Landing Gear.docx
Document Details
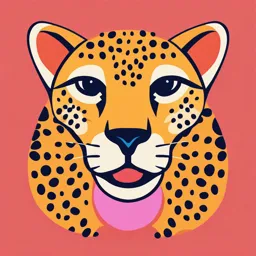
Uploaded by PhenomenalNumber
Full Transcript
2A-32-10: General Landing Gear The Main Landing Gear (MLG) and Nose Landing Gear (NLG) provide structural support for the aircraft as well as energy absorption during landing. The aircraft features atraditional tricyde gear arrangement. The landing gear system includes: gear and door indication, el...
2A-32-10: General Landing Gear The Main Landing Gear (MLG) and Nose Landing Gear (NLG) provide structural support for the aircraft as well as energy absorption during landing. The aircraft features atraditional tricyde gear arrangement. The landing gear system includes: gear and door indication, electrical landing gear control including Weight-On-Wheels CNQW) processing, Steer-by-Wire, Brake-by-Wire (BBW), a parking brake (PARK BRAKE) and Tire Pressure Monitoring System (TPMS). The mainlanding gear use conventional oleo-pneumatic shock struts.The nose landing gear shock strut is a dual-stage shock strut designed to provide damping under light aircraft weights. The nosewheel steering unit can be disconnected manually, without the use of tools, for towing purposes. The landing gear is primarily manufactured from high-strength steel and aluminum materials. The struts are designed to be highly efficient for absorbing the aircraft's kinetic energy under dynamic load conditions and provide energy dissipation with controlled rebound characteristics. The internal design includes a metering pinand orifice which causes a restriction of fluid ftOIN. This restriction creates the rate of compression. Normal extension and retraction of the landing gear is electrically-controlled and hydraulically-actuated by the left hydraulic (primary) system.If the left system Engine-Driven Pump (EDP) fails or if the left engine is shut down,the gear may be operated normally by utilizing the hydraulic Power Transfer Unit (PTU) or Auxiliary (AUX) system. The gear may also be extended through the use of the emergency gear extension system, which supplies pneumatic pressure to extend the gear (see Figure 1. Simplified Landing Gear Hydraulic System Diagram). Landing gear position indicators and an audiblewarning system are incorporated to provide positive indications of the position of the landing gear.A WOW system is induded in the landing gear system, to furnish "ground" or "air" mode reference signals to various aircraft systems during ground maintenance. Each gear incorporates three actuators (retraction I extension, uplock release / locking, door opening I closing) for movement. A Landing Gear Control Maintenance Panel is provided to operate the gear doors for preflight purpose and landing gear and door operation for maintenance functions. The landing gear system is divided into the following subsystems: 2A-32-20: Landing Gear and Doors System 2A-32-30: Extension and Retraction System 2A-32-40: Wheels and Brakes System 2A-32-50: Nose Wheel Steering System 2A-32-60: lire Pressure Monitoring System Figura 1.Simplified Landing Gear Hydraulic System Diagram ® SHUTOFF VALVE ELECTRICAL CONTROUSHUTOFF VALVE Q CONTROLJSHUTOFF VALVE RV REPEATER VALVE 0 CHECK VALVE LSYS R SYS LEFT AUX I PTU NITROGEN TIL 006186 2A-32-20: Landing Gear and Doors System General Description: The major components of each main landing gear assembly are: landing gear door, shock strut, sidebrace actuator I downlock mechanism and uplock mechanism. Each main landing gear assembly has dual wheels with integrated brakes mounted on an articulated trailing arm attached to the landing gear structural post. The hydraulic shock strut is attached between the wheel end of the articulated trailing arm and the top of the structural post. In flight with the landing gear down, the shock strut extends and the articulated trailing arm pivots downward, positioning the wheels for ground contact and compression of the shock strut. The major components of the mainlanding gear are shown in Figure 2. Main Landing Gear Components and Figure 3. Main Landing Gear Structure. The nose gear strut provides mounting provisions for the steering package, two nose wheels I tires, tie down ring, hydraulic lines, wiring harnesses, uplock roller, Weight-On-Wheel s 0NQW) sensors and a fixed jack pad. See Figure 4. Nose Landing Gear Components. The strut is locked in the extended position by a folding truss brace with a spring-loaded mechanical overcenter linkage. Internal centering cams are incorporated in the shock strut to center the nosewheels and retainthe wheels in the neutral position during extension or retraction or at any other time the strut is fully extended with no weight on wheels. A rotary steering unit is mounted to the strut outer cylinder concentrically and attached to the swiveling piston through a pair of torque arm scissors. Indication of landing gear position is provided to the flight crew through lights onthe landing gear control panel,an aural warning horn and by messages on the Crew Alerting System (CAS) in the event of malfunction. Description of Subsystems, Units and Components: Nose Landing Gear Components: The nose landing gear assembly consists of a separate trunnion supporting a cantilever dual-stage oleo shock strut with dual wheels. Further support is gained by a drag brace, which is attached to the lower end of the strut outer cylinder and to the fuselage at the aft end of the wheel well.The trunnion is mounted to the fuselage on a pivot axis that permits retraction of the nose wheels and strut, forward and up into the nose wheel well.Extension is aft and down. Nose Landing Gear Strut: (See Figure 5. Nose and Main Landing Gear Strut X Dimensions.) The nose landing gear strut is a dual-stage configuration with separate nitrogen and hydraulic chambers. The strut assembly is fitted with a dual-wheel axle. It is designed to absorb the shock of taxiing, takeoff and landing. It is essentially a steel piston riding in a cylinder, which utilizes ring seals to prevent fluid leakage. The dual-stage strut provides damping at light aircraft weights. The strut contains two different stages of compression. The lower portion of the strut is the first stage of compression; the upper portion of the strut is the second stage of compression. The reason for the dual stage is to reduce the landing loads based on the CG envelope. The strut uses a metering pin designed to reduce airframe loads by minimizing the vertical load factor onlanding. Individual air and oil filler valves are provided at the top and bottom of the shock strut for servicing. The shock strut, when compressed, is filled to overflowing with MIL-H-5606 or MIL-H-83282b hydraulic fluid and pressurized with dry nitrogen to proper specifications. Note Refertothe Aircraft Maintenance Manual (AMM) for proper strut servicing procedures. Nose Landing Gear Actuator: The nose landing gear actuating cylinder is attached to the aircraft structure and the nose landing gear trunnion. It retracts to raise the gear and extends to lower the gear. Nose Landing Gear Torque Links: The nose landing gear torque links provide a connection for the nosewheel steering mechanical input to the NLG tires for steering. The torque links should be disconnected for towing, which allows for a full 360° rotation of the nose wheels. Nose Landing Gear Trunnion: The nose landing gear trunnion is a truss design that connects the strut assembly to the fuselage. It provides attachment for the landing gear actuator and overcenter downlock mechanism. Nose Landing Gear Downlock Mechanism: The nose gear unlock mechanism consists of a folding forward and aft truss brace, spring loaded overcenter linkage, suitcase-type springs, hydraulic unlock actuator and incorporates two downlock proximity switches. The forward and aft truss braces provide the supports, which locksthe noselanding gear in the extended position. The overcenter linkage is unlocked from the overcenter position by the hydraulic unlock actuator during the retraction. VVhen hydraulic power is not applied to the downlock actuator, the overcenter linkage is maintained overcenter by the suitcase-type springs and gear safety pin (see Figure 6. Landing Gear Safety Pins). The linkage is locked approximately 0.250 inch overcenter. During ground operations, the ground safety pin should be installed in the overcenter linkage to prevent inadvertent collapse of the nose gear. The safety pinis designed to withstand full retract hydraulic pressure. Nose Landing Gear Drag Brace: The nose landing gear drag brace provides additional support and is attached to the fuselage structure at the aft end of the nose wheel well and nose landing gear strut. The drag brace forces the nose landing gear up and forward during retraction. Main Landing Gear Components: The main landing gear structural post and trunnion are attached with two trunnion pinsto the airframe atthe wingtrunnion mount. Thetrunnion pins have a fuse section to aid in landing gear breakaway in the event of an overtoad duringlanding. The structural post and trunnion provide mounting for the mooring ring, trailing arm pivot, main landing gear fairing door, mainlanding gear shock strut, wire harness and hydraulic lines. Main Landing Gear Strut: (See Figure 5. Nose and Main Landing Gear Strut X Dimensions.) Each shock strut is a conventional nitrogen hydraulic unit designed to absorb the shock of taxiing, takeoff and landing.It is essentially a steel piston riding in a cylinder and utilizing ring seals to prevent fluid leakage between the piston and the outer cylinder. It is mounted on the upper aft side of the structural post and attaches to the axle fitting assembly (trailing arm). An air/oilfiller valve is provided at the top of the shock strut and is used for strut servicing. The shock strut, when compressed, is filled to overflowing with MIL-H-5606 or MIL-H-832828 hydraulic fluid and is pressurized with dry nitrogen to the proper extension. Note Refer to the Aircraft Maintenance Manual (AMM) for proper strut servicing procedures. Main Landing Gear Sidebrace Actuator: The main landing gear sidebrace actuator provides structural support when the gear is down, as well as hydraulic extension and retraction of the main landing gear. The main landing gear downlock mechanism is an internal component of the sidebrace actuator. Four segments mechanically extend with the sidebrace actuator fully extended. The segments mechanically lock the sidebrace actuator in the extended position and also activate the main gear downlock switch (which signals both proximity sensors). A spring internal to the sidebrace provides positive locking tension when hydraulic pressure is depressurized. The sidebrace actuator features internal snubbing on the retract stroke for quiet operation. There is no internal snubbing on the extension stroke (to ensure gear extension). Main Landing Gear Trailing Arm I Axle Assembly: The main landing gear trailing arm provides pivot and attachment to the structural post, main landing gear axle, brake single pin torque takeout mount point and lower attachment for the main landing gear shock strut. On the bottom of the trailing arm between the axles is a jack pad which provides stability and support during tire and brake changes. 3. Limitations: See nose and main landing gear strut tables referenced in Figure 5. Nose and Main Landing Gear Strut X Dimensions. Figure 2. Main Landing Gear Components MAIN LANDING GEAR CONTROL VALVE (1 EACH DOOR, GEAR, DUMP VALVE) MAIN LANDING GEAR DOOR OPEN SENSORS SHUTTLE VALVES UPLOCK HOOK I ACTUATOR MAIN LANDING GEAR DOOR CLOSED SENSORS SIDEBRACE ACTUATOR UPLOCK ROLLER TIL-002526 Figure 3. Main Landing Gear Strudure TRUNNION ASSEMBLY SIDE BRACE ACTUATOR STRUCTURAL POST UPLOCK ROLLER AXLE FITTING ASSEMBLY (TRAILING ARM) SHOCK ABSORBER TIL-002527 OEM Provided Data Landing Gear Revision 4 2017-30 2A-32-00: B of 72 Figure 4. Nose Landing Gear Components TRUNNION ASSEMBLY NG ACTUATOR DOWNLOCK ACTUATOR AND SUITCASE SPRINGS TAXI LIGHTS (LEFT I RIGHT I CENTER) NG SCISSORS UPLOCK ROLLER TIL-002528 Figure 5. Nose and Main Landing Gear Strut X Dimensions Sl1'JT ST1'0l<E STATIC "X' PRES9URE (ttCHE8) M,O. 1.03 (..CHES) 12.11.1 11 713 11 1ZG (POI} F\JU.Y ,1,.2.0,. NGL STRUT 1.53 2.DO 101 . ..".' .....,.,.. LOO U.2 LOO U4 T.01 7.53 L01 L50 ao1 a50 1DO 150 11.DO 11.50 11.7fi 100 11.10 11.613 10..S19 10.149 9.142 B.825 e.120 7.854 7.... 7.810 7.6IO 7.541 7.4.26 7.312 7:2111 7.154 o:m 8.153 5.142 4...1.4.0. .3..1.4.0. 2.150 1.... 1.153 .0..1.1.4. ,.1.8.0.. ...,., "...,". 1.4.7, 111 174 72& 790 1080 1247 1479 1798 2,Z.T.1. 41.. 4110 EXTENCED 12.15 4711 RJU.YCOMPREIBED BTATIC "X' PAEBSURE DO 1,.9..1.15. 2.1.5. (l<CHEB) 1.00 1.&0 Z.DO Z.50 100 150 ..DO ..50 LOO 50 LOO L50 7.DO 7.50 LOO LOO aoo aoo moo 100 11.00 11.l50 100 100 (l<CHEB) (Pm} Ul.115 312 17.8115 321 17.115 331 1e.ee5 341 11!.115 352 1,._..,... .m.. 1..... .. 14.18'1 403 13.MIS 411 1'910ll 438 1..... ... 12.18'1 471 11 115 412 ,,_,. 514 1..... 531 10.195 """ 1.1115 m 8.195 703 7.815 741 7.1115 IQO F\JU.Y EXTENDED MLG STRUT 1100 11&0 1..00 1...0 1DO 1L&O 1LOO 1UO 17.IJO 17.60 1LOO 1L50 1aoo 1a01 e.1e& 121 Cli.lllli 1CIOI 6.1115 1mll 4""8 1210 4.115 1146 3.lllli 151Z 3.115 1723 2""8 19'7 2.115 2312 1.llO .... o1..1.1.5. 3.5.1.2. 0.115 1131 .... RJU.YCOMPREBSED TIL-003564 Figure 6. Landing Gear Safety Pins SEE DETAIL A NOSE LANDING GEAR GROUND LOCK PIN DETAIL A MAIN LANDING GEAR DETAIL B TIL-002525 2A-32-30: Extension and Retraction System General Description: (See Figure 7. Landing Gear Control and Indication System Diagram.) The Landing Gear Control Unit (LGCU) controls all gear and door movement. Landing gear extension and retraction is commanded via the landing gear lever on the copilot side of the center instrument panel. The landing gear lever is electrically connected to the LGCU mounted in the Right Electronics Equipment Rack (REER). Movingthe landing gear handle into the extend or retract detent provides an electrical signal to the LGCU. The LGCU, if all parameters have been met, commands boththe Nose and Main Landing Gear Control Manifolds (LGCMs). The LGCU provides an electrical signal to solenoids on the LGCMs to routeleft system hydraulic pressure to the extend or retract side of the actuators for the main and nose gear doors. If the left system pressure is not available, but hydraulic lines andfluid quantity are intact, the Power Transfer Unit (PTU) or the Auxiliary (AUX) system can provide pressure to operate the landing gear. If no hydraulic pressure is available,the landing gear may belowered by discharging nitrogen gas stored in emergency bottles located in the nose wheel well. Note The emergency extension system may only be used once and cannot retract the landing gear. Two Weight-On-V\lheels (WOVV) sensors are installed on each landing gear. The WOW sensors provide the ground or air mode reference signals to the LGCU, which intum provides the WOW status to various aircraft systems. Description of Subsystems, Units and Components: Landing Gear Control Panel (LGCP): WARNI NG _ FAILURE TO INSTALL ALL LANDING GEAR SAFETY PINS AND DOOR SAFETY PINS BEFORE WORKINGIN ANY WHEEL WELL MAY RESULT IN SERIOUSINJURY OR DEATH. PRIOR TO APPLYING ANY FORM OF HYDRAULIC PRESSURE TO THE AIRCRAFT, ACCOMPLISH THE FOLLOWING: ENSURE LANDING GEAR SAFETY PINS AND DOOR SAFETY PINS ARE INSTALLED. ENSURE ALL PERSONNEL AND EQUIPMENT ARE CLEAR OF WHEEL WELL AREAS. The Landing Gear Control Panel (LGCP) is located on the forward portion of the center pedestal next to the right Engine Fire Pull handle (see Figure 8. Landing Gear Control Panel). The LGCP contains three down-and-locked position indicators, a hom silence switch and a manual lock release. The lock release is a solenoid-controlled mechanical lock to prevent inadvertent movement of the landing gear handle from gear down to gear upwith the aircraft on the ground. The solenoid is energized to the closed position if WOW is false (airborne) to allow retraction of the gear. However, if the WOW system malfundions after takeoff, the lock release button can be depressed to override the solenoid. Landing Gear Control Unit (LGCU): The LGCU is located in the REER. The LGCU contains two control lanes and a monitor lane. Either control lane is capable of controlling the gear system. The control lanes have separate power sources: LDG GEAR CTRL 1 L ESS 28V DC LDG GEAR CTRL 2 R Main 28V DC Each of the control lanes supports its own set of 15 proximity sensors (a total of 30 sensors) to provide position indications for the landing gear system. The proximity sensors monitor the following gear components: NLG LEFT MLG RIGHT MLG Door Closed Door Closed Door Closed Door Open Door Open Door Open Down and Locked Down and Locked Down and Locked Up and Locked Up and Locked Up and Locked wow wow wow The LGCU controls movement of the landing gear by energizing solenoids on both the nose landing gear and mainlanding gear manifolds. The position of the landing gear is reported by the LGCU to the Modular Avionics Units (MAUs) to various aircraft systems via ARINC 429. The LGCU receives WOW status from the two WOW proximity sensors on each gear. The WOW status is provided from the LGCU to various aircraft systems. The status is sent to, but not limited to, the following systems: Cabin Pressure Controller (CPC) Traffic Collision Avoidance System (TCAS) Standby Multifunction Controller (SMC) Nose Wheel Steering (NWS) Crew Alerting System (CAS) Fuel Quantity Indicator (FQI) Bleed Air Controller (BAC) Security System Lightning Sensor System Cockpit Clocks Local Area Network (LAN) Remote Interface Units (RIUs) Enhanced Vision System (EVS) Processor Cockpit Voice Recorder (CVR) Flight Control Computer (FCC) Backup Flight Control Unit (BFCU) Display Unit (DU) reversion Auxiliary Power Unit (APU) Auxiliary (AUX) pump Brake Control Unit (BCU) Landing Gear Control Manifolds (LGCMs): When commanded by the LGCU, two LGCMs control hydraulic pressure to the gear; one controls the nose landing gear and nose landing gear doors, and the other controls the main landing gear and main landing gear doors. For emergency extension, each of the manifolds contains a dump valve to allow nitrogen to reposition the gear. The Nose Landing Gear Manifold is located on the left side of the nose landing gear wheel well. The manifold ports hydraulic pressure to the following components: NLG Door Actuator NLG Uplock NLG Actuator The Main Landing Gear Manifold is located on the center torque box in the main wheel well. The manifold ports hydraulic pressure to the following components: MLG Door Actuator (2) MLG Uplock Actuator (2) MLG Sidebrace Actuator (2) Each manifold has a dump valve installed. The dump valve is part of the emergency gear system and is repositioned from the normal position by nitrogen pressure when the emergency gear handle is pulled. VVhen the dump valve has been repositioned, the valve closes a switch illuminating the DUMP legend on the Cockpit Overhead Panel (COP). Each dump valve is reset by energizing (depressing) the associated LOG GEAR DUMP VALVES, NOSE or MAIN switches on the COP. Proximity Sensors: Thirty proximity sensors are used in the landing gear system. Fifteen sensors are for each control lane of the LGCU. These proximity sensors replace position switches and operate on two principles: Guaranteed Activation (GA) Target-Near Guaranteed Deactivation (GD) Target is Far Proximity sensors operate just as their name implies: As they enter within dose proximity to the magnetic inductance field, interruption in the field will cause the sensor to indicate that the component is in the correct position. Twelve proximity sensors per control lane provide landing gear and landing gear door position. These sensors monitor the following components: NLG: Up and Locked Down and Locked MLG: Up and Locked Down and Locked Gear Doors: Doors Open NLG MLG Doors Closed NLG MLG Each of the proximity sensors reports their position to the LGCU for proper gear sequencing. e. Landing Gear Control Maintenance Panel: (See Figure 9. Landing Gear Control Maintenance Panel.) The landing gear system incorporates the capability of independent operation of the landing gear and gear doors to facilitate ground maintenance and servicing. The Maintenance mode can be used to open the gear doors for inspection and maintenance activities. The Landing Gear Control Maintenance Panel islocated on the right side forward of the external power door. Six switches are located on the Landing Gear Control Maintenance Panel: wow OVRD (Guarded): GND I AIR I NORM LG MODE (Guarded): MAINT / NORM MLG (Guarded): RETR / EXTD MLG DR: CLS / OPEN NLG (Guarded): RETR / EXTD NLG DR: CLS / OPEN Safety interlocks inhibit entry into the maintenance mode. Both control lanes must agree they are in the maintenance mode for the maintenance mode operation to commence. The followingswitches must agree to enter the maintenance mode: External LGCMP Door: Door Open Maintenance Mode Selected Switch: Selected to MAINT Once the LGCU enters the maintenance mode, any further landing gear handle inputs will be ignored. The LGCUwill consider the true VVOW state of the gear to manual retraction instead of the simulated WOW override state. This ensures that the gear cannot be retracted without the aircraft on jacks. Nose Landing Gear Extend and Retract Components: Nose Landing Gear Control Manifold: The nose landing gear control manifold is located on the left side of the nose wheel well. The manifold is solenoid-controlled by the LGCU, to control NLG extension and retraction. The manifold, in response to the inputs from the LGCU, ports pressurized hydraulic fluidto the following components: Door Actuator Uplock Actuator Gear Actuator The NLG Manifold contains a dump valve controlled by the emergency gear handle. The valve ports nitrogen to allow the gear to be blown down. Nose Landing Gear Uplock: The Nose Landing Gear (NLG) uplock assembly retains the NLG in a mechanically locked position within the landing gear bay during aircraft flight by the use of an uplock latch that captures an uplock roller on the gear. Upon uplock release, the uplock actuator acts on a lever which pushes the lock link assembly out of a spring loaded over-center position. This initiates a rotation of the latch assembly which is further driven by the weight of the gear transmitted through the uplock roller. Once the gear uplock roller disengages from the latch assembly, the latch continues to rotate under the influence of the same spring system to a hard stop position, where it remains ready to receive the uplock roller on the gear retraction cyde. Upon retraction, the gear is driven by the retract actuator and delivers the uplock roller into the uplock latch. As the roller engages into thelatch (assisted by the uplock spring system), the uplock latch rotates, pushing the lock links over-center and securely locking the latch assembly. The uplock assembly housing also includes two sensors that provide signals when the NLG is in the up-and-locked position. The nose gear uplock assembly consists of a hydraulic actuator, a hook, overcenter linkage and proximity sensors. The hydraulic actuator receives pressure duringthe gear down cyde. The actuator contains a shuttle valve which ports nitrogen pressure to the uplock port of the actuator, allowing the hook to open; thereby freeing the gear for extension. The overcenter linkage maintains the uplock hook in the gear up position without the need for hydraulic pressure. In the event the uplock is inadvertently in the up-and-locked position, upon applying hydraulic pressure to the gear system the uplock will open. The uplock receives hydraulic pressure from the gear down side of the NLG manifold. Nose Door Actuator: The nose door actuator is located in the nose wheel well on the forward bulkhead. The actuator extends to close the doors and retracts to open the doors. A bellcrank is connected to both ends of the actuator. The bellcranks reposition torque tubes or open or close the NLG doors. The actuator body contains a shuttle valve for emergency gear extension. Nose Gear Actuator: The nose gear actuator is a dual-acting actuator, located on the left side of the nose wheel well aft of the trunnion. The actuator controls extension and retraction of the nose gear. The actuator is controlled by the nose landing gear manifold and has a shuttle valve for emergency gear operations. Nose Landing Gear Downlock Actuator: Located on the folding truss assembly, the actuator hydraulically locks the folding truss in the down-and-locked position. Main Landing Gear Extend and Retract Components: Main Landing Gear Control Manifold: The main landing gear control manifold is located on the center torque box of the main wheel well. This manifold is solenoid controlled by the LGCU and also controls MLG extension I retraction, door open I close and dump. The manifold, in response to the inputs from the LGCU, ports pressurized hydraulic fluid to the following components: Door Actuators Uplock Actuators Sidebrace Actuators The MLG manifold contains a dump valve controlled by the Emergency Gear Handle. The valve ports nitrogen to allow the gear to be blown do.vn. Main Landing Gear Uplock: The Main Landing Gear (MLG) uplock assembly retains the MLG in a mechanically-locked position within the landing gear bay during aircraft flight by the use of an uplock latch that captures an uplock roller on the gear. Upon uplock release, the uplock actuator acts on a lever which pushes the lock link assembly out of a spring loaded over-center position. This initiates a rotation of the latch assembly which is further driven by the weight of the gear transmitted through the uplock roller. Once the gear uplock roller disengages from the latch assembly, the latch continues to rotate under the influence of the same spring system to a hard stop position, where it remains ready to receive the uplock roller on the gear retraction cycle. Upon retraction, the gear is driven by the retract actuator and delivers the uplock roller into the uplock hook. As the roller engages into the hook (assisted by the uplock spring system) the uplock hook rotates and pushes the lock links over-center to securely lockthe hook assembly. The uplock assembly housing also includes two sensors that provide signals when the MLG is in the up-and-locked position. The main gear uplock assembly consists of a hydraulic actuator, a hook, overcenter linkage and proximity sensors. The hydraulic actuator receives pressure during the gear down cycle. The actuator contains a shuttle valve and is part of the actuator for the emergency extension system. The shuttle valve ports nitrogen pressureto the uplock port of the actuator,allowingthe hook to open; thereby freeing the gear for extension. Main Door Actuator: The main door actuators are located on the left and right side of the center torque box forward of the MLG manifold. The actuators extend to close the doors and retract to open the doors. A bellcrank is connected to the actuator and to the MLG inboard door. The bellaanks reposition the door to open or dose the inboard MLG doors. The actuator body contains a shuttle valve for emergency gear extension. Main Landing Gear Doors: Each main landing gear wheel well is enclosed by a hydraulically-operated inboard door and mechanically-operated fairing. The fairing is controlled by movement of the gear. The MLG fairing drive link is connected to the structural post and a fairingdrive crank. The drive crank repositions the fairing with gear movement. Main Sidebrace Actuator: The main sidebrace actuator is dual acting actuator, located on the forward portion ofthe mainwheelwell andtothe MLG structural post. The actuator controls extension and retraction of the main gear. The actuator is controlled by the MLG manifold. The actuator has a shuttle valve for emergency gear operations. Landing Gear Normal Operation: The landing gear is extended (down) and retracted (up) using the left hydraulic system with PTU or AUX as backup. The PTU provides OEM Provided Data Landing Gear Revision 4 2017-30 2A-32-00: 1B of 72 hydraulic pressureif the left engine-driven hydraulic pump fails.If boththe left and right engine driven pump fails and the AUX pump is in the ARM position and the gear handle and the gear position disagree, the AUX pumpwill power up and provide hydraulic pressureto extend or retract the gear. Note Normal landing gear movement time is five seconds for retraction and 9.7 seconds for extension. The landing gear control handle is located near the forward portion of the center pedestal, adjacent to the right engine fire pull handle and is electrically connected to the LGCU. Landing gear movement is controlled electrically by switches activated by the landing gear control handle. These switches send electrical power to the LGCU. The LGCU provides an electrical signal to the nose and main landing gear manifolds. Electrical power is supplied from the L ESS and R Main 28V DC buses. The LGCU confirms the aircraft is in Weight-Off-V\lheels (air mode) and verifies the nose wheel is centered. Nose Landing Gear Retraction (Normal): The LGCU provides the NLG manifold door solenoid with 28V DC power to energize the door valve to the open position. The door valve ports hydraulic pressure to the NLG door actuator, retracting the actuator.The actuator repositions the door linkage which opens both of the NLG doors. As the doors fully open, proximity sensors provide a target-near (guaranteed activation) to the LGCU. V\lhen the doors are fully open, the LGCU provides 28V DC power to the gear solenoid. The gear solenoid repositions the valve to the gear up position, porting hydraulic pressure to the NLG actuator and to the downlock actuator (unlocking the downlock). The actuator retracts, resulting in gear retraction. As the uplock roller strikes the uplock hook, the uplock hook rotates up to lock the gear in the up position. VVhen the uplock closes, the proximity sensors for the uplock transmits the gear up position to the LGCU. The LGCU continues to power the gear to the up position untilthe gear doors are closed. 'Mth the gear in the up and locked position the LGCU again provides the door solenoid with 28V DC to close the gear doors. The valve ports hydraulic pressure to the extend side of the NLG door actuator. As the door actuator extends, the NLG doors close. VVhen the doors close, the proximity sensors provide the LGCU with a "door closed" signal.The LGCU provides 28V DC power to the door solenoid while the gear handle remains in the up position. Nose Landing Gear Extension (Normal): The LGCU provides the NLG manifold door solenoid with 28V DC power to energize the door valve to the open position. The door valve ports hydraulic pressure to the NLG door actuator, retracting the actuator. The actuator repositions the door linkage, opening both of the NLG clamshelldoors. As the clamshell doors fully open, proximity sensors provide a target-near (guaranteed activation) to the LGCU. With the doors open, the LGCU provides 28V DC power to the gear solenoid. The gear solenoid repositions the valve to the gear down position, porting hydraulic pressure to the NLG actuator and to the uplock actuator. The uplock actuator extends to open the uplock, thereby allowing the gear to extend. The NLG actuator extends the gear into the down-and-locked position. As the gear is fully extended, the NLG downlock actuator also has hydraulic pressure waiting to extend the downlock as the foldingtruss assembly positions the gear over-center. The downlock proximity sensors on the folding truss brace transmits the gear down position to the LGCU. The LGCU continues to power the gear down solenoids to the down position while the aircraft is powered and gear is down. With the gear in the down-and-locked position, the LGCU again provides the door solenoid with 28V DC to dose the gear clamshell doors. The valve ports hydraulic pressure to the extend side of the NLG door actuator. As the door actuator extends, the NLG clamshell doors dose. When the doors dose, the proximity sensors provide the LGCU with a "door dosed" signal. Main Landing Gear Retraction (Normal): The LGCU provides the MLG manifold door solenoid with 28V DC power to energize the door valve to the open position. The door valve ports hydraulic pressure to the both MLG door actuators for retraction. The actuators reposition the door linkages which open both of the MLG inboard gear doors. As the doors fully open, proximity sensors provide a target-near (guaranteed activation) to the LGCU. The LGCU removes the power signal from the door solenoid after the doors are fully open. With the doors open, the LGCU provides 28V DC power to the gear solenoid. The gear solenoid repositions the valve to the gear up position, porting hydraulic pressure to the MLG sidebrace actuators. The actuators retract, raising the gear into the retracted position. As the uplock roll strikes the uplock hook, the uplock hook rotates up locking the gear in the up position. When the uplock doses, the proximity sensors for the uplocks transmit the gear up position to the LGCU. The LGCU continues to power the landing gear to the up position until the gear doors are closed. With the gearinthe upandlocked position, the LGCU again provides the door solenoid with 28V DC to close the gear doors. The valve ports hydraulic pressure to the extend side of the MLG door actuators.As the door actuators extend, mechanical action causes the MLG inboard doors to dose. When the doors dose, the proximity sensors provide the LGCU with a "door dosed" signal. The LGCU provides 28V DC power to the door solenoid while the gear handle remains in the up position. Main Landing Gear Extension (Normal): The LGCU provides the MLG manifold door solenoid with 28V DC power to energize the door valve to the open position. The door valve ports hydraulic pressure to both MLG door aduators to retrad these aduators. The aduator repositions the door linkage which in tum opens the MLG inboard doors. As the doors fully open, proximity sensors provides a target-near (guaranteed activation) to the LGCU. VVith both doors in the open position, the LGCU provides 28V DC power to the gear solenoid. The gear solenoid repositions the valve to the gear down position, porting hydraulic pressure to both MLG sidebrace actuators and to the uplock actuator. The uplock actuator extends to open the uplock, thereby allowing the gear to extend.The MLG sidebrace actuator extends the gear towards the down-and-locked position.As the gear is fully extended, segments in the sidebrace actuators effectively lock the gear in the down-and-locked position. The downlock proximity sensors are part of the sidebrace actuator and will transmit the gear down position to the LGCU. The LGCU will continueto power the gear down solenoids to the down position provided that the aircraft is powered and the gear is down. VVith the gear in the down-and-locked position, the LGCU again provides the door solenoid with 28V DC to close the gear inboard doors. The valve ports hydraulic pressure to the extend side of the MLG door actuators. As the door aduators extend,this mechanically causes the MLG inboard doors to dose. When the doors close, the proximity sensors provide the LGCU with a "door closed" signal. Landing Gear Control Maintenance Panel Operation: The Landing Gear Control Maintenance Panel is located on the right side of the aircraft forward of the external power doors. The maintenance panel allows control of the gear(s) and WOW override from outside of the aircraft. Prior to the maintenance panel becoming functional, both of the control channels of the LGCU must have certain interlock conditions met. The three interlock (switch) conditions required are: Landing Gear Control Maintenance Panel Door -"Open• LG Mode -"MAINT" WOW Override -"NORM" After the conditions have been met by both control channels, all landing gear movement in the Maintenance mode is controlled by the following six switches located on the Landing Gear Control Access Panel (LGCAP): WOW OVRD: This switch is used to change the WOW output state from the LGCU to other systems. The LGCU must be in the Maintenance mode for the WOW override to function. The switch is a three-position non-momentary switch. With the switch in the NORM position, the LGCU outputs the true WOW state. With the switch in the AIR position, the LGCU outputs Weight-Off-Wheels (air mode) to all user systems. Wrth the switch in the GND position, the LGCU outputs Weight-On-VVheels (ground mode) to all user systems. Note The landing gear system will always consider true WOW regardless of switch position, which prevents gear retraction while not on jacks. LG MODE: This switch is used to place the LGCU into the Maintenance mode. All other switches on the panel are deactivated while this switch is in the NORM (nonnal) position. The switch is a two-position non-momentary switch. While the switch is in the MAINT (maintenance) position, the cockpit landing gear control handle is deactivated. MLG: This switch is usedto retract and extend both MLGs. The LGCU must be in the Maintenance mode for this switch to function.The switch is a three-position momentary switch. VVith the switch is in the center position the landing gear remains unpowered. With the switch in the RETR (retract) position, the landing gear will retract. If no system hydraulic pressure is detected, the system also energizes the AUX pump. Similarty, with the switch in the EXTD (extend) position, the landing gear extends and the AUX pump activates (if no hydraulics are present). Note If the LGCU does not detect that the doors are in the OPEN position the landing gear will not retract. MLG DR: This switch is used to open and close the MLG doors. The LGCU must be in Maintenance mode for this switch to function. The switch is a three-position momentary switch. With the switch in the center position, the doors remain unpowered. With the switch in the OPEN position the doors will open. If no system hydraulic pressure is detected, the system also energizes the AUX pump. The LGCU will continuously power the respective MLG doors open during MLG movement. Similarty, with the switch in the CLS (close) position, the doors close and the AUX pump activates (if no hydraulics are present). Ifthe doors are stopped in any position (other than dosed) they will continue to move due to gravity, manual force, or transient spikes in the hydraulic system. Nways pin the doors open when movement is not desired. NLG: This switch is used to retract and extend the NLG. The LGCU must be in the Maintenance mode for this switch to function. The switch is a three-position momentary switch. With the switch in the center position, the landing gear remains unpowered. VVith the switch in the RETR (retract) position, the landing gear will retract. If no system hydraulic pressure is detected, the system also energizes the AUX pump. Similarty, with the switch in the EXTD (extend) position, the landing gear extends and the AUX pump activates (if no hydraulics are present). Note The NLG doors must be open for this switch to function. The LGCU will continuously power the NLG doors open while the NLG is in motion. NLG DR: This switch is used to open and close the NLG damshell doors. The LGCU must be in Maintenance mode for this switch to function. The switch is a three-position momentary switch. With the switch in the center position the doors remain unpowered. With the switch in the OPEN position the doors will open. If no system hydraulic pressure is detected, the system also energizes the AUX pump. Similarty, with the switch in the CLS (close) position, the doors close and the AUX pump activates (if nohydraulics are present). If the doors are stopped in any position (other than closed) they will continue to move if subjected to gravity, manual force, or transient spikes in the hydraulic system. Always pinthe doors open when movement is not desired. Landing Gear Emergency Extension Components: (See Figure 11. Emergency Gear Extension Controls and Figure 12. Emergency Gear Extension Components.) Emergency Extension T-Handle: The emergency extension T-handle is located on the forward instrument panel right side below Display Unit (DU) #3 and initiates the landing gear emergency extension. The handle is mechanically connected to the emergency extension air release valve. Emergency Extension Air Release Valve: The pneumatic, three-way, two-position control and vent air release valve is located in the upper right side of the nose wheel well. The valve has three ports as follows: Inlet (from the landing gear emergency extension bottles) Outlet (to the landing gear emergency extension system) Vent (overboard) When the emergency landing gear T-handle is pulled into the detent position, the air release valve lever doses the vent port and opens the outlet port, permitting 3,000 psi of nitrogen pressure to flow from the emergency landing gear nitrogen storage bottles. The high pressure nitrogen is directed to the dump valve portion of the two landing gear manifolds, and out to the three uplocks, three door actuators, two sidebrace actuators and the NLG actuator. The nitrogen is then ported via pneumatic lines to the emergency down port on both MLG sidebrace actuators, NLG retract actuators, both MLG uplocks, NLG uplock and each of the LG door actuators. Nitrogen Storage Bottles: Two 412 cubic inch emergency landing gear botUes are used to store pressurized nitrogen for emergency landing gear extension. The bottles are serviced to 3,000 psiwith dry nitrogen at 70"F. The bottles are interconnected and are located on the forward left and forward right side of the nose wheel well.Their combined capacities provides enough nitrogen pressure to emergency extend (blow down) the landing gear. The right bottle inlet has a relief valve providing overpressure protection for both bottles and is set to relieve if the pressure increases above 3,750 psi. Nitrogen Servicing Panel: The direct-reading pressure gauge for the emergency landing gear bottlesis mounted on the servicingpanel on the right side of the nose wheel well. The gauge indicates the pressure within the emergency landinggear botues (which should read 3,000 psiwith the bottles fully charged at 70"F). A nitrogen filler valve is mounted on the pressure gauge,on the right side of the nose wheel well. A pressure transmitter, for display of cylinder pressure on CAS, is mounted above the servicing panel.The transmitteris powered by the LOG GEAR IND (E-1) circuit breaker on the COP. The transmitter signal is sent to MAU 1DGIO 1. Dump Valve Reset Switches: Two dump valve reset switches are located on the COP (one for the NLG and one for the MLG manifolds). The switches are used to electrically reset the dump spool valves in the manifolds after an emergency extension has been accomplished. The guarded switches illuminate a blue DUMP legend when the landing gear has been extended pneumatically, and extinguishes when the dump valve has been reset. Landing Gear Emergency Operation: The emergency landing gear extension system is a backup system used when normal landing gear extension has failed either electrically or hydraulically. Emergency landing gear extension is accomplished by pulling the emergency landing gear T-handle. A cable connects the handle to the emergency extension air release valve. VVhen the valve is opened, high-pressure nitrogen ft01Ns from both nitrogen storage botues to several of the landing gear actuators. The nitrogen pressure also repositions the dump valve portion of both the landing gear manifolds selector/dump valve, isolating the landing gear from the hydraulic system. This action prevents hydraulic system pressure from entering the landing gear manifolds as the dump valve blocks the pressure ports. At the same time, the return port is opened, permitting a direct path for hydraulic fluid displaced by the nitrogen pressure to return to the reservoir. Pneumatic pressure is also supplied direcUy to the unlock port of the landing gear uplock actuators, the open port of all three door actuators and the extend side of the landing gear actuators, enabling the landing gear to extend. VVith the landing gear down and locked, the door closing sequence is bypassed and all landing gear doors remain open. As long as the emergency landing gear T-handle isleft in the extended position, nitrogen pressure remains in the actuators of each landing gear. VVhen the T-handle is returnedto the stowed position (bylifting the handle up out of the detent position and then pushing the handle forward), the nitrogen pressure is released from the actuators and exhausted overboard through a vent on the right side of the nose wheel well, just aft of the NLG doors. WARNING CLEAR AREA ON THE RIGHT SIDE OF THE AIRCRAFT FORWARD FUSELAGE OF ALL PERSONNEL PRIOR TO RESETTING (STOWING) THE EMERGENCY LANDING GEAR T-HANDLE.WHEN THE T-HANDLE IS RETURNED TO THE STOWED POSITION, NITROGEN PRESSURE USEDTO EXTEND THE LANDING GEAR WILL BE EXHAUSTED VIOLENTLY TO THE ATMOSPHERE WHICH CREATES A HYDRAULIC FLUIDVAPOR THATIS EXPELLED THROUGH AN UNMARKED VENT (ADJACENT TO THE NOSE LANDING GEAR TRUNNION ON THE FUSELAGE SKIN). Pneumatic repositioning of the dump valve causes the valve position switch to make contact and illuminate each of the LOG GEAR DUMP VALVES, NOSE and MAIN switches with a blue "DUMP• on the COP. Repositioning the dump valve to normal is accomplished by momentarily depressing the LDG GEAR DUMP VALVES NOSE or MAIN pushbuttons, which provides electrical power to a solenoid that repositions the valve and extinguishes the DUMP legend for each of the landing gear manifolds. Weight-On-Wheels 0JVOW) Operation: The landing gear WOW system provides air I ground status to the LGCU and then to other aircraft systems. It uses input from two proximity sensors {Chan A and Chan B) on each gear. The WOW proximity sensors function in the same manner as the proximity sensors for gear and gear door position. The proximity switch operates on two principles: Guaranteed Activation {GA) Target-Near {AIR) Guaranteed Deactivation {GD) Target is Far {GROUND) Note Many systems on the aircraft operate differently on the ground than they do in the air, or may enable different modes of units self-test or other functions. WOW System Components: Nose Gear WOW: The nose gear WOW proximity sensors are located on the aft side of the upper steering collar. The targetsfor the switches are on the torque link. Main Gear Wow: The main gear WOW proximity sensors are located on the bottom of the post and the targets are on the trailing arm. Combined Wow: Multiple inputs are evaluated from the left main gear WOW system and the right main gear WOW system to determine that the aircraft isweight-off-wheels and the airborne WOW signal is sent to all the systems supported. Controls and Indications: Landing Gear Controls: Landing Gear Control Panel: The landing gear control panel provides normal extension and retraction indication for the landing gear. The panel contains three down-and-locked position indicators (green), a horn silence switch and a manual handle lock release. The manual lock release allows retraction of the landing gear if the WOW system malfunctions. Landing Gear Control Unit {LGCU): The LGCU is located in the REER. The LGCU is electrically connected to the landing gear handle and to both landing gear manifolds and controls the sequencing of the landing gear system. Landing Gear Control Manifolds {LGCMs): Two LGCMs are onboard the aircraft: One LGCM (located in the nose wheel well) for nose gear operation, and one LGCM (located in the main wheel) well for main gear operation. These units are electrically controlled to distribute hydraulic power to the individual valves and actuators to correctly sequence the landing gear and landing gear doors. They containthe valves and provide the ability to operate the main landing gear doors and nose landing gear doors independently for ground maintenance and service. Emergency Extension T-Handle: The emergency extension T-handle is located on the right side of the copilot instrument panel below the DU3 and initiates the landing gear emergency extension.It ismechanically connected to the emergency extension air release valve. Dump Valve Reset Switches: Two dump valve reset switches are located onthe COP and are used to electrically reset the dump spool valves after an emergency extension has be accomplished.The guarded switches illuminate a blue DUMP legend when the landing gear has been extended pneumatically and extinguish when the selected dump valve has been reset. Landing Gear Indications: Landing Gear Position and Warning System: The landing gear position and warning system provides indication of the position of the landing gear and doors. It also provides an audible warningwhen the landing gear and flaps are not property configured for landing. Twenty-four proximity sensors provide gear and door position to the LGCU. Landing Gear Downlock Proximity Sensors: Two downlock proximity sensors (control lanes 1 and 2) are located at each landing gear position. The two nose downlock proximity sensors are attached to the folding truss assembly and are activated by targets on the overcenter linkage. The main landing gear downlock proximity sensors are mounted inside the sidebrace actuators and are activated by the internal downlock mechanism. The sensors provide the down-and-locked indications on the landing gear control panel. A light in the landing gear handle indicates that the handle disagrees with the position of the gear. Electrical power through the LGCU issupplied by the ESS DC power bus LOG GEAR IND circuit breaker. Landing Gear Uplock Proximity Sensors: Two landing gear uplock proximity sensors (control lanes 1 and 2) are located at each gear position and are located on the uplock hook linkage. The proximity sensors provide the LGCU gear up or not up indications for sequencing landing gear movement. OEM Provided Data Landing Geer Revision 4 2017-06-30 2A-32-00: 'll of 72 Main Landing Gear Door Open Proximity Sensors: Two main landing gear door open proximity sensors (control lanes 1 and 2) are located on the aft hinge point for the inboard MLG doors. When the inboard gear doors are in the full open position, the proximity sensors provide the door position to the LGCU. Main Landing Gear Door Closed Proximity Sensors: Two main landing gear door closed proximity sensors (control lanes 1and 2) are located on the forward hinge point for the inboard MLG doors. When the inboard gear doors are in the dosed position, the proximity sensors provide the door position to the LGCU. Nose Landing Gear Door Open and Closed Proximity Sensors: Two nose landing gear door open and two door dosed proximity sensors (control lanes 1and 2) are located on the forward bulkhead of the nose landing gear wheel well. Movement of the nose landing gear door linkage provide either the door open or dosed position to the proximity sensors which in tum provide the door position to the LGCU. (7) Control Panel: The control panel contains three green DOWN annunciators which illuminate when the respective landing gear is in the down-and-locked position. A red (or white for EASA) annunciator light in the landing gear control handle illuminates whenever there is a disagreement between the handle position and the position of the landing gear. Upon landing gear retraction, the light remains illuminated until each gear is fully up and locked. Upon landing gear extension, the light remains illuminated until the gear is down and locked, regardless of door position. The panel also contains a HORN SILENCE button to silence the warning horn (if desired). Door Closed Proximity Sensors: The door closed proximity sensors provide indications to the CAS through the LGCU. After completion of the gear up cycle, the red (or white for EASA) light in the landing gear handle extinguishes when all three gear up and door closed proximity sensors are activated. After gear extension if the any or all of the gear doors do not close, no CAS indications for the doors are displayed (due to the emergency gear extension). Door position is displayed on the DOORS synoptic page. The synoptic page indications are colored blue for door in transit and amber if the door remains open after the gear up cycle. FaultIndications: CAS warning messages are provided for landing gear not down, not up, or landing gear doors not dosed. After the landing gear handle is repositioned, the MAU's software delays any CAS messages for fifteen seconds to allow the gear to complete the normal cycle. During this delay, the gear doors on the door synoptic page will appear in blue. After the gear cycle is complete, if the gear is not in the down-and-locked or up-and-locked position, the following amber messages will be triggered: L-R Main Gear Door Open L-R Main Gear Not Up L-R Main Gear Not Down Nose Gear Door Open Nose Gear Not Up Nose Gear Not Down If after fifteen seconds a gear is not up and locked, only the applicable Gear Not Up CAS message will be displayed. The software disables the door message (based on the logic).If the gear is not up, the door will not close. The logic is designed to aid the pilot in detennining the situation causing the malfunction. Landing gear position and system operation are presented graphically on the flight control synoptic page. V\lhen the landing gear is down and locked, the wheels and struts are displayed in green. V\lhen the landing gear is in transit, the wheel and strut are displayed in magenta. V\lhen the landing gear is up and locked, they are not depicted on the display. If any (or all) of the landing gear disagree with the position of the landing gear handle, the malfunctioning landing gear(s) is displayed in amber. Audio Warning System Operation: (See Figure 10. Gear Warning Audio Interface.) Thelanding gear audio warning is provided by the MAUs. The MAUs monitor aircraft altitude (radio altimeter), power lever position, flap extension and gear downlock signals. V\lhen specific combinations of these conditions exist, the landing gear audio warning is provided. The aew is alerted by a warning tone when the following landing gear conditions are true: Engine Power Levers -<5° Flaps-<22° Radio Altitude (AGL) -<500 ft Any Gear - Not down and locked Note Depressing the HORN SILENCE button on the landing gear control panel silences the landing gear warning tone (provided flap position is less than 22°). OR: Flaps >22" Any Gear - Not dov.m and locked Note If the flap position is greater than 22", the warning horn can only be silenced by either retracting the flaps or by extending the gear. Circuit Breakers (CBs): The foll01Ning circuit breakers protect the operation and indication of the landing gear and associated WOW system elements. Circuit Breaker Name CB Panel Location Power Source LOG GEAR IND CPOP E-1 R ESS 28V DC Bus LOG GEAR CTRL 1 POP E-2 L ESS 28V DC Bus LOG GEAR CTRL 2 CPOP E-2 R ESS 28V DC Bus LOG GEAR DUMP VALVES CPOP D-1 R ESS 28V DC Bus Crew Alerting System (CAS) Messages: The following CAS messages are associated with the landing gear and WOW systems: Area Monitorad CAS Massage Landing Gear Control Handle and Aircraft Configuration Main Gear Door L-R Main Gear Door Ope (caution) Main Gear Downlocks L-R Main Gear Not Down {caution) Main Gear Uplocks L-R Main Gear Not U {caution) Nose Gear Door Nose Gear Door Ope (caution) Nose Gear Downlock Nose Gear Not Down {caution) Nose Gear Uplock Nose Gear Not U {caution) LGCU in Reversionary Mode Landing Gear Maint Re (caution) LGCU Detects Faulty LRU Landing Gear System Fail {caution) LGCU Unable to Process WOW Data M•MIOll {caution) LGCU Detects Faulty LRU Landing Gear System Faul (advisory) Note CAS messages associated with landing gear and/or door position are not presented until 15 seconds after the landing gear control handle is placed in a detent - the delay allows for completion of the extension or retraction cycle. Other Annunciations: Annunciation Cause or Meaning Aural warning horn sounds (gear position not corresponding to aircraft landing configuration) Landing gear unsafe Limitations: Landing Gear Extended Speed CVLE I Mu): Do not exceed 250 KCAS with landing gear extended (gear doors open or closed). Landing Gear Operation Speeds CVLo I MLO): Normal Operation: Do notlower or raise landing gear at speeds in excess of 225 KCAS. Alternate Operation: Do not lower landing gear utilizing alternate system at speeds in excess of 175 KCAS. Landing Gear Extension I Operation: Maximum operating altitude for extending landing gear or flying with landing gear extended is 20,000 ft. Speed Brakes With Landing Gear Extended: Speed brakes are not approved for extension with flaps set at 39° (DOWN) or with the landing gear extended in flight. Figure 7. Landing Gear Control and Indication System Diagram 1-- --w:l.NCIHQ OEAR DOWN m !i! LANDIM> I E I ! I 6-'- •as• !! Q GEAR I CONTROL MANIFOLD I I LDOOROP,,.coMMANDmG>W. -OOORCL08EOOMtMND• otW. LANDING GEM. CONlRIJL LNT ! -L>H>NO; OEAR DOWNCOM.W.D •orw. (LGCIJ) ffi -LANDING GEM.UP ca.llMM> SIG ..L..EI.._ ..IO.I,.._ aJS21YDC a.JS21YDC CHANNEL A CHANNEL& I MAIN LANDING I co w .....FOil) LMDINGIOEMUP I -LANDINJlilENt.DOWN i DOOR OPEN i t !i! LEFTMAl\IL.AN>NQ GEAR T I TIL-007441 Figure 8. Landing Gear Control Panel DETAIL A DETAIL B TIL-015023 Figura 9. Landing Gear Control Maintenance Panel SEE DETAIL A SWITCH GUARDS ARE INSTALLED ON SWITCHES IDENTIFIEDWITH AS ASTERISK(") DETAIL A TIL-002524 Figure 10. Gear Warning Audio Interface 29 VDC REMBUS LDGGEAR INDICATION TOCOCKPrJ AUDIO SYSTEM DIM lEST MAIJ2 AUDIO TONE OUT HORN SILENCE SWITCH LANDINGGEAR CONTROL PANEL LANDINGGEAR MANUAL VN..\/E Ei.e:t 90TTI..E8 CONTROL FRCN COCl<P - IL---- - _ _ TOLANDINGGEAR I MANIFa..08 I DUW ACTIJA.llON HORNWT'E MAU1 f- ------------ EGEAR BTl. PRESSURE DC H r-c-------------- E OEAR BTl PRESSURE DC L NOii!: DENOTE8 LANDING GEAR EM BOTTLE Nrl'ROGEN PRESSURE LINE llL-002621 Figure 11.Emergency Gear Extension Controls SEE DETAIL A SEE DETAIL B EMERGENCY LANDING GEAR HANDLE DETAIL A LEFT AND RIGHT BLOWDOWN BOTTLES LANDING GEAR EMERGENCY EXTENSION PRESSURE GAUGE DETAIL B TIL-002533 Figure 12. Emergency Gear Extension Components SEE DETAIL A NOSE LANDING GEAR EMERGENCY AIR RELEASE VALVE DETAIL A LANDING GEAR EMERGENCY FILLER a VALVE AND GAUGE (jl ,. DETAIL B TIL-002612 2A-32-40: Wheels and Brakes System General Description: (See Figure 13. Brake By VVire (BBW) System Block Diagram (1 of 2) and Figure 14. Brake Hydraulic Schematic.) The landing gear incorporates dual wheels on each main and nose strut. The nose gear wheels are free to rotate, with no braking system installed. The braking system features two independent primary brake systems, each operating two of the four main wheel brakes. The brakes are controlled in inboard and outboard pairs, ensuring ground directional control with one system failed. Both pairs of brakes are operated via the pilot or copilot brake pedals, and normal brake pressure is supplied from both the left and right hydraulic systems. Nose Landing Gear Wheels And Tires: The nose gear wheel assemblies, each consisting of two half-hubs, are split-type units measuring 22 x 6.