Hoshin Planning - PDF
Document Details
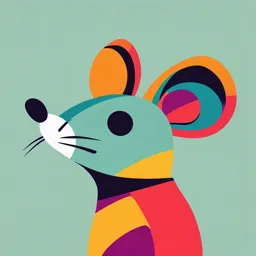
Uploaded by AdventuresomeBoolean
BITS Pilani, Pilani Campus
Tags
Summary
This document discusses Hoshin planning, a strategic planning methodology for organizations. It covers various aspects, including what planning is, why it's important, challenges in planning, the Hoshin planning system, its four phases: generation, deployment, implementation, and evaluation. The document also details related concepts like PDCA, standardization, visual management, teamwork, and the importance of continuous improvement.
Full Transcript
HOSHIN PLANNING OBJECTIVES o What is planning? o Why plan? o Problems with planning o Hoshin planning system o 4 phases of Hoshin planning system WHAT IS PLANNING? Planning means answering two questions: ◾Where are we going? ◾How do we get there? The road me...
HOSHIN PLANNING OBJECTIVES o What is planning? o Why plan? o Problems with planning o Hoshin planning system o 4 phases of Hoshin planning system WHAT IS PLANNING? Planning means answering two questions: ◾Where are we going? ◾How do we get there? The road metaphor Why plan? To develop a shared vision of where we are going and how we will get there. To improve as individuals and as an organization To compel renewal and reinvention To learn Effective planning compels us to take stock of our strengths and weaknesses and to take countermeasures. Planning also bursts the bubble of complacency by continually setting breakthrough goals. ◾Unrealistic forecasts or expectations; the planning process is too rigid to adapt to changing conditions. ◾Goals are set arbitrarily with no clear link to need, means, or feasibility. ◾Too many goals; inadequate focus. ◾Wrong goals. ◾Goals are not SMART. PROBLEMS ◾Planned activities are not regularly reviewed; disconnect in time. WITH ◾Planned activities are reviewed punitively. ◾Planning is regarded as an event rather than an ongoing process. PLANNING ◾Planning is done in the absence of data. ◾Data is overanalyzed. ◾A separate department does planning. ◾ Inadequate communication between and within departments; horizontal and vertical alignment disconnect. ◾ The management team is reluctant to take stock of strengths and weaknesses HOSHIN PLANNING Hoshin kanri means ◾ Shining metal or compass ◾ Ship in a storm on the right path ◾ Strategic policy deployment Hoshin kanri or hoshin planning is the nervous system of Lean production. Hoshin planning is the short-term (one year) and long-term (three to five years) process used to identify and address critical business needs and develop the capability of our people, achieved by aligning company resources at all levels and applying the PDCA cycle to achieve critical results consistently. FOCUS OF HOSHIN PLANNING Hoshin planning targets the critical few problems, the big boulders on our road which are the key to improvement. Plan-do-check-act Nemawashi HOSHIN PLANNING Catchball SYSTEM Control department concept A3 thinking PDCA Hoshin planning comprises overlapping PDCA cycles ◾ Macro (three to five years): Practiced by senior management ◾ Annual: Practiced by operating managers ◾ Micro (weekly, monthly, and biannual): Practiced by operating managers and their subordinates PDCA PDCA requires supportive management systems that make the current status visible to all and compel countermeasures. These can include both formal and informal reviews. Formal reviews should be held every six months (at the beginning of the year, midyear, and year-end). The year-end review entails a summary of what happened and informs next year’s strategic plan (which is presented in January) Less formal reviews can include ◾ Daily status reports shared by the management team ◾ Weekly management team meetings wherein department heads report status ◾ Shop floor process reviews of hot items PDCA also requires a solid understanding of metrics and visual management. SMART goals must be developed both for outcomes and the process. Control panels or dashboards need to be generated on a daily basis with minimal effort. Visual systems such as report boards and line-side process reviews help to create a shared understanding of the data. NEMAWASHI To prepare a tree for transplanting Connects the process of consensus building that creates alignment. Nemawashi entails reviewing a hoshin with all affected customers before its implementation. Nemawashi involves numerous revisions based on customer feedback. CATCH BALL Catchball refers to the give and take required between and among management levels during the planning process. The catchball seeks to link the vision of the officers and the daily activities of shop floor team members. 1. Company officers develop a vision of what the organization needs to do, and capabilities that need to be developed. They “toss” the vision to senior managers. 2. Senior managers “catch” the officers’ vision and translate it into hoshins. Then they toss them back to the officers, and ask, in effect, “Is this what you mean? Will these activities achieve our vision?” 3. Officers provide feedback and guidance to senior managers. The hoshins can be passed back and forth several times. 4. Eventually a consensus is reached. Officers and senior managers agree that, “These are the hoshins that our company will use to achieve our vision.” 5. Senior managers now toss their hoshins to middle managers, who catch them and translate them into activities. These in turn are tossed back to senior managers who provide feedback and guidance. Eventually, a consensus is reached. Senior and middle managers agree that, “These are the activities (hoshins) we will use to achieve the senior managers’ hoshins, which in turn will achieve our company vision.” 6. Middle managers will in turn toss their hoshins to their subordinates. CONTROL DEPARTMENT The control department, in this case quality, would coordinate the cross- functional activities required to achieve company goals. This includes ◾ Leading the hoshin planning process for quality ◾ Leading the setting of goals and means (through nemawashi and catchball) ◾Applying PDCA at the micro and annual level to confirm success ◾Making problems visible and supporting countermeasure activity A3 THINKING There are now four kinds of A3s: Hoshin planning A3: Used to summarize department and company Hoshins Problem-solving A3: Used to summarize problems and countermeasures Proposal A3: Used to present new ideas Current status A3: Used to summarize current condition of a hoshin, problem, or concern A3 THINKING To make Hoshin Planning work, it is important that A3 Thinking combines scientific methods with “telling the managers do not accept their leader’s Hoshin story”. It can be used for planning, problem solving, proposals without questioning. Leaders should not attempt and summarizing current status of conditions. Combining with to deploy without verifying their subordinates the “Tools of Quality” can increase the effectiveness of the understanding and support of the plan. Review of presentation. Dennis discusses the benefits of standardizing the plans on a routine basis is critical to their and shortening reports. success. Dennis shared his amazement the first Departmental scoreboards can display departmental metrics time he was informed that he had a bi-monthly 2 and summaries to drive their performance. Visualizing their hr. Hoshin review scheduled with his superior, Mr. plan and activities makes it is easy for staff and management Cho. Obviously, their plans weren’t going to sit on to get a feel for what they are doing and verify their alignment the shelf and collect dust. Hoshin follow through with top level activities. can also be audited as part of the PDCA check process. Telling stories with A3 Thinking Example of a Problem solving A3 A3 REPORT Strategic planning Current status Hoshin generation Hoshin deployment 4 PHASES OF HOSHIN PLANNING Hoshin implementation Final evaluation Hoshin Generation means setting the annual goals of a company and its departments. HOSHIN GENERATION Goals address both processes and outcomes and are usually developed by senior management in consultation with their subordinates. This entails establishing lower-level goals and plans, both within and across departments, through nemawashi and catchball. HOSHIN DEPLOYMENT Each level must translate the hoshin goal and means into meaningful action. Subordinates should not accept the leader’s hoshin without question. This refers to the management activities required to implement the hoshins developed and involves applying the various PDCA cycles. HOSHIN IMPLEMENTATION There should be both formal and informal reviews throughout the year to make the current status and countermeasures visible. This refers to the year-end assessment of each hoshin. HOSHIN EVALUATION Were process and outcome goals achieved? If so, ask why five times. If not, also ask why five times. What did we learn? How can we strengthen our capabilities? This is what it means to be a learning organization. LEAN CULTURE OBJECTIVES o What is lean culture? o PDCA o Standardization o Visual management o Team work oParadox o Intensity & do of lean culture o How does lean culture feel? ◾The day-to-day experience of our team members ◾Current behavior Day-to-day experience and behavior in each includes the following: ◾ Plan-do-check-act What is lean ◾ Standardization culture? ◾ Visual management ◾ Teamwork ◾ Paradox ◾ Intensity ◾ The do concept PDCA GTS – grasping the situation, big picture, key parts, what is-should happen, trends, value-goal-related. ◦ Plan – 5Ws + 1H, measurement plan, visual system ◦ Do – contains its own PDCA cycle with pilot activities; assessment of team capabilities, assess current condition. ◦ Check – metrics to check outcome (final score) and process (along the way). Go see what is happening. ◦ Act – reflect on our condition, standardize when outcomes are on-target, make countermeasures – when outcome or process results are substandard. (stop bleeding or root cause) A manager’s job is to practice and teach PDCA, do it in the day-to-day. Warm Heart Principle – Hard on problem, easy on people. Standard – the best current method, but is meant to continually change. Standards make out-of-standard conditions obvious. STANDARDIZATION A problem is a deviation from a standard (gap). Problem-solving funnel Five Why’s (should get at root cause), which is usually: inadequate standards, inadequate adherence to standard, or inadequate system. VISUAL MANAGEMENT Visual management triangle Management as theatre – make problems visible Line-side process reviews Safety or quality “auctions” presentation (attendees can ask questions, give advice, offer to help investigation) Current condition presentations Hoshin (strategic) planning presentations Safety first – core Employment value, like security – last productivity & choice quality Uniforms – same No executive TEAMWORK regardless of position offices and no walls No executive Genchi genbutsu dining rooms or (Go see) – shop parking floor Jidoka – Stop production so that production never has to stop. Standards – change all the time. One-at-a-time production – is more effective than batch production. PARADOX Maximizing unit efficiencies – does not maximize overall efficiency. Don’t make something - unless a customer has ordered it. Team members – not industrial engineers, develop standardized work. Seek perfection – even though we know we will never achieve it. (humility) INTENSITY & “DO” OF THE LEAN CULTURE Intensity (more and greater The “do” concept is a “path” or a demands) “way” compels recognizing muda (waste) and kaizen Humility (make small improvements). Lifelong learning Recognize strain Respect for people Provide support and training Maintain intensity of improvement How does lean culture feel? ◾ Disciplined ◾ Freewheeling ◾ Warm ◾ Indomitable PDCA provides both scientific discipline and the freewheeling spirit of inquiry that asks: “How can we do this better?” Respect for people creates pleasing warmth and camaraderie. Team members interact as equals. “Them versus us” does not exist. Meeting daunting challenges year after year gives us confidence in the future. This then is the culture of Lean production, the soil in which this remarkable system thrives. In your Lean implementation efforts, please reflect on these ideas and take action to improve. The Toyota Way - 14 Management Principles The Toyota Way 14 Management Principles 1 2 3 4 5 6 7 8 9 10 11 12 13 14 Reference: The Toyota Way, by Jeffrey Liker The Toyota Way - 14 Management Principles 14 13 ❑ Principle 1 12 Base your management decisions on a long- 11 term philosophy, even at the expense of 10 short-term financial goals. 9 8 7 6 5 4 3 2 1 The Toyota Way - 14 Management Principles 14 13 ❑ Principle 2 12 Create a continuous process flow to bring 11 problems to the surface. 10 9 8 7 6 5 4 3 2 1 The Toyota Way - 14 Management Principles 14 13 ❑ Principle 3 12 Use “pull” systems to avoid overproduction. 11 10 9 8 7 6 5 4 3 2 1 The Toyota Way - 14 Management Principles 14 13 ❑ Principle 4 12 Level out the workload (heijunka). (Work like 11 the tortoise, not the hare.) 10 9 8 7 6 5 4 3 2 1 The Toyota Way - 14 Management Principles 14 13 ❑ Principle 5 12 Build a culture of stopping to fix problems, to 11 get quality right the first time. 10 9 8 7 6 5 4 3 2 1 The Toyota Way - 14 Management Principles 14 13 ❑ Principle 6 12 Standardized tasks and processes are the 11 foundation for continuous improvement and 10 employee empowerment. 9 8 7 6 5 4 3 2 1 The Toyota Way - 14 Management Principles 14 13 ❑ Principle 7 12 Use visual control so no problems are hidden. 11 10 9 8 7 6 5 4 3 2 1 The Toyota Way - 14 Management Principles 14 13 ❑ Principle 8 12 Use only reliable, thoroughly tested 11 technology that serves your people and 10 processes. 9 8 7 6 5 4 3 2 1 The Toyota Way - 14 Management Principles 14 13 ❑ Principle 9 12 Grow leaders who thoroughly understand the 11 work, live the philosophy, and teach it to 10 others. 9 8 7 6 5 4 3 2 1 The Toyota Way - 14 Management Principles 14 13 ❑ Principle 10 12 Develop exceptional people and teams who 11 follow your company’s philosophy. 10 9 8 7 6 5 4 3 2 1 The Toyota Way - 14 Management Principles 14 13 ❑ Principle 11 12 Respect your extended network of partners 11 and suppliers by challenging them and 10 helping them improve. 9 8 7 6 5 4 3 2 1 The Toyota Way - 14 Management Principles 14 13 ❑ Principle 12 12 Go and see for yourself to thoroughly 11 understand the situation (genchi genbutsu). 10 9 8 7 6 5 4 3 2 1 The Toyota Way - 14 Management Principles 14 13 ❑ Principle 13 12 Make decisions slowly by consensus, 11 thoroughly considering all options; 10 implement decisions rapidly (nemawashi). 9 8 7 6 5 4 3 2 1 The Toyota Way - 14 Management Principles 14 13 ❑ Principle 14 12 Become a learning organization through 11 relentless reflection (hansei) and continuous 10 improvement (kaizen). 9 8 7 6 5 4 3 2 1 The Toyota Way - 14 Management Principles Reference: The Toyota Way, by Jeffrey Liker.