Cost Classifications-New PDF
Document Details
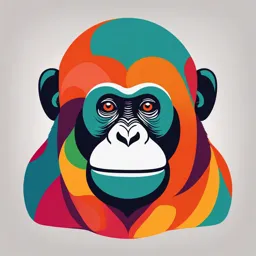
Uploaded by WorkableSanAntonio
Strathmore University
Tags
Summary
This document presents a summary of various cost classification methods in cost accounting. It details different types of costs, including direct and indirect material and labor costs, direct and indirect expenses, and describes how these classifications are used for managing resources and making business decisions.
Full Transcript
COST ACCOUNTING COST CLASSIFICATIONS Intended Learning Outcomes At the end of the chapter, you will able to 1. Identify the elements of costs 2. Understand various classification of costs 3. Identify the cost unit COST CLASSIFICATIONS COST The CIMA London cost define as, the amount of expenditu...
COST ACCOUNTING COST CLASSIFICATIONS Intended Learning Outcomes At the end of the chapter, you will able to 1. Identify the elements of costs 2. Understand various classification of costs 3. Identify the cost unit COST CLASSIFICATIONS COST The CIMA London cost define as, the amount of expenditure incurred (actual) or attributable (notional) to a specified thing or activity. Cost refers to the value sacrificed with the aim of gaining something in return which is the basis of profit determination. Expenses: Are the consumption of asset for the purpose of generating revenue. Expenses can simply be defined as expired costs. ELEMENTS OF COSTS In order to ascertain, control, manage, forecast and interpret cost, the elements of cost must be classified. The elements of cost are; 1. Material 2. Labour 3. Expenses MATERIAL COST Material is the substance, from which a product is made. It may be in a raw or a manufactured state. It can be direct or indirect. Direct Material Direct materials are raw materials that become an integral part of the finished product and can be conveniently traced to the units. Example: Steel used to manufacture the automobile INDIRECT MATERIAL Indirect Material Cost is used to support the production process and cannot be conveniently identified with the individual cost center. Example: Consumable stores, oil and grease, printing and stationery material etc. LABOUR COST This is the cost incurred in the form of remuneration paid to the employees or labour of the organization. The workforce required to convert material into finished product is called labour. It can be direct or indirect. Direct Labour Direct labor consists of that portion of labor cost that can be easily traced to a product. Sometimes referred to as “touch labor,”. Example: Wages paid to automobile assembly workers INDIRECT LABOUR Indirect Labour Cost is the cost incurred on those employees who do not directly take part in the manufacturing process and cannot identified with the final product. Example: Maintenance workers Janitors Security guard OTHER EXPENSES Expenses are the costs of services provided to the organization. It can be direct or indirect. Direct Expenses Direct Expenses are the expenses which can be directly identified with the cost unit. Example: raw materials, sales commissions, manufacturing supplies, direct labor, customer service, purchase of goods to be sold, transit of goods from the supplier e.t.c INDIRECT EXPENSES Indirect Expenses are the expenses which cannot be directly, conveniently and wholly allocated to cost center & cost unit.. Example: Equipment depreciation Salaries Equipment maintenance Rent Utilities e.g. Lighting.. Office supplies Advertising Marketing Printing and stationery Legal fees HR costs Insurance Transit of goods to a customer COST CARDS A cost card is used to show the breakdown of the costs of producing output based on the classification of each cost. A cost card can be produced for one unit or a planned level of production. The following costs are brought together and recorded on a cost card: direct materials direct labour direct expenses prime cost (total direct costs) variable production overheads fixed production overheads non-production overheads. ELEME NTS OF COST Material Labour Other expenses Direct Indirect Direct Indirect Direct Indirect CLASSIFICATION OF COSTS Cost classification is the logical process of categorizing the different costs involved in a business process according to their type, nature, frequency and other features to fulfil accounting objectives and facilitate economic analysis. The different bases of cost classification are: 1. By time ( Historical , Pre determined) 2. By nature or element (Material ,labour and overhead) 3. By degree of traceability to the product ( Direct , indirect) 4. Associated with the product (( Product , Period) 5. By change in activity or volume ( Fixed , variable ,semi variable) 6. By function (Manufacturing, Administrative , R&D , Pre production) 7. Relationship with accounting period ( Capital , Revenue) 8. Controllability ( Controllable , Non controllable) 9. Cost for analytical & decision making purpose (Opportunity, sunk, differential, joint, common, imputed, out of pocket, marginal, uniform, replacement) 10. Others ( conversion , Traceable, normal, avoidable , unavoidable ,total) NEED FOR COST CLASSIFICATIONS Management will require a variety of different cost summaries, including: costs for a particular product – a cost unit or cost object costs for use in the preparation of external financial reports costs for a particular department – a cost centre costs to be used for decision making costs that are useful for planning and control. 01. CLASSIFICATION ON THE BASIS OF TIME a) Historical costs: costs are ascertained after they are incurred. Such costs are available only when the particular thing has already been done. b) Pre-determine costs: These costs are calculated before they are incurred on the basis of a specification of all factors affecting cost. Such costs may be: i. Estimated costs: Costs are estimated before goods are produced: these are naturally less accurate than standard. ii Standard costs: setting up predetermined standards for each element of cost and each product. 02. CLASSIFICATION OF ELEMENTS Materials – all costs of materials purchased for production or non- production activities. For example, raw materials, components, cleaning materials, maintenance materials and stationery. Labour – all staff costs relating to employees on the payroll of the organisation. Expenses – all other costs which are not materials or labour. This includes all bought-in services, for example, rent, telephone, sub-contractors and 03. CLASSIFICATION BY NATURE Direct Costs-A direct cost is one that is traceable to and the responsibility of a particular operating department or division. Most direct costs are variable by nature (direct material, labour and expenses) and will increase or decrease in relation to increases and decreases in sales revenue. Examples: Cost of wood for making furniture, cost of sales–food and –beverages, wages and salaries, operating supplies and services, and linen and laundry. Indirect Costs-An indirect cost is one that cannot be identified with and traceable to a particular operating department or division, and thus, cannot be charged to any specific department or division. General building maintenance could only be charged to various departments or divisions (such as rooms, food, or 04. ASSOCIATION WITH THE PRODUCT Product Costs: Period costs are traceable to the product & included in inventory values. It comprises the cost of (Prime costs (direct materials, direct labour, direct expenses) and manufacturing overheads (indirect material, indirect labour and indirect expenses). Cost per unit/Total cost Prime cost Direct material, direct labour & direct expenses xx Manufacturing O/H Indirect material, indirect labour & indirect expenses xx Product costs are used for valuing inventories which are shown in the balance sheet as asset till they are sold. The product cost of goods sold is transferred to the cost of goods sold account. PERIOD COSTS (EXPENSES) Period costs are incurred on the basis of time such as rent, salaries etc.. Include selling & administrative costs. They are charged to the period in which they are incurred and treated as expense. 05. BY CHANGE IN ACTIVITY OR VOLUME-COST BEHAVIOR Total Fixed Costs The cost which is incurred for a period and within certain output tends to be unaffected by fluctuations in the level of activity (output or turnover) Fixed costs remain fixed only in the short run. Ex: rent , property , insurance , supervisor's salaries E.g Your monthly contract fee for your cell phone is fixed for the number of monthly minutes in your contract. The monthly contract fee does not change based on the number of calls you make. FIXED COSTCAN BE CLASSIFIED INTO FOLLOWING CATEGORIES FOR PURPOSE OF ANALYSIS: 1. Committed costs: These costs are incurred to maintain certain facilities and cannot be quickly eliminated. e.g: rent, insurance etc. 2.Policy & managed costs: These costs are incurred for implementing particular management policies such as executive development , staff services. 3.Discretionary costs: This is a cost that may or may not be incurred based on the decision of a particular person, usually the general manager. Non- 4.Step costs: Costs are constant for a given level of output & then increase by a fixed amount at a higher level of output. 70,000 60,000 50,000 40,000 30,000 20,000 10,000 0 0 20 40 60 80 100 Relevant Range or volume Production Units (In Thousands) Between 20,000 & 80,000 units of production, fixed cost is Kes. 50,000 In excess of 80,000 units, fixed cost becomes Kes. 60,000. This assumes that increase in production after a certain level requires increase in fixed expenses such as additional supervision, increase in quality control costs. FIXED COST PER UNIT Fixed cost per unit goes down as activity level goes up. Within the monthly contract allotment, the average fixed cost per cell phone call made decreases as more calls are made. Fixed cost = TFC per unit No of Unit Making cake Months Total Fixed cost Cake Unit cost May 5000 5 5000/5=1000 June 5000 20 5000/20=250 July 5000 25 5000/25=200 July 5000 50 5000/50=100 GRAPHICAL REPRESENTATION OF FIXED COSTS Total Variable Cost Costs which vary directly or proportionately with the output. Direct materials cost & direct labour costs are the costs which are generally variable Total variable costs change as more units are produced. If a factory is shut down, variable costs are eliminated. e.g : the more food and beverages sold, the more costs will VARIABLE COST PER UNIT MAKING CALL Minutes Cost per unit Total variable costs 1 5 5 2 5 10 3 5 15 4 5 20 5 5 25 50 5 250 Cost Classifications for Predicting Cost Behavior Behavior of Cost (within the relevant range) Cost In Total Per Unit Variable Total variable cost Increase Variable cost per unit and decrease in proportion remains constant. to changes in the activity level. Fixed Total fixed cost is not affected Fixed cost per unit decreases by changes in the activity as the activity level rises and level within the relevant range. increases as the activity level falls. EXAMPLE OF CALL PER MINUTE CALL Unit variable cost Minutes Cost per minute Total variable cost 1 4 4 2 4 8 3 4 12 4 4 16 5 4 20 Unit variable cost=Total variable cost/level of activity Total variable cost=Level of activity * unit variable cost MIXED COSTS (SEMI- VARIABLE) A mixed cost contains both variable and fixed elements. Consider the example of utility cost. Y Total Utility Cost Variable Cost per KW X Fixed Monthly Activity (Kilowatt Hours) Utility The graph depicts the mixed costs of a normal utility Charge bill. As illustrated in the graph, a utility bill contains a fixed and a variable cost component. The fixed portion of the utility bill is constant regardless of kilowatt hours consumed. This cost represents the minimum cost that is incurred to have the service ready and available for use. The variable portion of the utility bill varies in direct proportion to the consumption of kilowatt hours. The total mixed cost line can be expressed as an equation: Y = a + bX Y = The total mixed cost. a = The total fixed cost (the vertical intercept of the Where line). : b = The variable cost per unit of activity (the slope of the line). X = The level of activity. MIXED COSTS – AN EXAMPLE Y = a + bX Y = Kes 40 + (Kes 0.03 × 2,000) Y = Kes 100 VARIABLE COST PER UNIT Variable cost per unit remains the same over wide range of activity. E.g: The petrol cost per km constant. Variable Cost per unit Cost 0 20 40 60 Km 06. FUNCTIONAL CLASSIFICATION OF COSTS Manufacturing/production Costs It is the cost of operating the manufacturing division. It include DM, DL , DE, VPO & FPO e.t.c… EXAMPLES OF PRODUCTION COSTS Examples of production costs for a construction company Direct materials – bricks, cement Direct labour – builders, plasterers, electricians Direct expenses – the cost of a subcontracted crane and driver Variable production overheads – electricity Fixed production overheads – site managers salary NON-PRODUCTION COSTS Non-production costs are costs that are not directly associated with the production of the businesses output. Non-production costs Administration Costs They are indirect & covers all expenditure incurred in formulating the policy, directing the organization & controlling the operation. E.g: managers salaries, rent ,training ,welfare Selling & distribution costs-Cost of seeking to create & motivate demand. E.g. advertise, market research , cartage..etc.. Research & Development Costs-Cost of discovering new ideas, process, and products by experiments. Pre-production Cost-When a new factory started or new product is introduced those costs are incurred. There are trial run. 07. RELATIONSHIPS WITH ACCOUNTING PERIOD Capital Expenses Provide benefits to future period & is called as “asset” Revenue Expenditure Benefits only current period & is treated as “expenses.” 08. CONTROLLABILITY Controllable Cost Cost which can be influenced by its budget holder/person in authority. Uncontrollable cost. Costs that a manager cannot influence significantly. Cost item Manager Classification Restaurant Cost of food used in a restaurant manager Controllable Cost of national advertising by restaurant Restaurant chain manager Uncontrollable 9. COSTS FOR ANALYTICAL & DECISION MAKING PURPOSE Opportunity Costs Opportunity cost is the Cost of selecting one courses of action and the losing of other opportunities to carry out that courses of action. The potential benefit that is given up when one alternative is selected over another. Eg: Capital invested in plant & machinery. It cannot be now invested in shares. The loss of interest and dividend that would be earned is the opportunity cost. Opportunity costs are not recorded in the books. It is important in decision making & comparing alternatives Sunk Costs All costs incurred in the past that cannot be changed by any decision made now or in the future are “sunk cost”. Sunk costs should not be considered in decision. It has also been defined as the different between the purchase price of an asset and its salvage value. E.g: you bought an automobile that cost Kes 12,000 two years ago. The Kes 12,000 cost is sunk because whether you drive it, park it, trade it, or sell it you cannot change the Kes 12,000 cost. Differential Costs The difference between total costs among alternatives. Differential cost is the decrease or increase in total costs resulting out of: 1. Producing few more or few less of products 2. A change in method of production 3. An additional or deletion products E.g; you can earn Kes 1500 per month in your hometown or Kes 2000 per month in a nearby city. Your commuting costs are Kes 50 per month in your home town and Kes 300 per month to the city. Differential cost = (300-50) = Kes 250. MARGINAL COSTS: The extra cost incurred to produce one additional unit. The marginal cost of production is the change in total production cost that comes from making or producing one additional unit. To calculate marginal cost, divide the change in production costs by the change in quantity. Joint costs: Joint costs may include direct material, direct labor, and overhead costs incurred during a joint production process. A joint process is a production process in which one input yields multiple outputs. It is a process in which seeking to create one type of output product automatically also creates other types of output product. For instance, let’s consider a poultry plant. The plant takes live chickens and turns them into chicken parts used for food. The chickens yield chicken breasts, drumsticks, livers, gizzards, and other parts of the chicken that are used for human consumption. Similarly, let’s consider an oil refinery. The refinery takes crude oil and refines it into a substance that may be used for auto gasoline, motor oil, heating oil, or kerosene. All of these various outputs come from a single input – crude oil. In both of these examples, a single input yields multiple outputs. These are both examples of joint production processes. COST UNIT Costs units are usually the units of physical measurement like number, weight, area, length, value, time etc… Industry/ Product Cost unit Automobile Number Cement Tonne Transport Km, Passenger Chemicals Litre , gallon Steel Tonne Sugar Tonne END OF LECTURE 2! THANK YOU.