Formula Bharat 2025 Rules Booklet PDF
Document Details
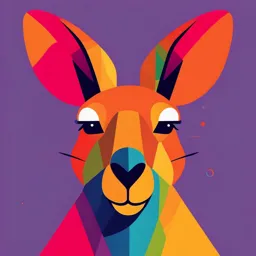
Uploaded by SufficientReasoning4306
2025
Tags
Summary
This document is the Formula Bharat 2025 Rules Booklet, detailing the technical regulations for electric vehicles. The booklet covers various aspects including definitions, electric powertrain, traction systems, energy storage, and electrical safety guidelines. It's a comprehensive guide for teams participating in the Formula Bharat competition, ensuring adherence to safety and performance standards.
Full Transcript
FORMULA BHARAT 2025 RULES BOOKLET EV ELECTRIC VEHICLES EV1 DEFINITIONS EV1.1 Tractive System (TS) EV1.1.1 Tractive System (TS) – every part that is electrically conn...
FORMULA BHARAT 2025 RULES BOOKLET EV ELECTRIC VEHICLES EV1 DEFINITIONS EV1.1 Tractive System (TS) EV1.1.1 Tractive System (TS) – every part that is electrically connected to the motor(s) and TS accumulators. EV1.1.2 TS enclosures – every housing or enclosure containing parts of the TS. EV1.2 Galvanic Isolation EV1.2.1 Galvanic Isolation – two electric circuits are defined as galvanically isolated, if all of the following are true: the resistance between both circuits is ≥500 Ω/V, related to the maximum TS voltage of the vehicle, at a test voltage of maximum TS voltage or 250 V, whichever is higher. The isolation voltage RMS, AC for 1 min, between both circuits is higher than three times the maximum TS voltage or 750 V, whichever is higher. The working voltage of the isolation barrier, if specified in the datasheet, is higher than the maximum TS voltage. EV2 ELECTRIC POWERTRAIN EV2.1 Motors EV2.1.1 Only electric motors are allowed. EV2.1.2 Motor attachments must follow T10. EV2.1.3 Motor casings must follow T7.3. EV2.1.4 The motor(s) must be connected to the accumulator through a motor controller. EV2.2 Power Limitation EV2.2.1 The TS power at the outlet of the TSAC must not exceed 80 kW. EV2.2.2 Regenerating energy is allowed and unrestricted. EV2.2.3 Wheels must not be spun in reverse. EV3 GENERAL REQUIREMENTS EV3.1 Grounding EV3.1.1 TS enclosures, see EV1.1.2, must consist of either + Version 1.7 | 10.24.2024 | Adaptation of FS-Rules 2024 v1.1 87 / 136 FORMULA BHARAT 2025 RULES BOOKLET a grounded solid layer made of at least 0:5 mm thick electrically conductive material, aluminum or better, having a resistance below 300 mΩ, measured with a current of 1A, to LVS ground and able to continuously carry at least 10% of the TS accumulator main fuse current rating or be fully made out of electrically insulating materials having an isolation resistance of at least 2MΩ, measured with a voltage of 500V. The enclosure must be rigid and must prevent possible mechanical penetrations. Protruding electrically conductive parts, such as fasteners or connectors, must follow EV3.1.2 The TSAC might use at least 0.9 mm thick steel layer as the grounded layer. EV3.1.2 Electrically conductive seat, driver harness, and firewall mounting points as well as the aluminum layer of the TS firewall, see T4.8, and the LVS ground measuring point, see EV4.7.8, must have a resistance below 300 mΩ, measured with a current of 1A, to LVS ground and be able to continuously carry at least 10% of the TS accumulator main fuse current rating. EV3.1.3 Parts of the vehicle which are or may become electrically conductive within 100 mm of any TS component must have a resistance below 100Ω to LVS ground EV3.1.4 The rotating part of the wheels may not be grounded. EV3.2 Overcurrent Protection EV3.2.1 All electrical systems must have appropriate overcurrent protection. EV3.2.2 The continuous current rating of the overcurrent protection must not be greater than the continuous current rating of any electrical component, for example wire, busbar or other conductor that it protects. i.e. if multiple pins of a connector are used to carry currents in parallel, each pin must be appropriately protected. EV3.2.3 All overcurrent protection devices must have an interrupt current rating which is higher than the theoretical short circuit current of the system that it protects. EV3.2.4 All overcurrent protection devices must be rated for the highest voltage in the systems they protect. All devices used must be rated for DC. EV3.2.5 All overcurrent protection devices which are part of the TS must not rely on programmable logic. The overcurrent protection function of motor controllers/inverters for the motor outputs may rely on programmable logic. EV3.2.6 The overcurrent protection must be designed for the expected surrounding temperature range but at least for 0°C to 85°C. EV3.2.7 The TS high current path through the accumulator(s) must be fused. + Version 1.7 | 10.24.2024 | Adaptation of FS-Rules 2024 v1.1 88 / 136 FORMULA BHARAT 2025 RULES BOOKLET EV4 TRACTIVE SYSTEM (TS) EV4.1 General Requirements EV4.1.1 The maximum permitted voltage that may occur between any two electrical connections is 600 V DC and for motor controller/inverters internal low energy control signals 630 V DC. EV4.1.2 All components in the TS must be rated for the maximum TS voltage. The TS area of a PCB (see EV4.3.6), is considered as one component. Every input connected to the TS must be rated to the maximum TS voltage. EV4.1.3 All components must be rated for the maximum possible temperature which may occur during usage. EV4.1.4 Fans with > 50W total power must not be connected to the TS. EV4.2 TS System Enclosures EV4.2.1 TS enclosures, see EV1.1.2, must be labeled with (a) reasonably sized sticker(s) according to “ISO 7010-W012” (triangle with black lightning bolt on yellow background). The sticker must also contain the text “High Voltage” if the voltage is more than 60 V DC or 50 V AC RMS. EV4.3 Separation of Traction System and Grounded Low Voltage System EV4.3.1 The entire TS and LVS must be completely galvanically isolated (see EV1.2.1 and IN4.1.1). EV4.3.2 All connections from a TS component to external devices, such as laptops must include galvanic isolation, see EV1.2.1. EV4.3.3 TS and LVS circuits must be physically segregated such that they are not running through the same conduit or connector, except for interlock circuit connections. EV4.3.4 Where both TS and LVS are present within an enclosure, they must be separated by barriers made of moisture resistant insulating materials or maintain the following spacing through air, or over a surface: Voltage Spacing U < 100 V DC 10 mm 100 V DC < U < 200 V DC 20 mm U > 200 V DC 30 mm EV4.3.5 Components and cables capable of movement must be positively restrained to maintain spacing. EV4.3.6 If TS and LVS are on the same PCB, they must be on separate well defined areas of the board, meeting the spacing requirements in Table 5, each area clearly marked with “TS” or “LV”. The outline of the area required for spacing must be marked. + Version 1.7 | 10.24.2024 | Adaptation of FS-Rules 2024 v1.1 89 / 136 FORMULA BHARAT 2025 RULES BOOKLET Over Through Air Conforma Voltage Surface (Cut in Board) l Coating 0 V DC to 50 V DC 1.6 mm 1.6 mm 1.0 mm 50 V DC to 150 V DC 6.4 mm 3.2 mm 2.0 mm 150 V DC to 300 V DC 9.5 mm 6.4 mm 3.0 mm 300 V DC to 600 V DC 12.7 mm 9.5 mm 4.0 mm Table 5: Spacing required between TS and LV. “Conformal coating” refers to a coating insulator, solder resist is not a coating. EV4.3.7 Teams must be prepared to demonstrate spacing on team-built equipment. For inaccessible circuitry, fully assembled spare boards must be available. EV4.4 Positioning of Tractive System Parts EV4.4.1 Except what is permitted according to EV4.4.3, all parts belonging to the TS including cables and wiring must be located within the rollover protection envelope, see T1.1.16. “Part” is the whole device such as the complete HVD. EV4.4.2 Any part of the TS that is less than 350 mm above the ground, except what is permitted according to EV4.4.3, must be protected from impacts, see T3.15. Impact protection must follow T3.16 when having bolted attachments. TS wiring in front of the front hoop may alternatively be shielded by the front bulkhead support structure according to T3.14. The TSAC must be no higher than the top of the impact structure as mentioned in EV5.5.1. EV4.4.3 Outboard wheel motors are allowed only if an interlock is routed along the TS wiring such that the shutdown circuit, see EV6, is opened before the TS wiring or its clamping fails an interlock is routed along a suspension member such that the shutdown circuit, see EV6, is opened if the suspension fails TS wiring is not be able to reach the cockpit opening or the driver regardless of where it breaks wiring outside of the rollover protection envelope, see T 1.1.15 is minimum length wiring outside of an impact structure or front bulkhead support structure (see EV4.4.2), is minimum length Minimum length is the shortest distance plus extra wiring caused by bending radius. EV4.5 Tractive System Insulation, Wiring and Conduit EV4.5.1 All live parts of the TS must be protected from being touched. This must include team members working on or inside the vehicle. This is tested with a 100 mm long, 6 mm diameter insulated test probe when the TS enclosures are in place. EV4.5.2 Insulation material that is rated for the maximum TS voltage must be used. Using only insulating tape or rubber-like paint for insulation is prohibited. EV4.5.3 The temperature rating for TS wiring, connections, and insulation must be appropriate for the expected surrounding temperatures but at least 85°C. EV4.5.4 TS components and containers must be protected from moisture in the form of rain or puddles (see IN9). + Version 1.7 | 10.24.2024 | Adaptation of FS-Rules 2024 v1.1 90 / 136 FORMULA BHARAT 2025 RULES BOOKLET EV4.5.5 It must be possible to clearly assign and prove wire gauge, temperature rating and insulation voltage to each used wire. EV4.5.6 All TS wiring must be completed to professional standards with appropriately sized conductors and terminals and with adequate strain relief and protection from loosening due to vibration etc. EV4.5.7 TS wiring must be located out of the way of possible snagging or damage. EV4.5.8 All TS wiring that runs outside of TS enclosures must: Be enclosed in separate orange non-conductive conduit or use an orange shielded cable. The conduit must be securely anchored to the vehicle, but not to wire, at least at each end. Be securely anchored at least at each end so that it can withstand a force of 200 N without straining the cable end crimp. Body work is not sufficient to meet this enclosure requirement. EV4.5.9 Any shielded cable must have the shield grounded. EV4.5.10 Every TS connector outside of a housing must include a pilot contact/interlock line which is part of the shutdown circuit. Housings only used to avoid interlocks are prohibited. EV4.5.11 All TS connections must be designed so that they use intentional current paths through conductors such as copper or aluminum and should not rely on steel bolts to be the primary conductor. EV4.5.12 All TS connections must not include compressible material such as plastic in the stack-up or as a fastener. FR-4 is allowed. Screw type connectors are allowed to be used inside the TSAC if only it is part of an OEM product given that the OEM product is automotive grade or is tested for appropriate vibrations. EV4.5.13 TS connectors outside of TS enclosures must be designed in a way that the TS cannot be activated, see EV4.11, if connected in any way other than the design intent configuration. EV4.5.14 All electrical connections, including bolts, nuts, and other fasteners, in the high current path of the TS must be secured from unintentional loosening. Fasteners must use positive locking mechanisms, see T10.2, that are suitable for high temperatures, see EV4.5.3. Components, e.g. inverters, certified for automotive use might be allowed without positive locking feature, if connections are completed as recommended by the manufacturers’ datasheet and no positive locking is possible. EV4.5.15 Teams must be prepared to demonstrate positive locking. For inaccessible connections, appropriate photographs must be available. EV4.5.16 Soldered connections in the high current path are only allowed if all of the following are true: connections on PCBs the connected devices are not cells or wires the devices are additionally mechanically secured against loosening + Version 1.7 | 10.24.2024 | Adaptation of FS-Rules 2024 v1.1 91 / 136 FORMULA BHARAT 2025 RULES BOOKLET EV4.6 Data Logger EV4.6.1 A calibrated data logger will be provided by the officials and must be inserted during competition. The data logger measures TS voltage and TS current. EV4.6.2 The data logger must be in an easily accessible location so that it is possible to insert, remove or replace it within 15 min in ready to race condition. EV4.6.3 The data logger must not be placed within the accumulator container. EV4.6.4 All current supplying the TS must run through the data logger. The data logger must be inserted in the negative TS supply between the most negative AIR(s) and the inverters. EV4.6.5 The TS voltage sense connection of the data logger must be directly connected (see T1.3.1) to the most positive AIR(s) on the vehicle side. The direct connection must not carry any current. EV4.6.6 The data logger must be directly supplied (see T1.3.1) from the LVMS. EV4.6.7 The specification of the data logger will be available on the competition website. EV4.7 Tractive System Measuring point (TSMP) EV4.7.1 Two TSMPs must be installed directly next to the master switches (see EV6.2). EV4.7.2 The TSMPs must be directly connected (see T1.3.1) to the intermediate circuit capacitors even if the HVD has been opened or the TS accumulator is disconnected. EV4.7.3 4 mm shrouded banana jacks rated for 1000V CAT III or better must be used for the TSMPs. EV4.7.4 The TSMPs must be directly connected to the positive and negative motor controller/inverter supply. The TSMPs must be marked “TS+” and “TS-” and exclusively mounted on an orange background. EV4.7.5 The TSMPs must be protected by a non-conductive housing that can be opened without tools. The cover must always be mechanically linked to the vehicle. EV4.7.6 Each TSMP must be secured with a current limiting resistor according to the following table. Fusing of the TSMPs is prohibited. The resistors power rating must be chosen such that they are able to continuously carry the current if both TSMPs are short circuited. Maximum TS Voltage Resistor Value Umax≤ 200 V DC 5 kΩ 200 V DC