Chapter 9 Solid State Welding PDF
Document Details
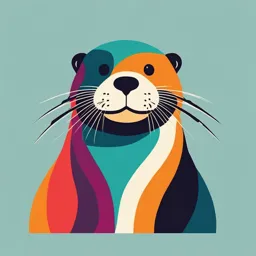
Uploaded by PhenomenalHedgehog
Tags
Summary
This document covers various solid-state welding processes. It includes details on different joining methods, such as cold welding, roll bonding, ultrasonic welding, friction welding, resistance welding, and their applications. The document explains the principles and mechanisms involved in each welding technique.
Full Transcript
CHAPTER 9 JOINING PROCESSES: SOLID-STATE WELDING BMFS 2613 MANUFACTURING PROCESS 1 Chapter Outline Introduction Cold Welding and Roll Bonding Ultrasonic Welding Friction Welding Resistance Welding...
CHAPTER 9 JOINING PROCESSES: SOLID-STATE WELDING BMFS 2613 MANUFACTURING PROCESS 1 Chapter Outline Introduction Cold Welding and Roll Bonding Ultrasonic Welding Friction Welding Resistance Welding 2 Introduction Solid-state welding processes are joining takes place without fusion at the interface of the two parts to be welded. In solid-state welding no liquid or molten phase is required for joining. For a strong bond, it is essential that the interface be free of contaminants, such as oxide films, residues, metalworking fluids, and even adsorbed layer of gas. Solid-state bonding involves one or more of the following: Heat Pressure Relative interfacial movement Most joining processes are now automated by robotics, vision systems, sensors, and adaptive computer controls for the purposes of cost reduction, consistency of operation, reliability of weld quality, and higher productivity. 3 Cold Welding In cold welding (CW), pressure is applied to the workpieces through dies or rolls. Because of the plastic deformation involved, it is necessary that at least one (but preferably both) of the mating parts be sufficiently ductile. CW is usually performed on nonferrous metals or on soft iron with little carbon content. Prior to welding, the interface is degreased, wire brushed, and wiped to remove oxide smudges. Applications include products made of wire and electrical connections 4 Roll Bonding The pressure required for welding can be applied through a pair of rolls, a process called roll bonding or roll welding (ROW). Surface preparation is important for good interfacial strength. The operation can be carried out at elevated temperatures (hot roll bonding). Example; cladding of pure aluminum over precipitation hardened aluminum alloy sheet for a corrosion resistant surface with a strong inner core, typically used in aerospace industry. 5 Ultrasonic Welding In ultrasonic welding (USW), the faying surfaces of the two components are subjected to a normal force and oscillating shearing (tangential) stresses. The shearing stresses are applied by the tip of a transducer (Fig. 31.2a). The frequency of oscillation is generally in the range of 10 – 75 kHz, although a lower or higher frequency can be employed. proper coupling between the transducer and the tip (called a sonotrode/horn) is important for efficient operation. 6 FIGURE 31.2 (a) Components of an ultrasonic-welding machine for making lap welds; the lateral vibrations of the tool tip cause plastic deformation and bonding at the interface of the workpieces. (b) Ultrasonic seam welding, using a roller as the sonotrode. Ultrasonic Welding The shearing stresses cause plastic deformation at the interface of the two components, breaking up oxide films and contaminants, and thus allowing good contact and producing a strong solid-state bond. The temperature generated in the weld zone is usually 1/3 to ½ of the melting point (no melting/fusion). Can be used with metallic or nonmetallic materials, including dissimilar metals. The welding tip can be replaced with a rotating disks (Fig. 31.2b) for seam welding. 8 Video- Ultrasonic Welding 9 Friction Welding In friction welding (FRW), the heat required for welding is generated through friction at the interface of the two components being joined. One of the workpiece components in friction welding remains stationary while the other is placed in a chuck or collet, and rotated at a constant peripheral speed as high as 15 m/s. The two members to be joined are then brought into contact under an axial force (Fig. 31.3). After sufficient contact is established, the rotating member is brought to a quick stop while the axial force is increased. Oxides and other contaminants at the interface are expelled by the radial outward movement of the hot metal at the interface. 10 FIGURE 31.3 Sequence of operations in the friction-welding process: (1) The part on the left is rotated at high speed. (2) The part on the right is brought into contact with the part on the left under an axial force. (3) The axial force is increased, and the part on the left stops rotating; flash begins to form. (4) After a specified upset length or distance is achieved, the weld is completed. The upset length is the distance the two pieces move inward during welding after their initial contact; thus, the total length after welding is less than the sum of the lengths of the two pieces. The flash subsequently can be removed by machining or grinding. Friction Welding The pressure at the interface and the heat resulting from friction are sufficient for a strong joint to form. The weld zone is usually confined to a narrow region, and its size and shape depend on: Amount of heat generated Thermal conductivity Mechanical properties of the materials being joined at elevated temperatures Rotational speed Axial pressure applied Join a wide variety of materials, provided that once the components has some rotational symmetry. Solid or tubular parts can be welded, with good joint strength. The interface in FRW develops a flash by plastic deformation of the heated zone. Flash can easily be removed by machining. 12 Video – Friction Welding 13 Video – Friction Welding in slow motion 14 Friction Stir Welding In the friction stir welding (FSW) process, a third body (called a probe) is plunged into the joint and rubs against the two surfaces to be joined. The nonconsumable rotating probe is typically made of cubic boron nitride, 5 to 6 mm in diameter and 5 mm high. The contact pressure causes frictional heating, raising the temperature 230 ° C to 260°C. The tip of the rotating probe forces mixing or stirring of the material. No shielding gas/surface cleaning is required. 15 FIGURE 31.5 The friction-stir-welding process. (a) Schematic illustration of friction stir welding; aluminum-alloy plates up to 75 mm (3 in.) thick have been welded by this process. (b) Multi-axis friction stir welding machine for large workpieces, such as aircraft wing and fuselage structures, that can develop 67 kN (15,000 lb) axial forces, is powered by a 15 kW (20 hp) spindle motor, and can achieve welding speeds up to 1.8 m/s. Source: (b) Courtesy of Manufacturing Technology, Inc. Friction Stir Welding Thickness of welded material: 1mm – 50 mm, welded in a single pass. Materials have been welded: aluminum, magnesium, nickel, copper, steel, stainless steel and titanium. Extend to polymers and composites. Applications: aerospace, automotive, shipbuilding and military vehicles. The welding equipment can be conventional, vertical spindle milling machine. For special applications, machinery dedicated to FSW is also available. Quality: good, minimal pores, uniform material structure, low distortion and little microstructural changes. 17 Resistance Spot Welding In resistance spot welding (RSW), the tips of two opposing solid, cylindrical electrodes touch a lap joint of two sheet metals, and resistance heating produces a spot weld (Fig. 31.6a). In order to obtain a strong bond in the weld nugget, pressure is applied until the current is turned off and the weld has solidified. Accurate control and timing of the alternating current (AC) and of the pressure are essential in RSW. Resistance Spot Welding The surfaces of a spot weld have a slightly discolored indentations. The weld nugget (Fig. 31.6b) may be up to 10 mm in diameter. The current level depending on the materials being welded and their thicknesses; for example, the current is typically 10,000 A for steels and 13,000 A for aluminum. Electrodes generally are made of copper alloys and must have sufficient electrical conductivity and hot strength to maintain their shape. 19 FIGURE 31.6 (a) Sequence of events in resistance spot welding of a lap joint. (b) Cross-section of a spot weld, showing the weld nugget and the indentation of the electrode on the sheet surfaces. This is one of the most commonly used processes in sheet-metal fabrication and in automotive-body assembly. Spot welding maybe performed by means of single or multiple pairs of electrodes; the required pressure is supplied through mechanical or pneumatic means. Rocker-arm-type spot welding machines normally are used for smaller parts. Press-type machines are used for larger workpieces. Spot welding is widely used for fabricating sheet metal parts; examples range from attaching handles to stainless steel cookware to spot welding mufflers and large sheet metal structures. Modern spot welding equipment is computer controlled, for optimum timing of current and pressure. Spot welding guns are manipulated by programmable robots. Wide application: automobile bodies 21 FIGURE 31.8 Spot-welded (a) cookware and (b) muffler. (c) A large automated spot-welding machine. The welding tip can move in three principal directions; sheets as large as 2.2 m × 0.55 m (88 in. × 22 in.) can be accommodated in this machine, with proper workpiece supports. (d) A spot welding machine. Source: (c) and (d) Courtesy of Taylor-Winfield Technologies, Inc. Test methods for spot welds: (a) tension-shear test, (b) cross- tension test, (c) twist test, and (d) peel test Video – Resistance Spot Welding Resistance Seam Welding Resistance seam welding (RSEW) is a modification of spot welding wherein the electrodes are replaced by rotating wheels or rollers (Fig. 31.10a). Using a continuous AC power supply, the electrically conducting rollers produce a spot weld whenever the current reaches a sufficiently high level in the AC cycle. The typical welding speed is 1.5 m/min for thin sheets. 25 FIGURE 31.10 (a) Seam-welding process in which rotating rolls act as electrodes; (b) overlapping spots in a seam weld; (c) roll spot welds; and (d) mash seam welding. Resistance Seam Welding With a sufficiently high frequency or slow traverse speed, these spot welds overlap into a continuous seam and produce a joint that is liquid- and gas-tight (Fig. 31.10b). Applications: longitudinal seam of steel cans for household products, mufflers and gasoline tanks. In roll spot welding, the current to the roll is applied only intermittently, resulting in a series of spot welds that are specified intervals along the length of the seam (Fig. 31.10c). In mash seam welding (Fig. 31.10d), the overlapping welds are about one to two times the sheet thickness, and the welded seam thickness is about 90% of the original sheet thickness. 27 High-frequency Resistance Welding High-frequency resistance welding (HFRW) is like seam welding, except that a high-frequency current of up to 450 kHz is employed. Applications: butt-welded tubing or pipe, where the current is conducted through two sliding contacts to the edges of roll-formed tubes. The heated edges are then pressed together by passing the tube through a pair of squeeze rolls; the flash formed, if any, is then trimmed off. 28 Resistance Projection Welding In resistance projection welding (RPW), FIGURE 31.12 (a) Schematic illustration of resistance projection high electrical resistance at the joint is welding. (b) A welded bracket. (c) and (d) Projection welding of nuts or threaded bosses and studs. (e) Resistance-projection-welded grills. developed by embossing one or more projections (dimples) on one of the surfaces to be welded. The projections may be round or oval for design or strength purposes. High localized temperatures are generated at the projections, which are in contact with the flat mating part. Weld nuggets are like those in spot welding and are formed as the electrodes exert pressure to soften and compress and flatten the projections. 29 FIGURE 31.13 (a) Flash-welding process for end-to-end welding of solid rods or tubular parts. (b) and (c) Typical parts made by flash welding. (d) and (e) Some design guidelines for flash welding. Flash Welding In flash welding (FW), also called flash butt welding, heat is generated very rapidly from the arc as the ends of the two members begin to make contact and develop an electrical arc at the joint. The FW process is suitable for end-to-end or edge-to-edge joining strips and sheets of similar or dissimilar metals. 30 Stud Welding Stud welding (SW), also called stud arc welding, is like flash welding. Ceramic ring (called ferrule) is placed around the joint in order to concentrate the heat generated, prevent oxidation, and retain the molten metal in the weld zone. Applications: automobile bodies, electrical panels, shipbuilding and building construction. Sequence of operations in stud welding, commonly used for welding bars, threaded rods, and various fasteners onto metal plates. 31 THANK YOU 32