Fuel Injection Systems for CI Engines PDF
Document Details
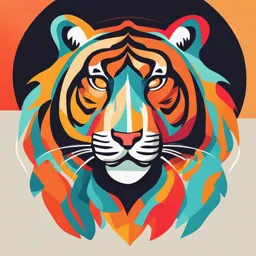
Uploaded by HumourousGreekArt
Politecnico di Torino
Tags
Summary
This document provides an overview of fuel injection systems for compression-ignition (CI) engines. It covers different architectures, the historical trend of pressure, component parts, and performance aspects. The technical information is aimed at a level suitable for engineering students or professionals.
Full Transcript
Fuel injection systems for CI engines and engine performance 12.1 Introduction Fuel injection systems have several purposes The first and most important is to deliver fuel to the cylinders at the proper time. This is because, if we have a short enough injection delay, we can closely relate SOI...
Fuel injection systems for CI engines and engine performance 12.1 Introduction Fuel injection systems have several purposes The first and most important is to deliver fuel to the cylinders at the proper time. This is because, if we have a short enough injection delay, we can closely relate SOI and SOC which makes the control of the engine much easier. Another important function of the injection system is to properly meter the fuel, which means to inject the right amount of fuel depending on the load. We also need to guarantee a proper atomization of the fuel, which can only be achieved through very high pressures (up to 3000 bar) and with small holes at the injector end. The diameter of the droplets is inversely proportional to the speed of the liquid during injection. The last two main functions are to ensure proper mixing with air and to ensure that we are utilizing as much air as possible for the combustion (ideally, all of it). A good injector ensures that the chamber has a large number of localized zones with lean combustible levels. 12.1.1 Diesel fuel injection system architectures The two main components of an injection system are the nozzle and the injector. While the nozzle is the part that does most of the work, the injector could also be very important in fuel metering, especially if we are using the most modern technology. In older engines, the injector was just a nozzle-holder. The three main architectures in fuel injection are: 1. Pump-line-nozzle: the oldest system, which had a pump for each cylinder. The pumps fed one injector. The solution was fairly expen- sive, so the system was converted to a single pump system. In both cases, the pump provides the metering; 2. Unit injector: in this system, the injector and pump are incorporated in a single element, with the benefit of removing the high pressure line, which reduces the risk of unwanted injections. The pump provides the metering; 156 3. Common rail: this system has a single high pressure pump, feeding an high pressure accumulator, called rail. The pump produces the high pressure, while the injector provides the metering. 12.1.2 Historical trend of pressure The pressure achieved in injection systems has historically being increasing. We started from around 10 bar with the first Diesel engines, but nowadays we can go above 2000 bar. 12.2 Components in fuel injection systems Injection systems are made out of several components, some of which work at high pressure (all of the ones that provide high pressure or have high pressure fluid going through them) and low pressure components (they deliver the fuel from the tank to the high pressure components). 12.2.1 Low pressure components There are several low pressure components which all work in order to bring the fuel from the tank to the high pressure pump or work to take the unused high pressure fuel back to the tank. The first of these components is obvi- ously, the fuel tank. It is the reservoir in which the fuel is stored and its main function is to keep the temperature of the fuel at a level below the flash point. Then we have the fuel supply pump which is responsible for draw- ing fuel from the tank and delivering it to the high pressure pump. Since it is a low-power pump, it is usually electric and it is powered by the car’s battery. We usually deliver more fuel than it is actually needed, in order to use it as lubricant and coolant for the injectors and pumps. This means that we have some high pressure excess fluid for each injection. this fuel must be returned to the fuel tank. Since the pressure of the fuel is pretty high, its temperature will be significantly higher than the tanks’. This is why we need a cooler in order to reduce the temperature of that fuel before it reaches the tank. This cooler runs on a separate circuit. Other components include fuel filters and heaters, which prevent or minimize the presence of contaminants in the fuel. 12.2.2 High pressure components High pressure components have the role of generating the high pressure in the fuel and of delivering that fuel to the combustion chamber. The first element is the high pressure pump, which is a piston or rotary pump, powered directly by the engine, by means of a connection (belt, chain,...) 157 with the crankshaft or camshaft. The pump can have a design that can di- rectly meter the fuel (in common rail systems this duty is left to the injector). In common rail systems, we have a rough metering done by the pump (in order to conserve energy) by pressurizing roughly the amount of fuel needed by the engine. The final, precise metering is left to the injector. Another component is the accumulator, which basically holds a certain amount of pressurized fuel before it goes to the injectors. This basically dampens pressure fluctuations inside of the system. It is mostly used in common rail systems (it is the rail). In systems in which the generation of high pressure is coordinated with the injection, we do not have an accumulator. Fuel injector and fuel injection nozzle The fuel injector is mounted on the cylinder head and contains the nozzle. It changes from system to system. For example in pump-line-nozzle sys- tems, the injector is just a nozzle holder, while in common rail systems it provides fuel metering functionality. In unit injectors, it provides most of the functionalities of the high pressure systems. The nozzle, instead, is the one that has the last word on the fuel that goes into the chamber. We have two types of nozzles: throttling pintle and hole-type nozzles. In the pintle nozzle, we have a needle (pintle) which ex- tends into the injection orifice of the nozzle. The pintle can move, opening and closing the nozzle. Hole-type nozzles, have several holes which are place at a certain angle in order to shoot the jet of fuel in a certain way in the chamber. 12.3 Pump-line-nozzle systems This injection system is the oldest of the ones that we will consider. It has one or more pumps, depending on the configuration, which create the high pressure in the fuel and an injection line for each cylinder, which takes the fuel from the pump to the injector. We can have two types of PLN systems: one with a pump per cylinder (in-line pump) and one with a single rotary pump (distributor). When there are multiple pumps, they are gear driven by the engine crankshaft and they are located in a central position, in order to have injection lines of equal length. Also, we would like to keep the lines as short as possible, since pulsating pressure waves going through narrow pipes are never particularly good for a proper control. The high pressure pump produces both the desired injection pressure and the desired metering. It does that by using a plunger/barrel system. The fuel coming from the low pressure pump flows to the barrel through a fuel gallery along the length of the high pressure pump and it is inserted in the barrel by means of one or two intake ports, also known as spill ports. The plunger has a vertical motion by means of the pump camshaft through the cam profile, with the 158 Figure 12.1: PLN system with multiple pumps return vertical motion given by the return spring. Fuel from the gallery enters into the cavity on top of the plunger through the two spill ports. Considering fig. 12.2, we can see that the upward motion of the plunger resulting from the camshaft (15) rotation, cam profile, and the cam follower continues to push the fuel atop the plunger upward to- wards a delivery valve. As the plunger continues its upward move- ment, it eventually blocks both fill ports and thus traps the fuel and forces it to unseat the delivery valve (6), flow into the high pressure pipe, and proceed on to the injector. It is important to notice that the cre- ation of high injection pressure oc- curs via the pressure pulse or wave that is formed when the plunger exerts its force onto the column of fuel accumulated on top of the plunger. The intensity of this pres- sure wave depends on the high pres- sure pump cam profile which con- trols the plunger linear speed. It also depends on the amount of fuel accumulated on top of the plunger, Figure 12.2: Plunger/barrel which is controlled by the volume of 159 the cavity receiving fuel from the fuel gallery. Each plunger is machined with a slot and a helix near its top. Further upward movement of the plunger causes a direct fluid communication between the high pressure fuel and the low pressure supply side through the slot, the bottom of the helix, and via the fill port that switches its role and becomes a spill port. This action di↵uses the high pressure and helps end the injection. The plungers move in a vertical direction, but they also rotate around their vertical axis to change their e↵ective stroke length, which provides the metering function. They achieve this rotating motion by means of a control rod (control rack) attached to the accelerator pedal via a series of linkages. Thus, when the driver demands more power, the control rack linear movement is transmit- ted to the plunger in the form of a circumferential movement that changes the relative position of the plunger helix to the pump spill port. 12.3.1 Delivery valves The job of the delivery valve is to interrupt the high pressure circuit between the high-pressure fuel injection lines and the pump plunger, as well as to relieve the high-pressure lines and the nozzle space by reducing pressure to a given static level. This reduction in pressure causes the nozzle to close rapidly and precisely, as well as preventing undesirable fuel dribble (that can provide secondary injections). During the actual injection process, the pressure which is generated in the nozzle high-pressure chamber causes the delivery valve cone to lift from its seat in the valve holder, and the pressurized fuel is forced through the In-Line Pump System Control delivery- valve holder, and the high-pressure lines to the injection nozzle. As soon as the plunger helix terminates the fuel delivery, pressure drops in the nozzle high-pressure chamber, and the delivery-valve spring forces the valve cone back onto its seat. This separates the chamber above the pump plunger from the high pressure circuit until the next e↵ective (working) stroke of the plunger. 12.3.2 Timing device During the injection process, the needle is opened by a pressure wave started by the plunger in the pumping element and propagated through the high pressure line at the speed of sound. The injection event in each combustion cycle occurs at the same crank angle position relative to TDC. Yet, as engine speed increases, injection lag between start of delivery and start of injection increases (occupies a greater number of crank angle degrees). Since the most favorable combustion occurs at a fixed position of the piston relative to its TDC position, a timing device can be used to reposition the injection pump camshaft relative to the plunger follower. This new camshaft position is such that the fuel pressure wave is advanced by a proportional amount 160 Figure 12.3: Axial distributor to ensure that the injection takes place at the same crank angle relative to TDC. Before the introduction of electronic controls, injection timing was commonly controlled with a mechanical coupling mounted directly on the injection pump camshaft. Inside the coupling were flyweights that moved further outward as engine speed increased. The motion of these flyweights was used to change the phasing of the pump camshaft relative to engine camshaft and crankshaft to provide injection timing variations with engine speed. These timing devices are sealed and oil filled either via their own oil supply or via the engine lubricating oil circuit. 12.3.3 Nozzle and injector Like we said before, the injector is nothing more than a nozzle holder. The nozzle can be of either types and it consists of a pin which is pushed away by the pressure of the fuel, opening the nozzle. When the pressure subsides, a spring closed the nozzle by pushing the pin back into position. 12.3.4 Distributor pump system The distributor is the pump that feeds high pressure fuel to all cylinders’ injectors in the PLN configuration with one pump. It can be either radial or axial. In case of an axial pump (fig. 12.3), we have a rotating cam plate (3) which is driven by the engine. The number of cam lobes on the bottom of the cam plate is equal to the number of engine cylinders. They travel over rollers (2) on the roller ring and thus cause the distributor piston to describe a rotating as well as a lifting (axial) motion. In the course of each rotation of the drive shaft, the piston completes a number of strokes equal to the number of engine cylinders to be supplied. In a port-controlled axial-piston distributor pump with mechanical governor or electronically controlled actuator mechanism, a control collar (5) determines the e↵ective 161 stroke, thereby controlling the injected-fuel quantity. The timing device can vary the start of delivery of the pump by turning the roller ring. The fuel delivery from an axial piston distributor pump system is a dynamic process comprising several stroke phases. The pressure required for the actual fuel injection is generated by the high pressure pump. The distributor plunger’s stroke and delivery phases show the metering of fuel to an engine cylinder. Axial-piston distributor pump system For a 4-cylinder engine the distributor plunger rotates through 90° for a stroke from BDC to TDC and back again. As the distributor plunger moves from TDC to BDC, fuel flows through the open inlet passage and into the high-pressure chamber above the plunger. At BDC, the plunger’s rotating movement then closes the inlet passage and opens the distributor slot for a given outlet port. The plunger now reverses its direction of movement and moves upwards, the working stroke begins. The pressure that builds up in the high-pressure chamber above the plunger and in the outlet-port passage suffices to open the delivery valve in question and the fuel is forced through the high-pressure line to the injector nozzle. The working stroke is completed as soon as the plunger’s transverse cuto↵ bore reaches the control edge of the control collar and pressure collapses. From this point on, no more fuel is delivered to the injector and the delivery valve closes the high-pressure line. Radial distributor Referring to fig. 12.4, high pressure is generated by a radial-piston pump with cam ring (3), and from two to four radial pistons (4). Radial-piston pumps can generate higher injection pressures than axial-piston pumps. However, they have to be capable of withstanding greater mechanical stresses. The cam ring can be rotated by the timing device (1), and this shifts the start of delivery. With radial-piston distributor pumps, the start of injec- tion and injection duration are always controlled by solenoid valve (5) that meters the injected-fuel quantity and varies the start of injection. When the solenoid valve is closed, pressure can build up in the high-pressure chamber (6). When it is open, the fuel escapes so that no pressure buildup occurs and therefore fuel injection is not possible. One or two electronic control units (pump control unit and engine control unit) generate the control and regulation signals. 12.4 Unit injector system The unit injection system comes in two types: unit injector and unit pump systems. These systems can achieve the highest possible (for now) pressures and they are electronically controlled by a solenoid valve. They are capable of high-precision fuel injection that is infinitely variable in response to the engine operating state. Diesel engines equipped with these systems produce 162 Figure 12.4: Radial distributor low emission levels, are economical and quiet to run, and o↵er high perfor- mance and torque characteristics. The essential di↵erence between the unit injector system and the unit pump system lies in the engine layout. In the unit injector system, the high-pressure pump and the nozzle form a single unit: the “unit injector”. There is a unit injector fitted in each cylinder of the engine. As there are no high-pressure fuel lines, extremely high injection pressures can be generated and precisely controlled injection patterns can be produced. With the unit pump system, the high-pressure pump – the “unit pump” – and the nozzle-holder assembly are separate units that are connected by a short length of high-pressure line. This arrangement has advantages in terms of use of space, pump-drive system, and servicing and maintenance. Each cylinder has its own unit injector (UI), which is installed directly in the cylinder head. The engine camshaft has an actuating cam for each unit injector, the particular cam lift being transferred to the pump plunger by a rocker arm. The injection curve is influenced by the shape of the actuating cams. These are shaped so that the pump plunger moves more slowly when fuel is taken in (upward movement) than during injection (downward movement) in order, on the one hand, to prevent air from being accidentally drawn in and, on the other hand, to achieve a high delivery rate. 12.5 Common rail system Common rail systems are one of the most advanced injection systems that we have. The main advantage of the common-rail system is its ability to vary injection pressure and timing over a broad scale. This was achieved by separating pressure generation (in the high-pressure pump) from the fuel- injection system (injectors). The rail here acts as a pressure accumulator. Through this system, we can achieve very high pressures, with the pressure being adjustable depending on the load. We can also have a variable injec- 163 (a) Unit injector (b) Unit pump Figure 12.5: Unit injection systems tion start with the possibility of having multiple injection shots. We have three main systems in the common rail: the low pressure system, the high pressure system and the control system. The key components of the common-rail system are the injectors. They are fitted with a rapid-action valve (solenoid valve or piezo-triggered actuator) which opens and closes the nozzle. This permits control of the injection process for each cylinder. All the injectors are fed by a common fuel rail, this being the origin of the term “common rail”. One of the main features of the common-rail system is that system pressure is variable dependent on the engine operating point. Pressure is adjusted by the pressure-control valve or the metering unit. The modular design of the common-rail system simplifies modification of the system to di↵erent engines. The functions of pressure generation and metering are now split by the rail. The fuel is supplied by the pump to the accumulator (rail) and then it reaches the injectors. Owing to the almost uniform injection pattern, the high-pressure pump design can be much smaller and its drive-system torque can be lower than conventional fuel-injection systems. This results in a much lower load on the pump drive. The high-pressure pump is generally a radial-piston pump. 164 12.5.1 Fuel injection The injectors spray fuel directly into the engine combustion chambers. They are supplied by short high-pressure fuel lines connected to the fuel rail. The engine control unit (ECU) controls the switching valve integrated in the injector to open and close the injector nozzle. The injector opening times and system pressure determine the quantity of fuel delivered. At a con- stant pressure, the fuel quantity delivered is proportional to the switching time of the solenoid valve. This is, therefore, independent of engine or pump speed (time-based fuel injection). Separating the functions of pres- sure generation and fuel injection opens up further degrees of freedom in the combustion process compared with previously described fuel-injection systems. The common-rail system allows a further reduction in exhaust- gas emissions by introducing multiple injection events and also attenuating combustion noise significantly. Multiple injection events of up to eight per cycle can be generated by triggering the highly rapid-action switching valve several times. 12.5.2 Pressure control We have several ways of controlling the pressure in the system. Control on the high pressure side On first-generation passenger-car systems, the required rail pressure is con- trolled on the high-pressure side by a pressure-control valve. Fuel not re- quired for injection flows back to the low-pressure circuit via the pressure control valve. This type of control loop allows rail pressure to react rapidly to changes in operating point (e.g. in the event of load changes). Control on the high-pressure side was adopted on the first common-rail systems. The pressure-control valve is mounted preferably on the fuel rail (PSAV12 63 for picture). Fuel-delivery control on suction side Another way of controlling rail pressure, implemented in second generation CR systems, is to control fuel delivery on the suction side (Fig. 3b). The metering unit (10) flanged on the high-pressure pump makes sure that the pump delivers exactly the right quantity of fuel to the fuel rail in order to maintain the injection pressure required by the system. In a fault situation, the pressure-relief valve (9) prevents rail pressure from exceeding a maxi- mum. Fuel-delivery control on the suction side reduces the quantity of fuel under high pressure and lowers the power input of the pump. This has a positive impact on fuel consumption. At the same time, the temperature of the fuel flowing back to the fuel tank is reduced in contrast to the control 165 method on the high-pressure side (PSAV12 63 for picture, numbers refer to picture). Two actuator system The two-actuator system (Fig. 3c) combines pressure control on the suction side via the metering unit and control on the high-pressure side via the pressure-control valve, thus marrying the advantages of high-pressure side control and suction-side fuel-delivery control. If pressure is only adjustable on the low-pressure side, it takes too long to lower the pressure in the fuel rail when rapid negative load changes occur. Adapting pressure to dynamic changes in load conditions is then too slow. This is particularly the case with piezoelectric injectors due to their very low internal leakage. For this reason, some common-rail systems are equipped with an additional pressure-control valve (Fig. 3c) besides the high-pressure pump and metering unit. This two-actuator system combines the advantages of control on the low-pressure side with the dynamic response of control on the high-pressure side (PSAV12 63 for picture, numbers refer to picture). 12.5.3 High pressure pump The high-pressure pump is the interface between the low-pressure and high pressure stages. Its function is to make sure there is always sufficient fuel un- der pressure available in all engine operating conditions. At the same time it must operate for the entire service life of the vehicle. The pump must provide a fuel reserve that is required for quick engine starting and rapid pressure rise in the fuel rail (fig. 12.6). A 3- plunger radial-piston pump is used as the high-pressure pump to gen- erate pressure in passenger-car sys- tems. The pump is driven by the en- gine via coupling, gearwheel, chain, or toothed belt. Pump speed is therefore coupled to engine speed via a fixed gear ratio. The high- pressure radial-piston pumps used in passenger cars are lubricated and cooled by the fuel itself. The drive shaft in the housing of the pump Figure 12.6: High pressure pump is mounted in a central bearing (1). The pump elements (3) are ar- ranged radially with respect to the central bearing and o↵set by 120°. The eccenter (2) fitted to the drive shaft forces the pump plunger to move up and down. Force is transmitted between the eccentric shaft and the deliv- 166 ery plunger by means of a drive roller, a sliding ring mounted on the shaft eccenter, and a plunger base plate attached to the plunger base plate. The pre-supply pump (usually an electric fuel pump in the tank) delivers fuel via a filter and water separator to the inlet of the high-pressure pump (6). The drive shaft with its eccenter moves the pump plunger up and down to mimic the eccentric lift. Fuel passed through the high-pressure pump inlet valve (4) into the element chamber and the pump plunger moves downward (inlet stroke). When the bottom dead center of the pump plunger is exceeded, the inlet valve closes, and the fuel in the element chamber can no longer escape. It can then be pressurized beyond the delivery pressure of the pre-supply pump. The rising pressure opens the outlet valve (5) as soon as pressure reaches the level in the fuel rail. The pressurized fuel then passes to the high-pressure circuit. The pump plunger continues to deliver fuel until it reaches its top-dead center position (delivery stroke). The pressure then drops so that the outlet valve closes. The remaining fuel is depressurized and the pump plunger moves downward. When the pressure in the element chamber exceeds the pre-delivery pressure, the inlet valve reopens, and the process starts over. As the high-pressure pump is designed for high delivery quantities, there is a surplus of pressurized fuel when the engine is idling or running in part-load range. On first-generation systems, excess fuel deliv- ered is returned to the fuel tank by the pressure control valve on the fuel rail. As the compressed fuel expands, the energy imparted by compression is lost; overall efficiency drops. Compressing and then expanding the fuel also heats the fuel. An improvement in energetic efficiency is possible by controlling fuel delivery by the high-pressure pump on the fuel-delivery side (suction side). Fuel flowing into the pump element is metered by an infinitely vari- able solenoid valve that acts as a metering unit. This valve adapts the fuel quantity delivered to the rail to system demand. This fuel-delivery control not only drops the performance demand of the high-pressure pump, it also reduces the maximum fuel temperature. 12.5.4 Injectors The injectors are subject to a servo control. A servo control is a system in which a small input force is able to control a larger output force. What controls the injector is a solenoid/piezoelectric actuator, which drives the nozzle control valve. On a common-rail diesel injection system, the injectors are connected to the fuel rail by short high-pressure fuel lines. The injectors are sealed to the combustion chamber by a copper gasket called “washer”. Depending on the injection-nozzle design, common-rail injectors are intended for straight or inclined mounting in direct-injection diesel engines. The injection time is controlled by the angle/time system of the Electronic Control unit (ECU). This requires the use of sensors to detect the crankshaft position and the 167 Figure 12.7: Operation of a solenoid-controlled nozzle camshaft position (phase detection). An optimum mixture formation is required to reduce exhaust-gas emissions and comply with continuous de- mands to reduce the noise of diesel engines. This requires injectors with very small pilot-injection quantities and multiple injection events. Referring to fig. 12.7, fuel is conveyed by the high-pressure connection (13) via a supply passage to the injection nozzle and via an inlet restrictor (small orifice) (14) to the valve-control chamber (6). The valve-control chamber is connected to the fuel return (1) via the outlet restrictor (a larger orifice, 12) which can be opened by a solenoid valve. The nozzle changes state (closed start of open- ing, open, closed at end of injection) because of a change in the balance of the forces between the ones that push the pin down and the ones that push the pin up. The injector is initially closed since the solenoid-valve spring (11) presses the valve ball (5) onto the seat of the outer restrictor (12). This means that the chamber between the two restrictors is filled with fuel and exerts a pressure on the needle that is greater than the one that the fuel not going in the chamber is exerting. When the injection starts, the solenoid valve is activated with a current which is called pickup current. The valve opens and the fuel in the chamber flows in a lower pressure ambient. This means that the chamber between the two restrictors is no longer pressurized and cannot exert a pressure on the needle. The fuel in pressure is now free to lift the needle and flow outside. The rate of movement of the nozzle nee- dle is determined by the di↵erence in the flow rates through the inlet and outlet restrictors. The control plunger reaches its upper stop and dwells there on a cushion of fuel (hydraulic stop). The cushion is created by the flow of fuel between the inlet and outlet restrictors. The injector nozzle is then fully open. Fuel is injected into the combustion chamber at a pressure 168 approaching that in the fuel rail. The balance of forces in the injector is similar to that during the opening phase. At a given system pressure, the fuel quantity injected is proportional to the length of time that the solenoid valve is open. This is entirely independent of the engine or pump speed (time-based injection system). If we want to close the nozzle, we need to cut out the current and release the armature (which is the part governed by the solenoid). The pressure in the control chamber rises again and, with the help of a spring, brings the needle down, closing the nozzle. 12.5.5 Solenoid system The “control volume” required in addition to the injected fuel quantity reaches the fuel-return line via the restrictors in the control chamber. In addition to the control volume, there are also leakage volumes through the nozzle-needle and valve-plunger guides. The valve plunger/nozzle needle unit reaches the hydraulic stop if the triggering period in vehicle operation is of sufficient length. The section until the nozzle needle reaches its maxi- mum stroke is termed ballistic mode. The ballistic and non-ballistic sections in the fuel quantity map, where the injected fuel quantity is applied for the triggering period is separated by a kink in the program map. To have a proportional relationships between time and injected quantity, solenoid in- jection systems are generally ballistic. The needle displacement to reach the stop is of the order of 1 mm. Initially, in order to ensure tight tolerances and high levels of reproducibility for the injected fuel quantity, the current for opening the solenoid valve features a steep, precisely defined flank and increases rapidly up to approximately. 20 A. In order to reduce power loss in the ECU and injector, the current is dropped to approximately 13 A in the holding-current phase. Single injection: delays We can notice that in a single injection the pressure drops in the rail as the injector opens and it rises again as the injection ends. We have significant pressure oscillations in the injector and they are much higher with respect to the rail. Since the solenoid takes some time in order to open (and to receive current) the injection will be delayed. We call this time (1 ÷ 2) µs energising time. A larger delay is the one that the nozzle takes to open (up to 300 µs). This time is the nozzle opening delay (NOD). We also have a corresponding nozzle closing delay (NCD). The total injection time is computed as IT L = ET + N CD N OD 169 Multiple injections When we have multiple injections, like the pilot, main and end injections combination, we need to take the dwell time into account. This is the time between the end of the injection (pilot) and the beginning of the next one (main). We need, in fact, to have that the dwell time is large enough to avoid the superposition (fusion) of the two injections. This is especially true for older engines, since the fusion of the two injections causes low repeatability of the combustion. 12.5.6 Piezoelectric system Instead of the solenoid, we can use a piezoelectric material, stacked to form a piezoelectric stack. The stack can elongate when it receives a signal (elec- tric). In order to make it return to its original size, we need to use a signal in reverse direction (negative current). The displacement of the piezo-stack is very small, so an hydraulic cou- pler is used to amplify it (4). This system is still an indirect way to actuate the needle, since the piezo- stack only opens and closes the con- trol chamber. We can actually use a similar setup in order to have the piezo-stack open and close the nee- dle directly. Piezoelectric actua- tors can generate sufficient force in a compact form to move the noz- zle needle rapidly enough to provide an advantage over servo-controlled injectors. One important challenge with using piezoelectric actuators to directly actuate a fuel injec- tor nozzle needle is that displace- ments from piezoelectric stacks are very small and sensitive to actua- Figure 12.8: Piezoelectric injector tor length variations that are of the same order of magnitude as the achievable displacement. A common ap- proach to address the challenges of directly coupling a piezoelectric actu- ator to the nozzle needle is to use a link that amplifies the displacement of the actuator into a larger displacement that is more appropriate for the nozzle needle. The typical injection characteristic of the direct piezoelectric injector is boot-shaped in a mass flow rate-time graph. In general, the per- formance of the piezoelectric (both direct and indirect) is not that superior 170 Figure 12.9: Distribution of efficiency to the one of the solenoid injector to justify the cost of such equipment. 12.6 CI engine performance 12.6.1 Efficiency distributions with respect to air-fuel ratio We will for now consider naturally aspirated engines, with no EGR and with mechanical injection. We will consider constant speed and we will only vary ↵. The combustion is in general, dependent mainly from the distribution of the fuel in the chamber, by the pressure and by the temperature. Moreover, as the amount of fuel injected per cycle is increased, problems with air utilization during combustion lead to the formation of excessive amounts of soot which cannot be burned up prior to exhaust. This excessive soot or black smoke in the exhaust constrains the air/fuel ratio at maximum engine power to values 20 percent (or more) greater than stoichiometric. Referring to fig. 12.9, we can see that: the internal thermodynamic efficiency ⌘✓i takes the partial or incom- plete combustion into account when ↵ = (1 ÷ 1.2)↵st. For ↵ < ↵st , it is constant since the incompleteness of the combustion is considered in ⌘a f already. For ↵ > 1.2↵st , the internal thermodynamic efficiency is fairly constant, and diminishes for high values of ↵ because of the heat transfer to cylinder walls; the air-fuel cycle efficiency ⌘a f quickly decreases when there is not enough air (↵ < ↵st ); The fuel conversion efficiencies (both normal and indicated one) de- crease with increasing ↵, showing a maximum a bit after 1.2↵st ; 171 (a) Control characteristic (b) Mechanical characteristic Figure 12.10: Control and mechanical characteristics the imep has a peak for ↵ = 1.2↵st. 12.6.2 Control characteristic Now it is possible to relate the fuel conversion efficiency and the brake mean e↵ective pressure. The fuel conversion efficiency versus bmep for SI engines is included between the two half-lines corresponding to the extreme value of the air-fuel ratio of the combustibility field, that is relatively narrow, while for the CI engine, that operates always with a lean mixture, the maximum value of ↵ is relatively high. It is evident that there is a range in which the fuel conversion efficiency for the CI is relatively high: this part of the characteristic is used for the engine control. The maximum bmep supplied by the CI engine, at the limit of the smoke region, is lower than the maximum bmep of the SI engine (for old configurations in which not only SI but also CI was NA). However, the maximum value of the fuel conversion efficiency of the SI engine, that occurs for lean mixtures, is always lower than the maximum value of the fuel conversion efficiency of the CI engine. This di↵erence is higher for DI diesel engines, while for indirect injection diesel engines the di↵erence between the fuel conversion efficiencies is more contained. Control for CI engines is obtained through the variation of ↵, while for SI engines, the control is obtained through the variation of the volumetric efficiency. The fuel conversion efficiency at maximum power is greater for CI engines and, therefore, the fuel conversion efficiency for CI engines is always greater with respect to SI engines. We can also display the efficiency behaviour with respect to the speed. See PSAV12 113-119 for control of Euro 6 diesel engine (important!). 172