CP-004 Lean Control Tools- 5S and Kanban.pptx
Document Details
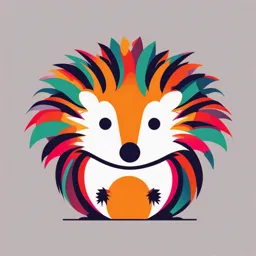
Uploaded by HottestNickel
Tags
Full Transcript
CERTIFIED LEAN SIX SIGMA PHASE CONTROL INTRODUCTION This course has been designed to build your knowledge and capability to improve the performance of processes and subsequently the performance of the business of which you are a part. The focus of the course is process centric. Your role in pro...
CERTIFIED LEAN SIX SIGMA PHASE CONTROL INTRODUCTION This course has been designed to build your knowledge and capability to improve the performance of processes and subsequently the performance of the business of which you are a part. The focus of the course is process centric. Your role in process performance improvement is to be through the use of the methodologies of Six Sigma, Lean and Process Management. By taking this course you will have a well rounded and firm grasp of many of the tools of these methodologies. We firmly believe this is one of the most effective classes you will ever take and it is our commitment to assure that this is the case. CONTROL PHASE Lean Tools- 5S 4 WHAT IS 5S? 5. Sustain 1. Sort Control and Remove improve unnecessary 5S is one of the most important basic methods of lean management and lean production which 2. Set in order Arrange and o has the target to generate simplify value without wastage. o is an ongoing cycle to foster continuous improvement for 4. Standardize higher productivity. Define rules o is a management tool to create 3. Shine commitment and ownership. Clean 5 WHAT IS THE BENEFIT OF 5S? Reduction of risks for accidents at workplaces and in Safety processes caused by spills, excess of equipment/tools on the floor, insufficient information flow etc. Reduction of risk of contamination. Reduction of faulty operation. Quality Reduction of business risk from poor master data and poor communication between 5S is one of the most cost- interfaces. effective lean techniques Reduction of searching and waiting time. available. Efficiency Reduction of movements. 5S is foundational to all other lean Reduction of inventory. techniques. 5S makes the perfect starting Mindset Increased employee pride. Established ownership of everyone in the point for bringing the benefits of organization. lean to your workplace. 5S has much more benefits than Impressive workplace design reflects the high only keeping workplaces clean Customer claim for quality, reliability and sustainability. and tidy. Sustainable improvements of order fulfillment. 6 5S IS BACKBONE OF WORLD- CLASS MANUFACTURING 5S is a core element of lean thinking and a visual workplace and is a fundamental platform for world-class manufacturing There is no end to the 5S process; it is a continuous process to develop simplified work environments and reduce wastage (see TIMWOOD) while improving quality and safety “5S is not just a methodology, it is a culture that has to be built in to any organization which aims for spontaneous and continuous improvement of working environment and working conditions. The key to the Toyota Way and what makes Toyota stand out is not any of the individual elements…But what is important is having all the elements together as a system. It must be practiced every day in a very consistent manner, not in spurts.” Taiichi Ohno Be consistent, and you can expect impressive long- term results 7 WHAT ARE THE 7 TYPES OF WASTAGE? 5S is the base methodology to avoid the 7 types of wastage. WHO IS THIS UNCOVE R THEM They cost our Money, Time and Nerves Skills is considered as the 8th Waste 8 5S ADDRESSES TIMWOOD – 7 WASTES They cost our Money, Time and Nerves 9 WHAT IS HOUSEKEEPING? Traditionally, Housekeeping has been related to cleaning up the working area: Managers visit their factories only a few times a year. On the rare occasions of inspecting company facilities, they have only the vaguest idea about what occurs there. Knowing this, their subordinates prepare for such inspections by tidying up the sites, adding a new coat of paint here and straightening up the shelves there. Following the inspection tour, everyone congratulates themselves on a job well done. The show is over. Hirozuki Hirano (5 pillars of the visual workplace) 1 DIFFERENCE BETWEEN 0 HOUSEKEEPING & 5S? Housekeeping is the basis of a safe From sweeping dust to keep From occasional manual clean environment but a good housekeeping at the up of master data … keeping the area clean plant… and tidy is not enough. 5S takes housekeeping to a higher level keeping the basis of Trolley located housekeeping and at the dust adding a new culture to generation the company that will source for enable continuous avoiding the improvement and dust is spread so higher productivity. less sweeping will be needed 5S is applicable in all production and supply chain areas e.g... to defining a way to avoid.. to defining a process that maintenance, offices, prevent incorrect master data the dust to spread around warehouse, lab, from occurring customer service, planning, master data, 1 IS HOUSEKEEPING SUSTAINABLE? 1 Good Housekeeping helps to organize and clean. Looking closer to the office with good house keeping we see… – Folders are not identified so you need to open them to know what they contain – Different pens in different colors, some pens do not work but are still in the same location – Working documents of the different tasks are mixed up: documents to be sent, to be stored, blank papers, etc. Taking Housekeeping to the next level will improve productivity 1 EXAMPLE OF 5S AT THE OFFICE 2 Implementing 5S at the office to ensure sustainable workplace organization FROM TO – Clear identification of the folders – One location for every tool assuring we only keep the tools needed and we can easily detect if anything is missing – Working documents sorted by type 1 TOYOTA 3 Taiichi Ohno Hero of the Toyota Production System Toyota has painted its equipment white to detect issues such as leaks early. 1 OUR WORKPLACE 4 How many of you are comfortable with a customer or your CEO dropping into your workplace unannounced? This is the Boeing final assembly area in St. Louis for the F/A18 Super Hornet. Very clean, well-lit facility for multi-million dollar aircraft. They clean and sweep the area multiple times a day to reduce the potential of foreign object damage to an engine or aircraft. 1 WHAT DO YOU SEE? 5 1 WHAT DO YOU SEE? 6 Office example of Poor Housekeeping, slip, trip and fall hazards, reduced efficiency, and potential security breaches. (passerby can take a confidential paper without person noticing). 1 WHY USE 5S? 7 Remove waste from the workplace. Provide an environment where continuous improvement is encouraged and embraced. Create a culture of discipline. Improve safety. Improve quality. 1 WHAT IS THE 5S PROCESS? 8 1 5S PROCESS 9 2) SET IN ORDER 4) STANDARDIZE Arranging Necessary — Items Creating Consistency 1S 2S 3S 4S 5S 1) SORT — 3) SHINE — 5) SUSTAIN — Decide What Is Needed Cleaning the Maintaining the 5S Workplace 2 5S EXAMPLE? 0 Let’s experience 6S with an Example Double Click Above Image to Open the Simulation 2 WHAT IS SORT ABOUT? 1 Sort begins by removing what you do not need from your working area Only keep the right items. Right means: Sort In the right place In the right quantities Setting up a clean and organized workplace (system, tools, documentation, physical workplace) also support back-up and replacement of Unnecessar personnel y items In supply chain, this concept removed can be applied to organize the data and documentation of process 2 WHAT ARE THE BENEFITS? 2 Visual order allows the workplace to be Before Sorting After Sorting self -explaining improving the communication between workers Improve workplace efficiency, eliminating unnecessary motion and earning valuable floor space Reduces inventory of items not needed Prepare the workplace to be self-explaining and able to hold Where Where would would you you find find your your material material easier? easier? visual information 2 HOW TO SORT? 3 The red-tag strategy allows quick identification of items that will be potentially removed from the work area. Red-tag will be used for: o Unneeded items (or items rarely used). o Excess needed items (duplicate items). A red-tag holding area must be created (quarantine area). This area is aside of the standard areas and stores the items that need further evaluation. If needed, an Excel list of items can be created to follow-up the red-tag items. 2 HOW TO SORT? 4 Process steps Description Define and print Red tags must contain: the red tag format Red tag number. Date. Department / Area. Name of the person that tagged the item. Action to take. Important: the number of red tags printed must be known. Define and mark the The quarantine are must be located aside standard areas. quarantine area Area must be clearly marked and can only have red tag items for maximum 2 weeks. Tag items to be Apply one tag per individual item (do not tag one entire shelf). removed Items to be tagged: Unneeded items; excess items. Move red tagged items to the quarantine area. Evaluate red tag Involve Controlling to assure the items staged for disposal are reviewed against the asset list for items proper documentation. Regular team meeting led by the area manager with all department members where all items in the area will be evaluated and their final location will be decided (see next slide for more details). Dispose / relocate Items should be disposed / relocated immediately. items If longer time is required, a responsible person will be defined to assure the item is out of the quarantine area within the following week. 2 PROPOSE ACTIONS FOR RED-TAGGED 5 ITEMS Actions to be decided during the evaluation of every red tagged item located in the quarantine area: If needed elsewhere Transfer it If not needed or Sell or throw it away obsolete If broken Repair or throw it away If dirty Clean it If stored in wrong Move it to correct location location If needed but there is Store the excess too much 2 RULES OF THUMB FOR HOLDING 6 TIMES How Often is it Used What to do with it Give, sell, recycle, discard, Never delete Store off-site / on alternate server, if Once or twice a year possible Store in the facility / on shared Once a month folder Once a week Store in the general area / on PC Store at point of use (ex. at the Once a day or more machine, on desktop) 2 SMALL AREA, QUICK 5S APPROACH 7 Pick a small area to Remove all remaining complete a quick or items from the area 1 “just do it” 5S activity, (from a desk to a room Along with area stake 3 and sort items to determining possible 2 holders remove and in size) use dispose of all obvious trash, broken, old, soiled items Return only those items Completely clean and back to desk/room that Place necessary items in paint entire desk/room as 4 5 6 are necessary for the logical, easy to reach needed. tasks performed in this positions, labeling these Enhance/upgrade lighting area positions professionally as needed. 2 WHAT IS SET IN ORDER 8 ABOUT? Set in order begins by finding the best way to store items so that BEFORE AFTER anyone can understand where an item is kept and quickly put it back in its proper place after usage Set in order should be implemented only if the first step (Sort) is in place 2 HOW TO SET IN ORDER? 9 Set in order must be Process steps for Set in order:Detailed in next slides implemented following the process Take photos of workplace in the illustration Analyze current areas to show the current 1 situation. Return regularly Two important steps situation to take photos and use them to motivate the team have to be Conduct an inspection of a Identify with the examples of 2 considered for defined area and use target issue improvements an observation It’s key that items are implementing set in checklist Define arranged so that they are 3 easy to use and that anyone order phase: appropriate can find them and put them location for o Define Make obvious where things belong item 4 Mark location away appropriate location for items o Decide how to mark location once has been defined 3 DEFINE APPROPRIATE LOCATION FOR 0 ITEMS Points to be considered when defining location of the items Locate items in the workplace according to their frequency of Frequency of use use: the more often an item is used, the closer it should be to where it used Store items together if they are used together and store them Interaction with other tools in the sequence in which they are used. Store tools and manuals close to the point of use. This will facilitate that the equipment is returned to its designated Location of the tasks location after use. Get things off of the floor when ever possible Motion and ergonomic studies could be required for assuring the location of the tools is adapted to the tasks where is needed Quantity required Set limits on quantities for tools, equipment, raw material and office product s quantities 3 DECIDE HOW TO MARK LOCATION 1 Once best locations have been determined, a way to mark these Where? locations is needed so that everyone will know: o Where best locations are How? o What goes where How many? o How many items belong to each location Set up of a temporary storage area is often recommended, during the final area preparation by applying the different strategies Signboard strategy: is often used to identify names of work areas, There are inventory locations, equipment storage locations, standard procedures different and machine layout strategies Painting strategy: is often used for identifying locations on floor and for marking walkways what, where Color coding strategy: can be used to show clearly which materials or and how many: tools are used for which purpose Shadow boards: is normally used to show which tools are stored where 3 DECIDE HOW TO MARK LOCATION 2 THE SIGNBOARD STRATEGY Signboard The signboard strategy uses signboards to label what, where and how strategy many Three main uses of signboards are: Location indicators, which show where items are stored Painting Item indicators which show what specific items are stored there strategy Amount indicators which show how many of these items should be Location stored in that location indicator A1 Color coding Item strategy indicator 11112813 3/8"- 16 100 pieces Amount Shadow indicator boards 3 DECIDE HOW TO MARK LOCATION 3 THE SIGNBOARD STRATEGY ACTION PROCESS STEPS ACTIONS Signboard Once items quantity is strategy defined, decide the best Determine location to facilitate 1 location operations Organize Be sure to put frequently shelving and used items as close as Painting cabinets 2 Prepare location possible to the place of strategy according to use the specified Make and post location 3 Indicate location signboards that clearly indicate where each Make and post item belongs signboards that Indicate 4 Color coding clearly indicate item names Indicate the number of items names strategy items covered by each 5 Indicate amounts signboard (also maximum and minimum Make amounts could be orderliness Make set in indicated (Kanban)) 6 easy to order a habit Shadow maintain boards Maintain discipline 3 DECIDE HOW TO MARK LOCATION 4 PAINTING STRATEGY Signboard Comments strategy – The painting strategy is a method for identifying locations on floors and walkways. Painting – The painting strategy is used to create strategy divider lines that mark off the factory’s walking areas (walkways) from the working areas (operation areas) and for Walkwa Storage Exit staging areas (More details at How to areas indication optimize the material flow) Color coding y strategy Beside paint, acrylic sheets that can be cut in different length or width can also be used as well as different type of tape (e.g.. For applying tiger stripe lines) Shadow boards Tape can be used before painting to test the new layout before making it final while painting. It is easier to adjust the layout using tape first. 3 DECIDE HOW TO MARK LOCATION 5 COLOR CODING STRATEGY Signboard strategy Comments The color coding strategy is a method for showing which materials or tools are used for which purpose. Painting strategy If certain materials need to be used to make a particular product, they can be color coded with the same color and even stored in a location that is painted that color Color coding strategy Color coding facilitates tracing of Storage bins painted in product, from production planning different colors to Shadow to finished product packaging & indicate color of product storing area content boards 3 DECIDE HOW TO MARK LOCATION 6 THE SHADOW BOARD STRATEGY Signboard Comments strategy The shadow boards is a good way to show which tool is stored where The shadow boards are drawing outlines of Painting tools in their proper storage positions strategy When you want to return a tool, the shadow provides an additional and visual indication of where it belongs Color coding If the work area has several strategy shadow boards similar in nature (e.g. same equipment), the tool board layout and composition should be standardized as to not Shadow require workers to re-orient boards themselves when changing function 3 HOW TO EVALUATE IF SET IN ORDER 7 WAS SUCCESSFUL AND SUSTAINABLE? Check that items are put back on the right marked place after being used Confirm that preliminary painting or taping are in the right position before finally marking Schedule visual tour and use workplace check list for monitoring status changes WHAT IS SHINE ABOUT? 3 8 The “Shine” phase is the component of 5S activities that Making sure that every… emphasizes the removal of dirt, Tool …is swept, grime and dust from the Piece of equipment cleaned workplace. and free of Machine grime, dirt and One obvious target of Shine Square foot on the floor grease, properly phase is to turn workplace into a Working surface painted and clean place, where everyone will sealed, and kept Wall that way enjoy working. Storage area Other target is to keep every tools, equipment or machine in top condition, so it is at every time ready to be used. If it doesn’t get dirty, it doesn’t have to be cleaned SHINE TO SUPPLY CHAIN 3 9 MANAGEMENT One obvious target of Shine phase in supply chain Making sure that every… …is cleaned management is to turn a process Tool and kept free of into a clean and optimized flow, redundant data, Master data with which everyone enjoy is understood working. Interface and accepted, Process properly prepared and Other target is to keep every Directory entered, and tool, process, equipment or Documentation kept up to date machine in top condition, so it is at every time ready to be used. If you do not let “dirt” into your systems & processes, you do not have to clean them HOW TO SHINE? 4 0 Only ask or sending reminder to Way to Excellence at work clean up is not enough to ensure implementation of the Shine phase or to ensure that Shine activities become part of the operator tasks. Daily cleaning should be understood Shine, inspection and simple maintenance as a set of steps and rules that tasks integrate in employees need to maintain with Inspection work duties discipline. activities integrated in Shine activities work duties If the initial Shine phase is integrated in implemented correctly, it is possible work duties Work duties and to introduce further controls by the cleaning operator. He/she will also take over activities are tasks like inspection and not integrated maintenance increasing operators ownership on machines and equipment. WHAT IS STANDARDIZE ABOUT? 4 1 Simple example of the process for hand washing, simple Standardization is the and visual: implementation of procedures and designs to achieve and maintain the required level of operational performance, the way to work Standardize creates the work structure to convert the new practices into habits, a standard “way to work” Standardize is the way to assure the benefits out of “Sort”, “Set in order” and “Shine” will be properly maintained Standardization will prevent setbacks and will set the bases for sustainability Standardization creates the basis for continuous improvement. For improving the standard to start from must be defined HOW TO STANDARDIZE? 4 2 The Standardization process is focused on creating visual control procedures that allows: Align & implement a criteria on housekeeping standards & workplace arrangement methods Assure consistency on tasks Identify missing parts, or parts not in the right place Reinforce continuous self-training Common tools and methods of standardization includes: Labels, signs, posters, banners and floor area marks Visual control methods Work Level control instructions Operating procedures/cleaning guidelines Areas of responsibility Area reference Daily check-lists/job cycle COMMON TOOLS AND METHODS OF 4 3 STANDARDIZATION Clear labeling indicating the name and/or code of each piece of equipment Common Tools and Methods Floor marks indicate specific areas for of Standardization are as equipment and/or product (e.g. pallet following: allocation). Visual control methods should include the use of color marks, color codes or cards. Labels Procedures must be updated and modified Floor area marking to make the process simple/easier Visual control methods Responsibility of monitoring of a specific area during working hours is assigned to a Operating procedures & specific employee. cleaning guidelines Award the area by developing an “area Areas of responsibility reference”. This document includes Location and Responsible of the area in Area reference scope (map if possible) Max/ min Daily check lists/job cycle Check lists should include activities related levels chart to ‘shining’ and autonomous maintenance WHAT IS SUSTAIN ABOUT? 4 4 Maintain the benefits obtained with the previous 4 Sustain is the piece that makes S’s. 5S a culture and not only a o Organized and visual one-time event (1 & 2S) o Safe and clean (3S) o Procedures are clear (4S) Keep everyone aware of 5S and its benefits and don’t let 5S become another “flavor of Sort Shine the month” Sustain Give recognition where it is due Set in order Standardize Establish audits and checklists to keep 5S sustainable Establish KPIs and HOW TO SUSTAIN? 4 5 5S campaign Dashboards Sustain is based in 3 pillars: material (Culture showing 5S change) results (Discipline) o Culture change o Discipline o Evaluation (5S Audits) Sustain is about promoting and creating the best environment to meet the 5s Audits challenge of sustaining 5S (Evaluation) HOW TO ENSURE 5S IS SUCCESSFUL 4 6 AND SUSTAINABLE? 5S sustained at the shop floor: 5S is sustainable if Areas are always clean and self organized. 5S boards are up to date supporting working processes New promotional tools/themes on 5S are visible at shop floor Standards are maintained and are available at shop floor Continuous improvements ideas are generated based on results of 5S audits or checklists. Process improvements are easily executed as the processes are clear HOW TO ENSURE 5S IS SUCCESSFUL 4 7 AND SUSTAINABLE? When operators and technicians question their own Perform regular training on 5S to colleagues if the standards are not followed the 5S the employees culture is in a high level. Ensure new employees are trained in 5S, integrated in the 5S routines and assigned as responsible of an area Promote job rotation and include 5S routines in the trainings for the new positions Promote information sharing between plants and with other organizations Walk the talk, management must show continuous support to 5S and be a role model for the organization CONTROL PHASE Lean Tools- Kanban WHAT IS KANBAN Kanban is a method for managing knowledge work with an emphasis on just-in-time delivery while not overloading the team members. Kanban is an approach to incremental, evolutionary process and systems change for organizations. It comes from Japanese word, kanban is literally translated as billboard or signboard. THE PRINCIPLES OF KANABN BOARD Principle 1: Start With What Do want Now. Principle 2: Agree to Pursue Incremental, Evolutionary Change. Principle 3: Respect the Current Process, Roles & Responsibilities. Principle 4: Encourage Acts of Leadership at All Levels. THE 6 PRACTICES OF KANBAN 1. Visualize the Workflow. 2. Limit Work in Progress. 3. Manage Flow. 4. Make Process Policies Explicit. 5. Feedback Loops. 6. Improve Collaboratively. VISUALIZE THE WORKFLOW Visualizing workflows supports proper understanding of changes planned and helps to implement them according to this plan. A common way to visualize the workflow is to use a card wall with cards and columns. The columns on the card wall represent different states or steps in the workflow. KANBAN WORKFLOW Replenishment Acceptance Meeting Marking delivered work This meeting is held by items as “DONE” product director & is according to definition of similar in essence to “Done”. Sprint planning in scrum. Ideation Developmen Production Preparing product t according Pulling in work Shipping the product features together with to one’s capacity. Staying increment; starting back from shareholders. within the work-in-- square one & continuously progress limit. improvement the product. SCRUM VS KANBAN It doesn’t necessarily recommend a set of roles. Yet, Scrum comes with three roles product sometimes Roles owner, scrum master and scrum team. you may stumble upon service delivery & request manager. Scrum involves plain before Planning Kanban doesn’t require through research. the start of each sprint. Each sprint lasts between one to four weeks. After There are no time-boxes & deadlines. You’re Time Delivery the sprint, working software must be delivered. constantly releasing working software. KANBAN SCRUM Velocity and Capacity charts helps Lead and cycle time help you determine KPI - you track the overall scrum progress. the time it takes you to finish a task. Indicator Daily sprint stand-ups are encouraged Meeting are necessarily required. Yet, many Meetings so the team can be on the same page. Kanban teams do daily stand-ups. The scrum board consist of all the task without having The Kanban board features “To-do”, specific columns. The scrum board is rest after each Boards “Work in progress”, and “Done” columns. sprint. There is a WIP limit for each The WIP limit allows you to work only Work in batch of tasks. At only a few tasks at a time. Progress KANBAN BOARD Input Refine Resolve Estimate Backlog Description Description Description Description Description Text Text Text Text Text Description Description Description Description Description Text Text Text Text Text Description Description Description Description Description Text Text Text Text Text Description Description Description Description Description Text Text Text Text Text KANBAN BOARD Implement To Do Accepted Test Done To do In Progress Done Send Invite guest Update Interviews Optimize search Monthly report Link to registration newsletter speaker Website Blogger engine Team Apply for Mobile app Part 01 Link to Mobile app Verify updates meeting business award development completed homepage part 01 done Prepare Add new Invite VIP Audience Invite sent Conference employee persons arrangement to guest Take part in Blogger invite Place booked webinar KANBAN BOARD 04 04 Pending 04 04 Analysis 05 05 Developmen 03 03 Test Board 01 01 Deploy Task t Doing Done Doing Done Description Description Description Description Description Text Description Text Description Text Text Text Text Text Description Description Description Description Text Description Text Text Text Text Description Description Text Description Text Text Description Description Text Text LIMIT WORK IN PROGRESS Limiting work-in-process implies that a pull system is implemented on parts or all of the workflow. The pull system acts as one of the main stimuli for continuous, incremental and evolutionary changes to the system. The pull system can be implemented as a kanban system. The critical elements are that work-in-process at each state in the workflow is limited and that new work is “pulled” into the new information discovery activity when there is available capacity within the local WIP limit. MANAGE FLOW Each transition between states in the workflow is monitored, measured and reported. By actively managing the flow the continuous, incremental and evolutionary changes to the system can be evaluated to have positive or negative effects on the system. MAKE PROCESS POLICIES EXPLICIT Until the mechanism of a process is made explicit, it is often hard or impossible to hold a discussion about improving it. Without an explicit understanding of how things work and how work is actually done, any discussion of problems tends to be emotional, anecdotal and subjective. With an explicit understanding it is possible to move to a more rational, empirical, objective discussion of issues. FEEDBACK LOOPS The Kanban method encourages small continuous, incremental and evolutionary changes that stick. When teams have a shared understanding of theories about work, workflow, process and risk, they are more likely to be able to build a shared comprehension of a problem and suggest improvements which can be agreed to by consensus. Teams measure their effectiveness by tracking flow, quality, throughput, lead times and more. Experiments and analysis can change the system to improve the team’s effectiveness. IMPROVE COLLABORATIVELY The way to achieve continuous improvement and sustainable change within an organization is through shared vision of a better future and collective understanding of the issues that need to be overcome.. THE POSITIVE AND NEGATIVE SIDE OF KANBAN Positive Side Negative side 1. Everyone is on the same page 1. Outdated Kanban board can lead to 2. Kanban reveals bottlenecks in your issues in the development process. workflow. 2. Some time Kanban team make the board 3. Kanban brings flexibility overcomplicate. 4. team gets more responsive 3. Lack of timing is another disadvantage 5. focus on finishing work to boost because there is no timeframes are collaboration and productivity associated with each phase. 6. Easy access for remote team members 7. Flow analytics 64 THANK FOR YOUR ATTENTION!!! YOU