flight controls 2.docx
Document Details
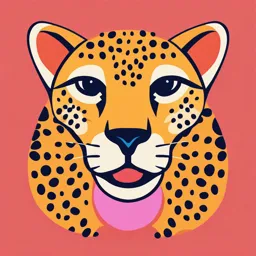
Uploaded by PhenomenalNumber
Full Transcript
standby configuration. One motor is capable of full performance of the HSTA. The HSTA has fully independent primary and secondary load paths. Under normal conditions, only the primary load path carries the HSTA operating and static loads, while the secondary load path remains unloaded. In case of a...
standby configuration. One motor is capable of full performance of the HSTA. The HSTA has fully independent primary and secondary load paths. Under normal conditions, only the primary load path carries the HSTA operating and static loads, while the secondary load path remains unloaded. In case of a structural failure in the primary load path, the secondary load path immediately engages to carry the static loads and the HSTA locks, holding the horizontal stabilizer in the last commanded position for the remainder of the flight. As the locked-up HSTA is commanded to move, the stabilizer system detects the HSTA's failure to move and annunciates the failure to the flight and maintenance crews. The HSTA irreversibility is provided by a mechanical no-back device mounted on the HSTA ballscrew and by electro-mechanical brakes on each motor-brake assembly. Either the no-back device or the motor brake is capable of providing HSTA irreversibility under application of the limit load. Controls and Indications: A full description of the Primary Flight Display appears in section 2B-05-00 and a description of the Flight Controls 2/3 synoptic page appears in section 2B-07-00. Circuit Breakers (CBs): The following CBs protect the horizontal stabilizer system: Circuit Breaker Name CB Panel Location Power Source STAB 1 DC LEER B-10 L ESS 28V DC STAB 2 DC REER A-7 R ESS 28V DC STAB CH 1 REER E-1 EMER 115V AC STAB CH 2 RPDB RMAC Right Main AC Crew Alerting System (CAS) Messages: The following CAS messages are associated with the horizontal stabilizer system: CAS Message Possible Cause(s) Stab Primary Trim Fail (caution) NOTE: This message may be accompanied by the FCC Alternate Mode (caution) CAS message. Loss of valid pitch trim communication from the FCCs to the HSCU. Stabilizer Channel Fail (caution) A horizontal stabilizer control channel has failed. Stabilizer Failed (caution) Horizontal stabilizer not responding to movement commands. OR Surface position information is unreliable or unavailable. Stab Maintenance Required (advisory) A failure within the horizontal stabilizer system has occurred that does not prohibit movement. Stab Rigging Complete (advisory) Rigging is valid for the current aircraft. Message occurs when in Maintenance Mode after Auto Rigging is satisfactorily completed. Limitations: There are no limitations established for horizontal stabilizer system at the time of this writing. Figure 20. Horizontal Stabilizer System Schematic TIL-000641 Figure 21. Horizontal Stabilizer Electro-Mechanical Components TIL-003040 2A-27-60: Wing Flaps System General Description: (See Figure 22. Wing Flaps System Schematic.) The Flap Actuation System (FAS) interfaces with the following aircraft systems: Aircraft Hydraulic System Aircraft Electrical DC Power System Flight Control Computer (FCC) Avionics, Crew Alerting System (CAS) Central Maintenance Computer (CMC) The FAS provides the actuation and control of a Fowler-type, single flap surface on the trailing edge of each wing. When extended, the flap surfaces provide an increase in the wing lift and drag for use primarily during takeoff, approach and landing. The FAS architecture is composed of components performing electrical, mechanical and hydraulic functions. Pilot commands are via the FLAP handle (Figure 23. Flap Handle Assembly). The handle interfaces with the Flap Electronic Control Unit (FECU), as well as the FCC and Backup Flight Control Unit (BFCU). The FECU provides excitation to the FLAP handle position sensors and monitors the handle position. The FECU interfaces via digital data busses with CAS, FCC and CMC systems. The Hydraulic Control Module (HCM), powered by the left, PTU, or AUX hydraulic system, provides hydraulic system pressure and flow to the FAS Power Drive Unit (PDU). The HCM manifold houses the Solenoid Operated Shutoff Valve (SOV) and the Electro-Hydraulic Servo Valve (EHSV) (both controlled by the FECU). The PDU converts hydraulic power into mechanical power, which is then transmitted through the torque shafts to the flap actuators attached to the flap surface. The following redundant design features are incorporated into the flap system: Three electrically-independent position sensors inside the FLAP handle (two Rotary Variable Displacement Transducers [RVDTs] and a set of discrete position switches) FECU powered by two, independent, aircraft-supplied 28V DC power supplies The HCM SOV and EHSV Electrically-duplicated position sensors on the left and right outboard actuators HCM SOV pressure shutoff capability checked by the FECU at every flight System Operation: Flap surface movement only occurs when the FLAP handle is moved from one detent position to another detent position, provided the FECU determines that the command and FAS integrity are valid. The FECU command and monitor paths each excite and demodulate one of the FLAP handle position sensors. Both the command and monitor paths must agree on a valid commanded position before flap movement is allowed. The FECU controls the flap surface rate and direction via the HCM EHSV. The EHSV supplies the PDU hydraulic motor with hydraulic flow. The PDU drives both flap surfaces, via torque shafts and actuators. Aircraft hydraulic system pressure to the EHSV is provided only if the HCM SOV is energized by the FECU. The FECU monitors the flap position, asymmetry, speed and direction based on feedback from the dual-channel position sensors on the left and right outboard actuators. If either FECU channel fails, then the FECU loses the ability to control the flaps, but a remaining healthy channel continues to report flap positions and flap status. A FECU failure results in the loss of control of the flap surfaces; however, the flap surfaces will remain in their last position. The FECU interfaces with FCC and avionics systems through digital Buses. The FECU provides the CMC with the flap system fault reporting / isolation and the avionics CAS with the flap system failure annunciation and flap surface position data / indication. In instances of total loss of hydraulic or electrical power to the flap system, the flaps will remain in their last position (held by the no-back devices integral with each actuator) when power was lost. The FCC angle-of-attack limiting schedule defaults to the 'clean and protected leading edges' condition for all flaps settings when 'on ground stationary' and remains latched in this condition up to 1500 ft radar altitude. This logic was implemented to support the immediate return scenario where flaps cannot be extended from 0o. In the event of a failure resulting in an uncommanded flap motion (for example, due to a failure in the HCM EHSV), the FECU will immediately detect the failure and arrest the uncommanded motion by de-energizing the HCM SOV, removing hydraulic pressure/flow to the HCM ESHV. In the event of a failure in the flap system that results in loss of PDU control of one flap surface (as for example, due to the mechanical disconnect of the torque shaft between the PDU and the inboard actuator), the FECU detects this failure by continuously monitoring the position feedback signals from the dual-channel position sensors on the left and right outboard actuators. Once a failure occurs, if the flap system is commanded to a new position and the flap surfaces start to move, the FECU will immediately detect the discrepancy between the left and right position sensors. The FECU then disables the flap system for the remainder of the flight by de-energizing the HCM SOV. The failure is annunciated to the flight crew and both flap surfaces remain at the position when the failure was detected. In the event of a jam in any component of the flap actuating system, the FECU immediately detects that there is no system motion when commanded. In the event of a flap actuator mechanical disconnect from the flap surface, the unfailed flap actuator attached to the same surface is capable of holding the surface in position for the remainder of the flight. Upon flap system command to move (following the actuator disconnect failure), the unfailed actuator operation results in skewing of the associated flap surface. In this condition, the output forces produced by the unfailed actuator increase rapidly to the point at which the force limiter inside the unfailed actuator engages and locks the flap system. Since the system is locked by the force limiter, the command-response monitor in the FECU immediately detects that there is no system motion when commanded and it disables the flap system for the remainder of the flight. Both left and right wing flap surfaces are simultaneously operated by the flap actuation system to extend or retract according to pilot input. The FAS consists of the following components: Flap Control Handle Flap Electronic Control Unit (FECU) Hydraulic Control Module (HCM) Power Drive Unit (PDU) Torque Drive Shafts and Pillow Blocks Flap Actuators Flap Position Sensors Description of Subsystems, Units and Components: Flap Control Handle: (See Figure 23. Flap Handle Assembly.) The FLAP handle is installed on the center console and provides pilot input command to the FECU, which provides excitation and demodulation of the FLAP handle's two RVDTs. The handle travel is divided by the following four detents: 0 (Flaps Up), 10, 20 (Takeoff / Go Around), and 39 (Flaps Down). Each detent represents a commanded flap surface position. The FCC monitors the FLAP handle's three micro-switches that indicate the four gate positions of the FLAP handle. Flap Electronic Control Unit (FECU): (See Figure 22. Wing Flaps System Schematic.) The FECU, located in the Right Electronics Equipment Rack (REER) provides control and system safety monitoring of the FAS. The FECU performs the control of the flap surface rate and direction of the movement by providing commands to the flap HCM. Hydraulic Control Module (HCM): (See Figure 22. Wing Flaps System Schematic and Figure 24. Flap Components.) The HCM is installed on the landing gear center torque box immediately aft of the PDU. The HCM consists of a solenoid, an electro-hydraulic servo valve and a hydraulic manifold. The HCM responds to electrical commands received from the FECU and provides directional control, extend / retract and low / high speed rate control of the PDU. The HCM houses a SOV that stops hydraulic flow when not energized. The SOV is spring-loaded to the closed position. The valve opens when the solenoid coil is energized with 28V DC provided by the FECU. When open, the valve allows hydraulic system flow and pressure supply to the EHSV. The EHSV provides flow control to the PDU. Power Drive Unit (PDU): (See Figure 24. Flap Components.) The motion of the left and right flap surfaces are mechanically synchronized by the flap PDU. The PDU consists of a hydraulic motor and a gearbox with splined output shafts on both sides to interface with the flap drive shafts. Located in the main landing gear wheel well, the PDU receives hydraulic power from the flap HCM. The PDU converts hydraulic power into mechanical power in order to simultaneously drive the left and right hand flap surface actuators via torque shafts and pillow blocks. A port located on the bottom of the PDU gearbox provides for any external leakage into an ecological bottle. Torque Drive Shafts and Pillow Blocks: (See Figure 24. Flap Components.) 16 rigid drive shafts are installed on both wings and in the torque box area to transfer the torque generated by the PDU to the flap system actuators. Both ends of the drive shafts have universal joints to accommodate the angular misalignment and linear offset between the pillow blocks or flap actuator splines to which the tubes attach. Each end of the torque shafts has an internal spline that mate with the external spline shafts located on the actuators, PDU and pillow blocks. One end of each tube is secured to its mating spline with standard hardware; the remaining end is free to float axially to ensure freedom of motion during wing bending and flap deployment. A total of 12 pillow blocks are installed on both wings to support the torque tube ends. Each pillow block consists of two ball bearings, an aluminum housing and an externally-splined through-shaft (which interfaces with the internally splined end fittings of the torque drive shafts). The pillow block bearings are sealed to prevent FOD and moisture ingress and are packed with grease. Flap Actuators: (See Figure 24. Flap Components.) Each flap surface is simultaneously driven by two linear ballscrew flap actuators. The actuators are lubricated with grease and vented to prevent corrosion. Flap actuators perform three basic functions: Conversion of high speed rotary motion at the input shaft to low speed linear motion at the translating nut. Irreversibility (the translating nut cannot be back-driven in normal operation) and/or torque shaft or actuator disconnect system failure mode. System overload protection (by limiting maximum force that each actuator can apply). In a case of a FAS jam or any other condition that results in increased FAS loading, the force-limiting function in each actuator provides overload protection of FAS components and the supporting structure by limiting the maximum actuator output load. Engagement of the force limiting device stalls the actuator. This causes a "trip" in one of the system safety monitors, which completely disengages the FAS. Flap Position Sensors: (See Figure 24. Flap Components.) A dual-channel position sensor is installed on each outboard flap actuator. Excitation of the flap position sensor is provided by the FECU. Controls and Indications: A full description of the Primary Flight Display appears in section 2B-05-00 and a description of the Flight Controls 2/3 synoptic page appears in section 2B-07-00. Circuit Breakers (CBs): The following CBs protect the wing flaps system: Circuit Breaker Name CB Panel Location Power Source FLAP CMD LEER A-10 L ESS 28V DC Bus FLAP MON REER A-8 R ESS 28V DC Bus Crew Alerting System (CAS) Messages: The following CAS messages are associated with the wing flaps system: CAS Message Possible Cause(s) Flap Asymmetry (caution) Flap position asymmetry detected. Flaps have stopped moving toward selected position. Flap Command Invalid (caution) Flap handle not in detent, or an RVDT channel has failed. Flaps Failed (caution) No surface movement when flap handle is commanded OR Surface movement in opposite direction OR Uncommanded flap surface movement. Flaps Maintenance Required (advisory) A failure within the flaps system has occurred that does not prohibit commanded flap movement. Flaps Rigging Complete (advisory) Rigging is valid for the current aircraft. Message occurs when in Maintenance Mode after Auto Rigging is satisfactorily completed. Limitations: There are no limitations established for the wing flaps system at the time of this writing. Figure 22. Wing Flaps System Schematic TIL-000646 Figure 23. Flap Handle Assembly TIL-002994 Figure 24. Flap Components SEE DETAIL E SEE DETAIL F SEE DETAIL C, D SEE DETAIL B SEE DETAIL A LEFT FLAP ASSEMBLY (RIGHT FLAP COMPONENTS AND QUANTITIES IDENTICAL) DUPLEX RESOLVER (OUTBD ACTUATOR ONLY) DETAIL A DETAIL B OUTBD FLAP ACTUATOR (ONE PER FLAP) INBD FLAP ACTUATOR (ONE PER FLAP) PILLOW BLOCK TORQUE SHAFT DETAIL C, D TORQUE SHAFTS (8 PER SIDE) PILLOW BLOCKS (6 PER SIDE) DETAIL F FLAP HYDRAULIC CONTROL MODULE (HCM) DETAIL E FLAP POWER DRIVE UNIT (PDU) TIL-003052 2A-27-70: Speed Brake and Ground Spoilers System General Description: (See Figure 25. Spoiler System Schematic and Figure 26. Inboard, Mid and Outboard Spoiler Hydraulic Components.) The aircraft has three pairs of spoiler surfaces (three on each wing). Each of the six spoiler panels provides speed brake and ground lift dump functions. Additionally, the midboard and outboard spoiler pairs provide roll control. For the inboard (IB) and midboard (MB) spoiler panels, the actuators are conventional Hydraulic Actuators (HAs). The outboard (OB) spoiler panel actuators use Electric Backup Hydraulic Actuators (EBHAs). In the event the right hydraulic system is lost, the outboard spoiler EBHAs operate in Electric Backup (EB). Speed brake and ground spoiler functions are not available when the Primary Flight Control System (PFCS) is in Backup mode (amber BFCU Active). Ground spoilers and Speed Brake auto retract are not available in Direct Mode. The Flight Control Computers (FCCs) control ground spoiler deployment and speed brakes. The spoiler commands are based on the pilot wheel positions and the speed brake lever. The FCCs perform the necessary control law computations (including command mixing between roll control and speed brake / ground lift dump functions) and send the spoiler position commands via two digital databuses to each of the REUs. In normal operation, each REU averages the position commands from the two FCCs. Actuator ram position feedback is sent back on the databus to the FCC(s) for monitoring. The speed brake function is performed by manually commanding the speed brake lever. The actuation of the speed brake lever will cause the three pairs of spoiler panels to deploy proportionally to the lever displacement. The speed brake handle input is provided to the FCCs through four Rotary Variable Differential Transducers (RVDTs). The control laws resident within the FCCs provide the necessary interlocks and protection for the deployment of speed brakes (simultaneous / symmetric deployment of the spoilers). Ground spoiler deployment is automatically controlled by the FCCs. Description of Subsystems, Units and Components: Speed Brakes: All six spoiler panels can be controlled by the speed brake handle located on the left side of the center pedestal (see Figure 27. Speed Brake Handle Assembly). The handle is a fly-by-wire module. The handle module contains four RVDTs to translate the flight crew speed brake commands into analog signals, which are read by the FCCs. An internal friction device contributes to the feel and operation of the lever by the pilots. The handle module has a detent position for the speed brake handle which holds the handle in the stowed position. The detent requires positive handle movement for spoiler deployment. Moving the handle out of the detent position will cause a light in the handle to illuminate and a Speed Brake Extended (advisory) CAS message. If the handle is moved out from the detent position and the throttles are not at idle, the handle will illuminate along with a (caution) message. When the speed brakes are out of the stowed position and the throttles are advanced above 95% Throttle Resolver Angle (TRA), the speed brakes will "auto retract" without the speed brake handle being repositioned. This auto retraction will cause a Speed Brake Auto Retract (caution) CAS message to be displayed. To reset the auto retract, the speed brake handle must be placed back to the stow / retracted position, and then if needed the speed brakes will react to the handle input. The reset of the handle is required even if the throttles are less than 95% TRA. The speed brake "auto retract" function will only activate in FCC Normal or Alternate modes. Ground Spoilers: All six spoilers are used to reduce lift on the wing to enhance the effectiveness of the main landing gear brakes. When the conditions have been meet for auto ground spoiler deployment, all six spoiler panels will deploy to a full 55o. The ground spoiler deploy requirements are: GND SPOILER Switch: ARMED AND Both Throttles at idle AND One or more of the following conditions: Left MLG WOW AND (left wheel speed > 47 kts) Right MLG WOW AND (right wheel speed > 47 kts) Both WOW AND (radalt < 10 ft OR invalid) (Both wheel speed > 47 kts) AND (radalt < 10 OR invalid) AND (flaps > 22 ORGPWS/GND SPLR FLAP ORIDE switch ON) AND BFCU is not ACTIVE The ground spoilers are normally armed prior to takeoffs and full-stop landings. During takeoff the ground spoilers will remain stowed provided that the throttles are out of the idle position (>2.5o TRA). If the flight crew elects to abort the takeoff, the ground spoilers will deploy when the throttles are retarded to idle. Ailerons as Ground Spoilers: The ailerons deploy as ground spoilers to reduce lift and increase drag after landing or during a rejected takeoff. For the ailerons to function as ground spoilers, the GND SPOILER switch in the cockpit center pedestal must be ARMED. The activation logic is the same as that used for the ground spoilers (i.e., weight-on-wheels or wheel speed, and both throttles at the idle position). When the ailerons deploy as ground spoilers, the Flight Control Computer (FCC) commands them to the full trailing edge-up position; however, aircraft roll control is unaffected, utilizing a single aileron with an approximate doubled displacement ratio with respect to control wheel input. Additionally, to balance the nose-up pitching moment created with the ailerons deploying as ground spoilers, a slight elevator trailing-edge-down displacement is simultaneously commanded by the FCC. Removing the ground spoiler function of the ailerons requires the same pilot actions as stowing the ground spoilers (i.e., selecting the GND SPOILER switch to the OFF position or advancing at least one throttle forward, out of the idle position). The 'ailerons as ground spoilers' function is only available when operating in FCC Normal and Alternate modes. GND SPOILER and GPWS / GND SPLR FLAP ORIDE Switches: (See Figure 28. Spoiler System Indications and Controls.) GND SPOILER: For automatic ground spoiler deployment, the GND SPLR switch must be placed in the ARMED position. The switch is a split lens with the upper portion labeled OFF (amber), and the lower portion labeled ARMED (blue). When the switch is extended, OFF is illuminated (gear down) or the switch is dark (gear up). When the switch is depressed, ARMED is illuminated. GPWS / GND SPLR FLAP ORIDE: The GPWS / GND SPLR FLAP ORIDE switch serves two functions. The primary function is that it allows the flight crew to inhibit certain EGPWS aural warnings that occur when the aircraft is at lower altitudes (calculated by the EGPWS system based on the flight conditions and local terrain) with flaps not set to a landing configuration. The other function is to allow the use of only wheelspeed logic in the automatic ground spoiler deployment when the flap setting is 20 degrees or less. The presence of both wheelspeed signals by themselves is not allowed to trigger deployment unless the flap setting is greater than 22 degrees (provided the system is armed and throttles at idle). This feature is primarily to remove wheelspeed logic from the take off condition where flaps are normally set at 20 or less and the aircraft is climbing out with the landing gear still extended. In that situation, both wheelspeed signals can remain present as the wheels spin down. If the throttle was brought back to idle for any reason, there could be automatic deployment since the system is normally ARMED on take off. The chances of such an occurrence is further reduced by adding the radar altimeter < 10feet logic. However, if both radar altimeters are invalid, they are removed from the logic -- leaving only the wheelspeed and flap position. (Reference the logic definition above.) If landing with flaps less than 22 degrees, depressing the GPWS GND SPLR / FLAP ORIDE switch to ON enables the combined left and right wheelspeed logic to deploy the spoilers. Controls and Indications: A full description of the Primary Flight Display appears in section 2B-05-00 and a description of the Flight Controls 2/3 synoptic page appears in section 2B-07-00. Circuit Breakers (CBs): The following CBs protect the spoiler system: Circuit Breaker Name CB Panel Location Power Source L INBD SPLR HA LEER A-7 L ESS 28V DC Bus R INBD SPLR HA LEER A-6 L ESS 28V DC Bus L MID SPLR HA PRI REER B-5 R ESS 28V DC Bus R MID SPLR HA PRI REER B-6 R ESS 28V DC Bus L MID SPLR HA SEC REER C-5 R ESS 28V DC Bus R MID SPLR HA SEC REER C-6 R ESS 28V DC Bus L OUTBD SPLR EBHA PRI REER C-1 UPS 28V DC Bus R OUTBD SPLR EBHA PRI REER C-2 UPS 28V DC Bus L OUTBD SPLR EBHA SEC LEER B-7 L MAIN 28V DC Bus R OUTBD SPLR EBHA SEC LEER B-6 L MAIN 28V DC Bus L OUTBD SPLR EBHA PWR EBHA PDB EBHA Bus 28V DC L OUTBD SPLR EBHA PWR EBHA PDB EBHA Bus 28V DC THROT QUAD CPOP D-8 R MAIN 28V DC Bus Crew Alerting System (CAS) Messages: The following CAS messages indicate the status of the speed brake / ground spoiler system: CAS Message Possible Cause(s) Aircraft Configuration (warning) On ground: Position of one or more of the following is not correct: FLAP Handle SPEED BRAKE Handle PARK / EMERG BRAKE Handle Landing Gear Control Handle Thrust Reverser Lever(s) GPWS/GND SPLR FLAP ORIDE Switch Pitch, Rudder, and/or Roll Trim Main Door NOTE: Message activation inhibited at speeds greater than V1 - 20 kts. In flight: One or more of the following: Speed brakes extended with Flaps >22o Speed brakes extended with landing gear down PARK / EMERG BRAKE Handle not down Ground Spoiler (warning) NOTE: Not available in FCC Direct mode or BFCU operation. Failure of ground spoiler component or deployed ground spoiler panel. Speed Brake Auto Retract (caution) NOTE: Not available in FCC Direct mode or BFCU operation. Speed brakes (flight spoilers) automatically retracted with speed brake handle not in stowed position and TLA �90%, or AOA limiting encountered. Speed Brake Extended (caution) NOTE: Not available in FCC Direct mode or BFCU operation. Speed brakes (flight spoilers) are deployed with throttles above idle. Speed Brake Fail (caution) Speed Brake control failed OR At least two pair of spoilers inoperative. CAS Message Possible Cause(s) Spoiler Panel Fail (caution) REU failure OR Loss of spoiler command to any spoiler panel. Ground Spoiler Unarm (advisory) Ground spoiler system is not armed, with landing gear extended. Speed Brake Extended (advisory) NOTE: Not available in FCC Direct mode or BFCU operation. Speed brakes are extended, throttles at idle. Limitations: Speed Brakes: Speed brakes are not approved for extension with flaps at 39o (DOWN) or with landing gear extended in flight. Automatic Ground Spoilers: If a touch-and-go landing is to be performed, the GND SPLR switch must be OFF and manual spoiler landing distances must be taken into account. With automatic ground spoilers inoperative, takeoff is permitted on dry and wet runways (less than 3mm of standing water) provided 20o flaps are used. Figure 25. Spoiler System Schematic Copilot Roll Sensor Cluster Air Data IRU Data AHRS Data FCC 2 FCC 1 Ch A Command Ch A Monitor Ch B Command Ch B Monitor STBY Left/Right Wing Trailing Edge Routing Right Wing Leading Edge Routing P S(P) P S P S P REU 6 SEL CTL REU 8 SEL CTL REU 10 SEL CTL REU 9 SEL CTL Actuator Command Actuator Command Actuator Command Actuator Command JMH 5/21/07 Ch A Command S REU 7 Ch A Monitor P SEL CTL Actuator Command Pilot Roll Sensor Cluster Ch B Command Ch B Monitor STBY Left Wing Leading Edge Routing S S(P) P REU 5 SEL CTL Actuator Command Right Hydraulic Gulfstream Proprietary Competition Sensitive MAC = One spoiler pair always Left Hydraulic Electrical Power TIL-003113 Figure 26. Inboard, Mid and Outboard Spoiler Hydraulic Components EHSA MANIFOLD MCE (EBHA) REU (EBHA) EHSA ACTUATOR EB MANIFOLD EBHA ACTUATOR HA MANIFOLD DETAIL A TIL-003010 Figure 27. Speed Brake Handle Assembly TIL-002995 Figure 28. Spoiler System Indications and Controls SEE DETAIL A DETAIL A TIL-003117