GAAT Study Material 2024 PDF
Document Details
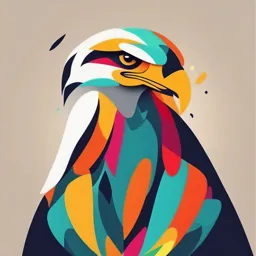
Uploaded by TrustworthyRetinalite165
Kendriya Vidyalaya No 2
2024
Tags
Summary
This document is GRSE LTD. Study Material for GAAT 2024. It details the company's history, starting in 1884, and covers its progression from providing logistics and repair facilities to becoming a premier shipyard, building vessels for the Indian Navy. Key milestones and developments are outlined, including the establishment of various units and the diversification of activities.
Full Transcript
GRSE LTD. STUDY MATERIAL FOR GAAT - 2024 CHAPTER - 1 GRSE - COMPANY PROFILE BRIEF HISTORY The Company originally named as River steam workshop was established in 1884 mainly for pro...
GRSE LTD. STUDY MATERIAL FOR GAAT - 2024 CHAPTER - 1 GRSE - COMPANY PROFILE BRIEF HISTORY The Company originally named as River steam workshop was established in 1884 mainly for providing logistics and repairing facilities to the fleet owned by the then River Steam Navigation Company, a Company incorporated in England and whose registered office was situated at No. 37, Minsing Lane, London and having an office in Calcutta (now Kolkata) at 2, Fairlie Place. Due to growth of business, this company necessitated a docking and repairing facility for their fleet at Calcutta. The river steam workshop was set up in an adjoining area of the then picturesque and fashionable residential “Reach” (meaning a continuous straight stretch of river between two bends) of river Hooghly named Garden Reach as the Botanical Gardens adorned the opposite bank of the river. On 26 November 1895, the River Steam Navigation Company purchased the plot numbers 43 to 45, Garden Reach Road having an area of 66 bighas, from Babu Okhoy Commer Ghosh and Gooroo Prosono Ghose, the executor of the will of Babu Durga Prosono Ghosh and administrator of the estate of Dijendra Commer Ghose. On March 30, 1901, the Steam Navigation Company purchased an adjacent plot being No. 46, Garden Reach Road, having an area of 75 bighas for the purpose of carrying out repairing of their fleet. In 1926, after amalgamation of RSNC (River Steam Navigation Company-Inland Water Transport Company) and BISN (British India Steam Navigation Company), It was decided that the workshop at Garden Reach would function as a Repairing unit, in the form of a partnership concern, On 26 February 1934, the Company was incorporated as a Joint Stock Company and was registered under the Indian Companies Act, 1913 under the name and style of Garden Reach Workshop Limited (GRW). During the Second World War (1939-45) the Company made its mark in carrying out construction, conversion and repair of a number of Naval and Merchant Vessels. Reportedly, during the war years over 4000 vessels were repaired at GRW. From 1934 to 1960 “GRW Ltd.” was managed by Macneill & Barry Ltd., the Managing Agents of the Company. After independence from the early 1950’s onwards, GRW started meeting the nation’s need for small vessels and harbor crafts. On 5th November 1957, the name of Garden Reach Workshops Limited was changed to Garden Reach Workshop Private Limited under the Companies Act, 1956. GRSE LTD. STUDY MATERIAL FOR GAAT - 2024 On 1957, Sri V. K. Krishna Menon, the Defence Minister played key role in deciding to develop India as Self Reliant for its defence requirements and purchased Mazagon Dock Pvt. Ltd. (MDL) of Bombay and Garden Reach Workshops Private Ltd. (GRW) of Calcutta in a package deal at a price of Rs. 3.85 Crores on 19 April 1960. With Government’s taking over of GRW, the tenure of Macneill & Barry Ltd. as Managing Agents ended on 31 August 1960. However, they were appointed as Secretaries and Treasurers for the period from 15 August 1960 to 31 March 1961. Macneill & Barry Ltd. Ceased to be the Secretaries and Treasurers of GRW after 31 March 1961. On 28 March 1961, the Registered Office of GRW Private Ltd. was moved from 2, Fairlie Place, Calcutta- 700001 to 43/46, Garden Reach Road, Calcutta–700024 and once again the Company’s name was changed from Garden Reach Workshops Private Ltd., to Garden Reach Workshop Ltd. From 01 April 1961, the Managing Director of GRW Ltd., assumed responsibility for the functions previously performed by Macneill & Barry Ltd., Calcutta. INS AJAY was the first Naval ship built in India after Independence, which was built in the year 1961 was powered by twin diesel turbines which propelled the craft at speed in excess of 17 knots. Despite its diminutive size, the craft packs a powerful punch in its surface armament and antisubmarine equipment. INS AJAY, after undergoing a major refit at GRW, was gifted to Bangladesh Navy (Later the ship was renamed as B.N.S. SURMA) in 1974. During the first few years after take over by the Government, the main business of the Company remained to be Marine Repair Work. During 1960-61, the Company diversified itself into Engineering products such as steel pontoons & Barges, as well as manufacturing of miscellaneous industrial Products, using level luffing cranes, EOT cranes, Mining machinery, Turbine pumps and Railway Signalling Equipment, Package Boilers, Electric Cargo Winches, Air Compressors, Aerial Ropeways and even vitreous enamelled sanitaryware. During the year 1962-63, GRW undertook a major refit work to the Indian Navy’s INS GOMATI for which the commissioners for the port of Calcutta were most helpful in making a Dry Dock available for over six months. Establishment of DEP Ranchi Having regard to the facilities available the country especially in Heavy Engineering Corporation, Ranchi, and the Heavy Vehicle Factory, Avadi, it was proposed that the new facilities to be set up should be mainly for assembling and testing of the Diesel Engines. A proposal was then put up to the Government of India recommending the establishment of an assembly and testing plant for Diesel Engines at Ranchi in order to be able to coordinate more effectively with the Heavy Machine Building Plant of HEC which would supply majority of the heavy components required for the medium and large bore engines. The approval of the Govt. of India was received on 31 March 1967 for the establishment of a Diesel Engine Plant at Ranchi. Marine Diesel Engine Plant (MDEP) was renamed as Diesel Engine Plant (DEP) on 17 December 1988. GRSE LTD. STUDY MATERIAL FOR GAAT - 2024 Establishment of Baranagar Unit During the year 1966 GRW was approached by the Government of India (Cabinet Secretariat) with a suggestion that the Development Workshop set up by the Indian Statistical Institute (ISI) at Baranagar utilising mostly machine tools supplied to them under Govt. scheme should be taken over by GRW as the Government of India wished to discontinue the annual grants in aid which were being given to the Institute for Maintaining the Development Workshop. GRW accepted this proposal and took over the machine tools from the Indian Statistical Institute along with the connected manpower. The unit was then converted into a full-fledged subsidiary unit of GRW and started contributing for the Main Workshops and also for the Marine Diesel Engine Plant at Ranchi for undertaking the manufacture of jigs, fixtures, and various other tools. With effect from 1st April 1995, the Unit was converted into a Technical Training Centre (TTC). It conducts training for Trade Apprentices, Graduate / Diploma Engineers, and Trainee Marine Engineers. Establishment of Shipbuilding Activities at GRW Of the various activities of GRW, shipbuilding activities were also started In 1969-70. GRW received orders for one number Cutter Suction Dredgers for Ministry of Transport, two numbers Cutter Suction Dredgers for DGS & D and two Hydroklapp Hopper Barges for Vizag Port Trust. GRW by and large became the principal producer of harbour crafts like Tugs, Dredgers, Hopper Barges etc. By the end of 1969-70, the Company had shipbuilding orders to the tune of Rs 190 million in hand for execution. The port trust and Government of India had tremendous Confidence in the ability of indigenous shipbuilding facility available at GRW while placing orders for sophisticated vessels. GRW being in the Defence Sector, it was only appropriate that it should participate in a greater measure for the supply of Naval equipment. The plans of GRW to develop capacity for construction of ocean going cargo vessels reached an advanced stage, and the detailed project report was submitted to Government in 1969. While the existing shallow No.1 Dry Dock was proposed to be modernized as a construction Dry Dock for construction of hulls for cargo ships upto 26000 DWT, the problem of finding suitable area for constructing a Fitting Out Jetty (FOJ) was posing certain difficulties. The Calcutta port Commissioners in their centenary year had in principle agreed to lease some water front and some land in the King George Docks (later renamed as Netaji Subhas Docks) extension area where the Company’s Fitting out Jetty could be Constructed inside a fully protected basin. The Govt. of India approved a 3 years project in 1971 at a cost of Rs 30 million, and the work commenced in 1972. The first vessel of Calcutta port commissioners costing about Rs. 9 crores was built and the vessel was 7500 tons Twin Screw Dredger. GRSE LTD. STUDY MATERIAL FOR GAAT - 2024 Establishment of 61 Park as Production Unit In order to keep pace with the accelerated growth of shipbuilding activities, it was decided in 1969 to reorganize and relocate some of the facilities in the Main Works in such a way so that whole area of 43/46, Garden Reach was available mainly for shipbuilding activity and steel structural works. Accordingly, the additional area for production activities was made available by converting the company’s residential estate for senior executives at 61, Garden Reach Road into Factory space. Thus 61- Park was finally got ready as Engineering Production Unit of GRW in 1971. Presently, the 61 Park Unit is concentrated mainly on manufacturing of Bailey Bridges and Steel Plant Equipment. Deck Machinery (Taratala Unit) GRW acquired the assets of Agrind Fabrications Ltd. (in liquidation) at Taratalla, from the Industrial Finance Corporation of India in April 1972. The production unit of “GRW BRAND” Road Rollers was immediately shifted there as a diversification measure. After the production of Road Rollers was phased out, this unit has been converted into Deck Machinery unit as a separate cost centre. To achieve self-reliance, Deck Machinery Department was established in 1970 with a view to indigenize sophisticated Deck Machinery items. The department has been developing, designing, manufacturing, & supplying both Electro-Hydraulic as well as Electric Marine Equipment meeting different class requirements. Raja Bagan Dockyard GRSE acquired the Raja Bagan Dockyard (RBD) from Central Inland Water Transport Co. Ltd.- a Public Sector Unit under the administrative control of the Ministry of Shipping, Govt. of India, as per the Union Cabinet’s decision. The RBD has been transferred to GRSE with effect from 1st July 2006 at a total purchase consideration of Rs 58 crores, making the GRSE the biggest Defence Shipyard in India for the asset holding. Soon after taking over, the steel fabrication work for ship construction started in RBD. On 29 August 2007, the keels for the Third and Fourth Water Jet FACs for the Indian Navy were laid signalling commencement of official full-fledged production of Warship in Raja Bagan Dockyard. The yard has large infrastructure with three Dry Docks, two slipways, four shipbuilding berths and five water front jetties. The RBD has an area of 33 acres having river frontage of about 600 metres. GRSE LTD. STUDY MATERIAL FOR GAAT - 2024 CURRENT SCENARIO Garden Reach Shipbuilders & Engineers Ltd., has today grown into a premier shipyard of India, under the administrative control of the Ministry of Defence, Govt. of India, building state of the art warships for the Indian Navy & Indian Coast Guard. The shipyard was conferred the status of a Miniratna Category I Company in 2006. Over last 63 years, GRSE has built over 790 platforms including 109 warships for Indian Navy, Indian Coast Guard, and friendly foreign countries - highest warships built & delivered by any Indian shipyard till date. From building 05 ton boats to 24600 ton Fleet Tanker, GRSE has done it all and has proved its mettle as a pioneer warship builder of the nation. Shipbuilding has been the core business vertical and the shipyard has modernized its infrastructure spread across the three ship production locations in Kolkata. With integrated ship construction using modular construction technology, the shipyard is equipped to construct 20 ships concurrently powered with a strong team of multi- disciplinary Design Engineers creating innovative designs for current & future ready warships. The state-of-the-art Virtual Reality Lab and the latest design software, aid the design team in their efforts towards innovation in ship design using better ergonomics. GRSE is currently executing four warship building projects for Indian Navy worth approximately Rs. 25,000 Crore including a Prestigious P17A Project for three Advanced Frigates and two projects won on competitive bidding, four Survey Vessels (Large), eight Anti-Submarine Warfare Shallow Water Crafts & 04 Next Generation Offshore Patrol Vessel. GRSE also built the first ever Indian Export Warship “CGS Barracuda” for Govt. of Mauritius, a Fast Patrol Vessel “SCG PS Zoroaster” for Seychelles and an Ocean-Going Cargo & Passenger Ferry Vessel “MV Ma Lisha” for Cooperative Republic of Guyana. GRSE has made commendable progress by successfully incorporating a high percentage of indigenous equipment fit into the ships being built for the Indian Navy and Indian Coast Guard, having achieved over 90 % indigenous content onboard Anti- Submarine Warfare Corvettes, Landing Craft Utility Ships & Survey Vessel (Large). In addition to shipbuilding, GRSE as a diversified organisation, is also having a dedicated ship repair vertical since 2018 to focus on the demand for repairs in the Indian Maritime sector. GRSE, with its in-house design capability and vast pool of expertise and modern assets, has built and repaired ships for countries including Sri Lanka, Mauritius and Seychelles. GRSE is also engaged in engine overhaul, assembly & testing and other engineering activities. The engineering division manufactures deck machinery items, pre- fabricated portable steel bridges and marine pumps. While shipbuilding has been GRSE’s core competency, the Shipyard have supplied more than 5500 Portable Steel Bridges to the Indian Army, Border Roads Organisation, State PWDs & Central Government. These bridges, primarily used for disaster management, have also been exported to friendly countries including Bangladesh, Bhutan, Nepal, Myanmar & Sri GRSE LTD. STUDY MATERIAL FOR GAAT - 2024 Lanka. GRSE has achieved notable milestones in Bridge development, including the introduction of the Double Lane Portable Steel Bridge & Portable Assault Bridge, both firsts in India. In 2022, GRSE became the first shipyard to receive Green Channel Certification by DGQA for supplying Bailey Portable Steel Bridges to the Indian Army. GRSE installed the Majherhat Bridge in Kolkata in a record time of six days and also installed a bridge connecting VIP Road & Salt Lake, again in a record time of 12 days. Pre-fabricated Portable Steel Bridges have also been installed at Darjeeling, Bankura, Tamluk, Jalpaiguri and Krishnanagar, Nadia District of West Bengal. GRSE also has a Technical Training Centre in Taratala Unit, Kolkata. The Deck Machinery of GRSE is a vertical which provides tailor-made equipment for ships being built at different shipyards in the country. The product range includes Anchor and Mooring Capstans, Boat Davits, Helicopter Handling Systems, Miscellaneous Winches and Telescopic Helicopter Hangars of different sizes. Over the past year, the Deck Machinery Division has been reinventing its product portfolio to inject contemporary design and technology into its products. Towards this, successful partnerships have been forged with partner companies to design and develop the GRSE Helicopter Handling System (GHHS) as well as the Ground Support Equipment (GSE) for various Helicopter in use in the Indian Navy and Coast Guard. The existing portfolio has also seen improvement in design, aesthetics and technology. The national motto of "Atmanirbhar Bharat" is the core philosophy of all products being developed at TU. Our Diesel Engine Plant or DEP is situated on 62 acres at Ranchi, Jharkhand. This is where we assemble, test and overhaul marine engines. GRSE's DEP is fully equipped with a test bench facility and has highly trained service personnel. The Plant was modernised recently and it tied-up with MTU, Germany for the indigenous manufacture of engine parts. The 1 MW Diesel Alternator (DA) for naval applications is also manufactured at DEP. It comprises a prime mover coupled with a flexible coupling to an alternator, housed by an acoustic and thermal enclosure. The complete assembly with associated accessories is seated on the steel base frame with resilient mounts. The steel base frame is provided with a set of mounts at the interface to the ship structure to provide resistance to shock and vibration. The DA features a closed ventilation system. It is equipped with all necessary systems required for operation of engine and alternator along with the operational safety systems for the equipment and working personnel for all Naval applications. In GRSE's pursuit for self - reliance in defence manufacturing and to minimize imports, GRSE has embarked on an ambitious project for Indigenisation of a technologically complex weapon system like the 30mm Naval Surface Gun. For this, GRSE has created yet another new business vertical for manufacture and supply of 10 Naval Surface Guns with Electro Optical Fire Control System (EOFCS) for the Indian Navy. GRSE has entered into a joint venture with an Industry Partner for this project and an assembly set up has been established at Taratala Unit. GRSE has considerable expertise & capability for on-board installation of various Guns and engineering GRSE LTD. STUDY MATERIAL FOR GAAT - 2024 support for such products. The 30mm NSG will be fitted onboard small ships as its primary weapon and on large ships as a secondary weapon for engaging fast moving surface targets/threats. It is envisaged that with the technological features of this gun, all future warship projects will be equipped with the NSG-30. Autonomous systems is the most important technology area which has the potential to bring about disruptive changes in the maritime sector in the near future. GRSE has been able to successfully combine intricate knowledge imbibed over years of designing and building complex platforms and the transformative potential of start- ups, to work on following critical technologies.: a) Unmanned Surface Vessel (USV): Swadheen, is a 5 m long USV designed specifically to meet the unique needs of the Indian Navy, while also acting as a robust testing ground for future larger and more sophisticated USVs. Swadheen which is being developed in collaboration with a start-up is now being outfitted with a complete bathymetry survey suite to facilitate autonomous surveys. b) Autonomous Underwater Vehicle (AUV): GRSE in collaboration with an industry partner has developed a Man Portable AUV. The AUV has been designed as a completely autonomous vehicle and is designed to take on a variety of payloads depending on the required role including mine detection, ASW training, underwater inspection, search & rescue missions and scientific exploration. c) Ship Based Autonomous Drones/ Unmanned Aerial Vehicle (UAV): The UAV currently being developed by GRSE will be capable of day & night autonomous operations and autonomous recovery on deck, without any manual intervention. The UAV will be able to provide day and night surveillance video feed to a ground control station on the mother ship and complete a pre-defined mission autonomously. GRSE’S LAND MARK ACHIEVEMENTS OVER THE YEARS First Shipyard of Independent India to build a Seaward Defence Boat (SDB): INS Ajay was delivered to the Indian Navy in 1961. This ship was later gifted to Bangladesh and was renamed as BNS Surma. First Ever Patrol Vessel Built for Indian Coast Guard: 23 December 1980 would remain a red letter day in the history of both GRSE & Indian Coast Guard when the first ever patrol vessel built for Indian Coast Guard (ICG) CGS Rajhans was commissioned. CGS Rajshree delivered to the ICG in 2012 has a unique distinction of being launched by two women employees of GRSE. First Ever Indigenous Survey Vessel: The first Survey Vessel for Indian Navy was also designed and built by GRSE. This ship INS Sandhayak, was commissioned on 26 February 1981. The Landing Ship Tanks built by GRSE were termed as Landing Ship Tanks GRSE LTD. STUDY MATERIAL FOR GAAT - 2024 (Large), to differentiate from the medium sized LSTs then in service with Indian Navy. The First of Class LST (L) designed in-house & built by GRSE, INS Magar was commissioned in 1987. GRSE the only Indian Shipyard to have built a Fleet Replenishment Tanker: INS Aditya, the largest indigenously built Fleet Replenishment Tanker was delivered to the Indian Navy on 21 March 2000. First Indian Shipyard to build a Marine Acoustic Research Ship for Indian Navy / Naval Laboratory, INS Sagardhwani. First Indian Shipyard to have built Hovercrafts: GRSE had built a total of six Hovercrafts for the Indian Coast Guard. The First Hovercraft H-181 was commissioned on 18 September 2000. First Ever Warship Built in India for Export: CGS Barracuda was commissioned at Port Louis, Mauritius on 12 March 2015, in the august presence of Hon’ble Prime Minister of India, Shri Narendra Modi and Hon’ble Prime Minister of Mauritius, Sir Anerood Jagnauth. This was a historic occasion for India and GRSE in particular. The In-House Design & Construction of this first ever export warship of the country, has been yet another feather in the cap of GRSE. In recognition of its efforts, GRSE was awarded the Raksha Mantri’s Award for Excellence 2015-16 for In house Design Effort for this Vessel. GRSE achieved over 70 % indigenous content in construction of the four Follow On WJFACs for Indian Navy. INS Kamorta & INS Kadmatt, the First Two of Class of 4 ASW Corvettes became the first warships built in the country with indigenously developed warship grade steel, thus having the distinction of achieving over 90 % indigenous equipment fit and hence a major step towards achieving self- reliance in state-of-the-art warship design and construction. LCUs have also achieved the distinction of 90% indigenous content. The 3rd & 4th ASW Corvettes, INS Kiltan & INS Kavaratti , delivered to Indian Navy, have the unique feature of superstructure made of carbon fibre composite material. It is for the first time in the country that such composite material has been integrated with steel hull of a ship and GRSE is the first shipyard in the country to have successfully achieved this feat. Use of this special material in superstructure has helped in reducing the overall weight of the ship resulting in greater stability of the platform. GRSE is the first DPSU Shipyard to be listed in Stock Exchanges. GRSE LTD. STUDY MATERIAL FOR GAAT - 2024 The 100th Warship, IN LCU L-56 which have made GRSE the first Indian shipyard to make and deliver 100 warships to the Indian Navy, Indian Coast Guard and Mauritius Coast Guard have the distinction of Zero Shipbuilder’s Liability and Gun Trials completed prior delivery to Indian Navy on 30 March 2019. GRSE accomplished a key milestone in the prestigious Project 17A on 14 Dec 20, with the launch of the first of three Stealth Frigates, “Himgiri”. The ship was “Launched” by Smt. Madhulika Rawat, wife of General Bipin Rawat, PVSM, UYSM, AVSM, YSM, SM, VSM, ADC, Chief of Defence Staff who graced the occasion as the Chief Guest. Launching of the ship was done 02 months ahead of schedule. Transportation of a 250T fully assembled goliath crane by sea and the complex process of unloading from ship to shore directly on crane tracks has been undertaken for the first time in India on 22 Jun 21 GRSE Launched "Dunagiri" (Yard 3023) the second of GRSE’s three Advanced Frigates on 15 Jul 22, by Shri Rajnath Singh, Hon'ble Minister of Defence, Government of India, the Chief Guest on the occasion. GRSE is the first shipyard to receive the Green Channel Certification by DGQA on 30 Aug 22 for supply of Portable Steel Bridges (Bailey Type) to Indian Army The Hon’ble President of India Smt. Droupadi Murmu launched INS Vindhyagiri, the last in the series of three P17 Alpha being built for the Navy by GRSE on 17 Aug 23. This is for the first time that a ship being built by an Indian shipbuilder is being launched by the President of India, who is also the Supreme Commander of the Indian Armed Forces. For the first time in the company’s history of 63 years as a DPSU, achieved an Annual Turnover to the tune of Rs 3588.46 Crore for FY 2023-24 Ongoing Projects – 04 Projects comprising of 18 warships for Indian Navy, 01 Project comprising of 01 NG Electric Ferry for Govt of West Bengal, 01 Project comprising of 01 vessel for NCPOR, 03 Projects comprising of 05 vessels for Bangladesh, 01 Project comprising of 04 Multi Purpose Vessels for Germany GRSE LTD. STUDY MATERIAL FOR GAAT - 2024 Recent Achievements Only Indian Shipyard to deliver over 100 Warships since 1960 (109 Warships delivered till 31 Mar 24) Bagged orders for delivering an advanced Ocean Research Vessel for NCPOR, MoES, an Ocean-Going Tug and TSH Dredger for the Government of Bangladesh, and four multi-purpose vessels for a German company. Only PSU Shipyard to receive Raksha Mantri’s Award 2022 for Excellence in Defence & Aerospace Sector for ‘Design of Most Silent Ship for IN, for ASW SWC Operations’ Received the Defence Minister’s Award of Excellence for in-house Design Effort for OPV built for Government of Mauritius Design and R&D Unit of GRSE has been recognized by DSIR, Ministry of Science and Technology, GoI A Profit Making and Dividend Paying company for the past 30 years First Defence Shipyard to get listed with Stock Exchanges Approximately 90% Indigenous Content on ASW Corvettes, LCUs & SV(L) Bagged an order to build Next Generation Electric Ferry for Government of West Bengal Only Shipyard to receive Green Channel Certification by DGQA for supply of Bailey Type Portable Steel Bridges to Indian Army Developed Double Lane Portable Steel Bridge and Portable Assault Bridge for the 1st time in India Delivered Export Warship, SCG PS Zoroaster, FPV to Seychelles Coast Guard Delivered MV ‘Ma Lisha’, an Ocean-Going Passenger-cum-Cargo Ferry to Cooperative Republic of Guyana Diversified successfully into the manufacture of 30 mm Naval Surface Guns First DPSU shipyard in the country to secure 100 Intellectual Property Rights (IPRs) from the Government of India Best Performing Defence Shipyard of India for Four Years in a Row Bagged Prestigious Awards for AI, R&D, CSR, Sustainability, Corporate Governance, HR Practices, Communication Outreach, Digital Transformation, Best Organisational Efforts, Outstanding Initiatives in Promoting Medical and Health etc. Launched two editions of GRSE Accelerated Innovation Nurturing Scheme (GAINS) for Indian Startups to develop innovative technologically-advanced solutions for the shipbuilding industry Yard Vision With our motto “In Pursuit of Excellence and Quality in Shipbuilding”, our vision is to become a “Global Leader in Warship Building”. ************ GRSE LTD. STUDY MATERIAL FOR GAAT - 2024 CHAPTER - 2 CENTRAL DESIGN OFFICE (CDO) 1. Role of CDO: The role of CDO gains greater significance considering that most shipbuilding projects undertaken by GRSE follow a concurrent design and production approach wherein production commences well before the design is frozen or complete, making the task of design, planning and construction even more challenging for the yard. The role of CDO encompasses the complete spectrum of activities of the shipbuilding division of GRSE from the pre-contract stage to post-delivery guarantee period. The stage wise role of CDO is enumerated below: (a) Pre-contract stage: Technical offers of bids made by GRSE in competitive ship building orders are made by CDO. The technical offer will require a concept design of ship to be completed so that costing of the project can be arrived at by the CE&C department. The concept design will include the following activities: i. Design of Hull form, stability Calculations & Powering Estimates ii. Model Testing – Validation of Hull form (for nomination projects) iii. Development of preliminary GA iv. Estimation of Auxiliary Power – Electrical Load Chart v. Design Calculations as per Statutory Regulations / Class vi. Preparation of Specifications vii. Preparation of BOM for costing viii. Obtaining Budgetary Quotes for equipment fit ix. Interactions with OEMs for finalization of specifications x. Technical interaction with Owner (IN / CG) (b) Contract Stage: The CDO plays a pivotal role in the formulation of the Build Specifications of the ship and finalizing the ship building contract. The Build Specifications, which amplifies the Preliminary Staff Requirements (PSR) of the ship, specifies the functional requirements of all equipment and systems on board the ship. The rules and standards to which the ship is to be designed and constructed and the general contours of the project are covered in the Build Specifications which hitherto has been prepared almost entirely by CDO. For all future projects, whilst the Build Specifications will continue to be prepared by CDO, it is planned to involve other Page | 11 GRSE LTD. STUDY MATERIAL FOR GAAT - 2024 departments, such as Production, Material, Planning and QA during the finalization of the Build Specification. (c) Preparatory Phase: During this stage, which commences immediately after signing of contract until the commencement of production, the CDO is actively involved in its core activity of design. The nature of work varies depending on the type of the project. In the present scenario, almost all the shipbuilding orders from IN/ IGC, other government agencies, foreign customers are secured by the shipyard through competitive bidding and all the design activities starting from basic design to detailed design are carried out by CDO and solely responsible for the design. IN/ IGC/ class nominated by the owner is approving authority. However, for major frontline naval warships (whether nominated or on competitive bidding), the basic design is done by Warship Design Bureau (WDB) of IN and the detailed design is carried out by CDO. The following major activities are carried out during the design stage of the project by CDO: i. Preparation of Schedules along with Planning Drawing schedule Schedule of SOTRs Indent schedule GRAQs schedule ii. Basic / Preliminary Design Hull Classification drawings Hull Outfit system drawings Engineering system drawings L&W system drawings Interaction with Owner / Classification Societies for drawings approval Conducting various design studies: (a) Model Testing (b) PSI (c) EMI/EMC (d) Stealth iii. Indent for material / binding data Page | 12 GRSE LTD. STUDY MATERIAL FOR GAAT - 2024 Preparation of SOTRs Generation of material code for each item Preparation of BOM for raising indent Technical evaluation of offers Correspondence with bidders Conduct of TNC Technical clearance of offers Obtaining of drawings, documents & QAP from OEMs Scrutiny / approval of binding data / drawings Updating of indents based on outcome of TNC (d) Detailed Design: On completion of the functional design and on availability of binding data and drawings from various OEMs, CDO commences the ‘Detailed Design’ phase of the project. The detailed design is the longest phase of the project and for concurrent design and construction projects, this phase continues until the trials phase of the project. The major activities of detailed design are as follows: i. Hull Preparation of structural arrangement / Class approval drawings Block / Unit 3D modelling of Hull structure in Aveva Marine software Generation of unit / block production drawings from Aveva Marine Structural analysis using FEM software (Hyperworks) Plate nesting and generation for CNC plate cutting Generation of skid info from 3D Aveva Marine model Generation of plate / stiffener bending information from 3D model Creation of 3D models / drawings of all seatings / foundations ii. Engineering / L&W /Hull outfit Creation of 3D component library Modelling of all compartments / modules Page | 13 GRSE LTD. STUDY MATERIAL FOR GAAT - 2024 Routing of 3D piping of all systems through all modules / compartments. Preparation of cable schedule / route and connecterization Checking of collision / interference Generation of pipe sheets for production Technical discussions with IHQ/CGHQ/ class for approval of drawings (e) Production Support: Once the construction of the ship commences at the yard, considerable time and resources of CDO is spent on Production support. This involves daily interaction at the production site and various production reviews and interaction with yard, QA and WOT. The major activities of CDO for production support are as follows: i. Design Modification / support Raising MODs for changes sought by the Owner Design re-work for MODs Design re-work for production related issues Resolving production issues with QA/WOT Resolving specifications / standards related issue with IHQ / CGHQ ii. Launching and docking Carry out calculations for all launchings and dockings Pre-launching & Pre-docking/undocking activity schedule iii. Yard Sub-contracted work Preparation of SOTRs of all sub-contracted work Participation in TNC for sub-contracted work Page | 14 GRSE LTD. STUDY MATERIAL FOR GAAT - 2024 (f) Trials Phase: CDO works closely with IHQ, IN trial agencies, WOT, GRSE QA and Production floor during the trials of all ships. The involvement of CDO is particularly high for the first of class and requirement gradually tapers for subsequent ships. Some of the major activities related to trial that CDO is engaged in are: i. GRAQs Finalisation of GRAQs for systems / Equipment Approval of GRAQs by IHQ / Owner after comments from WOT/MTU/ETMU Issue of approved GRAQs to berth and trial agencies Assistance to berth during conduct of trials ii. HATs/SATs Preparation of BT/HATs/SATs schedule Approval of HATs/SATS schedule by Owner Attending all HATs and SATs Participation in CST / FMT Conducting of Inclining Experiment Association in Citadel Test (g) Delivery and Post Delivery: CDO is actively involved with the Ship Staff, WOT and IHQ during the Delivery of the vessel and co-ordinated with the PP&C Department to prepare the D448 document. The following major activities are carried out by CDO during delivery and post delivery period of the ship: i. Documentation ii. Preparation of D787 iii. Preparation of allowance list and CRETE items iv. Preparation of system exploitation/ machinery information document v. Preparation of NBCD Class book, Ship’s Book vi. Preparation of Maintops and SFD vi. As-Fitted vii Drawings viii Preparation of all As-Fitted drawings (Hull/Engg./L&W/Outfit) Page | 15 GRSE LTD. STUDY MATERIAL FOR GAAT - 2024 ix. Preparation of As-Fitted composite layouts of all compartments x. Post Delivery xi. Design support for Guarantee defects xii. Design coverage for D448 liabilities xiii. Design support for all ships until GRDD The basic design procedure for a ship is furnished below: Basic Design of Commercial Ship The economic factor is of prime importance in designing a merchant ship. An owner requires a ship which will give him the best possible returns for his initial investment and running costs. This means that the final design should be arrived at taking into account not only present economic considerations, but also those likely to develop within the life of the ship. With the aid of computers it is possible to make a study of a large number of varying design parameters and to arrive at a ship design which is not only technically feasible but, more importantly, is the most economically efficient. Preparation of the Design The initial design of a ship generally proceeds through three stages: concept; preliminary; and contract design. The process of initial design is often illustrated by the design spiral (Figure 1.1) which indicates that given the objectives of the design, the designer works towards the best solution adjusting and balancing the interrelated parameters as he goes. A concept design should, from the objectives, provide sufficient information for a basic techno-economic assessment of the alternatives to be made. Economic criteria that may be derived for commercial ship designs and used to measure their profitability are net present value, discounted cash flow or required freight rate. Preliminary design refines and analyses the agreed concept design, fills out the arrangements and structure and aims at optimizing service performance. At this stage the builder should have sufficient information to tender. Contract design details the final arrangements and systems agreed with the owner and satisfies the building contract conditions. Total design is not complete at this stage, it has only just started, post-contract design entails in particular design for production where the structure, outfit and systems are planned in detail to achieve a cost and time effective building cycle. Production of the ship must also be given consideration in the earlier design stages, particularly where it places constraints on the design or can affect costs. Information Provided by Design When the preliminary design has been selected the following information is available: Dimensions Displacement Page | 16 GRSE LTD. STUDY MATERIAL FOR GAAT - 2024 Stability Propulsive characteristics and hull form Preliminary general arrangement Principal structural details Each item of information may be considered in more detail, together with any restraints placed on these items by the ships service or other factors outside the designer’s control. The dimensions are primarily influenced by the cargo carrying capacity of the vessel. In the case of the passenger vessel, dimensions are influenced by the height and length of superstructure containing the accommodation. Length where not specified as a maximum should be a minimum consistent with the required speed and hull form. Increase of length produces higher longitudinal bending stresses requiring additional strengthening and a greater displacement for the same cargo weight. Breadth may be such as to provide adequate transverse stability. A minimum depth is controlled by the draft plus a statutory freeboard; but an increase in depth will result in a reduction of the longitudinal bending stresses, providing an increase in strength, or allowing a reduction in scantlings. Increased depth is therefore preferred to increased length. Draft is often limited by area of operation but if it can be increased to give a greater depth this can be an advantage. Many vessels are required to make passages through various canals and this will place a limitation on the dimensions. The Suez Canal has a draft limit, locks in the Panama Canal and St. Lawrence Seaway limit length, beam and draft. In the Manchester Ship Canal locks place limitations on the main dimensions and there is also a limitation on the height above the water-line because of bridges. Displacement is made up of lightweight plus deadweight. The light-weight is the weight of vessel as built, including boiler water, lubricating oil, and cooling water system. Deadweight is the difference between the light-weight and loaded displacement, i.e. it is the weight of cargo plus weights of fuel, stores, water ballast, fresh water, crew and passengers, and baggage. When carrying weight cargoes (e.g. ore) it is desirable to keep the lightweight as small as possible consistent with adequate strength. Since only cargo weight of the total deadweight is earning capital, other items should be kept to a minimum as long as the vessel fulfils its commitments. In determining the dimensions statically stability is kept in mind in order to ensure that this is sufficient in all possible conditions of loading. Beam and depth are the main influences. Statutory freeboard and sheer are important together with the weight distribution in arranging the vessel’s layout. Propulsive performance involves ensuring that the vessel attains the required speeds. The hull form is such that it economically offers a minimum resistance to motion so that a minimum power with economically lightest machinery is installed without losing the specified cargo capacity. Page | 17 GRSE LTD. STUDY MATERIAL FOR GAAT - 2024 A service speed is the average speed at sea with normal service power and loading under average weather conditions. A trial speed is the average speed obtained using the maximum power over a measured course in calm weather with a clean hull and specified load condition. This speed may be a knot or so more than the service speed. Unless a hull form similar to that of a known performance vessel is used, tank tests of a model hull are generally specified nowadays. These provide the designer with a range of speeds and corresponding powers for the hull form, and may suggest modifications to the form. Published data from accumulated ship records and hull tests may be used to prepare the hull form initially. The owner may often specify the type and make of main propulsion machinery installation with which their operating personnel are familiar. The general arrangement is prepared in co-operation with the owner, allowing for standards of accommodation peculiar to that company, also peculiarities of cargo and stowage requirements. Efficient working of the vessel must be kept in mind throughout and compliance with the regulations of the various authorities involved on trade routes must also be taken into account. Some consultation with shipboard employees’ representative organizations may also be necessary in the final accommodation arrangements. Almost all vessels are built to the requirements of a classification society such as Lloyd’s Register. The standard of classification specified will determine the structural scantlings and these will be taken out by the ship-builder. The calculation of hull structural scantlings can be carried out by means of computer programs made available to the shipyard by the classification society. Owners may specify thicknesses and material requirements in excess of those required by classification societies and special structural features peculiar to the trade or owner’s fleet may be asked for. Purchase of a New Vessel In recent years the practice of owners commissioning ‘one off’ designs for cargo ships from consultant naval architects, shipyards or their own technical staff has increasingly given way to the selection of an appropriate ‘stock design’ to suit their particular needs. To determine which stock design, the ship owner must undertake a detailed project analysis involving consideration of the proposed market, route, port facilities, competition, political and labour factors, and cash flow projections. Also taken into account will be the choice of shipbuilder where relevant factors such as the provision of government subsidies/grants or supplier credit can be important as well as the price, date of delivery, and yards reputation. Most stock designs offer some features which can be modified, such as outfit, cargo handling equipment, or alternate manufacture of main engine, for which the owner will have to pay extra. Purchase of a passenger vessel will still follow earlier procedures for (a) ‘one-off’ design but there are shipyards concentrating on this type of construction and the owner may be drawn to them for this reason. A non-standard cargo ship of any form and a number of specialist ships will also require a ‘one-off’ design. Having decided on his basic requirements, i.e. the vessel’s objectives, after an appropriate project analysis the larger ship-owners may employ their own technical Page | 18 GRSE LTD. STUDY MATERIAL FOR GAAT - 2024 staff to prepare the tender specification and submit this to shipbuilders who wish to tender for the building of the ship. The final building specification and design is prepared by the successful tendering shipbuilder in co-operation with the owners technical staff. The latter may oversee construction of the vessel and approve the builders drawings and calculations. Other ship-owners may retain a firm of consultants or approach a firm who may assist with preliminary design studies and will prepare the tender specifications and in some cases call tenders on behalf of the owner. Often the consultants will also assist the owners in evaluating the tenders and oversee the construction on their behalf. Ship Contracts The successful tendering shipbuilder will prepare a building specification for approval by the owner or his representative which will form part of the contract between the two parties and thus have legal status. This technical specification will normally include the following information: Brief description and essential qualities and characteristics of ship. Principal dimensions. Deadweight, cargo and tank capacities, etc. Speed and power requirements. Stability requirements. Quality and standard of workmanship. Survey and certificates. Accommodation details. Trial conditions. Equipment and fittings. Machinery details, including the electrical installation, will normally be produced as a separate section of the specification. Most shipbuilding contracts are based on one of a number of standard forms of contract which have been established to obtain some uniformity in the contract relationships between builders and purchasers. Three of the most common standard forms of contract have been established by: 1) AWES—Association of West European Shipbuilders. 2) MARAD Maritime Administration, USA. 3) SAJ Shipowners Association of Japan. The AWES standard form of contract includes: 1) Subject of contract (vessel details, etc.). 2) Inspection and approval. 3) Modifications. 4) Trials. 5) Guarantee (speed, capacity, fuel consumption). 6) Delivery of vessel. 7) Price. Page | 19 GRSE LTD. STUDY MATERIAL FOR GAAT - 2024 8) Property (rights to specification, plans, etc.). 9) Insurance. 10) Defaults by the purchaser. 11) Defaults by the contractor. 12) Guarantee (after delivery). 13) Contract expenses. 14) Patents. 15) Reference to expert and arbitration. 16) Conditions for contract to become effective. 17) Legal domicile (of purchaser). 18) Assignment (transfer of purchaser’s rights to third party). Irrespective of the source of the owner’s funds for purchasing the ship payment to the shipbuilder is usually made as progress payments which are stipulated in the contract under item 7 above. A typical payment schedule may have been as follows: 10 per cent on signing contract. 10 per cent on arrival of materials on site. 10 per cent on keel laying. 20 per cent on launching. 50 per cent on delivery. Given modern construction techniques, where the shipbuilder’s cash flow during the building cycle can be very different from that indicated above with traditional building methods, the shipbuilder will probably prefer payments to be tied to different key events. Also of concern to the shipbuilder employing modern building procedures is item 3 in the standard form of contract where modifications called for at a late date by the owner can have a dramatic effect on costs and delivery date given the detail now introduced at an early stage of the fabrication process. Ship Dimensions and Form The hull form of a ship may be defined by a number of dimensions and terms which are often referred to during and after building the vessel. An explanation of the principal terms is given below: After Perpendicular (AP): A perpendicular drawn to the waterline at the point where the aft side of the rudder posts meets the summer load line. Where no rudder post is fitted it is taken as the centre line of the rudder stock. Forward Perpendicular (FP): A perpendicular drawn to the waterline at the point where the foreside of the stem meets the summer load line. Length between Perpendiculars (LBP): The length between the forward and aft perpendiculars measured along the summer load line. Amidships: A point midway between the after and forward perpendiculars. Length Overall (LOA): Length of vessel taken over all extremities. Page | 20 GRSE LTD. STUDY MATERIAL FOR GAAT - 2024 Lloyd’s Length: Used for obtaining scantlings if the vessel is classed with Lloyd’s Register. It is the same as length between perpendiculars except that it must not be less than 96 per cent and need not be more than 97 per cent of the extreme length on the summer load line. If the ship has an unusual stem or stern arrangement the length is given special consideration. Register Length is the length of ship measured from the fore-side of the head of the stem to the aft side of the head of the stern post or, in the case of a ship not having a stern post, to the fore-side of the rudder stock. If the ship does not have a stern post or a rudder stock, the after terminal is taken to be the aftermost part of the transom or stern of the ship. This length is the official length in the register of ships maintained by the flag state and appears on official documents relating to ownership and other matters concerning the business of the ship. Another important length measurement is what might be referred to as the IMO Length. This length is found in various international conventions such as the Load Line, Tonnage and SOLAS conventions and determines the application of requirements of those conventions to a ship. It is defined as 96 per cent of the total length on a waterline at 85 per cent of the least moulded depth measured from the top of keel, or the length from the fore-side of stem to the axis of rudder stock on that waterline, if that is greater. In ships designed with a rake of keel the waterline on which this length is measured is taken parallel to the design waterline. Moulded dimensions are often referred to; these are taken to the inside of plating on a steel ship. Base Line: A horizontal line drawn at the top of the keel plate. All vertical moulded dimensions are measured relative to this line. Moulded Beam: Measured at the midship section is the maximum moulded breadth of the ship. Moulded Draft: Measured from the base line to the summer load line at the midship section. Moulded Depth: Measured from the base line to the heel of the upper deck beam at the ship’s side amidships. Extreme Beam: The maximum beam taken over all extremities. Extreme Draft: Taken from the lowest point of keel to the summer load line. Draft marks represent extreme drafts. Extreme Depth: Depth of vessel at ship’s side from upper deck to lowest point of keel. Half Breadth: Since a ship’s hull is symmetrical about the longitudinal centre line, often only the half beam or half breadth at any section is given. Freeboard: The vertical distance measured at the ship’s side between the summer load line (or service draft) and the freeboard deck. The freeboard deck is normally the uppermost complete deck exposed to weather and sea which has permanent means of closing all openings, and below which all openings in the ship’s side have watertight closings. Page | 21 GRSE LTD. STUDY MATERIAL FOR GAAT - 2024 Sheer: Curvature of decks in the longitudinal direction. Measured as the height of deck at side at any point above the height of deck at side amid-ships. Camber (or Round of Beam): Curvature of decks in the transverse direction. Measured as the height of deck at centre above the height of deck at side. Rise of Floor (or Deadrise): The rise of the bottom shell plating line above the base line. This rise is measured at the line of moulded beam. Half Siding of Keel: The horizontal flat portion of the bottom shell measured to port or starboard of the ship’s longitudinal centre line. This is a useful dimension to know when dry-docking. Tumblehome: The inward curvature of the side shell above the summer load line. Flare: The outward curvature of the side shell above the waterline. It promotes dryness and is therefore associated with the fore end of ship. Stem Rake: Inclination of the stem line from the vertical. Keel Rake: Inclination of the keel line from the horizontal. Trawlers and tugs often have keels raked aft to give greater depth aft where the propeller diameter is proportionately larger in this type of vessel. Small craft occasionally have forward rake of keel to bring propellers above the line of keel. Tween Deck Height: Vertical distance between adjacent decks measured from the tops of deck beams at ship side. Page | 22 GRSE LTD. STUDY MATERIAL FOR GAAT - 2024 Sheer forward Sheer aft Freeboard Amidships Summer load line Length between perpendiculars (LBP) Length on waterline (LWL) Length overall (LOA) Aft Ford perpendicular perpendicular Tumblehome Camber Depth Moulded beam Draft Base Rise of floor line Half siding of keel FIGURE 2.1 Principal ship dimensions GRSE LTD. STUDY MATERIAL FOR GAAT - 2024 Parallel Middle Body: The length over which the midship section remains constant in area and shape. Entrance: The immersed body of the vessel forward of the parallel middle body. Run: The immersed body of the vessel aft of the parallel middle body. Tonnage: This is often referred to when the size of the vessel is discussed, and the gross tonnage is quoted from Lloyd’s Register. Tonnage is a measure of the enclosed internal volume of the vessel (originally computed as 100 cubic feet per ton). This is dealt with in detail in Chapter 30. Deadweight: This is defined in Chapter 1. It should be noted that for tankers deadweight is normally quoted in ‘long tons’ rather than ‘metric tonnes’. The principal dimensions of the ship are illustrated in Figure 2.1 Development of Ship Types A breakdown into broad working groups of the various craft which the shipbuilder might be concerned with are shown in Figure 3.1. This covers a wide range and reflects the adaptability of the shipbuilding industry. It is obviously not possible to cover the construction of all those types in a single volume. The development of the vessels with which the text is primarily concerned, namely dry cargo ships, bulk carriers, tankers, and passenger ships follows. Dry Cargo Ships If the development of the dry cargo ship from the time of introduction of steam propulsion is considered the pattern of change is similar to that shown in Figure 3.2. The first steam ships followed in most respects the design of the sailing ship having a flush deck with the machinery openings pro-tected only by low coamings and glass skylights. At quite an early stage it was decided to protect the machinery openings with an enclosed bridge structure. Erections forming a forecastle and poop were also introduced at the forward and after end respectively for protection. This resulted in what is popularly known as the ‘three island type’. A number of designs at that time also combined bridge and poop, and a few combined bridge and fore- castle, so that a single well was formed. Another form of erection introduced was the raised quarter deck. Raised quarter decks were often associated with smaller deadweight carrying vessels, e.g. colliers. With the machinery space aft which is proportionately large in a small vessel there is a tendency for the vessel to trim by the bow when fully loaded. By fitting a raised quarter deck in way of the after holds this tendency was eliminated. A raised quarter deck does not have the full height of a tween deck, above the upper deck. Further departures from the ‘three island type’ were brought about by the carriage of cargo and cattle on deck, and the designs included a light covering built over the wells for the protection of these cargoes. This resulted in the awning or spar deck type of ship, the Page | 24 GRSE LTD. STUDY MATERIAL FOR GAAT - 2024 temporarily enclosed spaces being exempt from tonnage measurement since they were not permanently closed spaces. These awning or spar deck structures eventually became an integral part of the ship structure but retained a lighter structure than the upper deck structure of other two-deck ships, later referred to as ‘full scantling’ vessels. The ‘shelter deck type’ as this form of vessel became known, apart from having a lighter upper structure, was to have the free-board measured from the second deck, and the tween deck space was exempt from tonnage measurement. This exemption was obtained by the provision of openings in the shelter deck and tween deck bulkheads com-plying with certain statutory regulations. At a later date what are known as open/closed shelter deck ships were developed. These were full scantling ships having the prescribed openings so that the tween deck was exempt from tonnage measurement when the vessel was operating at a load draft where the freeboard was measured from the second deck. It was possible to close permanently these temporary openings and re-assign the freeboard, it then being measured from the upper deck so that the vessel might load to a deeper draft, and the tween deck was no longer exempt from tonnage measurement. Open shelter deck vessels were popular with ship owners for a long period. However, during that time much consideration was given to their safety and the undesirable form of temporary openings in the main hull structure. Eliminating these openings without substantially altering the tonnage values was the object of much discussion and deliberation. Finally Tonnage Regulations introduced in 1966 provided for the assignment of a tonnage mark, at a stipulated distance below the second deck. A vessel having a ‘modified tonnage’ had tonnage measured to the second deck only, i.e. the tween deck was exempt, but the tonnage mark was not to be submerged. Where a vessel was assigned ‘alternative tonnages’ (the equivalent of previous open/closed shelter deck ship), tonnage was taken as that to the second deck when the tonnage mark was not submerged. When the tonnage mark was submerged, tonnage was taken as that to the upper deck, the freeboard being a minimum measured from the upper deck. The tonnage mark concept effectively dispensed with the undesirable tonnage openings. Further changes to tonnage requirements in 1969 led to the universal system of tonnage measurement without the need for tonnage marks although older ships did retain their original tonnages up until 1994. Originally the machinery position was amidships with paddle wheel propulsion. Also with coal being burnt as the propulsive fuel, bunkers were then favourably placed amidships for trim purposes. With the use of oil fuel this problem was more or less overcome, and with screw propulsion there are definite advantages in having the machinery aft. Taking the machinery right aft can produce an excessive trim by the stern in the light condition and the vessel is then provided with deep tanks forward. This may lead to a large bending moment in the ballast condition, and a compromise is often reached by placing the machinery threequarters aft. That is, there are say three or four holds forward and one aft of the machinery space. In either arrangement the amidships portion with its better stowage shape is reserved for cargo, and shaft spaces lost to cargo are reduced. The all aft cargo ship illustrating the final evolution of the dry cargo ship in Figure 3.2 could represent the sophisticated cargo liners of the mid-1960s. By the mid-1970s many of the cargo liner trades had been taken over by the container ship and much of the short haul trade undertaken by the conventional dry cargo ship had passed to the ‘roll on roll off’ (roro) type of vessel. A feature of the container ship is the stowage of the rectangular container units within the fuller rectangular portion of the hull and their arrangement in tiers above the main deck Page | 25 GRSE LTD. STUDY MATERIAL FOR GAAT - 2024 level. In order to facilitate removal and placing of the container units of internationally agreed standard (ISO) dimensions hold and hatch widths and lengths are common. The narrow deck width outboard of the hatch opening forms the crown of a double shell space containing wing ballast tanks and passageways (see Figure 17.8). Considerable ballast is required in particular for the larger container ships trading to the Far East where the beam depth ratio is low to allow transit of the Panama Canal. More recent container ship designs have featured hatchless vessels which are attractive to operators looking for a faster turnaround in port. These may have hatch covers on the forward holds only, or none at all, and are provided with substantial stripping pumps for removing rain and green water from the holds. Another development in the cargo liner trade was the introduction of the barge-carrying vessel. This type of ship has particular advantage in maintaining a scheduled service between the ports at mouths of large river systems such as that between the Mississippi river in the USA and the Rhine in Europe. Standard unit cargo barges are carried on board ship and placed overboard or lifted onboard at terminal ports by large deck mounted gantries or elevator platforms in association with travelling rails. Other designs make provision for floating the barges in and out of the carrying ship which can be ballasted to accommodate them. This development appears not to have been as successful as was initially envisaged in the late 1970s, and the type is now rarely seen. Ro-ro ships are characterized by the stern and in some cases the bow or side doors giving access to a vehicle deck above the waterline but below the upper deck. Access within the ship may be provided in the form of ramps or lifts leading from this vehicle deck to upper decks or hold below. Ro-ro ships may be fitted with various patent ramps for loading through the shell doors when not trading to regular ports where link-span and other shore side facilities which are designed to suit are available. Cargo is carried in vehicles and trailers or in unitized form loaded by fork lift and other trucks. In order to permit the drive through vehicle deck a restriction is placed on the height of the machinery space and the ro-ro ship was among the first to popularize the geared medium speed diesel engine with a lesser height than its slow speed counterpart. The dramatic loss of the ro-ro passenger ships Herald of Free Enterprise in 1987 and Estonia in 1994, respectively, saw much attention directed at the damage stability of this type of passenger ship when water entered the open un-subdivided vehicle deck space. This has resulted in international regulation requiring, amongst other things, strengthening and surveillance of bow doors, surveillance of internal water-tight doors used at sea, enhanced damage stability criteria (SOLAS 90) and additional simplified stability information for the master. The Estonia loss led to further more stringent damage stability requirements adopted on a regional basis by northern European countries (Stockholm Agreement, 1997). A midship section of a ro-ro passenger/vehicle/train ferry complying with the requirements of the latter agreement is shown in Figure 17.9. Between the 1940s and 1970s there was a steady increase in the speed of the dry cargo ship and this was reflected in the hull form of the vessels. A much finer hull is apparent in modern vessels particularly in those ships engaged in the longer cargo liner trades. Bulbous bow forms and open water sterns are used to advantage and considerable flare may be seen in the bows of container ships to reduce wetness on deck where containers Page | 26 GRSE LTD. STUDY MATERIAL FOR GAAT - 2024 are stowed. In some early container ships it is thought that this was probably overdone leading to an undesirable tendency for the main hull to whip during periods when the bows pitched into head seas. Larger container ships may have the house three-quarters aft with the full beam maintained right to the stern to give the largest possible container capacity. Cargo handling equipment, which remained relatively unchanged for a long period, has received considerable attention since the 1960s. This was primarily brought about by an awareness of the loss of revenue caused by the long periods of time the vessel may spend in port discharging and loading cargoes. Conventional cargo ships are now fitted with folding steel hatch covers of one patent type or another or slab covers of steel, which reduce maintenance as well as speed cargo handling. Various new lifting devices, derrick forms and winches have been designed and introduced which simplify as well as increase the rate of loading and discharge. Bulk Carriers The large bulk carrier originated as an ore carrier on the Great Lakes at the beginning of the 20th century. For the period to the Second World War dedicated bulk carriers were only built spasmodically for ocean trading, since a large amount of these cargoes could be carried by general cargo tramps with the advantage of their being able to take return cargoes. A series of turret-deck steamers were built for ore carrying purposes between 1904 and 1910 and a section through such a vessel is illustrated in Figure 3.4(a). Since 1945 a substantial number of ocean-going ore carriers have been built of uniform design. This form of ore carrier with a double bottom and side ballast tanks first appeared in 1917, only at that time the side tanks did not extend to the full hold depth. To overcome the disadvantage that the ore carrier was only usefully employed on one leg of the voyage the oil/ore carrier also evolved at that time. The latter ship type carries oil in the wing tanks as shown in Figure 3.4(c), and has a passageway for crew protection in order to obtain the deeper draft permitted tankers. The common general bulk carrier takes the form shown in Figure 3.4(d) with double bottom, hopper sides and deck wing tanks (see also Figure 17.7). These latter tanks have been used for the carriage of light grain cargoes as well as water ballast. Specific variations of this type have been built, Figure 3.4(e) shows a ‘universal bulk carrier’ patented by the McGregor Inter-national Organization that offers a very flexible range of cargo stowage solutions. Another type shown in Figure 3.4(f) has alternate holds of short length. On single voyages the vessel may carry high density bulk cargoes only in the short holds to give an acceptable cargo distribution. Such stow-age is not uncommon on general bulk carriers with uniform hold lengths where alternate hold loading or block hold loading may be utilized to stow high density cargoes. With such loading arrangements high shear forces occur at the ends of the holds requiring additional strengthening of the side shell in way of the bulkheads. Page | 27 GRSE LTD. STUDY MATERIAL FOR GAAT - 2024 A general arrangement of a typical bulk carrier shows a clear deck with machinery aft. Large hatches with steel covers are designed to facilitate rapid loading and discharge of the cargo. Since the bulk carrier makes many voyages in ballast a large ballast capacity is provided to give adequate immersion of the propeller. The size of this type of ship has also steadily increased and bulk carriers have reached 250 000 tonnes deadweight. Ships of the general bulk carrier form have experienced a relatively high casualty rate during the late 1980s and early 1990s giving rise to concern as to their design and construction. Throughout the 1990s bulk carrier safety has received considerable attention in the work of IMO, the classification societies and elsewhere, and this work is ongoing. Based on experience of failures with lesser consequences it was concluded that the casualties occurred through local structural failure leading to loss of watertight integrity of the side shell followed by progressive flooding through damaged bulkheads. The flooding resulting either in excessive hull bending stresses or excessive trim, and loss of the ship. Much of this work has concentrated on the structural hull details, stresses experienced as the result of loading and discharging cargoes, damage to structure and protective coatings arising from discharging cargoes, poor maintenance and subsequent inadequate inspection of the ship structure. The outcome of this work has been the introduction of a new Chapter XII of SOLAS covering bulk carrier ship safety and enhanced survey procedures for bulk carriers. Also, following evidence from the discovery of the wreck of the bulk carrier Derbyshire, work at IMO directed at revision of the Load Line Convention 1969 is look-ing closely at adequacy of bow height and strength of hatch covers in the forward part of these ships. The safe operation of bulk carriers is dependent on not exceeding allowable stresses in the cycle of loading, discharging, ballasting and de-ballasting. The size of bulk carriers may often be referred by one of the following classes: ‘Handy size’ the smallest bulk carriers of between 10 000 and 30 000 tonnes deadweight. ‘Handy max’ bulk carriers of between 35 000 and 50 000 tonnes deadweight. ‘Pana max’ bulk carriers designed to be of the maximum size that may transit the Panama Canal and generally being just under 80 000 tonnes deadweight. ‘Capesize’ bulk carriers of 80 000 to 150 000 tonnes deadweight which are too large for the Panama Canal and trade from the Atlantic around the Cape of Good Hope. Oil Tankers Until 1990 the form of vessels specifically designed for the carriage of oil car-goes had not undergone a great deal of change since 1880 when the vessel illustrated in Figure 3.5(a) was constructed. The expansion tank and double bottom within the cargo space having been eliminated. The greatest changes in that period were the growth in ship size and nature of the structure (see Figure 3.5(b)). The growth in size of ocean-going vessels from 1880 to the end of the Second World War was gradual, the average deadweight rising from 1500 tons to about 12 000 tons. Since then the average deadweight increased rapidly to about 20 000 tons in 1953 and about 30 000 tons in 1959. Today there are afloat tankers ranging from 100 000 tons deadweight to 500 000 tons deadweight. It should be made clear that the larger size of vessel is the crude oil carrier, and fuel oil carriers tend to remain within the smaller deadweights. Page | 28 GRSE LTD. STUDY MATERIAL FOR GAAT - 2024 Service speeds of oil tankers have shown an increase since the war, going from 12 knots to 17 knots. The service speed is related to the optimum economic operation of the tanker. Also the optimum size of the tanker is very much related to current market economics. The tanker fleet growth increased enormously to meet the expanding demand for oil until 1973/ 1974 when the OPEC price increases slowed that expansion and led to a slump in the tanker market. As a result it is unlikely that such a significant rise in tanker size and rise in speed will be experienced in the foreseeable future. Structurally one of the greatest developments has been in the use of welding, oil tankers being amongst the first vessels to utilize the application of welding. Little difficulty is experienced in making and maintaining oil-tight joints: the same cannot be said of riveting. Welding has also allowed cheaper fabrication methods to be adopted. Longitudinal framing was adopted at an early date for the larger ships and revision of the construction rules in the late 1960s allowed the length of tank spaces to be increased, with a subsequent reduction in steel weight, and making it easier to pump discharge cargoes. As far as the general arrangement is concerned there appears always to have been a trend towards placing the machinery aft. Moving all the accommodation and bridge aft was a later feature and is desirable from the fire protection point of view. Location of the accommodation in one area is more economic from a building point of view, since all services are only to be provided at a single location. The requirements of the International Convention for the Prevention of Pollution from Ships 1973 (see Chapter 29) and particularly its Protocol of 1978 have greatly influenced the arrangement of the cargo spaces of oil tankers. A major feature of the MARPOL Convention and its Protocol has been the provision in larger tankers of clean water ballast capacity. Whilst primarily intended to reduce the pollution risk, the fitting of segregated water ballast tanks in the midship region aids the reduction of the still water bending moment when the tanker is fully loaded. It also reduces corrosion problems associated with tank spaces which are subject to alternate oil and sea water ballast cargoes. In March 1989 the tanker Exxon Valdez, which complied fully with the then current MARPOL requirements, ran aground and discharged 11 mil-lion gallons of crude oil into the pristine waters of Prince William Sound in Alaska. The subsequent public outcry led to the United States Congress passing the Oil Pollution Act 1990 (OPA 90). This unilateral action by the United States Government made it a requirement that existing single hull oil tankers operating in United States waters were to be phased out by an early date, after which all oil tankers were to have a double hull (see Figures 3.5 and 22.7). In November 1990 the USA suggested that the MARPOL Convention should be amended to make double hulls compulsory for new tankers. A number of other IMO member states suggested that alternative designs offering equivalent protection against accidental oil spills should be accepted. In particular Japan proposed an alternative, the mid-deck tanker. This design has side ballast tanks providing protection against collision but no double bottom. The cargo tank space (see Figure 3.5) has a structural deck running its full length at about 0.25 to 0.5 the depth from the bottom which ensures that should the bottom be ruptured the upward pressure exerted by the sea prevents most of the oil from escaping into the sea. Page | 29 GRSE LTD. STUDY MATERIAL FOR GAAT - 2024 In 1992 IMO adopted amendments to MARPOL which required tankers of 5000 tons deadweight and above contracted for after July 1993, or which commenced construction after January 1994, to be of double-hulled or mid-deck construction, or of other design offering equivalent protection against oil pollution. Studies by IMO and the US National Academy of Sciences confirm the effectiveness of the double hull in preventing oil spills caused by grounding and collision where the inner hull is not breached. The mid-deck tanker has been shown to have more favourable outflow performance in extreme accidents where the inner hull is breached. The United States authorities consider grounding the most prevalent type of accident in their waters and believe only the double hull type prevents spills from tanker groundings in all but the most severe incidents. Thus, whilst MARPOL provides for the acceptance of alternative tanker designs, the United States legislation does not, and at the time of writing none of the alternative designs had been built. Present MARPOL requirements are that existing single hull crude oil tankers of 20 000 tons or more deadweight and existing single hull products carriers of 30 000 tons or more deadweight that: do not have segregated ballast tanks with protective location will not be able to operate after June 2007; and do have segregated ballast tanks with protective location will not be able to operate after July 2021. As the result of the breakup of the tanker Erika and subsequent pollution of the French coastline in 1999 proposed amendments to MARPOL were before IMO at the time of writing aimed at having the above phase out dates brought forward. The proposed amendments would see older tankers phased out at earlier dates with all single hull tankers of 5000 tons dead-weight or more being phased out by 1 January 2017. Oil tankers now generally have a single pump space aft, adjacent to the machinery, and specified slop tanks into which tank washings and oily residues are pumped. Tank cleaning may be accomplished by water driven rotating machines on the smaller tankers but for new crude oil tankers of 20 000 tons deadweight and above the tank cleaning system shall use crude oil washing. Passenger Ships Early passenger ships did not have the tiers of superstructures associated with modern vessels, and they also had a narrower beam in relation to the length. The reason for the absence of superstructure decks was the Merchant Shipping Act 1894 which limited the number of passengers carried on the upper deck. An amendment to this Act in 1906 removed this restriction and vessels were then built with several tiers of superstructures. This produced problems of strength and stability, stability being improved by an increase in beam. The transmission of stresses to the superstructure from the main hull girder created much difference of opinion as to the means of overcoming the problem. Both light structures of a discontinuous nature, i.e. fitted with expansion joints, and superstructures with heavier scantlings able to contribute to the strength of the main hull girder were introduced. Present practice, where the length of the superstructure is appreciable and has its sides at the ship Page | 30 GRSE LTD. STUDY MATERIAL FOR GAAT - 2024 side, does not require the fitting of expansion joints. Where aluminum alloy superstructures are fitted in modern ships it is possible to accept greater deformation than would be possible with steel and no similar problem exists. The introduction of aluminum alloy superstructures has provided increased passenger accommodation on the same draft, and/or a lowering of the lightweight center of gravity with improved stability. This is brought about by the lighter weight of the aluminum structure. A feature of the general arrangement is the reduction in size of the machinery space in this time. It is easy to see the reason for this if the Aquitania, built in 1914 and having direct drive turbines with twenty-one double-ended scotch boilers, is compared with the Queen Elizabeth 2. The latter as originally built had geared drive turbines with three water tube boilers. Several modern passenger ships have had their machinery placed aft; this gives over the best part of the vessel amidships entirely to passenger accommodation. Against this advantage, however, allowance must be made for an increased bending moment if a suitable trim is to be obtained. Passenger accommodation standards have increased substantially, the volume of space allotted per passenger rising steadily. Tween deck clearances are greater and public rooms extend through two or more decks, whilst enclosed promenade and atrium spaces are now common in cruise vessels. The provision of air conditioning and stabilizing devices have also added to passenger comfort. Particular attention has been paid to fire safety in the modern passenger ship, structural materials of low fire risk being utilized in association with automatic extinguishing and detection systems. There has been a demise of the larger passenger liner and larger passenger ships are now either cruise ships, short-haul ferries or special trade passenger (STP) ships. The latter are un-berthed immigrant or pilgrim passenger ships operating in the Middle East to South East Asian region. The development of high speed passenger ferries of lightweight construction and often of radical hull form and/or non-displacement modes of operation has been notable since the early 1980s. Initially relatively small, these craft may now be more than 100 meters in length and carry upwards of 500 persons plus 100 cars/30 trucks or more. The lightweight construction is usually of Aluminium alloy but some have been constructed of lighter higher tensile steels and fibre reinforced plastics may be used in the super-structure and accommodation areas. With speeds of up to 50 knots many craft are of twin-hull form and include conventional catamarans, wave-piercers with twin hulls and a faired buoyant bridging structure forward, also small water plane twin hulled (SWATH) ships. The latter have a high proportion of their twin-hull buoyancy below the waterline and very narrow twinhull beam at the waterline (see Figure 3.5). Other high speed craft include hydrofoils, and various surface effect ships (SESs) including hover-craft which maintain a cushion of air, fully or partially, between the hull and the water to reduce (drag). The increasing use of these vessels led in 1994 to the promulgation by IMO of specific international regulations concerning their design, safety and operation. An updated version of this Code of Safety was due to be adopted in December 2000. Figure 3.6 illustrates the various types of high speed craft. Also, see Figure 17.10 which shows the midship section of a high speed wave piercing catamaran. Page | 31 GRSE LTD. STUDY MATERIAL FOR GAAT - 2024 20. Ship Construction ER (b) 49 000 TONNE CONTAINER SHIP (a) ROLL ON - ROLL OFF SHIPS No.8 No.7 No.6 No.5 No.4 No.3 No. 2 No. 1 Upper deck ER Lift Main deck Ramps Tween ER Hold FIGURE 3.3 Angled stern ramp Vessel has adjustable internal ramp giving access to decks Page | 32 GRSE LTD. STUDY MATERIAL FOR GAAT - 2024 Weather deck Development of Ship Types 21 Stern Main deck door Hold 4. TURRET TYPE ORE CARRIER 1910 Water ballastOre Double bottom (b) ORE CARRI ER (c) ORE/OIL CARRIER Passageway Passageway Page | 33 GRSE LTD. STUDY MATERIAL FOR GAAT - 2024 (d) GENERAL BULK CARRIER Ore Oil Ore Double bottom Water ballast Water ballast or grain Page | 34 GRSE LTD. STUDY MATERIAL FOR GAAT - 2024 Cargo Double bottom (e) UNIVERSAL BULK CARRIER (shown carrying ore) 5 432 1 Machinery 6 5 3 2 1 (f) GENERAL CARGO SHIP WITH SHORT HOLDS FOR ORE Machinery 1 9 Ore 7Ore3 Ore FIGURE 3.4 Bulk carriers Page | 35 GRSE LTD. STUDY MATERIAL FOR GAAT - 2024 Development of Ship Types 23 (a) DOUBLE-HULL TANKER Deadweight 1680 Length 77.6m tonnes Beam 10.4m Wing Wing Depth 5.8m Speed 10 k Centre Expansion trunk tank tank Wing tank Centre tank Wing tank tank S B SBT T SBT SBT SBT Double bottom Page | 36 GRSE LTD. STUDY MATERIAL FOR GAAT - 2024 Length Deadweight 332 000 B.P. 330m tonnes (b) Beam 53.3m Depth 32m Speed 14½ k MID-DECK TANKER PRINCIPLE Wing Wing Centre tank tank tank Mid-deck Oil Oil FIGURE - 3.5 Oil tankers Page | 37 GRSE LTD. STUDY MATERIAL FOR GAAT - 2024 Development of Ship Types 25 Ship Construction 26 Bridge Accommodation GRSE LTD. STUDY MATERIAL FOR GAAT - 2024 Vehicle deck Machinery WAVE PIERCING CATAMARAN HYDROFOIL MULTI-HULL CATAMARAN SWATH CONCEPT ************* GRSE LTD. STUDY MATERIAL FOR GAAT - 2024 GRSE’s New Generation Electric ferry and Autonomous Vessels Dheu--New Generation Electric Ferry (Yard no. 2120) GRSE’s New Generation Electric ferry is a significant step towards reducing the Carbon emission in the water transport sector in West Bengal. The cutting-edge electric ferry is set to revolutionize public transportation in West Bengal. The ferry’s reduced energy consumption and environmentally friendly operation align with global trends towards sustainable development in the maritime sector. The vessel is Battery operated and it has a catamaran type hull structure. The vessel is suitable to carry 150 passengers with Ergonomically designed passenger area on Main deck. The vessel is fit to ply in shallow draft in the inland water ways of West Bengal. The vessel features low wake and good seakeeping characteristics Sl no. Description Specification 1. Endurance 4 hours at cruising speed 2. Length 24 m 3. Breadth 8.1 m (max depth of demi hull: 2.1m) 4. Draft 1m 5. Displacement 60 T 6. Speed 8 knots 7. No. of 150 passengers 8. Propulsion Electric (Battery) 9. Construction Hull: Aluminium, Superstructure: FRP Jaldoot (Yard no. 1324) USV (Unmanned Surface Vessel) for NSTL, DRDO Jaldoot USV is a man-portable autonomous surface vessel which is designed for communication between underwater vehicles and the mother ship/shore. With its compact size and lightweight composite construction, this USV is easy to deploy and operate in confined aquatic environments. It can also serve multiple roles, including acting as a communication and positioning aid for Unmanned Underwater Vehicles (UUVs), performing surveys, monitoring water quality, and conducting inspections in rivers, dams, harbors and lakes. This USV offers a flexible and reliable platform for entry into unmanned operations. Sl no. Description Specification 1. Endurance 3 hours at 3knots 2. Dimensions 1.6m x 0.85m 3. Displacement 55Kg max 4. Construction Composite + Anodized Aluminum 5. Navigation RTK GNSS (with NavIC) + IMU 6. Connectivity IP Radio / Cellular 7. Perception 360° day night cameras 8. Autonomy Waypoint Navigation, Station Keeping, Failsafe Behaviors with goal based planning 9. Payloads USBL Acoustic Modem, Altimeter, Camera GRSE LTD. STUDY MATERIAL FOR GAAT - 2024 Swadheen USV (Unmanned Surface Vessel) Swadheen is a cutting-edge autonomous surface vessel engineered for force multiplication through fleet and swarm deployments from mother vessels or shore. Designed for efficient maritime operations, it offers fully autonomous capabilities ideal for commercial surveying, defence, coastal, and mid-ocean applications. With rapid deployment, extended endurance, and unparalleled adaptability, Swadheen redefines the boundaries of unmanned surface operations. Sl no. Description Specification 1. Endurance 12 hours at 4knots