Battery Electric Machine (BEM) Systems Products Review PDF
Document Details
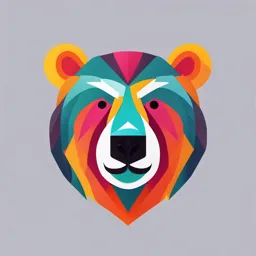
Uploaded by InspiringSerpentine6457
Tags
Related
- Bomasang Magazine PDF - Mining Technologies
- Bomasang Magazine PDF - Mining Technology
- SFD.081 - Battery and Electric Vehicle Fires PDF
- Spring Fire Department - Battery and Electric Vehicle Fires PDF
- Battery Electric Machine Systems Fundamentals PDF
- Battery Electric Machine Preventive Maintenance PDF
Summary
This document provides an overview of Battery Electric Machine (BEM) systems, focusing on their components and operation. It discusses hazardous voltage, safety procedures, and key components, like the Power Electronics Module (PEM), for both Caterpillar machines currently in production and soon to be released.
Full Transcript
Course Reason: To effectively service and repair Battery Electric Machine (BEM) systems, it is necessary to have an understanding of the BEM system components, systems operation, and preventive maintenance procedures. Course Objective: Provide the learner with the knowled...
Course Reason: To effectively service and repair Battery Electric Machine (BEM) systems, it is necessary to have an understanding of the BEM system components, systems operation, and preventive maintenance procedures. Course Objective: Provide the learner with the knowledge of the components, basic system operation, and preventive maintenance procedures for BEM systems. At the end of this course, you should be able to: Identify the Hazardous Voltage (HaV) features in BEM systems Identify the key components in BEM systems. Describe the key components in BEM systems. Explain BEM basic systems operation. Describe the safe shutdown procedures for BEM systems. Identify preventive maintenances procedures for BEM systems. Describe the preventive maintenances procedures for BEM systems. Caterpillar: Confidential Green Battery Electric Machine (BEM) Systems Products Review In Battery Electric Machine (BEM) systems, rechargeable Lithium- ion (Li-ion) batteries are used for the power source instead of an engine. The batteries provide electric power to propel the machine and drive the hydraulic pump(s). Currently, there are two Cat machines in production that are equipped with BEM systems: R1700 XE Load Haul Dump (LHD) 301.9 Mini Hydraulic Excavator (MHEX) Machines with BEM systems soon to be released include: 906 Compact Wheel Loader (CWL) R1700 XE 301.9 950 GC Medium Wheel Loader (MWL) 320 Hydraulic Excavator (HEX) LHD MHEX 906 CWL 950 GC MWL 320 HEX Caterpillar: Confidential Green Updated TOC – FET08 2.1.1 Hazardous Voltage Safety 2.1.2 Battery Electric Machine (BEM) Component Overview 2.1.3 Battery System Components 2.1.4 Charging System BEM 2.1.5 HaV Electrical System SR ED FET08 Components FET04 2.1.6 Auxiliary Components 2.1.7 Electronic Control Systems 2.1.8 System Operation 2.1.9 Battery System Cooling 2.1.10 HaV Electrical System Cooling Caterpillar: Confidential 2.1.11 Lubrication Systems Green (HaV) 2.1.1 The battery electric machine system contains Hazardous Voltage (HaV), which can pose an electrocution hazard when servicing the BEM system. Always assume hazardous voltage is present when making contact with the components in the BEM system. Make sure to use proper Personal Protective Equipment (PPE) and insulated tooling when making contact with the BEM system components. Caterpillar: Confidential Green (HaV) 2.1.1 (HaV) Caterpillar: Confidential Green Component Overview The BEM system key components are similar. Specific components and their location is dependent on the machine. Many of the HaV components require dedicated systems for component cooling and lubricating. Battery electric machine systems are monitored and controlled by ECMs. In this example of a 950 GC MWL, stored electric power from the batteries (1) is discharged to a Power Electronics Module (PEM) The PEM provides a connection point between the battery system, Hazardous Voltage (HaV) electrical system, and charging system. When the battery system is charging, the PEM receives electric power from an external power source, which charges the batteries. When the battery system is discharging (machine operating), the PEM supplies electric power to the Power Distribution Unit (PDU) (4). The PDU directs electric power to the inverters(s) (5) and DC/DC converter(s) (6). 950 GC The inverter changes and controls the incoming electric power, which is sent to an electric motor(s). The pump motor drives the Need image of 950 GC showing hydraulic pumps and the prop motor and pump motor propulsion motor on wheel machines transfers power to the drivetrain to propel the machine. The DC/DC converter reduces the hazardous DC voltage to 12 or 24 volts to charge the 12 or 24 volt battery and supply the low voltage electrical system, similar to an alternator which charges the 12 or 24 volt battery on a diesel engine powered machine. Caterpillar: NOTE: Confidential The HaV junction box of the R1700 XE LHD and the PEM of Green the 50V battery pack (301.9 MHEX) essentially function as both a Most battery electric machines have a Cat Battery Pack to supply the machine HaV electrical system. The current battery packs are: 50V, 300V, 600V battery packs. A Cat Battery Pack consists of three main components: Multiple Cat-branded battery modules (1) that store electric power. A PEM (2) that directs hazardous voltage into and out of the battery system. A Battery Management System (BMS) (3) that monitors and controls the battery modules and PEM in the charging and discharging of the battery system. Caterpillar: Confidential Green Battery Modules The battery modules of a Cat Battery Pack are organized into two columns placed side-by-side with one another. The battery modules are connected in specific configurations to either increase the voltage of the battery system (when connected in series) or extend the period in which electric power can be supplied by the battery system (when connected in parallel). Slides 9-11 can be either scrolling or a Pickup from slideshow 301.9 ITTP Mod 2 Caterpillar: Confidential Green PEM The PEM of a Cat Battery Pack connects the battery modules to the machine’s HaV electrical system. Its internal components are configured by the BMS to direct the flow of hazardous voltage when the Cat Battery Pack is in either a charging or discharging state. Pickup from 301.9 ITTP Mod 2 Caterpillar: Confidential Green BMS The BMS of a Cat Battery Pack consists of a BMS ECM (1), a Cat Product Link® radio (2), and multiple interface connectors which allow it to connect to the battery modules, the PEM, and the machine’s electronic control system. Pickup from 301.9 ITTP Mod 2 Caterpillar: Confidential Green The R1700 XE LHD has a battery system that is distinct from other battery electric machines and supplies 715 VDC to the machine HaV electrical system. The R1700 XE battery system consists of three main components: Two battery boxes (1) that store electric power. HaV junction box (2) that directs hazardous voltage into and out of the battery system. A BMS (3) that monitors and controls the battery modules, HaV junction box, and charger receptacle box in the charging and discharging of the battery system. Pickup from BEM Fund ITTP Mod 2 Caterpillar: Confidential Green Battery Box Each battery box of the R1700 XE organizes the battery modules inside into five sets of battery strings. The modules of each string, and the strings that comprise each box, are connected in a specific configuration to provide 715 VDC to the HaV electrical system. Caterpillar: Confidential Green HaV Junction Box The HaV junction box connects the battery boxes to the charger receptacle box (charging system), the DC/DC converter (low voltage electrical system), and the inverter (HaV electrical system). Its internal components are configured by the BMS to direct the flow of hazardous voltage when the battery boxes are in either a charging or discharging state. Caterpillar: Confidential Green BMS The BMS for the R1700 XE consists of two Battery ECMs (1) and additional control units to monitor and control the battery system at the battery string and battery module level. The control units are located in a battery control compartment (2) on the outside of each battery box. The R1700 XE BMS is explained in further detail later in this module. Pickup from BEM Fund ITTP Mod 2 Caterpillar: Confidential Green NOTE: The HaV junction box of the R1700 XE LHD and the PEM of the 50V battery pack (301.9 MHEX) essentially function as both a PEM and PDU. Caterpillar: Confidential Green Inverter The inverter in a battery electric machine converts incoming DC voltage into a specific voltage, current, and frequency for the electric drive motor(s) being supplied with electric power. The components within the inverter vary depending on the machine. The incoming DC voltage is transmitted through the input section (1) of the inverter, where it energizes the DC bus of the inverter. Electric charge from the DC bus is stored in capacitors to assist the inverter in being able to respond to changing power demands of the electric drive motor(s). The DC bus voltage then travels through the output section(s) (2) of the inverter, where modules with transistors and diodes invert the DC voltage to a Pulse Width Modulated (PWM) AC output voltage that has its voltage, current, and frequency precisely controlled. Once the inverter has attenuated the AC voltage, electric power is sent to the drive motor(s) via HaV cables. Some inverters require coolant to control the internal component temperature. Coolant ports (3) allow coolant to enter and exit the inverter. The 301.9 MHEX and 320 HEX have one inverter that supplies the pump motor with electric power. The 906 CWL and 950 GC MWL have two inverters; one dedicated to the propulsion motor, and one dedicated to the pump motor. The R1700 XE LHD has one inverter that supplies both the propulsion motor and pump motor with electric power. Caterpillar: Confidential Green Electric Motors Electric power from the inverter is directed to the electric motor by way of HaV cables. The drive motor provides output torque needed to propel the machine and drive the hydraulic pump(s). The drive motors consist of a rotor assembly and stator assembly. Electric power is delivered to the bus bars of the motor via HaV cables. The three-phase AC power emulates a rotating magnetic field inside the cavity of the stator assembly. This magnetic field produces a force that acts upon the rotor assembly, causing a mechanical rotation. Some drive motors require coolant to control the internal component temperature. Coolant ports allow coolant to enter and exit the cooling jacket surrounding the stator assembly within the motor housing. 301.9 Some drive motors also require oil to lubricate and cool the components of the rotor assembly. Lubrication ports allow lubrication oil to enter and exit the motor housing. Images of drive motors not connected to pump or drivetrain Caterpillar: Confidential Green Propulsion Motor Wheel machines are equipped with a propulsion motor that determines the rotational speed and direction of the machine’s travel. The 906 CWL propulsion motor connects to a dropbox that connects the front and rear axle assemblies. The 950 GC MWL 950 prop propulsion motor and R1700 XE LHD propulsion motor are 906 prop motor attached to an output transfer gear box that connects the front motor and rear axle assemblies. Pump Motor The pump motor is attached directly to a hydraulic pump or to a pump drive. The pump drive actuates multiple hydraulic pumps. The pump(s) provide the hydraulic oil flow for the machine hydraulic systems. For the 301.9 MHEX and 320 HEX, this includes the travel hydraulic system that propels the tracks of the machine. The pump motor on the 301.9 MHEX, 320 HEX, and 906 CWL connect directly to the machine’s hydraulic pump. The pump motor on the 950 GC MWL and R1700 XE LHD connect to a pump drive that rotates gears to drive the machine hydraulic pumps. 906 pump motor Caterpillar: Confidential Green DC/DC Converter Battery electric machines are equipped with one or more DC/DC converters that convert hazardous voltage from the DC bus of the PDU to either 12 VDC or 24 VDC depending on the machine. The low voltage charges the 12 VDC or 24 VDC batteries and supplues the low voltage electrical system The low voltage system consists of components such as lights, control panels, ECMs, and other electrical and electronic machine components. A DC/DC converter typically has one HaV input port (1) that receives hazardous voltage from the PDU, and multiple low voltage output ports (2) that directly supply key components of the low voltage system. Some DC/DC converters require coolant to control the temperature of their internal components. Coolant ports (3) allow coolant to enter and exit the converter Caterpillar: Confidential Green Some battery electric machines are equipped with auxiliary components that need to be supplied with hazardous voltage. Examples of auxiliary components that require hazardous voltage include: - Cab heater (1): 301.9 MiniHEX - Positive-Temperature-Coefficient (PTC) heating elements (2): 906 CWL and 950 GC MWL - A/C compressor (3): 950 GC MWL - Thermal Management System (TMS) (4): 950 GC MWL. Caterpillar: Confidential Green DC Charging System Battery electric machines have a DC charging system to recharge their battery modules using an external DC power source. The R1700 XE LHD is equipped with a charger receptacle box (1) at the left rear of the machine. There are two DC charger ports (2), each of which allows the LHD to connect to a Mobile Equipment Charger (MEC) unit. Both DC charger ports can connect to a MEC unit to charge the machine faster. The charger receptacle box also contains several safety features (fuses, relays, vehicle electrical center) to ensure proper voltage and current is being delivered when the machine is charging. R1700 DC Charge Receptacle The charger receptacle box is monitored by the BMS and controlled by the battery ECMs. The DC charging system for the other battery electric machines consists of a DC charger port (3) that directly connects an external DC source. The charger port is monitored by the machine’s electronic control system. 301.9 DC Charge Receptacle Caterpillar: Confidential Green AC Charging System Battery electric machines other than the R1700 XE LHD also have an AC charging system to recharge the batteries using an external AC power source. The AC charging system consists of an AC charger port (1), that 5 directly connects an external AC source. The charger port is monitored by the machine’s electronic control system similarly to the DC charging system. 2 4 NOTE: The AC port type varies depending on region. Type 1 charger ports (2) are installed on machines located in the U.S. Type 2 charger ports (3) are installed on machines located in the European Union (EU). AC voltage coming from the AC charger port must be rectified by one or more onboard chargers (4) into DC voltage before entering the PDU. Fuses (5) control current of the AC voltage that is entering the onboard chargers. 4 NOTE: An AC power source and DC power source cannot be used at the same time to charge the Cat Battery Pack. 301.9 AC Charge Receptacle Caterpillar: Confidential Green Charge Mode – Cat Battery Pack When a battery electric machine with a Cat Battery Pack is in charge mode, the battery system is being supplied with voltage from a DC or AC power source. If the Cat Battery Pack (1) is being charged through the DC charger port (1), the appropriate ECM checks the status of the charging system and if no faults are detected, DC voltage is allowed to charge the batteries. If the Cat Battery Pack is being charged through the AC charger port (2), the appropriate ECM checks the status of the charging system and if no faults are detected, AC voltage is allowed to flow to the onboard chargers. The onboard DC Charging chargers rectify the AC voltage into DC voltage and the rectified DC voltage charges the batteries. DC voltage is supplied to the battery modules based on specific charge demand from the BMS ECM. Caterpillar: Confidential Green AC Charging Charge Mode – R1700 XE LHD When the R1700 XE LHD is in charge mode, the battery system is being supplied with DC voltage from the charging system. When a MEC (1) unit is connected to a DC charger port (2), the Battery ECM responsible for that port checks the status of the charger receptacle. If no faults are detected, the HaV junction box is enabled, and DC voltage can flow to the HaV junction box. The Battery ECMs then have the BMS check the status of every battery module. If no faults are detected, DC voltage is allowed to charge the batteries. DC voltage is supplied to the battery modules based on specific charge demand from the BMUs. Pickup from MEC Charger – SERV2225 Intro Caterpillar: Confidential Green BEM systems require multiple ECMs to control the battery system and HaV electrical system. A Primary ECM communicates over the CAN data link with one or more additional ECMs. This charts list the ECMs involved in controlling each machine’s battery system, HaV electrical system, and overall machine systems operation. Caterpillar: Confidential Green Battery System Control In battery electric machines with a Cat Battery Pack, the BMS is responsible for monitoring and controlling the functions of the battery modules and PEM. The BMS consists of a BMS ECM (1), a Cat Product Link® radio (2), and multiple interface connectors (3) which allow it to connect to: - Battery modules - PEM - HaV electrical system ECM Caterpillar: Confidential Green Battery System Control On the R1700 XE machines, the BMS is responsible for monitoring and controlling the functions of the battery modules, HaV junction box, and charger receptacle box. Each battery module is monitored by a Safety Module Unit (SMU) (4). Each string of battery modules has their SMUs monitored by a Battery Management Unit (BMU) (5) located in a battery control compartment (6) on the outside of each battery box. A Master Battery Management Module (MBMM) (7) inside the left battery control compartment oversees all of the BMUs in both battery control compartments. The BMUs and MBMM in the left battery control compartment are also controlled by a dedicated Battery ECM (8). The BMUs in the right battery control compartment are also controlled by a dedicated Battery ECM (9). Slideshow for R1700 XE Caterpillar: Confidential Green HaV Electrical System Control The HaV electrical system components are monitored and controlled by the Electric Drive ECM or Machine ECM depending on the machine. On the R1700 XE, the Electric Drive ECM (1) monitors and controls the functions of the inverter and DC/DC converter. On the 301.9 MHEX, the Machine ECM (2) monitors and controls the functions of the inverter, DC/DC converter, onboard chargers, and charger ports. On the 906 CWL the Electric Drive ECM (3) monitors and controls the functions of the PDU, inverters, DC/DC converter, onboard chargers, and charger ports. On the 950 GC MWL the Machine ECM (3) monitors and controls the functions of the PDU, inverters, DC/DC converter, onboard chargers, and charger ports. Indirect monitoring and control of the pump motor and propulsion motor (wheel machines) can be performed by interpreting or adjusting the voltage, current, and frequency of the electric power being sent to them by their inverter. Caterpillar: Confidential Green BEM Systems Control 4 The ECMs responsible for managing the battery electric machine systems are typically governed by an ECM that monitors and controls the functions of the machine as a whole. The R1700 XE LHD has a Powertrain ECM (1) located within an ECM enclosure above the propulsion motor of the machine. Both Battery ECMs and the Electric Drive ECM are overseen by this ECM. On the 301.9 MHEX, the Machine ECM (2) is located at the front of the machine below the cab floor and oversees the BMS ECM. The 906 CWL and 950 GC MWL have a Machine ECM (3) located behind the operator’s seat 2 inside the cab of the machine. On the 950 GC MWL, the Machine ECM oversees the BMS ECM. 3 On the 906 CWL the BMS ECM and the Electric Drive ECM (4), located near the machine’s PDU, are overseen by the Machine ECM. By processing sensor inputs throughout the machine and input commands from the controls within the operator station, the ECM that governs the battery electric machine systems can issue specific outputs to the ECMs that Add 301.9 Machine directly control the battery system and HaV electrical system components when the ECM machine is in operation. Caterpillar: Confidential Green Caterpillar: Confidential Green Caterpillar: Confidential Green Caterpillar: Confidential Green Caterpillar: Confidential Green Discharging Mode When the machine is operating the battery system is discharging DC voltage to the HaV electrical system. NOTE: This image shows the battery electric machine system components on the 950 GC MWL. During machine operation, the ECM (1) responsible for overseeing the battery electric machine systems determines electric motor output based on operator input and the demands of the system. The ECM also communicates actionable data to the other ECMs responsible for the BMS and the HaV electrical system. The ECM(s) (2) responsible for the battery system has the BMS check the status the batteries (3). If no faults are detected, the battery system is enabled and DC voltage is discharged from the battery modules to the PEM (4) or HaV junction box (R1700 XE). The ECM responsible for the HaV electrical system checks the status of the PDU (5) (PEM 950 GC on 301.9 and HaV junction box on R1700 XE) and the inverter (6) responsible for supplying the electric motor (7) with electric power. If no faults are detected, the PDU Need image of 950 GC showing and inverter are enabled, and DC voltage from the PEM or HaV junction box can flow to the DC bus of the inverter. The inverter converts the incoming DC voltage into AC prop motor and pump motor voltage, whose voltage, current, and frequency is precisely controlled by commands from the governing ECM. AC voltage from the inverter is sent to the pump motor and to the propulsion motor on wheel machines. Click or tap on the drop-downs below to view these different methods of electric motor operation: Pump Motor Operation The pump motor actuates a hydraulic pump(s), which provides oil flow to the machine hydraulic systems. The pump motor speed determines the hydraulic pump(s) rpm, which is a factor in the volume of hydraulic pump output flow. Propulsion Motor Operation (wheel machines) For the 950 GC MWL and R1700 XE LHD, the propulsion motor drives the output transfer gears, which transfer power to the front and rear axles to propel the machine. For the 906 CWL, the propulsion motor drives the gears in a dropbox, which transfers power to Caterpillar: Confidential the front and rear axles to propel the machine. The speed and direction of the propulsion Green motor determines the speed and direction of machine travel. Wheel Machines Caterpillar: Confidential Green 2.2.2 2.2.3 R1700 XE LHD 2.2.4 301.9 MHEX 2.2.5 Caterpillar: Confidential Green 2.2.1 Overview Maintenance ensures that Cat® machines will function reliably and without any unforeseen actions or interventions. The data obtained during the walk-around inspection and Preventive Maintenance (PM) is useful for planning needed services and detecting potential problems with the battery electric machine systems. It is recommended that maintenance programs be designed and executed by qualified personnel only. The instructions and recommendations found in the Operation and Maintenance Manual (OMM) of Cat machines should be read carefully and used as a basis when planning its maintenance program. Note that maintenance recommendations found in the OMM represent only a minimum level of maintenance. R1700 XE OMM.png Caterpillar: Confidential Green 2.2.2 Caterpillar: Confidential Green R1700 XE LHD 2.2.3 There is a hazardous voltage components check for the R1700 XE LHD BEM machines, which is covered in the machine OMM. Hazardous Voltage Components Check- Housing Hazardous Voltage Components Check- HaV Cables Hazardous Voltage Components Check- Grounding Caterpillar: Confidential Green 2.2.3 Hazardous Voltage Components Check- Housing This maintenance procedure is performed on all battery electric machines. Scheduled maintenance is recommended every 500 service hours or 3 months. Begin by visually checking the component housings and enclosures of the BEM systems components covered in Module 2. Check for any of the following conditions: Seals that are damaged or loose Hardware or fasteners that are damaged, loose, or missing Casing dents or punctures Debris build-up prop mod housing.png Caterpillar: Confidential Green 2.2.3 Hazardous Voltage Components Check- HaV Cables After checking the component housings and enclosures, inspect the HaV cables and HaV electrical harnesses (indicated by their orange color) of each HaV component for any of the following conditions: Cable damage or able to see cable insulation Wire clips or straps that are damaged or missing Cables with signs of rubbing, pinching, or kinking Connections that are corroded, damaged, or loose Debris build-up on or between cables prop mod HaV cables.png Caterpillar: Confidential Green 2.2.3 Hazardous Voltage Components Check- Grounding Once the HaV cables and electrical harnesses have been inspected, check the bonding wires (1) and grounding wires (2) of each HaV component for any of the 2 following conditions: Wires that are corroded, damaged, or worn Connections that are corroded, damaged, or loose Wires or connections that are contaminated Cables/straps that have become separated from their cable/strap end 1 Debris build-up If any of the conditions mentioned exist, make the necessary repairs. Debris can be cleaned by using pressurized air. Use a maximum air pressure of 205 kPa (30 psi) when cleaning debris build-up. Always refer to a Cat machine’s OMM for the most current and correct procedure. prop mod grounding.png Caterpillar: Confidential Green 301.9 MHEX 2.2.4 For the 301.9 MHEX BEM machines there are several preventive maintenance procedures provided in the OMM. Bond - Check Insulation Resistance – Check Inverter Cooling Fans – Inspect/Clean Voltage Components – Check Voltage Components – Clean Battery Pack Charger Fans Caterpillar: Confidential Green In trblstg manual, also see SERV2281, Mod 3 In trblstg manual, also see SERV2281, Mod 3 Caterpillar: Confidential Green Caterpillar: Confidential Green Caterpillar: Confidential Green