Food Plant Pumps PDF
Document Details
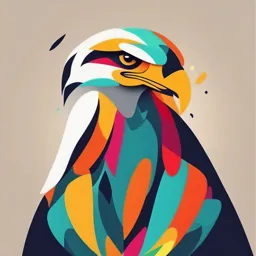
Uploaded by WellBehavedWilliamsite368
Karunya Institute of Technology and Sciences
Dr. Wasiya
Tags
Summary
This document provides an overview of food plant pumps, including different types of pumps such as centrifugal, reciprocating, rotary gear, vane, diaphragm, and peristaltic pumps. Topics covered include construction, working principles, and applications of these pumps.
Full Transcript
Unit-1 Food Plant Pumps Dr. Wasiya Syllabus ► Pumping theory- head developed-Types of pumps-Centrifugal pumps- Reciprocating pumps- piston pump-Rotary gear pumps- vane pumps- and diaphragm pumps-peristaltic pump-construction- working principles and applications (S...
Unit-1 Food Plant Pumps Dr. Wasiya Syllabus ► Pumping theory- head developed-Types of pumps-Centrifugal pumps- Reciprocating pumps- piston pump-Rotary gear pumps- vane pumps- and diaphragm pumps-peristaltic pump-construction- working principles and applications (Simple problems). Rotary Gear pump ► The gear pump is perhaps the most common rotary type and consists of two inter-meshing gear wheels inside a casing; one gear is driven and the other idles. ► The gears rotate such that they move in the direction of flow when close to the casing, allowing liquid to be pushed forward in the spaces between consecutive teeth. ► Liquid is discharged before the teeth mesh together. ► In a lobe pump the teeth on a wheel are replaced by two, three or four lobes which operate in a similar manner. ► The gear pump is self-priming. ► There is some leakage or slip between the gears and the casing but this decreases as the fluid viscosity increases. ► The pump is therefore particularly useful for very viscous liquids but cannot be used for suspensions. ► Gear pumps will deliver against very high pressures and the delivery is more or less constant with pressure. Gear pumps are positive displacement (or fixed displacement), meaning they pump a constant amount of fluid for each revolution. Some gear pumps are designed to function as either a motor or pump. Spur Gear Pump Classification ► A gear pump uses the meshing of gears to pump fluid by displacement There are two main variations of gear pumps; 1. External Gear Pump. 2. Internal Gear Pump. ► External gear pumps which use two external spur gears ► Internal gear pumps which use an external and an internal spur gear. Principle ► While the pump keeps on rotating, the fluid also moves as the cavities tend to move. ► There comes a time when the seal present between the outlet part and the fluid so accumulated is broken. ► This is the time when the fluid is forced to come out of the pump because of the forced volume. ► This cycle repeats again and again and that is how new cavities get opened and the fluid is transported. External Gear Pumps ► External gear pumps are a popular pumping principle and are often used as lubrication pumps in machine tools, in fluid power transfer units, and as oil pumps in engines. Large-capacity external gear pumps typically use helical or herringbone gears Small external gear pumps usually operate at 1750 or 3450 rpm and larger models operate at speeds up to 640 rpm. External gear pumps have close tolerances and shaft support on both sides of the gears. Because of this, external gear pumps are popular for precise transfer and metering applications involving polymers, fuels, and chemical additives. Construction Working Principle ► External gear pumps are similar in pumping action to internal gear pumps in that two gears come into and out of mesh to produce flow. The external gear pump uses two identical gears rotating against each other -- one gear is driven by a motor and it in turn drives the other gear. 1. Liquid flows into the cavity and is trapped by the gear teeth as they rotate. 2. Liquid travels around the interior of the casing in the pockets between the teeth and the casing. 3. Finally, gears forces liquid through the outlet port under pressure. Working Working Applications ► Common external gear pump applications include, but are not limited to: Various fuel oils and lube oils Chemical additive and polymer metering ► Chemical mixing and blending (double pump) ► Industrial and mobile hydraulic applications (10g splitters, lifts, etc.) ► Acids and caustic (stainless steel or composite construction) ► Low volume transfer or application. Internal Gear Pumps Internal gear pumps are exceptionally versatile. While they are often used on thin liquids such as solvents and fuel oil, they excel at efficiently pumping thick liquids such as asphalt, chocolate, and adhesives. The useful viscosity range of an internal gear pump is from 1cPs to over 1,000,000cP Working Principle 1. Liquid enters the suction port between the rotor (large exterior gear) and idler (small interior gear) teeth. 2. Liquid travels through the pump between the teeth of the "gear-within-a-gear" principle. The crescent shape divides the liquid and acts as a seal between the suction and discharge ports. 3. The pump head is now nearly flooded, just prior to forcing the liquid out of the discharge port. Intermeshing gears of the idler and rotor form locked pockets for the liquid which assures volume control. 4. Rotor and idler teeth mesh completely to form a seal equidistant from the discharge and suction ports. This seal forces the liquid out of the discharge port. Internal Gear Pump –Working Internal Gear Pump Applications ► Common internal gear pump applications include, but are not limited to: All varieties of fuel oil and lube oil Resins and Polymers Alcohols and solvents Asphalt, Bitumen Vane pumps ► These pumps consists of a slotted rotor splined to the drive shaft which rotates inside a cam ring in pump casing. ► Vanes are fitted to the rotor slots matching with the inner diameter of the ring. ► During the rotation of the rotor, the centrifugal force and the system pressure behind the vanes push the radially movable vanes towards the outside. ► The vanes take position with their external edge touching with the internal running area of the cam. ► Pumping chamber is thus formed between the vanes and are enclosed between the rotor, vane and two side plates. ► At the suction side a partial vacuum is created as the space between the rotor and ring increases. ► Liquid entering here is tapped in pumping chambers and then is pushed to the outlet as the space decreases. ► The displacement of the pump depends on the width of the ring and rotor and on the “throw” of the cam ring. ► Most fixed displacement pumps utilize the balanced cartridge design. ► In this design the cam is elliptical rather than a circle and permits two set of internal ports. ► The cam is designed as double eccentric such that each vane is involved in the delivery process twice per revolution. ► The outlet ports are 180 degree apart so, the pressure forces on the rotor are cancelled out preventing side loading of the drive shafts and bearings. ► In balanced vane pump, the discharge is fixed. ► But it can be modified to increase or decrease the discharge by putting interchangeable rings by different cam sizes. ► The vane pumps are available in various designs covering the low to medium volume ranges with operating pressures upto 200 atmospheres. ► They are reliable, efficient and easy to maintain. ► Various control units like the pressure controller and horse power controller etc are provided by the manufacturer, as per customer’s requirement. ► Cleanliness and the proper liquid are essential to long life of the pump. Unbalanced Vane pump Balanced Vane pump Vane types ► Rotary vane pumps can be of two types: ► 1. Swinging vane type ► 2. Sliding vane pump ► Swinging vane pump has a series of hinged vanes which swing out as a rotor turns, trapping liquid and forcing it out the discharge pipe of the pump. ► In sliding vane (blade) pumps the operation is also based on the principle of increasing the size of the cavity to form a vacuum allowing the space to fill with fluid and then forcing the fluid out of the pump under pressure by diminishing the volume. Swinging Vane Pump Sliding Vane Pump Sliding Vane type ► The Sliding Vanes or blades fit into slots in the rotor. ► Ahead of the slots and in the direction of rotation, grooves admit the liquid being pumped by the vanes, moving them outward with a force or locking pressure which varies with the pressure that the pump is operating against. ► The groves also serve to break the vacuum on the admission side. ► The operating cycle and the alternate action of centrifugal force and hydraulic pressure hold the vanes in contact with the casing. ► Vane type pumps can be made as single stage and double stage pumps. ► The double stage vane type pump may be assembly of two single stage pumps mounted end to end on a single shaft. ► A combination of vane type pump is also available, which may be a combination of two pumps mounted on a common shaft; the larger pump may be pumping at a low pressure and the smaller pump may be delivering at higher pressure. ► This type of pump may be called as high-low pump. ► In variable volume vane pump, a pressure compensator used to control maximum system pressure. ► Pump displacement is changed automatically to supply the exact rate of flow required by the system. ► If the pump displacement changes, system pressure remains nearly constant at the rate selected by the compensator settings. Characteristic features and Applications of Various pumps Thank You