Cleanroom Introduction & Classification PDF
Document Details
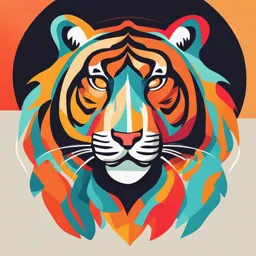
Uploaded by SpiritualAbundance9099
Universiti Malaya
Dr. Auni Hamimi Idris
Tags
Related
- Biosafety in Biomanufacturing (v6 updated) PDF
- Microcontamination and Cleanroom Control PDF
- Contamination - Innopharma Education PDF
- Assessment 2 Cleanroom & Pharmaceutical Industry
- Applied Microbiology/Pharmaceutical Microbiology and Cleanroom Technology PDF
- Pharmaceutical Environmental Control Tutorial PDF
Summary
This document provides an introduction to cleanrooms, covering their concept, regulatory standards, and classification according to ISO standards and PIC/S guidance. It explores the importance of cleanrooms in pharmaceutical manufacturing, discussing contaminants, control strategies, and barrier technologies.
Full Transcript
INTRODUCTION & CLASSIFICATION OF CLEAN ROOM Dr. Auni Hamimi Idris LEARNING OUTCOME By the end of this lesson, students should be able to: Understand the concept of cleanrooms Familiarize himself with the regulatory standards for cleanrooms ...
INTRODUCTION & CLASSIFICATION OF CLEAN ROOM Dr. Auni Hamimi Idris LEARNING OUTCOME By the end of this lesson, students should be able to: Understand the concept of cleanrooms Familiarize himself with the regulatory standards for cleanrooms The oversight The on-going monitoring of controls The confidence in controls The pillars of controls The foundations PDA TR90: contamination Control Strategy Development in Pharmaceutical Manufacturing Let’s do some activities – in pair Upload a picture of you and your partner List THREE potential sources of contaminants in a pharmaceutical manufacturing facility. State ONE way to reduce the risk of contamination from entering our product during manufacturing. Why do we need cleanrooms? Chapter 3 – Principle: Premises and equipment must be located, designed, constructed, adapted and maintained to suit the operations to be carried out. Their layout and design must aim to minimise the risk of errors and permit effective cleaning and maintenance in order to avoid cross- contamination, build-up of dust or dirt and, in general, any adverse effect on the quality of products Chapter 5.21: Design of manufacturing process, premises and equipment to minimize risk for cross- contamination during processing, maintenance and cleaning. PHARMACEUTICAL INSPECTION CO-OPERATION SCHEME, GUIDE TO GOOD MANUFACTURING PRACTICE FOR MEDICINAL PRODUCTS PART I PE009-17, Aug. 2023 What is a cleanroom? Definition Standard A room in which the concentration of airborne particles is (US Federal controlled to specific limits. Standard 209) A room with control of particle contamination, constructed (British Standard and used in such a way as to minimize the introduction, 5295) generation and retention of particles inside the room and in which the temperature, humidity and pressure shall be controlled as is necessary. Room in which the concentration of airborne particles is (ISO standard controlled, and which is constructed and used in a manner to 14644-1) minimize the introduction, generation, and retention of particles inside the room and in which other relevant parameters, e.g. temperature, humidity, and pressure, are controlled as necessary What is a cleanroom? A cleanroom is a room, which is designed, maintained and controlled to prevent particulate and microbiological contamination of drug products. Cleanzone: an area with a defined particulate and microbiological cleanliness standard. Definitions Classification The particulate cleanliness of air shall be defined in one or more of three occupancy states - “as-built”, “at-rest”, or “in operation” Occupancy states As-built: installation is complete, all services functioning, no production equipment, materials, or personnel present At-rest: no personnel present In operation: the installation is functioning in the specified manner, specified number of personnel present and working Classifications are determined by number of particles measured in 1ft3 / 1m3 of air Cleanroom users are usually concerned with.. Viable particles Non-viable particles Dust particles, hairs etc. Bacteria, spores, virus etc. Definition of particles Any solid or liquid object, which, for purposes of classification of air cleanliness, falls within a threshold size in the range from 0.1 to 5µm Classification - ISO standard 14644-1:1999 Published on 1999 Cover wide variety of issue such as classification, design, testing, operation and bio- contamination Particles are measured in cubic meter (m3) Cleanzone Reference: PIC/S Guide To GMP For Medicinal Products classification Annex 1 Cleanzone Reference: PIC/S Guide To GMP For Medicinal Products classification Annex 1 Recommended limits for microbiological monitoring of clean areas during classification (‘at rest’ and ‘in operation’) Classification (comparison between different standards) maximum particles/m3 FED STD EU GMP Class 209E ≥0.1 µm ≥0.2 µm ≥0.3 µm ≥0.5 µm ≥1 µm ≥5 µm Classification equivalent ISO 1 10 2.37 1.02 0.35 0.083 0.0029 ISO 2 100 23.7 10.2 3.5 0.83 0.029 ISO 3 1,000 237 102 35 8.3 0.29 Class 1 ISO 4 10,000 2,370 1,020 352 83 2.9 Class 10 Grade A and ISO 5 100,000 23,700 10,200 3,520 832 Not Class 100 Grade B specified ISO 6 1.0×106 237,000 102,000 35,200 8,320 293 Class 1,000 ISO 7 1.0×107 2.37×106 1,020,000 352,000 83,200 2,930 Class 10,000 Grade C ISO 8 1.0×108 2.37×107 1.02×107 3,520,000 832,000 29,300 Class 100,000 Grade D ISO 9 1.0×109 2.37×108 1.02×108 35,200,000 8,320,000 293,000 Room air Cleanzone Classification Grade A: The critical zone for high-risk operations (e.g. aseptic processing line, filling zone, stopper bowl, open primary packaging or for making aseptic connections under the protection of first air). Grade B: For aseptic preparation and filling, this is the background cleanroom for grade A (where it is not an isolator). Air pressure differences should be continuously monitored. Cleanrooms of lower grade than grade B can be considered where isolator technology is used. Grade C and D: These are cleanrooms used for carrying out less critical stages in the manufacture of aseptically filled sterile products or as a background for isolators. They can also be used for the preparation/filling of terminally sterilised products. Let’s take a look at a pharmaceutical manufacturing facility PIC/S General Paragraphs Clean Areas: – Entry through airlocks for personnel and/or for equipment and materials. – Supplied with air has passed through filters of an appropriate efficiency. The various operations of component preparation, product preparation and filling in separate areas within the clean area Manufacturing operations: – Product is terminally sterilized, – Conducted aseptically at some or all stages. In order to meet “in operation” conditions, areas should be designed to reach certain air-cleanliness levels in the “at rest” occupancy state. PIC/S General Paragraphs “In operation” classification may be demonstrated during normal operations, simulated operations or during media fills (worst-case) Clean rooms and clean air devices should be routinely monitored – Monitoring locations based on risk analysis and the results of classification – Grade A: full duration of critical processing – Grade A: Such a frequency and sample size that all interventions, transient events is captured and alarms triggered – Grade B: The same as grade A; the sample frequency may be decreased. – Grade C and D: in accordance with the principles of quality risk management. PIC/S General Paragraphs Terminally Sterilized Products – Preparation of components and most products should be done in at least a grade D environment Where the product is at a high or unusual risk of microbial contamination Grade C – Filling of products for terminal sterilization Grade C Where the product is at unusual risk of contamination from the environment, filling Grade A with Grade C background. – Preparation and filling of ointments, creams, suspensions and emulsions should grade C before terminal sterilization PIC/S General Paragraphs Aseptic Preparation – Components after washing Grade D – Handling of sterile starting materials, unless subjected to sterilization or filtration Grade A with Grade B background. – Otherwise Grade C – Handling and filling of aseptically prepared products Grade A – Transfer of partially closed containers, as used in freeze drying, either in a Grade A environment with grade B background or in sealed transfer trays in a grade B environment Barrier Technologies Restricted Access Barrier System Isolator (RABS) Barrier Technologies – What are the differences? Isolator RABS Closed system (product not exposed to external Open or closed environment) Grade A inside with unidirectional flow Grade A inside (unidirectional or turbulent flow) Minimum background is Grade B (in operation) Minimum background Grade D Decontamination system into the room Integrated decontamination system Validation procedure according to cleanroom Biodecontamination procedure using biological standards and chemical indicators Transfer of materials using transfer devices Entry or exit from using closed transfer devices possible: e.g mobile LAF cart, open airlock. Suitable for handling highly potent or toxic Not for highly potent or toxic products products Air tightness typically not required. Leak tightness testing according to ISO 14644-7 Working at typically positive pressure Working at positive pressure or negative pressure or double design pressure Auni Hamimi Idris TOPIC OUTCOMES: o Analyze the physical contaminants, chemical contaminants and biological contaminants related to cleanrooms What are contaminants in cleanroom???? Contaminants A contaminant is something, either material (in solid, liquid or gaseous form) or a physical state, that is considered to be in the wrong place and at the wrong time. Impurities (of a chemical or microbiological nature) or of foreign matter, into or onto a starting material or intermediate or API during: production sampling packaging or repackaging storage or transport Pharmaceutical Cleanroom Contaminants anything that is A viable/microbial unwanted visibly seen & is not contaminant is any chemical that part of the product infectious material makes a drug unfit or the raw material that affects the quality for use originally of the drug e.g. API of different e.g. airborne non-viable E.g. bacteria, yeast, drug product, particulate mould, fungi, virus, intermediate contaminants & prions, protozoa ortheir excipients, foreign materials such toxins and by-products intermediate as metals, glass chemical reagents particles and fibers and cleaningagents Particulate contaminant Dead Live particles particles Not able to reproduce by Able to reproduce/ multiply if themselves, e.g dead microorganisms the environmental conditions are suitable (warm, humid) Standards used: US Federal Standard 209 E, British Standards 5295 and ISO. US Federal Standard 209 E defines particle as something that either solid or liquid and with size ranging from 0.001µm to 1000µm. ISO; A particle is defined as something solid or liquid with a size ranging from 0.1 µm to 5 µm. Depending on the nature of the industry, particles can either be harmful or harmless Microbial contaminants ▪ Found almost everywhere ▪ Posed much bigger problem due to its ability to reproduce rapidly if basic demand for nutrition, moisture & temperature are fulfilled ▪ Ability to adapt to current environment Non scientific classification of microorganisms based on their use: responsible for the breakdown of organic material in Essential nature industrial: tobreak down contaminants use in the production of commodities such as Useful wine, milk-based products, antibiotics Found in human body Harmless Of the intestinal tract: maintaining healthy internal environment, aid in nutrition digestion negative effects on products, food, beverages, Harmful cosmetics, pharmaceutical product Spoilage of the final product, making it look bad, taste bad, smell bad pathogenic microorganisms causing diseases Dangerous in human Scientific Classification of Microorganisms Fungi Algae Viruses Bacteria Protozoa ▪ The most common contaminants of cleanroom ▪ To survive and reproduce, bacteria need water ▪ Despite the need of water, many bacteria have the ability to survive in very dry environments THUS they can be widely dispersed by the flow of surrounding air ▪ Some aerobic; they require oxygen to survive and produce ▪ Some anaerobic; able to survive and produce in the absence of free oxygen. ▪ Exists in many different morphological forms: rods or bacilli, spheres of cocci, spirals or spirilla Require both light and water to survive Have the ability to perform photosynthesis Can be found in environments where supply of water and light are plentiful Not a problem within contamination control & cleanroom but can be a problem in recirculating water systems Exist in two forms Mold Yeast Commonly found on food that has been stored for too long at high temperature The fuzzy mass: mycelium and consists of multicellular filament of hyphae Found on media Found on any surfaces with optimum temp and humidity Commonly found in natural water environment: ponds, lakes, rivers Complexed single-celled microorganism Concern within the field of contamination control – associated with naturally- occurring water environments. Commonly found in water system and wastewater Viruses are the smallest of all the microbes They are so small that 500 million rhinoviruses (which cause the common cold) could fit on to the head of a pin Unique because they are only alive and able to multiply inside the cells of other living things Made up of a core of genetic material, either DNA or RNA, surrounded by a protective coat called a capsid which is made up of protein. Sometimes the capsid is surrounded the envelope Viruses only exist to make more viruses virus particle attaches to the host cell before penetrating it. virus uses the host cell’s machinery to replicate its own genetic material Once replication has been completed the virus particles leave the host by either budding or bursting out of the cell (lysis) Chemical contaminants ▪ Definition: Contaminants other than particles - in liquid or gases forms ▪ Can affect in many different ways since they can be either inert, toxic, reactive or explosive ▪ Can be harmful/hazardous to the product, production process and/or to the personnel ▪ The types of airborne chemical contamination considered in ISO 14644-8 fall into the following classifications: ▪ Acid ▪ Corrosive ▪ Base ▪ Dopant ▪ Biotoxic ▪ Total organic ▪ Condensable ▪ oxidant Let’s do some activities Upload a picture of your groupmates List THREE potential sources of contaminants in a pharmaceutical manufacturing facility. Discuss ONE way to reduce the risk of contamination from entering our product during manufacturing. Source of contamination Cleanroom air Adjacent areas Materials/ Packaging Personnel Machines/ ancillaries Surfaces 70 - 80% of contamination comes from humans! Source of contamination Skin Hair 10 million skin Old hairs cells shed/day Dandruff Cells shed contain microbes Cosmetic Clothing particles Textile fibers Dust Mouth and Particles shed nose from movement activity Sneeze o Sitting Cough o Standing Talk o Walking Smoking o Moving arms etc. Human microbial flora Normal flora Harmless, important for the well-being of a person Composition varies from person to person Transient flora Mainly on skin, can contain pathogens Transmitted from environment/ other people Removable by skin washing/ disinfection *cfu: colony forming unit Three major components of contamination control state of being clean Especially true in Cleanliness according to the required pharmaceutical level & microelectronic conditions and practices industry that help to maintain health Hygiene and prevent the spread of diseases Minimize freedom fromfaults and number of faulty Quality defects; product product performance ▪ Greatly depends on the activity of the industry ▪ Industry must set a standard cleanliness level for particles in the air Two major considerations: ▪ Formation of contaminants inside the room ▪ Dependent on the activity taking place within the room ▪ Including the movement of personnel ▪ Formation from process ▪ Removal of contaminants from the room ▪ Depends on the amount of air added through ventilation ▪ Cleanliness level of introduced air ▪ Filters are used to remove contaminants from the air before being introduced into clean room Monitoring particulate contaminant Particle analysis of a cleanroom environment → concentration of particles and/or the size of the particles are measured ▪ Determine location of measurement ▪ Define basis of measurement: by percentage of weight or percentage by number? Microbial contamination control ▪ Antiseptic – chemicals that reduces the probability of organism reproducing or in any other way being active ▪ Disinfection – eradicate the microbe but not majority resulting a cleaner but not sterile environment ▪ Sanitation – cleaning process. Followed by disinfection to non living material ▪ Decontamination – reduce microbiological content to a lower level but still not sterile ▪ Sterilization - total absence of living microorganism B T F 2 2 3 2 C O N TA M I N AT I O N C O N T R O L & C L E A N R O O M PHARMACEUTICAL CLEANROOMS: DESIGN & LAYOUT Ts. Dr. Auni Hamimi Idris LESSON OUTCOME Students should be able to describe factors to consider when designing a pharmaceutical cleanroom. Introduction to Pharmaceutical Cleanroom Introduction to Pharmaceutical Cleanroom Introduction to Pharmaceutical Cleanroom Design Importance of cleanroom design Manufacture of sterile and non-sterile pharmaceutical products should be carried out in an appropriately controlled environment. Design considerations Design considerations include cleanliness levels (cleanroom grade), layout to optimize workflow, Heating, Ventilation and Air Conditioning (HVAC) system, ergonomics, equipment placement and building finishes. Components in Cleanroom Include HVAC and utility systems, lighting, furniture, machines, passbox, doors and windows Key considerations in cleanroom design Cleanliness level Workflow optimization HVAC system Cleanroom grade Efficient layout design Ensure that the specified A,B,C,D? ensures smooth material room conditions are Defined as ‘at rest’, ‘as flow and minimizes attained, for example built’, ‘in operation’? contamination risks. through heating, cooling, air filtration, air distribution, airflow rates and air exchange rates Key considerations in cleanroom design Ergonomics Equipment placement Finishes Designing workstations for Strategic placement of Building finishes should be operator comfort and equipment enhances designed to minimize safety improves overall productivity and reduces generation/accumulation efficiency. cross-contamination. of particles and easy to clean and disinfect. Cleanliness level (GMP) Grade A Grade B Grade C and D Critical zone for high-risk operations Background cleanroom for grade A Cleanroom for less critical stages in (e.g. aseptic processing lines, filling (for aseptic preparation and filling, manufacture, e.g. background of zone, or for making aseptic where it is not an isolator) isolators, filling of terminally sterilised connections. Direct intervention by products. operators should be minimized e.g. by premises, equipment design. Example of Grade A/B of sterile manufacturing cleanroom Grade B (in operation) Grade A (in operation) Grade A (in operation) Isolator grade A, background of isolator grade C Example of Grade C/D manufacturing cleanroom Preparation of terminally sterilized product Workflow optimization - How to optimize the workflow? Process Mapping Identify and streamline processes to minimize movement and reduce contamination risks. Layout Design Arrange workstations and equipment in a logical sequence to enhance efficiency and safety. Standard Operating Procedures Establish clear SOPs for cleanroom operations to ensure consistency and minimize errors. Flows within a pharmaceutical manufacturing facility Personnel flow Material flow Equipment flow Waste flow Generic cleanroom cascade Conceptual flow Outdoor environment Ancillary area Personnel flow diagram Material flow diagram Example flow for aseptic manufacturing facility Grade CNC A/B Grade C Example personnel flow for OSD manufacturing facility Example material flow for OSD manufacturing facility LAYOUT REQUIREMENT LAYOUT REQUIREMENT LAYOUT REQUIREMENT PURPOSE OF AIRLOCKS Minimize microbial and To provide physical particle contamination of separation different cleanliness zones. Personnel airlock (PAL) and Provide buffer zones for material airlock (MAL) should material and personnel be physically separated. If transfer between cleanroom not possible, then separate of different grades. by procedure. TYPES OF AIRLOCKS Cascading airlock Higher pressure on one side, lower pressure on the other side. Bubble airlock Higher pressure inside the airlock and lower pressure both outside to create a barrier. Sink airlock Lower pressure inside the airlock and higher pressure on both sides of the airlock. Dual compartment airlock Combination of bubble and sink airlock. MATERIAL AIRLOCK (EXAMPLE) Material transfer passbox Material airlock CHANGING ROOMS AS PERSONNEL AIRLOCK CHANGING ROOMS Areas of increasing cleanliness should be used for entry of personnel, e.g. Grade D --> C --> B. Hand washing facilities only in the first stage of changing room and not present in CR directly accessing grade B. CHANGING ROOMS B T F 2 2 3 2 C O N TA M I N AT I O N C O N T R O L & C L E A N R O O M CLEANROOMS DESIGN: MATERIAL AND METHOD OF CONSTRUCTION Dr. Auni Hamimi Idris LESSON OUTCOME General requirements according to PIC/S GMP Method of construction: modular and conventional Requirements for doors, windows, floors, ceilings What makes a clean room 'Cleanroom'? Internal surfaces Air quality Operation Pest Control Smooth, easy to clean and The control and quality of Adequacy of working Prevention and Protection crack-free internal air through the clean room space, logical flow of from pests surfaces of the clean room operations and the equipment within them Principles Dedicated/ Defined Areas Receiving of materials Sampling area Dispensing/ weighing Gowning/ Changin room Storage areas for quarantined, approved and rejected materials Dedicated/ Defined Areas Production area Laboratory Washing room Equipment storage areas (idle/ cleaned/ cleaning tools Storage of intermediate products Packaging/ labelling areas STORAGE AREAS Should be of sufficient capacity to allow orderly storage of various categories of materials and products with proper segregation. Should be designed to ensure good storage conditions. Temperature, humidity and other appropriate conditions should be monitored and checked. PRODUCTION AREAS Areas arranged and connected in a logical order according to flow of operations. Production areas should be effectively ventilated with air control facilities (HVAC system) METHOD OF CONSTRUCTION Conventional building technique built using traditional construction methods and materials like concrete, steel, and drywall Modular construction. pre-fabricated, self-contained units that can be easily assembled, disassembled, and reconfigured. CONVENTIONAL BUILDING TECHNIQUE CONVENTIONAL BUILDING TECHNIQUE Advantages of conventional cleanrooms include: Durability - Conventional cleanrooms are generally more robust and have a longer lifespan than modular cleanrooms. Customization - Conventional cleanrooms can be designed and built to meet the unique requirements of a specific industry or application, allowing for greater customization and optimization. Disadvantage of Conventional Cleanrooms Can be more expensive and time-consuming to construct compared to modular cleanrooms May be less flexible in terms of expansion or reconfiguration. MODULAR CONSTRUCTION MODULAR CONSTRUCTION Advantages of modular cleanroom: Flexibility - Modular cleanrooms can be easily expanded, downsized, or reconfigured to accommodate changing needs or requirements. Construction Speed - Modular cleanrooms can be assembled more quickly than conventional cleanrooms, reducing downtime and allowing for faster project completion. Cost-effectiveness - Modular cleanrooms often have lower construction costs than conventional cleanrooms, requiring less labor and materials. Disadvantage of Modular Cleanrooms: These rooms offer reduced structural stability and a potentially shorter lifespan compared to conventional cleanrooms. PIC/S PARAGRAPH ON PREMISES General principle Premises and equipment must be located, designed, constructed, adapted and maintained to suit the operations to be carried out. Their layout and design must aim to minimise the risk of errors and permit effective cleaning and maintenance in order to avoid cross-contamination, build-up of dust or dirt and, in general, any adverse effect on the quality of products. PIC/S PARAGRAPH ON PREMISES GENERAL REQUIREMENT FOR CONSTRUCTION MATERIAL GENERAL REQUIREMENT FOR CONSTRUCTION MATERIAL CONTRUCTION MATERIAL REQUIREMENT FOR CLEANROOM FLOORS, WALLS AND CEILINGS FLOORS Floors must have sufficient sloping towards a drain, thus allowing proper drainage Floor gradients: Wash area 1:25 Wet areas 1:50 Other areas 1:100 Drains are kept to a minimum amount and designed to prevent backflow. Open channels should be avoided. FLOORS cont.. Epoxy resin, PVC, Polyurethane are typical materials for flooring. Can be made conductive floors to prevent static electricity, especially in low humidity areas. Selection depends on several factors, e.g. Is the humidity high in the area? How high is the mechanical load when heavy objects are moved? Epoxy resin floor recommended for high humidity area/ where water are present, e.g. washing areas, steam outlets due to anti-slip properties PU floor recommended in the area where heavy objects are often moved, e.g. packaging area, has better stain protection PVC floors economical and easy to install. Recommended for labs, hallways, or rooms that don’t have heavy traffic. WALLS AND CEILINGS Traditionally, walls and ceilings are constructed on site from raw materials (bricks), smoothly plastered, waterproofed by the application of a PVC or epoxy finish coating and non-dust generating. Modular clean room walls are typically made from steel frames with glass/plexiglass or clear vinyl/PVC curtains. They may include materials like: Painted aluminum Melamine Vinyl-covered gypsum Seamless and rounded floor-to-wall, wall-to-wall and wall-to-ceiling junctions. CEILINGS AND LIGHT FIXTURE GENERAL REQUIREMENT FOR DOORS GENERAL REQUIREMENT FOR DOORS GENERAL REQUIREMENT FOR WINDOWS GENERAL REQUIREMENT FOR WINDOWS Air filtration and air flow BTF2232 Ts. Dr. Auni Hamimi Idris Key considerations in cleanroom design Cleanliness level Workflow optimization HVAC system Cleanroom grade Efficient layout design Ensure that the specified A,B,C,D? ensures smooth material room conditions are Defined as ‘at rest’, ‘as flow and minimizes attained, for example built’, ‘in operation’? contamination risks. through heating, cooling, air filtration, air distribution, airflow rates and air exchange rates Source of contamination Cleanroom air Adjacent areas Materials/ Packaging Personnel Machines/ ancillaries Surfaces Cleanzone classification For airborne particles, Reference: PIC/S Guide To GMP For Medicinal Products Annex 1 Definition Standard A room in which the concentration of airborne particles is (US Federal controlled to specific limits. Standard 209) A room with control of particle contamination, constructed (British Standard and used in such a way as to minimize the introduction, 5295) generation and retention of particles inside the room and in which the temperature, humidity and pressure shall be controlled as is necessary. Room in which the concentration of airborne particles is (ISO standard controlled, and which is constructed and used in a manner 14644-1) to minimize the introduction, generation, and retention of particles inside the room and in which other relevant parameters, e.g. temperature, humidity, and pressure, are controlled as necessary Airborne particle control Materials of construction Operating procedure Air supply How much air is needed in that particular area? Air volume/ air changes Consider heat dissipation from equipment load Air filtration HEPA/ ULPA filters Air distribution Direction of air flow in the room Air Handling System Air handling system refers to Heating, Ventilation and Air- Conditioning (HVAC) system. An ideal HVAC system provides: Product protection Personnel protection Environment protection Preservation of materials Maintenance of equipments Air Handling System HVAC refers to: an arrangement of system that treats outside air to produce cleaned (from microbes and dust) and conditioned air (controlled temperature and humidity), which is circulated or re-circulated for use in controlled and critical area within a pharmaceutical manufacturing space. OR, can be simply said to be a utility system used to provide air ventilation, heating, cooling and air conditioning services to a building or a pharmaceutical space for drug manufacturing Air Handling System HVAC system comprises of Air Handling Unit ( AHU) connected to a ductwork ventilation system that distributes the conditioned air through the building and returns it to the air handler(AHU). Air Handling Unit (AHU) is a device used to condition and circulate air as a part of HVAC. It is usually a large metal box containing a blower, heating or cooling elements, filter racks or chambers, sound attenuators and dampers. INSIDE AN AIR HANDLING UNIT Air Handling System SCHEMATIC OF AIR HANDLING UNIT (AHU) AHU SECTION Air Handling System Air filtration The required cleanliness of air can be achieved through correctly designed and installed filters to meet the specifications or requirements for intended activity. Filter location can be e.g. in the AHU, terminal distribution system Filters are of various types , specifications and classes Air filtration Air filtration Air filtration Air distribution Prime movers Distribution Terminal control equipment Terminal distribution equipment Airflow pattern Unidirectional flow: Air circulated by high velocity air Displacement principle Class A and LAF cabinets Non-unidirectional airflow: Air circulated in optimum rate Dilution principle Class B, C, D, non-classified Mixed airflow: airflow may be unidirectional in one part of cleanroom, while other is turbulent Airflow patterns Grade A Grade B Unidirectional airflow Also called as laminar flow Design for Class A and LAF cabinets The airflow direction can be horizontal or vertical Air flows down through the room like air piston, efficiently remove all airborne contamination, mixes with some fresh air, exits through floor, and recirculates back to the room through filters Airborne contamination immediately removed by this flow of air (displacement principle) whereas non-unidirectional rely on mixing and dilution. Unidirectional airflow Air velocity 0.3m/s to 0.5m/s is necessary to quickly reform the disruption of unidirectional airflow With a vertical air flow of available velocity 0.3m/s to 0.5m/s from a fully filtered ceiling, particle transfer is easier to predict, there being no dead areas for increase of contamination Higher velocity, cleaner the room The volume of air supplied 10-100 times greater than non-unidirectional Vertical unidirectional airflow cleanroom Flow down from ceiling to the floor Air leaves through wall extract grill at floor level Horizontal unidirectional airflow cleanroom Flow down from the wall across the room to other side Less cost in capital and running cost (wall smaller than ceiling) but not popular because air quality destroys quickly. Each operation ends the airflow through the room, reducing predictability of direction and introducing contamination which is continued to following operations Vertical flow gives better contamination control Contamination generated closed to filter could contaminate place downwind Horizontal This type is good if most critical unidirectional operation close to filter and dirtier at airflow the exhaust cleanroom Good if machine or process is placed close to filter and no one allowed to pass between that. Non-unidirectional airflow Also called as turbulent airflow which is a traditional design The ventilation principle similar to most air HEPA filter at terminal end condition room The air enter the cleanroom passes through a HEPA filter installed at the terminal end and supplied through diffuser in the ceiling It is used in cleanrooms where terminal outlets form only a part of the total area of ceiling placed to suit the individual process requirements or general room transfer Extracts may be located at the ceiling or at low level of walls Supply air moves in random, Non-unidirectional mixing with airborne airflow contamination, diluting it then remove through low-level extract. Air diffuser Install at the point where the supply air enters the room Diffuser are designed to ensure good air distribution in the room 4-way diffuser Air diffuser Air filtration and distribution Air flow condition produced by Air flow condition by dump ceiling diffuser + low level system + high level exhaust exhaust (usually for Non-UDAF (usually where UDAF required) ventilated room) Air filtration and distribution The type, number and placement of air supply diffusers, as well as the extract grilles, is an important consideration in a turbulently ventilated cleanroom. Air circulation If cleanroom generates large amount of heat, recirculated air must pass air conditioning system (mix with fresh air 2%-20%) to adjust temp, humidity and enter cleanroom through filter Necessary to provide fresh air for personnel health. Fresh air also required to pressurized cleanroom against contamination from less-clean adjacent areas Excess air supplied is extracted by fan to the outside or allowed to find its way out of the cleanroom eg via door gaps, hatches Visit www.classpoint.app and use code BTF2232 to join Air changes Air changes per hour (ACH) are defined as the volume per unit time in hours, of air entering a closed space, divided by the total volume of that space. Mathematically is expressed by means of this simple equation: Exercise: Surface area of HEPA filters: 0.6 m2. The average face velocity of the filter: 0.4 m/s. Cleanroom dimension: 6m X 4 m X 3 m. Where: There are 4 HEPA filters in the room ACH = number of air changes per hour (h-1) Q = air flow (m3/h) Calculate: V = space volume (m3) Air supply volume in m3/h. Answer: ____________ m3/h. Higher ACH, higher cleanliness is achieved Air changes per hour. Answer: ____________ ACH Answer Volume of air supplied through 1 HEPA filter (VA): = air velocity x surface area of filter = 0.4 m/s x 0.6 m2 = 0.24 m3/s Convert to m3/h: 0.24 x 60 x 60 = 864 m3/h Q (air volume supplied to the room): = 864 m3/h x 4 filter = 3456 m3/h ACH = Q /VR = 3456 m3h-1/ (6m x 4m x 3m) = 48 ACH Air changes The number of air change depend on the size of room, and correlates with particle removal Cleanroom vs air-conditioned room Air supply rate much greater for cleanroom than air- conditioned room High efficiency air filter (placed before diffuser) – to remove very small particles Air movement design to assist removal of contamination Cleanroom is pressurized to prevent contaminated air form outside Construction material are chosen to minimize particle shredding & facilitate cleaning Normal air-conditioned room supply air to achieve comfort condition (2 - 10/h) Typical non unidirectional airflow have predetermined ACH (10 -100/h) Thank you Personnel hygiene and behaviour in cleanroom Lesson outcome Students should be able to explain the importance of hygiene and proper gowning when working in cleanroom. Students should be able to explain the gowning requirements for working in cleanroom. The oversight The on-going monitoring of controls The confidence in controls The pillars of controls The foundations PDA TR90: contamination Control Strategy Development in Pharmaceutical Manufacturing PIC/S GUIDE TO GOOD MANUFACTURING PRACTICE FOR MEDICINAL PRODUCTS PART I In Chapter 2 Personnel, All personnel should be aware of the principles of GMP that affect them and receive initial and continuing training, including hygiene instructions, relevant to their needs. Visitors or untrained personnel should be given information, about personal hygiene and the prescribed protective clothing. Detailed hygiene programmes should include procedures relating to the health, hygiene practices and clothing of personnel. Hygiene programmes should be discussed during training sessions. Source of contamination: 80% comes from human! Skin Hair 10 million skin Old hairs cells shed/day Dandruff Cells shed contain microbes Cosmetic particles Clothing Textile fibers Dust Particles shed Mouth and nose from movement activity Sneeze o Sitting Cough o Standing Talk o Walking Smoking o Moving arms etc. Human microbial flora Normal flora – Harmless, important for the well-being of a person – Composition varies from person to person Transient flora – Mainly on skin, can contain pathogens – Transmitted from environment/ other people – Removable by skin washing/ disinfection People as source of contamination How to minimize contamination from people? Efficient and correctly worn protective clothing Correct work methods Good personal hygiene Particle dispersion Particles ≥ 0.3 µm per minute Routes of particle dispersion Cleanroom garments To protect the cleanroom environment and products from contamination by people Disposable garment Purpose To protect the personnel from any hazardous materials from products Reusable garment Types of garment and disinfection Disposable/ Single Use Used where contamination can occur from harmful biological, chemical, or radioactive substances/ sterile processing – Low number of garments required – Disposed of after use Reusable garment Wash Dry Inspection for damage Sealed for dispatch Disinfection using gamma radiation/ autoclave or disinfectant during washing Selection of cleanroom garment Not all cleanroom garments are created equal! Some questions you may ask.. What are the fabrics available for reusable/ disposable cleanroom apparel? What are the Institute of Environmental Sciences and Technology (IEST) standards for fabric selection? How do you choose the right garment for your cleanroom needs? Fabric for cleanroom garments Woven fabric Commonly used to make reusable garment for their durability and ability to withstand multiple laundering cycles while minimizing particle shedding. normally made from 100% filament polyester or polyester combined with carbon fibers. Polyester + cotton thread Monofilament polyester fabric thread Prone to yarn breaking up and Tightly woven and non-shedding shedding of particles Fabric for cleanroom garments Non-woven - produced directly from synthetic fibers or filaments by a variety of processes and are referred to commonly by the type of process. Usually for single-use garments only Offer excellent barrier properties and are designed for single-use applications to prevent contamination Example of fabric material:Tyvek® (high-density polyethylene), microporous films, or spunbond- meltblown-spunbond (SMS) fabrics. Selection of cleanroom garment The Institute of Environmental Sciences and Technology (IEST) provides guidance on cleanroom garment systems through its Recommended Practice IEST-RP-CC003.5. This document offers non-mandatory guidance for the selection, specification, maintenance, and testing of apparel and accessories appropriate for use in cleanrooms and other controlled environments Key considerations from IEST-RP-CC003.5 Fabric performance, e.g. Particle Filtration Efficiency – able to filter particles generated by wearer Durability – e.g. durability after sterilization cycle for reusable garment Fluid/ chemical resistant - The ability of the fabric to repel water/ chemicals to which it will be exposed Garment Construction, e.g. Should be comfortable to wear Seam types and closure - Able to prevent microbial penetration and the passage of particle contamination Maintenance, e.g. Some fabrics are treated for antistatic properties Guidelines for laundering and sterilization to maintain garment integrity. How to choose the right garment? Cleanroom Classification Garment Design Compliance with Determine the ISO class of Choose designs that Standard your cleanroom, as higher provide adequate Ensure that the selected classifications (e.g., ISO Class coverage and minimize garments meet relevant 5) require garments with particle release, such standards, such as those superior barrier properties as coveralls with hoods outlined in IEST-RP- and lower particle shedding. and boot covers. Reusable vs. CC003.5 and GMP, to Material Disposable maintain proper Compatibility contamination control. Decide between reusable Ensure the fabric is and disposable garments compatible with your based on factors like cost, cleanroom environment, environmental impact, considering factors like and the specific chemical exposure and requirements of your static sensitivity. cleanroom processes. PIC/S Guide to GMP – Annex 1 Manufacture of Sterile Medicinal Products Cleanroom garment Body garment Coat and trousers or coverall No pockets, belts or tucks Minimum seams Zipper covering Secure closures at wrist, neck, ankle Comfortable size Cleanroom garment Head gear Must cover hair completely If using hood, should fully cover head and under coverall neck Beard cover if required For handling hazardous material, cleanroom helmet with a ventilating fan and exhaust filter Face mask (single use surgical mask or mask sewn into the hood) Goggles for additional protection Cleanroom garment Shoe cover Single use for lower classification areas AS first stage protection before entering changing rooms Boots Cover pant leg of the coverall until above the calf Plastic/rubber soles Zipper, straps on the top hem to fasten boots Cleanroom garment Gloves Glove materials Powder-free Latex, nitrile or vinyl as Should enclose wrist barrier gloves Double gloves for increased Latex: excellent fit and protection comfortable Nitrile: tear and chemical resistant Vinyl: economical but easily tear Clothing recommendation Lower standard of cleanroom used cap, smock, shoe cover, glove & mask Clothing recommendation higher standard of cleanroom used hood tuck under neck, coverall, knee-high over boot, glove & mask Gowning for cleanroom Garments are donned prior entering a cleanroom Best method is the one that minimizes the amount of contamination to environment A written instruction should be available in the changing rooms Changing rooms as air-locks Entry and exit of cleanroom should be separated, either by time interval or different area to minimize contamination Gowning for cleanroom Prior to arriving at the cleanroom. Take a shower Washing – remove the natural skin oils Clothing made from artificial fibers is a better choice than wool and cotton Remove jewellery, watches etc. Changing into cleanroom garments. - Three zones – common clothing change area - Pre-change zone; for removing clothes that are not to be worn underneath the cleanroom garment. - Changing zone; storing and donning/taking off cleanroom garments - Cleanroom entrance zone; checking of the garments and entrance to the cleanroom. Approaching the pre-change zone Shoe cleaners should be used to retain contamination dispersed from the shoe being cleaned. Sticky cleanroom mats or floorings. If use a laminated mat shoes should be applied to a mat three times to ensure the removal of all footwear contamination. Pre-change zone Remove sufficient street or factory clothes. Outdoor shoes should be removed and cleanroom dedicated shoes put on. Watches, rings and jewelry should be removed. Items such as cigarettes and lighters, wallets and other valuables should be securely stored. Remove cosmetics Don a mop cap or hairnet – ensures hair will not stick out. Put on beard cover or beard mask. Put on a pair of disposable footwear coverings or change into dedicated cleanroom shoes. Wash and disinfect the hands and dry them. Cross over from the pre-entry area into the change zone. Changing zone Garments to be worn are selected. A facemask and cap is put on. If a hand washing system is installed in this area, hands should be thoroughly washed. Put on the gloves The coverall/gown should be removed from its packaging and unfolded without touching the floor. Don the coverall. The outer side of the coverall should not touch your clothing or skin. Lift the gloves cuffs over the coverall cuffs. Cleanroom entrance zone Crossover the bench Sit on the bench. One leg should be raised, the cleanroom footwear put on, the leg transferred over the bench and placed on the floor of the entrance zone. Then, do the same thing for the other leg. If required, protective goggles can be put on – prevent eyelashes and eyebrow hair falling onto the product. Check the garment using a full length mirror to see that they are worn correctly. Wash hands and apply an alcohol solution containing a skin disinfectant. Low particle working gloves should be put on without the outside of them becoming contaminated. Enter the cleanroom over a cleanroom mat. Gowning SOP Gowning SOP Gowning SOP Exit Changing Procedures When leaving a cleanroom: 1. Discard all their garments and re-entry use a new set of garments. 2. Discard their disposable items (masks, gloves) and reuse their coverall and smock. ENVIRONMENTAL MO N ITO RING IN C LEAN RO O M BTF2232 TS. DR. AUNI HAMIMI IDRIS LESSON OUTCOME At the end of this lesson, students should be a b le to: Id e ntify d iffe re nt monitoring p rog ra mme s in c le a nroom Exp la in the me thod s us e d for te s ting a nd monitoring c le a nroom a ir q ua lity PURPOSE OF EN VI RO N MEN TAL MO N ITO RING To ensure specifications comply with the requirements. WHAT SHOULD BE MONITORED? Room temperature Relative humidity Differential pressure Viable particle count Non- viable particle count TEMPERATURE AND REL.HUMIDITY MONITORING Temperature, humidity, and differential pressure must be monitored continuously An increase/decrease in temperature and/or humidity may ⚬ s up p ort b a c te ria l a nd mold g rowth ⚬ ma ke s c ond itions unc omforta b le for the op e ra tor ⚬ Pos e ris k to p rod uc t/ ma te ria l d e g ra d a tion Differential pressure will reduce risk of airborne contaminants from adjacent less clean areas to stream into the DIFFERENTIAL cleaner area. PRESSURE MONITORING Magnehelic is typically used to measure and monitor differential pressure Permanent installation is preferred TEMPERATURE AND REL.HUMIDITY MONITORING General requirement In general, regulations suggest that temperature and humidity should be appropriate within manufacturing areas, with attention given to long -term storage areas. Regulations related to temperature and humidity control in cleanroom Source Regulatory guidance EudraLex Volume 3.3. Lighting, temperature, humidity and ventilation should be appropriate 4, Part 1, Chapter and such that they do not adversely affect, directly or indirectly, either the 3 medicinal products during their manufacture and storage, or the accurate functioning of equipment EudraLex Volume 16. Other characteristics such as temperature and relative humidity 4, Annex 1 depend on the product and nature of the operations carried out. These parameters should not interfere with the defined cleanliness standard. CFR 211.46b Equipment for adequate control over air pressure, microorganisms, dust, humidity, and temperature shall be provided when appropriate for the manufacture, processing, packing, or holding of a drug product. PIC/S Annex 1 9.6 Other characteristics, such as temperature and relative humidity, GMP should be controlled within ranges that align with product/ processing/ personnel requirements and support maintenance of defined cleanliness standards (e.g. grade A or B) TEMPERATURE AND REL.HUMIDITY MONITORING Good engineering practice suggests s pe cifying conditions tha t provide comfortable conditions for operators and workers. As with temperature, regulatory guidance suggests that humidity levels should be appropriate for the product and process as well as for operator comfort to limit shedding and sweating. Factors to consider when defining comfortable conditions include: Metabolic rate (activity level) Amount of clothing Temperature Comfort conditions in Fig 1: wearing ‘street clothes’ Humidity Individual local preferences TEMPERATURE AND REL.HUMIDITY MONITORING Common industry practice is to provide lowe r e nvironme nta l te mpe ra ture s a s the le ve l of gowning incre a s e s. S ugge s te d room te mpe ra ture s : for occupa nts we a ring “s tre e t clothe s ” s hould ha ve a s e tpoint a round 22°C, IS O 8 e nvironme nts s hould ha ve a s e tpoint a round 20°C IS O 7 e nvironme nts a s e tpoint clos e r to 17°C–18°C. Typica l cle a nroom gowning The s e s ugge s tions a re ba s e d on the ne e d for highe r le ve ls of gowning in more highly cla s s ifie d a re a s (Gra de A or B or IS O 5 or 7, in ope ra tion) TEMPERATURE AND REL.HUMIDITY MONITORING Microbial growth Microbial growth and germination of spores Temperature and relative humidity are also a are very unlikely in areas with an RH below consideration for microbial growth: 60% Mold propagation is more likely at warmer Vegetative cells would normally be carried temperatures (up to about 35 °C–40°C). on particles, such as skin flakes. Mold spores and bacterial spores can enter a facility on people or materials. They can exist as individual spores and then grow when they find a suitable growth environment. Although high -efficiency particulate air (HEPA) and ultra -low particulate air (ULPA) filters are highly effective against microbial contamination, they are not truly absolute filters. If the microbial load upstream of these filters is high enough, some penetration is possible. TEMPERATURE AND REL.HUMIDITY MONITORING Fig. 4: environment health and comfort Controlling the lower range of humidity is not generally important to address microorganism-related concerns, but it may be important to manage static electricity, human comfort, and shedding. TEMPERATURE AND REL.HUMIDITY MONITORING Suggested temperature ranges for facility space design conditions Suggested % RH ranges for facility space design conditions Space Lower Limit, °C Operating Range, °C Upper Limit, °C Lower Limit, % RH Operating Range, % RH Upper Limit, % RH Plant utilities room 5 15–27 90 N/A ≤80 90 Clean utilities 5 20–25 65 N/A ≤60 65 b (technical space) Raw materials warehouse 10 15–30 35 N/A 20–80 90 (ambient) Raw materials 15 20–25 30 N/A 30–60 65 b warehouse CNC 15 20–24 30 25 30–60 65 b CNC+/Grade D 15 18–22 30 25 30–60 65 b ISO 8/Grade C 15 18–22 30 25 30–60 65 b ISO 7/Grade B 14 17–20 30 25 30–60 65 b ISO 5/Grade A 14 17–20 30 25 30–60 65 b Finished goods 2 3–7 8 N/A 20–80 90 (refrigerated) Finished goods (Controlled Room 15 20–25 30 N/A 20–75 80 Temperature) Differential Differential pressurisation as the mechanism to create segregated zones within a controlled environment. pressure Helps prevent cross-contamination betweencf adjacent areas. PIC/S Annex 15: 10 – 15 Pa between room of different grade. A room can be more positive or negative than adjacent room. Pressure cascade dictate the air movement in cleanroom facilities. Example of pressure cascade ENVIRONMENTAL MONITORING OF PARTICLES VIABLE LIMIT REQUIREMENT FROM PIC/S ANNEX 1 Active air sampling Passive air sampling Surface contact plates Surface swabs Personnel gown and glove Appropriate alert and action limits should be set for the results of microbiological monitoring. If limits are exceeded, should prescribe corrective action. ENVIRONMENTAL MONITORING OF VIABLE PARTICLES A C T I V E A I R S A M P LI N G PASSIVE AIR SAMPLING Wh a t it is What it is Uses me c ha nic a l d e vic e s to a c tive ly d ra w a known Passive collection of airborne viable contamination volume of a ir (e.g. 1m 3 ) throug h a c olle c tion me d ium, by ‘‘fall out’’ or settling into an open Petri dish. s uc h a s a n a g a r p la te. Relies on gravity to collect airborne particles. Te c h n iq u e Filtra tion Technique Imp a c tion Particle sedimentation. SURFACE MONITORING For all sampling methods, the incubation time What it is should be long enough to ensure the growth of Active collection of viable particulate deposited on recovered microorganisms. Usually 3 - 5 days at surfaces 30 °C- 35 °C for mesophilic bacteria. Fungi might Technique require additional 2- 4 days of incubation at room Contact plates temperature in daylight. Swab ENVIRONMENTAL MONITORING OF VIABLE PARTICLES A C T I V E A I R S A M P LI N G Wh a t it is Uses me c ha nic a l d e vic e s to a c tive ly d ra w a known volume of a ir (e.g. 1m 3 ) throug h a c olle c tion me d ium, s uc h a s a n a g a r p la te Typ e s o f a ir s a m p le rs a n d t e c h n iq u e s Slit sampler Slit- to- a g a r s a mp le r Sie ve imp a c tor Ce ntrifug a l s a mp le r Surfa c e a ir s ys te m s a mp le r Ge la tine a ir s a mp le r. 6- stage Andersen cascade Surface air impactor system sampler MONITORING OF VIABLE AI R BO R N E PART I C LE S F I LT R A T I O N T E C H N I Q U E F O R A C T I V E M I C R O B I O LO G I C A L A I R S A M P LI N G Filtration constitutes a separation of particles on a membrane or depth - type filter. Particles penetrate into the filter and are retained and bound therein. Filter is placed directly on growth medium or dissolved & cultured on solid agar medium Filtration is not a suitable method for evaluating the levels of vegetative cells due to its desiccating effects. MONITORING OF VIABLE AI R BO R N E PART I C LE S IM P A C T IO N T E C H N IQ U E F O R A C T IV E M I C R O B I O LO G I C A L A I R S A M P LI N G Most commonly used technique Impaction samplers increase the velocity of airborne particles by means of a hole, slit, or by a fan blade in the sampling head during the sampling. The stream of air is drawn toward the surface of the collecting medium at high velocity. Because of inertia, the particles will be impacted on the surface. The cutoff size value d 50 describes the aerodynamic size of impacting particles. d 50 is the 50 % cut - off particle size where 50 % are likely to be impacted and 50 % are likely to pass through the air sampler. The collecting surface may consist of different sticky, solid materials such as agar media. MONITORING OF VIABLE PASSIVE AIR SAMPLING AI R BO R N E PART I C LE S Wh a t it is Pa s s ive c olle c tion of a irb orne via b le c onta mina tion F A LLO U T T E C H N I Q U E F O R P A S S I V E b y ‘‘fa ll out’’ or s e ttling into a n op e n Pe tri d is h. M I C R O B I O LO G I C A L A I R S A M P LI N G Re lie s on g ra vity to c olle c t a irb orne p a rtic le s. Te c h n iq u e Based on the sedimentation of airborne particles Pa rtic le s e d ime nta tion into open growth media (solid agar) in settling plates. Easy to handle and allow exposure times up to four hours The settling of particles onto the exposed plate is affected by local air movements, exposure time, and the particle settling velocity. Cannot be used for quantitative analysis MONITORING OF VIABLE P A R T I C L E S O N S U R F AC E S C O N T A C T P LA T E S Lim it a t io n s : Ca n only b e us e d on fla t s urfa c e s Contact plate method is more suitable to flat, firm Ve ry s e ns itive to re s id ua l d is infe c ta nt surfaces, and may be used for personnel monitoring Employs small Petri dishes (diameter of approximately 55 mm), overfilled with nutrient agar The contact plate is pressed against the flat surface to be tested. Organisms on the surface of the equipment will be lifted off and remain adherent to the agar. The plate is then covered and incubated, with the CFU/plate reported. Media residue on the surface must be removed. MONITORING OF VIABLE P A R T I C L E S O N S U R F AC E S SURFAC E SW AB Lim it a t io n s : Swab is more useful for flexible, uneven, or heavily He a vily d e p e nd e nt on op e ra tor's s wa b contaminated surfaces te c hniq ue A s w a b is a s olid p in e q uip p e d with a p orous tip Swa b ma te ria l typ e c a n ha ve a n e ffe c t whic h ma y b e ma nufa c ture d from c otton or a more on the re c ove ry s olub le ma te ria l s uc h a s a lg ina te Swa b Te c hniq ue : ⚬ Ge ntly wip e ove r the te s t a re a to c olle c t the p a rtic le s ⚬ Re s us p e nd in b uffe r a nd p la te d , or filte re d a nd p la te d in g rowth me d ia ⚬ Inc ub a te the me d ia Whe n the tip s of the s wa b is ma d e of a lg ina te , it c a n b e d is s olve d , a nd the e ntire s olution c a n b e p la te d MONITORING OF VIABLE P A R T I C L E S O N S U R F AC E S G LO V E F I N G E R T I P S A M P LI N G Sampling method : using contact plates. Sampling execution : After aseptic handling and before glove disinfection. Sampling technique : The underside of the thumb was pressed for at least 3s on the agar surface and then the same for the other 4 fingers. 1 plate for each hand. Glove fingertip sampling is used to Incubation : After sampling the agar plates were evaluate competency of personnel in incubated for 7 days at 30 +/ - 1 °C. performing hand hygiene and gowning procedure in addition to educate on proper Results : Count the CFU. CFU should be less than 1/ work practices glove. ENVIRONMENTAL MONITORING OF PARTICLES NON-VIABLE LIMIT REQUIREMENT FROM PIC/S ANNEX 1 The maximum permitted airborne particle concentration for each grade is given in the following table : Continuous monitoring with computerized data monitoring system Discreet samples using portable particle counters with local data printout or data storage Appropriate alert and action limits should be set for the results of particulate monitoring. If limits are exceeded, should prescribe corrective action. MONITORING OF NON -VI ABLE AI R BO R N E PART I C LE S P A R T I C LE C O U N T IN G Aim: To test & classify the cleanliness of the room. Airborne cleanliness classification should be met Portable particle counters with a short length of sample tubing should be used for classification purposes because of the relatively higher rate of precipitation of particles ≥5.0 μm in re mote s a mp ling s ys te ms with long le ng ths of tub ing. Is okine tic s a mp le he a d s s hould be us e d in unid ire c tiona l a irflow s ys te ms. Sa mp ling s ize : 1 m3 Fre q ue nc y: At the c ommis s ioning a nd s c he d ule d re - te s ting SAMPLING LOCATIONS Re fe r ISO 14 6 4 4 - 1:2 0 15 for numb e r of s a mp le H O W T O D E T E R M IN E loc a tions a nd s a mp le s ize for tota l p a rtic ula te S A M P LI N G LO C A T I O N ? c ount. Ba s e d on Ris k As s e s s me nt - Ris k a na lys is for Are a o f c le a n ro o m in m 2 Min im u m n o. o f s a m p le p rod uc t c onta mina tion (le s s t h a n o r e q u a l t o ) lo c a t io n s (NL) Hig h ris k a re a s ma y inc lud e loc a tions in p roximity of e xp os e d p rod uc ts , c onta ine rs a nd p rod uc t c onta c t s urfa c e s 1 1 Eva lua te a c tivitie s , p ra c tic e s , ma te ria ls tha t ma y p re s e nt p ote ntia l ris k for p rod uc t c onta mina tion 8 4 Exa mp le of s a mp ling loc a tions for via b le p a rtic ula te 28 7 monitoring : Environme nta l a ir ne a r filling line in p roximity of fille d or op e ne d c onta ine r Surfa c e of d oor ha nd le s , wa lls , inte rc oms NL = 27 x (A/ 10 0 0 ) Fing e r g love of op e ra tor on filling line ENVIRONMENTAL MONITORING Why do we set different alert and action limits? LIMITS Alert Limits serve as an early warning signal, prompting increased monitoring and investigation to prevent potential escalation into more serious contamination issues. For example, if the microbial Appropriate alert and action limits should be set for count in a cleanroom approaches the alert limit, environmental monitoring. If limits are exceeded, staff may increase sampling frequency or should prescribe corrective action. investigate potential sources of contamination without requiring immediate corrective actions12. Alert limit is predefined thresholds that indicate a deviation from normal operating conditions but do Exceeding an action limit necessitates immediate not necessarily signify a critical failure. investigation and corrective actions to restore control over the environment. This could involve Action limit is stricter thresholds that indicate a implementing corrective and preventive actions significant deviation from acceptable operational (CAPA), such as additional cleaning, retraining parameters, suggesting that product quality or personnel, or reassessing processes to identify safety may be compromised root causes of the contamination event ENVIRONMENTAL MONITORING Proactive Management : Role of Alert and Alert limits enable facilities to proactively manage potential contamination risks by signaling when conditions are approaching unacceptable levels. This allows for timely interventions before Action Limits in reaching critical failure points, thus maintaining operational integrity and product safety. For instance, if air sampling results approach the alert threshold, increased monitoring can help Responding to identify trends or sources of contamination early. Immediate Response Protocols : Contamination When action limits are breached, immediate response protocols must be activated to investigate the cause and mitigate risks. This includes conducting root cause analyses to understand why the Events limit was exceeded and implementing corrective measures swiftly to prevent recurrence. Regulatory authorities expect facilities to have well - defined standard operating procedures (SOPs) in place for responding to such breaches, ensuring compliance with industry standards and safeguarding product quality Let’s continue next week.. HEP A Fil t e r in Cle a n ro o m 02 04 Airflow 01 03 Filte r Inte g rity Te st Visualisation Air change rates Re c ove ry Te st AIR CHANGES MEASUREMENT Air changes per hour (ACH) are defined as the vo lu m e p e r u n it t im e in h o u rs , of a ir e nte ring a c los e d s p a c e , d ivid e d b y t h e t o t a l vo lu m e o f t h a t s p a c e. ACH= Ave ra g e a ir s up p ly x 6 0 Room volume Me a s uring e q uip me nt: Flo w h o o d Flow hoo d d e te rmine the a c tua l a ir s u p p ly vo lu m e c oming into the room throug h the HEPA filte rs. Ma y a ls o us e va n e a n e m o m e t e r tha t c a n b e utilize d to re a d ve lo c it y p re s s u re d ire c t ly o n t h e filt e r fa c e , whic h the n a utoma tic a lly c onve rte d to ve loc ity, whic h c a n la te r b e c onve rte d to volume ma nua lly. No re g ula tory GMP e ithe r ISO 14 6 4 4 rule tha t re q uire s a d e te rmine d minimum a ir c ha ng e numb e r for p ha rma c e utic a l a p p lic a tions , b ut ISPE re c omme nd s following va lue for ACH (Ta b le 1) For Class A, the air velocity and airflow pattern are more important. Table 1: ISPE recommendations on ACH AIRFLOW PATTERN VISUALISATION Airflow visualisation studies can assist in knowing h o w a ir m o ve s in a c le a n ro o m a nd a ffe c ts a ny c onta mina tion tha t mig ht b e p re s e nt. Us ua lly c a rrie d out within a n a s e p t ic fa c ilit y (o r Cla s s A) A s uc c e s s ful a irflow d e s ig n will e ns ure : ⚬ e ffe c tive c onta mina tion c ontrol in the c le a nroom ⚬ e ffic ie nt d e live ry of a ir to the c le a nroom Airflow s tud ie s c a n he lp in a s s e s s ing : ⚬ whe the r a irflows a re d ra wing p ote ntia lly c onta mina te d a ir to wa rd s a c ritic a l zone ⚬ whe the r c e rta in ob je c ts in the a ir- s tre a m c a us e c onta mina tion b y forc ing the a ir to c ha ng e d ire c tion Airflow s tud ie s a re norma lly p e rforme d u s in g a s m o ke g e n e ra t o r During the s tud ie s , a irflow d ire c tion a nd a ir ve loc ity s hould b e note d a nd re c ord e d. FILTER INTEGRITY TEST/ LEAK TEST Wh a t is it ? Us ing a n o il- b a s e d a e ros ol c ha lle ng e to s e c ure the inte g rity of the filte rs (d is p e rs e d oil p a rtic ula te (DOP) s c a n te s ting ). Re c omme nd e d to b e re p e a te d a t re g ula r time inte rva ls to ve rify the c ontinue d e ffic ie nc y of the filte r. Te s t p roc e d ure re fe rs to ISO 14 6 4 4 - 3 Method : Establish proper flow rate of the air coming out of filter. Inject challenge aerosol just after the air handling unit (AHU) to ensure aerosol is well - mixed with air in air ducts. If not possible, aerosol must be introduced into the ductwork system at least 15 to 20 duct diameters from the filter. Ensure challenge aerosol concentration uniform over upstream of filter to avoid false results.ISO 14644 - 3 suggests no more than ±15% variation. Start scanning at the gasket area, then filter face. Adequate scanning velocity with overlapping strokes. FDA guidance states 0.01% penetration is a leak. CLEANROOM RECOVERY TEST Pu rp o s e : To determine the amount of time that is necessary for the environmental conditions in a clean area to return to a specified steady state of control after a brief particle generation event. Carried out only on non - unidirectional airflow systems upon an installation in the as- built or at - rest state. According to PIC/S GMP Annex 1, recommended clean up time is 15 - 20 minutes. According to ISO 14644 - 3:2005 there are two recovery tests : Recovery Time Recovery Rate Method of recovery time according to ISO 14644 - 3: 100 :1 Recovery Time method The purpose of the test is to establish how long it takes for the cleanroom to recover from a challenge concentration by a factor of 100 to the Target Cleanliness Level, while at the same time minimizing the risk of “residue contamination of the installation” Set up particle counting and run particle count in the room’s background to establish the particle baseline count (Target Cleanliness Level). Introduce aerosol concentration of 100 x TCL. Measure particle concentration. CLEANROOM RECOVERY TEST Re s u lt s : Plot particle concentration on the Y- axis by a logarithmic scale and the time values on the X- axis by a linear scale Establish the duration where the particle concentration has decreased from 100x TCL to TCL. As an example, figure shows recovery test carried out in Class C environment. In the example, the calculated average baseline of the cleanroom is 65,000 particles (≥ 0.5µm) per3 mof a ir. We c a n s e le c t TCL a b it hig he r a t 1.5 x b a s e line c ons id e ring fa c tors s uc h a s p a rtic le s from p e rs onne l. In this e xa mp le , re c ove ry time is 12 minute s. CLEANROOM RECOVERY TEST Ot h e r c o n s id e ra t io n s : The presence of test personnel may slightly elevate particle concentrations in the air. Suggested that the Target Cleanliness Level should be higher than the particle baseline, but no more than 1.5 x the particle baseline. In this way, it is possible to conduct the recovery test while avoiding the risk of compromising the cleanroom with excessively high particle concentrations. CLEANING & DI SI N FEC T I O N Ts. DR. AUNI HAMIMI IDRIS BTF2232 LESSON OUTCOME At the end of this lesson, students should be a b le to: Diffe re ntia te c le a ning me thod s Id e ntify the imp orta nc e of the tools us e d to a p p ly the c le a ning a nd d is infe c ting s olutions Re c og nize the d iffe re nc e b e twe e n the va rious d is infe c ta nts a nd the ir c la s s PIC/S PARAGRAPH O N C LEAN I N G AN D DI SIN FEC T IO N Ma nufa c turing e q uip me nt s hould b e d e s ig ne d s o tha t it c a n b e e a s ily a n d t h o ro u g h ly c le a n e d. It s hould b e c le a ne d a c c ord ing to d e ta ile d a nd writte n p roc e d ure s a nd s tore d only in a c le a n a nd d ry c ond ition There should be w rit t e n p o lic ie s , p ro c e d u re s , p ro t o c o ls , re p o rt s a n d t h e a s s o c ia t e d re c o rd s o f a c t io n s ta ke n or c onc lus ions re a c he d , whe re Pre mis e s s hould b e c a re fully ma inta ine d , e ns uring tha t a p p rop ria te , for ma inte na nc e , c le a ning a nd s a nita tion. re p a ir a nd ma inte na nc e op e ra tions d o not p re s e nt a ny ha za rd to the q ua lity of p rod uc ts. The y s hould b e c le a ne d a nd , whe re a p p lic a b le , d is infe c te d a c c ord ing to Us e of a utoma tic c le a n in p la c e s ys te ms of va lid a te d d e ta ile d writte n p roc e d ure s e ffe c tive ne s s CLEANING Pu rp o s e : To release, collect and re move a ll und e s ire d c onta mina nts from s urfa c e of va rying imp orta nc e (with re g a rd to c le a nline s s ) in the c le a nroom or c le a nzone. Re s p o n s ib ilit y: Pe rs onne l who works in c le a nroom Profe s s iona l c le a ne r hire d for c le a ning c le a nroom DEVELOPING CLEANING PROGRAMME Th in g s t o c o n s id e r w h e n d e ve lo p in g a c le a n in g p ro g ra m Cla s s ify all existing surfaces as critical, general or others Determine the optimal cleaning and surface treatment methods needed to obtain the desired cleanliness levels Determine the frequency of cleaning required to maintain the desired cleanliness levels for each surface type Prepare the cleaning schedules Determine which part of the cleaning schedule is to be performed by cleanroom operators and which is to be performed by cleaning staff Choose the correct material, machines, cleaning solutions and surface treatments to be used for the method specified Train all personne l, both operators and cleaning staff Provide adequate storage facilities for cleaning materials Monitor the cleaning program: visual inspection, microbial sampling Prepare back up plan in the event of discrepancies Organize all documents & schedules for ease of review and management CLEANING P R E V E N T I V E C LE A N I N G PURPOS E To avoid and/or to minimize the creation and transportation of contaminants from the outer to the inner environment To avoid the dispersion of contaminants inside a critical area To facilitate active cleaning Examples of preventive cleaning: Permanent pavement outside facility Floor grill outside the door to collect soil Entrance carpets at the hall entrance as wide as entrance door Use of tacky mats Entrance carpet Tacky mat A C T I V E C LE A N I N G 01 Dry cleaning Tw o p ro c e d u re s : c le a n in g & d e c o n t a m in a t io n Vacuum systeml Cle a n in g : to remove contaminants that are visible to the naked eye Decontamination : to eliminate all other contaminants; that are not visible to the naked eye Tacky roll Production cleaning : only take place in the facility including the production machinery & tooling, 02 Wet cleaning carried out by operators. Maintenance cleaning : degreasing, industrial Two and three bucket washing and removal of surface coatings such as mopping system pigments and oxide Cleanroom sponge - type mop suitable for cleaning walls SINNER CIRCLE - F O U R B A S I C F AC T O R S FO R EFFEC T I VE C LEAN I N G Tim e Ch e m ic a ls Contact time Working time Cleaning solution Te m p e ra t u re Higher temperature loosen dirt more quickly Me c h a n ic a l im p a c t The abrasiveness (scrubbing effect) The contact pressure The frequency of the movement DRY CLEANING METHOD WET CLEANING METHOD WET CLEANING METHOD - C H O O SI N G C LEAN I N G SO LU T I O N Must not be hazardous Non - toxic Cle a n in g s o lu t io n m u s t Non - flammable Fairly quick drying time n o t a ffe c t t h e s u rfa c e Must not affect the surfaces to be cleaned in a in a n e ga t ive wa y negative way Should not contain any particles/contaminants Should not leave any residual material on the surfaces Should be effective in solubilizing/removing contaminants from surfaces Commercially available at reasonable price WET CLEANING METHOD - C H O O SI N G C LEAN I N G SO LU T I O N CRITICAL SURFACE GENERAL SURFACE CLEANING PROGRAMME No n - p ro d u c t c o n t a c t s u rfa c e Pro d u c t c o n t a c t s u rfa c e Cleaned at intervals