Enginge Controls and Ignition 2.docx
Document Details
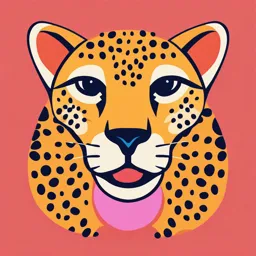
Uploaded by PhenomenalNumber
Full Transcript
Source /Input Left Engine Right Engine Channel A Channel B Channel A Channel B AF (MAU 1/ DGIO 1) Primary Primary AF (MAU 2 / DGI0 2) Primary Primary There are two types of input signals to the EEC: Duplex: These are signalsthat are input separately in...
Source /Input Left Engine Right Engine Channel A Channel B Channel A Channel B AF (MAU 1/ DGIO 1) Primary Primary AF (MAU 2 / DGI0 2) Primary Primary There are two types of input signals to the EEC: Duplex: These are signalsthat are input separately into Channel A and Channel B Simplex: These are singular signals which are either: Internally cross-wired before validation Internally cross-linked during validation Internally cross-communicated during processing All input signals are validated (checked for accuracy). There are seven methods of input signal validation: For All Data: Parity Check: Each channel checks its input value withinthe Operating System (OS) software Source Destination Identifier (SDI) Check: Each channel checks its input value to confirm that the data is being received from the expected source Sign Status Matrix (SSM) Check: Each channel checks its input value to check the status of the data as identified by the sender Update Rate Check: Each channel checks its input value to confirm that the data is being received at the expected frequency Bus Check: Each channel checks its input value to confirm that the bus is inactive for a prolonged period and are used to support maintenance annunciations For Discrete Data Only: Cross-check: Each channel compares its own input signal value against the other channel's input signal value For Non-Discrete Data Only: Range Check: Each channel checks its input value to ascertain that it is within the normal operating range (minimum and maximum) values (f) Fault Monitoring: The EEC has afullself-test (Built-In Test Equipment [BITE]) and fault isolation, accommodation system. This system operates continuously to detect and isolate errors in the FADEC system. The FADEC System communicates errors in three formats: Maintenance messages are for the maintenance crew only Status messages are displayed on the Crew Alerting System (CAS) and are for flight crew recognition FADEC internal "Health Logic", for safe operation and control only Maintenance Messages: Each FADEC fault sets a Maintenance message. Maintenance messages are stored in the NVM and are for maintenance crew awareness only. Status Messages: Status Messages appear on the Engine Alert Display (EAD) and are for flight crew recognition. There are three major types of Status Messages: DND requires immediate repair, STD requires repair very soon, and LTD requires repair as soon as possible. DND - Do Not Dispatch STD - Short Term Dispatch LTD - Long Term Dispatch Health Level Scheme: The Engine Control System has a dual-channel EEC to enable fault accommodation.The selection of the channel to control is based upon the health of the channel. The loss of some inputs, communications, EEC internal functions or outputs or combinations of these in one channel may cause a degradation of but not loss of engine control. In these cases the faults may be accommodated by switching to the other lane, if it is more healthy. The health scheme has the ability to command pull back to idle or to shut down the engine by de-powering the drives. An intermediate health score (Health Level 20 to 25) will cause pull back to idle, a high health score (Health Level 26 to 30) will de-power drives. Outside of the health score related faults, an EEC-commanded shutdown can be achieved by the overspeed protection function or the fire and overheat protection function. Outside of the health score related faults, an EEC-commanded thrust limitation to idle is performed for inadvertent thrust reverser deployment and for ThrotUe Resolver Angle (TRA) fault accommodation. OEM Provided Data Engine Control• Revision 13 2023..03-23 2A-76-00: B of 30 Health Skew is a temporary re-prioritization of health scores during engine start. In this way, more relevant starting specific faults wouldlead to a channel change. Health scores are allocated as indicated in Table Table 2. Health Levels and Their Associated Control Effect on the next page for single faults. A higher index indicates degraded channel health, a fully-healthy channel has a health level of zero. The channel in control shall perform a pullback to idle when it cannot transfer control to the other channel and a failure is detected leading to Health Levels between 20 and 25. Table 2. Health Levels and Their Associated Control Effect Health Level Associated Control Effect Fault Description 0 No Effect- Full Functionality N A 3 Degraded Control VSV Actuator Torque Motor Monitor Fault 4 Degraded Control FMVActuator Torque Motor Monitor Fault 5 Degraded Control Dual Ignition Fault 8 Degraded Control TCC Drive Fault 10 Degraded Control SAVITRIV I Hydr. Sol. / TR lntertock Fault 10 Degraded Control ARINC Input Bus Failure (from MAU) (TBC) 10 Degraded Control Dual ARINC Input Bus Failure {from ADS) 10 Degraded Control PMA Failure {0/C Detected) 15 Degraded Control Dual Ignition Fault (During Start Only) 15 Degraded Control Own Channel Fire and Overheat Amber Exceedance 15 Degraded Control Own Channel Fire and Overheat Sensor Fault 19 Degraded Control VSV Actuator Torque Motor Null Fault 19 Degraded Control Single HP5 Bleed Valve (Single Solenoid Fali ure) 20 Degraded Control SOV Failed Closed (During Start Only) 20 Degraded Control Single HPB Bleed Valve (Single Solenoid Fali ure) 20 Degraded Control FMVActuator Torque Motor Null Fault Health Level Associated Control Effect Fault Description 20 Degraded Control VSV Position Cross-Check Fault 20 Degraded Control N2V Fault (Validated NH Speed) 20 Degraded Control P30 Fault 20 -21 Degraded Control Dual or Multiple HP5 Bleed Valve Failures 21-23 Degraded Control Combination of HP8 and HP5 Bleed Valve Failures 26 Relinquish Control Safety I Control Processor Communication Failure 30 Relinquish Control N1V Fault (Validated NL speed) 30 Relinquish Control VSV Actuator Torque Motor Wire Fault 30 Relinquish Control VSV Actuator Jammed Fault 30 Relinquish Control FMVActuator Torque Motor Wire Fault 30 Relinquish Control FMVActuator Jammed Fault 30 Relinquish Control Computer Power Up Check Fault 30 Relinquish Control Own Channel Fireand Ovemeat AES Exceedance 30 Relinquish Control FMV Position Cross-Check Fault 30 Relinquish Control VSV Position IActuator Fault 30 Relinquish Control FMV Position I Actuator Fault Overspeed Protection: The BR725 overspeed protection system provides individual protection against LP and HP rotor overspeed.Rotor overspeed can result in hazardous engine effects. Each lane of the EEC has dedicated data inputs for both rotor speeds and both EEC channels must detect overspeed in order for the engine to implement overspeed protection. The Control System compares validated High-Pressure (HP) Shaft Speed with the following: HP amber line threshold HP redline threshold HP transient redline threshold For each HP redline threshold exceedance, the function records the cumulative time above redline and the peak value of HP. These values are stored in EEC NVM. The engine is protected from hazardous engine effects resulting from HP Shaft Overspeed via inherent HP compressor surge. OEM Provided Data Engine Control• Revision 13 2023..03-23 2A-78-00: 10 of 30 The Control System will compare validated Low-Pressure (LP) Shaft Speed with the following: LP amber line threshold LP redline threshold - forward thrust LP redline threshold - reverse thrust LP transient redline threshold For each LP redline threshold exceedance, the fundion will record the cumulative time above redline and the peak value of LP. These values are stored in EEC NVM. The engine is proteded from hazardous engine effects resulting from LP Shaft Overspeed by the LP Turbine Overspeed Protection System (TOS). The TOS system rapidly detects and accommodates an LP shaft break, shutting off the fuel flow for safe engine shutdown. Quick response of the TOS system is essential for minimizing turbine overspeed and thereby the potential for the release of high-energy debris. Pressure Transducer Module: The pressure transducer module is attached to the top of the EEC. It contains two PO, two P30 and two P50 pressure transducers to measure pressures at different parts of the engine (one transducer for each channel). The air pressures measured by the EEC for control functions are as follows: PO is the ambient air pressure which is measured below the cowls P30 is the air pressure at the exit from the HP compressor P50 is the air pressure at the exit from the Low-Pressure (LP) turbine The transducer module also has the housing for the data entry plug which is installed between the air tube connectors. Permanent Magnetic Alternator (PMA): The EEC is powered by its own PMA when the engine is running. The PMA is driven by the accessory gearbox and supplies power to the EEC above HP PMA online speed.The PMA will come online at 35% HP (HP PMA on-line speed). The PMA assembly has a rotor and a stator. The PMA provides a three-phase power supply to each lane of the EEC. The PMA operates as a variable reluctance generator where output voltage is proportional to the change in ftux generated by magnets. The magnets are part of the rotor assembly. Stator: OEM Provided Data Engine Controls Revision 13 2023-03-23 2A-76-00: 11 of 30 The stator is the stationary part of the PMA. The stator has two sub-stators (one sub-stator for each lane of the EEC) that gives full separation and isolates the power supply to each EEC channel. Rotor: The PMA rotor is fitted to the end of the AG B drive shaft and turns at the same speed as the gearbox driveshaft. The rotor is positioned in the center of the stator housing. When the shaft turns, the magnets give the changing magnetic flux necessary to generate an output voltage for each phase of the PMA alternator stator. The tandem design ensures an isolated power supply to each EEC channel. Controls andIndications: Circuit Breakers (CBs): The following CBs power the engine control system: Circuit Breaker Name CB Panel Location Power Source L FADEC CHA POP C-8 L ESS DC L FADEC CH B CPOP C-8 R ESS DC R FADEC CHA POP C-9 L ESS DC R FADEC CH B CPOP C-9 R ESS DC Crew Alerting System (CAS) Messages: The following CAS messages are associated with the engine control system: Area Monitored CAS Message (caution) EEC is in a Do Not Dispatch (DND) condition. EEC Short Term Dispatch (STD) has timed out without corrective maintenance. EEC is now in a DND condition. L-R Engine Maintenance STD (caution) Loss of both FADEC channelsARINC 429 data by the CAS system. L-R FADEC A-B Bus Fail (caution) EEC internal temperature is above amber line limit. ll;l#;j•J:kl:Mt (caution) Loss of channel AARINC 429 data by the CAS system. L-R FADEC A Bus Fai (advisory) Loss of channel BARINC 429 data by the CAS system. L-R FADEC B Bus Fai (advisory) EEC is in a Long Term Dispatch (LTD) condition. L-R Engine Maintenance LT (advisory) OEM Provided Data Engine Control• Revision 13 2023-03-23 2A-78-00: 12 of 30 Limitations: Status Messages: Takeoff is not authorized with a DND (Do Not Dispatch) or STD (Short Tenn Dispatch) status message displayed. OEM Provided Data Engine Controls Revision 13 2023-03-23 2A-76-00: 13 of 30 Figure 1. Eledronic Engine Controller (EEC) Schematic AIRFRAME -y _ _ I AIRFRAME TIL-IJ01818 OEM Provided Data Engine Control• Revision 13 2023.03-23 2A-78-00: 14 of 30 Figure 2. Electronic Engine Controller (EEC) DATA ENTRY PLUG (DEP) TIL-001819 2A-76-30: Engine Thrust Management System 1. General Description: (See Figure 3. Engine Thrust Management System Overview and Figure 4. Power Lever I EEC Interface Simplified Block Diagram.) Flight crew management of engine thrust is accomplished by manual or autothrottle movement of the power levers on the center console. Thrust settings are monitored by reference to the indications on the selected display window (Engine, Alternate Engine or Compacted Engine 1/6 windows). The power levers signal thrust commands through Rotary Variable Displacement Transducers (RVDTs) incorporated into the power lever mounts beneath the OEM Provided Data Engine Controls Revision 13 2023-03-23 2A-76-00: 15 of 30 cockpit center console panel. Each engine power lever RVDT has two channels linked to the corresponding channels of the Electronic Engine Controller {EEC) withinthe Full Authority Digital Engine Control {FADEC). Flight crew management of engine thrust is accomplished by manual or autothrottle movement of the power levers on the center console. Thrust settings are monitored by reference to the indications on the selected display window {Engine,Alternate Engine or Compacted Engine 1/6 windows). Power lever movement thus results in the controlling EEC channel adjusting fuel flow to the engine to match the thrust setting dictated by the power lever. (See Sections 2A-76-20: Electronic Engine Control System and 2A-73-10: Engine Fuel System.) The autothrottle system is engaged I disengaged via switches on the Throttle Quadrant Assembly (TQA) and controlled by the Automated Flight Control System (AFCS)which is an integral part of the Modular Avionics Units (MAUs). Eachthrottle lever incorporates an autothrottle servo and drive motor to move the throttlelevers during autothrottle operation as commanded by the AFCS. Since actual engine thrust can only be measured in atest facility, a surrogate measurement of thrust is used to manage engine power. The primary thrust setting reference on the Engine window{s) display is Engine Pressure Ratio (EPR). EPR is defined as the ratio of pressure sensed at the rear of the Low Pressure {LP) turbine to the pressure of the ambient atmosphere. The ratio measures the increase in ambient pressure generated by the action of the engine compressor stages and the energy of combustion driving the engine turbinestages.EPRis measuredbythe engine EEC and communicated tothe MAUs for use by the display systems. A typical EPRvaluefor takeoffthrust at an airport near sea level on astandard day is 1.55.The EPRvalue is not atrue indication of actual enginethrust since itdoes not measure the propulsive force generated bythe LPfanstage air that effectively contributes a thrust component equivalent to some turboprops. EPR is used for thrust management because it most accurately measures the internal forces of the engine compressor and turbine stages. If a malfunction prohibits EPR measurement by the engine EEC, an alternate method of thrust management is control of the speed of the LP rotor. LP rotor rpm provides a convenient method of engine control since it is easily measured, however, like EPR, it does not reflect actual engine thrust and has the additional disadvantage of being unable to directly determine engine combustion forces since the LP rotor is not mechanically driven by the High Pressure {HP) turbine. Forward Trust Management: The EEC usestwo distinct control modes: Primary (or"EPR.) and Alternate (or "LPj.These distinct control modes operate as follows: Engine Pressure Ratio (EPR) Primary Control Mode: The primary control mode uses EPR to calculate the power setting for forward thrust control under steady-state operating conditions.The EEC calculates an EPR command corresponding to the actual power lever position from linear interpolation between maximum available EPR at OEM Provided Data Engine Control• Revision 13 2023..03-23 2A-78-00: 18 of 30 maximum forward Throttle RVDTAngle (TRA) and an idle EPR reference at idle TRA. Thrust is then set and held by closed loop control of EPR. EPR idle reference is a calculated datum. At Ground, Flight and Approach Idles, the enginewill be controlled to one of the minimum limiters of Shaft Speeds (NL and NH) and HP Compressor Discharge Total Air Temperature (P30) depending on environmental conditions and bleed air demands. VVhen the aircraft is in the landing configuration, the EEC will automatically raise the idle setting to Flight Idle in order to assure compliance with go-around requirements in the case of an aborted landing. b. LP Alternate Control Mode: (See Figure 5. Alternate Control Mode Diagram.) If any of the required resources for EPR control are not available (primarily air data and bleed requirements), the EEC automatically soft-reverts to the Alternate (LP) Control Mode. This mode can also be manually selected (considered a hard reversion) by commands entered through the Standby Multifunction Controller (SMC). In Alternate (LP) Control Mode, thrust is set and held by closed-loop control of LPshaft speed.In this control mode, LP Command is calculated from interpolation between max LP Command at maximum forward TRA and the LP Forward Idle reference. Simi ar to the Primary (EPR) Control Mode at Idle TRA, the engine is controlled to an appropriate limiter. Flight Idle is set for the aircraft in landing configuration. Once an engine reverts to Alternate Control Mode, itwill not automatically recover Primary (EPR) Control Mode even if the EEC has the required resources available for this mode. Return from Alternate Control Mode to Primary (EPR) Control Mode can only be achieved when Hard Reversion is deselected via the SMC and the EEC has all the required resources available. Therefore, follo.ving a Soft Reversion, an engine must first be Hard-Reverted before a return to Primary (EPR) Control Mode is possible. VVhen an engine Soft-Reverts to Alternate Control Mode, the EEC ensures that the transfer to the LP Control schedule is "bumpless".This is achieved within the EEC soft.ware by applying a delta to the LP Command. In this situation, LP Command is determined as a function of the power lever position and an LP schedule. The LP Delta is determined by the EEC as the difference between the LP Command and the measured LP Actual at the time of Soft Reversion. c. Autothrottle System: The autothrottle and engine synchronization functions are carried out by the MAUs and are independent ofthe FADEC system. The EEC transmits engine data to the MAUs, which calculate a required EPR. The MAU commands the throttle to the required position using closed-loop control via an ARINC 429 interface to the TQA. The FADEC system uses measured throttle position in the normal way to calculate the enginethrust requirement. OEM Provided Data Engine Controls Revision 13 2023-03-23 2A-76-00: 17 of 30 The autothrotde system is engaged Idisengagedvia switches onthe TQA and controlled by the AFCS which is an integral part of the MAUs. Each throttle lever incorporates an autothrottle servo and drive motor to move the throttle levers during autothrottle operation as commanded by the AFCS. Each throttle quadrant has an Autothrottle Disconnect switch to deselect the autothrottles.The system will also automatically disengage if the flight crew manually changes the power lever position set by the autothrottles. (See Figure 6. Autothrottle System Simplified Block Diagram and Figure 7. Power Lever Installation.) When the autothrotde system is engaged for takeoff, the Flight Management System (FMS) will drive the power levers forward to the thrust setting selected on the Multi-Function Control and Display Unit (MCDU) takeoff initialization page. During takeoff, the FMS will maintain a constant power lever position after the airplane has accelerated through 60 knots. The fD<ed power lever position is maintained until400 feet, at which time the FMS will position the power levers to the dimb power settingselected on the PERFORMANCE INIT page of the MCDU as long as another vertical mode has been selected i.e.FLCH, Vertical Speed, or Autopilot ON. Because of the close integration of the FMS and the autothrottle system, airplane speed can be controlled by the FMS accordingto standard regulatory limits - i.e.,maintaining 250 knots below 10,000 feet or until passing into uncontrolled airspace. V\lhen speed is no longer restricted, the FMS will command the power levers to the selected appropriate dimb speed schedule and when cruise altitude is reached, reduce power to long range cruise or other selected setting. With both autopilot and autothrottle engaged, the flight crew can control airplane speed by entries made on the MCDU or by manual selections made on the Flight Guidance Panel.Guidance panel entries are made by depressing the pushbutton below the speed window (the legend within the button will illuminate ON), and manually rotating the CHG knob between the pushbutton and the speed window. The autothrottle will change power lever position to achieve the selected speed.Any manual selection made on the guidance panel will override selections programmed with the MCDU. For a complete description on the use of the autothrottle and autopilot including descent and approach modes, see Sections 28-04-00 through 28-06-00. A sub-function of the autothrottle system called the Electronic Thrust Trim System (ETTS), enables the flight crew to synchronize the engines in order to reduce noise in the cabin area. The crew can select synchronization of either EPR, LP rpm or HP rpm using the SMC Thrust Rating Selection (TRS) menu. Thelower left Line Select Key (LSK) on the menu page is used to select the controlling engine parameter. When synchronization is selected, the FMS uses a discrete ARINC 429 bus signal to increase the power setting at the EEC of the lower performing engine to match the selected criteria of the other engine. The control OEM Provided Data Engine Control• Revision 13 2023..03-23 2A-78-00: 18 of 30 authority of the ETTS is limited to ±5% change. See Section 2B-05-00 for more information. Note The autothrottle system cannot be used if the engines are in alternate LP rotor speed control. Reduced Takeoff (FLEX) Thrust Settings: (See Figure 8. Rated And FLEX Takeoff Thrust Diagram.) The use of reduced takeoff (FLEX) thrust is permissible when airplane weight and runway conditions are such that full takeoff thrust is not necessary. The use of FLEX thrust reduces wear and maintenance; therefore prolonging engine life by reducing the high turbine gas temperatures that occur during the use of takeoff thrust. The implementation of FLEX thrust is by the use of an assumed temperature higher than ambient day temperature. Prior to takeoff, flight aews using the FMS determine the assumed temperature and corresponding de-rate takeoff EPR rating values required for the current aircraft weight, flap position, runway length, airport ambient condition, etc. They then enter the assumed temperature into the FMS. Autopilot will calculate takeoff EPR rating values using the assumed temperature (rather than actual) and then set the throtUes to the de-rate takeoff EPR values. The requirements outlining the use of de-rated thrust are as follows: The use of flex thrust is always at pilot discretion VVhen conducting a FLEX takeoff, max takeoff power can beselected (if required) at any time without introducing any control difficulties Reduced thrust does not result in loss of any function, enginefailure warnings or takeoff configuration warnings At least 75% of full rated thrust is used on all takeoffs De-rated Climb: In the same way as utilizing de-rated takeoff thrust, de-rated dimb thrust can be used to operate the aircraft without incurring noise violations. Refer to the Airplane Flight Manual (AFM) for additional information on de-rated climb procedures. Note Derivation ofthe EPR command is achieved by the performance computers and does not affect EEC functionality. Idle Thrust Management: Idle is the minimum thrust available from each engine. Three idle power settings are provided: Ground Idle (Low Idle): The lowest thrust rating for sustained ground operation while ensuring stable operation within the safety margins of the engine. OEM Provided Data Engine Controls Revision 13 2023-03-23 2A-76-00: 19 of 30 Flight Idle: The minimum thrust rating that can be used in flight and is generally a higher thrust setting than Ground Idle, depending upon airframe configuration (e.g.,flaps, weight-on-wheel,etc., and engine conditions, such as bleeds, TRUs, etc.). Approach Idle (High Idle) directed by landing configuration: Approach Idle (A/I) is higher to support aborted landings and maximum reverse thrust demands. The engine EEC controls HP rpm when the power lever is positioned to idle. The idle power lever setting has two ranges: Flight (high) idle and Ground (low) idle. The EEC will control the engine at the high idle setting if data from the MAUs indicate that the airplane is in approach mode. Approach mode is indicated if the flaps are set to more than 22 , the Weight-On-Wheels (WOW) system is in the air mode and the anti-skid wheel speed sensors detect wheel rotation less than 53 knots. If a datafailure prevents the EEC from determining the approach configuration, the EECwill default to the high idle mode. High idle during an approach ensuresa more rapidengine response in the event of a go around. The EECwillcontinuethe high idle control modefor five seconds after landing to allow rapid engine acceleration for reverse thrust if needed. The exact HP rpm settingfor both low and high idle is dependent upon pressure altitude, with a minimum rpm setting predicated upon the following engine functions: Supplying sufficient bleed air to meet pneumatic system and anti-icing requirements Prevent ice accumulation on the engine fanstage Maintain the engine-driven generator at operational speed Operation of the engine handling bleed valves during rain ingestion or other indement conditions Reverse Thrust Management: (See Figure 3. Engine Thrust Management System Overview.) The Thrust Reverser (TR) levers are located on the upper portion of the throttle lever. Positioning the TR levers deploys or stows the thrust reversers and controls reverse thrust. With the thrust reversers deployed, a continued upward movement of the TR levers results in an increase in reverse thrust. Reverse thrust is controlled to a LP and selection of reverse thrust must be made from the forward idle position. The throttle quadrant indudes a mechanical locking device that prevents the TR levers from moving into the reverse thrust positionwhen they are notatthe forward idle position. It also has a reverse throttle inter1ock, which prevents increase in reverse thrust until the doors are 12% deployed and the WOW or Wheel Spin-Up (WSU) signal is valid. Inorder for the TR levers to move up and aft to command reverse thrust levels, the main power levers must be in the idle position. Selecting reverse thrust with the TR levers will initiate hydraulic deployment of the reverser doors on OEM Provided Data Engine Control• Revision 13 2023-03-23 2A-78-00: 20 of 30 the engine exhaust section. Reverse thrust is limited to idle until the engine reverser doors are open at least 12% - the doors are indicated fully open at 85%. VVhen the doors reach the minimum opening deployment, the EEC will adjust fuel flow to the engine to achieve the reverse thrust levels commanded by the TR levers. Maximum reverse thrust is limited to 77.7% LP rpm. For a description of the operation of the engine thrust reversers see Section 2A-78-20: Thrust Reverser System. Controls and Indications: The Engine system 1/6window display contains the primary indicators for controlling engine thrust. If the Engine system window is not available, the Compacted Enginewindow and Alternate (Secondary) Enginewindow may be used to monitor engine thrust. If no display system is available, engine thrust may be controlled and monitored using entries on the MCDU. V\lith the autothrottle system engaged, the Primary Flight Display (PFD) contains text annunciations of the autothrottle control modes selected with the SMC. For descriptions of the engine parameters shown on the various display windows and the formats of autothrottle annunciations, see the appropriate Sections 28-03-00 thru 28-06-00. Circuit Breakers (CBs): The following circuit breakers power elements of the engine thrust management system: Circuit Breaker Name CB Panel Location Power Source THROT QUAD CPOP D-8 R MAIN DC Bus Crew Alerting System (CAS) Messages: CAS messages associated with the engine thrust management system are: Area Monitored CAS Massage FMS I Autothrottle L-R Engine ALT Contra (advisory) EEC FMS I Autothrottle fleifj@ {advisory) FMS I Autothrottle AfT 1-2 TQA Power Fail {advisory) FMS I Autothrottle AfT Inhibit - AD (advisory) FMS I Autothrottle AfT Inhibit - AFC {advisory) FMS I Autothrottle AfT Inhibit - Eng ALT Con :(advisory) FMS I Autothrottle AfT Inhibit - Disconnect S (advisory) FMS I Autothrottle AfT Inhibit - ED :i {advisory) FMS I Autothrottle AfT Inhibit - EP {advisory) OEM Provided Data Engine Controls Revision 13 2023-03-23 2A-76-00: 21 of 30 Area Monitored CAS Message A/T Inhibit -IR (advisory) FMS IAutothrottle FMS IAutothrottle FMS IAutothrottle A/T Inhibit - Spee {advisory) FMS IAutothrottle A/T Inhibit - Thrust Re {advisory) FMS IAutothrottle A/T Manual Overrid (advisory) FMS I FADEC I Autothrottle Engine Sync Fai {advisory) FMS I FADEC I Autothrottle Engine Sync Limi (advisory) Power Lever RVDTs I FADEC Throttle Quadrant 1-2 Fai (advisory) Limitations: Primary Operating Limits: The following Engine Operating Limits exist for the BR700-725A1-12 engines: Slgnal Operating Limit Value LP Speed Transient LP Limit 104.3% LP Redline 102.8% LP 102.8% LP Reverse Redline n.7% Time Delay 30 seconds HP Speed Transient HP 101.3% HP Redline 100.0% HPAmber1ine 98.7% Time Delay 20 seconds TGT Transient TGT Limit 920"C TGT Redline 900"C TGTAmbertine 885"C Start Redline: - Ground Start -Airstart {Relight) - 700"C 850"C Time Delay 20 seconds OEM Provided Data Engine Control• Revision 13 2023..03-23 2A-78-00: 22 of 30 Signal Operating Limit value OilPressure OilPressure Low Red 25 psi OilPressure Low Amber Below 72.3% HP: Ground - 35 psid Flight- 25 psid Above 90% HP: Ground - 45 psid Flight- 35 psid 72.3% to 90% HP: Linear Fit Oil Temperature: Oil Temperature Upper Red 160°C OilTemperature L01Ner Red (1) -40°C Oil Temperature Lower Amber c1J 19°C c1i Refer to Engine Operating Instructions. Takeoff Power. Minimum acceptable power for takeoff is shown in AFM I Performance I Normal Takeoff Planning. Takeoff in the Alternate Control (LP) mode is prohibited. OEM Provided Data Engine Controls Revision 13 2023-03-23 2A-76-00: 23 of 30 Figura 3. Engine Thrust Management System OveNiew R.wf,..Mlfdl•no.I Stop -ldo -ldo- Throttle vs. TRA Angler Relatlonshlps l11-0035S4 OEM Provided Data Engine Control• Revision 13 2023.03-23 2A-78-00: 24 of 30 Figure 4. Power Lever I EEC Interface Simplified Block Diagram SEE DETAIL A FMU DETAIL A TIL-000595 OEM Provided Data Engine Controls Revision 13 2023-03-23 2A-76-00: 25 of 30 Figure 5. Alternate Control Mode Diagram Thrust (EPR or N1) -- EPR- norrjnal - - - - EPR- debited -Unrated N1 N1 Red Une MaxEPRor N1 command ------------------------------------------------------; --- •JEPR Debit / I I Reversa I Max N1 I Referance i------ ------------- ldla Approach Idle FlightIdle GroundIdle TRA@ Max RIM!ISll TRA@ Idle TRA @ Forward Idle TRA @ Max Forward TRA Note: 1.) In whichIdle Schedule the engine is running is determined by lcle Limfters and not by TRA posldon. 2.) EPR dabit will only be applied above kinkpoint temperatura with Cuslama" Bl-ion Air Data Fai uresr----------, Dual P50 Failure Piot Initialed Reversion DEP Rating Errors (DEP failure) Note: The EEC will check ror vertftcallon of 1he radngs structure. If this ched( tails the control wll revert to Alternate Control (Unrated N1) Mode. TIL-004680 OEM Provided Data Engine Control• Revision 13 2023-03-23 2A-78-00: 28 of 30 Figura 6. Autothrottle System Simplified Block Diagram POWER LEVER No.1 RVDT POWER LEVER No.2 RVDT AUTO lHROTTlE DlllCONNECT BUTION8 TRr.I NC INPUTS EPR i_ AUTOFLT SERVO MONITOR TRr.I COMMAND COMPUTERS lEPR l UJllTERS & COMMAND CONTROL lEEPPRRACCOT..U.A.L..O EPRMAX EPRIDLE LP HP ENGINER\J G AIRCRAFT ENGINES TIL-004681 OEM Provided Data Engine Controls Revision 13 2023-03-23 2A-76-00: 27 of 30 Figure 7. Power Lever Installation TAKEOFF I GO AROUND (TO/GA) SWITCH (2 PLACES) .._FWD-- AUTOTHROTTLE ENGAGE I DISENGAGE SWITCH (2 PLACES) TIL-003547 OEM Provided Data Engine Control• Revision 13 2023-03-23 2A-78-00: 28 of 30 llN'ETY INPUTII CONTROL INPUTS Figura 8. Rated And FLEX Takeoff Thrust Diagram CROeS - CHANNEL DATA CONTRa. INPUTS - CONTROL OIJ!l'UTII SAFETY INPUTII -----------ARFRAMEDATA.BU8ES TIL-000598 OEM Provided Data Engine Controls Revision 13 2023-03-23 2A-76-00: 29 of 30