Dash-8-400 Maintenance Manual: Propeller Systems PDF
Document Details
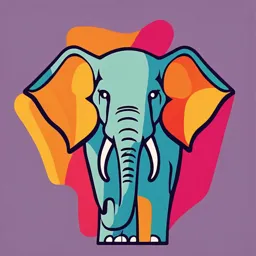
Uploaded by WellKnownEuropium7993
Riga Technical University
2010
Tags
Summary
This excerpt from the Dash-8-400 Maintenance Manual, Rev 3.0 from April 2010 covers various aspects of the propeller system, including the assembly, control system, propeller modes, and feathering systems. It provides detailed information on the components and functions of the system. The manual is produced by AERO- Bildung Aviation Training Center.
Full Transcript
61-00-00 Propeller General............................................................................................................................................................................................... 2 61-10-00 Propeller Assembly......................................................
61-00-00 Propeller General............................................................................................................................................................................................... 2 61-10-00 Propeller Assembly....................................................................................................................................................................................... 4 61-20-00 Propeller Control System.............................................................................................................................................................................. 8 61-20-01 Propeller Control......................................................................................................................................................................................... 20 61-20-10 Propeller Modes.......................................................................................................................................................................................... 22 61-20-11 Propeller Overspeed Governing.................................................................................................................................................................. 32 61-20-12 Automatic Underspeed Protection Circuit.................................................................................................................................................. 47 61-20-13 Propeller Synchrophasing System............................................................................................................................................................... 51 61-20-14 Propeller Feathering System....................................................................................................................................................................... 54 Rev 3.0 Apr 2010 Dash-8-400 Maintenance Manual 1/65 61-00-00 Propeller General The Dowty Aerospace Model R408 Propeller is a six-blade, fully feathering, reversible, counter-weighted constant-speed propeller. Bonded to the inner leading edge are electrical heater elements for anti-icing. The propeller blade is manufactured from carbon fiber and glass fiber-reinforced plastic with lightweight foam filler. The propeller is driven through a reduction gearbox that also provides mounting pads for the following accessories: The Pitch Control Unit (PCU). The Propeller Control Unit Oil Pump and Propeller Overspeed Governor. The Main Hydraulic Pump and The 115 V AC Variable Frequency Generator. Rev 3.0 Apr 2010 Dash-8-400 Maintenance Manual 2/65 Rev 3.0 Apr 2010 Dash-8-400 Maintenance Manual 3/65 61-10-00 Propeller Assembly The Dowty R408 propeller is a is constant speed, variable pitch six bladed propeller with full feathering and full reverse capabilities. The blades are installed in a flange mounted aluminum hub. Rev 3.0 Apr 2010 Dash-8-400 Maintenance Manual 4/65 Installed on the hub is a cylinder assembly which houses the pitch change actuator. A spinner is attached to the propeller composite backplate. Each blade is an all composite aerofoil construction with a steel outer root sleeve. The aerofoil has a foam core and twin carbon fibre spars with an overall braided carbon/glass fibre shell. Rev 3.0 Apr 2010 Dash-8-400 Maintenance Manual 5/65 A polyurethane spray coat for erosion protection is applied to the complete blade surface. A nickel leading edge guard is installed for blade erosion protection. A heater element to de-ice 70 percent of the blade radius is installed on the blade leading edge. The hub assembly has a one piece aluminum hub, with 15 integral steel mounting studs and 3 location/drive dowels. A backplate constructed of carbon fibre composite, and attached to the hub forms the aerodynamic interface between the spinner and engine nacelle. Rev 3.0 Apr 2010 Dash-8-400 Maintenance Manual 6/65 Three bronze rings sliprings installed directly onto the backplate are used to transfer electrical power for blade deicing. The hub supports six blades and has six pairs of blade root bearings. The lower bearing is an angular contact ball race, and the upper bearing is a taper roller race. Rev 3.0 Apr 2010 Dash-8-400 Maintenance Manual 7/65 61-20-00 Propeller Control System The propeller control system modulates blade angle or pitch to achieve the necessary propeller RPM (NP) in flight, to control pitch/thrust on the ground and also to feather the propeller when the engine is shut down. The propeller control system consists of the following components: Rev 3.0 Apr 2010 Dash-8-400 Maintenance Manual 8/65 Rev 3.0 Apr 2010 Dash-8-400 Maintenance Manual 9/65 The cockpit controls and indication lights. The Propeller Electronic Control (PEC) Unit. The Propeller Pitch Control Unit (PCU). The High Pressure PCU Oil Pump and Propeller O/S Governor Units (referred to as overspeed governor). The Propeller Feathering Pump and The Propeller System Sensors The Propeller Electronic Control (PEC) is a dual-channel microprocessor-based controller which uses inputs from the aircraft, propeller control system sensors, and the engine control system to control propeller pitch and speed. Rev 3.0 Apr 2010 Dash-8-400 Maintenance Manual 10/65 Rev 3.0 Apr 2010 Dash-8-400 Maintenance Manual 11/65 The PECs, one for each propeller system, perform a number of safety functions including Autofeather and Automatic Underspeed Propeller Control (AUPC) and provide an UPTRIM command to the FADEC of the working engine. The propeller Pitch Control Unit (PCU) is a hydromechanical device that interfaces with the propeller. Commanded electrically by the PEC, the PCU meters high pressure engine oil to a two-stage servo valve mounted on the PCU. Rev 3.0 Apr 2010 Dash-8-400 Maintenance Manual 12/65 Rev 3.0 Apr 2010 Dash-8-400 Maintenance Manual 13/65 The PCU controls the flow of high pressure oil into the fine or coarse pitch chambers of the propeller pitch change cylinder as directed by the PEC so that the blades turn at the desired blade angle. In the event of electronic control malfunction, the PCU controls the minimum blade pitch that can be obtained in flight. The High Pressure PCU Pump and Propeller Overspeed Governor Unit, driven by the reduction gearbox, provide the PCU with high pressure oil from the engine oil system. Rev 3.0 Apr 2010 Dash-8-400 Maintenance Manual 14/65 Rev 3.0 Apr 2010 Dash-8-400 Maintenance Manual 15/65 The Propeller Overspeed Governor Unit is an independent mechanical system used to limit the propeller overspeed in the event of a malfunction. The O/S Governor is a flyweight design, driven directly from the driver gear of the pump. The Auxiliary Propeller Feathering Pump Unit provides an independent means of feathering the propeller in the event of a failure of the primary means of feather. Rev 3.0 Apr 2010 Dash-8-400 Maintenance Manual 16/65 Rev 3.0 Apr 2010 Dash-8-400 Maintenance Manual 17/65 The auxiliary pump consists of a 28Volt DC electrical motor driving an external gear pump which supplies a secondary source of pressurized oil for feathering the propeller. The feather pump is also used for feathering and unfeathering the propeller as required for maintenance purposes. The propeller system is fitted with a Magnetic Pickup Unit (MPU) to provide a signal to the PEC Unit. The PEC will use this signal for propeller speed governing as well as synchrophasing and to send to the ANVS for propeller balance monitoring. Rev 3.0 Apr 2010 Dash-8-400 Maintenance Manual 18/65 Rev 3.0 Apr 2010 Dash-8-400 Maintenance Manual 19/65 61-20-01 Propeller Control The propeller blade pitch or blade angle is controlled by modulating oil pressure on either side of the pitch change piston. Rev 3.0 Apr 2010 Dash-8-400 Maintenance Manual 20/65 The natural twisting moment applied to the blades is dominated in the in-flight pitch range by the centrifugal twisting moment. This arises because the center of mass of the blade does not coincide with the axis of pitch rotation. Each blade is fitted with a counterweight, phased around the blade root outer sleeve so that the blade’s natural twisting moment in flight is towards high pitch. In the event of loss of hydraulic pitch change pressure during flight, the propeller will therefore assume a safe, high pitch, which is associated with minimal windmilling drag. Rev 3.0 Apr 2010 Dash-8-400 Maintenance Manual 21/65 61-20-10 Propeller Modes The two main modes of control for propeller operation during flight and on the ground are the Constant Speed mode and the Beta Control mode. During in-flight "constant speeding" operation, the Propeller Electronic Control Unit directs the servo valve to meter high pressure oil into the propeller fine pitch chamber. Rev 3.0 Apr 2010 Dash-8-400 Maintenance Manual 22/65 Rev 3.0 Apr 2010 Dash-8-400 Maintenance Manual 23/65 This is to balance the coarse-seeking moment applied to the blades, so that the propeller stays at the selected speed (Np). If the Np is greater than the demanded speed, the servo valve will send the oil pressure to the coarse pitch chamber to reduce propeller speed. Should the propeller underspeed for reasons other than loss of oil supply or servo valve failure, the servo valve will direct more HP oil into fine pitch to restore propeller speed. Constant speeding mode is entered when the propeller speed reaches 850, 900 or 1020 rpm, according to which speed is selected by the Condition Lever. High pressure oil for constant speeding passes through the overspeed governor before it reaches the servo valve. Rev 3.0 Apr 2010 Dash-8-400 Maintenance Manual 24/65 Rev 3.0 Apr 2010 Dash-8-400 Maintenance Manual 25/65 Should the servo valve stick at a fine pitch selection, propeller rpm will increase until approximately 105 percent (1071 RPM), when the overspeed governor will start to isolate the propeller control system from high pressure oil circuit. Propeller RPM will then drop due to propeller counterweight action and the overspeed governor will reconnect the high pressure oil supply, which will achieve a stable governing condition at 105 percent. Safe overspeed governing is therefore provided, regardless of failures in the servo valve, PEC or electrical supply. When the propeller is in the Beta mode the blade angle is set by power lever input. During on-ground 'beta control', the PEC receives the PLA signals via the FADEC and directs the servo valve to meter oil into the fine or coarse pitch chamber to achieve the desired blade angle. Rev 3.0 Apr 2010 Dash-8-400 Maintenance Manual 26/65 Rev 3.0 Apr 2010 Dash-8-400 Maintenance Manual 27/65 Moving the Power Levers below Flight Idle causes the PROPELLER GROUND RANGE lights to turn on and causes the overspeed governor to be locked out by the ground beta enable valve. When in the beta range, propeller speed is generally governed by the FADEC and engine fuel at 660 rpm (NP underspeed governing). Rev 3.0 Apr 2010 Dash-8-400 Maintenance Manual 28/65 Rev 3.0 Apr 2010 Dash-8-400 Maintenance Manual 29/65 In the Reverse Speed Control mode the system operates in closed loop propeller RPM control, maintaining the propeller speed between 660 and 950 RPM. Rev 3.0 Apr 2010 Dash-8-400 Maintenance Manual 30/65 At low airspeeds it is possible for the propeller to reach the maximum reverse stop; in this case the propeller rotational speed is then controlled by the engine overspeed governor and can increase to 1020 RPM. This mode is similar to forward speed control, except that it operates in reverse, that is, driving more negative to absorb more power and reduce propeller RPM. Rev 3.0 Apr 2010 Dash-8-400 Maintenance Manual 31/65 61-20-11 Propeller Overspeed Governing The overspeed governor and hydraulic pump system incorporates a hydraulic section and an electronic section: The propeller overspeed governor is a hydromechanical unit mounted on the PCU hydraulic pump. In normal operation it routes pressure oil to operate a selector valve in the PCU. Rev 3.0 Apr 2010 Dash-8-400 Maintenance Manual 32/65 Rev 3.0 Apr 2010 Dash-8-400 Maintenance Manual 33/65 The governor monitors propeller speed (NP), and in the event of an overspeed bleeds pressure oil, which will increase the propeller blade angle and increase the load on the power turbine, which reduces the propeller speed (NP). The overspeed governor is set to limit propeller speed to 1071 RPM NP. If this speed is exceeded, governor flyweight force overcomes spring pressure, the flyweights move out, lifting the valve allowing oil to drain, and increasing propeller blade angle. Rev 3.0 Apr 2010 Dash-8-400 Maintenance Manual 34/65 Rev 3.0 Apr 2010 Dash-8-400 Maintenance Manual 35/65 When speed falls to a point where spring pressure exceeds flyweight force, the valve moves down, restoring the flow of pressure oil to the selector valve and the PCU to normal functioning. The electronic section uses FADEC NPt overspeed circuitry to signal the Fuel Metering Unit to reduce the amount of fuel being supplied to the engine when an overspeed of approximately 1173 RPM is reached. Rev 3.0 Apr 2010 Dash-8-400 Maintenance Manual 36/65 Rev 3.0 Apr 2010 Dash-8-400 Maintenance Manual 37/65 Reducing fuel to the engine causes power to drop, in turn lowering the propeller RPM. When NPt drops below the overspeed point, the governor allows the Fuel Metering Unit to restore normal fuel flow. In reverse mode, the hydraulic section of the overspeed governor is locked out and the FADEC electronic section is the primary means of overspeed protection. The overspeed governor can be tested at a lower value of approximately 80 percent Np. The overspeed governor switch is located on the pilot’s side panel. Rev 3.0 Apr 2010 Dash-8-400 Maintenance Manual 38/65 Rev 3.0 Apr 2010 Dash-8-400 Maintenance Manual 39/65 PEC Power Supply Rev 3.0 Apr 2010 Dash-8-400 Maintenance Manual 40/65 PEC Servo Valve Rev 3.0 Apr 2010 Dash-8-400 Maintenance Manual 41/65 Steady State in Flight Rev 3.0 Apr 2010 Dash-8-400 Maintenance Manual 42/65 Steady State on GND Rev 3.0 Apr 2010 Dash-8-400 Maintenance Manual 43/65 Normal Feather Rev 3.0 Apr 2010 Dash-8-400 Maintenance Manual 44/65 Electrical Feather Rev 3.0 Apr 2010 Dash-8-400 Maintenance Manual 45/65 Propeller Overspeed Rev 3.0 Apr 2010 Dash-8-400 Maintenance Manual 46/65 61-20-12 Automatic Underspeed Protection Circuit The Automatic Underspeed Protection circuit (AUPC) is independent of the control software and protects against failures which drive the propeller in the coarse direction. Rev 3.0 Apr 2010 Dash-8-400 Maintenance Manual 47/65 Rev 3.0 Apr 2010 Dash-8-400 Maintenance Manual 48/65 AUPC is armed with PLA at or above Flight idle, the CLA above START & feather, and torque above 50 percent, providing both Auto feather and Alternate Feather are inactive. It is triggered if NP drops below 816 rpm while torque remains above 50 percent for 1 second and indicated by the #1 or #2 PEC caution light. When AUPC triggers, an unmodulated drive fine signal is sent to the PCU servo valve causing the pitch change mechanism to be driven onto the hydraulic fine pitch stop in the PCU. Rev 3.0 Apr 2010 Dash-8-400 Maintenance Manual 49/65 At higher airspeeds, this will result in speed governing on the overspeed governor. During Auto Feather, the Auto Feather drive coarse input has higher priority than AUPC drive fine input; therefore the AUPC can not override the Auto Feather function. Rev 3.0 Apr 2010 Dash-8-400 Maintenance Manual 50/65 61-20-13 Propeller Synchrophasing System The propeller synchrophasing system provides automatic speed and phase angle synchronizing for the propeller system, which helps to reduce propeller noise. When in flight and the speeds of both propellers are within a predetermined range, the PEC enters a synchrophasing mode, ensuring that the relative position or phase difference between the slave propeller and master propeller is controlled to a demanded angle. Rev 3.0 Apr 2010 Dash-8-400 Maintenance Manual 51/65 Rev 3.0 Apr 2010 Dash-8-400 Maintenance Manual 52/65 This phase angle is calculated by timing the differences between the master and slave propeller Magnetic Pickup Unit signals over a complete propeller revolution. NOTE: The propeller synchrophasing system does not operate during take-off. Rev 3.0 Apr 2010 Dash-8-400 Maintenance Manual 53/65 61-20-14 Propeller Feathering System Propeller feathering systems provide auto feathering, alternate feathering, unfeathering and manual feathering. The auto feather system provides automatically initiated propeller feathering following an engine failure during take-off and power uptrim of the operating engine. Auto feather is selected ON for takeoff only, using the AUTOFEATHER switchlight on the engine instrument panel. This causes the SELECT light to turn on, and displays AUTOFEATHER SELECT on the engine display. Rev 3.0 Apr 2010 Dash-8-400 Maintenance Manual 54/65 Rev 3.0 Apr 2010 Dash-8-400 Maintenance Manual 55/65 The ARM light will turn on when both engine torques exceeds a minimum value of 50 percent and both power levers are advanced beyond 60 degrees PLA. Rev 3.0 Apr 2010 Dash-8-400 Maintenance Manual 56/65 The Uptrim is triggered (regardless of auto feather selection) when the torque of the failed engine falls below 25 percent, or when NP (as indicated by the torque sensor) falls below 80 percent, the PLA is in the rating detent, and Max. take-off power is not set. Rev 3.0 Apr 2010 Dash-8-400 Maintenance Manual 57/65 Rev 3.0 Apr 2010 Dash-8-400 Maintenance Manual 58/65 Whenever these conditions occur, a dual uptrim signal is sent to the FADEC of the working engine to increase its power by approximately 10 percent. The effect of this is to replace normal take-off power rating with maximum take-off power rating. If Uptrim occurs independent of auto feather, it may only be disarmed by moving both power levers below the rating detent position. Following a 3-seconds delay, the propeller of the failed engine will feather. When one propeller is auto feathered, the auto feather function of the other propeller is automatically disarmed. The auxiliary feathering pump is activated for approximately 30 seconds to make sure adequate oil pressure is available for propeller feathering. Rev 3.0 Apr 2010 Dash-8-400 Maintenance Manual 59/65 Rev 3.0 Apr 2010 Dash-8-400 Maintenance Manual 60/65 The respective feathering pump advisory light in the feather switchlight turns on when the auxiliary feathering pump electrical contractor is closed. The NP underspeed cancel signal prevents the FADEC from raising NH in an attempt to maintain propeller rpm as the feathered propeller speed decreases below 660 rpm. Rev 3.0 Apr 2010 Dash-8-400 Maintenance Manual 61/65 The auto feather system can be disarmed by pushing OFF the autofeather switchlight, retarding one or both power levers to flight idle or the remote propeller auto feathers. Rev 3.0 Apr 2010 Dash-8-400 Maintenance Manual 62/65 Propeller manual feathering is used during engine shutdown by selecting the appropriate condition lever to the START & FEATHER and/or FUEL OFF. In the event the propeller does not feather, Alternate Feather can be accomplished by operating the #1 or #2 Alternate Feather switchlight on the PROPELLER control panel. Rev 3.0 Apr 2010 Dash-8-400 Maintenance Manual 63/65 Rev 3.0 Apr 2010 Dash-8-400 Maintenance Manual 64/65 Provided that the Condition Lever is at START/FEATHER or FUEL OFF, the alternate Feathering Pump is energized with opposite secondary 28V DC bus power through a 30 second time delay. Pressure oil from the Feathering Pump operates a back-up feather valve in the PCU which ensures that the propeller can be feathered regardless of failures in the normal control system. Rev 3.0 Apr 2010 Dash-8-400 Maintenance Manual 65/65