Engine Company Operations (CFD) PDF
Document Details
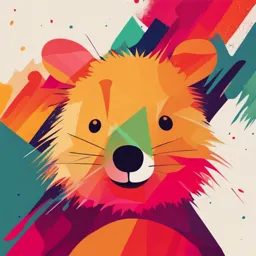
Uploaded by ProdigiousJasper737
Clark University
2025
Lt. Steve Chesshir
Tags
Summary
This manual is a guide for Columbus Firefighters (CFD) on engine company operations, covering equipment, procedures, and tactics. The second edition, adapted for 2025 CSC Fire promotional exams, includes diverse sections from experiences to skills. The manual offers practical knowledge, best practices, and SOPs for various firefighting scenarios.
Full Transcript
ENGINE COMPANY OPERATIONS A MANUAL FOR THE CFD FIREFIGHTER SECOND EDITION Adapted Version for the 2025 CSC Fire Promotional Exams Second Edition 01/31/22 ENGINE OPERATIONS UNDERSTANDING THE ENGINE COMPANY This manual was created to help guide Columbus Fi...
ENGINE COMPANY OPERATIONS A MANUAL FOR THE CFD FIREFIGHTER SECOND EDITION Adapted Version for the 2025 CSC Fire Promotional Exams Second Edition 01/31/22 ENGINE OPERATIONS UNDERSTANDING THE ENGINE COMPANY This manual was created to help guide Columbus Firefighters in their path to a better understanding of Engine Company Operations as they progress through their apprentice training. However, this book is not limited to apprenticeship training; it has been designed as a reference material for all members of the department. The information within this manual has been gathered from past experiences, manufacturer manuals, calculations, and previous training. The most important of these sources are the experiences shared by members of the Columbus Fire Department (CFD). Their successes and failures have been used to construct this manual to give all CFD members a better understanding of their role on the engine company. CFD Standard Operating Procedures (SOPs) pertaining to the engine company’s actions at fire scenes and other emergency scenes are very important, and you should familiarize yourselves with these SOPs. They are a guideline to aid your initial actions and help you work with other companies during an emergency response. It is important to understand that SOPs should be followed whenever possible. However, it is impossible to create an SOP for every situation you will encounter on this job. Some decisions must be guided by experience and what the situation presents to you. This manual has been organized into nine sections: Experiences, Equipment, Foam, General Considerations, Nozzle Options, Hose Line Deployment, Pump Operations, Elevated Master Streams, and Teach-Backs and Hands-On Skills. In the first section of this manual, you will find experiences shared by current and retired CFD members. These stories have been shared to allow you to learn from their experiences, good or bad, and to help you make your own decisions when the time comes. The fire service is an experience-based job; unfortunately, there is no substitute for experience. We should pay close attention to what others have learned as we strive to work hard and train day in and day out. The second section will cover the tools and equipment carried on the engine that is vital to the success of any operation. The equipment section is designed to help you become more familiar with the capabilities and limitations of your tools. CFD provides us with a great complement of resources and equipment. It is our responsibility to be proficient in their uses and capabilities. The third section will cover information about foam. Foam is not used on a daily basis, and because of that it can easily be forgotten. However, foam can be very helpful for fire attack and a variety of other tactics when needed. Placing foam products into operation takes special tools, equipment, and a knowledge base of how these things work together. Use this section to increase your understanding of when to use foam and how to successfully use it on the fireground. Second Edition 01/31/22 The fourth section will cover general considerations about apparatus positioning on roadway incidents. These incidents can be very dangerous for firefighters; it is important that apparatus drivers understand how to best position their vehicles to provide protection for firefighters operating at these emergency scenes. The fifth and sixth sections will cover the nozzle options, hose loads, and hose deployment techniques commonly used by CFD engine companies. One of the most important functions of the engine company is the successful deployment of initial and back-up attack lines. For this reason, you should become very familiar with the capabilities and limitations of each CFD hose load. Take time to understand the flow and pressure needed to properly supply and operate CFD nozzles. Work to know what hose line works best in certain situations. Ask yourself, is this the right nozzle for this size line? Is this an appropriate attack package? We are first and foremost a professional fire department. This is one of the main reasons we need to be better than just average at things like hose deployment. Quickly stretching the first attack line sets the tone for how the rest of the fire will go. If our initial line is quick and set in the right place, chances are high that we will be very successful at the emergency scene. To help you accomplish this goal, these sections show you how to best deploy basic types of CFD hose loads to aid you in faster and smoother stretches. The heart and soul of Engine Company Operations is the pump. For this reason, a section has been created to help you understand how our engine pumps work and what their limitations are. This section will cover the capacity, ratings, and parts of our fire pumps. Along with these basics, CFD firefighters should know how the Pump Boss pressure governor functions. The Pump Boss is a very helpful tool that can aid pump operators. However, understanding the Pump Boss settings and limitations are vital for becoming a proficient pump operator. This section will also discuss how the two-stage pump works, advantages and disadvantages of the pressure and volume modes, and when to use one or the other. Knowledge of water supply is needed when you are operating a fire pump. This section discusses information on supply lines and how they can be used in certain situations, why series pumping is beneficial to us, and when you should be setting up for bigger water. When acting as the pump operator, you are making decisions by yourself that could ultimately determine if we will be successful on an emergency scene. This responsibility handed to the pump operator should not be taken for granted, nor should it be taken lightly. It is our obligation as professional firefighters to become true pump operators, not just “lever pullers.” Next, this manual will cover supplying elevated master streams. Supplying ladder trucks is something that all pump operators should have a solid understanding of. When supplying these pieces of equipment, you will be required to use a greater volume of water than if you were supplying hand lines. This section is designed to add to your knowledge of how to make your connections, as well as the different types of flows you should expect from the different tip sizes. Second Edition 01/31/22 The final section contains both hands-on skill sheets and teach-back topics. These skills are not just for apprentice firefighters, but for the veteran firefighter as well. The practical hands-on skills required of the engine company firefighter will make or break any emergency scene. The basics like getting our gear on or operating a handline are the core foundation of what we do. As you transition from an apprentice to an experienced firefighter, you will need to teach the next generation of firefighters what you have picked up throughout your career. Doing live teach- backs to coworkers will help you prepare for this next step. Take time to prepare the material and conduct a class for your crew. This is an opportunity for you to practice, and for your crew to review some of the tools we carry. As you progress through your career in the fire service, it is important to stay proficient in these skills. Finally, it is important to understand that this manual is not written in stone. It can and will be changed as our department continues to learn new ideas and techniques. If there is something you do not understand, ask. One of the greatest things about CFD is the amazing people that can be found in the Division. Our membership is our most valuable resource. Please pass on what you have learned, as this is the life blood of the fire service. Respectfully, Lt. Steve Chesshir Second Edition 01/31/22 TABLE OF CONTENTS EXPERIENCE Experience Considerations – Lt. Steve Saksa 2 The Process – Ret. Capt. Jim Lewis 4 Reverse Lay – Lt. Steve Kerns 6 Outside of the Box – Capt. Steve Riley 8 It’s Your Engine…Train – Capt. Ian Garriott 9 Adapt and Attack – Lt. Steve Treinish 11 EQUIPMENT 904K Piercing Nozzle 13 Bresnan Distributor 14 Elkhart Brass R.A.M. XD 15 Mercury Quick Attack Monitor/MQA 16 Fire Extinguishers 17 Recharging Water Cans 18 FOAM Foam Reference 21 Task Force Tip PRO/Pak 22 Elkhart Brass Inline Eductor 23 GENERAL CONSIDERATIONS Apparatus Positioning on Roadways 25 NOZZLE OPTIONS Nozzle Overview 31 Smooth Bore Nozzles 32 2 ½” Smooth Bore Nozzles 33 Fixed Gallonage/Automatic Nozzles 34 Nozzle Construction 35 Nozzle Maintenance and Checks 36 Second Edition 01/31/22 HOSE LINE DEPLOYMENT Hose Deployment Overview 39 Reviewing the Basics 40 Hose Line Selection Considerations 43 Expectations for Medium and Large Diameter Handlines 44 Hose Loads 53 Building a 100’ Minuteman Bundle 55 Deploying a Modified Minuteman Load 59 Estimating the Stretch 63 Splitting Cars 64 Splitting the Door 69 Extending a Hose Line 72 Garden Stretches 75 PUMP OPERATIONS Pump Principles 81 Estimating Available Hydrant Flow 85 Understanding Supply: Advantages of a Series Supply 89 Driver Priorities and Supply Guidelines 94 Single-Stage vs. Two-Stage Pumps 97 FRC Pump Boss 400 Pressure Governor 102 Discharge Relief Valve 105 Intake Relief Valves 107 Back Flushing the Pump 111 Cold Weather Maintenance 116 ELEVATED MASTER STREAMS Tiller Master Streams 119 Platform Master Streams 121 TEACH-BACKS AND HANDS-ON SKILLS TB 1 – Extinguishers 124 TB 2 – Foam 125 TB 3 – General Pump Operations Knowledge 126 HO 1 – Back Flushing the Pump 127 HO 2 – Big Water: Maximizing a Hydrant 128 HO 3 – Handline Deployment 129 ACKNOWLEDGMENTS Second Edition 01/31/22 EQUIPMENT OVERVIEW ENGINE OPERATIONS MANUAL SECTION TOPICS Mercury Quick Attack 904K Piercing Nozzle Monitor/MQA Bresnan Distributor Fire Extinguishers Elkhart Brass R.A.M. XD Recharging Water Cans SECTION OBJECTIVES State the Piercing Nozzle’s basic Understand the tactical considerations operating pressure and flow rate when using the MQA State the Bresnan Distributor’s Identify all extinguishers carried on operating pressures and flow rates CFD engines Be able to place all specialty nozzles Explain the UL classification/rating for in service each extinguisher Identify tactical scenarios in which Explain the specifications for each each special nozzle could be used type of extinguisher Understand the flows and pressures Understand how to properly fill a water associated with the R.A.M can Understand the active safety system Identify the differences between a built into the R.A.M. normal water can and a Badger WP-61 State the pressure and flows for the Understand how to fill a Badger WP-61 Mercury Quick Attack water can Second Edition 01/31/22 12 904K PIERCING NOZZLE SPECIFICATIONS 904K – K refers to the built-in shut off valve 1.5” National standard threaded connection 1.25” diameter shaft Up to 25’ of coverage in all directions (2,500 square feet) Limited back pressure due to check mark piping Replaceable hardened steel tip Comprised of 1020 soft alloy steel (10 is iron, 20 is carbon) Nozzle only has to be driven in 3.75” to have full penetration of the sprayer head Removable safety strike handle Replaceable strike plate 24” extensions 175 GPM at 100 PSI USES Attic fires Basement fires Box truck or semi-truck fires Dumpster fires Car fires Hidden compartment fires Confined space fires OPERATION Completely assemble the nozzle with the desired number of extensions Attach a short section of hose and a shut-off (disregard if model K with built in shut-off) Locate the fire area and place the hardened tip on the exterior surface Drive the nozzle into the compartment and open the shut-off valve ADVANTAGES Safely extinguishes confined space fires Allows steam expansion to suppress the fire Limits structural damage due to a small opening DISADVANTAGES May need multiple firefighters to place it in service May hit hidden electrical or gas services within the structure when driven into the building Possible smoke explosions when introducing fresh air into starved air confined spaces Limited reach Click here to view Vector Solutions video on Using Piercing Nozzles with Aerial Ladders Second Edition 01/31/22 13 BRESNAN DISTRIBUTOR ELKHART BRASS MODEL Covers a 36’ diameter area when flowing 2 ½” female coupling Chrome plated finish Length—6.25” Weight—7.5 lbs. Nine outlets ranging in size from.5” to.625” 340 GPM at 50 PSI; 495 GPM at 100 PSI AKRON BRASS MODEL Covers a 14’ diameter area when flowing 2 ½” female coupling Length—5.125” Weight—4.5 lbs. Nine variable angle orifices—three 3/8” and six 13/32” 250 GPM at 100 PSI EXAMPLES OF USE Basement fires Attic fires Limited access fires (such as warehouses with high rack storage) PLACING IN SERVICE Inspect for cleanliness and obvious damage Attach a short section of hose with a 2 ½” shut off device (ball valve) Select a location directly above the fire and cut a hole approximately 12”x12” Lower the nozzle down one to two feet below the opening to clear the joist or rafter INDIRECT ATTACK VS DIRECT ATTACK Indirect Attack—Extinguishing fire by converting the water to steam and using heat absorption to cool the environment. This allows an attack team to follow up with a direct interior attack and place water on the remaining burning material Direct Attack—Applying water directly to the fire and using water, steam, and thermal disruption to extinguish the fire ADVANTAGES Makes the job easier for the entry team Coarse water droplets absorb more heat than solid streams DISADVANTAGES May conduct electricity (not Class C compatible) Limited stream reach; must be set up directly over the hazardous fire compartment Second Edition 01/31/22 14 ELKHART BRASS R.A.M. XD SPECIFICATIONS Has a patent pending hydraulic stability system that harnesses the reaction force to stabilize the RAM Has four fold-out aluminum forged legs with carbide tipped ground spikes (Rear ground spikes are angled to help with grip) Locking pin holds valve in a closed position to prevent accidental opening (allows RAM to be carried while attached to a charged hose line) Attached safety strap comes with a storage pouch Has a 2 ½” inlet and outlet Has 20 of travel left and right from center Click here to view Brass Tacks and Can be set from 51 to 35 while unmanned Hard Facts video on the R.A.M Can be lowered from 35 down to 14 when manned PRESSURE AND FLOW Operation is not to exceed 500 GPM and/or 150 psi Comes with 1 3/8” deluge tip 1 3/8” deluge tip = 505 GPM at 80 psi NP (55 lbs of friction loss per 100’) To achieve optimal flow, ensure there is 20 feet of hose in a straight line behind the RAM 9.5 lbs of friction loss within the RAM when flowed at 500 GPM ACTIVE SAFETY SYSTEM The RAM XD has a built-in safety system with an upper and lower pivot point. The offset configuration of the two pivot points creates a condition where the reaction force of the water acting upon the upper pivot point (if sufficient enough) will cause the nozzle to rotate upward about the lower pivot point This produces a self-correcting increase in nozzle angle to protect against possibly dangerous unmanned use of the monitor at nozzle angles less than 35 above horizontal The hydraulic effect of the system is active at approximately 350 GPM Second Edition 01/31/22 15 MERCURY QUICK ATTACK MONITOR/MQA SPECIFICATIONS AND PERFORMANCE Rated for flows up to 500 GPM Only 6 PSI friction loss through the unit at 500 GPM Tip can rotate 20 left or right from center Can be operated from 60 to 30 when unmanned Top handle contains a spring- loaded mechanism that allows the user to travel down to 20 (will self-adjust back to 30) PRESSURE AND FLOW Generally comes with triple stacked tips 1” = 266 GPM at 80 psi nozzle pressure (15 lbs of FL per 100’) 1-1/8” = 336 GPM at 80 psi nozzle pressure (25 lbs of FL per 100’) 1-1/4” = 415 GPM at 80 psi nozzle pressure (38 lbs of FL per 100’). With the 1-1/4” tip, over pumping the MQA to 115 psi nozzle pressure is an option. Doing so results in the max rated flow of 498 GPM 1-3/8” = 502 GPM at 80 psi nozzle pressure (55 lbs of FL per 100’) Some models may have 1-1/2” deluge tip on them (shown above) 1-1/2” = 496 GPM at 55 psi nozzle pressure (55 lbs of FL per 100’)* *This tip must be pumped at or below 55 psi nozzle pressure. Higher pressures would exceed the GPM rating of the MQA and 2-1/2” hose TACTICAL CONSIDERATIONS Most companies will forgo running the 1” tip on the end of the MQA The 1” tip provides no GPM advantage over a 1-1/8” tip at 50 psi on a handline The MQA has a 2-1/2” inlet and outlet Hoselines can be extended from the MQA after initial knockdown for clean-up and hot spots o A 1-3/4” hoseline can be connected to the end of the 1-1/4” stacked tip o MQA 2-1/2” outlet allows for a 2-1/2” attack line to be extended off the outlet base of the unit Second Edition 01/31/22 16 FIRE EXTINGUISHERS WATER CAN Also called “the can” or “pw can” (pressurized water) Common model is the Amerex 240 H (shown on the right) The UL (Underwriters Laboratories) Classification/Rating System is a water equivalency rating; this model has a 2A rating Each A = 1.25 gallons (2A = 2.5, 3A = 3.75, etc.) Intended for Class A fires Six year warranty Polished stainless-steel construction 2.5 gallon capacity (7.5 lbs. empty; roughly 28.3 lbs. full) Max effective range is 44-55 feet with a 55 second discharge time DRY CHEMICAL EXTINGUISHER Common model is the Ansul Sentry 10 (shown on the right) Has Class A:B:C capabilities Use caution with certain electrical equipment; the powder is corrosive Use caution in small/contained areas; the powder is an irritant UL rating comes with two different ratings: 10-A:60-B:C 10-A means the agent is as effective as 12.5 gallons of water 60-B:C is equivalent to the square footage an operator can extinguish; 60-B:C means it will cover 60 square feet 10 lbs. of extinguishing agent (17 lb. weight total) Max effective range is 19 feet with a 21 second discharge time After use, can be exchanged at Tools and Equipment Should be inspected yearly; check the inspection tag CO2 EXTINGUISHER Common model is the Badger B10V-1 (shown on the right) Class B:C capabilities; ideal for sensitive electrical equipment because it leaves no residue behind UL Rating is the square footage that an operator can extinguish; 10-B:C means it will cover 10 square feet Note the lack of a pressure gauge; operating pressure is 850 psi Max effective range is 3-8 feet with a ten second discharge time. The reach is greatly affected by any wind or air movement Five year hydrostatic test interval; six year warranty After use, can be exchanged at Tools and Equipment Should be inspected yearly; check the inspection tag Second Edition 01/31/22 17 RECHARGING WATER CANS AMEREX 240 H WATER CAN 1) The water can should be filled any time it is discharged. The pressure gauge should be inspected daily to ensure that there has not been an undetected leak, or that the extinguisher was not recharged after previous use. 2) Ensure that the extinguisher is fully depressurized prior to removing the valve assembly. 3) The extinguisher can be depressurized via normal operation of the discharge handle (discharging both air and the water), or by inverting the extinguisher and operating the discharge handle (air and the contents within the pickup tube). 4) Remove the valve assembly and pickup tube by unscrewing the valve collar nut. 5) Prior to filling the extinguisher, rinse the unit with clean water to remove any residue that may be left over from foam/soap. Filling the unit without rinsing can lead to excessive foaming, giving a false indication through the fill tube that the unit is full. 6) When filling the extinguisher, ensure the plastic fill tube is in place. The extinguisher is full once the water overflows from the top of the fill tube. 7) Once the extinguisher is full, remove the fill tube. An additive can then be added to the extinguisher. This can either be Class A Foam concentrate or normal dish soap. A few ounces of additive should be sufficient (about 1 cup). Soap will not have the blanket effect like Class A foam, but it will still reduce the surface tension in the water to allow for better “wetting” of Class A materials. Second Edition 01/31/22 18 8) Replace the fill tube and valve assembly. The locking collar only needs to be installed hand tight. Using a wrench can cause overtightening and damage the collar and valve assembly. 9) Use the Schrader valve to pressurize the extinguisher until the gauge reads 100 psi; over pressurizing can cause the valve assembly to fail (eye protection is recommended). Be sure not to rely solely on the pressure gauge when inspecting the extinguisher during morning checks. There may be times the extinguisher has adequate air pressure, but contains less than the rated 2.5 gallons of water. Pull the extinguisher from the bracket to feel its weight (roughly 28 lbs. full). If in doubt about the extinguisher’s water level, depressurize it and fill it. BADGER WP-61 The Badger model of extinguisher can only be filled via the nozzle. This model can be identified by the lack of a Schrader valve opposite the pressure gauge. These extinguishers require the firefighter to hold the fill line onto the nozzle of the extinguisher to keep it from detaching while pressurizing. For air to enter into the extinguisher, the firefighter will also have to open the water can’s discharge handle. Firefighters must remember to release the discharge handle prior to detaching the air hose! Second Edition 01/31/22 19 FOAM OVERVIEW ENGINE OPERATIONS MANUAL SECTION TOPICS Foam Reference Elkhart Brass Inline Eductor Task Force Tip PRO/Pak SECTION OBJECTIVES Understand different classifications of Understand basic operating pressures foam concentrates and flow rates for the PRO/Pak Understand the operating ranges of Demonstrate how to clean the Class A and Class B Foam PRO/Pak after use Understand the difference between Understand the dangers of mixing Polar Solvents and Hydrocarbons different types of Foam concentrate Understand basic Foam Operations Identify all the components of the and how to troubleshoot problems inline eductor Understand situations in which Class Understand the pressure needed for A and Class B Foam should be used the 95 GPM and 125 GPM eductors Successfully identify all parts of the State the maximum hose lengths that PRO/Pak can be used with each eductor Discuss tactical considerations for the Understand how to operate the inline PRO/Pak eductor Second Edition 01/31/22 20 FOAM REFERENCE TYPES OF FOAM Class A Foam Class B Foam o Older Class B Foam will be in the 3-6% range; newer Class B Foam will be in the 1- 3% range CFD foam has a nearly unlimited shelf life when left in sealed containers Foam carried on engines comes in 5-gallon pails EXAMPLE OF CLASS A USE Ordinary combustible materials, such as overhaul at a house fire (.1 – 1%) Recommended application rates: o Air Aspirating Nozzle (PRO/Pak low and medium nozzles): 0.3-0.5% o Non-Air Aspirating Nozzle (SM-20FLP): 0.3-0.6% EXAMPLE OF CLASS B USE Fuel spills and vehicle fires Recommended application rates: o Hydrocarbons, such as gasoline or diesel, do not mix with water; they float on top. A 3% application rate is recommended o Polar solvents, such as alcohol base or acetone, do mix with water. A 6% application rate is recommended TROUBLE SHOOTING FOAM OPERATIONS Excessive back pressure in the foam system is the most common cause of eductor failure. This can be caused by any of the following: o Kinks in the hose line o Nozzle elevated too high above the eductor o Too much hose between the eductor and the nozzle o Nozzle clogged or not fully opened; clogged pickup tube o Nozzle GPM does not match the eductor GPM o Pressure at eductor is too low (Elkhart inline eductor=200 psi; PRO/Pak=100 psi) o Poor maintenance leading to a clogged control unit or stuck check valve ball Second Edition 01/31/22 21 TASK FORCE TIP PRO/PAK COMPONENTS Control Unit Percentage Knob Pull Pins Twist Grip Flow Control Tank (2.5 Gallons) Outlet Hose (2.7’ long) Straight Stream Nozzle – 50’ Reach Low Expansion Nozzle – 37’ Reach Medium Expansion Nozzle – 9’ Reach Tank Fill Cap Selector Wheel PRESSURE AND FLOW Minimum pressure – 40 PSI (7 GPM); maximum pressure – 500 PSI (27 GPM) Recommended pressure – 100 PSI at the PRO/Pak (12 GPM) CLASS A USE Ordinary combustible materials, such as mop-up and overhaul operations. The recommended percentage knob setting for Class A operations ranges from 0.1% – 1% CLASS B USE Fuel spills and vehicle fires Hydrocarbons (gasoline, diesel) are fuels that are mostly distilled from crude oil or vegetable matter. Hydrocarbons do not mix with water; they float on top. The recommended percentage knob setting for hydrocarbons is 3% Polar solvents (alcohol base, amines, acetone, ethers, esters, ketones) do mix with water. The recommended percentage knob setting for polar solvents is 6% PRO/PAK ASSEMBLY Attach fire hose to the coupling on the inlet side of the PRO/Pak Connect the outlet hose to the control unit Select the appropriate nozzle and connect it to the outlet hose CLEANING AFTER USE Reduce pump pressure to 100 PSI or less. Remove the nozzle and hose from the unit Remove the two pull pins, then pull straight up to remove the control unit from the tank Install the cap on the outlet of the control unit Turn flow control valve until a trickle of clean water flows out the end of the pickup tube Turn the percentage knob back and forth to make sure all foam passages are flushed Shut off the water, reinstall the control unit on the tank, and insert the pull pins Remove the cap Second Edition 01/31/22 22 ELKHART BRASS INLINE EDUCTOR COMPONENTS Pick Up Tube Metering Device PRESSURE AND FLOW 200 PSI required at the eductor The 95 GPM eductor should be used with a SM20-FLP nozzle. The max length of 1 ¾” hose that can be used between this eductor and the nozzle is 400’ The 125 GPM eductor should be used with a SM20-FLP nozzle. The max length of 1 ¾” hose that can be used between this eductor and the nozzle is 200’ CLASS A USE Ordinary combustible materials, such as mop-up and overhaul operations. The recommended percentage knob setting for Class A operations ranges from 0.1% – 1% CLASS B USE Fuel spills and vehicle fires Hydrocarbons (gasoline, diesel) are fuels that are mostly distilled from crude oil or vegetable matter. Hydrocarbons do not mix with water; they float on top. The recommended percentage knob setting for hydrocarbons is 3% Polar solvents (alcohol base, amines, acetone, ethers, esters, ketones) do mix with water. The recommended percentage knob setting for polar solvents is 6% EDUCTOR OPERATION Select the appropriate foam concentrate for the burning fuel Place the foam concentrate by the eductor Open enough foam concentrate to handle the task, and request more if needed Check the eductor and nozzle for compatibility as listed above Adjust the eductor metering valve to the desired percentage Attach the eductor to a hose capable of effectively flowing the rated capacity of the eductor and nozzle Attach the attack line and the appropriate nozzle to the discharge side of the eductor; see above restrictions on hose length between the eductor and the nozzle Place the eductor pick up tube into the foam concentrate and charge the hose line to the appropriate pressure (200 PSI at the eductor) Second Edition 01/31/22 23 GENERAL CONSIDERATIONS ENGINE OPERATIONS MANUAL SECTION TOPICS Apparatus Positioning on Roadways SECTION OBJECTIVES Understand the differing goals of law Understand the safety precautions that enforcement vs. the fire service while should be taken during pump operating at auto accident scenes operations on roadway incidents Understand size-up considerations for Understand how to use fire apparatus scenes on roadways as a blocker on roadway incidents Understand how road and weather Understand the role of the State Farm conditions can affect roadway Blockers and know what radio channel incidents to contact them on Identify optimal apparatus placement Understand how to position fire on wires down runs, EMS runs, and apparatus on working extrications to when checking hydrants provide room for Rescues Second Edition 01/31/22 24 APPARATUS POSITIONING ON ROADWAYS OVERVIEW Although fires may be predictable, people are anything but. What do you get when you cross the iPhone era with a full-size SUV? A mass of traveling steel that can weigh upwards of 5,000 pounds with an operator who may be distracted by conversations, texting, movies, or even the warning lights on the apparatus. It is absolutely a risk of life and limb to operate around moving traffic, and it scares many firefighters more than any fire they might face. There is no more ill-at-ease feeling for firefighters than trying E-2 was on the scene of a freeway accident when three to extricate a patient with traffic cars in oncoming traffic got into another accident. One rushing by a few inches away, and vehicle ended up this close to the bumper of E-2. there is no excuse for it. One aspect often discussed about working auto accident scenes is the different goals of law enforcement and the fire service, especially on freeways or during heavier traffic conditions. Law enforcement’s general goal is to get traffic moving again to reduce future travel impacts to drivers. While many auto accidents can be moved to a relatively safer location such as the median or other spaces away from the heaviest and fastest traffic flows, this presents two problems. One—a median is not a safe space, especially in slick conditions. Traffic still rushes by, drivers are still distracted, and there are usually only inches separating stationary vehicles from speeding vehicles. Two— emergency crews often are the first arriving companies and have other duties such as size-up, triage, extrication, packaging, and securing the vehicles before being able to move them, if they can be A CPD cruiser after being hit by a vehicle while stopped moved at all. on the side of a freeway to assist a stranded motorist. Second Edition 01/31/22 25 SIZE-UP A good size-up on any accident run starts with giving good consideration to the location, conditions, caller information, and any known hazards such as blind curves and frequent accident locations. Firefighters should also consider how to stage their apparatus best to protect their crews on arrival. Generally, the goal is to keep all personnel in the same safe area, preventing crews from crossing lanes of traffic on foot, and utilizing the bigger trucks as blocking apparatus. ROAD, WEATHER, AND DRIVER CONDITIONS Slick conditions such as rain, snow, and ice all cause both initial and resulting accidents, and these conditions also cause stopping distances to increase for all vehicles. However, even during warm, dry nights, a black vehicle on a poorly lit road may surprise many crews. How many freeway runs has the actual location matched the reported location? Not many. Realizing this and slowing a bit when approaching the dispatched area may help prevent a catastrophe. Good radio communications with other incoming companies can also help with an efficient and safe search for the wreck itself. While the 02:30 am freeway run could be the drunk driver trying to get home after last call, today’s society can have drivers impaired at any time. Many drivers will exhibit a “me first” attitude and will either not reduce speed enough or not reduce it at all. Mechanical issues with a vehicle, such as poorly maintained brakes, might not allow a driver to stop in time to keep from hitting firefighters or apparatus. Also, the driver that swerves around a large truck only to hit the gas may find himself speeding right up into an emergency scene. A driver’s experience or state of mind might also factor into things as new drivers might panic, and older drivers may not see as well or process information as well as when they were younger. Stacking the deck in favor of our safety is paramount, not just during auto accidents, but other times as well. Not only do we possess large, heavy fire apparatus with warning lights all around it, we can place the apparatus very deliberately to protect our firefighters while they work. In addition, CFD also has plenty of apparatus, including some that can almost block an entire freeway by itself. AUTO ACCIDENTS Obviously the most contact firefighters will have with moving vehicles is on our streets and highways. The highway speeds now common will play a huge factor in how to place our apparatus. Out of control vehicles can travel hundreds of yards once a driver reacts, and that assumes the driver will react. FREEWAYS An engine company always has to prioritize safety during freeway runs. Engines can generally be placed behind the accident to be used as a blocker, creating a physical barrier that will hopefully take the brunt of the collision if a vehicle strikes it. One aspect to consider is the task of placing an attack line in service if needed. Smaller scenes may allow the bumper line for this, but using the 200’ 1 ¾” line allows more space between the vehicle and the engine, creating the buffer Second Edition 01/31/22 26 zone. Use caution when pulling a pre-connect off the rear where crews are directly exposed to oncoming traffic. Angling the engine can also allow a deflection of sorts should another vehicle strike the engine, but be aware of the pump operator being exposed to traffic. It may be much safer for the pump operator to “set it and forget it” when the pump needs to be used; the pump operator can then take a place of safety ahead of the scene. This positioning also allows the medic units to park in front of the wreckage, creating an easy exit if transporting. Rescues can park beside or slightly ahead of the wreckage, allowing good access for tools and lighting in case of an extrication. Battalion Chiefs and EMS/Rescue Supervisors may park ahead of the wreckage out of the way when possible. Parking a buggy behind an engine puts a smaller, lighter car in a bad spot, and it also requires the firefighter to walk forward to the engine, increasing risk. Once the engine is positioned for firefighters’ protection, it is recommended the engine stays in place, even on non-injury accidents, until the accident site is rendered safe for our personnel to leave. STATE FARM BLOCKERS The Ohio Department of Transportation often works with sponsor companies to fund and staff freeway assistance vehicles. These vehicles are staffed by operators that have large signs to warn and block traffic, traffic cones to physically create lane barriers, and they even have some towing capabilities. These vehicles are invaluable; they will generally create barriers behind CFD apparatus, making a much safer scene overall. They are controlled and dispatched by a worker that monitors several dozen cameras, giving a good remote view of a scene. Contacting these dispatchers can help narrow down a confusing location if firefighters are having trouble finding an accident scene. Even before firefighters arrive on scene, they can request the freeway assistance trucks be dispatched. These dispatchers can be contacted on 9 D06-FSP, one click past 9 Police Fire. Second Edition 01/31/22 27 OTHER VEHICLES Ladder trucks respond on many freeway responses as extrication companies. Even if a ladder is not assigned, consider calling one if needed. The length of the ladder apparatus can provide a significant barrier for protection. Detailed instructions and directions may be needed to place the ladder where needed to create an effective buffer zone. In a pinch, and if it can be done safely, other vehicles can also be used. Semi-trucks or large box trucks can be used to create barriers. Many professional drivers are sympathetic to the risk firefighters face, and they may readily assist when asked. SMALLER ROADS Smaller roads also create hazards for the same reasons mentioned previously. These scenes can actually be worse due to traffic moving in different directions and/or speeds. Sizing up a scene to create protection can be done in the same manner as freeway responses, but more specific radio instructions on apparatus placement will likely be needed. EMS RUNS On ALS medic runs, firefighters can often place the engine in a position to protect the crew. Just like the rescue technician feeling spooked working close by moving traffic, medic crews often find themselves loading patients while the rear of the medic unit is exposed to traffic passing by. This is especially an issue downtown or on busier streets. While many crews may put the engine in front of the medic to make leaving easier, positioning the engine behind the medic offers greater protection to mitigate the traffic risk. OTHER CONSIDERATIONS A Wires Down run may not be one that crews consider a traffic risk, but it can easily place crews in traffic as they investigate. Crews are at additional risk if a vehicle strikes a pole or downed wire. Blocking the roadway the proper distance away and calling for other apparatus to block from other directions as needed is key. In fact, any other instance where firefighters are exposed to traffic, such as checking hydrants, will benefit from a smart position that minimizes the risk of being hit. Second Edition 01/31/22 28 PAGE LEFT BLANK FOR DOUBLE SIDED PRINTING Second Edition 01/31/22 29 NOZZLE OPTIONS OVERVIEW ENGINE OPERATIONS MANUAL SECTION TOPICS Nozzle Overview Fixed Gallonage/Automatic Nozzles Smooth Bore Nozzles Nozzle Construction 2 ½” Smooth Bore Nozzles Nozzle Maintenance and Checks SECTION OBJECTIVES Correctly identify basic CFD nozzles State the pressure and flow for all and their components combination nozzles Define Nozzle Pressure, Nozzle Understand the SM20FLP Select-O- Reaction, and Flow Matic nozzle and its characteristics State the pressure and flow for each Understand the difference between a smooth bore tip size full round ball and a double cut ball Understand how to identify an Understand basic station level integrated tip in a shutoff maintenance for all nozzle types Second Edition 01/31/22 30 NOZZLE OVERVIEW OVERVIEW CFD carries both Elkhart Chief and Chief XD series nozzles Most engines 2019 and newer are equipped with Chief XD nozzles This section will discuss nozzle components, nozzle maintenance, pressures, and flows ELKHART CHIEF NOZZLE Standard double cut ball shutoff construction; some newer models will have full round 1 ¾” internal shutoff Nozzles (most) come with integrated smooth bore tips ELKHART CHIEF XD NOZZLE Standard full round ball shutoff construction 1 ¾” internal shutoff Laser etched labeling Does not have integrated tips Tapered smooth bore tips Click here to view Brass Tacks and Hard Facts video on the new Chief XD series TERMINOLOGY Nozzle Pressure – the pressure required at the nozzle to achieve the designed flow o Smooth bore hand line nozzles are designed to be flowed at 50 PSI at the nozzle o Nozzle pressure for combination and automatic nozzles will vary Nozzle Reaction – the force (measured in pounds) exerted from the discharge of water out of a nozzle back at the nozzle firefighter while the hand line is flowing Flow – quantity of water measured in gallons per minute (GPM) Click here to view Brass Tacks and Hard Facts video on Nozzle Reaction ATTACK HANDLINE CONSIDERATIONS Flow – Target a flow rate of 150 GPM minimum for initial interior residential attack lines Reaction – It is important to understand that there is a direct correlation between the amount of water flowed through a hand line and the nozzle reaction it produces. The more water is flowed, the more reaction is created. Flow less water, and nozzle reaction will decrease Stream – Nozzles must be pumped at the appropriate pressures to maintain reach and penetration of the attack stream FREEMAN PRINCIPLE – SMOOTH BORE This principle states that when selecting a nozzle and hose to build an attack package, the orifice of the nozzle should ideally not be greater than half the diameter of the hose This helps maintain the optimal exit velocity of the stream, which ensures the adequate reach and penetration needed for fire attack is obtained Click here to view Brass Tacks and Hard Facts video on the Freeman Principle Second Edition 01/31/22 31 SMOOTH BORE NOZZLES OVERVIEW Smooth bore nozzle options vary depending on the year the engine was purchased CFD smooth bore nozzles are designed to operate at 50 PSI nozzle pressure in most cases Pump operators must understand that overpumping or underpumping a hand line has repercussions for flow and nozzle reaction Nozzle Pressure Flow (GPM) Nozzle Reaction (lbs) 7/8” Tip 40 144 48 Smooth Bore 50 160 59 60 176 71 Nozzle Pressure Flow (GPM) Nozzle Reaction (lbs) 15/16” Tip 40 165 55 Smooth Bore 50 185 68 60 202 82 Nozzle Pressure Flow (GPM) Nozzle Reaction (lbs) 1” Tip 40 188 62 Smooth Bore 50 210 78 60 230 93 Nozzle Pressure Flow (GPM) Nozzle Reaction (lbs) 1 1/16” Tip 40 212 69 Smooth Bore 50 240 87 60 259 104 Nozzle Pressure Flow (GPM) Nozzle Reaction (lbs) 1 1/8” Tip 40 238 79 Smooth Bore 50 266 98 60 291 118 Nozzle Pressure Flow (GPM) Nozzle Reaction (lbs) 1 3/16” Tip 40 265 85 Smooth Bore 50 296 109 60 324 131 Nozzle Pressure Flow (GPM) Nozzle Reaction (lbs) 1 1/4” Tip 40 293 97 Smooth Bore 50 328 121 60 360 145 Second Edition 01/31/22 32 2 ½” SMOOTH BORE NOZZLES 2 ½” ELKHART BRASS XD SHUTOFF Newer style found on most engines purchased after 2019 Dual drive shutoff with full round metal ball Forged aluminum shutoff body and bale handle Under or over pumping will have repercussions for flow and nozzle reaction in either direction Does not have an integrated tip; it is just a shutoff ELKHART BRASS TIP SIZES 188XD Smooth Bore 1 1/8” Single Tip Lightweight aluminum construction Orange urethane molded bumper 266 GPM at 50 PSI NP (98 lbs nozzle reaction) 188XD Smooth Bore 1 3/16” Single Tip Lightweight aluminum construction Orange urethane molded bumper Can be pumped at a range of pressures based on the desired GPM and nozzle reaction 265 GPM at 40 PSI NP (85 lbs nozzle reaction) 296 GPM at 50 PSI NP (109 lbs nozzle reaction) 324 GPM at 60 PSI NP (131 lbs nozzle reaction) Click to view Brass Tacks and Hard Facts video on Pumping the 1 3/16" Tip at Various Pressures 2 ½” ELKHART DB-375-GAT SHUTOFF Forged aluminum body with a pistol grip 1 ¼” integrated discharge has 328 GPM at 50 PSI NP (121 lbs nozzle reaction) Older style nozzle generally found on engines purchased prior to 2019 ELKHART ST-185-AIFD “INDY STACK” Indy Stack- 1 1/8” and 1 ¼” stacked tips Rubber bumper on 1 ¼” tip to protect threads 1 1/8” tip = 266 GPM at 50 PSI NP 1 ¼” tip = 328 GPM at 50 PSI NP Can change tip size to achieve the desired GPM Second Edition 01/31/22 33 FIXED GALLONAGE/AUTOMATIC NOZZLES OVERVIEW Combination nozzle options will vary depending on the year the engine was purchased CFD combination nozzles are designed to be operated at a variety of pressures Pump operators must understand that overpumping or underpumping a hand line has repercussions for flow and nozzle reaction Nozzle Pressure Flow (GPM) Nozzle Reaction (lbs) 160/50 40 143 51 Combination Nozzle 50 160 57 75 196 69 Nozzle Pressure Flow (GPM) Nozzle Reaction (lbs) 175/75 50 143 63 Combination Nozzle 75 175 77 100 202 88 Nozzle Pressure Flow (GPM) Nozzle Reaction (lbs) 200/75 50 163 71 Combination Nozzle 75 200 88 100 231 101 Nozzle Pressure Flow (GPM) Nozzle Reaction (lbs) 250/50 40 224 89 Combination Nozzle 50 250 109 75 306 126 Nozzle Pressure Flow (GPM) Nozzle Reaction (lbs) SM20-FLP 60 67 26 Select-O-Matic 70 156 65 Automatic Nozzle 75 204 89 SM20-FLP/SELECT-O-MATIC It is important to understand that the ratio between nozzle pressure and flow is not a simple 1:1 ratio for this nozzle The more water that is flowed, the more the spring must be compressed to allow the increased quantity of water to be discharged. As the spring reaches full compression, the forces required to do so are very high. This creates an exponential growth regarding nozzle reaction and GPM as pressure is increased Pumping trash lines at higher pressures provides limited benefits, and it causes extreme workloads on operating crews. If more water is needed, pull a more appropriate attack line instead of over pumping a trash line Click here to view Brass Tacks and Hard Facts video on the Select-O-Matic Nozzle Second Edition 01/31/22 34 NOZZLE CONSTRUCTION TYPES OF SHUTOFFS Double Cut Ball Designed to allow the flow of water to assist with opening/closing the nozzle bale Creates turbulence within smooth bore nozzles and reduces the attack stream quality Less of a factor in combination nozzles The arrow indicates the double cut ball shutoff in the Elkhart Brass schematic on the right Full Round Ball Creates a smooth discharge orifice which produces a tighter stream with less turbulence This type of shutoff is preferred for smooth bore nozzles The arrow indicates the full round ball shutoff in the Elkhart Brass schematic on the right Click to view Brass Tacks and Hard Facts video on Full Round vs. Double Cut Ball Shutoffs INTEGRATED TIPS One key difference between the Elkhart Chief nozzles and the Chief XD is the lack of an integrated tip in the Chief XD nozzles An integrated tip can be identified by the beveled machined edge on the inner face of the nozzle discharge orifice. There will also be a laser etched discharge size on top of the nozzle shutoff These tips create turbulence in the stream when additional tips are screwed on the end Notice the slight offset between the arrows. This indicates there is an integrated tip. The discharge size will be laser etched on it. Second Edition 01/31/22 35 NOZZLE MAINTENANCE AND CHECKS MONDAY CHECKS All nozzles exposed to dirt, debris, road grime, etc. should be cleaned frequently. The nozzle is the primary weapon for fire attack, and it must be taken care of Inspect the nozzle for overall cleanliness and any obvious defects Check the bumper and teeth (combination nozzle) to make sure there is no obvious damage; check to make sure no teeth are missing or loose o Damaged teeth can be replaced by removing two allen screws and replacing the damaged tooth ring with a new one from Tools and Equipment Inspect the swivel to make sure it spins freely; inspect the gasket Soak the nozzle in warm water and mild degreaser (Simple Green or Dawn). Elkhart states that using warm water and mild degreaser is sufficient in MOST cases to remove dirt and debris within the nozzle, bale, bumper, and swivel While moving the nozzle in and out of the warm water/degreaser mixture, cycle the nozzle bumper through all ranges of motion (flush to straight stream). Open and close the bale to loosen and remove any dirt buildup After cleaning, dry the nozzle using a rag. Use lubrication per manufacturer guidelines; it must be a silicone-based lubricant. Only use a minimum amount of lubricant; any type of excess grease can attract dirt and grit, which can interfere with the moving nozzle parts Dow-Corning #7 lubricant is the recommended lubricant per the operating manual Click here to view Brass Tacks and Hard Facts video on Nozzle Maintenance ADDITIONAL MAINTENANCE Over time, dirt and grime can gunk up bearings causing nozzles not to swivel. This is NOT normal station level maintenance and should not be done on your own; refer to your senior engineer for their guidance if basic nozzle maintenance does not resolve the issue Used in extreme cases when nozzles are stiff and the swivels are hard to move The ball bearings can be removed carefully, placed on a towel, and cleaned with Simple Green. The bearings can be removed by removing the Allen set screw on the female swivel Second Edition 01/31/22 36 PAGE LEFT BLANK FOR DOUBLE SIDED PRINTING Second Edition 01/31/22 37 HOSE LINE DEPLOYMENT ENGINE OPERATIONS MANUAL SECTION TOPICS Deploying a Modified Minuteman Hose Deployment Overview Load Reviewing the Basics Estimating the Stretch Hose Line Selection Splitting Cars Considerations Expectations for Medium and Splitting the Door Large Diameter Handlines Hose Loads Extending a Hose Line Building a 100’ Minuteman Bundle Garden Stretches SECTION OBJECTIVES Understand firefighter positioning for Understand how to properly split cars basic hose advancement using the Minuteman hose load Define the ADULTS acronym and Understand the importance and understand how it can be used tactical benefits of splitting the door Identify common CFD hose loads and Understand the general guidelines to understand the benefits of each follow when extending hose lines Understand how to build a 100’ bundle Understand how to perform a garden for a Minuteman load stretch Understand how to deploy a Understand how to vertical stretch by Minuteman load using a back stretch, dropping the bundle down or doing a forward stretch, or split stretch hook stretch Know the formula for estimating hose Understand the expectations for stretches medium and large diameter handlines Second Edition 01/31/22 38 HOSE DEPLOYMENT OVERVIEW OVERVIEW The following section is a brief overview of CFD attack line packages and techniques It is crucial to understand that deployment packages, techniques, and communication will differ around the city. However, a basic understanding of position assignments and fundamentals should be universal throughout the city The basics will be reviewed not only as a refresher for new firefighters, but also to help senior firefighters and officers understand what is being taught at a recruit level The goal is for apprentice firefighters to build on the fundamental knowledge they obtained in the recruit training academy This section is not an all-encompassing manual about hose deployment. Hose loads and deployment techniques are specific to each engine company. All firefighters must be familiar with the hose loads on their engines and how to deploy them CONTENTS Reviewing the Basics Hose Line Selection Considerations Expectations for Medium and Large Diameter Handlines Hose Loads Building a 100’ Minuteman Bundle Deploying a Modified Minuteman Load Estimating the Stretch Splitting Cars Splitting the Door Extending a Hose Line Garden Stretch Second Edition 01/31/22 39 REVIEWING THE BASICS OVERVIEW From the beginning of water week in the TA, it is emphasized to the recruits that hose advancement is about teamwork and communication Slow is smooth and smooth is fast – hose lines must be advanced as a team to be efficiently stretched to the seat of a fire Moving in as fast as possible and pulling the hose tight on a friction point only makes the stretch harder in the long run. Patience and moving at a good pace are a necessity Once inside the structure, recruits will use the following three phases: o Moving Up—used any time the recruits are moving around a pinch point. This signals the next person on the line to bring hose and move up to that pinch point o Fire Room—used when the nozzle firefighter has reached the fire room. This signals everyone inside the structure that water will soon be applied to the fire o I Need ___ Feet—used when more hose is needed. Recruits will request a certain number of feet required to make the stretch instead of yelling “more hose.” This helps members of the hose team determine if they have enough hose pre-loaded in the building, or if they need to go back out and get more While advancing the line, the nozzle firefighter will state these commands out loud; every person on the line will relay the command back to the next person The section below will describe each hose team position A—ATTACK Consists of the firefighter positioned on the nozzle Responsible for pulling and flaking out the hose line Brings the first 50’ coupling to the door. This creates at least 50’ of “workable” hose in line with the target Before entry, the attack firefighter checks the nozzle and attack package for the following: o Reach o Pressure Click here to view Brass Tacks and Hard Facts o Penetration video on Stream Angles in Interior Attacks o “Is this something I want to fight fire with?” Moves in a three-point stance; only utilizes the pistol grip to advance the line. While flowing water, recruits are instructed to keep the nozzle out in front (not holding the pistol grip) to make the hose easier to manipulate with good technique Second Edition 01/31/22 40 B—BACKUP Backs up the nozzle firefighter This firefighter is responsible for forcing the front door if needed, as well as the following actions: o Sweep the immediate egress area around the door o Check for “LFL” ▪ Life – Are there any victims around the door? SWEEP THE FLOOR! ▪ Fire – Can I see where the fire is, or at least the general direction? ▪ Layout – What is the building layout? Where are the stairs? Can any of the nearby rooms be identified? Living room, kitchen, bathroom, etc.? Relay these findings to the nozzle firefighter prior to entry into structure Assist with hose advancement by minding pinch points and pre-loading hose where appropriate o Recruits are taught not to stack hose in the building; they keep pre-loading on the floor o Only preload what the building gives you; do not force it! Too much hose can be a negative; it can lead to kinks Second Edition 01/31/22 41 C—CONTROL This firefighter is positioned behind the backup and the nozzle firefighter Responsible for managing the line from the backup firefighter to the door o Can assist with fixing kinks outside the structure prior to entry Assists with hose advancement by minding pinch points and pre-loading hose where appropriate o Recruits are taught not to stack hose in the building; they keep pre-loading on the floor o Only preload what the building gives you; do not force it! D—DOOR This firefighter is positioned behind the control, backup, and nozzle firefighters Responsible for managing the line outside the structure up to the front door o Removes any kinks outside the structure o Responsible for helping split the door and keeping a neat entryway Assists with hose advancement by minding any pinch points developed at the entry point Second Edition 01/31/22 42 HOSE LINE SELECTION CONSIDERATIONS OVERVIEW A common phase echoed across training grounds around the country is “The fire goes as the first line goes” Even before deploying a hose line, the most important step an engine company can make is deciding which hose line to use Selecting the appropriate attack line/defensive stream for the amount of fire on hand is critical to the successful outcome of any operation A few different examples and rules of thumb for selecting the appropriate attack package on the fire ground are shown below INITIAL LINE SELECTION – WHAT IS ON FIRE? Anything from a single room and contents fire up to three rooms of fire—1 ¾” hose line More than three rooms of fire—two 1 ¾” hose lines or one 2” hose line One floor or more of fire—2 ½” hose line Commercial structure—consider a 2” or 2 ½” hose line Defensive operations—consider master streams EXPONENTIAL ENGINE THEORY – BRIAN BRUSH Ensure there is enough water to safely extinguish the number of BTUs burning, no matter what the scenario is Uses the idea that every line on our engines should not be set up to fight the same fire There must be different weapons to choose from for different fights Uses the rule of thumb that increasing to the next larger line/nozzle size should approximately double the GPM available, as shown in the chart below Line Selection Nozzle/Tip Size GPM GPS (Gallons Per Second) 1 ¾” Attack Line 160/50 or 7/8” SB 160 GPM 2.6 GPS 2 ½” Attack Line 1 3/16” SB at 50 PSI 296 GPM 4.9 GPS Deck Gun 1 ½” SB Tip at 80 PSI 600 GPM 10 GPS WHEN TO PULL A 2 ½” HANDLINE – ANDY FREDERICKS The following ADULTS acronym can be used to outline situations when a 2 ½” hand line should be used This acronym was created by a FDNY firefighter studying for the promotional examination o Advanced fire on arrival o Defensive operations o Unable to determine the extent/size of the fire area involved o Large, non-compartmentalized areas o Tons of water o Standpipe system operations Second Edition 01/31/22 43 EXPECTATIONS FOR MEDIUM AND LARGE DIAMETER HANDLINES IN PROBLEM OCCUPANCIES This article will discuss the expectations and limitations of using a 2” attack line or a 2 ½” attack line when fighting fires in problem occupancies. Some of the different ways these two lines are carried on many Columbus engine companies will be discussed. There are some significant differences between these two lines; these differences can help or hurt firefighters depending on what the building presents to them. First, it is important to define the occupancies that are being referred to in this article. The term commercial occupancy has a tendency to be used to encompass everything from a large un-compartmentalized space like a Lowes or auto body shop to a multi-level office building. A multi-story residential building, such as a common hall apartment building, is also a problem occupancy that will be discussed. These buildings offer very different hazards and have the potential to require a very different application rate to quickly contain the fire. For the purposes of this article, a commercial space The photo above shows a true commercial or occupancy is defined as a large, occupancy. The building is composed of uncompartmentalized space, typically with a fire resistive materials. It consists of large larger than “normal” fire load. That definition uncompartmentalized space that spans a does not include a multi-story office building or full city block. common hall apartment building, both of which offer multiple compartmentalized occupancies under one roof. These photos show a three-story wood frame multi-family common hall apartment building. Although this building is a problem occupancy in regards to the hazards it presents, it is not a commercial structure and should not be treated as such. Second Edition 01/31/22 44 2” HANDLINE TARGET FLOW The target flow for the 2” line is between 200 and 250 GPM. The nozzles used with this handline could consist of any of the following: o Smooth bore with 1” tip—210 GPM at 50 PSI at the nozzle o Smooth bore with 1 1/16” tip—240 GPM at 50 PSI at the nozzle o 250/50 combination nozzle—250 GPM at 50 PSI at the nozzle There are some disadvantages that should be noted regarding the 2” hose attack package. While equipping the 2” line with the 1” tip technically aligns with the Freeman Ratio, the 1” tip is at best only 50 GPM more than the GPM from a 1 ¾” hose. Typically, having at least 100 GPM difference in our preconnected handline sizes gives enough of a return on investment to justify pulling the bigger size line. A bigger picture of an ideal target flow spec would illustrate that with an increase in line size, the application rate would increase exponentially. If the fire is large enough that a 1 ¾” line cannot be immediately effective, the next size line should overwhelm the problem, not just meet the demand. After all, “If you find yourself in a fair fight, your tactics suck.” A 2” line equipped with a 1” tip does not meet the industry standard of 250 GPM for commercial occupancies. It is necessary to achieve this flow because of the very nature of the fire, both actual and potential. Firefighters are not afforded the protection of a compartmentalized space; studies and experience show that our smaller flows can easily be outpaced in these situations. However, there are disadvantages to trying to achieve target flows that exceed what is optimal for any specific handline. The nozzle firefighter needs to be aware that when approaching flows of 250 GPM with the 2” handline, the additional hydraulic forces start to add to an increasingly uncontrollable nozzle that will undoubtedly start to limit the ability to “paint the room.” This can cause a situation in which the hose team cannot effectively fight the fire because they are occupied fighting the nozzle. The ultimate goal is not only to deliver the maximum amount of water, but also to maintain the ability to have an open nozzle and the control to place the water where it needs to go. A way that engine companies can use this particular tip to their advantage is by utilizing this attack package as a longer line option for a more difficult stretch in a structure that is compartmentalized. Multi-level office buildings or three-story common hallway structures with longer stretches and multiple corners that must be navigated prior to making the point of service are perfect examples of situations where this line’s potential can be maximized. The increased size of the 2” line coupled with the 210 GPM target flow will benefit firefighters on these longer stretches by decreasing friction loss; this allows these lines to operate farther away from the apparatus at an appreciable pump discharge pressure. This gives the 2” line a particular identity and widens our operational envelope considerably. Second Edition 01/31/22 45 2 ½” HANDLINE TARGET FLOW The target flow for the 2 ½” line is between 260 GPM and 328 GPM. For this reason, the nozzles used with this handline could consist of the following: o Smooth bore with 1 1/8” tip—266 GPM at 50 psi at the nozzle o Smooth bore with 1 3/16” tip—296 GPM at 50 psi at the nozzle o Smooth bore with 1 ¼” tip—328 GPM at 50 psi at the nozzle Typically, engine companies with the 1 1/8” tip have what is referred to as an “Indy Stack.” This is the stacked tips with the 1 1/8” tip on top of the 1 ¼” tip. Engine companies with the 1 3/16” tip can take advantage of the 2 ½” hose and the smooth bore’s operational range of 40-60 psi to achieve a wide range of flow and reaction forces that are relatively close to what the Indy Stack offers (See 2 ½” Smooth Bore Nozzles in this manual for more information on the 1 3/16” tip). However, flows of more than 300 GPM in an attack situation are not recommended unless in a fixed position, such as when using a quick attack, RAM XD monitor, or even a Keenan loop. Our ability to use the operational range of the smoothbore is due to the inherent characteristics of the 2 ½” hose. Please keep in mind that we cannot utilize the lower end of the smoothbore’s operational range with our 1 ¾” handlines. LAYOUT On CFD engines, most of the time the 2” attack line will be found loaded on the cross lay bed. The hose is red and consists of a preconnected 200 foot load. The 2 ½” attack line is normally loaded on the rear of the engine. This will be a static load of either 200 or 300 feet; it will be white with red racing stripes. The line will either be preconnected to the rear discharge, or it may not be preconnected with the female coupling lying in the bed on the bottom of the stack. Usually if the 2 ½” is not preconnected, it is because that company has chosen to connect a 100 foot section with a MQA or RAM to the rear discharge (Refer to the Equipment section of this manual for information on the MQA and the RAM). Second Edition 01/31/22 46 These are some of the more common ways these two lines are carried. However, there are some companies that choose to change their loads depending on the needs within their district. Recently, some companies have changed their 2 ½” line to the cross lay and put their 2” line off the rear of the hose bed. It is up to each firefighter to learn what is carried on their specific engine. The side-by-side photos above show different rear bed configurations. On the left, E15 shows a slightly more traditional CFD layout with the 2 ½” hose loaded as a static bed with an Indy Stack on the nozzle. The last 100’ is then preconnected to the MQA and loaded on top of the static bed. Their 2” hose is located in the cross lay. On the above right, new E17 has the 2” hose coming off the rear connected to a gated wye on the right rear discharge. Their 2 ½” hose is located in the cross lay. Their RAM is then located in a readily deployable layout in the rear compartment. It is important that some thought is given to how these attack packages are loaded. A CFD engine is equipped with a generous amount of hose, but that is only half the solution. All firefighters need to ensure that the attack packages are loaded in such a way that they can be deployed both effectively and efficiently under realistic conditions. For a CFD engine, this means being able to deploy effectively while staffed at 1 and 2. If our options are not realistically laid out on our engines, they truly fail to be realistic options in the time-compressed, task-saturated environment of the initial moments of an incident due to their perceived reflex time. Firefighters should evaluate their first due, determine a stretch potential, and aim to lay out their engines to best achieve these goals. Enough consideration Second Edition 01/31/22 47 cannot be given to the fact that the longer stretch often means navigating multiple corners prior to reaching the point of service (POS). The multi-floor office building or common hall apartment building are perfect examples. A fire on an upper floor of either of these two buildings would require multiple corners and even stairs to be navigated prior to getting to the fire floor. Fire doors have proven reliable for keeping smoke and fire isolated to that segment of the building, further extending our POS into the building. It is important to take advantage when the building allows for the POS to be closer to the fire occupancy. DEPLOYMENT Recently, the Division has seen more fires within open warehouse commercial buildings. Some of these fires were caused by common combustibles catching fire and spreading to other areas of the structure. Others were due to explosions that rapidly grew in size and spread to the roof of the structure. It will be up to you and ultimately the officer on the engine to decide what line will help your company be successful. Recon for these types of fires is critical. On these very large buildings, figuring out where to enter the building to best get to the fire is as important as what line will be pulled. Doing good recon will also set you up to have a better stretch and get to the fire quicker. Regardless of the size line selected for fire attack, firefighters must not get complacent and disregard all the markers of a good deployment. Having the nozzle and a coupling at the point of service is the gold standard for any deployment, but it becomes increasingly important as the size of the attack line increases. Another useful technique, especially when using larger diameter hose, is to deploy the working length in an “Attack over Supply” orientation. This will raise a large portion of that first 50’ off the ground, which will help with the advance. Also, when possible, firefighters need to attempt to deploy inline with respect to the advance. Firefighters should ensure that handlines are loaded in such a way that they can be deployed in relatively short order, taking advantage of these methods. This photo shows an example of the “Attack over Supply” orientation discussed above. The first 50’ of hose is elevated off the ground by resting on the remaining section of hose. This will help with advancement by reducing the amount of friction between the hose and the ground. Second Edition 01/31/22 48 FUNCTION Next, this article will discuss the differences in function between these two attack packages. These lines need to be framed properly. The 2” and 2 ½” handlines are the biggest in our arsenal, and we cannot and should not expect to manipulate them in the same manner as their smaller counterpart. When attacking with a 1 ¾” line, our operational tempo is usually elevated. We are able to operate this way not because we are bringing with us a lighter, more maneuverable line, but rather because we are entering an environment that is usually relatively compartmentalized and our target flow (160 GPM) has been shown to afford us all the protection needed to do so. This allows us to bring the smaller, more maneuverable line. In contrast, our commercial environment does not afford us these luxuries. We must change our mindset and move more methodically though these environments. Because of the nature of the potential fire, we should not aim to move with the same tempo in a commercial environment. We should start flowing water early, using the inherent strengths of the larger handline. Our goal should be to win back the structure five feet at a time. Nozzle technique with larger handlines could and should be dramatically different than what is generally expected to be achieved with a 1 ¾” line. With 1 ¾” handlines, the nozzle firefighter can achieve 90° left, right, and up from center, which is widely considered a standard goal. Picture 90° being on the same plane as your shoulders when operating the nozzle. However, we cannot expect to manipulate our larger handlines as aggressively. It is ok to adjust our expectations with our larger lines to approximately half of what we can achieve with the smaller handline. This is due to the larger reaction force we will be experiencing at these larger target flows, as well as the larger line’s natural tendency to resist manipulation. Utilizing a 2” line over the 2 ½” line might lead firefighters to believe it will give them a greater range due to the smaller line size, but they might actually find a larger perceived reaction force at the 250 GPM target flow due to the reduced weight in the last six feet of the line. This is not to say firefighters cannot attempt to widen their pattern, but they must be cognizant of their foundation prior to getting outside 45°. Firefighters are strongly encouraged to go out with their companies, flow these lines, operate these nozzles, and get a feel for how they handle. This section should help illustrate the reason the nozzles feel different, but it cannot take the place of experiencing how they actually react. This photo depicts the horizontal Center = 0o range when utilizing larger handline nozzles with higher reaction forces. Keeping the nozzle 45o 45o within the 45° angles both left and right of center, as shown, will help the nozzle firefighter combat the higher reaction forces associated with larger lines. Wider angles can of course be taken; however, the nozzle firefighter should adjust their stance appropriately to combat the reaction forces. Second Edition 01/31/22 49 It has been shown that in a large commercial space, the ideal nozzle pattern is not the typical O pattern. Instead, firefighters should utilize a sweeping motion at the ceiling level. Start high and sweep left to right, as wide as possible with the goal of achieving that 45° from center, continuing to sweep and lowering the angle with each sweep. This will do a few things for the attack. First, it cools the ceiling above the area which firefighters will potentially be occupying next. The stream is being used to displace any ceiling tiles, expose that void space, and cool the roof structure. Firefighters should then lower their stream angle incrementally to do the same with the next sweep, repeating this process to win back the building. Because the hose team is realistically limited to a relatively reduced pattern width, great effort must be made to ensure the fire stays in front of them in these situations. It is also important to discuss the reach and penetration of our assortment of nozzles. These aspects are crucial to fighting these fires because they represent possibly the most beneficial attributes of our larger lines. Generally speaking, fires do not go out for one of two reasons— firefighters do not have enough water, or they do not have access to the seat of the fire. Using the larger line delivers as much water as reasonably can be used while maintaining interior attack capability. Now, firefighters must strive to use the water as efficiently as possible. The most efficient way to extinguish a fire is to get the water on the material that is burning, not evaporation of that water to steam. To quote Andy Fredericks: “The goal is to get water on the fuel-flame interface without premature vaporization of the water and excess steam production.” The naturally bigger droplets from our smoothbore nozzles travel farther through the thermal column and resist vaporization due to their mass, ultimately providing a better chance of impacting that fuel-flame interface. This is precisely the penetration that is referenced. The exit velocities of the smooth bore nozzles at 50 psi are equivalent. Our combination nozzles can have slightly higher exit velocities, which translates to the water moving faster though the thermal column. However, this is not the advantage it sounds like it is because the droplets from the refocused stream are more readily vaporized in the thermal column. Increased exit velocities do very well to push water though the elements, specifically wind, on the exterior of the building, but the increased velocity is not necessarily a desired trait in an offensive attack. When evaluating the differences in maneuverability, the 2” line is a more maneuverable line compared to the 2 ½” line. This is mostly because of the weight in the charged line. The weight within a charged 2” line is 68 pounds per 50’ section of hose, while the weight within the charged 2 ½” hose is 103 pounds per 50’ section. This creates a significant difference in the total weight of the attack package, which translates to an increased amount of effort to move it. If there are a lot of obstacles to navigate (corners, cubicles, shelving, or pallets), the 2” line could be the better choice. As a general rule, the larger the line, the less forgiving it is. The 2 ½” line cannot be preloaded without overloading nearly as much as its smaller counterparts. As a result, firefighters have to accept the fact that they are advancing the larger handline straight though buildings, with any preloading being reduced to shallow “S” patterns within the spans. Second Edition 01/31/22 50 The two photos above show the 2” red hose (left) and 2 ½” white hose (right) pre-loaded into a tight area to represent possible obstacles found on scene. Because the 2 ½” line is less forgiving, it is not able to be preloaded as well. Operating crews must work within the confines of the hose and what the building gives them when attempting to preload and advance. The 2 ½” line will need to be advanced straight through buildings, with any preloading being reduced to shallow “S” patterns within the spans. While the difference in the weight of the line is significant, it should be noted that the extra weight is not strictly a disadvantage. The extra size and weight will help the nozzle firefighter operate the handline because it will reduce the perceived reaction force. Furthermore, the weight of the line will aid the operation as more hose falls in line behind the operator. The most dangerous position for a nozzle firefighter to become unseated is directly after a turn while flowing, with the hose not in a line behind him or her. This applies regardless of the size of the line, but it is less and less forgiving as size and target flow increase. Caution should be taken when opting to deploy a handline with a less than favorable target flow in favor of maneuverability. Flow should be the first and most important consideration when choosing a handline to combat a fire, and it should not be compromised because it is the Battalion 3 companies stretching a 2 ½” on primary factor for efficiently achieving a working fire at 2898 E. 14th Ave. Crews extinguishment. Regardless which line the made a great line choice based upon the initial arriving engine company chooses to building type and the fire conditions deploy, this should not lift from the shoulders present on arrival. Second Edition 01/31/22 51 of the second due engine the responsibility of first ensuring the primary line is properly staffed and moving before committing to the back-up line. There are real and tangible benefits to both of these handlines. It is very much a balancing act as firefighters strive to maximize these handlines’ potential to widen our operational capability and provide the most effective and efficient attack possible. It comes down to the firefighter and ultimately the officer to interpret what the fire has already written and to translate that to the proper line selection based on the size of the building, extent of the fire, and the fire’s potential. Get out and train, make it fun, and start to reverse some of the training scars that may have been formed from our preliminary training so we can have confidence in the line the fire has selected. Second Edition 01/31/22 52 HOSE LOADS OVERVIEW Three main hose loads are found on CFD engines This does not mean these are the only loads, just the more common ones TRIPLE FOLD Advantages o Deploys quicker than both the modified minuteman loads o Less chance of making a mistake during deployment due to less moving parts Disadvantages o Not as versatile around obstacles such as cars and fences o No shoulder load to carry and place in tight spaces MODIFIED MINUTEMAN – 50’ BUNDLE Advantages o Easier to manage on your shoulder; not as tall as the 100’ bundle o Can split cars easier than a triple layer load Disadvantages o 50’ may not be enough to reach the objective o Does not deploy as quickly as a triple fold o More moving parts that may cause a deployment issue as opposed to simpler loads Second Edition 01/31/22 53 MODIFIED MINUTEMAN – 100’ BUNDLE Advantages o More versatile around cars and fixed obstacles than the triple fold o Since 100’ is bundled together, the dead stack is shorter and more manageable o Provides more usable hose near the entry point of the structure. The 100’ bundle should be able to reach all areas of most common residential structures o Easier to split cars since more of the hose is on the firefighter’s shoulder instead of being dragged on the ground where it can easily catch on obstacles Disadvantages o The 100’ bundle can be difficult to manage on your shoulder. It can also be prone to “spaghetti” if used without straps to secure the bundle o Does not deploy as quickly as the triple fold o Has more moving parts that could possibly cause a deployment issue as opposed to simpler loads Second Edition 01/31/22 54 BUILDING A 100’ MINUTEMAN BUNDLE OVERVIEW This section shows how to build a modified minuteman load with a 100’ bundle These procedures apply to both the 200’ and 250’ preconnected hose lines Building this hose bundle is split into the following two steps: o Step One—Building the 100’ bundle section (the live stack) o Step Two—Loading the remaining hose (the dead stack) and connecting it to the 100’ bundle Click here to view Vector Solutions video on Building a 100’ Bundle BUILDING THE BUNDLE The bundle is built to the approximate size of the hose bed. Companies can measure their bed and place two marks on the bay floor, similar to how most stations have marks for their high-rise packs. An additional third mark should be made approximately 12”-14” past one end to designate the location of the nozzle coupling. This ensures enough tail is left to wrap around the bundle as shown later. If no marks are present, a 6’ hook can be substituted. The bundle should be slightly shorter than the hose bed. This is to make room for the small loops in the back of the bundle. With the nozzle coupling placed on the first mark (approximately 12”-14” past the end of the hook if no marks are present), the crew members will begin folding the hose on its side. The crew members will start closest to themselves and build the pack away from them. This will allow the tabs on the straps securing the pack to be facing up when the pack is placed on the ground during deployment. Second Edition 01/31/22 55 The crew members will then continue to fold the hose back and forth on its side between the first two marks. They will continue until the midpoint of the first 50’ of hose is reached. When the midpoint of the first section of the hose is reached, a small loop is placed in the rear of the bundle (opposite the nozzle end). This loop allows the midpoint of the hose to be easily grabbed when performing a back stretch or split stretch (shown later in this manual). The midpoint of the hose can easily be marked with a marker or tape. This can also help provide a quick reference point when crews are moving hose on the fireground. With the first loop at the midpoint, continue loading the hose until the 50’ connection coupling is reached. The coupling should be kept at the front of the bundle, towards the nozzle. If needed, a dutchman or extra fold should be placed in the hose to ensure the coupling is placed to the front of the bundle as shown below. Keeping the coupling at the front will make it easier to find for deployment and make performing a forward stretch faster. Second Edition 01/31/22 56 Now that the coupling is properly placed, continue to fold the hose on its side until the midpoint of the second section of hose is reached. At this point, a second small loop is placed in the rear of the bundle. The midpoint might not fall exactly on the loop. That is perfectly okay as long as it is the general midpoint of the hose. Not all hose is cut to a perfect 50’. With the second loop placed appropriately, continue loading the hose on its side back and forth until the final coupling is reached. At this point, connect the nozzle and fold it up and over the front of the bundle as shown below. Notice that the nozzle sits farther back than the midpoint coupling. This is important because it allows the strap to secure the bundle more easily. If the nozzle sits in line with the midpoint coupling, it can be bulky and hard to secure. Building the pack away from us with the straps facing up sets ourselves up for success when deploying the bundle. Remember Ear to Tab when placing the bundle on your shoulder; doing so allows the pack to be set down on the ground with the straps facing up. This prevents delays when unstrapping the bundle. Second Edition 01/31/22 57 FINISHING THE LOAD Now that the 100’ bundle has been built, the remainder of the hose needs to be loaded into the hose bed. This will be 100’ for the 200’ preconnect, and 150’ for the 250’ preconnect. Start by connecting the first 50’ section of hose to the pump discharge plumbing in the selected hose bed. Once that is connected, load the hose in a single straight stack. Place a loop in the stack of hose approximately 50’ into the load or in the middle of the dead stack. Remember the loop is designed to help clear the hose bed. The farther away from the pump discharge connection the loop is, the farther the firefighter must walk to clear the bed. With the dead stack hose load complete, finish the hose load by sliding the premade 100’ bundle into the opening next to the dead stack. The two stacks will sit side by side. Connect the coupling at the tail of the bundle to the coupling on top of the dead stack like a traditional CFD modified minuteman hose load. If the hose bed divider is set up for a single stack, load the dead stack on the bottom and leave the last coupling of the dead stack draped over the back of the hose bed. Stack the 100’ bundle on top of the dead stack, bring the draped over coupling back on top of the bundle, and connect the two couplings together. The photo below shows the 200’ preconnect in a single stack configuration and the 250?