Różnice i podobieństwa między kauczukiem a gumą PDF
Document Details
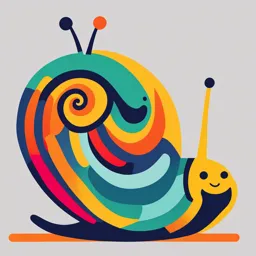
Uploaded by SuperbTrust
Tags
Summary
Ten dokument porównuje i kontrastuje kauczuk i gumę, omawiając ich elastyczność, zastosowania i właściwości. Omawia również proces wulkanizacji i zastosowanie gumy jako materiału konstrukcyjnego. Dokument zawiera również informacje dotyczące różnych metod przetwarzania kauczuku.
Full Transcript
**1. Różnice i podobieństwa między kauczukiem a gumą.** Różnice ---------------------------------------------------------------------------------------------------- ------------------------------------...
**1. Różnice i podobieństwa między kauczukiem a gumą.** Różnice ---------------------------------------------------------------------------------------------------- ------------------------------------------------------------------------------------ Kauczuk Guma Polimer naturalny lub syntetyczny, całkowicie rozpuszczalny w odpowiednio dobranym rozpuszczalniku Produkt usieciowania (wulkanizacji) kauczuku Możliwość ruchów translacyjnych całych makrocząsteczek Brak ruchów translacyjnych, ograniczone pełzanie Zdolność do płynięcia i pełzania Ograniczone pełzanie i relaksacja Makrocząsteczki są powiązane między sobą za pomocą poprzecznych wiązań chemicznych Podobieństwa: - **Elastyczność**:\ Zarówno kauczuk, jak i guma są materiałami elastycznymi, co oznacza, że po rozciągnięciu wracają do swojego pierwotnego kształtu. - **Zastosowanie**:\ Oba materiały znajdują zastosowanie w produkcji przedmiotów takich jak opony, uszczelki, węże, taśmy i inne produkty wymagające wytrzymałości i elastyczności. - **Podobne składniki chemiczne**:\ Zarówno kauczuk naturalny, jak i syntetyczny (który jest podstawą większości gum) są polimerami, składającymi się głównie z węglowodorów. - **Proces wulkanizacji**:\ Zarówno kauczuk, jak i guma mogą być poddane wulkanizacji (procesowi polegającemu na dodaniu siarki), co poprawia ich właściwości, takie jak odporność na temperatury czy ścieranie. **2. Guma jako materiał konstrukcyjny. Wymienić i opisać charakterystyczne właściwości.** - ELATYCZNOŚĆ - zdolność do dużych (nawet \> 1000 %) odwracalnych (elastycznych) odkształceń w szerokim przedziale temperatury (170 - 570 K), pod działaniem niewielkich naprężeń - ZDOLNOŚĆ DO GROMADZENIA, pochłaniania i rozpraszania ENERGII - izolatory, dielektryki, półprzewodniki, guma przewodząca - NIEROZPUSZCZALNOŚĆ w żadnym rozpuszczalniku - guma jedynie pęcznieje w określonym stopniu w cieczy - DOBRE WŁAŚCIWOŚCI MECHANICZNE - wytrzymałość na rozciąganie, odporność na ścieranie, rozdzieranie, twardość, odkształcenie trwałe, sztywność (moduł) - PRZEPUSZCZALNOŚĆ PAR I GAZÓW - mała lub bardzo mała - ODPORNOŚĆ ELEKTRYCZNA I NA PRZEBICIE - stal zwykła - 1-10 J/kg (1 J/l); stal specjalna - 300 J/kg (40 J/l), drewno - 360 J/kg (360 J/l); guma - 44000 J/kg (44000 J/l) - ODPORNOŚĆ NA DZIAŁANIE MEDIÓW TECHNICZNYCH - odporność na paliwa, oleje, smary, płyny techniczne, substancje chemiczne - ŁATWE ŁĄCZENIE Z INNYMI MATERIAŁAMI KONSTRUKCYJNYMI - z metalami, materiałami konstrukcyjnymi - ŁATWOŚĆ NADAWANIA DOWOLNEGO KSZTAŁTU - duże, zróżnicowane kształty, w relatywnie prosty sposób **3. Metody dekrystalizacji kauczuków.** - Klasyczne NR: twarde, sztywne i nie nadają się w tej formie do dalszego przetwarzania. Charakteryzują się zbyt dużą lepkością lub za małą plastycznością, a w okresie zimowym dodatkowo znacznym udziałem fazy krystalicznej. - uszkodzenie urządzeń przetwórczych - konieczność wstępnego przygotowania NR Przebieg: krystalizacja rozpoczyna się z dużą szybkością podczas składowania w t \< 10 oC, natomiast topnienie krystalitów przebiega z dużą szybkością w t \~ 40-45 oC. Technicznie dekrystalizację przeprowadza się ogrzewając całe baloty NR w taki sposób, aby temperatura w ich wnętrzu osiągnęła 40-45 oC, w tej T szybkość dekrystalizacji jest dużą. Zależnie od sposobu ogrzewania i stosowanego urządzenia: czas od kilku minut do kilkunastu godz. Metody techniczne dekrystalizacji NR: ❑ okresowa przechowywanie w komorach/tunelach powietrznych ogrzewanych przeponowo parą wodną, temperatura powietrza 50-70 oC; wyższa nie jest zalecana ze względu na niebezpieczeństwo znacznego utlenienia powierzchniowych warstw NR; czas: nawet kilkadziesiąt godz. ❑ ciągła przepuszczanie balotów NR przez tunele, wyposażone w transportery, tunele ogrzewane przeponowo parą wodną, krótszy czas ❑ okresowa lub ciągła ogrzewanie balotów NR za pomocą prądów wysokiej częstotliwości, czas dekrystalizacji 3 - 5 min, bo ogrzewanie następuje w całej masie balotu (drgania dipoli wewnętrznych), a nie na skutek przewodnictwa cieplnego NR. Postęp dekrystalizacji bada się wciskając w baloty NR termoparę igłową o określonej średnicy, z odpowiednim ostrzem (opór, temperatura), z odpowiednią siłą. Dopiero po dekrystalizacji NR można kierować do dalszych operacji przetwarzania (cięcie, mastykacja, sporządzanie mieszanek) **4. Mastykacja kauczuków. Istota procesu i metody jej przeprowadzania.** Wprowadzenie do kauczuku odpowiedniej ilości napełniaczy oraz sporządzenie mieszanki kauczukowej o określonej charakterystyce przetwórczej wymaga zastosowania kauczuku o określonej plastyczności/lepkości. Im bardziej plastyczny kauczuk (mniejsza lepkość), tym lepiej i szybciej zwilża on inne składniki, ale tym trudniej dyspergują one potem w elastomerze, co wynika z wielkości możliwych do osiągnięcia sił ścinających τ, proporcjonalnych do lepkości środowiska η, a ta związana jest z ciężarem cząsteczkowym Mw : η \~ Mw 3,4 Im kauczuk bardziej twardy, mniej plastyczny, tym łatwiej dyspergują w nim napełniacze, ale tym większe zużycie energii, większy przyrost temperatury podczas mieszania, problemy z bezpieczeństwem przerobu. STOSOWANE OBECNIE TECHNICZNE METODY MASTYKACJI: \* mastykacja zimna (t \< 90 ^o^C) w nieobecności peptyzatorów, realizowana za pomocą walcarek, \* mastykacja gorąca (t \> 120-130 ^o^C) w obecności peptyzatorów, prowadzona w mieszarkach zamkniętych. Cechy charakterystyczne zimnej mastykacji: \* duża szybkość uplastyczniania na początku procesu, silnie malejąca z czasem uplastyczniania w atmosferze powietrza; \* podobny efekt można osiągnąć poddając NR obróbce mechanicznej w atmosferze beztlenowej, w obecności zmiataczy wolnych rodników; \* efekt mastykacji w atmosferze ściśle beztlenowej jest nieznaczny; \* skończona, osiągalna wartość plastyczności, a zatem i M~av~, pomimo przedłużania czasu zimnej mastykacji; \* ujemny współczynnik temperaturowy reakcji chemicznej (pękanie wiązań w łańcuchu głównym); \* podczas mastykacji do NR przyłącza się \< 0,4 % O~2~ (zmiatacza wolnych rodników), ale ciepło spalanie bez zmian; zatem małe zmiany struktury; \* w mastykowanych kauczukach powstają ugrupowania o budowie hydro-nadtlenków i produkty ich dalszych przemian; \* szybkość uplastyczniania zależy od gradientu szybkości ścinania. MASTYKACJA NA ZIMNO JEST REALIZOWANA (W PRZEMYŚLE): za pomocą walcarek przy frykcji 1: (1,25-1,3), opłacalna jedynie przy małej produkcji, kauczuk podawany w małych kęsach, przy wąsko zestawionych, dobrze chłodzonych walcach, NR zdekrystalizowany; uplastycznianie 3-5 min przy małej szczelinie, potem przy większej; czas 10-15 min; przedłużenie może doprowadzić do zbytniego uplastycznienia; ścinanie i przekładanie przyśpiesza mastykację MASTYKACJA GORĄCA W OBECNOŚCI PEPTYZATORÓW: Peptyzatory: substancje chemiczne ułatwiające mastykację na gorąco. Korzyść: zmniejszenie zużycia energii, skrócenie czasu i zwiększenie wydajności urządzeń, jednolite właściwości mastykatu. Stosowane peptyzatory, dawki 0,25 --0,75 phr: pentachlorotiofenol, sól cynkowa pentachlorotiofenolu, disiarczek 2,2'-dibenzamidodifenylowy. Inne substancje o działaniu peptyzującym: - związki nitrozowe; - kwasy dialkiloditiokarbaminowe i ich sole; - niektóre przyspieszacze (MBT, DBTS, sulfenamidy) i nadtlenki. Techniczne uplastycznianie (mastykacja) na gorąco: \* mieszarki zamknięte, czas kilka min, w obecności peptyzatorów; znacznie większa szybkość mastykacji ze względu na większe szybkości rotorów i większe gradienty szybkości ścinania, bardziej równomierne właściwości (powtarzalność); wytłaczarki ślimakowe/dwuślimakowe. **5. Parametry wpływające na lepkość kauczuków.** LEPKOŚĆ (A ZATEM I PLASTYCZNOŚĆ ) KAUCZUKÓW ZWIĄZANA JEST Z: - budową chemiczną makrocząsteczek i występującymi w nich oddziaływaniami kohezyjnymi (van der Waalsa), w tym pomiędzy grupami polarnymi lub polaryzowalnymi; kauczuki polarne mają zawsze większą lepkość niż kauczuki niepolarne o tej samej M~av~ - wielkością M~av~ i jej dyspersją - giętkością makrocząsteczek związaną m. in. z mikrostrukturą łańcucha - temperaturą i szybkością ścinania podczas przetwórstwa - obecnością zmiękczaczy i/lub napełniaczy w kompozycji **6. Cele sporządzania i parametry technologiczne mieszanek kauczukowych.** Cele sporządzania mieszanki kauczukowej (poza samym wytworzeniem): optymalne i powtarzalne zdyspergowanie składników mieszanki, z punktu widzenia zbioru właściwości charakteryzujących mieszankę jako produkt. wytworzenie materiału o określonych cechach technologicznych (lepkość i płynność, wytłaczalność, kalandrowalność, wulkanizacja itp.); niska tendencja (lub jej brak) do migracji składników na powierzchnię kompozycji podczas magazynowania lub przetwarzania. Parametry technologiczne wpływające na sporządzanie mieszanek kauczukowych i efektywność procesu: ❖ rodzaj maszyny; decyduje o intensywności ścinania, związanej z szybkością części roboczych (walcarki, mieszarki zamknięte -- urządzenia o działaniu okresowym); wytłaczarkomieszarki (działanie ciągłe); ❖ osiągalne wielkości sił rozpierających (← sztywność materiału); ❖ lepkości kauczuku i mieszanki kauczukowej w warunkach mieszania. **7. Sporządzanie mieszanki kauczukowej za pomocą walcarki -- schemat urządzenia, opis** **działania, wady i zalety procesu. Etapy sporządzania mieszanki kauczukowej.** DZIAŁANIE WALCARKI: Elementy robocze: dwa walce o średnicy D i długości części roboczej L, obracające się z różną szybkością, a zatem w układzie frykcyjnym. W przestrzeni pomiędzy łukami chwytu i powierzchniami bocznymi walców (kotlina walcownicza) na obrabiany materiał działa siła normalna N dociskająca mieszankę do powierzchni walca oraz siła ściskająca P mieszankę. Wypadkowa tych sił W wciąga mieszankę do kotliny walcowniczej, jeśli oczywiście siła tarcia W = T. f jest większa od siły reakcji W' usiłującej wyrzucić mieszankę z kotliny walcowniczej, przy f -- współczynnik tarcia mieszanki o powierzchnię walca, f = k(V, T, skład). Ze względu na odmienną szybkość obwodową walców oraz istnienie gradientu prędkości w wejściu do kotliny walcowniczej mieszanka podlega działaniu pary siły i momentu obrotowego, co prowadzi do obrotów warkocza mieszanki, a w kotlinie mieszanka podlega dodatkowo ścinaniu i ściskaniu. Pod wpływem tych naprężeń pojawiają się odkształcenia postaciowe, co przy wielokrotnym przejściu mieszanki przez kotlinę prowadzi w efekcie do wchłonięcia i zdyspergowania składników. Etapy sporządzanie mieszanki za pomocą walcarki (standardowo): 1\. załadunek i uplastycznianie kauczuku aż do utworzenia jego ciągłej warstwy na powierzchni walca przedniego, 2\. wprowadzenie aktywatorów i przeciwutleniaczy, 3\. wprowadzenie 1. porcji napełniaczy wzmacniających, 4\. wprowadzenie części zmiękczaczy, 5\. wprowadzenie w 2-3 porcjach reszty napełniaczy i zmiękczaczy, 6\. wprowadzenie przyspieszaczy i innych składników, homogenizacja, 7\. wprowadzenie siarki (substancji sieciującej), 8\. płytowanie, zdjęcie z walców i ewentualne ochłodzenie mieszanki. Podczas sporządzania mieszanka jest okresowo ścinana z każdej ze stron i przekładana → intensyfikacja procesu. Niekiedy kolejność wprowadzania i mieszania składników może być odmienna od standardowej. Uwarunkowania: ❖ konieczne chłodzenie walców i utrzymywanie ich odpowiedniej temperatury; ❖ ważną wielkością jest frykcja walców (\< 1 : 1, 25), ❖ szerokość szczeliny (decyduje o intensywności procesu). Czas sporządzania mieszanki za pomocą walcarki: t = 10 -- 45 min. WADY: ✓ okresowy charakter pracy i trudne warunki BHP, pylenie, powstawanie ładunków elektryczności statycznej, ✓ znaczny wpływ czynników subiektywnych/personalnych, zatem umiarkowana powtarzalność właściwości mieszanki, bo duży rozrzut właściwości reologicznych i przerobowych, w tym kinetyki wulkanizacji, ✓ mała wydajność (200- 300 kg/h). DLATEGO: Obecnie mieszanki kauczukowe sporządza się najczęściej za pomocą mieszarek zamkniętych z tłokiem dociskowym (stemplem). ZALETY: - **Kontrola temperatury** -- zapobieganie degradacji składników. - **Uplastycznianie kauczuku** -- łatwiejsze przygotowanie do dalszej obróbki. - **Regulacja grubości** -- możliwość ustawienia żądanej grubości arkusza. - **Wizualna kontrola** -- bieżąca ocena jakości mieszanki. - **Wszechstronność** -- nadaje się do różnych typów kauczuku i dodatków. - **Niższe koszty operacyjne** -- prostsza i tańsza w obsłudze niż inne urządzenia. **8. Sporządzanie mieszanki kauczukowej za pomocą mieszarki -- schemat urządzenia, opis działania, wady i zalety procesu. Etapy sporządzania mieszanki kauczukowej.** **[Schemat budowy i opis działania ]** - Dwa wirniki (rotory)- rozwinięta przestrzeń powierzchni, łożyskowe, toczne, ślizgowe, obrót w przeciwnych kierunkach wewnątrz komory mieszarki, wymuszają cyrkulację materiału w komorze \- komora mieszarki zamykana od góry za pomocą ruchomego tłoka dociskowego \- system regulacji temperatury komory i wirników \- układ podnoszenia i opuszczania tłoka dociskowego \- układ otwierania i zamykania luku rozładowczego \- układ napędu i sterowania napędem \- urządzenia współpracujących z mieszarka ( silosy, zbiorniki do przechowywania składników, dozowniki i wagi, urządzenia do płytowania mieszanki po wyładowaniu). Etap sporządzania mieszanki kauczukowej : 1. W tłoku podniesionym -- załadować kauczuk, aktywatory, i substancję przeciwst. 2. Tłok opuszczony- uplastycznienie kauczuku i wyrobienie składników 3. Podniesienie tłoka- wprowadzenie części napełniaczy 4. Opuszczenie tłoka -- wrobienie napełniaczy 5. Wprowadzenie części zmiękczaczy 6. Wprowadzenie reszty n. i z. 7. Homogenizacja mieszanki -wprowadzenie pozostałych składników 8. Otwarcie łuku rozładowczego -- opróżnienie komory mieszanki 9. S.s zwykle na etapie płytkowania -- płytkowanie mieszanki za pomocą walcarki +-----------------------------------+-----------------------------------+ | **Wady procesu przy użyciu | **Zalety procesu przy użyciu | | mieszarek** | mieszarek** | +===================================+===================================+ | ✓ nierównomierne mieszanie | - Lepsze warunki pracy, | | | wydajność | | - Wysoka temperatura | | | | - Lepsza powtarzalność | | - Wysokie zużycie energii | właściwości mieszanki | | | | | ✓ ograniczenia z rodzajem | - Mechanizacja i automatyzacja | | wykorzystania materiałów | pracy | | | | | | - Czas cyklu 1,5- kilka min | +-----------------------------------+-----------------------------------+ **9. Istota kalandrowania i schematy drogi mieszanki kalandrowanej. Parametry wpływające na pracę kalandra i kalandrowanie**. *[Istota i schemat ]* Proces technologiczny formowania płyt lub folii mieszanki kauczukowej o określonej grubości lub wzorzystej powierzchni. Ciągły proces technologiczny pokrywania tanin/ dzianin mieszanką. Kalandry o 3,4,5 walcach. Budowa walców- analogiczna do walcarek, większa gładkość beczki. Przetwarzana mieszanka podlega odkształceniom plastycznym na długości części roboczej walca kalandra L o średnicy D, w kotlinie walcowniczej, w strefie odkształceń plastycznych. Warunki rzeczywiste: układ frykcyjny, bezfrykcyjny. Gradient prędkości- powoduje pojawienie się momentu obrotowego (moment siły) w szczelinie pomiędzy walcami kalandra i obracanie się tzw. warkocza obrabianego materiału. Można wytworzyć płyty mieszanki kauczukowej o stałej grubości Regulacja temperatury i grubości folii. Urządzenia pomocnicze: \- zasilające ciągle i równomiernie kalander podgrzaną mieszanką \- urządzenia odbierające płytę lub folie mieszanki \- urządzenia do chłodzenia kalandrowanie płyty \- urządzenie do zbierania ładunków elektryczności statycznej z powierzchni wykalandrowanej płyty lub folii *[Droga mieszaki kalandrowej]* Układy walców i operacje wykonywane za pomocą kalandrów: \- płytowani mieszanek (kalandry płytujące bez frykcji) \- profilowanie mieszanek (kalandry profilujące) \- okładanie tkanin mieszanką (kalandry okładowe) -frykcjonowanie tkanin/kordu mieszanką \- zdwajanie (dublowanie) płyt (kalandry zdwajające) *[Parametry wpływające na pracę kalandra i kalandrowanie]* 1. właściwości reologiczne mieszanki (lepkość) 2. zawartość kauczuku w mieszance (im jej więcej tym gorsze kalandrowanie, większy skurcz) 3. równomierność zasilania kalandra podgrzaną/ bardzo plastyczną mieszanką 4. szybkości obwodowe walców (szybkość kalandrowania \