including the pressure and suction surfaces, blade tips, platforms and endwalls of static turbine Details of turbine blade cooling features vanes Factors affecting turbine film cooling Comparison of cooling hole designs Illustration of surface and leading edge cooling Internal Cooling Coolant air extracted from the compressor first cools the internals of the structure prior to exiting the film cooling holes on the airfoil, or exiting the trailing edge or cooling or dirt purge holes at the tip of the airfoil. The primary methods employed in modern turbine airfoils are jet impingement, serpentine (often turbulated) passages, pin fins and trailing edge slots. In modern turbine airfoil cooling designs, these internal cooling passages are typically used in conjunction with one another, in series. The leading edge is typically cooled via impingement cooling, the midchord region is cooled via serpentine passages and the latter portions of the internal structure are cooled via pin fins and trailing edge slots. Jet impingement: Jet impingement cooling, as discussed above, is employed to cool the inside surface of the leading edge of turbine airfoils. Illustration of an impinging jet and impingement cooling of a leading edge Serpentine passages and ribbed turbulators: The center sections of the internal structure of a turbine airfoil are most commonly cooled using serpentine passages. These passages include ribs, or turbulators, in order to enhance the convective heat transfer coefficients, allowing the cooling air to transport more heat away from the walls. Serpentine passage with ribbed turbulators Pin fins: Pin fins are round (or other shaped) projections near the aft portion of the inside of the turbine airfoil structure oriented perpendicular to the flow which conduct heat from the surfaces (pressure and suction surfaces of the turbine airfoil) and are convectively cooled by the internal cooling flow prior to the flow exiting the trailing edge of the structure. Illustration of pin fin cooling system