Flocculation PDF
Document Details
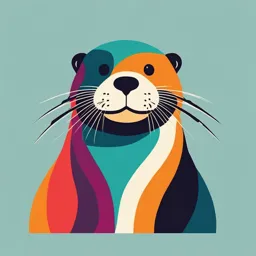
Uploaded by FertileDravite5145
Tags
Summary
This document provides details on flocculation, including definitions of colloids and flocs, and explanations of inhibitors in polymerization processes. It also covers types of polymerization and considerations for process control, like pH meters and catalysts.
Full Transcript
# Polymerization ## MBA - Methylene Bis-Acrylamide: Branching agent that thickens without changing UL. Only used with BPMoive products - Too much MBA: Lots of crosslinking - 3 steps of polymerization: Initiation, Propagation, Termination - 3,000 KG before shoot VAZO - 13,000 KG is a half charge....
# Polymerization ## MBA - Methylene Bis-Acrylamide: Branching agent that thickens without changing UL. Only used with BPMoive products - Too much MBA: Lots of crosslinking - 3 steps of polymerization: Initiation, Propagation, Termination - 3,000 KG before shoot VAZO - 13,000 KG is a half charge. - Spanntween 80, Vazo, and water makes SLURRY - Dissolution tank: Raw material order: - Water - Acrylamide - Urea - Acrylic acid - Caustic - Salt (If applicable) - 3 monomers: - Acrylamide - Acrylic acid - ATN - Flocculation - Colloid: Substance that is microscopically dispersed within another substance (for example, oil in water, milk fat in water) - Floc: Grouping of dispersed substances (polymers) to overcome molecular interactions and settle out (settle colloid out of solution) - Inhibitors: Copper, Iron, Oxygen, MEHQ - Poly ACM types and differences: - Anionic: Negative charge (Acrylamide, Sodium AMB) - Cationic: Positive charge (Cationic monomer, Acrylamide) - Nonionic: Neutral charge (Acrylamide) - Acrylamide-solid form is most hazardous: Carcinogen - Hazards/Exposure: Inhalation, skin, eyes, ingestion ## Inhibitors - Anything that interferes with free radical polymerization - Cooper: inhibits polymerization by reacting with any free radicals before free radicals can react with monomer molecules - Oxygen: inhibits polymerization by reacting with free radicals and forming a more stable free radical which is unable to initiate a polymerization reaction - MEHQ: prevents auto-initiation in D-tanks - inhibits cationic monomer + acrylic acid - transfers hydrogen atom to free radical and forms stabilized radical which is unable to act as an initiator - Versenex 80: also inhibits cationic monomer - Antifoam: removes foam from D-tank before it is transferred to the reactor - Adding too much antifoam will cause slow heat up in the reactor - Adding too little antifoam will allow foam to regenerate during transfer to reactor, causing catalyst to sit on top of reaction and won't allow proper mixing ## PH Meters - Inline pH meters are on recirculation lines and used to PH D-tanks - Caustic is used to raise pH. Acrylic Acid lowers pH. - If pH is above 12, D-tank should be split (get pH to 8). - pH probes are calibrated using buffer solutions with known pH value. - Acrylic Acid gives product its charge (negative charge) - Anionic has negative charge. - Too much acrylic acid: high anionicity - Too little acrylic acid: low anionicity - Acetic Acid pH control in post hydro (gives no charge) - Tank samples are removed once QC silo blend is confirmed. - Product is affected by polymerization issues and drying upsets. - Centrifugal Pumps are used to transport aqueous phased solution to reactors. - Centrifugal pumps are used to prevent equipment damage if high back pressure or clogging occurs - Centrifugal pumps can be head headed for short periods of time - Motor monitor is used to protect motor if dead headed or during pump cavitation - Low level probe on discharge side of pump for when no level is seen - -2°C in D-tank, 0°C in reactor - Finished product is bad for aquatic organisms - Sump or dike: pH level 6.0 to 9.0 - If D-tank exceeds 15°C it will alarm and prevent caustic addition. - If D-tank temp. exceeds 25°C then caustic addition will shut off. ## Tube Reactors - Electro-polished coating on interior reactor walls - Oil reactors before drawdown. - Oil prevents gel from sticking to internal reactor parts, preventing contamination. - Oil improves reactor draining speed as well as reduce equipment strain caused by friction. ### Catalysts - Thermocatalyst 1: Vazolet VA2064, Anti-foam (5E2220), Span 80/Tween 80. - Branching Agent: MBA - Chelating Agent: Versener/Trilon (3 minutes) - Chain Transfer Agent: Hypo (5 minutes) - Thermocatalyst 2: VA044 (5 minutes) - Oxidizer 1: TBHP (30 seconds) - Oxidizer 2: Sodium Persulfate (1 minute) - Initiator: Mohr's Salt (1 minute) - Versenex: Takes Copper/Iron out of Acrylamide. - Large amount of versened can be used as a catalyst. - Nitrogen purges displace oxygen, dissolve in polyacrylamide. ### Auto Initiation Happens if: - Hot gel left over from last reaction. - Solution is not at set point in D-tank during transfer to heater - Leftover catalyst in reactor during drawdown ## 3 Steps of Polymerization - Initiation: Free radicals attack C-C bond in monomer molecule, creating free radical on the end. Initiation occurs when Reducers from Redox package is added to monomer solution. - Propagation: Newly formed free radicals at the end of monomer attacks other C-C bonds on other monomers, creating chain of monomers (polymers). Chain will continue to lengthen until there are no more monomers available, or until chain transfer agent terminates the chain and starts a new chain. Thermal catalysts and chain transfer agent drive propagation step. - Termination: Absence of monomer - Disproportionation: When another free radical attacks the end of polymer chain, not allowing a new free radical to form. - Combination: Occurs when 2 chains with free radicals combine. ## Characteristics of Product - Charge and molecular weight determines product ## Vazo - Takes over reaction at 30℃ + 35℃ ## VA044 - Takes over reaction at 10℃ to 15℃ ## Rotary Valves - Create suction ## Oil - PK.455: mix in tanks (thinner) - 5275: mix in talks (thicker) - Spom 80/Tween 80: goes in VAZO pot (20ml to make slum) - PPG: only for Post hydro to GR1 - LPA: clear oil, mix in tanks (Consode 260) ## Vazo Pot order 1. Water 2. Antifoam 3. Oil 4. VAZO/AZEN (Powder) (pellets) ## Filter ratio - Too much oil in GR2 - High monomer: Too much unreacted acrylamide in finished product caused by leaking valves, bad sparges, bad catalyst, foam on top ### Louvers - Control air flows to burners ### Hypo - Affects UL - MBA doesn't affect UL but affects molecular weight ### Versened - Chelating agent ### Venturi Effect - Oxygen pushed through sparges (leaking sparges) ### Vazo - 30° to 35° ### VA044 - 10° to 15° ### LP1+2 Cyclones - Rotary valves ### LPB Cyclones - Fans - Dryer 1 ### S2 Cyclone - 1-Fan, Cyclone 2+3-share form, Cyclone 4+5-Rotary Valve ### S3 Cyclone - 1,2,3-Own Rotary valve + share Blower - 4 + 5 - Own Butterfly valve to pans ## LINE 8 - Dryer 1: Manually. - Dryer 2+3: Cascade - Sparges: 150-170 - D-tank: -20℃ to heater (55℃) ## LPB and LP4 Differences - LPB: Hot water jacket. (Batch rotates M1-M3). - LP4: Steam jacket, Cyclone above M1. - Add MEHQ after Acrylamide - Propagation: Building molecular weight - Oil: PK 455, 5875, Spor 80/Tween 80, PPG. ## Filter Ratio - Too much oil in GR. - High monomer: Too much unreacted acrylamide in finished product caused by leaking valves, bad sparges, bad catalyst, foam on top ### Louvers - Control airflow to burners ### Hypo - Affects UL, MBA doesn't affect UL but affects molecular weight. ### Versened - Chelating agent ### Venturi Effect - Oxygen pushed through sparges (Leaking sparges). ### Vazo - 30° to 35°. ### VA044 - 10° to 15°. ### LP1+2 Cyclones - Rotary Valves. ### LPB Cyclones - Fans - Dryer 1 ### S2 Cyclone - 1: Fan, Cyclone 2+3:share form, Cyclone 4+5: Rotary Valves ### S3 Cyclone - 1,2,3: own Rotary Valley + share Blower - 4+5: own Butterfly valve to pans.