ME-515 Ceramics Shaping and Forming PDF
Document Details
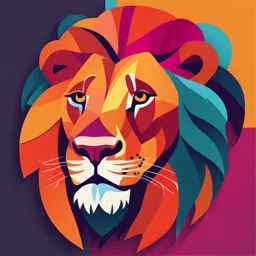
Uploaded by ThrilledYeti9069
Al-Balqa' Applied University (BAU)
Dr. Al-Montaser Bellah Al-Ajlony
Tags
Summary
This document is a chapter from a course on ceramics, discussing various shaping and forming techniques. It covers topics such as powder compaction, casting, and plastic forming along with different considerations.
Full Transcript
ME-515 CERAMICS Chapter -23 Shaping and Forming By Dr. Al-Montaser Bellah Al-Ajlony Fall-2024/2025 Shaping and Forming This is the pottery chapter! Many of the techniques that are now being used to shape high-tech ceramics have...
ME-515 CERAMICS Chapter -23 Shaping and Forming By Dr. Al-Montaser Bellah Al-Ajlony Fall-2024/2025 Shaping and Forming This is the pottery chapter! Many of the techniques that are now being used to shape high-tech ceramics have been used by potters for millennia but have been refined for today’s high-tech applications and for new ceramic materials. We can just process dry powder and sinter it, but it’s much more common to add some amount of liquid, just as the potter adds water to clay; we then shape the object and fire it. Shaping transforms an unconsolidated powder mixture into a coherent, consolidated body having a chosen geometry. The selection of a shaping operation for a particular product is dependent on the size and dimensional tolerances of the product, the requisite microstructural characteristics, the levels of reproducibility required, economic considerations, and of course the required shape. Here we concentrate on three-dimensional objects ranging from fishhooks to turbine blades. However, we do cover slip casting, which we use in only a limited way for thin films. 2 The Words There’s a special vocabulary for shaping ceramics because it’s an ancient art. Once the constituent powders have been prepared in the desired purity and particle size, the next step in the processing of most ceramic products is fabricating them into useful shapes. Many shaping methods are used for ceramic products, and they can be grouped into three basic categories, which are not necessarily independent. 1) Powder compaction: e.g., dry pressing, hot pressing, cold isostatic pressing 2) Casting: using a mold with the ceramic as, or containing, a liquid or slurry 3) Plastic forming: e.g., extrusion, injection molding—using pressure to shape the green ceramic 3 Main ceramic shaping techniques ❑ Powder compaction is simply the pressing of a free flowing powder. The powder may be dry pressed (i.e., without the addition of a binder) or pressed with the addition of a small amount of a suitable binder. The pressure is applied either uniaxially or isostatically. The choice of pressing method depends on the shape of the final product. We make simple shapes by applying the pressure uniaxially; more complex shapes require isostatic pressing. ❑ Casting ceramics is carried out at room temperature and generally requires the ceramic powder particles to be suspended in a liquid to form a slurry; note that this process is quite unlike the casting of metals. The slurry is then poured into a porous mold that removes the liquid (it diffuses out through the mold) and leaves a particulate compact in the mold. This process is known as slip casting. The process has been used to form many traditional ceramic products (e.g., sanitaryware) and more recently in forming advanced ceramic products (e.g., rotor blades for gas turbines). The other main casting process for ceramics is tape casting, which is used to make thick films or sheets. 4 Main ceramic shaping techniques ❑ Plastic forming is done by mixing the ceramic powder with a large volume fraction of a liquid to produce a mass that is deformable (plastic) under pressure. Such processes were developed and used originally for clay and have since been adapted to polymeric materials. For traditional clay-based ceramics, the liquid is mainly water. For ceramic systems that are not based on clay, an organic liquid may be used in place of, or in addition to, water. The binders are often complex and contain multiple components to achieve the required viscosity and burn-out characteristics. Table 23.1 lists the major methods that are included in each of the above categories and the types of shape that can be produced 5 First, some of the words: Binder: a component that is added to hold the powder together while we shape the body. Slurry: a suspension of ceramic particles in a liquid. Plasticizer: the component of a binder that keeps it soft or pliable. It improves the rheological properties. Green: a ceramic before it’s fired. Brown, white, or gray potter’s clays are well-known green ceramics. Slip: the liquid-like coating used to form the glaze when fired. Some of the shaping methods we describe in this chapter produce a ceramic compact that is strong enough to be handled and machined; but it is not fully dense, and the bonds between the grains are not strong. This is called the “green” state and represents a transition state between the loose powder and the high-density sintered product. Other shaping methods—those that involve the use of high temperatures and pressures—can directly produce a very dense sintered product. Much of what we talk about here has a parallel in the field of powder metallurgy; the theme is often processing powders, which are not necessarily ceramic powders. 6 Binders and Plasticizers It is often necessary to add a binder to the ceramic powder. The binder has two functions. In some shaping methods, such as extrusion, the binder provides the plasticity necessary for forming. The binder also provides the (green) shape with sufficient strength that it can survive the handling process between shaping and sintering. One of the most important requirements for the binder is that we must be able to eliminate it from the compact during the firing process without any disruptive effect: polymers are thus often ideal binders. In pottery, the binder is often water, which is present in sufficient quantity to make the clay easily shaped but retains the shape during firing. The idea is that we then add a plasticizer to optimize the rheology of the material. The distinction between binder and plasticizer is sometimes not too clear. 7 Slip and Slurry In general, slip consists of fine (1,000C because they become ductile, and the die bulges. Special alloys, mostly based on Mo, can be used up to 1,000C at pressures of about 80 MPa. Ceramics such as Al2O3, SiC, and Si3N4 can be used up to about 1,400C at similar pressures. Graphite is the most widely used die material and can be used at temperatures up to 2,200C and pressures of 10–30 MPa. The difficulty is that a graphite die tends to produce a very reducing environment. (You can make an Al2O3 sample vanish using a graphite die!) However, graphite does have many properties that make it suitable for a die. ❑ Easy to machine (but the dust is toxic if inhaled—like coal dust) ❑ Inexpensive ❑ Strength increases with increasing temperature ❑ Good creep resistance ❑ Excellent thermal conductivity ❑ Relatively low coefficient of thermal expansion 16 Hot Pressing Hot pressing, like dry pressing, is limited to simple solid shapes, such as flat plates, blocks, and cylinders. More complex or large shapes are difficult and often impossible to produce by hot pressing. Although it is extensively used in university and government laboratories, the technique is limited as a production tool because of its high cost and low productivity. For any mass-produced ceramic product, there would be considerable commercial pressure for a company to find a less expensive alternative. However, some commercial hot pressed ceramic products are available. These products are those that require a small grain size, high density (low porosity), or low impurity levels. 17 Hot Pressing Examples of such products are given in Table 23.2. Isostatic pressing involves the application of hydrostatic pressure to a powder in a flexible container. The advantages of applying pressure in all directions are that there is more uniform compaction of the powder and more complex shapes can be produced than with uniaxial pressing. Isostatic pressing can be performed either with or without applied heat. 18 Cold Isostatic Press (CIP) There are many variations on using the cold isostatic press (CIP); here we just emphasize some basic themes. Figure 23.3 illustrates the so-called wet- bag CIP process. Powder is weighed into a rubber bag, and a metal mandrel is inserted that makes a seal with the mouth of the rubber bag. The sealed bag is placed inside a high- pressure chamber that is filled with a fluid (normally, a soluble oil–water mixture) and hydrostatically pressed. The pressures used can vary from ~20 MPa up to 1 GPa depending on the press and the application. For production units, the pressure is usually 400 MPa. Once pressing is complete, the pressure is released slowly, the mold is removed from the pressure chamber, and the pressed component is removed from the mold. 19 Cold Isostatic Press (CIP) The advantages of the wet-bag process are: ❑ Wide range of shapes and sizes that can be produced ❑ Uniform density of pressed product ❑ Low tooling costs ❑ The disadvantages are: ❑ Poor shape and dimensional control (particularly for complex shapes) ❑ Products often require green machining after pressing ❑ Long cycle times (typically 5–60 min) that give low production rates A small wet-bag isostatic press, for producing laboratory samples and low-volume production parts, might have an internal diameter of 150 mm and a depth of 460 mm. Large wet-bag presses may have cavity diameters >1.8 m and lengths up to 3.7 m. The wet-bag CIP process can be automated. 20 Cold Isostatic Press (CIP) A mold for the dry-bag CIP is shown in Figure 23.4. The main distinction of the dry-bag process is that the rubber mold is now an integral part of the press. The high-pressure fluid is applied through channels in the mold. After pressing, the pressed part is removed without disturbing the mold at all. Hence, the dry-bag press can be readily automated. Fully automated units are widely available and have been operating in the high-volume production of ceramic parts for over two decades. Production rates of up to one part per second are being achieved industrially. 21 Cold Isostatic Press (CIP) The dry-bag CIP has been used for many years to press spark-plug insulators. The steps in this process are shown in Figure 23.5. Notice the insertion of the inner pin in the mold. The world’s largest producers of spark plugs produced by this method are Champion and AC Spark Plug. 22 Hot Isostatic Pressing (HIP) The hot isostatic press (HIP) uses the simultaneous application of heat and pressure. We refer to this process as HIPing and the product as being HIPed. A furnace is constructed within a high- pressure vessel, and the objects to be pressed are placed inside. Figure 23.6 shows a typical HIP arrangement. Temperatures can be up to 2,000C, and pressures are typically in the range 30–100 MPa. A gas is used as the pressure medium— unlike in the CIP where a liquid is often used. Argon is the most common gas used for HIPing, but oxidizing and reactive gases can also be used. Note that the high-pressure vessel is not inside the furnace. 23 Hot Isostatic Pressing (HIP) There are two variants of HIPing. ❑ Encapsulated: using a deformable container ❑ Not encapsulated: shape and sinter first, then HIPed In the original HIPing method, the ceramic powder was filled into a deformable metal can and then subjected to heat and pressure. This method was subsequently modified for small particle size powders. The powder compact was preformed to the desired shape by a process such as dry pressing or injection molding. The green compact was then encapsulated in a glass envelope that could be removed from the product after HIPing, as shown in Figure 23.7. 24 Hot Isostatic Pressing (HIP) The second variant does not involve encapsulation at all. The ceramic powder is first compacted using another shaping method, such as dry pressing or injection molding, and then sintered at relatively high temperatures in a furnace to close all the surface pores, thereby preventing the entry of the gas during subsequent HIPing. The steps in this process, which is sometimes referred to as sinter-plus-HIP, are shown in Figure 23.8. 25 Hot Isostatic Pressing (HIP) Now HIPing is used for a wide variety of ceramic (and metallic) components, such as alumina-based tool bits and the silicon nitride nozzles The advantages of the HIPing process are becoming more important as interest in structural ceramics (e.g., Si3N4) grows. Nonoxide ceramics can be HIPed to full density while keeping the grain size small and not using additives. Very high densities combined with small grain sizes (because of the relatively low temperatures) leads to products with special mechanical properties. HIPing has also been applied to the formation of piezoelectric ceramics— e.g., BaTiO3, SrTiO3, lead zirconate titanate (PZT)— for use in acoustic wave filters and oscillators. ❖ Uses: produces dense materials without growing the grains ❖ Disadvantage: cost 26 Slip Casting For slip casting, the slip is poured into a mold (usually plaster of Paris: 2CaSO4H2O) that has been made by casting around a model of the required shape, which was itself suitably enlarged to allow for shrinkage of the cast ceramic on drying and sintering. The fineness of the powder (in the slip) and the consequent high surface area ensure that electrostatic forces dominate gravity so that settling does not occur. The electrochemistry of the slip is quite complex: Na silicate (or soda ash) is added to the slip to deflocculate the particles. The water passes, via capillary action, into the porous plaster, leaving a layer of the solid on the wall of the mold. Once a sufficient thickness has been cast, the surplus slip is poured out, and the mold and cast are allowed to dry. These steps are shown in Figure 23.9. This variant of slip casting, which is the most widely used, is also called drain casting. A very effective technique used by some potters is to produce a multilayer slip, parts of which are removed before firing. 27 Slip Casting Slip casting is a low-cost way to produce complex shapes. In the traditional pottery industry, it is the accepted method for the production of teapots, jugs, and figurines, although handmade items are likely to be hand-thrown. Large articles, such as wash- hand basins and other whitewares, are also mass- produced by slip casting. (Whitewares are not necessarily white.) One of the telltale signs of a ceramic product made by slip casting is that it is hollow. 28 Slip Casting A variant of the slip casting process is solid casting. In solid casting, slip is continually added until a solid cast is made. These items will not be hollow—relatively, they will be heavier. Slip casting is also used in the fabrication of some technical and structural ceramics. It is the standard method used to make alumina crucibles and has been successfully used to make complex structural ceramic components such as gas-turbine rotors. The technique of doctor-blading, is just another method of shaping the slip—ensuring that the slip is spread as a uniform layer. 29 Extrusion Extrusion involves forcing a deformable mass through a die orifice (e.g., toothpaste from a tube). The process is widely used to produce ceramic components having a uniform cross section and a large length-to-diameter ratio, such as ceramic tubes and rods, as illustrated in Figure 23.10. Clay with a suitable rheology for the extrusion process (essentially a paste) can be made by controlling the amount of water. Clay-free starting materials (e.g., Al2O3) are mixed with a viscous liquid such as polyvinyl alcohol or methylcellulose and water to produce a plastically deformable mass. 30 Extrusion An extrusion press such as that shown in Figure 23.11 is standard equipment in the potter’s barn. 31 Extrusion Table 23.3 lists examples of compositions of extrusion bodies. Extrusion is also used to produce the alumina shells for sodium vapor lamps and the honeycomb-shaped catalyst supports for automotive emission-control devices. The catalyst supports are designed to give a high surface area; they can consist of hundreds of open cells per square centimeter and a wall thicknesses of $10,000 and a mold for a turbine rotor >$100,000, but such molds are reusable because they are never subjected to high temperatures. 36 Rapid Prototyping (RP) Rapid prototyping (RP), or solid free-form fabrication (SFF), is a relatively recent approach to forming ceramic components. There are various forms of RP techniques, but they are based on a common principle: a computer directly controls the shaping process by accessing computer-aided design (CAD) files. We can thus use RP to form a three dimensional component without the use of a die or a mold. RP techniques are used commercially for fabrication of parts from polymers for design verification and form-and fit applications; these techniques have more recently been applied to forming parts out of ceramics. In this section we look at just two of the several RP methods. ❑ Stereo Lithography (SLA) ❑ Fused Deposition Modeling (FDM) Both these methods have been successfully used to form ceramic components. 37 SLA The SLA process is illustrated in Figure 23.13. In SLA, the component is formed from an epoxy resin. As the z-stage elevator is lowered, an ultraviolet laser beam whose position is controlled by a computer cures successive layers of the uncured resin. In this way, a three-dimensional component is made, one layer at a time. It can take many hours to build a large complex object, but this is still rapid compared to the time taken to form a component by, for example, injection molding, where fabrication of the tools can take a considerable amount of time. To form ceramic components by SLA, it is necessary that the polymer is loaded with ceramic powders. Si3N4, SiO2, and Al2O3 powders have all been used for SLA. 38 FDM In FDM, the source material is a thermoplastic polymer filament that is heated and extruded to form the product, as shown in Figure 23.14. The product is formed in a layer by- layer manner. The computer controls the x-y position of the filament and the deposition rate. The filament can be loaded with up to 60 vol% ceramic powders; once the part is completed, the binder is removed and the part is sintered. Most of the work in the RP of ceramic parts by FDM has involved Si3N4. The feasibility of making components out of Al2O3, SiO2, and PZT has also been demonstrated. 39 Green Machining To obtain the desired shape of a ceramic product, it is often necessary to machine it. Machining can be performed either before or after the product has been sintered. If the machining is done before sintering, while the component is still in the green state, the process is called green machining. The advantages of green machining compared to machining the sintered product are that there is a considerable reduction in machining time and a reduction in cost because of less tool wear and the possibility of using cheaper tools. Table 23.5 compares the use of different tool materials in the green machining of a Si compact before nitriding it to form Si3N4. In the processing of spark plug insulators, the final step prior to firing involves green machining, as shown earlier in Figure 23.5. 40 Binder Burnout In pottery, the binder burnout is the removal of water from the shaped clay. The rest of the firing process causes structure changes and transformations in the silicate itself. Forming methods for engineering ceramics (e.g., injection molding) produce green bodies that can contain 30–50 vol% of organic binder. We generally want to remove this binder without cracking or distorting the ceramic compact. Binder burnout is one of the most likely stages to form defects in the processing of a ceramic: macroscopic defects, such as cracks and blisters, can be introduced at this stage; and they affect the mechanical strength and other properties. An additional complication is that the binder system used in fabricating many commercial ceramic parts often consists of several components. These components have different boiling points and decomposition temperatures. The components with low boiling points (e.g., waxes) may be removed by evaporation at fairly low temperatures. Oxidation or decomposition at higher temperatures removes components with high molecular weight. 41 Binder Burnout For oxide ceramics, the binder can be oxidized to form H2O, CO, and CO2 when the green compact is heated in air. Binder burnout in air generally presents no problem. However, there are some situations where binder burnout in air can be a problem. An example is the use of poly(vinyl butyral) with Al2O3, where carbon residues can be as high as thousands of parts per million even after burnout in air at 700C for 24 h. Nonoxide ceramics generally cannot be heated in oxidizing environments, and binder burnout in inert or reducing atmospheres is more difficult. Pyrolysis of many binders in these environments is not well understood, and most binders leave some carbonaceous residue that could be detrimental to the subsequent sintering stage. The process of binder removal is kept slow to reduce the possibility of macrodefects being produced 42 Binder Burnout Figure 23.15 shows a plot of a binder removal cycle. In this plot, a pressurized gas, called a sweep gas, has been passed over the part to help sweep away the vapor. The cycle time depends on the size of the part. Thin sections take much shorter times than thick sections. The debinding time is proportional to the square of the section thickness of the compact. Binder burnout continues to be an active area of ceramics research, with one of the main thrusts being in developing models of binder decomposition and diffusion. 43 Making Porous Ceramics In many traditional applications for ceramics, particularly in structural and electrical applications, the sintered ceramic component is required to have minimum porosity. However, in a growing number of applications (e.g., in ceramic humidity and gas sensors), porosity is not just desirable, it is required. Several different methods can be used to produce porous structures. ❑ Use large particles with a very small size distribution to avoid dense packing. ❑ Underfire a green compact to leave a large amount of fine pores. ❑ Add organic particles (diameter >20 μm) to the powder mixture. When they burn out, they leave behind porosity. ❑ Use a binder system that contains a foaming agent and produces a large amount of gas bubbles in the mixture. ❑ Impregnate a foam that has continuous porosity, and then burn it out. ❑ Use a glass composition that phase-separates and then leaches out (e.g., using an acid) one of the phases to produce a porous glass. 44 Shaping Glasses Glass can be shaped using many different processes. Casting or molding: examples are the 20-in. thick Palomar telescope mirror and sub-millimeter thick molded-glass aspheric lenses that are used in everything from laser printers to optical disk storage devices and optical communications systems. Pressing needs a mold that is gray cast iron (to 1,000C), stainless steel (can use for borosilicates at 1,185C and glass ceramics at 1,480C), or even bronze. Usually, though, the mold is cooled. The process uses a viscosity of ~4 kP and has been applied to objects weighing 5 g to 15 kg. The finished object can be fire- polished. This process, shown in Figure 23.19, is quite similar to the HIPing technique 45 Shaping Glasses Sagging or slumping is a simple method whereby the glass is heated, so that it “slumps” into the mold. The technique can also be used for clay; effectively, it is pressing, with gravity providing half the press. Glass blowing was clearly in use in the first century BCE. The temperature is critical as it determines the working range. There are other factors as well, such as the air pressure, the role of gravity and the centrifugal force produced by the blower. The craftsman produces free-blown objects or can blow the glass inside a mold. When a ribbon or hub machine is used, the glass is invariably blown into a mold. Drawing is used for glass tubes and sheets. For tubes, the variations are Danner (e.g., tubes for fluorescent lights), Vello (large-diameter tubes), downdrawn tubes (used for vacuum tubes or uses a vacuum), and updrawn tubes (for glass thermometers). Sheets are drawn in the same way: using a slot orifice, with an overflow pipe, using updraw or floating. 46 Shaping Glasses Spinning is used for fibers and is very reminiscent of the beginnings of industry (the spinning jenny). Rolling is an old technique that is still in use. The lost wax process of forming glass shapes has been used since the fifth century CE to make glass shapes. Originally, the molten glass was poured into an outer mold made of beeswax, which could easily be removed. Inlays in glass, such as sandwiched-gold glass—gold leaf is pressed between two layers of glass—was made perhaps as early as ~250 BCE. Final machining is done using Vycor (the “cor” is from Corning), Macor, or similar specially treated glasses. (Vycor contains “built-in” pores; Macor contains small grains of mica). Core forming was one of the earliest methods used to shape glass. A shape was fashioned in clay, and the glass was then trailed around the core until it completely covered it. It could be heated further so that the coils fused together. When cool, the clay core would be removed, leaving a stand-alone glass vessel. 47 The End Thank you 48