ETOS® MD-IV Explanation PDF
Document Details
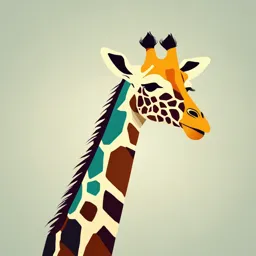
Uploaded by BestSellingBeige
null
2025
null
null
Tags
Summary
This document provides an explanation of the ETOS MD-IV switching sequence, including comparisons with the MD-III system. It covers topics such as the control circuit, motor circuit, signals, and functions. The document is richly illustrated with diagrams, making it a comprehensive resource.
Full Transcript
ETOS® MD-IV. Switching sequence © MR 01/30/2025 | RM-SOR E. Espitia confidential Agenda 1. Comparison MD-III vs. MD-IV 2. Switching sequence Control Circuit MD-IV 3. Switching sequence Motor Circuit MD-IV 4. ETOS MD-IV Signals 5. ETOS MD-IV Functions © MRJan 30, 202...
ETOS® MD-IV. Switching sequence © MR 01/30/2025 | RM-SOR E. Espitia confidential Agenda 1. Comparison MD-III vs. MD-IV 2. Switching sequence Control Circuit MD-IV 3. Switching sequence Motor Circuit MD-IV 4. ETOS MD-IV Signals 5. ETOS MD-IV Functions © MRJan 30, 202 2 5 Electrical comparison with TAPMOTION® MD- III Jan 30, 2025 | 3 MD-III vs MD-IV. Motor + MD-III + Motor circuit (single phase) + Heater (permanently connected) 01/30/2025 | 4 MD-III vs MD-IV. Motor + MD-IV + Motor circuit (three phase) + Heater (thermostatically controlled) + Verification switches (186, 187) 01/30/2025 | 5 MD-III vs MD-IV. VIM + MD-III + VIM circuit (86X) + Runback circuit (86XA) + Verification switches (186, 187) 01/30/2025 | 6 MD-III vs MD-IV. VIM + MD-IV + VIM circuit (86X) + Runback circuit (86XA) + Brake circuit (88) 01/30/2025 | 7 MD-III vs MD-IV. Control + MD-III + Brake circuit (88) + Control circuit + Without step-by-step circuit (continuous operation) 01/30/2025 | 8 MD-III vs MD-IV. Control + MD-IV + Control circuit + Without step-by-step circuit (continuous operation) 01/30/2025 | 9 MD-III vs MD-IV. Signalling + MD-III + Signals 01/30/2025 | 10 MD-III vs MD-IV. Signalling + MD-IV + Signals − - On terminals 01/30/2025 | 11 MD-III vs MD-IV. Signalling + MD-IV + Signals − - Outputs on ISM modules 01/30/2025 | 12 MD-III vs MD-IV. Signalling + MD-IV + Signals − - Inputs on ISM modules 01/30/2025 | 13 MD-III vs MD-IV. Signalling + MD-III + Position Signals 01/30/2025 | 14 MD-III vs MD-IV. Signalling + MD-IV + Position Signals 01/30/2025 | 15 Switching sequence Control circuit Jan 30, 2025 | 16 + Direction impulse direct to DI | after the ism check DO running direction closes 84L contactor closes Motor is not starting! Break contactor will start the operation thru ISM | 84L goes to electrical self- sealing DO last direction closes Motor starts running S13 operates after 2 sections (of 33) | auxiliary contactor 84Z closes thru cam S13 -> mechanical sealing | 84L is held thru running cam S13 | Cam S13 switches back at the end of operation (section 31 of 33) | 84L opens + -> motor stops | 84Z opens + -> ready for next operation | Switching sequence Motor circuit Jan 30, 2025 | 25 Phase shift capacitor Starting capacitor Run back contactor-VIM lockout Raise / Lower contactors Brake contactor Brake & start circuit 3PH Motor | | ISM DO | operating capacitor Starting capacitor | | | 200ms | | | | Ready for next operation | Signals Jan 30, 2025 | 37 + standar Signals MD-IV – based on SSE scale d Jan 30, 2025 | 38 + optiona Incomplete tap change (LTC off position) l What is it? The predecessor actuator TAPMOTION MD-III has the cam switch (DO) 180, which signals when a tap- change operation has not been completed. In MD-IV this is done while watching the S13 cam in the motor unit. When does it happen ? + Activation at SSE 2/3 - 31 (not in the gray area) What needs to be set up ? + Always standard, just DO signal as an option selectabel 01/30/2025 | 39 + optiona Off position (Alarm unsafe position) l -> new OPA: Incomplete Tap Change What is it? + Checks if the OLTC is in unsafe position and the gives a alarm after configurable countdown + Tapmotion MDIII: OPA When does it happen ? + Trigger condition: Activation at SSE 2/3 - 31 (not in the gray area) + Expiry of alarm time What needs to be set up ? + Alarm time (default =30sec) + Parameter time adjustable by customer in the GUI. 01/30/2025 | 40 + optiona OLTC running l What is it ? A signal which shows that the OLTC is running (same like for all tap changers). Its based on S13 and a time based software solution When does it happen ? Optional DO OLTC running (S22/122) can be choosen: For a left running motor, the DO is switched from SSE 4 – 33. The SSEs are calculated based on the switching time together based on the S13 via software solution. Optional OLTC running (S23/123) can be choosen : For a right running motor, the DO is switched from SSE 4 – 33. The SSEs are calculated based on the switching time together based on the S13 via software solution. 01/30/2025 | 41 + optiona Motor running l What is it? Signal while motor is running What is connected ? DOs: + Motor rotates clockwise, DO high when the corresponding direction contactor is energized, continuous in continuous positions = Motor running (Q2/84R) + Motor rotates anticlockwise, DO high when the corresponding direction contactor is energized, continuous in continuous positions = Motor running (Q1/84L) + Motor rotates in any direction, DO high if the corresponding direction contactor is energized, continuous in continuous positions (Q1/L-Q2/R) 01/30/2025 | 42 + optiona Motor running l Special behaviour for run trough positions Motor running old Run through position Motor running new Jan 30, 2025 | 43 + standar STATUS OK ? d + Signal that checks if SICAM modules started correctly + Normally takes ~2 min after switching the device on + Possible errors for STATUS OK=0: − Missing power supply − Software errors − Device errors + What needs to be set up ? Always standard, possible as an optional DO Jan 30, 2025 | 44 Functions Jan 30, 2025 | 45 + standard Homing/Hand Cranking What is it? Homing means to synchronize the tap position between motor unit and cabinet When needs Homing to be done ? + After first setup + every time after inserting the handcrank + after the MSS was tripped 01/30/2025 | 46 + standard Tap Position indication Microswitch Cams (Panasonic) S186, S187, S186, S187, S13 S13 1. Setting up the tap position / calibrate the tap position 2. Every S13 activation together with 84L or 84R activation is counting the tap position SSE-Scale Jan 30, 2025 | 47 + standard MDU lockout Function to block the motor drive after finishing the actual operation Triggered by: + OLTC Oil Level + VIM Status/Lockout + MCB trip + Temperature blocking of motor unit + Thermal motor switch (49) + (Low) Temperature lockout + Invalid tap position/hand crank inserted Jan 30, 2025 | 48 + optional Motor heating What is it? One phase of the motor will be supplied with current to raise the temperature correspondingly When does it happen ? + When the motor reached a temperature of -15°C is reached, the heating function will be deactivated. What needs to be set up ? Motor heating needs to be selected in SAP − Mandatory in arctic variance − Optional in Basic variance 01/30/2025 | 49 + optional Thermal motor switch (49) What is it? + The function monitors the motor winding temperature. + The input value is an analog PT100 sensor that is always wound into the motor winding. + This temperature is to be monitored for the higher limit values. The lower limits are taken over by the motor heating feature. + If the upper limit value (greater than greater) is exceeded, the MDU lockout will prevent further switching until the motor temperature falls below the configured reset temperature. The same applies to the warning message, which is present until the temperature falls below the set temperature again. When does it happen ? + Thermal motor switch needs to be selected What needs to be set up ? + Temperatures need to be set up + Default value for limit: Trip:130°C - Reset: 95°C + Default value for warning: 110°C 01/30/2025 | 50 + optional (Low) temp lockout What is it? Temperature Blocking for high & low temperatures + OLTC Temperatur Limit Lowest -> blocking (value calculated like in MD-III) + OLTC Tempreatur Limit Warning Low -> warning (can be set up in SAP) + OLTC Temperatur Limit Warning High -> warning (can be set up in SAP) + OLTC Temperatur Limit Highest -> blocking (value always 100°C) What is connected ? DO for blocking 01/30/2025 | 51 + standar End position detection SOD2 d What is it? Monitoring of power factor of phase W at the motor unit. + End position + Standstill trough power fail + normal operation All have a different power factor. => So the algorithm can detect if there is an error and which one. When does it happen and what is algortihm doing? + Running in end position: If algorithm detects end position MBS will be tripped and homing needs to be done + Power fail: If an engine standstill is detected, a completely new operation is triggered. This means that 88 drops out and is energized again together with 83. This also resets the run-through protection and there is no motor circuit breaker tripping. 01/30/2025 | 52 + standar Extended run-through protection d What is it? + recording of the motor running time. + calculate an average value of the motor running time and store it persistently + if motor running time > 1.5 ' average motor running time then leads to tripping of the motor protection switch after finishing the operation + if motor running time > 1.94 ' average motor running time then immediate tripping of the motor protection switch. + the limit values of the running time and the default motor running time of 2 sec. should be adjustable by the MR service. Factors:1.5 & 1.94. When does it happen ? Tripping of MCB if motor runtime exceeds limit avlue 01/30/2025 | 53 + optional Mechanical interlock What is it? Mechanical interlock option like used from MDIII. The Mechanical Interlock is designed to prevent the switch from being moved with the crank handle in the event of a VIM fault. Hand cranking is prevented by means of a brake located in the motor unit, which can be specifically controlled by an electromagnet. In the normal state, the electromagnet is supplied via 24 VDC, i.e. the drive can be moved with the hand crank. In the event of a fault, the current flow from the ISM is interrupted via DO. The brake is then applied and operation using the hand crank is not possible. Plug connection is monitored. Option 1: If the VIM board detects a fault (self-test of the VIM board or the vacuum tubes of the RMV) and hand crank operation is detected, the current flow to the solenoid of the electromagnet is lost so that the gearbox is blocked in its position. Option 2: Functional like option 1, extended by a signal to a terminal strip (DO) for tripping the coil of the high- voltage circuit breaker of the power transformer. 01/30/2025 | 54 Operations Counter Standard Add-On Always counting Resettabl e counter Jan 30, 2025 | 55 THE POWER BEHIND POWER. reinhausen.com