EDMS Lecture 7: CAD Assemblies and Standard Mechanical Parts PDF
Document Details
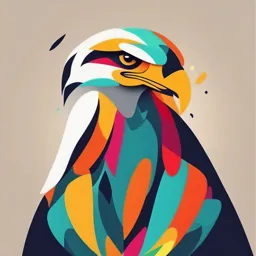
Uploaded by KindlyChrysoprase5172
ETH Zurich
Dr. Tino Stankovic and Prof. Dr. Kristina Shea
Tags
Summary
Lecture notes on engineering design and material selection, covering CAD assemblies, standard mechanical parts, and associated topics. This lecture, from ETH Zurich, outlines concepts, exercises, and potential quizzes.
Full Transcript
Engineering Design and Material Selection Lecture 7 — CAD: Assemblies and Standard Mechanical Parts Dr. Tino Stankovic Prof. Dr. Kristina Shea Prof. Kristina Shea 1 Course Schedule Week/ Topic...
Engineering Design and Material Selection Lecture 7 — CAD: Assemblies and Standard Mechanical Parts Dr. Tino Stankovic Prof. Dr. Kristina Shea Prof. Kristina Shea 1 Course Schedule Week/ Topic Case study Quiz Lecturer Dates 1 Introduction and Sketching 2 Introducing Engineering Design Health Prof. Dr. Kristina Shea 3 Technical Drawing: Projections and Cuts 4 CAD: Introduction and Modeling Operations 5 CAD: Features and Parametric Modeling Future Mobility 6 CAD: Freeform Modeling Dr. Tino Stankovic 7 CAD: Assemblies and Standard Mechanical Parts X (45 min) 8 Technical Drawing: Dimensioning Health 9 Sustainability in Engineering Design 10 Materials and their Properties 11 Manufacturing Processes with Focus on Additive Manufacturing Sustainable Materials Prof. Dr. Kristina Shea 12 Material Selection 13 Review and Q+A X (75 min) Prof. Kristina Shea Engineering Design + Computing Laboratory 2 This week: Quiz 1 ▪ Bring… ▪ Your Legi ▪ Pencil (Pen), one A4 sheet of writting paper will be provided by us ▪ Closed-book: no further materials (calculators, summaries, electronic devices etc.) allowed ▪ Dictionnaries (Eng-Ger, Eng-Fre, Eng-Ita) are provided by us ▪ Make sure you are able to log in to the computers in your exercise room If you are ill… ▪ Don’t come to the quiz ▪ Inform us about your absence (email to [email protected]) ▪ Send doctor’s certificate (can happen after quiz) Prof. Kristina Shea Engineering Design + Computing Laboratory 3 Learning Objectives ▪ Understand the need for CAD assemblies in product development ▪ Create assembly structures in CAD ▪ Learn about standard parts in mechanical design ▪ Read assembly drawings and identify standard parts Prof. Kristina Shea Engineering Design + Computing Laboratory 4 Why Do We Need Assembly Drawings? Prof. Kristina Shea Engineering Design + Computing Laboratory 6 Assembly: Car Prof. Kristina Shea Engineering Design + Computing Laboratory 7 Front Cut Part List Quantity Prof. Kristina Shea Engineering Design + Computing Laboratory 8 CAD assemblies support… Visualization of Assembly Assembly Checking Drawings Functionality Interference Bill of Materials Analysis Use of Norm CAD Assembly Motion Simulation Elements Manufacturing Part Re-Use Assembly and Planning Disassembly Evaluation Prof. Kristina Shea Engineering Design + Computing Laboratory 10 Breathe: Motion Simulation Prof. Kristina Shea Engineering Design + Computing Laboratory 11 CAD Model of the PLUS II: Exploded View Highlights Assembly Process Chassis Bodywork Windshield Electronics Door Steering system and front wheels Drivetrain and back wheels Prof. Kristina Shea Engineering Design + Computing Laboratory 12 Assembly Structure Main-Assembly Sub-Assembly 1 Sub-Assembly 2 Standard Normteil2:2:Element Normteil 10x 10x 1: 8x Standard Normteil2:2:Element Normteil 10x 10x 2: 2x Part 1: 1x Part 4: 2x Tretlagerwelle Part 2: 1x Part 3: 5x Tretlagerwelle Tretlagerwelle Tretlagerwelle Prof. Kristina Shea Engineering Design + Computing Laboratory 14 Assembly Structure – Example Car Body Wheel Sub-Assembly: 2x Front: 1x 6-Stud Axle: Normteil 1x 2: 10x Back: 1x Wheel: 2x Tretlagerwelle Chassis: 1x Prof. Kristina Shea Engineering Design + Computing Laboratory 15 Bottom-Up Modeling The lowest level parts are identified and then modeled as components and assembled together to form subassemblies, moving up the assembly Assembly hierarchy, until the main assembly is assembled. Bottom up Sub-assembly 1 Sub-assembly 2 Part 1 Part 2 Part 3 Part 4 Part 5 Prof. Kristina Shea Engineering Design + Computing Laboratory 16 CAD Assembly: Bottom-Up Modeling Create Assembly Create Sub- Assemblies Model / Reuse Parts Prof. Kristina Shea Engineering Design + Computing Laboratory 17 Assembly in CAD: Assembly Features Represent a relationship between two form features that are on different parts, e.g.: ▪ Against ▪ Align Co-planar ▪ Offset Offset-x Against ▪ Co-axial ▪… Against Offset-x Co-axial Co-axial Prof. Kristina Shea Engineering Design + Computing Laboratory 18 Part Positioning with Kinematic Simulation: Universal joint Prof. Kristina Shea Engineering Design + Computing Laboratory 19 “Assembly Constraints” in NX ▪ Examples: ▪ Touch Align ▪ Concentric ▪ Distance ▪ Fix ▪ Angle ▪… Prof. Kristina Shea Engineering Design + Computing Laboratory 20 “Assembly Constraints” in NX ▪ Setting of constraints: ▪ Possible options: ▪ Touch Align ▪ Concentric ▪ Align surfaces ▪ 2 DOF remain (z-axis, rotation) Prof. Kristina Shea Engineering Design + Computing Laboratory 21 “Assembly Constraints” in NX ▪ Setting of constraints: ▪ Additional constraint fixes the z-coordinate Prof. Kristina Shea Engineering Design + Computing Laboratory 22 Assembly Array Component of a pattern feature Prof. Kristina Shea Engineering Design + Computing Laboratory 23 CAD Assembly: General Creation Fix Empty File... Prof. Kristina Shea Engineering Design + Computing Laboratory 24 Assembly Constraints: Car Touch Align Touch Align Touch Align Prof. Kristina Shea Engineering Design + Computing Laboratory 25 Which statement regarding the assembly constraints for the axle is true? A. The center of the axle needs to be constrained as co-axial to the holes on both sides. B. Two constraints are needed to correctly position the axle, while keeping one degree of freedom. C. A single co-axial constraint is enough to correctly position the axle, while keeping one degree of freedom. D. Since the axle can rotate freely, no constraint should be added. Prof. Kristina Shea Engineering Design + Computing Laboratory 26 Move Components YEEFespE.LYEstraints Collision Prof. Kristina Shea Engineering Design + Computing Laboratory 27 CAD Assembly: Assembly Structure and Constraints in NX Prof. Kristina Shea Engineering Design + Computing Laboratory 28 Standard Parts (ISO) ▪ To reduce the effort to draw common parts or geometries ▪ Two types: ▪ Standard components ▪ Physical parts that fulfill certain functions ▪ Usually bought from an external provider ▪ Not always officially normed, e.g., bearings ▪ Standard elements ▪ Common types of geometries, e.g. for manufacturing or assembly to simplify drawings Image Source: SNV Normen-Auszug 2018. Swissmem, Zürich Prof. Kristina Shea Engineering Design + Computing Laboratory 29 Standard Components – Examples Nuts and bolts Circlips (Retaining rings) Fasten several parts together Hold the axial position of elements on a shaft in place reduce energy Ball Bearings Springs Reduce friction between Pre-tension parts and rotating parts and support assemblies or store energy radial and axial load Prof. Kristina Shea Engineering Design + Computing Laboratory 30 Standard Components – Examples Parallel key Rotary shaft lip seals Connect and secure a rotating machine element, Seals rotationally moving parts, e.g. shaft e.g. gear, to a shaft and transmit torque Gears, spur gear (left) and worm gear (right) O-rings Rotating elements with teeth that transmit motion. Rubber parts that are used to seal non-rotary They are often used to adjust the rotational speed. parts. Prof. Kristina Shea Engineering Design + Computing Laboratory 31 BREATHE Gearbox Assembly – exploded view Prof. Kristina Shea Engineering Design + Computing Laboratory 32 Section Views in Assemblies Prof. Kristina Shea Engineering Design + Computing Laboratory 34 Part Families of Standard Parts Defining current instance LEGO elements DIN elements Reuse Library Types of Parallel Keys Prof. Kristina Shea Engineering Design + Computing Laboratory 35 same Eig Gearbox Example guitar Prof. Kristina Shea Engineering Design + Computing Laboratory 36 Gearbox Example - Usage ▪ Gearbox with worm gear used in robot at ETH Fotos taken in ETH: HG E 4 Prof. Kristina Shea Engineering Design + Computing Laboratory 37 Gearbox Example - Exploded View O-ring Bering Worm gear Spur gear Prof. Kristina Shea Engineering Design + Computing Laboratory 38 Gearbox Example Screws turned 30° into plane of projection; 6 at circumference Gear Prof. Kristina Shea Engineering Design + Computing Laboratory 40 Connection of Threaded Parts A cuts hole but not screw + = External Internal thread thread Combined Prof. Kristina Shea Engineering Design + Computing Laboratory 41 Screw Connections Prof. Kristina Shea Engineering Design + Computing Laboratory 42 Screw Connections rubberseal Prof. Kristina Shea Engineering Design + Computing Laboratory 43 Screw Connections Prof. Kristina Shea Engineering Design + Computing Laboratory 44 Screw Connections Prof. Kristina Shea Engineering Design + Computing Laboratory 45 Standard Part Selection Hexagon socket Head cap screw DIN 4762 Thread Thread diameter Length M1.6 M2 M2.5 M3 M4 M5 M6 𝐿𝑚𝑖𝑛 2,5 3 4 5 6 8 10 𝐿𝑚𝑎𝑥 16 16 20 20 25 25 30 Prof. Kristina Shea Engineering Design + Computing Laboratory 46 Nuts Screws, Bolts, Nuts & Washers Washer ISO 7089-10-200 HV elastic aIs ISO 4032-M10-8 Bolt ISO 2338-8 h8x40 SN 4014-M10x70 Prof. Kristina Shea Engineering Design + Computing Laboratory 47 Bearing and Circlip Prof. Kristina Shea Engineering Design + Computing Laboratory 48 Bearing and Circlip DIN 471-12x1 Circlip DIN 625-6207 Ball bearing Prof. Kristina Shea Engineering Design + Computing Laboratory 49 Seals O-ring DIN 3771-31x1 DIN 3760-AS 15x24x7 Radial shaft lip seal Prof. Kristina Shea Engineering Design + Computing Laboratory 50 Key & Gearing Prof. Kristina Shea Engineering Design + Computing Laboratory 51 Key & Gearing Gearing Parallel key DIN 6885-A 5x4x18 Prof. Kristina Shea Engineering Design + Computing Laboratory 52 How Many Bearings Can Be Found in This Drawing? im a) 0 b) 2 c) 4 0 f d) 8 Prof. Kristina Shea Engineering Design + Computing Laboratory 53 CAD Assemblies and Standard Mechanical Parts: Wrap-up Assembly models in CAD are necessary for evaluation of the product in terms of function, fit and manufacturing. Creating assemblies in a CAD system uses assembly features, or constraints. There are many ways to create assembly models. The chosen approach should match the desired goals. Some degrees of freedom (DOF) can be left unconstrained allowing movement. Mechanical systems and products use many standard parts that can be bought in different configurations off the shelf. You should be able to recognize standard mechanical parts in a 2D drawing and know their basic function. Prof. Kristina Shea Engineering Design + Computing Laboratory 54 Exercise 7: Working with CAD Assemblies Working with assemblies in NX Create an assembly model of your car Prof. Kristina Shea Engineering Design + Computing Laboratory 55