Corrosion and Its Prevention PDF
Document Details
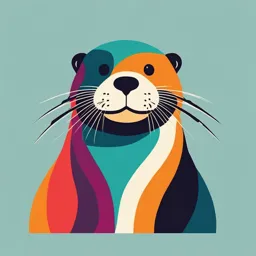
Uploaded by EffectiveTsilaisite9452
NUST
Tags
Summary
This document provides an overview of corrosion, a natural process that degrades metals. It discusses the different types of corrosion, the factors contributing to corrosion such as pH value, electrochemical potential, and microbial induced corrosion. Furthermore, the document describes methods of preventing corrosion, such as using coatings and corrosion inhibitors.
Full Transcript
Corrosion and Its Prevention Definition: A natural process that converts a refined metal into a more chemically stable oxide. Gradual decay of metals or even nonmetals caused by action of air, moisture or a chemical reaction (such as an acid) on their surface. Nature: natural, spontaneous,...
Corrosion and Its Prevention Definition: A natural process that converts a refined metal into a more chemically stable oxide. Gradual decay of metals or even nonmetals caused by action of air, moisture or a chemical reaction (such as an acid) on their surface. Nature: natural, spontaneous, and thermodynamically stable process. Materials tend to return to their most thermodynamically stable state, such as oxidized states or ores, by reacting with the environment. Examples: rusting of iron, tarnishing of silver, and the appearance of green color in copper. Due to corrosion, lots of buildings, bridges, and ships that are constructed using iron get affected. Corrosion can cause significant damage to buildings, bridges, pipelines, vehicles, home appliances, and wastewater systems. It can also lead to safety concerns, loss of life, and damage to reputation. Factors that can contribute to corrosion: pH value Solutions with a pH value below 7 (neutral) are more acidic and can lead to corrosion. Electrochemical potential Metals gain electrochemical potential when exposed to a conductive solution. Microbial induced corrosion Some types of bacteria, such as sulfate-reducing bacteria (SRB), can cause corrosion. To prevent corrosion, you can try coating iron with a thin layer of zinc, or painting or greasing it. Types of Corrosion: There are 2 basic types of corrosion. Nature corrosion: has 2 types, metals and nonmetals. Metals: includes electro chemicals o Metallic corrosion is a chemical reaction that occurs when a metal is exposed to its environment and breaks down. Explanation Metals are unstable, except for noble metals, and can be converted into more stable compounds like oxides, hydroxides, carbonates, and sulfides. This process is irreversible and can cause metals to lose their useful properties, such as malleability, ductility, hardness, luster, and electrical conductivity. Causes Corrosion can be caused by a number of factors, including: Humidity: Too much humidity or water vapor condensation on metal surfaces can cause corrosion. Corrosive gases: Gases like chlorine, hydrogen oxides, ammonia, and sulfur oxides can corrode parts of electronic equipment. Examples Some examples of metallic corrosion include: Rusting of iron: Iron converts into its oxide, Fe2O3. Tarnishing of silver: Silver converts into its sulfate, Ag2S. Green film on copper and brass: A green film forms on copper and brass. Nonmetals: involves certain chemicals. Yes, non-metallic materials can corrode, though they don't rust like metals. Causes Non-metals can corrode when exposed to certain environments, such as air, water, or other substances. Examples Non-metals that can corrode include glass, plastics, polymers, ceramics, and concrete. Effects Corrosion can cause non-metallic materials to break down structurally, which can lead to cracking, leaking, pitting, and eventual failure. Prevention Non-metallic materials can be engineered to resist corrosion, wear, chemical exposure, and other environmental factors. For example, lime is added to soda-lime glass to reduce its solubility in water and protect against corrosion. Non-metallic materials are often used in applications where corrosion resistance or insulation properties are important. Media Corrosion: Media corrosion occurs when a material reacts with a corrosive medium, such as a gas, particle, or liquid, through chemical or electrochemical reactions. The type of corrosion that occurs depends on the corrosive medium and the surface films formed in the solution. Some examples of media corrosion include: Industrial media Can be highly corrosive, containing gases, sulfur vapor, and other particles. Moisture, such as rain, can cause severe corrosion on galvanized steel. Nitric media Austenitic stainless steels can remain in a passive state in most nitric media, but can experience inter granular corrosion in some cases. Chloride media Unalloyed copper corrodes in chloride media, especially at concentrations similar to seawater. Magnetic recording media Corrosion can occur if the protective overcoat is porous or damaged. Corrosion products include oxides, hydroxides, and chlorides of cobalt and nickel. Plant-based extracts have been used to mitigate corrosion in acidic media. Here are some examples of plant-based extracts that can be used to prevent corrosion: Neem oil: Can prevent corrosion on the metal surfaces of offshore oil rigs Tamarind seed polysaccharides: Can protect ship hulls from corrosion in seawater Cucumber peel extract (CPE) and cucumber seed oil (CSO): Can inhibit the corrosion of AISI 1007 steel Green tea extract: Can be used as a corrosion inhibitor on carbon steel Eucalyptus globulus leaves extract: Can be used on low carbon steel immersed in sulfuric acid Ficus tikoua leaf extract: Can be used as a corrosion inhibitor on carbon steel in hydrochloric acid Other plant extracts that can be used as corrosion inhibitors include: Aloe vera Ceratonia siliqua Acacia fruit Olive leaf extract Jatropha extract Terminalia chebula Hibiscus sabdariffa Turmeric and ginger rhizomes Watermelon rind Plant extracts are effective because they contain phytochemicals and functional groups that act as organic green corrosion inhibitors. These extracts are also renewable, biodegradable, and low cost. However, there are some challenges associated with using plant extracts as corrosion inhibitors, such as the time and cost of extraction, and the uncertainty of the active compound. Dry Media Corrosion: Dry media corrosion, also known as oxidation, is a chemical reaction that occurs when a metal reacts with gases in a dry environment, without the presence of liquid. This reaction forms an oxide layer on the surface of the metal. Dry corrosion is usually not as damaging as wet corrosion, but it is very sensitive to temperature. The extent of dry corrosion depends on the environment and the properties of the oxide film that forms on the metal. There are three main types of dry corrosion: Oxidation corrosion: Occurs when oxygen reacts with metals at normal temperatures. Liquid metal corrosion: Occurs when a liquid metal flows over a solid metal at high temperatures. Corrosion by other gases: Occurs when certain gases chemically react with metals to form surface layers. One of the easiest and cheapest ways to prevent dry corrosion is to use barrier coatings like paint, plastic, or powder. Wet Media Corrosion: Wet corrosion, also known as electrochemical corrosion, is a type of corrosive damage that occurs when a metal reacts with oxygen in the presence of a liquid, such as water. It can be classified into two main types: Uniform corrosion: Corrosion that occurs evenly across the entire surface of a material. Localized corrosion: Corrosion that is concentrated in specific areas of a material. Wet corrosion occurs through electron transfer, which involves oxidation and reduction. In oxidation, the metal atoms lose electrons, and in reduction, the surrounding environment gains the electrons. Factors that affect the rate of corrosion include: The amount of oxygen available The presence of water or moisture The presence of other elements, ions, and compounds Some ways to prevent wet corrosion include: Selecting a material that does not corrode in the environment Changing the environment by removing oxygen or adding anticorrosion chemicals Designing to avoid corrosion, such as preventing water from collecting. Mechanism: Corrosion is the process by which metals return to their natural oxidation state, and it occurs through a number of mechanisms: Electrochemical When metals are exposed to electrolytes like water or moisture, electrons are released from the metal surface into the electrolyte. This is a reduction-oxidation reaction, where the metal is oxidized by its environment, usually oxygen in the air. Dry When metals react directly with atmospheric gases like carbon dioxide and sulfur dioxide in the absence of moisture. This can include oxidation corrosion, which occurs when oxygen reacts directly with metals at normal temperatures, or liquid metal corrosion, which occurs when a liquid metal flows over a solid metal at high temperatures. Corrosion can occur on both metal and non-metal surfaces, but the method of corrosion may differ depending on the surface. Factors Affecting Corrosion: Several factors affect the rate and form of corrosion, including: Temperature Corrosion increases rapidly with temperature as electrochemical reactions occur faster at higher temperatures. Stress Stress can lead to cracking and fatigue, depending on the magnitude and nature of the stress. Conductivity The electrical conductivity of the corroding medium can affect the rate of corrosion. Higher conductivity accelerates corrosion by allowing ions and electrons to move more rapidly. Oxygen When metals come into contact with oxygen, they produce metallic oxides, which are weaker than the pure metal. Electrochemical potential The electrochemical reaction is a major factor in metal pipe corrosion. The friction of the metal pipe with water flow generates an extra electric charge that affects the electrochemical reaction and corrosion process. Corrosion inhibitors Corrosion inhibitors are chemical compounds that can be added to liquids or gases to decrease the rate of corrosion. The effectiveness of a corrosion inhibitor depends on the fluid composition, flow regime, and quantity of water. Other factors that can affect corrosion include: The position of metals in the electrochemical series, The presence of electrolytes, Impurities and metals, and Concentration of oxygen. Prevention: There are many ways to prevent corrosion, including: Use non-corrosive metals: Use metals like stainless steel or aluminum that are less likely to corrode. Keep surfaces clean and dry: Keep metal surfaces clean and dry to prevent corrosion. Apply a coating: Apply a protective coating like grease, oil, paint, or carbon fiber coating to prevent the metal from coming into direct contact with corrosive elements. Use corrosion inhibitors: Apply corrosion inhibitors to the surface of the metal to create a protective film. Use sacrificial coatings: Apply a sacrificial coating to protect steel from corrosion. Use cathodic protection: Use cathodic protection to convert active sites on the metal surface to passive sites. Use electrochemical means: Use electrochemical means, such as anodic and cathodic materials, to prevent corrosion. Alloy the metal: Mix the metal with another metal to create an alloy that is more resistant to corrosion. Modify the design: Change the design of a project to eliminate potential causes of corrosion. Prevention using packing: Here are some ways to prevent corrosion when packing: Volatile corrosion inhibitor (VCI) packaging A protective material that creates an enclosed environment to prevent corrosion. VCI packaging can be used in the form of bags, sheeting, Kraft paper, or wraps. VCI molecules create an invisible barrier on the metal surface to protect it from water, oxygen, and contaminants. Desiccants These hygroscopic substances absorb moisture from the air to keep the environment around metal products dry. Desiccants can also prevent the growth of mold, mildew, and bacteria. Moisture barrier bags Also called vapor barrier bags, these bags prevent condensation and water vapors from collecting on products. They protect items from humidity, oxygen, and grease. Rust preventives These are used for temporary corrosion protection on unfinished pipe, steel consumer products, car underbodies, and more. They are often chosen when removal is important. Protective coatings These limit the exposure of metal to a corrosive environment by adhering to the substrate. Anodic and Cathodic Preventions: Anodic protection and cathodic protection are both methods used to prevent corrosion, but they differ in how they work: Cathodic protection This is the more common method and is used to prevent corrosion on carbon steel and other structural metals. It works by converting active sites on a metal surface to passive sites using an external electrical current. There are two types of cathodic protection: sacrificial anodes and impressed current. Sacrificial anodes: A more active metal, such as zinc, aluminum, or magnesium, is attached to the metal being protected to create a galvanic cell. Impressed current: A DC power source is connected between the metal being protected and the cathodic protection anodes. Anodic protection This method is used in the chemical and mining industries in environments with extreme corrosion. It works by making the metal surface the anode of an electrochemical cell and controlling the electrode potential. In the anodic cathodic reaction, the anode is the metal that gives up electrons and corrodes, while the cathode is the metal that gains electrons and remains intact. Coatings: Metallic and non-metallic coatings are both used to protect objects from corrosion, moisture, and other environmental factors. Coatings can be applied to metallic or non-metallic objects and surfaces, and can be classified by their composition, such as whether they are metallic or non-metallic, organic or inorganic, and solid, liquid, or gas. Here are some types of metallic and non-metallic coatings: Metallic coatings These include pure metals, solid solutions, and alloys. Some examples of metallic coatings include aluminum, zinc, and chromium. Types: Physical vapor deposition (PVD) and chemical vapor deposition (CVD) are both techniques used to create thin films on a substrate, but they differ in the process used and their applications. Requires high temperate especially in CVD. PVD Uses physical reactions to change a solid or liquid source material into a gas, which then condenses into a solid film on the substrate. PVD processes always take place in a vacuum. CVD Uses chemical reactions to create a solid film on the substrate from a gaseous or vapor source. CVD can take place at a range of pressures, from high vacuum to atmospheric pressure. Here are some other differences between PVD and CVD: Applications PVD coatings can improve the hardness, wear resistance, and oxidation resistance of a surface. CVD can create conformal coatings that cover complex geometries. Thickness PVD coatings are typically 2–5 microns thick, while CVD coatings are typically 5–10 microns thick. Precursors In CVD, the molecular structure of precursors affects the volatility, reactivity, and decomposition pathways. Vacuum PVD requires a high vacuum because even the smallest particles can be problematic Non-metallic coatings These can be inorganic, such as oxides, nitrides, sulfides, and carbides, or organic, such as polymers and rubbers. Coatings can improve a substrate's appearance, corrosion resistance, and wear resistance. They can also prolong the life of a product by creating a barrier between the surface and external elements. Requires Low temperature. Electrochemical Corrosion Cells: An electrochemical corrosion cell is a device that converts chemical energy into electrical energy through a process called electrochemical corrosion: Components An electrochemical corrosion cell has four components: o Anode: The corroding metal o Cathode: A metal, graphite, or semiconducting electron conductor o Electrolyte: Contains a reducible species o Electron-conducting connection: Connects the electrodes Process During electrochemical corrosion, the anode metal corrodes and dissolves into positive metal ions. The electrons produced are then consumed by reactions at the cathode surface. Corrosion prevention Corrosion can be prevented by galvanizing, which is the process of coating steel with zinc. Cathodic protection is another method that uses an external voltage source to protect underground structures. Feasibilty of Corrosion: (Thermo dynamic corrosion) Thermodynamics is a way to understand the energy changes that occur during corrosion, and to predict whether corrosion is possible. Corrosion is a natural process that occurs when metals degrade through an electrochemical reaction with their environment. Thermodynamics can't predict the rate of corrosion, but it can predict the direction or tendency. Here are some things to know about thermodynamic corrosion: Energy minimization Metals in their pure state have higher energy than their ores, so they corrode to reach a more stable state and minimize their energy. For example, when iron forms hematite, its ore, it releases a large amount of energy. Gibb's free energy The Gibb's free energy equation can be used to predict if a corrosion reaction is thermodynamically possible. If ∆G is negative, the reaction is possible. Deviation from the hydrogen electrode The more negative the deviation of the half-cell reaction from the hydrogen electrode, the greater the driving force for corrosion. Reversible reactions For thermodynamic validity, all reactions must be reversible. Composition Difference A chemical reaction that occurs when a material, usually a metal, reacts with elements in the environment, such as water or air, and is oxidized. The most common type of corrosion is metal oxidation, where metals react with oxygen to form metal oxides or other compounds. The composition of a material can affect its resistance to corrosion. For example, particles containing iron and copper can reduce a material's resistance to corrosion. High concentrations of impurities like lead at grain boundaries can also negatively affect corrosion resistance. Other factors that can affect corrosion include: The heat treatment and stress state of the material, The composition of the electrolyte, The distance between the anode and the cathode, Temperature, and Protective oxides and coating. Corrosion resistance is the ability of a material to protect itself from corrosion. The microstructure of a coating, such as the presence of cracks or open porosity, can be more important than the composition of the coating. PITS FORMATION Pits can form in a variety of ways, including: Pitting corrosion: A localized form of corrosion that creates holes in a material. Pits are usually small and numerous, and they can grow quickly. Pitting corrosion can be caused by scratches, inclusions, or other damage. It's more dangerous than uniform corrosion because it's harder to detect, predict, and design against. Material processing defects: Defects in material processing can cause pits to form. For example, the inclusion of MnS in carbon steel can lead to the formation and expansion of SCC. Gas escape: Pits can form when gas escapes from a workpiece. Contamination: Pits can form if contamination isn't removed properly. Lunar pits: Lunar pits are mostly found in impact melt deposits. SURFACE CORROSION Surface corrosion is a type of corrosion that occurs on the surface of a metal, causing it to roughen, etch, or pit. It can also appear as exfoliation or a combination of both. Surface corrosion can be caused by direct chemical or electrochemical attack, and can be brought on by: Dissimilar metals Adverse environments, such as salt water The absence of a protective coating The most common type of surface corrosion is general corrosion, which occurs uniformly across the surface of a metal. It's caused by electrochemical and chemical reactions that dissolve the metal, causing it to thin out and form oxides. General corrosion is visible to the naked eye as a rust-like appearance. Corrosion can affect all areas of the economy, and its cost is estimated to represent 4% of the gross national product. STRESS CORROSION Stress corrosion, also known as stress corrosion cracking (SCC), is a process that causes cracks to form in a material when it's exposed to a corrosive environment and tensile stress. This can lead to the sudden and unexpected failure of ductile metal alloys, especially at high temperatures. Here are some things to know about stress corrosion: How it occurs Stress corrosion occurs when atoms leave cracks due to internal or applied stress, which sharpens the cracks in certain environments. How it's dangerous Stress corrosion can be dangerous because it may not occur until stress is applied, even in a relatively inert environment. How it's detected Signs of stress corrosion include visible cracks, changes in the material's color or texture, and sudden or unexpected failure. Cracks often start at stress risers like notches and scratches, making them difficult to detect until they've grown significantly. How it's controlled Stress corrosion can be controlled by maintaining low levels of oxygen and chloride ions in the environment, and by using low carbon steels. Industries affected Industries commonly affected by stress corrosion include nuclear power, chemical processing, food processing, petroleum and oil extraction, and medical and pharmaceutical. ACID RAIN AND CORROSION Yes, acid rain can cause corrosion: Metals Acid rain increases the rate of corrosion for metals like iron, steel, copper, and bronze. For example, the Statue of Liberty has been damaged by acid rain and oxidation for over 30 years, causing it to turn green. Stone Acid rain reacts with calcium compounds in rocks like limestone and marble to create gypsum, which can flake off. This can cause the inscriptions on old gravestones to become illegible. Paint Acid rain can contribute to the deterioration of paint. Concrete Acid rain can corrode the components in reinforced concrete, turning it into a water-soluble medium. Acid rain is formed when certain emissions come into contact with water in the atmosphere. RUSTING OF IRON Rusting of iron is a chemical reaction that occurs when iron is exposed to water and oxygen, and is an example of oxidation: Rusting of iron What happens Iron reacts with oxygen and water to form hydrated iron(III) oxide, also known as rust Chemical Fe (s) + O2 (g) + H2O (l) → Fe2O3.xH2O (s) equation What it looks A brown powdered mass forms on the iron like Factors that Salt dissolved in water, acid rain speed up rusting What it does Rust eats away at the metal, and the oxides take up more volume than the original metal, which can damage structures Rusting is a chemical change that can't happen to other metals, only iron or steel. When other metals oxidize in air, it's called corrosion.