DOH Warehouse Operations Manual 2022 PDF
Document Details
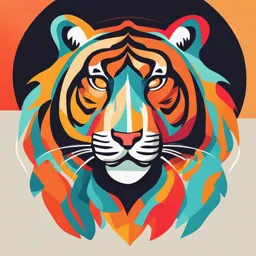
Uploaded by UnparalleledGhost
2022
Tags
Summary
This is a 2022 warehouse operations manual for the Department of Health (DOH) in the Philippines. It covers various topics including the supply chain management and procedures for receiving, storing, and dispatching health commodities. The manual aims to improve the management, monitoring, and distribution of drugs, medicines, and health supplies within the country.
Full Transcript
WAREHOUSE OPERATIONS MANUAL 2022 Department of Health Supply Chain Management Service Department of Health Supply Chain Management Service Warehouse Operations Manual 2nd Edition 2022 Manila, Philippines This publication is made possible by the generous support of the US Agen...
WAREHOUSE OPERATIONS MANUAL 2022 Department of Health Supply Chain Management Service Department of Health Supply Chain Management Service Warehouse Operations Manual 2nd Edition 2022 Manila, Philippines This publication is made possible by the generous support of the US Agency for International Development (USAID) under contract no. 7200AA18C00074 for Medicines, Technologies, and Pharmaceutical Services (MTaPS) Program. The contents of this publication are the responsibility of the authors and do not necessarily reflect the views of USAID or the US Government. This document is published by the Department of Health (DOH) – Supply Chain Management Service (SCMS) with office at Building 12, San Lazaro Compound, Tayuman St. cor. Rizal Ave., Sta. Cruz, Manila, Philippines 1003, for general distribution. All rights reserved. Subject to the acknowledgement of DOH-SCMS, the Manual may be freely abstracted, reproduced or translated in part or in whole for non-commercial purposes only. If the entire work or substantial portions will be translated or reproduced, permission should be requested from the DOH-SCMS. iii Contents MESSAGE.................................................................................................................................................. 1 FOREWORD.............................................................................................................................................. 3 ACKNOWLEDGEMENTS........................................................................................................................ 4 PART I INTRODUCTION.............................................................................................................. 8 1.1 BACKGROUND............................................................................................................... 8 1.2 PURPOSE OF THE MANUAL.......................................................................................... 8 1.3 USERS OF THE MANUAL............................................................................................... 8 PART II – GUIDING PRINCIPLES..................................................................................................... 10 2.1 THE SUPPLY CHAIN MANAGEMENT.......................................................................... 10 2.2 WAREHOUSE MANAGEMENT..................................................................................... 10 2.3 HOW TO USE THIS MANUAL...................................................................................... 13 A. DEFINITION OF TERMS USED IN THIS MANUAL.............................................. 14 B. LIST OF ANNEXES.............................................................................................. 21 PART III STANDARD OPERATING PROCEDURES....................................................................... 88 SOP-01-A: PREPARATION FOR DELIVERY FROM SUPPLIER............................................... 89 SOP-01-B: PREPARATION FOR DELIVERY FROM UPPER TIERS.......................................... 94 SOP-02-A: RECEIVING OF COMMODITY FROM SUPPLIERS.............................................. 98 SOP-02-B: RECEIVING OF COMMODITY FROM UPPER TIERS........................................ 107 SOP-03: PUT-AWAY......................................................................................................... 115 SOP-04: STORAGE AND WAREHOUSING..................................................................... 120 SOP-05: PICK AND PACK................................................................................................ 133 SOP-06: DISPATCH.......................................................................................................... 139 SOP-07: WASTE MANAGEMENT FOR PHARMACEUTICALS AND UNSERVICEABLE MEDICAL EQUIPMENT........................................ 144 SOP-08-A: REVERSE LOGISTICS: PRODUCT RECALL........................................................ 151 SOP-08-B: REVERSE LOGISTICS: PULLING ITEMS FROM LOWER TIERS FOR REDISTRIBUTION............................................ 157 SOP-08-C: REVERSE LOGISTICS: RELEASING ITEMS FOR REDISTRIBUTION............................................................................... 163 SOP-09: EMERGENCY SUPPLY CHAIN MANAGEMENT................................................ 168 SOP-10: COLD CHAIN MANAGEMENT......................................................................... 174 LIST OF REFERENCES.................................................................................................................. 184 1 Republic of the Philippines Department of Health OFFICE OF THE SECRETARY MESSAGE from the Secretary Of Health The enactment of the Universal Health Care (UHC) marked one of the biggest milestones in the history of the Philippine Health Sector. This paved the way for the commencement of significant reforms across the healthcare systems of the country, to ensure that every Filipino has equitable access to quality and affordable health care products, devices, facilities, and services without facing financial hardships, particularly the poor and marginalized members of our society. Aimed at attaining a more responsive healthcare system and a more equitable financing health mechanism, UHC espouses a holistic approach bettering the delivery of services, and underscores the significant role of a systematic approach, with clear delineation of roles of key agencies and stakeholders. Among the pipeline of significant reforms in improving the accessibility of health products are the implementation of a more streamlined and cost-effective Procurement and Supply Chain Management System (PCSM), capacity building for more competent, professional, and accountable human resource for strategic engagement with the private sector, and the implementation of Electronic Health Commodities Logistic Management Information System. These reforms play a crucial role in ensuring that we deliver quality products and services, by securing the availability and appropriate placement of critical health assets wherever they are needed. In line with the ongoing reforms in the Department of Health (DOH), guidelines for supply management are a critical component towards promoting accessibility to quality health products at all service delivery points. Hence, this Warehouse Operations Manual (WOM), as an essential part of supply and chain management, has been reviewed and updated with standards that will be critical in delineating roles and responsibilities of the entire supply workforce, and harmonise the concept of managing health commodities across all warehouses managed by the government. It is thus my fervent hope that the effort exhausted in the updating of this manual will effect positive changes for the realisation of a healthier, stronger Philippines. Together, let us create more responsive, more sustainable, and more equitable health systems and communities, for the benefit of every Juan and Juana. FRANCISCO T. DUQUE III, MD, MSc Secretary of Health 2 Republic of the Philippines Department of Health OFFICE OF THE SECRETARY MESSAGE from the Undersecretary Of Health Warehouse Management plays a vital role in building a strong healthcare supply chain management, this ensures that drugs, medicines, and other health commodities are available and accessible at the point of care thus providing quality, safe and effective health services at all levels of the health system. In line with our continuous pursuit to improve our services, the Department of Health presents the second edition of the Warehouse Operations Manual developed by the Supply Chain Management Service in coordination with the Regional Supply Officers and our partners from USAID - Medicines, Technologies, and Pharmaceutical Services (MTaPS). This manual was created to establish a system with streamlined processes to guide warehouse workforce in performing their daily operational tasks. Likewise, this also aims to provide guidance to the warehouses of both Centers for Health Development and the Local Government Units (LGUs) to ensure safe and efficient distribution of health care commodities within their area of jurisdiction. We hope that through this manual, we will be able to institute the much needed reform in the management, monitoring and distribution of drugs, medicines, and health supplies and prevent over or undersupply, expiration and wastage and ultimately support the health service delivery directive of the enhanced FOURmula ONE Plus (F1+) Strategy towards achieving the Universal Health Care (UHC) by ensuring the availability of essential quality health services at appropriate levels of care especially for the poor as well as strengthening good governance in health through improvement and innovations in the entire supply chain management system. MA. CAROLINA VIDAL-TAINO, CPA, MGM, CESO I Undersecretary of Health Procurement and Supply Chain Management Team 3 Foreword In line with the thrust of the Department of Health on UHC Act implementation and in support of the further devolution of the health sector, the Supply Chain Management Service (SCMS) developed these set of standards for warehouse management as an important part of the Supply Chain Management as a support to Service Delivery of Health Programs. This is to ensure the availability, and accessibility of safe and effective health commodities across the country. The SCMS team assumes the technical leadership and steers the coordination of initiatives to strengthen the country’s Supply Chain Management, from the national down to the local government level, which ultimately aims to ensure the delivery of patient-centered quality care. Standardization of processes and key areas of warehouse management is a step towards ensuring uniformity of warehouse processes at all levels of supply chain in preparation to achieving digitalization of supply management processes. This is through the implementation of the Electronic Logistics Management Information System (eLMIS) which will provide a more efficient, real-time, accurate data gathering and data management for monitoring, evaluation of the country’s supply chain for a more informed decision making. ARIEL I. VALENCIA MD, MPH, CESO III Director IV Supply Chain Management Service Department of Health, Philippines 4 Acknowledgements The Department of Health would like to acknowledge the leadership, expertise, support and dedication of the following persons/ entities who contributed to the finalization of this Manual: Department of Health - Procurement and Supply Chain Management Team Undersecretary Ma. Carolina Vidal-Taiño Ms. Nemencia Angelio Department of Health – Supply Chain Management Service (SCMS) Director Ariel I. Valencia Dr. Maria Joyce U. Ducusin Engr. Maximo A. Adan Jr. Mr. Edison S. Cervantes Mr. John Paul D. Casihan Ms. Jaqueline C. Hui Mr. Ferdinand F. Dela Cruz Mr. Rolando D. Palapar Department of Health – Centers for Health Development (CHDs) Ms. Zenaida B. Reyes (CHD – National Capital Region) Ms. Felina S. Carlos (CHD – Cordillera Administrative Region) Ms. Epigenia L. Bueno (CHD – Ilocos Region) Mr. Franklin A. Bugarin (CHD – Ilocos Region) Mr. David A. Aviles (CHD – Ilocos Region) Ms. Anabelle Ayumayum (CHD – Cagayan Valley) Ms. Ma. Ronalyn Jose Rodriguez (CHD – Cagayan Valley) Ms. Rhona G. Montilla (CHD – Cagayan Valley) Ms. Lolita Figuracion (CHD – Central Luzon) Mr. Rommel Capulong (CHD – Central Luzon) Mr. Moises Peralta (CHD – CALABARZON) Mr. Johndel P. Mendoza (CHD – CALABARZON) Mr. Carlos C. Carreon (CHD – MIMAROPA) Ms. Fe Q. Atento (CHD – Bicol Region) Ms. Josephine M. Tapales (CHD – Western Visayas) Ms. Mary Nonna Rose Durano (CHD – Central Visayas) Mr. Jonathan Neil Erasmo (CHD – Central Visayas) Mr. Arnulfo E. Lavares (CHD – Central Visayas) Mr. Marlo Calumpiano (CHD – Eastern Visayas) Mr. Jose Noel F. Torres (CHD – Zamboanga Peninsula) Mr. Voltaire Ucab (CHD – Northern Mindanao) Ms. Edith T. Villarin (CHD – Northern Mindanao) Mr. Rodrigo P. Uyos (CHD – Davao Region) Ms. Rosemarie G. Balite (CHD – Davao Region) Mr. Ben Cagumpang Jr. (CHD – Davao Region) Mr. Ramon Buenbrazo (CHD – SOCCSKSARGEN) Mr. Alvin R. Go (CHD – SOCCSKSARGEN) Mr. Earl Granado (CHD – SOCCSKSARGEN) Mr. Anthony Samson (CHD – CARAGA) Ms. Leslie C. Cortes (CHD – CARAGA) Ms. Aileen Sacol (CHD – CARAGA) Ms. Eleanor D. Lakag (CHD – CARAGA) Mr. Basir Guru (BARMM ) 5 Department of Health – Pharmaceutical Division (PD) Dr. Anna Melissa S. Guerrero Department of Health – Commission on Audit (COA) Ms. Corazon S. Rocas Association of Municipal Health Officers Dr. Clemencia D. Bondoc USAID – Medicines, Technologies and Pharmaceutical Services (MTaPS) Mr. Armando P. Enriquez Jr. Mr. Cristan Agaceta Mr. Gashaw Shiferaw Mr. Hasibul Haque Mr. Isaac Linatoc PART I Introduction 1.1 BACKGROUND The Department of Health (DOH) dedicates its time in rendering health services to all the citizens of our nation and so therefore, proper management of Health Commodities that the government procure are of vital importance in order to maintain the quality and potency during its storage and distribution. It is a primary commitment of the Department to provide safe and efficient health commodities to all Filipino in a timely manner through this initiative in fostering the Supply Chain Management. As part of improving the Supply Chain Management in the Department, the Warehouse Operations Manual (WOM) is written to standardize warehouse processes across all levels of supply chain and achieve seamless operations to support health services implemented by Public Health Programs. The WOM indicates standard processes on managing logistics which will be important in the preparation for automation pertinent to the Section 36 of the Implementing Rules and Regulations of the Republic Act No. 11223 otherwise known as the “Universal Health Care Act” indicating that electronic health commodities logistics management information system shall be implemented. The WOM is written in a simple and straightforward manner which clarifies operational tasks per position and per function. Every person will be clearly accountable for specific tasks within the warehouse with the intention of harmonizing all logistics operations of the government for health commodities. 1.2 PURPOSE OF THE MANUAL The purpose of this manual is to serve as general guideline for warehouse officials of the Government when carrying out their specific duties and responsibilities based on applicable local and international standards. This manual standardizes the procedures, accountabilities and responsibilities of warehouse staff in a step-by-step manner. 1.3 USERS OF THE MANUAL Users of this manual include all officials/employees and managers of various warehouses/storerooms managed by the Department of Health, its offices/units and attached agencies, Centers for Health Development, the Bangsamoro Autonomous Region in Muslim Mindanao (BARMM) and Local Government Units carrying health commodities. 10 WA R EHOU SE OPER ATI ON S M A N U A L 2022 PART II Guiding Principles PART II – GUIDING PRINCIPLES 2.1 THE2.1 THE SUPPLY SUPPLY CHAINCHAIN MANAGEMENT MANAGEMENT The country’s The country’s health health system system cannotefficiently cannot efficiently implement implementhealth healthservices without services a without a well-planned and well-operated supply chain management system well-planned and well-operated supply chain management system that maintains that maintains availability availability and and accessibility accessibility of of healthcommodities health commodities at atthe point the of care. point Supply of care. chain chain Supply management encompasses the planning and management of all activities involved management encompasses the planning and management of all activities involved in sourcing, procurement and logistics. Importantly, it also includes coordination and in sourcing, procurement collaboration and partners, with channel logistics.which Importantly, it also includes can be suppliers, coordination intermediaries, third and collaboration with providers, party service channel partners, which can and customers. In be suppliers, essence, intermediaries, supply third party chain management service providers, integrates supplyandand customers. In essence, supply demand management chain within and management across companiesintegrates and 1. organizations supply and demand management within and across companies and organizations1. The supply The supply management management in DOHin includes DOH includes the following the following processes: processes: needs needs assessment, assessment, product selection, procurement, warehousing, distribution, use and product selection, procurement, warehousing, distribution, use and monitoring & monitoring & tracking. tracking. Needs Assessment Product Use/ Customer Selection Service Monitoring and Tracking Warehousing Quantification & Distribution Procurement Figure 1: Supply Management Cycle in DOH Figure 1: Supply Management Cycle in DOH 2.2 WAREHOUSE MANAGEMENT 2.2 WAREHOUSE Warehouse Management MANAGEMENT is part of the supply chain management that optimizes and controls the day-to-day operations in the warehouse to ensure that products are Warehouse Management is part of the supply chain management that optimizes and stored and accounted for properly from the receiving up to releasing processes2. controls the day-to-day operations in the warehouse to ensure that products are stored and accounted for properly from the receiving up to releasing processes 2. This manual focuses on warehouse management operations as an important part of supply ______________________________ management of health commodities procured by and donated to the 1. Council of Supply Chain Management Professionals (CSCMP) government.2. The World Healthfollowing are Report Organization, Technical theSeries, recommended No. 957, 2010 - Annex minimum 5 standard processes in managing warehouses for storing health commodities: ______________________________ 1. Council of Supply Chain Management Professionals (CSCMP) 2. World Health Organization, Technical Report Series, No. 957, 2010 - Annex 5 Page 10 PAR T II : GUI D I N G P R I NC I P L E S 11 1. Preparation for Delivery: Is the process of preparing for deliveries from suppliers or transfers from other warehouses to ensure that incoming deliveries are properly managed. This is the process where requests for deliveries are assessed based on the storage capacity, products’ storage requirements and other warehouse activities. 2. Inspection and Receiving: The process of inspecting and receiving commodities upon arrival through routine delivery activities. This is the process where quantity and quality of delivered products are checked against the delivery documents, contract, technical specifications, and other legal standards prior to acceptance. 3. Put-Away: The process of transferring the commodities from the receiving area to the identified location for storage in the warehouse. This is the process where received products are handled using warehouse equipment in accordance with proper techniques ensuring that stocks are placed on locations appropriate to their storage requirements. 4. Storage and warehousing: The process of storing and warehousing commodities based on its storage requirements while waiting for shipment. This is the process where warehouse staff perform routine activities based on Good Storage Practices guidelines and maintain good condition of facility, tools and equipment associated with the daily operations of the warehouse. 12 WA R EHOU SE OPER ATI ON S M A N U A L 2022 5. Picking and Packing: The process of picking and packing of items from storage location to staging area according to requisition or allocation list. This is the process where preparations such as generation of shipping documents, assembling, and labeling items are done prior to shipment of items to its intended recipients. 6. Dispatch: The processing of releasing commodities based on the approved shipping documents for delivery to its intended recipients. This is the process where items are properly handed over to 3PL courier/ recipient based on the approved shipping documents. The manual also includes standard operating procedures for the following specific processes: 7. Pharmaceutical Waste Management – warehouse processes for proper handling and facilitation of waste management for health commodities in cases of damage and expiration. 8. Reverse Logistics – warehouse processes for proper management of health commodities to: a. Ensure that items are retrieved in cases of product recall notified by the manufacturer or by the Food and Drug Administration (FDA) due to manufacturing defects, contamination and other safety concerns associated with the product. b. Ensure transferring/ re-distribution of soon-to-expire items or slow-moving items between service delivery points in order to place them to locations where they will be more likely to be used. 9. Emergency Supply Chain Management – warehouse processes associated with maintaining and handling health commodities in preparation for emergencies and during emergencies (i.e., Calamities, Disasters, and other Public Health Emergencies). This process also tackles how to deal with donations during emergencies to prevent wastages and other problems associated with mismanagement of donations. 10. Cold Chain Management – warehouse processes associated with basic handling of health commodities requiring cold chain management. PAR T II : GUI D I N G P R I NC I P L E S 13 2.3 HOW TO USE THIS MANUAL The WOM contains guidelines in warehouse management, and standard operating procedures arranged according to different parts of warehouse operations. This includes process flow diagrams and training guides for each process. Specific details and procedures are discussed accordingly in their specific sections of this manual. Listed below are the processes covered in the manual. Each presents the flowchart containing all the procedures and description of the workflow process. 1. Preparation for Delivery: a. From supplier – applicable for own procurement b. From upper tier – applicable for items allocated by either central or regional level 2. Receiving: a. From supplier – applicable for own procurement b. From upper tier – applicable for items allocated by either central or regional level 3. Put-Away 4. Storage and Warehousing 5. Picking and Packing 6. Dispatch 7. Management of Pharmaceutical Waste and Unserviceable Equipment 8. Reverse Logistics a. Product recall from Manufacturer and/or FDA b. Releasing for redistribution c. Pulling product from lower tiers for redistribution 9. Emergency Supply Chain Management 10. Cold Chain Management – applicable for warehouses with cold rooms Each flowchart follows a particular legend that may be useful to the reader: Curved rectangles signify the starting and end point of a particular process. Rectangles contain processes that should be carried out by the responsible person(s) for a particular step. Diamonds signify decision points, which are answerable by a YES or NO. Each answer leads to a particular instruction for that step. Broken line rectangles indicate that the responsible person(s) is required to receive information or prepare to perform the succeeding process/procedure. Also included in this manual are Functional Flowcharts, which present redesigned flowcharts and restructured tasks and responsibilities of each warehouse personnel according to the function of a store manager, store supervisor, storekeeper, and store helper. 14 WA R EHOU SE OPER ATI ON S M A N U A L 2022 A. DEFINITION OF TERMS USED IN THIS MANUAL 3PL – Third Party Logistics is an external service provider contracted by an organization to carry out business functions (i.e. supply chain management functions). Average Monthly Consumption (AMC) – is the average of quantities of product dispensed to users or patients in the most recent months (i.e., last 3 or 6 months) Batch/ Lot No. - Distinct group of numbers, letters, or any combination thereof, designated to identify a drug or device produced during a given cycle of manufacture. Bill of Lading (BL) - Refers to a form or list of goods used for the computation of payment to be rendered to the courier for the shipment of goods to the consignee. Bin Card – a stock keeping record which hold all information about product/item placed on pallet in a certain location. Calibration – Process of adjusting the output or indication on a measuring instrument to comply with values of accuracy and applied standards. Certificate of Product Registration (CPR) – Document issued by the Food and Drug Administration (FDA) certifying that health commodities are cleared for distribution and fit for consumption. Contamination – The undesired introduction of impurities of a chemical or microbiological nature or, of foreign matter into or on to a starting material, intermediate or pharmaceutical product during handling, sampling, packaging/ repacking, storage and transportation. Cross docking – Refers to logistics mechanism or a distribution strategy where orders are sent to a collection or redistribution point (intermediate warehouses) for documentation and segregation purposes only before sending to its intended recipient/destination (Applicable to situations such as emergency, without being stored in the warehouse for a long period of time). Delivery Documents – Refers to set of documents required upon delivery of goods to DOH Warehouse(s) which include but not limited to: Purchase Order (PO)/ Contract; Notice to Proceed (NTP); approved Request for Schedule of Delivery Form (RSD); Delivery Receipt (DR); Sales Invoice (SI); Certificate of Product Registration (CPR); FDA Certificate of Analysis; Batch Notification (BN) for antibiotics; Lot Release Certificate for vaccines (LRC) and Delivery Notification Form (DNF). Delivery Notification Form (DNF) – Refers to documents that describe allocated goods with corresponding quantity, volume, end-user and estimated date of delivery provided by the consignor. Delivery Receipt (DR) – Refers to documents that describe goods with corresponding quantity and price as the basis of receipt of item(s)/service(s) provided by the supplier upon delivery. Delivery Status Report – Report generated by 3PL to track status of delivery. PAR T II : GUI D I N G P R I NC I P L E S 15 Expiration/Expiry Date - the date stated on the label of food, drug, cosmetic, device or hazardous substance after which they are not expected to retain their claimed safety, efficacy and quality or potency and after which it is no longer permissible to be utilized. Electronic Logistics Management Information System (eLMIS) – An electronic logistics management information system used to manage, collect, store, organize, and visualize logistics data which enables supply chain workforce to make operational and strategic decisions in supply management. End-user – Pertains to the specific office which owns the commodity (i.e. Health Programs). FDA Certificate of Analysis - Document issued by the Food and Drug Administration and/or other health regulatory agencies confirming that a regulated product meets its product specification after undergoing quality control and testing. FDA Test Result Database – Refers to a file or information system containing summary of items/products which have undergone FDA Test Analysis. FDA Test Status Label – Refers to a label indicating the Test Analysis Status of items which consist of the following distinction: Quarantine Commodities affixed with appropriate labels which are still waiting for the Test Analysis Result from the FDA. Passed Commodities affixed with appropriate labels which already conform to the FDA Test Analysis. Failed Commodities affixed with appropriate labels which failed to conform to the FDA Test Analysis. FEFO – Acronym for First Expiry, First Out. FIFO – Acronym for First in, First Out. Forklift – Industrial trucks operated by a certified operator used to lift and move items on pallets over short distances and different rack levels inside the warehouse/ storeroom. Gate Pass – Refers to the clearance on security measures indicating commodities for dispatch. Good Distribution and Practices (GDP) – part of quality assurance which ensures that the quality of a pharmaceutical product is maintained though adequate control throughout the numerous activities which occur during the distribution process. Good Storage Practices (GSP) – Set of Standards in maintaining quality, stability, and integrity of pharmaceuticals and non-pharmaceutical products during storage from the point of manufacture up to its utilization. Good Stocks – Items that are considered accepted once (1) inspected by Inspection and Acceptance Committee and (2) Passed the FDA Test Analysis. Items that are inspected and are not required to undergo FDA Test Analysis shall be tagged as Good Stocks as well. 16 WA R EHOU SE OPER ATI ON S M A N U A L 2022 Humidity - Refers to the concentration of water vapor in the air which indicates the likelihood of precipitation, dew, or fog. Inventory Label Form – label attached to commodities to easily identify stored items such as Product Identification Label and FDA Status Label. Inbound Summary Report – Report referring to the record of commodities received in a specified period. Inspection and Acceptance Report (IAR) – Report generated manually or thru Warehouse Management System which describe the conduct of inspection and acceptance of the Inspection Committee for items procured by and/or donated to DOH. Inspection Committee – The committee responsible for ensuring that the commodities delivered by the supplier meet the standards and technical specifications indicated in the Purchase Order/Contract. The committee is composed of the Procuring Entity/ End-user, Property/Supply Custodian, and other relevant unit. Inventory Stock Keeping Records – Set of documents (such as Bin Card, Stock Cards, Location Map, Inbound and Outbound Summary Report, and Monthly Inventory Report) containing necessary information of all commodities stored inside the warehouse / storeroom for monitoring and updating. Jack lift – Refers to a mechanical equipment used to lift and move items on pallet over short distances. Key Performance Indicator – A quantifiable measure used to evaluate the success of a given objective for performance. Location code - Distinct group of numbers, letters, or symbols, or any combination thereof, used to identify specific location (e.g. warehouse, shelf, shelving level, rack no) of an item Location Map - Refers to the blueprint of all commodities stored at various areas in the warehouse/storeroom. Lot Release Certificate (LRC) – Refers to a certificate that serves as a mechanism that provides FDA with a real-time system to continuously monitor product quality, through review and testing, of many of the biological products that it regulates. Manual Tally Sheet – is a form used by receiving officers to record data during actual delivery including vehicle information, item information, packaging information and item quantity. Material Safety Data Sheet (MSDS) – is a document from the Manufacturer or Supplier that contains information on the potential hazards (health, fire, reactivity and environmental) and how to work safely with the chemical product/item. Monthly Inventory Report – Report pertaining to the summary of items with their pertinent information for monitoring which provide a comprehensive account of stocks or supplies stored inside the warehouse/ storeroom. PAR T II : GUI D I N G P R I NC I P L E S 17 Months of Stock (MoS) – refers to the duration (in months) that the stock would last base on the recent Average Monthly Consumption. Non-Conformance Report – Report referring to non-compliance of suppliers and Forwarder to specified instructions defined by DOH. This report serves as justification for disapproval of any request and delivery. Notice of Delivery (NOD) – Refers to a form produced by the consignee to confirm successful delivery of allocated commodities, Notice to Proceed (NTP) - Refers to a formal letter from the Procuring Entity to the Supplier indicating the consent to deliver procured commodities in accordance with the Purchase Order/Contract. Outbound Summary Report – Report referring to the record of commodities released/ dispatched in a specified period. Pallets - Refers to a plastic or wood material used to stack bulk items and larger cartons. They keep things off the floor and can be used with forklifts or jacklifts to move around groups of larger items. Pest Control – Procedure on maintaining pest and vermin free warehouse, the pest- control agents used should be safe, and there should be no risk of contamination of materials and pharmaceutical products. Pharmaceutical Wastes – Are damaged, expired, unused, spilt, and contaminated pharmaceutical products, drugs, vaccines, and sera that are no longer feasible for use and need to be disposed of appropriately. The category also includes discarded items used in the handling of pharmaceuticals, such as bottles or boxes with residues, gloves, masks, connecting tubing, and drug vials. Pick List – List of items with corresponding instructions on which products shall be picked from a specific location in the warehouse/storeroom to staging area for packing in accordance with Shipment Plan and Shipping Documents. Picking Tool/Equipment - Tool/Equipment where picked items are placed such as a basket, cart, pallet, trolley or fork/jack lift as necessary to aid in transferring products from storage location to designated area for picking and packing. Procuring Entity – refers to any branch, department, office, agency, or instrumentality of the government, including state universities and colleges, government-owned and/ or -controlled corporations, government financial institutions, and local government units procuring Goods, Consulting Services, and Infrastructure Projects. Product Identification Label – Refers to a piece of paper or other material affixed to a commodity to easily identify stored items with information on the PO/Contract number, DR/SI number, product name and description, date received, end-user/ program; quantity; Batch/Lot no. and Expiry Date Property Transfer Report (PTR) - Form used to document the information associated with all commodity transfers from one office to another. 18 WA R EHOU SE OPER ATI ON S M A N U A L 2022 Purchase Order (PO) / Contract – Refers to the contract between the DOH and the Service Provider awarded by the Bids and Award Committee (BAC) and Head of Procuring Entity (HOPE) through Public Bidding and other modes of procurement. Quarantine Area – Space in the warehouse in which commodities are isolated physically or by other effective means while a decision is awaited on their acceptance, rejection and/or reprocessing. Receiving Area – Space in the warehouse in which commodities are checked prior acceptance as to its quality and quantity in accordance with Purchase Order/ Contract and other Delivery Documents. Request for Analysis (RFA) – Form issued by FDA for filing request for Test Analysis. Request for Inspection (RFI) – Official letter request from Supply Officer to the Inspection Committee for the conduct of inspection on commodities scheduled for delivery to DOH warehouse(s). Request for Schedule of Delivery (RSD) Form – Official form accomplished by suppliers to request schedule of delivery to warehouses. Request Requisition and Issueance Slip (RIS) – Form used to document the information associated with commodity transfer within the office based on request. Sales Invoice (SI) – Refers to documents that describe goods with corresponding quantity and price as a basis of payment to the Supplier for the item(s)/service(s) provided. Shipping Documents – Documents that serve as proof of transaction of shipment or transfer of property/item/goods from one office/department to another such as Shipment Plan, PTR, BL and RIS. Staging Area – Space in the warehouse where packing or repacking of commodities takes place based on the provided approved Allocation List(s) prior to dispatch and distribution. Stock Card – a stock keeping record which holds all information about a single product with different lot numbers / batch numbers, different expiration date and different location inside the warehouse/storeroom under a single Purchase Order/ Contract. It is the consolidation of all Bin Cards of a single item placed in different areas inside the warehouse/storeroom. Stock Keeping Unit (SKU) – Refers to codes projected as a distinct group of numbers, letters, or any combination thereof, designated to identify commodities (Pharmaceuticals and Non-pharmaceuticals) stored inside the warehouse/storeroom. PAR T II : GUI D I N G P R I NC I P L E S 19 Storage Area – Appropriate place for the storage of pharmaceuticals and non- pharmaceuticals in accordance to the commodity’s storage requirement. Summary of Supplies and Materials Issued (SSMI) – Form issued by Commission on Audit (COA) for filing up reports on the summary of items (Supplies and Materials) issued in a certain period as reference on books of account. Temperature and Humidity Monitoring - Refers to the process of observing and recording of temperature and relative humidity in a specified time and duration. Temperature and Humidity Monitoring Chart – Refers to a monitoring tool for consistent reading and recording of Temperature and Relative Humidity inside the warehouses/storerooms. Thermohygrometer – Diagnostic measuring device used for indoor climate and environmental monitoring of both temperature and relative humidity. Thermohygrometer Profile Database – Refers to a set of data maintained by the store/warehouse manager to access the description, location, and status of each thermohygrometer inside the warehouse. Ventilation - is the intentional introduction of ambient air into the warehouse and is mainly used to control indoor air quality by diluting and displacing indoor pollutants; as well as to promote thermal comfort or dehumidification. Warehousing Management System (WMS) – A collection of integrated software applications, designed to support and optimize warehousing and distribution management. Some WMS is integrated already in an electronic logistics management information system. LIST OF ANNEXES Annex No. Title: 1 Request for Schedule of Delivery 2 Delivery Notification Form 3 Non-conformance Report 4 Request for Inspection 5 Inspection and Acceptance Report 6 Bin Card & Stock Card 7 Location Map 8 Inbound Summary Report 9 Outbound Summary Report 10 Monthly Inventory Report 11 Notice of Delivery 12 Product Identification Label 13 FDA Status Identification Label 14 Corrective Requisition on Warehouse Operations 15 Warehouse Operations Routine Checklist 16 Incident Report 17 Pull out Request for Replacement 18 Temperature & Humidity Monitoring Chart 19 Thermohygrometers Profile & Calibration Plan Database 20 Pick List 21 Property Transfer Report 22 Bill of Lading 23 Request Requisition and for Issue Slip 24 Gate Pass 25 Manual Tally Sheet 26 FDA Test Result Database 27 Request for Analysis 28 Warehouse Essentials 22 WAREHOUSE OPERATIONS MANUAL 2022 ANNEX 1 Republic of Republic of the the Philippines Philippines Department of Health Department of Health Annex 1 OFFICE OFFICE NAME OF OFFICE OFFICE ADDRESS OFFICE ADDRESS ADDRESS REQUEST FOR SCHEDULE OF DELIVERY (RSD) Date of RSD Control Number ᬅ ᬆ Request I. REQUESTING SUPPLIER'S ACTION / DETAILS OF REQUEST For: From: ᬇ ᬈ Signature over Printed Name and Position Company Name ᬉ Signature over Printed Name and Position PO / Contract No: PO/ Contract Type of Delivery:________ᬊ________ _____ᬋ_____ Date:__________ᬌ___________ Weight of Quantity per Total number of Dimension of Item Description Tranche Quantity carton in Carton Carton carton in cm kg ᬍ ᬎ ᬏ ᬐ ᬑ ᬒ ᬓ Requested Date End user: ᬔ ᬕ of Delivery: II. OFFICE'S ACTION / RESPONSE Approved Recommendation: ᬖ ᬗ Quantity: Reason for disapproval Volume in ᬘ द (If disapproved): CBM: Place of Other remarks: ध न Delivery: Recommended by: Noted by: ऩ प Signature over Printed Name and Position Signature over Printed Name and Position IiI. INSTRUCTION TO SUPPLIERS फ Request Requestfor forDelivery Schedule Shall DeliverySchedule Shallbe befilled filledup upby byintended intendedrecipient recipientwith withthe thefollowing followinginformation: information: 1.1. RSD Control RSD ControlNumber Number 15. Weight of carton in kilograms (kg) 2. Date RSD was prepared/ filled-up 16. End-user / Program owner of the commodities for delivery 2. Date RSD was prepared/ filled-up 3. Name of the Head of Office 17. Requested Date of Delivery 4.3. NameName Company of theof Head of Officesupplier the requesting 18. Recommended Decision: Indicate whether approved or 5.4. NameCompany of the representative Name of the of requesting the requesting supplier disapproved supplier/company 19. Quantity approved based on the space availability in the 5. 6. Name of the representative of the requesting Type of Delivery: Indicate whether the delivery is Partial or supplier/companywarehouse. Put N/A if the delivery is disapproved 6. Full. Type of Delivery: Indicate whether the delivery is Partial20.or Full. Reason for disapproval. Attached the Non-conformance 7.7. PO orPO Contract Number or Contract of the delivery Number of the delivery form as necessary 8. Date indicated in the PO or Contract 21. Volume of delivery in Cubic Meter (CBM) or in number of 8. Item Date 9. indicated in the PO or Contract description as indicated in the PO/Contract pallets 9. If applicable, 10. Item description indicate inas indicated which trancheinthe thedelivery PO/Contract belongs 22. Other remarks as necessary 10. to (i.e: If 1st tranche, 2nd applicable, tranche, indicate 3rd tranche) in which based tranche the on the delivery 23. to belongs Place (i.e:of1st delivery: Name tranche, 2ndoftranche, the warehouse and address 3rd tranche) based on PO/Contract or NTP 24. Name of Store Manager the PO/Contract or NTP 11. Quantity of items requested for delivery 25. Name of Supply Officer 11. Quantity 12. Quantity of in of items items requested a carton (tertiaryfor delivery packaging) 26. Other instructions and reminders to suppliers as necessary 13. Total number of cartons requested for delivery 14. Dimension of carton (height, width, length) in centimeter (cm) ANNEXES 23 ANNEX 2 Republic Republicof of the Philippines the Philippines Department Department ofofHealth Health Annex 2 OFFICE OFFICE NAME OF OFFICE OFFICE ADDRESS OFFICE ADDRESS DELIVERY NOTIFICATION FORM (DNF) DNF Control ᬅ Date ᬆ Number DETAILS OF SHIPMENT For: From: ᬇ ᬈ Signature over Printed Name and Position Signature over Printed Name and Position Required Estimated Unit of Quantity per Total Quantity Expiration Space in End-user / Item Description Date of Measurement Cartons for delivery Date CBM/ or in Program Arrival pallet ᬉ ᬊ ᬋ ᬌ ᬍ ᬎ ᬏ ᬐ Estimated Total CBM / # of Pallets ᬑ required Other Remarks ᬒ Delivery Notification Form Shall be filled up by intended recipient with the following information: 1. DNF Control Number 2. Date DNF was prepared/ filled-up 3. Name & Signature of the Head of Office (Consignor) 4. Name & Signature of the Head of Office (Consignee/ Receiving Office) 5. Item description as indicated in the PO/Contract 6. Unit of Measure as indicated in the PO/Contract 7. Quantity per carton 8. Total Quantity for Delivery Delivery Notification 9. Form Shall Expiration Date be filled up by intended recipient with the following information: 10. Computed volume in CBM or in pallets 11. End-user or Program Owner of commodities for delivery 1. DNF Control 12. Number Estimated Date of Arrival 2. Date DNF 13. wasIfprepared/ multiple itemsfilled-up are in the DNF, compute and indicate the total volume of delivery in CBM or in pal 3. 14. Other remarks Name & Signature of the Head as necessary of Office (Consignor) 4. Name & Signature of the Head of Office (Consignee/ Receiving Office) 5. Item description as indicated in the PO/Contract 6. Unit of Measure as indicated in the PO/Contract 7. Quantity per carton 8. Total Quantity for Delivery 9. Expiration Date 10. Computed volume in CBM or in pallets 11. End-user or Program Owner of commodities for delivery 12. Estimated Date of Arrival 13. If multiple items are in the DNF, compute and indicate the total volume of delivery in CBM or in pal 14. Other remarks as necessary 24 WAREHOUSE OPERATIONS MANUAL 2022 ANNEX 3 Republic of the Philippines Department of Health Republic of the Philippines Annex 3 Department OFFICE NAME OFof Health OFFICE OFFICEOFFICE ADDRESS ADDRESS OFFICE ADDRESS NON-CONFORMANCE REPORT I. DETAILS OF SUPPLIER / SOURCE Supplier / Source: ᬅ Supplier / Source Address: ᬆ Email Address: ᬇ Contact Number: ᬈ PO / Contract / Document ᬉ Tracking No.: Date of PO / Contract / ᬊ Document Tracking II. TYPE OF NON-CONFORMANCE ᬋ A. During Request for Delivery B. During Delivery RSD No.: ᬌ RSD No.: ᬑ DNF No./ Pre alert reference: ᬍ DNF No.: ᬒ Incomplete document ᬎ Incorrect Warehouse Location ᬓ Incorrect document ᬏ Arrived beyond cut-off time ᬔ Others: _________ᬐ_________ Incorrect Volume ᬕ Quantity / UOM: ________________ Incomplete document submitted ᬖ Incorrect document submitted ᬗ Invalid date of delivery ᬘ Incomplete/No samples submitted द With Findings/Discrepancy against PO/Contract ध Damaged - Quantity/UOM:____न_____ Expired - Quantity/UOM:_____ऩ____ Inappropriate handling during transport प Excess quantity delivered against the approved RSD Quantity / UOM: ______फ__________ Others: ________ब__________ III. COMPLETE DESCRIPTION OF ABOVE-SELECTED CELL(S) भ Prepared By: म Validated By: य Acknowledge By: र Signature: Name: Designation: Date: Non-conformance report shall be filled up by the Store Supervisor with the following information: 1 If commodity for delivery is your own procurement, indicate company name of vendor/supplier. If commodity for delivery is allocated by the upper tier, indicate entity name of consignor (i.e. DOH central or Regions). ANNEXES 25 Non-conformance report shall be filled up by the Store Supervisor with the following information: 1. If commodity for delivery is your own procurement, indicate company name of vendor/supplier. If commodity for delivery is allocated by the upper tier, indicate entity name of consignor (i.e. DOH central or Regions). 2. Company Address of the vendor/supplier/consignor. 3. Email address of the vendor's/supplier's/consignor's representatives. 4. Contact number of the vendor's/supplier's consignor's representatives. 5. Control number indicated in the PO/Contract/ Donation. 6. Date indicated in the PO/Contract/ Donation. 7. Tick "A" box if the nature of non-conformance of the vendor/supplier/consignor is during delivery request scheduling while tick "B" box if the non-conformance of the vendor/supplier/consignor is during the actual delivery in the warehouse. 8. Indicate RSD control number (if the delivery request is from your own procurement). 9. Indicate DNF control number (if the delivery request is from the upper tier: DOH Central/Region). 10. Tick this box if the document(s) relative to the delivery request is incomplete. 11. Tick this box if the document(s) relative to the delivery request is incorrect. 12. Tick this box for other reason(s) in disapproving the delivery. Indicate the reason in the line provided. 13. Indicate RSD control number (if the delivery is from your own procurement). 14. Indicate DNF control number (if the delivery is from the upper tier: DOH Central/Region). 15. Tick this box if the item delivered is not intended for the warehouse. 16. Tick this box if the item delivered arrived beyond the defined cut-off time in the warehouse. 17. Tick this box if the volume of the item delivered is more than the volume (in CBM/Pallet) requested for delivery. Indicate the quantity of items rejected if applicable. 18. Tick this box if the required document(s) for the delivery is incomplete. 19. Tick this box if the required document(s) for the delivery is incorrect. 20. Tick this box if the schedule of delivery for the item is incorrect. 21. Tick this box if the supplier do not provide the right quantity of samples for required FDA test analysis. 22. Tick this box if the item has findings/discrepancy against the PO/Contract upon inspection with the inspection committee. 23. Tick this box if only a portion of the delivery will be rejected due to damage. Indicate the quantity and UOM. 24. Tick this box if only a portion of the delivery will be rejected due to expiry. Indicate the quantity and UOM. 25. Tick this box if the delivered items were handled inappropriately by the 3PL/courier (i.e., not compliant with Good Distribution Practices). 26. Tick this box if there is an excessive quantity delivered against the approved quantity indicated in the RSD. Indicate the quantity and UOM. 27. Tick this box for other reason(s) for rejection that are not indicated above. Site the reason on the provided space. 28. Briefly describe the nature of non-conformance. 29. Indicate the name, signature, designation of personnel who prepared the report. 30. Submit to the supply officer/head of office for validation and signature. 31. Indicate the name, signature, designation of the concerned personnel (3PL/Courier/Supplier/Upper tier). 26 WAREHOUSE OPERATIONS MANUAL 2022 ANNEX 4 Republic of Republic of the the Philippines Philippines Department of Department of Health Health Annex 4 OFFICE NAME OF OFFICE OFFICE OFFICE ADDRESS OFFICEADDRESS ADDRESS REQUEST FOR INSPECTION (RFI) RFI Control Number: ᬅ Date: ᬆ Chairperson (Name) ᬇ Inspection Committee Department of Health ᬈ Dear Sir/Madam, ᬉ May we request for the inspection of the approved delivery of Item(s) with the following details: Approved Date of Delivery Location of Delivery / Item Description RSD Control No. / Inspection Inspection ᬊ ᬋ ᬌ ᬍ Copy of RSD/s and PO/s are attached herewith for your reference. Please coordinate directly with ______ᬎ______, Store Manager, for the above mentioned inspection/delivery at ____ᬏ_____ Thank you. Very truly yours, ᬐ __________________ Request for Inspection shall be filled up by the office clerk with the following information: 1. RFI control number (manual or system generated). 2. Date filled-up/ Request for Inspectiongenerated. shall be filled up by the office clerk with the following information: 3. Name of the Inspection committee chair. 1. RFI control number (manual or system generated). 4. Indicate the Entity 2. Date filled-up/ generated. Name. 5. Indicate the right salutation. 3. Name of the Inspection committee chair. 6. List down all item(s) for inspection. 4. Indicate the Entity Name. 7. Indicate the RSD control number reference for inspection. 5. Indicate the right salutation. 6.8. Indicate List down thealldate when item(s) forthe item(s) will be delivered for inspection. inspection. 9. Indicate the location of 7. Indicate the RSD control number the warehouse wherefor reference items will be delivered. inspection. 8.10. Indicate Indicate the the date namewhen of thethestore/warehouse manager. for inspection. item(s) will be delivered 9. Indicate the location of the warehouse where itemsmanager 11. Indicate the contact details of the store/warehouse for coordination purposes. will be delivered. 12. Submit to the supply officer/head of 10. Indicate the name of the store/warehouse manager.office for signature. 11. Indicate the contact details of the store/warehouse manager for coordination purposes. 12. Submit to the supply officer/head of office for signature. ANNEXES 27 ANNEX 5 Republic of the Philippines DEPARTMENT OF HEALTH _______________________________________ NAME Name ofOF OFFICE Office ___________________________________________________________ ADDRESS Address INSPECTION AND ACCEPTANCE REPORT ENTITY NAME: FUND CLUSTER: Supplier: IAR NO: Address: IAR Date: P.O./Contract Number Invoice No.: P.O./Contract Date Invoice Date Requisitioning Office / End-user D.R. No.: Payment Terms: D.R. Date: Grand Total Quantiy Procured based on Delivery Date/s: PO/Contract: Grand Total Amount of Procured Place of Delivery: Quantity: Inspected Quantity: Unit of Measure: Inspected Total Cost: Unit Cost: Dimension & Volume of carton/case: Responsibility Center Code: Height____ Width____ Length___ Weight___ DESCRIPTIONS OF ITEMS PURCHASED ITEMS DELIVERED AS PER INSPECTION (ACTUAL PRODUCT) AS PER PURCHASED ORDER COMPLIANT NON-COMPLIANT Item description Brand Name / Model (If applicable): Packaging: Shelf-Life based on PO/Contract: Labelling Requirements -Blister pack, Foil strip/ Bottle, Box and Kits: Labelling Requirements - corrugated carton: Manufacturer (If indicated ):: Other Specifications (please indicate if necessary): DESCRIPTION OF FINDINGS / NON-COMPLIANCE: BREAKDOWN OF ACTUAL ITEM AND QUANTITY DELIVERED 4th 1st Tranche 2nd Tranche 3rd Tranche Others_____________ Tranche Number/Type of Delivery: Partial________ Complete Completion______ Lot / Batch Remaining Shelf Expiry Item Description no. (If Manufacturer Mfd. Date life (months) Unit Quantity Date applicable) upon delivery Total Quantity and unit delivered: Date Inspected: Are items inspected subject to FDA Test Analysis?: YES NO If yes, How many boxes/bottles are taken for FDA Test Analysis?: ALL ITEM/S INSPECTED ARE SUBJECT TO FINAL ACCEPTANCE OF END - USER INSPECTION TEAM ACCEPTANCE Please encircle if the item/'s delivered are: Accepted Rejected Print Name and Signature Date:______ Date:______ Position Title ___________ End-user / Representative Remarks(if rejected):____________________________________________________ Print Name and Signature _____________________________________________________________ Position Title___________ Technical Inspection Committee _____________________________________________________________ Print Name and Signature Position Title___________ Print Name and Signature Technical Inspection Committee End-user Print Name and Signature Print Name and Signature Position Title___________ Head of Supply Office (Property Custodian) Technical Inspection Committee 28 WAREHOUSE OPERATIONS MANUAL 2022 "IAR shall be filled up by the Inspection Committee with the following information: 1. Entity name (Procuring Entity). 2. The source of the funds used to procure the item for inspection (i.e., GOP, loan, grant, trust fund, etc.). 3. The company name of the supplier as stated in the PO/Contract. 4. The adress of the supplier as stated in the PO/Contract. 5. The PO/Contract number. 6. The PO/Contract Date. 7. The specific end-user (owner of the item - i.e., Health Programs). 8. The payment terms as stated in the PO/Contract/Delivery Documents. 9. The grand total quantity of items procured based on the PO/Contract/Delivery Documents. 10. The grand total amount of items procured based on the PO/Contract/Delivery Documents. 11. The quantity of items inspected on the date of inspection. 12. The amount of items inspected on the date of inspection. 13. The responsibility center code assigned by the accounting unit. 14. The manual/system generated IAR control number. 15. The date that the IAR created. 16. Put the invoice number as indicated in the delivery documents from the supplier. Put N/A if the supplier does not provided the Sales Invoice. 17. Put the date of the invoice number as indicated in the delivery documents from the supplier. Put N/A if the supplier does not provided the Sales Invoice. 18. Put the Delivery Receipt number as indicated in the delivery documents from the supplier. 19. Put the date of the Delivery Receipt as indicated in the delivery documents from the supplier. 20. The delivery date(s) of items. 21. The place of delivery (warehouse name & location). 22. Put the item's unit of measure as indicated in the PO/Contract/Delivery Documents. 23. Put the unit cost of the item as indicated in the PO/Contract/Delivery Documents. 24. Put the dimension of carton/package (height, width, and length) in centimeter and the weight in kilograms for the computation of volume in CBM/Pallet. 25. Put all the specifications indicated in the PO/Contract: Item description; Generic/Brand Names; Model; Packaging; Shelf-life requirement; labelling requirements and manufacturer. You may revise and align these specifications to capture what is indicated in the PO/Contract. Add rows as necessary. 26. Put a check () in the "Compliant" column if the actual item inspected complies with the specification indicated in the PO/Contract, otherwise put a check () in the "Non-compliant" column. 27. Put a brief description of the findings during the inspection. 28. Tick the appropriate box as stated in the PO/Contract and/or delivery documents (1st, 2nd, 3rd, 4th tranches). Indicate partial (if the delivery is only a portion of what is indicated in the PO/Contract), indicate complete (if the delivery constitute all the items and quantity indicated in the PO/Contract), indicate for completion (if there are previous partial deliveries and the one currently delivered is only for completion). 29. Item description as stated in the PO/Contract. 30. The lot/batch number as stated in the delivery document. If there are multiple batches/lots, insert more rows to input all the batches/lots in the delivery. 31. The Manufacturer including its address as stated in the PO/Contract/Delivery Documents. 32. The manufacturing date of the item as indicated in the actual product. 33. The expiration date of the item as indicated in the actual product. 34. Compute the remaining shelf life by counting the remaining months of the product before expiry from the time of delivery. 35. Unit of Measure as indicated in the PO/Contract. 36. Quantity received/inspected per batch/lot. 37. Total quantity delivered/inspected. 38. Date of inspection. 39. Tick the appropriate box. "Yes" if the product requires FDA test analysis; "No" if the product is not subject to FDA test analysis. Coordinate with the FDA, procuring entity and other relevant offices to determine if FDA test analysis is a requirement for the item before distribution. 40. If the item is subject to FDA test analysis, indicate the quantity taken as samples. The samples for FDA test analysis must be on top of the quantity indicated in the PO/Contract. 41. The name, signature and designation of inspection committee representatives/members 42. The end-user or procuring entity must encircle "accepted" if the delivered item conforms with the technical specifications and other requirements indicated in the PO/Contract upon inspection. Otherwise, encircle "rejected" and indicate the corresponding remarks describing the reason(s) for rejection. 43. Printed name and signature of the end-user or procuring entity. 44. Printed name and signature of the the supply officer (property custodian). ANNEX 6A Bin Card shall be filled up by the Store Keeper with the following information: 1. Stock Keeping Unit Code - refer to the latest SKU code developed by the Stock Keeping DOH Central Office. Unit (SKU) Code: 2. Location area code or rack number where the item is located. Develop your BIN CARD own location area code in your warehouse for easier reference. This location ANNEXES Location area Code / Rack area code shall also be reflected in your location map. Number: 3. PO/Contract number for the item. P.O. / Contract #: Unit Cost: 4. Company name of supplier. Supplier: Batch/ Lot No(s). 5. Item description as indicated in the PO/Contract. Expiration 6. If the item is a pharmaceutical product, indicate the dosage form as stated in Item Description: Date(s) the PO/Contract (i.e., tablet, capsule, suspension, syrup, etc.) Dosage Form (If End User(s): 7. If the item is a pharmaceutical product, indicate the dosage strength as stated applicable) Dosage Strength (If in the PO/Contract (i.e., 250mg ,500mg, 1g, etc.) applicable) 8. Unit of measure as indicated in the PO/Contract (i.e., pieces, Blister packs, Unit of Measure: bottles, box, kits, etc.) 9. Unit cost as indicated in the PO/Contract. 10. Batch/Lot number(s). If there are multiple batches/lots in the bin, ensure to DR/SI/RIS/ Recipient / account all of it including its quantities. Quantity PTR/BL No. Remarks Date 11. Expiration date(s). Make sure to account all batches/lots including its expiration dates and quantitties If there are expiration date due to multiple Received Issued Balance Total Cost 0 #VALUE! batches/lots, ensure to account all of it including its quantities. 12. End-user (i.e., Health programs). 13. Date of the transaction. 14. Quantity received. 15. Quantity issued. 16. Difference between the quantity received/stock on hand and the quantity issued. 17. Amount of the stock on hand. 18. Corresponding document for the transaction (receive or issuance). Put the Delivery receipt number or Sales Invoice receipt number if the transaction is "receiving" of item from the supplier. Put PTR/BL/RIS number if the transaction is "issuance". PTR/BL/RIS number can also be applicable as "receiving" if the item is an allocation by the upper tier (DOH central or Regional offices). 19. Put other remarks such as the recipient of the item issued or the consignor of the received items. 29 30 Stock Card shall be filled up by the Store Supervisor with the following ANNEX 6B information: 1. Stock Keeping Unit Code - refer to the latest SKU code developed by the DOH Central Office. Stock Keeping Unit STOCK CARD 2. PO/Contract number for the item. (SKU) Code: 3. Company name of supplier. 4. Item description as indicated in the PO/Contract. P.O. / Contract #: Entity Name: Supplier: Fund Cluster: