ECE 03 – Electronics 3: Electronics System & Design Final Exam PDF (2024)
Document Details
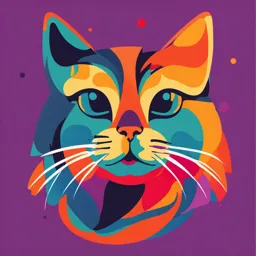
Uploaded by ImpeccableBlessing
null
2024
Engr. Joel Anthony L. Sevilla
Tags
Summary
This document provides a detailed explanation of Programmable Logic Controllers (PLCs). It covers various topics like PLC operation, hardware components, and advantages over traditional hardwire systems in several academic settings and industry applications.
Full Transcript
ECE 03 – ELECTRONICS 3: ELECTRONICS SYSTEM & DESIGN BSECE III ENGR. JOEL ANTHONY L. SEVILLA DECEMBER 2024 PROGRAMMABLE LOGIC CONTROLLER A special form of microprocessor‐based controller that uses a programmable memory to store instructions and to implement functio...
ECE 03 – ELECTRONICS 3: ELECTRONICS SYSTEM & DESIGN BSECE III ENGR. JOEL ANTHONY L. SEVILLA DECEMBER 2024 PROGRAMMABLE LOGIC CONTROLLER A special form of microprocessor‐based controller that uses a programmable memory to store instructions and to implement functions such as logic, sequencing, timing, counting and arithmetic in order to control machines and processes. It is developed to offer the same functionality as the existing relay logic systems. Either automated data collection points and human input points, such as buttons and switches, provide data to a PLC. A Programmable Logic Controller (PLC), is also referred to as programmable controller, is the name given to a type of computer commonly used in commercial and industrial control applications. PLCs differ from office computers in the types of tasks that they perform and the hardware and software they require to perform these tasks. PLC Examples and Control Panel While the specific applications vary widely, all PLCs monitor inputs and other variable values, make decisions based on a stored program, and control outputs to automate a process or machine. Basic PLC Operation The basic elements of a PLC include input modules or points, a Central Processing Unit (CPU), output modules or points, and a programming device. The type of input modules or points used by a PLC depend upon the types of input devices used. Some input modules or points respond to digital inputs, also called discrete inputs, which are either on or off. Other modules or inputs respond to analog signals. These analog signals represent machine or process conditions as a range of voltage or current values. The primary function of a PLC’s input circuitry is to convert the signals provided by these various switches and sensors into logic signals that can be used by the CPU. The CPU evaluates the status of inputs, outputs, and other variables as it executes a stored program. The CPU then sends signals to update the status of outputs. The programming device is used to enter or change the PLC’s program or to monitor or change stored values. Once entered, the program and associated variables are stored in the CPU. In addition to these basic elements, a PLC system may also incorporate an operator interface device of some sort to simplify monitoring of the machine or process. Output modules convert control signals from the CPU into digital or analog values that can be used to control various output devices. Basic PLC System PLC SYSTEM/HARDWARE 1. The processor unit or Central Processing Unit (CPU) is the unit containing the microprocessor and this interprets the input signals and carries out the control actions. 2. The power supply unit is needed to convert the mains AC voltage to the low DC voltage (5V). 3. The programming device is used to enter the required program into the memory of the processor. PLC Handheld Programming Devices 4. The memory unit is where the program is stored that is to be used for the control actions to be exercised by the microprocessor and data stored from the input for processing and for the output for outputting. 5. The input and output sections are where the processor receives information from external devices and communicates information to external devices. 6. The communications interface is used to receive and transmit data on communication networks from or to other remote PLCs. Advantages of PLC PLCs not only are capable of performing the same tasks as hard‐wired control, but are also capable of many more complex applications. In addition, the PLC program and electronic communication lines replace much of the interconnecting wires required by hard‐wired control. Additional Advantages of PLCs 1. Smaller physical size than hard wire solutions 2. Easier & faster to make changes 3. PLCs have integrated diagnostics and override functions 4. Diagnostics are centrally available 5. Applications can be immediately documented 6. Applications can be duplicated faster and less expensively.