Hydraulics.docx
Document Details
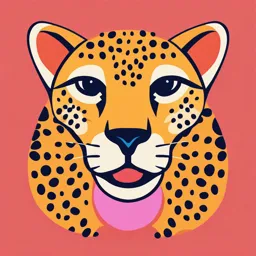
Uploaded by PhenomenalNumber
Full Transcript
2A-29-10: General Hydraulics Description: The aircraft has two (2) primary hydraulic systems, left and right, each powered by an Engine-Driven Pump (EDP) installed on the respective left and right engine that pressurizes fluid contained in dedicated reservoirs. The EDPs are not equipped with o...
2A-29-10: General Hydraulics Description: The aircraft has two (2) primary hydraulic systems, left and right, each powered by an Engine-Driven Pump (EDP) installed on the respective left and right engine that pressurizes fluid contained in dedicated reservoirs. The EDPs are not equipped with off I on switches, but continuously operate unless the respective engine is shut down with the cockpit fire handle. Both systems are independent, each with separate lines and no common point for fluid interchange to preserve the integrity of each system. However, since the failure of an EDP or the engine itself would result in the loss of the autonomous hydraulic system, replacement power sources are available. An overview of the hydraulic systems is shown in Figure 1. Component Hydraulic Power Sources and Figure 2. Hydraulics Synoptic Page. Aircraft sub-systems used in the takeoff and landing phases of flight are subject to many cycles, higher force loads and require a greater range of movement. For design simplicity, they are powered by the left hydraulic system only. However, these components are protected with a high level of redundancy. The left hydraulic system is unique in that left system fluid may be pressurized by two (2) sources other than the EDP. An electrically-driven Auxiliary (AUX) pump, or an impeller driven by right hydraulic system pressure, termed the Power Transfer Unit (PTU) can pressurize left system hydraulic fluid. These act as "backup" systems and function as follows: PTU: Primary backup pump for the utility systems AUX Pump: Ground operation and backup pump (in flight) for landing gear and flaps The primary function of both systems is to pressurize and deliver stored hydraulic fluid to components operated by the individual system. Although both left and right systems operate simultaneously, they are each powered by a respective EDP and are independent systems. Each pump is mounted on the gearbox at the forward lower side of the left and right engines and is accessible upon opening of its respective lower engine cowling. There is a redundancy within the hydraulic system which provides for system functionality should a failure occur. Since the failure of a single EDP (or the engine itself) would result in the loss of the autonomous hydraulic system, surrogate power sources are available. Aircraft components dependent upon hydraulics are redundantly protected by means of an alternate hydraulic source. Control surfaces used throughout the flight are powered using actuators connected to both hydraulic systems, with either system capable of independently powering the controls. Additionally, some surfaces have EBHAs (Electronic Back-up Hydraulic Actuators) to provide power for the surface. The hydraulic pump will be offloaded in flight, when the engine N2 speed drops below 55%. The hydraulic pump will be loaded in flight when the engine reaches at or above idle conditions or one second after the N2 speed exceeds 58%. A hydraulic offload will effectively be performed during assisted or windmill starts, during dry or wet cranks, or when the engine is sub-idle during autorelights, quickrelights or windmilling. On ground, the hydraulic pump will always be loaded, independent of N2 speed. The hydraulic system is designed only to use fire resistant phosphate-ester type hydraulic fluid to AS 1241, Type IV or Type V at 2850 to 3075 psi with only a 20 psi ripple throughout the system. System return pressure is designed to be 60 ±5 psi at normal temperature (-10 to 165°F). The system has a high pressure relief (both at the EDP and in the pressure plumbing) set at 3750 psi. Ground Service Panel: (See Figure 3. Hydraulic Ground Service Panel.) The ground service panel allows use of an external hydraulic test rig to operate the subsystems of the aircraft and to fill the reservoirs. It is located on the underside aircraft belly, just forward of the tail compartment access door. The six (6) quick disconnects, three (3) for the left system and three (3) for the right, permit attachment of an external hydraulic test rig to operate the hydraulic systems during ground maintenance of the aircraft or to service the system reservoirs. During such operations, the EDPs are isolated from the system by check valves installed in their respective main system pressure lines. An external service panel mounted on the underside of the tail of the aircraft has provisions for servicing the reservoirs of both hydraulic systems as well as connections for attaching pressurized lines and system drain lines. Onboard Replenisher: (See Figure 4. Hydraulic Onboard Replenisher.) Located on the aft right side of the tail compartment is the replenishing pump and reservoir servicing system panel. The system includes a 1.5 U.S. gallon reservoir, an electric motor driven pump, a hydraulic selector valve and an ONIOFF switch. The ground servicing panel is a dual-purpose servicing indicator. The panel controls servicing of engine oil to the APU and engines as well as controlling hydraulic servicing of left and right reservoirs. The selector valve is used to select Left Reservoir or Right Reservoir and the ONIOFF switch controls the pump operation. The pump outputs 0.5 GPM at 60 psi to the reservoir. The following table illustrates the actuation power sources for takeoff and landing controls, subsystems and actuators: COMPONENT LEFT SYSTEM RIGHT SYSTEM PTU AUX Aileron (Left Inboard) EBHA(1) Aileron (Left Outboard) X Aileron (Right Inboard) EBHA(1) Aileron (Right Outboard) X COMPONENT LEFT SYSTEM RIGHT SYSTEM PTU AUX Cabin Door X X X Elevator (Left Inboard) EBHA(1) Elevator (Left Outboard) X Elevator (Right Inboard) EBHA(1) Elevator (Right Outboard) X Flaps X X X Landing Gear X X X Nose Wheel Steering X X X Parking Brake (Inboard) X X X Parking Brake (Outboard) X PTU Motor X Rudder (Upper) X Rudder (Lower) EBHA(1) Spoiler (Left Inboard) X Spoiler (Left Mid) X Spoiler (Left Outboard) EBHA(1) Spoiler (Right Inboard) X Spoiler (Right Mid) X Spoiler (Right Outboard) EBHA(1) Thrust Reverser (Left) X Thrust Reverser (Right) X Wheel Brakes (Inboard) X(3) X X Wheel Brakes (Outboard) X(2) (3) (1) The electrical backup mode of the EBHA will continue to power the actuator following a Left or Right hydraulic system pressure loss. (2) In the event of a Right hydraulic system failure, the outboard brake accumulator will provide normal braking capability to the outboard brakes as long as accumulator pressure is available. (3) Both brakes (inboard and outboard) will isolate themselves from the main hydraulic system. If either hydraulic system loses pressure, an accumulator will provide pressure for the brakes. 2A-29-20: Left Hydraulic System 2A-29-30: Right Hydraulic System Limitations: a. Approved Hydraulic Fluid Types: The following fire-resistant Type IV Class 1 hydraulic fluids are approved for use: HyJet IV-A Plus Skydrol LD-4 The following fire-resistant Type V hydraulic fluids are approved for use: HyJet V Skydrol PE-5 Figure 1. Component Hydraulic Power Sources FLAPS LANDING GEAR NW STEERING OUTBD BRAKES OUTBD PARKING BRAKES SHUTOFF VALVE ELECTRICAL CONTROL/SHUTOFF VALVE CONTROL/SHUTOFF VALVE RV REPEATER VALVE CHECK VALVE ELECTRICAL BACK-UP HYDRAULIC ACTUATOR (EBHA) L SYS R SYS LEFT AUX / PTU NITROGEN TIL-006155 Figure 2. Hydraulics Synoptic Page TIL-033852$ Figure 3. Hydraulic Ground Service Panel RIGHT SYSTEM RETURN RIGHT SYSTEM PRESSURE RIGHT SYSTEM FILL LEFT SYSTEM RETURN LEFT SYSTEM PRESSURE LEFT SYSTEM FILL FWD HYDRAULIC SERVICE PANEL TIL-003552 Figure 4. Hydraulic Onboard Replenisher SEE DETAIL A REPLENISHER TANK AND SIGHT GAGE REPLENISHER SELECTOR VALVE (LEFT / RIGHT / OFF) LEFT AND RIGHT SYSTEM ACCUMULATOR GAGES DETAIL A TIL-001878 2A-29-20: Left Hydraulic System General Description: (See Figure 5. Left Hydraulic System Components.) The left hydraulic system supplies fluid drawn from a reservoir and pressurized by an engine-driven variable displacement pump to all aircraft components and subsystems that require the additional force of hydraulic pressure for normal operation. The left hydraulic system pressure is the only actuating force for some aircraft components and subsystems, An additional means of pressurizing the left system is incorporated to compensate for the loss of the left engine or pump: an impeller driven by right system pressure termed the Power Transfer Unit (PTU). The elements that make up the left hydraulic system are: Engine-driven Hydraulic Pump (EDP) Fluid Distribution Components Left Reservoir and Fluid Quantity Indicator Electric Auxiliary Pump Power Transfer Unit (PTU) System Displays Description of Subsystems, Units and Components: Engine-Driven Hydraulic Pump (EDP): The engine-driven variable displacement hydraulic pump is mounted on the engine accessory gear box within the nacelle. Engine rotation is translated by the gear interface to spin the hydraulic pump so that the pump operates whenever the engine is running. Hydraulic pump output is 3,025 ±50 psi but is maintained at 3000 psi throughout the aircraft pressure supply lines and is available instantaneously for use by hydraulic components. An attenuator and a pressure ripple pulsation damper are incorporated in the pump pressure line to reduce the pressure ripple, increase system performance and response, prevent component failures and reduce fluid-borne noise. Each pump incorporates hydraulic fluid to cool and lubricate the moving parts of the pump. This fluid will be hot and may contain contamination from pump wear. It is removed from the pump via a (case drain) bypass line to be cooled and filtered before returning to the reservoir. The fluid is cooled in the heat exchangers located in the wings. The purpose of the heat exchanger is to cool hydraulic fluid heated in the pumps and heat fuel in the wings to delay fuel jelling. There is no switch to disable the hydraulic pump; instead, a shutoff valve, located in the tail compartment, is installed in the supply line between the reservoir and the pump. The shutoff valve is powered by 28V DC from the left essential bus, and controlled by the left engine fire handle on the forward section of the cockpit center console. Pulling out the fire handle closes the shutoff valve, preventing hydraulic fluid from entering the engine nacelle. The shutoff valve may be physically opened or closed by positioning a pointer I handle on the valve body in the tail compartment. Fluid Distribution Components: The hydraulic system is a distributed system rather than a serial system - i.e., although pressurized fluid does flow through the system, fluid remains in the system lines after the engine is shut down. When the engine is started and the EDP pressurizes the fluid in the lines, the pressure is effective almost immediately at all points in the system. The following description is for illustrative purposes, and uses a sequential format rather than the immediate pressurization of components. Initially, hydraulic fluid is routed through an attenuator and a pressure ripple pulsation damper to reduce fluid resonance caused by fluctuations in hydraulic pressure upon system activation. Leaving the nacelle, routed hydraulic lines direct fluid to the tail compartment (aft) to pressurize a system actuator and enters the filter manifold in the tail compartment The manifold contains six filters: Left EDP Pressure, PTU Pump Pressure, Left System Return, Left EDP Case Drain, PTU Case Drain and an AUX Pump Case Drain. Locating all filters within a common manifold allows access to the replaceable elements of the filters without draining system hydraulic fluid. In addition to these filters, the filter manifold also contains a pressure transmitter. System fluid passes through the pressure filter and transmitter, then exits the manifold. From the filtration manifold in the tail compartment, fluid enters the lines supplying aircraft components and subsystems. Lines run aft to supply the elevators, rudder I yaw damper, and forward to the ailerons, spoilers, speed-brakes, flaps, landing gear and doors, brakes, nose wheel steering and main cabin door. A hydraulic pressure relief I unloading valve is installed behind the left main wheel well. The valve opens if system pressure exceeds 3,750 psi. Pressure is reduced by routing some of the system fluid back to the reservoir through the return filter in the filtration manifold. When system pressure falls to 3,200 psi, the relief valve closes. EDP case drain fluid enters a radiator type heat exchanger located in the left wing fuel tank. The hot hydraulic fluid is cooled by fuel in the tank (and tank fuel is slightly warmed, although the high ratio of fuel to hydraulic fluid results in a minimal temperature rise) then returned to the system reservoir, passing through the return filter enroute. Left Reservoir and Fluid Quantity Indicator (FQI): Reservoir: The left reservoir is located in the tail compartment, forward at approximately the 10:00 o'clock position. Hydraulic fluid is stored under pressure in the hydraulic reservoir system for instantaneous release to the hydraulic pumps. The hydraulic reservoir also aids in the diminishing of air trapped within the fluid. Air separation is accomplished by a radial acceleration to the fluid and air mixture. The radial acceleration drives the fluid outward to the outer can and through the outlet port. The air collects around the inner can and then migrates upward into the standpipe. This allows for entrapped air to be captured and bled prior to entering the reservoir. A bootstrap reservoir is integrated into the left system and is hydraulically pressurized from its own respective system by an internal pressure-operated piston in the reservoir. Upon activation, the piston pressurizes fluid within the reservoir to a pressurization of 50:1 ratio. When system pressure is at 3000 psi, the reservoir is pressurized to 60 psi. The reservoirs are pressure filled using the bypass quick-disconnects located on the ground test panel. Each reservoir system incorporates a pressure relief valve, two temperature transducers, manual bleeder valve, fluid quantity transmitter, visual quantity indicator and a standpipe for air removal. The left system reservoir has a single chamber and supplies fluid for operation of the flight controls and the ground systems. At nominal temperature, the total fluid capacity of the left system is approximately 19.38 gallons at FULL reservoir position, which includes reservoir, lines, valves, actuating cylinders, etc. The FULL volume of the left system reservoir is 2.97 gallons. Low quantity is identified through the message at < 1.98 gallons. (caution) CAS Three dedicated outlet suction ports supply the system at the bottom of the reservoir: EDP Suction GND TEST Suction PTU AUX Pump Suction Return hydraulic fluid from the subsystems is directed to the reservoir through the main return line and ground return line. Ground return goes through the main return filter first and then through the return line. Reservoir fluid volume at nominal temperatures are as follows: Overfill 4.55 gallons (Total piston stroke volume) Full 2.97 gallons Refill 1.98 gallons Empty 0.00 gallons FQI: (See Figure 6. Hydraulic Quantity Block Diagram.) A Rotary Variable Differential Transformer (RVDT) is located in the small piston rod end of each reservoir. The transducer determines fluid level through rotary movement, as a result of the pressure-operated piston displacement. The RVDT is supplied with 28V DC and converts to a 0.5 to 10.5V DC output. The output information is used by the FQI and also by the Modular Avionics Units (MAUs). The CAS synoptic page system quantity display is compensated to account for the 0.99 gallons of hydraulic fluid that leaves the reservoir and remains in the landing gear side brace actuators during landing gear retraction. This compensation eliminates a misleading low quantity indication by accounting for the fluid that is still in the system, but temporarily stored in the landing gear actuators. The compensation is accomplished by adding approximately one (1) gallon back to the reservoir quantity whenever the landing gear is retracted. Fluid quantity is also compensated for temperature. As the reservoir temperature varies from the baseline temperature of 21°C I 69.8°F, the calculated fluid expansion or contraction is subtracted or added to the measured reservoir quantity. The result is a quantity indication adjusted to always display what it would be if the reservoir temperature was 21°C I 69.8°F. The FQI panel is located in the tail compartment, below the engine oil servicing reservoir and the hydraulic servicing reservoir (see Figure 7. Hydraulic Fluid Quantity Indicator (FQI) Panel). The FQI provides digital readouts of the left and right system hydraulic reservoir fluid quantities. The quantity is displayed in a bar graph format as well as numerically in U.S gallons. For a numerical readout, the display shows the quantity of the selected reservoir in .05 gallon increments. The reservoir level is temperature compensated. The words "LO", "OK", or "HI" are displayed to indicate the quantity of the selected reservoir (see the following table for ranges): Indication Cause LO Left Fluid Quantity < 1.98 Gallons Right Fluid Quantity < 0.80 Gallons OK Left Fluid Quantity ;: 1.98 Gallons :: 2.97 Gallons Right Fluid Quantity ;: 0.80 Gallons :: 1.54 Gallons HI Left Fluid Quantity > 2.97 Gallons Right Fluid Quantity > 1.54 Gallons The FQI has a self-test capability. All functions are checked on a continuous basis. A failure detected within the indicator will cause a "FAULT" message to appear on the center display of the indicator. An out-of-range condition for the input signals will cause the appropriate bar graph display to read "FAULT". The numerical display will show "----" when the failed input is selected. A test switch initiates a display test to allow verification that all of the display segments are functioning properly. The Linear Variable Differential Transformer (LVDT) determines fluid level through rotary movement (which is connected to the large internal piston within the reservoir). Fluid quantity is compensated for the effects of temperature and landing gear actuator volumes. The RVDT converts its supplied 28V DC power to an output signal of 0.5 to 10.5V DC, which is sent to the respective MAU. The RVDT output is also displayed on the hydraulic reservoir quantity panel for servicing. The fluid quantity displayed in the cockpit and FQI is a compensated fluid quantity. Software is used to calculate a compensated quantity based on temperature and, in the case of left system, a quantity of fluid that is stored in the landing gears actuators. The PTU also monitors right system fluid temperature for use in its overload circuitry. This transducer will be also used for fluid quantity compensation. The second transducer indication will be used for fluid quantity compensation in the FQI and will be sent through ARINC Data Transmission to the MAU. Power Transfer Unit (PTU): The PTU is a hydraulic motor I pump installation located in the tail compartment on the left hand side of the aircraft on a shock-mounted bracket. It is made up of a fixed-displacement hydraulic motor powered by right system pressure, which turns a fixed displacement pump, pressurizing the left system with left system fluid. The pump is equipped with an outlet check valve to prevent a backflow of left system pressure from driving the PTU in reverse. The PTU is used when there is pressure available in the right system and containment of the left system has not been lost, but there is no pressure available in the system. The PTU transfers hydraulic power, but not fluid, from the right to left system. It is a combination motor and pump that uses hydraulic pressure from the right system to turn a hydraulic motor. The motor then turns a pump that pressurizes the left system. The PTU is capable of delivering 2550 ±50 psi at 22.5 gpm, with a 2750 psig inlet pressure, to operate the following systems: Flaps Landing Gear Nose Wheel Steering Inboard Brakes Inboard Parking Brakes Cabin Door When the PTU is required for operation (left system failed), right system pressure is routed through the 28V DC motor operated shutoff valve and then to a 28.8 gpm flow limiter inside the PTU hydraulic motor. A 34 gpm hydraulic fuse inside the PTU hydraulic motor is provided in case of flow limiter failure. The motor is designed with a hydraulic fuse, removable and testable in a separate fixture; in the case of flow limiter failure, and at 34 ±2 gpm, the motor will not consume any fluid and the speed of the motor will reduce to zero and remain there until the motor inlet pressure is reduced to 100 psig maximum. As the motor cycles, the return fluid is directed from the motor outlet port through a left system main return filter and back to the reservoir. Flight crew operation of the PTU Pump is accomplished by the PTU ON and the PTU OFFIARM pushbutton switches located on the HYDRAULIC CONTROL section of the Cockpit Overhead Panel (COP) (see Figure 8. AUX Pump and PTU Control Switches). The following logic is used to determine under which system conditions the PTU will operate: Manual Mode: Manual operation of the PTU is controlled by the flight deck NORMION switch. Placing the NORMION switch in the ON position will direct the Solid State Power Controller (SSPC) to close the PTU ON circuit breaker and open the PTU OFF breaker. The PTU shutoff valve will then be driven open and remain that way as long as the switch is in the ON position. Automatic Mode: The SSPC turns the PTU on automatically when the ARM switch is set in the armed position and the Honeywell system provides the pump control signal. The purpose is to supply pressure to the left system when its normal source of pressure is not available, and the right system is functioning normally. The PTU pump control discrete signal is based on the overall status of the hydraulic system and indicates that hydraulic conditions are appropriate for PTU operation, if desired. The signal is provided by the MAU as an input to the SSPC. A GROUND signal is provided under the following conditions: Left System Hydraulic Pressure < 2400 psi AND Left System Hydraulic Quantity > 0.36 Gallons (uncompensated quantity) AND Right System Hydraulic Pressure > 2850 psi AND Right System Hydraulic Temperature < 107°C (225°F) The SSPC will enable the PTU by closing the PTU ON circuit breaker if the following conditions are present: ARM switch set to ARM AND PTU Pump Control = Ground The PTU is enabled by way of energizing (opening) a fluid shutoff valve in the motor side pressure line. If the PTU is in the auto-operate mode, the valve is energized open if all the above operational conditions exist. Left system hydraulic pressure is monitored by a pressure transducer, which sends a signal to the MAU and triggers PTU operation. Seven seconds after left system EDP pressure recovers to 2750 psi or above, to deactivate PTU and immediately at 2400 psi, to activate PTU. Right system hydraulic pressure is monitored by a pressure transducer, which sends a signal to the MAU and triggers PTU operation seven seconds after right system EDP pressure recovers to 2850 psi or above, to activate the PTU and immediately at 2849 psi, to deactivate the PTU. Normal and high temperature ranges are defined as follows: As the temperature increases, it is considered to be in the normal range with an MAU low-range signal output until it reaches 107°C (225°F). At this point, it is in the high range with a MAU high-range signal output and will stay in the high range until it drops below 175°F (back to normal range). The PTU has a pump bypass (circuit) flow path. It consists of tubing from the PTU pressure filter outlet to the return circuit, with a restrictor in the circuit. For all operating conditions, the bypass flow will be 1.70 to 1.83 gpm, corresponding to 2000 to 2500 psi pump pressure and is temperature compensating to maintain relatively consistent flows at different temperatures. This bypass circuit provides flow anytime the PTU is operating, in order to prevent chugging of the PTU. In addition, this flow has to be subtracted from the available flow to the left system utility functions. The available flow to the left system (from the PTU) is 22.5 gpm at 2050 psig and nominal conditions, where sufficient flow is available in the right system. The motor-operated shutoff valve is located in the PTU motor pressure line. It is controlled by the cockpit switches and prevents the right system from pressurizing the PTU motor when the motor is not commanded to run. Auxiliary Hydraulic (AUX) Pump: The AUX pump is part of left hydraulic system and has both manual and automatic control modes. Manual control is provided by the operation of individual switches located on the cockpit control panel (see Figure 8. AUX Pump and PTU Control Switches), which directly operate the contact breaker to the relevant pump. Automatic mode causes these pumps to be operated automatically by control logic (in response to the relevant input parameters). The primary purpose of the pump is to provide hydraulic pressure to the utility systems for ground and maintenance activities; it consists of an electrically motor driven hydraulic pump, which will supply a maximum pressure of 3100 psi at 0.2 gpm or a maximum flow of 2800 psi at 2.07 gpm, to operate the following utility systems: Flaps Landing gear Inboard brakes I Inboard parking brakes Cabin door Nose wheel steering The AUX pump has a secondary function as an inflight backup power source. This system is normally inactive in flight, but will automatically power on for flap and landing gear operation after any of the following: Dual engine failure Dual EDP failure Left EDP failure plus PTU failure Left EDP failure plus landing gear in transition Timed (two minutes) operation in flight is used to limit the electrical load of the pump. The crew can still immediately turn the pump back on again by cycling the NORMION switch. The AUX pump and associated hydraulic components are located in the tail compartment on the left-hand side above the APU enclosure and below the left system hydraulic reservoir. The pressure transducer is located outboard and the pressure filter is located aft of the AUX pump. Associated components consist of the following: AUX pump pressure transducer AUX pump pressure filter AUX pump check valve AUX pump cockpit switches System Displays: The Engine Indicating and Crew Alerting System (EICAS) system and the Hydraulic synoptic page displays provide the flight crew with a system textual and graphical presentation, enabling them to make a quick determination of the system performance status. These displays represent a simplified "synoptic" type display. The display consists of a basic graphical representation of the system with all associated numerical displays, along with text (as required) to indicate system status. The colors of the numerical I text information also varies to provide additional system status information such as normal, abnormal and warning ranges. The system data includes all system parameters required for the pilots to determine the system status. The parameters may be analog (e.g. voltages, pressures, temperatures, positions, etc.) or discrete. The system includes adequate monitoring of its components to provide the system parameters and information required to generate the system display. In the case of parameters with dynamic ranges that are required to change the color or be presented with range limits, the system also transmits this data to the EICAS system. Performance of the hydraulic system components may be monitored on the Hydraulics or Summary synoptic 2I3 window displays or the Ground Service system 1I6 window display. The Hydraulics synoptic display offers the most comprehensive view of the left and right systems, containing the following information: Hydraulics synoptic (2I3 Hydraulic display) Ground Service synoptic (1I6 Ground Service display) Secondary Engine Instrument synoptic (1I6 Secondary Engine display) Engine Start synoptic (1I6 Engine Start display) Compact Engines synoptic (1I6 Compact Engines display) Brake synoptic (1I6 Brakes synoptic display) Hydraulic Pressure: Displayed in a range from 0 - 4,000 psi with a 100 psi resolution (readings below 200 psi are shown as 0 psi). The pressure readouts are displayed in white when within the range of 1,500 to 3,400 psi, otherwise the readout is shown in amber Hydraulic Pumps: Displayed symbolically and color-coded to reflect operating status for engine-driven, AUX and PTU pumps. The pumps are represented by a round circle with three green vanes when pumps are operating and producing pressures ;:1,500 psi, the symbol changes to a white circle with no vanes if the pumps are not operating or the shutoff valve to the pump is in transition, and if pump operation is unsatisfactory (low pressure <1,500 psi, overheated or overloaded) the pump is illustrated by an amber circle without vanes. Hydraulic Valves: Shown as circles with an internal line representing a standard gate valve. The internal symbol line is aligned with the respective hydraulic line when the valve is open, perpendicular to the hydraulic line when closed, or shown as a diagonal when in transition. The color of the valve representation corresponds to operating conditions: green when in agreement with commanded position and pressure 1,500 psi, amber when valve position does not correspond to commanded position, and white for all other conditions (off). Hydraulic Temperatures: Displayed for each reservoir with a range of -60° to 150°C with a resolution of 1°C. The digital readouts are green when temperatures are between 79.4° and 104.4°C, white when below 79.4°C, and amber when above 107°C. Hydraulic Quantities: System fluid is displayed numerically in gallons with a resolution of 0.1 gallons for the left and right reservoirs, and graphically by a green raster bar graph within the volume of the reservoir symbols. Labels depicting full and low fluid levels are shown to the side of the reservoirs, with full corresponding to 2.97 gallons for left and 1.54 gallons for the right. The Low (caution) CAS message is triggered at 1.98 gallons for the left and 0.80 gallons for the right. When reservoir quantities are zero, the green raster graph is replaced with an "X". On the Summary synoptic window, hydraulic pressures and quantities are shown digitally in colors reflecting system operation - white for normal ranges and amber for abnormal conditions. Controls and Indications: Circuit Breakers (CBs): The following CBs protect components of the left hydraulic system: Circuit Breaker Name CB Panel Location Power Source AUX HYD PRESS SEN MCDU SSPC (#2901) L ESS 28V DC AUX HYD PUMP MCDU SSPC (#2902) L ESS 28V DC Circuit Breaker Name CB Panel Location Power Source FLUID QTY IND MCDU SSPC (#2903) GND SVC BUS HYD SIO L MCDU SSPC (#2912) L ESS 28V DC HYD QTY SEN L MCDU SSPC (#2909) L ESS 28V DC HYD PRESS SEN L MCDU SSPC (#2906) L ESS 28V DC HYD EDP CTRL L MCDU SSPC (#2904) L ESS 28V DC HYD SVC SOV L MCDU SSPC (#2914) GND SVC BUS HYD REPLENISH PMP MCDU SSPC (#2911) GND SVC BUS HYD QTY GND SVC MCDU SSPC (#2908) GND SVC BUS HYD TEMP SEN MCDU SSPC (#2916) L ESS 28V DC PTU HYD PRESS SEN MCDU SSPC (#2917) R ESS 28V DC PTU OFF MCDU SSPC (#2918) L ESS 28V DC PTU ON MCDU SSPC (#2919) L ESS 28V DC Crew Alerting System (CAS) Messages: The following CAS messages are associated with operation of the left hydraulic system: CAS Message Possible Cause(s) L Engine Hot (warning) Engine cooling air temperature above 550° F with HP RPM less than 87%, or 647° F with HP RPM greater than 87%. OR: FADEC exceeds temperature limit. OR: Hydraulic fluid temperature exceeds 135°C. Aux Hydraulic Fail (caution) AUX hydraulic system pump inoperative. Aux Hydraulic Hot (caution) Temperature of AUX pump motor brushes is above 300°F CAS Message Possible Cause(s) Aux Hydraulic Pump Overload (caution) AUX pump demand excessive and unit has shut off. L Hydraulic Quantity Low (caution) Left Hydraulic System (L SYS) quantity less than 1.98 gallons. L Hydraulic Reservoir Hot (caution) Left hydraulic reservoir fluid above 107°C. L Hydraulic System Fail (caution) Left hydraulic system has failed. PTU Hydraulic Fail (caution) PTU output pressure is less than 1500 psi. Aux Hydraulic On (advisory) Auxiliary Hydraulic System pump is operating. L Hydraulic Temp Sen Fail (advisory) Left hydraulic fluid temperature sensor has failed. L Hydraulic Qty Sen Fail (advisory) Left hydraulic quantity sensor has failed. L Hyd Pressure Sen Fail (advisory) Left hydraulic pressure sensor has failed. L Hyd Gnd Svc Valve Fault (advisory) Left hydraulic system service valve is open and hydraulic service panel is installed OR Left hydraulic system service valve is closed and hydraulic service door is removed. PTU Hydraulic On (advisory) Power Transfer Unit hydraulic pump pressurized either manually or automatically. Limitations: Maximum Reservoir Quantities (Pressurized) as Indicated on the Hydraulics Synoptic Page: Left Hydraulic System: 4.55 gallons Right Hydraulic System: 2.77 gallons Left and Right Hydraulic System Accumulator Pre-charge: 1200 psi at 70°F I 21°C, ±25 psi for each 10°F I 5°C difference in temperature from 70°F I 21°C. Figure 5. Left Hydraulic System Components LEFT HYDRAULIC SYSTEM RESERVOIR LEFT SYSTEM MANUAL BLEEDER VALVE (RELIEF) AUXILIARY HYDRAULIC PUMP LEFT SYSTEM TEMPERATURE SENSOR AUXILIARY HYDRAULIC PUMP FILTER LEFT SYSTEM FILTER MANIFOLD ASSEMBLY SYSTEM REPLENISHER TANK LEFT SYSTEM ACCUMULATOR HYDRAULIC SYSTEM REPLENISHER PANEL TIL-001867 Figure 6. Hydraulic Quantity Block Diagram NOTE 1: DENOTES RESERVOIR REPLINISHER SYSTEM HYDRAULIC LINE TIL-000664 Figure 7. Hydraulic Fluid Quantity Indicator (FQI) Panel TIL-001877 Figure 8. AUX Pump and PTU Control Switches SEE DETAIL A OFF/ARM OFF: Amber NOT ARM legend illuminates. Automatic operation inhibited. Manual operation possible through use of ON switch. ARM: Amber NOT ARM legend extinguishes. Automatic operation enabled when: L SYS pressure is < 2400 psi L SYS fluid quantity is > 0.36 gal R SYS pressure is > 2850 psi R SYS reservoir temperature is < 107O C (225O F) HYDRAULIC CONT PWR XFR UNIT OFF/ARM ON ON Amber ON legend AUX PUMP illuminates. OFF/ARM ON Overrides automatic operation features. Pump operates regardless of DETAIL A OFF/ARM switch position. OFF/ARM OFF: Amber NOT ARM legend illuminates. Automatic operation inhibited. Manual operation possible through use of ON switch. ARM: Amber NOT ARM legend extinguishes. Automatic operation enabled when L SYS and PTU pressure are both less than 1500 psi and any brake pedal is depressed more than 10O . TIL-001879A 2A-29-30: Right Hydraulic System General Description: (See Figure 9. Right Hydraulic System Components.) The right hydraulic system is operationally similar to the left system, but is functionally limited to providing hydraulic power to the flight controls, and single source power to the right engine thrust reverser and the motor drive of the Power Transfer Unit (PTU) impeller. The size of the right system is commensurate with the smaller number of actuators served by the system and absence of actuators requiring large fluid volumes such as the landing gear. The total volume of fluid in the right system is 14.59 gallons. The right system, in conjunction with the left system or as a single pressure source, provides power to the dual system actuators: Flight Control Actuators: Left Inboard Aileron (Electric Backup Hydraulic Actuator [EBHA]) Right Outboard Aileron Left Inboard Spoiler Right Inboard Spoiler Left Outboard Spoiler (Multi-Function, EBHA) Right Outboard Spoiler (Multi-Function, EBHA) Lower Rudder (EBHA) Left Inboard Elevator (EBHA) Right Outboard Elevator Right Thrust Reverser PTU Motor Outboard Brakes I Outboard Parking Brakes The right system solely and independently powers: Right Engine Thrust Reverser PTU motor The right system includes the following components: Engine-Driven Hydraulic Pump Fluid Distribution Components Reservoir, Fluid Replenishing and Quantity Gage Power Transfer Unit System Displays Description of Subsystems, Units and Components: Due to the similarity of the right system to the left system, the following descriptions are cursory, with elaboration confined to systems differences. For additional information, refer back to the left hydraulic system description. Engine-Driven Hydraulic Pump (EDP): The EDP for the right hydraulic system is identical to the pump powering the left system. No control is provided for the pump, but flow to the pump may be interrupted by the shutoff valve in the fluid supply line when the engine fire handle is activated. Fluid Distribution Components: Right system pressurized fluid follows a similar path as the left system; through the same sequence of acoustic filter, dedicated thrust reverser, system accumulator, filter manifold, to the tail-mounted flight controls and forward to the front of the wing for powering the flight controls installed on the wing, through a pressure relief valve, into the radiator cooler in the right wing fuel tank hopper, through a return filter and back to the tail compartment to be available to power the PTU and return to the reservoir. Right Reservoir and Fluid Quantity Indicator (FQI): Reservoir: The right reservoir is located in the tail compartment, forward at approximately the 2:00 o'clock position. Hydraulic fluid is stored under pressure in the hydraulic reservoir system for instantaneous release to the hydraulic pumps. The hydraulic reservoir also aids in the diminishing of air trapped within the fluid. Air separation is accomplished by a radial acceleration to the fluid and air mixture. The radial acceleration drives the fluid outward to the outer can and through the outlet port. The air collects around the inner can and then migrates upward into the standpipe. This allows for entrapped air to be captured and bled prior to entering the reservoir. A bootstrap reservoir is integrated into the right system and is hydraulically pressurized from its own respective system by an internal pressure-operated piston in the reservoir. Upon activation, the piston pressurizes fluid within the reservoir to a pressurization of 50:1 ratio. When system pressure is at 3000 psi, the reservoir is pressurized to 60 psi. The reservoirs are pressure filled using the bypass quick-disconnects located on the ground test panel. Each reservoir system incorporates a pressure relief valve, two temperature transducers, manual bleeder valve, fluid quantity transmitter, visual quantity indicator and a standpipe for air removal. The right reservoir has a single chamber and supplies fluid for operation of the flight controls, and if required, for operation of the hydraulic motor which drives the PTU pump. At nominal temperature, the total fluid capacity of the right hydraulic system is approximately 14.85 gallons at FULL reservoir position, which includes the reservoir, lines, valves, actuating cylinders, etc. The FULL volume of the right hydraulic system reservoir is 1.54 gallons. The right reservoir has expansion capability to compensate for hydraulic fluid thermal expansion and also for air expansion. This volume is the volume difference between the overfill position and the full position (2.77 gallons - 1.54 gallons = 1.23 gallons). Compensated low quantity is indicated with a Low (caution) CAS message at < 0.80 gallons. The maximum available fluid volume with the reservoir and standpipe is 3.55 gallons. Reservoir fluid volume at nominal temperatures are as follows: OVERFILL 2.77 gallons (total piston stroke volume) FULL 1.54 gallons REFILL 0.80 gallons EMPTY 0.00 gallons FQI: There are two transducers per reservoir, providing the following functions: Transducer 1: Provides a dedicated input to the MAU. It supplies the temperature of the fluid to determine the respective amber L Hydraulic Reservoir Hot and R Hydraulic Reservoir Hot messages and cockpit quantity temperature compensation. On the right hydraulic system, the amber R Hydraulic Reservoir Hot message is also used to deactivate the PTU. Transducer 2: Provides a dedicated input to the Fluid Quantity Indicator (FQI). System Displays: The cockpit display indications of right hydraulic system performance are fully described in the text covering the left hydraulic system - there are no independent indicators for each system except the sight glass gages on the respective reservoirs. Controls and Indications: Circuit Breakers (CBs): The following circuit breakers protect components of the right hydraulic system: Circuit Breaker Name CB Panel Location Power Source HYD EDP CTRL R MCDU SSPC (#2905) R ESS 28V DC HYD PRESS SEN R MCDU SSPC (#2907) R ESS 28V DC HYD QTY SEN R MCDU SSPC #2910) R ESS 28V DC HYD SIO R MCDU SSPC (#2913) R ESS 28V DC HYD SVC SOV R MCDU SSPC (#2915) GND SVC Bus Crew Alerting System (CAS) Messages: The following CAS messages are associated with the operation of the right hydraulic system: CAS Message Possible Cause(s) R Engine Hot (warning) Engine cooling air temperature above 550° F with HP RPM less than 87%, or 647° F with HP RPM greater than 87%. OR: FADEC exceeds temperature limit. OR: Hydraulic fluid temperature exceeds 135°C. R Hydraulic Quantity Low (caution) Right reservoir quantity is less than 0.80 gallons R Hydraulic Reservoir Hot (caution) Right reservoir fluid above 107° C R Hydraulic System Fail (caution) Right hydraulic system has failed. R Hyd Gnd Svc Valve Fault (advisory) Right hydraulic system service valve is open and hydraulic service panel is installed OR Right hydraulic system service valve is closed and hydraulic service door is removed. R Hyd Pressure Sen Fail (advisory) Right hydraulic pressure sensor has failed. R Hydraulic Qty Sen Fail (advisory) Right hydraulic quantity sensor has failed. R Hydraulic Temp Sen Fail (advisory) Right hydraulic temperature sensor has failed. Limitations: See the operational limitations listed in 2A-29-20: Left Hydraulic System. Figure 9. Right Hydraulic System Components RIGHT SYSTEM MANUAL BLEEDER VALVE (RELIEF) RIGHT SYSTEM TEMPERATURE SENSOR RIGHT HYDRAULIC SYSTEM RESERVOIR RIGHT RESERVOIR QUANTITY SENSOR RIGHT SYSTEM ACCUMULATOR RIGHT SYSTEM FILTER MANIFOLD ASSEMBLY SYSTEM REPLENISHER TANK HYDRAULIC SYSTEM REPLENISHER PANEL TIL-001868