Polymers Used for Movable Dentures and Provisional Prosthesis PDF
Document Details
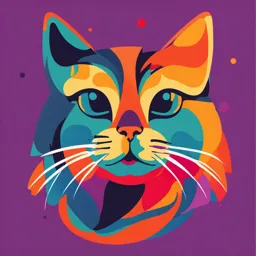
Uploaded by WellPositionedAntimony
UMF "Iuliu Hațieganu"
Tags
Summary
This document is a lecture on polymers used in creating movable dentures and provisional prosthetics. It explores the various types of acrylic resins utilized in dentistry, along with their classifications and polymerization techniques. The discussion also encompasses considerations for biocompatibility and related factors.
Full Transcript
POLYMERS USED FOR MOVABLE DENTURE AND PROVISIONAL PROSTHESIS LECTURE 11 Dentistry domains where are used different types of acrylic resins Full/partial denture bases Denture teeth Orthodontic retainers Surgical dentures Mouth guards Provisional acrylic part...
POLYMERS USED FOR MOVABLE DENTURE AND PROVISIONAL PROSTHESIS LECTURE 11 Dentistry domains where are used different types of acrylic resins Full/partial denture bases Denture teeth Orthodontic retainers Surgical dentures Mouth guards Provisional acrylic partial dentures As veneering material of the metallic framework of the acrylic-metal restorations Prosthetic uses of the self-curing acrylic resins Impression-pattern Functional impressions Relining materials of the full dentures Custom trays Repair of denture bases Classification Definitions. Terms. Polymers= materials with a high molecular weight, formed through repeating of thousands or millions times of some structural units (poly=many, mer= unit) Oligomer = a short polymer (2,3,4 units) Definitions. Terms. Monomer = molecules which form the polymer through polymerization (covalent bonds formation). Copolymers =bonding between 2 or more types of monomers within polymer The name of the monomer gives the name of the polymer Definitions. Terms. Degree of polymerization = total number of monomers from a molecule of a polymer Molecular weight of a polymer = the sum of molecular weights of the monomers Definitions. Terms. The degree of polymerization is proportional with the molecular weight The increase of molecular weight determines the increase of : –Mechanical strength –Hardness –Stiffness –Plastic strain strength = more brittle Spatial structure of the polymeric chain 1. Linear/branched chain – physical and weak bonds, which are breaking through heating of the polymer (fluid) = thermoplastic: low mechanical properties polystyrene, polyvinyl, PMMA (polymethyl methacrylate) 2. Cross-linked chain – covalent bonds, three- dimensional network; it isn’t thermoplastic Bis-GMA, cross-linked PMMA, impression silicones Linear polymer Branched polymer A linear and branched Cross-linked copolymer polymer General properties of the polymers The degree of crystallinity influences: –the degree of water sorption –stiffness –mechanical strength Most of the polymers =amorphous structure = glassy polymers General properties of the polymers Water sorption can partially compensate the polymerization shrinkage Thermoplastic glassy polymers + small molecules of plasticizers = –Reducing of the stiffness –Reducing of the transition temperature from the glassy state into flexible state General properties of the polymers Polymerization shrinkage Volumetric: –AR (acrylic resin) without filler: -21% –AR denture bases: -6% –CR (composite resins): -1-2% Shrinkage – accumulation of internal stresses – heating of the material – modification of the prosthetic restoration General properties of the polymers 1. Polymerization shrinkage Methods of reducing the polymerization shrinkage : Mixture of the monomer with an inert material to polymerization shrinkage (polymer, glass) Mixture of the powder (polymer) + liquid (monomer) Polymerization under pressure (heat-processed through injection moulding) Usage of monomers with low shrinkage (big molecules of monomer : Bis-GMA than MMA) Other methods specific to polymers used for direct restorations (fillings) General properties of the polymers 2. Biocompatibility PMMA = good biocompatibility Immediate allergic reactions due to soluble constituents from AR (more frequently to self-cured acrylic resins): residual monomer benzoic acid General properties of the polymers 2. Biocompatibility Delayed allergic reactions (years) = mycotic stomatitis Alternatives for allergic patients, prosthesis obtained through injection from: polycarbonate resins polyamides(nylon) Most frequent allergic reactions to MA(methacrylate) at dental technicians (direct contact, vapors) Polymerization reaction Polymerization through: ❖Addition (without by-products): PMMA Bis-GMA Addition-cured silicones ❖Condensation (with by-products release: water, alcohol): Polyamides Condensation-cured silicones Polysulphides Polymerization – addition reaction of the acrylic monomers 1. Initiation -Initiators= molecules with weak bonds which break under external factors : - Benzoyl peroxide: - Heat (740C) – heat-cured polymers - Chemical reaction with an accelerator (N,N dimethyl paratoluidine = amine) – self-cured polymers - Camphorquinone: - Light (460-470nm) – light-cured polymers Polymerization – addition reaction of the acrylic monomers 1. Initiation -Free-radicals formation with reactive groups (free e-) which attack the double bonds of monomer’s molecules = activated monomers with reactive ends -Initiators form the free radicals Polymerization – addition reaction of the acrylic monomers Polymerization – addition reaction of the acrylic monomers 2. Propagation -The activated monomers will attack the double bonds of the neighbor monomers – addition – polymeric molecular chain formation -The process continues until the activated molecules will be consumed -Typical acrylic polymer = 50.000 monomers Polymerization – addition reaction of the acrylic monomers 3. Termination - Branches or cross-linking formation through different mechanisms : - Dimerization = a growing polymeric chain reacts with another growing polymeric chain = cross-linked polymer - A transfer of chain which lead to a cross-linked polymer - The growing polymer reacts with the inhibitor of the polymerization (hydroquinone) Polymerization – addition reaction of the acrylic monomers -The termination is made to different lengths of the polymers from the material = variety of molecular weights -More longer the polymers are, better the properties of the material will be Polymerization reaction 1. cross-linked polymers -The acrylic polymers frequently form linear polymeric chains -Obtaining the cross- linked polymers in presence of monomers with reactive ends (bifunctional) = glycol dimethacrylates Polymerization reaction 1. cross-linked polymers - Linear PMMA = thermoplastic - Cross-linked PMMA = non-thermoplastic, higher hardness, reduced water sorption - AR used as aesthetic veneers of the metal-acrylic restorations are cross-linked PMMA, which are containing triethylene or tetraethylene glycol dimethacrylate: - Reduced vaporization degree, even at 100-1500C - Reduced risk of internal porosities formation Polymerization reaction 2. copolymers formation - Addition of other monomers to MMA - The copolymer between MMA and butyl methacrylate = a polymer with high impact strength - The copolymer between MMA and octyle methacrylate = a flexible material at O.C. T0C, used as soft liner Polymerization reaction 3. modified polymers formation - Addition of some components which don’t participate to polymerization – modification of the polymers’ properties - Addition of organical esteric oils (dibutyl phtalate) – reducing of the transition T = flexible material used as soft liner - The material becomes stiff while the saliva extracts the organic oil from the composition of the material Polymerization reaction 3. modified polymers formation - Addition of inorganic filler – increases the viscosity in the initial state (Duracrol – custom impression trays) - Addition of butadien-styrene rubber = a material with an impact strength 5 x higher (high-impact resins) - A light-cured oligomer of AR + inorganic filler = custom impression trays !!!! THEY AREN’T COMPOSITE RESINS!!! *Factors which influence the polymerization reaction 1. Number of free radicals (R-) - Initially formed by the initiator, their number depends on the concentration of the initiator (ci): - big ci =many R- = short chains = low polymerization degree Optimal ratio (which it must to be respected) P (polymer): L (monomer) - It is needed a homogeneous mixture ci higher in certain zones = unequal polymerization within the material *Factors which influence the polymerization reaction 1. Number of free radicals (R-) ci cannot be reduced under a certain value because the formed macro-radicals would be blocked before consumption of the whole amount of monomer residual monomer negative influences over the biocompatibilities and properties of the material *Factors which influence the polymerization reaction 2. The type and the frequency of the termination reactions - Termination through dimerization = higher molecular weight of the polymer 3. Polymerization degree and internal conversion rate Polymerization degree = molecular weight = index of quality appreciation of the polymerization - but the residual monomer modifies considerably the values Internal conversion rate (CR) = number of saturated double bonds C=C formed during polymerization - Determined through physical methods (spectrophotometry, pH-metry etc) - CR always < 100% - Higher the CR is, less residual monomer is Factors which influence the polymerization reaction 3. Polymerization degree and internal conversion rate Polymer with optimal properties: - High polymerization degree and - High CR 4. Heat release During polymerization reaction there are 2 causes: - Exothermal polymerization reaction - Light irradiation (light-curing) Factors which influence the polymerization reaction 5. Heat release through irradiation - Directly proportional with: - Irradiation intensity - Irradiation time - Features of the light - Importance only to direct restoration Factors which influence the polymerization reaction 6. Heat release through polymerization reaction ▪ Breaking of the double bonds C=C and their transformation into simple bonds –C-C- produces a high amount of energy (80kJ/Mol) ▪ Directly proportional with: - amount of material - monomer ratio - increasing speed of external T ▪ Negative effects over the heat-cured materials : - evaporation of residual monomer if T is too high (over 740C) – materials with porosities DENTURE BASE Polymers Imposed conditions natural appearance according to the replaced tissues; high strength, stiffness, hardness and toughness; accurate reproduction of surface detail and dimensionally stable; odourless, insipid(tasteless)and without toxic products; resistant to absorption of oral fluids and to bacterial growth; good retention to polymers, ceramics or dental alloys; easy handling and easy to repair them; easy to clean by the patients; low density, so a reduced weight; good thermal conductivity; radioopacity; cheapness. Composition Acrylic resins Powder Liquid Heat-cured PMMA (beads/ granules) - polymer Methyl metacrylate - Benzoyl peroxide – initiator monomer Ti dioxide – opacifier for the Hydroquinone – inhibitor translucency control Ethylene glycol (PMMA=transparent) dimethacrylate or Dibutyl phtalate – plasticiser other cross-linking Synthetic fibers (nylon/acrylic) – agent aesthetics Inorganic pigments - colour Self-cured PMMA (powder / grains) - polymer Methyl metacrylate - Benzoyl peroxide – initiator monomer Ti dioxide – opacifier for the Hydroquinone – inhibitor translucency control Ethylene glycol Dibutyl phtalate – plasticiser dimethacrylate or Synthetic fibers (nylon/acrylics) – other cross-linking aesthetics agent Inorganic pigments - colour Organic amine - accelerator Powder-Liquid system - advantages working is possible through a solid paste (dough); polymerization shrinkage is reduced comparing to the only use of monomer, because most of the material is already polymerized (grains from powder); the resulted temperature through the exothermal polymerization reaction (same reasons as for polymerization shrinkage); reducing the temperature will determine also thermal shrinkage of the material. Mixing technique A mixture of powder (P=polymer) with liquid (L=monomer) P:L ratio = 2:1 % weight = 1,6:1 % volume - More P = incomplete saturation of the P with L = a weak and porous material - More L= high polymerization shrinkage Mixing technique The mixture has 4 stages: - initial stage= mixture of the particles of P with L - sedimentation stage = ‘sandy’ consistency = immediately after mixing - “strings” formation stage= creamy appearance = the monomer has dissolved the exterior of the polymer beads; it’s like a fluid cream; it’s a ‘sticky’ mass which forms ‘strings’ of material sticking to the spatula - “dough” stage = a mouldable elastic dough; pasty, consistent material; = the monomer has entered inside the polymer beads, reducing the value of transition T and thus making them to be like plasticine = now the material should be packed into the mold Mixing technique Doughing time = the time taken to reach the dough stage = 20 min., it can be reduced through: - increasing environment T - increasing the P : L ratio - decreasing the polymer beads size - the presence of a plasticiser Working time ≥ 5 min (in this time the mixture is in the doughy state), increases through : - decreasing the environment T HEAT-CURED acrylic resins Composition Methyl methacrylate (monomer) clear, volatile liquid, aromatic smell, inflamable, bactericide insoluble in water, soluble in organic solvents boiling T at 100,30C it is chemically instable, has a spontaneous tendency to polymerize under heat and light influence (see storage conditions) over 650C it polymerize within its masse for storage one is adding a polymerization inhibitor : hydroquinone (under 1%) it can contain a cross-linking agent (ethylene glycol dimethacrylate) only if one wants to obtain a cross-linked polymer, non-thermoplastic !!!! AVOID contamination the liquid with powder!!!! Composition Polymethyl methacrylate (polymer) small beads or big globules - solid at room T - thermoplastic, softening T at 1250C, over this it will be dipolymerized - chemically stable - soluble in organic solvents, reduced water sorption - good stiffness and modulus of elasticity, but abrasion strength is very reduced - good optical properties, unlimited possibility of colouring, but in time it will become yellow (ageing of the PMMA under UV light action) Composition Polymethyl methacrylate (polymer) ❖ The presence of the cross-linking agent within liquid has positive effects for the new formed PMMA : - Transformation in cross-linked polymer, non-thermoplastic - It reduces the solubility in the organic solvents - It reduces the tendency of crazing (fissures) under pressure ❖ Presence of cross-linking agent simplifies the working technique through: - Acceleration of the increase of the molecular weight - Control the inhibitor effects of the O2 over the polymerization ❖ The amount of the cross-linking agent cannot be so much increased – become a brittle material (more stiff) Heat-curing ❖ the dough is introduced into mould through: - pressure - injection ❖ the polymerization of the monomer is induced by the T increase ❖ the mold is introduced in a steam bath with a T which is increasing continuously ❖ The most important elements of the heat-curing : › initiator (benzoyl peroxide - BPO)starts rapidly to decompose with free radicals formation if the T overpass 650C; › the polymerization reaction is exothermal; › if the T continues to increase and overpass 100,30C, the monomer will boil and will be evaporated = >porosities › one wants to obtain high CRs (conversion rates) of the monomer in to polymer - Slow polymerization: mold is placed in to cold water; in 1 hour the temp. is increased till 700C and is maintained here for 7 hours, followed by 3 hours at 1000C and then at a slow cooling (12 hours) - Rapid polymerization: mould placed in to cold water; during 1 hour the temp. is increased to 1000C and is maintained here 1 hour, followed by a slow cooling Rapid heat-curing (b) Slow heat-curing (a) Modifications of the T inside the mold Slow heat-curing/Slow polymerization the most part of the conversion of the monomer is being produced during the 7 hours at 700C at this water T, the mold’s temp. increases at 1000C (due to exothermal reaction) increasing the water T at 1000C assures a conversion rate of the monomer at almost 100% in those thin zones of the denture where the effect of the exothermal reaction is more reduced - Mistakes of the heat-curing - increasing too rapidly the T leads to lots of centers of polymerization –> polymer with short chains –> low mechanical properties - introducing of the mold directly in water at 1000C, at which will be added the exothermal polymerization reaction, it will determine increasing of the T of the mold at 1500C –> boiling of the monomer and its evaporation -with the air inclusions appearance (gaseous porosities) Properties of heat-cured acrylic resins Porosity Occurs through 2 mechanisms: › Porosity shrinkage (through polymerization) – polymer’s shrinkage -20% (volumetric) – residual polymer beads reduce the shrinkage to -5-8% – due to shrinkage can appear voids => pores – voids can be filled through the flow of the AR at its polymerization T, if there is pressure inside the mold (pressing the AR in the dough stage into mould) – reducing the voids through polymerization under pressure (heat-curing under pressure ) › Gaseous porosity (boiling and volatilization of the monomer) – avoided through slow and controlled increasing of the T (slow heat-curing) Properties of heat-cured acrylic resins Internal stress - initially the acrylate suffers a thermal expansion (heating of the mould), followed by the polymerization shrinkage and then followed by the cooling thermal shrinkage of the mold - a major internal stress which can be partially compensate through slow cooling of the mold Properties of heat-cured acrylic resins Internal stress The subsequent released internal stress determines minor defects on the surface of the denture (crazes=micro-cracks) CRAZE CRACK Dull zone, seems to be difficult to polish Reversible Irreversible Crazes increase in time –> fissures-> –> fractures Bringing the cross-linked agents inside the material reduces very much the risk of crazes’ appearance. Properties of heat-cured acrylic resins Internal stress Crazes occur by : – sudden thermal shrinkage (sudden/rapid cooling of the mold); – excessive heat during mechanical working and polishing; – unequal thermal shrinkage (use of AR for acrylic- metal restorations or ceramic teeth for dentures); – solvents’ attack (e.g. alcohol). Properties of heat-cured acrylic resins Mechanical properties - relatively reduced - lower hardness than the dentine – high rate of abrasion - tensile strength = 50MPa - reduced modulus of elasticity = elastic - extreme low fracture strength Dentures are susceptible to fractures (10% of them fracture in the first 3 years) Properties of heat-cured acrylic resins Mechanical properties Improvements of increasing fracture strength of an AR - C fibres –difficult handling, unaesthetic, so only on the oral sides of the artificial teeth and of the dentures - Kevlar fibres – inefficient because there isn’t adhesion with AR, unaesthetic - polypropylene fibres – neutral colour, biocompatible, good adhesion through certain treatments, but difficult packing - glass fibres – the most promising alternative, they cannot be directly packed within the polymer powder, or subsequently treated with a coupling agent to avoid injury of the soft tissues Properties of heat-cured acrylic resins Physical properties Thermal conductivity – reduced - problems during heat-curing – increases of the T - problems at the patient who have such complete maxillary dentures Coefficient of thermal expansion – high - a disadvantage at fixed partial dentures Water sorption (1-2% weight) - helps to compensate the shrinkage polymerization - slow– weeks till saturation – maintaining permanently the denture into a wet medium Solubility –enough high into organic solvents - more reduced for the cross-linked polymers - small phenomena of solubility of the constituents (residual MA, pigments) – losing of mass HIGH IMPACT Polymers - pressure technology of the paste into the mold - acrylic resins+ a rubbery phase mixed with polymer beads from the powder - Polymerization through inversion phase = dispersion of some rubbery islands + PMMAinto the continuous phase of the rubber - the liquid doesn’t contain a cross-linked agent because : - Rubber = - is opposing to crazes - increases the impact strength of the dentures - increases a lot the elasticity of the material – reducing of the stiffness of the denture – appearance of prosthetical injuries (=decubital ulcer=traumatic ulcer) SELF-CURED Polymers Indications: - repairs of fractured dentures - temporary full acrylic crowns made in the dental office - custom trays - impression-pattern of post and core, inlays, onlays Composition: Liquid: – dimethyl paratoluidine – role of activator Properties of Self-cured AR: Same properties as for heat-cured AR but with some differences : – slightly reduced hardness and stiffness – chromatic stability- reduced in time – high amount of residual monomer Self-curing - activated under the action of the activator from liquid - free radicals are formed starting from the benzoyl peroxide under the chemical action of the activator - polymerization speed is depending on activator/initiator ratio - exothermal reaction – affects the dental pulp - setting time can be influenced by the: - environment T (directly proportional) - the size of the polymer beads from powder (reduced dimension, many initiation centers – quicker polymerization) INJECTION MOLDED RESINS(IMR) General features Advantage: constant molecular weight Disadvantages: - reduced strength to crazing - difficulties to adhesion with the artificial teeth - expensive equipment Technology: - melting of the polymer powder and its injection into the mold 1. IM Acrylic resins Composition - Powder of linear PMMA, less residual monomer - without cross-linked PMMA, because would determine an exaggerate increase of melting T Technology - Slow melting and cooling – to avoid internal stresses - Adhesion between AR of the denture base and artificial teeth = mechanical adhesion - Insufficient molten material – dislocation of the artificial teeth - Overheating during melting = depolymerization - pores 2. IM Polycarbonate resins = alternatives for allergic patients to MA, Ni, Cr for complete/partial dentures Disadvantages: - depolymerization risk through explosion when overheating - no cross-linked polymer inside = crazes, it can be easily dissolved into solvents - adhesion problems with the artificial teeth 3. IM Polyamide resins (nylon) = alternatives to allergic patients to MA, Ni, Cr for complete/partial dentures = polymers obtained through condensation between a diamine and a diacid - nowadays: nylon reinforced with fibres or with crumbled glass particles Indications (i.e. Valplast, Flexite): -complete dentures -partial dentures -dental splints Advantages: -Flexible -High impact strength -Biocompatibility (they don’t have residual monomer) -Translucency -Lack of polymerization shrinkage Disadvantages: -Maintained only by anatomical undercuts areas -Severe decubital ulcer -Reduced strength to appearance and propagation of crazes -High porosity –water sorption -Mechanical adhesion with the artificial teeth -They don’t support any appliance of tissue conditioners LIGHT CURED ACRYLIC RESINS Composition -CR(Composite resins) = organic matrix (UDMA and acrylic copolymer) + inorganic filler (colloidal silica) Indications -complete denture bases Technology -Fitting of the plates over the functional cast -Light-curing -Acrylic artificial teeth subsequently added with extra amounts of light- cured composite resin - Other uses of AR : - Artificial teeth - Temporary crowns and dental bridges - Metal-acrylic restorations – only mechanical adhesion - Orthodontic devices - Surgical prosthesis - Resilient materials used as soft liners of dentures