Chapter 7 Pages 103 - 110.docx
Document Details
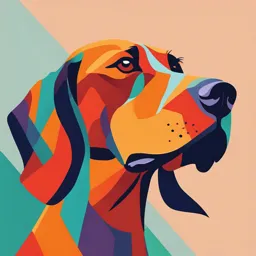
Uploaded by VisionaryAngel
Full Transcript
In many organisations, particularly manufacturing businesses, materials are a significant part of the total costs of operations. In a manufacturing company, most materials can be classified as raw materials and bought in components, as work in progress (part-finished production) or as finished good...
In many organisations, particularly manufacturing businesses, materials are a significant part of the total costs of operations. In a manufacturing company, most materials can be classified as raw materials and bought in components, as work in progress (part-finished production) or as finished goods (completed items of production not yet sold). This chapter explains the procedures and documentation that are used for purchasing and using materials, and the way that materials are accounted for within a cost accounting system. Materials costs, including wastage, need to be controlled. There must also be a method for giving a value to materials held in inventory at the end of an accounting period. This chapter goes into some detail about the system for costing materials and controlling materials costs. Materials r TOPIC LIST Types of material Buying materials Valuing materials issues and inventories Inventory control Inventory control levels Computers and inventory control SYLLABUS REFERENCE 81 (a) A2 Cc), 81 Cb), (e) 81 Cc) 81 (f), Cg) B1 Ch), (i) 81 (j) //}3 Management information 2 Cost accounting systems (cl Identify the documentation required, and the flow of s documentation, for different cost accounting transactions Cost recording Accounting for materials Cal Describe the main types of material classification K (bl Describe the procedures and documentation required to K ensure the correct authorisation, coding, analysis and recording of direct and indirect material costs s (cl Explain, illustrate and evaluate the FIFO, LIFO and periodic and cumulative weighted average methods used to price materials issued from inventory s (el Calculate material input requirements, and control measures, where wastage occurs K (fl Describe the procedures required to monitor inventory and to minimise discrepancies and losses s Explain and illustrate the costs of holding inventory and of being without inventory Chl Explain, illustrate and evaluate inventory control levels (minimum, maximum, reorder) Calculate and interpret optimal order quantities s Explain the relationship between the materials costing K system and the inventory control system I , Materials can be classified according to the substances that make them up, how they are measured, or ' their physical properties. I. I - - - - - - - - - - - - - - - - - - - - - - - - - Classifying materials - I There are a number of different ways in which materials can be classified. The three main ways of classifying materials are as follows. They can be classified according to the substances that make them up. They can be classified according to how they are measured. They can be classified according to their physical properties. Materials may be made of one or more substances. For example, when classifying materials according to the substances that make them up, they may be classified as either wood, plastic, metal, wool and so on. Many items may be made up of a combination of substances. CHAPTER 7 // MATERIALS You may also classify materials according to how they are measured. Accounting text books could make it easy for you to believe that all materials come by the litre, metre or kilogram. In practice however, you will find that materials really come in bags, packets or by the thousand. Finally, materials may also be classified by one or more of their physical properties. The same basic piece of material may be distinguished by one or more of the following features: Colour Shape Fire resistance Water resistance Abrasiveness Flexibility Quality ---- Performance Objective 10 requires you to manage working capital requirements (which include inventories) effectively. The knowledge you will gain in this chapter will help you to demonstrate your competence in this area. Raw materials Raw materials are goods purchased for incorporation into products for sale. Raw materials area direct cost. Raw materials is a term which you are likely to come across often, both in your studies and your workplace. But what are raw materials? Examples of raw materials are as follows: Clay for making terracotta garden pots Timber for making dining room tables Paper for making books Raw materials are a direct cost of production as they are easily identifiable with a unit of production. QUESTION Raw materials Without getting too technical, what are the main raw materials used in the manufacture of the following items? (a) A car (bl A box of breakfast cereal A house (just the basic structure) Your own organisation's products ANSWER Metal, rubber, plastic, glass, fabric, oil, paint, glue. Cereals, plastic, cardboard, glue. You might have included sugar and preservatives and so on, depending upon what you eat for breakfast. Sand, gravel, cement, bricks, plaster, wood, metal, plastic, glass, slate. You will have to mark your own answer. If you work for a service organisation like a firm of accountants, you could view the paper of sets of accounts sent out to clients as raw materials, although in practice.such materials are likely to be regarded as indirect costs. Work in progress Work in progress is a term used to represent an intermediate stage between the manufacturer purchasing the materials that go to make up the finished product and the finished product. Work in progress is another term which you are likely to come across often, and valuing work in progress is one of the most difficult tasks in costing. Work in progress means that some work has been done on the materials purchased as part of the process of producing the finished product, but the production process is not complete. Examples of work in progress are as follows. (a) (b) (c) Terracotta pots which have been shaped, but which have not been fired, and are therefore unfinished. Dining room tables which have been assembled, but have not been polished, and are therefore not ready for sale. Paper which has been used to print books, but which has not yet been bound. The books are therefore not yet assembled, and not yet ready for sale. Finished goods A finished good is a product ready for sale or despatch. Did you notice how all of the examples of work in progress were items which were not ready for sale? It therefore follows that examples of finished goods are as follows. Terracotta pots ready for sale or despatch Dining room tables ready for sale or despatch Books ready for sale or despatch The examples in the previous paragraph show terracotta pots which have now been fired, dining room tables which have now been polished, and books which have now been bound. These final processes have transformed our work in progress into finished goods. Direct and indirect materials costs Materials are either a direct or indirect cost, depending upon how easily they can be traced to a specific unit of production. Direct materials are materials that are easily identifiable with a specific unit of production, such as raw materials. Indirect materials are materials that are not easily identifiable with a specific unit of production. In general, indirect materials do not form part of the final product, but do make the manufacture of that product possible. There are some exceptions to this, for example, nails used in the production of a cupboard can be identified specifically with the cupboard and form part of the final product. However, because the cost is likely to be relatively insignificant, the expense of tracing such costs does not justify the possible benefits from calculating more accurate direct costs. Indirect materials are often referred to as 'consumables' and include such things as cleaning products, oi and grease for machines, protective clothing, disposable tools and stationary supplies. Indirect material costs are an overhead cost. QUESTION Materia Distinguish between raw materials, work in progress and finished goods. Give three examples of indirect materials costs. CHAPTER 7 // MATERIALS ANSWER Raw materials are goods purchased for incorporation into products for sale, but not yet issued to production. Work in progress is the name given to the materials while they are in the course of being converted to the final product. Finished goods are the end products when they are ready to be sold. ss Some examples of indirect materials costs are as follows. Oil for machine maintenance Cleaning fluids and substances Rags, dusters and the like Glue if used in small quantities Secondary packaging, for example the sort of boxes you can pick up at the check-out in supermarkets f.l Buying materials 1---------------------------------- - , )) 1 Procedures and documentation are required for material purchases. · Purchasing procedures All businesses have to buy materials of some sort, and this means that decisions have to be made and somebody has to be responsible for doing the buying. Large businesses have specialist buying departments managed by people who are very skilled at the job. One of the reasons for the success of certain large companies is that they are expert at buying good quality goods at the best prices. In spite of this, the essence of a buying transaction is simple and, in fact, familiar because you buy things every day and (mainly subconsciously) go through the following process. You need something. You find out where you can buy it. You identify the most suitable item (take into account cost, quality, and so on). You order the item, or perhaps several if you will need more in the future. You receive the item. You pay for the item. In a business this process will be more involved, but only because those spending the money are likely to be different from those looking after the goods and those using them, and because none of those people will actually own the money spent. The following diagram illustrates who will be involved. 31S /O'J Receive goods Stores Pay for goods Accounts Purchasing documentation b which different departments can let each other know what Clearly there needs t? be omdeo ee: ut\ and even the smallest business will need to keep records o: they wa a;d se ::inba manual sy;tem that might be used in a fairly large organisatio_n. In re l1t ti: i::iy ·tha much of the procedure would be computerised, but this does not alter the basic principle or information flows. Purchase requisition form The first stage will be that the department requiring the goods will complete a purchase requisition forn asking the purchasing department to carry out the necessary transaction. An example is shown below. Note that the purchase requisition will usually need some form of authorisation, probably that of a senior person in the department requiring the goods and possibly also that of a senior person in the finance department if substantial expense is involved. PURCHASE REQUISITION Req. No. Department Date Suggested supplier: Requested by: Latest date required: Quantity Description Estimated Cost Unit $ Authorised signature: Order form Often the business will use a regular source of supply. The purchasing department may, however, be aware of special offers or have details of new suppliers: part of its job is to keep up to date with what i on the market. Thus once a purchase requisition is received in the purchasing department, the first tasl is to identify the most suitable supplier. CHAPTER 7 // MATERIALS Often the requisitioning department will specify the goods they require but the buying department may have a choice (for example in deciding what quality paper will be ordered for stationery). Whatever the decision made, an order form is then completed by the purchasing department (again, it may have to be authorised by the finance department to ensure that budgets are not being over-stepped) and this is sent to the supplier. The order form, an example of which is shown below, will contain the following details. The name and address of the ordering organisation The date of order, and reference numbers for both ordering department and supplier The address and date(s) for delivery (by road, rail, air and so on) or collection Details of goods/services: quantity, code (if any), specification, unit costs and so on An order form should be sent even if goods are initially ordered by telephone, to confirm that the order is a legitimate one and to make sure that the supplier does not overlook it. Purchase Order/Confirmation Fenchurch Garden Centre Pickle Lane Westbridge Kent Our Order Ref: Date To ffAddress) 7 Please deliver to the above address Ordered by: Passed and checked by: L _J Total Order Value £ Quantity Code Description/Specification £ p Subtotal VAT (@ 17.5%) Total The purchase order is important because it provides a means by which the business can later check that the goods received are the same as those ordered. Copies can be sent to the person who requisitioned the goods so that he knows they are on their way and also to the stores so that they can arrange to accommodate the goods. Either now or later a copy can be sent to the accounts department so that they can see·that goods invoiced were genuinely required and that the purchase was properly authorised. Despatch note Certain other documents may arise before the goods are actually received. The supplier may acknowledge the order and perhaps indicate how long it is likely to take to be fulfilled. A despatch note may be sent to warn that the goods are on their way. Delivery note We now move to the stores department. When the goods are delivered, goods inwards will be presented with a delivery note or advice note (although bear in mind that smaller suppliers may not go to these lengths). This is the supplier's document (a copy is signed by the person receiving the goods and returned to the supplier) and, as such, there is no guarantee that its details are correct. If the actual goods cannot be inspected immediately, the delivery note should be signed 'subject to inspection'. Goods received note Once the goods have been delivered they should be inspected as soon as possible. A goo s received note (GRN) will be completed by goods inwards on the basis of a physical check,which involves counting the items received and seeing that they are not damaged. r ACCOUNTS COPY GOODS RECEIVED NOTE WAREHOUSE COPY DATE: 711(a,,420'X5 _ TIME:- - ?_.(!_O_ft'!! _ - - - NO 5565 ORDER NO: SUPPLIER'S ADVICE NOTE NO: ------------ WAREHOUSE A QUANTITY CAT NO DESCRIPTION 2() 7P40() 7 /P'U- RECEIVED IN GOOD CONDITION: (INITIALS) A copy of the GRN can be sent to the purchasing department so that it can be matched with the purchase order. This is to make sure that the correct number and specification of items have been received. Any discrepancies would be taken up with the supplier. A copy of the GRN would also be sent to the accounts department so that it can be matched with the purchase invoice when it is received. The payment of the invoice is the end of the transaction (unless there is a mistake on the invoice or there was some problem with the delivery, in which case a credit note may later be received from the supplier). Buying and costing Clearly the buying department needs to retain cost information for the purpose of identifying suitable suppliers. This is likely to be in the form of catalogues and price lists. The costing department is chiefly interested in the actual cost of materials as shown on the invoice and included in the accounting records as cash and credit transactions.