Palm Beach County Fire Rescue Driver Operator Manual Chapter 6 PDF
Document Details
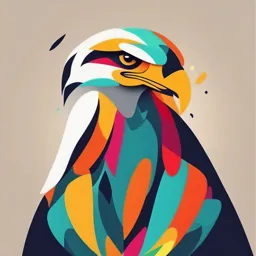
Uploaded by HealthfulCantor
Tags
Related
- Palm Beach County Fire Rescue Driver Operator Manual PDF
- Palm Beach County Fire Rescue Driver Operator Manual PDF
- Palm Beach County Fire Rescue Driver Operator Manual PDF
- Palm Beach County Fire Rescue Driver Operator Manual (2021) PDF
- Palm Beach County Fire Rescue Driver Operator Manual 2021 PDF
- Palm Beach County Fire Rescue Driver Operator Manual PDF
Summary
This document is a chapter from a driver operator manual for the Palm Beach County Fire Rescue. It details various tools and equipment used in fire rescue operations, including automatic fog nozzles, and provides information on their usage and specifications.
Full Transcript
Palm Beach County Fire Rescue Driver Operator Manual Chapter 6 Tools & Equipment 121 Introduction As the DO it is your responsibility to be familiar with each and every piece of equipment on the apparatus. Your Captain and crew are counting on you to ensure that the tools...
Palm Beach County Fire Rescue Driver Operator Manual Chapter 6 Tools & Equipment 121 Introduction As the DO it is your responsibility to be familiar with each and every piece of equipment on the apparatus. Your Captain and crew are counting on you to ensure that the tools and equipment are well maintained and in good working order. When the call comes in and they come to you for a vent saw, ram fan or any other piece of equipment, they expect it to be there, and they expect it to work. That is why each and every morning it is essential that you properly check out and run every piece of equipment on the apparatus. There is no substitute for getting your hands on the tools to really understand the ins and outs of its operation. In this chapter you will find basic information on the tools and equipment carried on PBCFR apparatus. This is a base level of information, and I encourage you to read the owner’s manual and manufacturer specifications to get an even better understanding. If you are unable to find the owner’s manual at the station, several of these have been uploaded to the file center on Target Solutions in the “Driver Operator” folder. If you are looking for an item that has not been uploaded, many resources can also be found online. From manufacturer websites to instructional videos, with perseverance you can almost always find what you are looking for. If you are still unable to locate the information that you need, the Central Shop is a wealth of knowledge and another resource available to you. Automatic Fog Nozzles Task Force Tips (TFT) automatic fog nozzles are found on all PBCFR fire suppression apparatus. Automatic nozzles are capable of variable flows while maintaining the same nozzle pressure. The nozzle pressure for the TFT nozzles is 100 psi and the flow rates are as follows: Size Flow (GPM) 1½” 70 - 200 2½” 95 - 300 Master Stream 150 - 1250 Both the nozzle pressure and the flow range are clearly marked on each nozzle, and the actual GPM flow depends on the pressure supplied to it. As with all 122 automatic nozzles, as the PDP increases, the nozzle opening automatically enlarges to produce the desired GPM while consistently maintaining the rated nozzle pressure. Note: When placed directly on a discharge, the 1½” TFT fog nozzle flows 100 GPM at 100 psi (NP). The TFT master stream fog nozzle flows approximately 400-450 GPM at 100 psi (NP) when placed directly on the deck gun. Years ago it was safe to assume that all fog nozzles operated at 100 psi nozzle pressure. But today, this is not always the case. Newer technology has evolved and the DO must know the operating pressure for each nozzle carried on the apparatus. PBCFR aerial apparatus are equipped with one of two nozzles. The Ferraras have an 80 psi automatic fog nozzle capable of flowing between 250 - 1250 GPM. The E-One aerial apparatus have a fog nozzle with an adjustable nozzle pressure. This nozzle pressure can be manually set between a range of 70 - 120 psi, but for consistency they are pre-set to 80 psi. The flow range for this nozzle is 300- 1500 GPM. The fire stream from an automatic nozzle can “look good”, but may not be supplying sufficient water for protection or extinguishment. The best way to confirm that you are achieving the proper GPM flow from these nozzles is with a flow meter, however, we do not have flow meters on our engines. With this in mind, it should be the goal of every DO to provide the proper PDP to the nozzle for every line placed in operation. In doing so, the DO can be assured that they are supplying the desired flow rate. Flow rates and hydraulic calculations are discussed in detail in Chapter 3 of this manual (“Fireground Hydraulics”). For ease of identification, PBCFR has color coded each 1¾” pre-connected hose line to match the discharge and the nozzle on many of its apparatus. 123 Elkhart Chief Combination Nozzle The term “combination nozzle” gets its name because these nozzles have the ability to produce either a fog stream or a solid bore fire stream. In either configuration, this is a low pressure nozzle designed to operate at 50 psi nozzle pressure. With the fog nozzle attached it supplies a constant flow of 150 GPM at 50 psi nozzle pressure. Unscrewing and removing the fog nozzle reveals a 15/16” solid bore tip which produces 185 GPM also at 50 psi nozzle pressure. This is known as a “constant flow” nozzle meaning the nozzle was designed to flow a specific amount of water at a specific nozzle pressure. Communication with the firefighter on the nozzle is essential. The DO must know which configuration the nozzle is operating in to properly calculate the friction loss and PDP. Piercing Nozzles PBCFR aerial apparatus are equipped with one of two types of piercing nozzles. The Akron Piercing Nozzle is designed to flow 125 GPM while operating at 100 psi nozzle pressure. The flow may be increased by raising the nozzle pressure, which should never exceed 200 psi. The Fyrestick Piercing Nozzle may be equipped with the standard spray head which delivers 100 GPM at 125 psi nozzle pressure. This is designed for use with a 1¾” hose line. The Fyrestick may also be equipped with a high volume spray head which is designed for use with a 2 ½” hose line. The high volume spray head is capable of flowing 200 GPM at 80 psi nozzle pressure. These nozzles are excellent tools to deliver water or foam solution to concealed or hard to reach places. Either can be used to penetrate an attic, sub-floor, walls, vehicle compartment, trailers and many other challenging access areas. They are capable of penetrating through cement block, brick, ¾” plywood, and corrugated steel. Selectable Gallonage Nozzles Selectable gallonage nozzles have been phased out as standard equipment on PBCFR apparatus. However, it is important to be familiar with these types of nozzles. These 124 nozzles allow the firefighter to select the desired GPM flow. They operate by rotating a dial until the desired flow lines up with the indication arrow. These nozzles are designed for either 1 ¾” and 2½” hand lines. The nozzle pressure for any selectable gallonage nozzle that may still be in circulation at PBCFR is 100 psi. When calculating your PDP communication with the firefighter is key to confirm the GPM setting. Solid Bore Nozzles PBCFR utilizes a number of solid bore nozzles. The hand line nozzles range from 15/16” to 1 ¼” tips, while the master stream tips range from 1 3/8” to 2”. Specific nozzle pressures and flow rates for these nozzles are discussed in detail in Chapter 3 of this manual (“Fireground Hydraulics”). Reciprocating Saws The 24 volt DeWalt ® reciprocating saw comes with a carrying case, battery charger, AC adaptor and various blades. This multi-function tool proves to be valuable for forcible entry and extrication, among other things. Blades are available in a variety of different lengths and types. Each blade can easily be identified by the number of teeth per inch. In general, wood cutting blades have less teeth per inch than those designed to cut metal. However, some blades are designed to cut both wood and metal. Depending on the application for use, the blade may be installed so the teeth are facing downward, which is the standard, or upward. Wood Blade Metal Blades 125 Before changing the blade, always ensure that the saw is in the locked position. If using the AC power adaptor, always unplug the tool prior to changing the blade. To change the blade, place the saw in the “lock” position and then simply lift the blade release lever. Remove the old blade, slide the new blade into place, and secure the blade release lever. The saw is now ready for use. When cutting metal, it is recommended that the saw be set to the low speed setting or “1”. When cutting wood or glass, the saw should be set to the high speed setting or “2”. ***Always remember to wear a mask when cutting glass!*** If needed, the depth of the blade can be adjusted. This is done by depressing the depth adjustment button and sliding the “foot” inward or outward. As a precaution, always ensure that the saw is in the locked position before adjusting the foot. The battery should be fully charged and connected to the saw so that it is ready for use. Should the battery fail or the battery power become exhausted, the AC adaptor can be used. To remove the battery, slide the battery release button upward and then slide the battery out of the saw. When inserting a replacement battery or the AC adaptor you will hear it click into position when inserted properly. Always keep the saw in the locked position when it is not in use. Some PBCFR apparatus are equipped with the 120V Milwaukee Orbital Sawzall. This reciprocating saw is useful for the same purposes as the DeWalt saw but there are a few important differences between the two. For starters, the Milwaukee saw operates solely on 120 Volt AC current and does not have a battery. Like the DeWalt saw, the blade can be installed with the teeth facing up or facing down depending on the application. To change the blade, twist the collar a quarter turn in the direction of the arrow and slide the blade into place. Always confirm that the saw is unplugged prior to changing the blade and give the blade a little pull to confirm that it is locked into place prior to plugging the saw back in. 126 If needed the depth of the blade can be adjusted. This is done by pulling the foot release lever out and sliding the “foot” inward or outward to the desired depth. Return the lever to lock the foot into position. As a precaution, always ensure that saw is unplugged prior to adjusting the blade depth. The Orbit Control Switch allows the tool to be operated with either a straight reciprocating action, or an orbital reciprocating action. Orbital action is recommended for fast, aggressive cutting and allows the blade to quickly remove material. The amount of orbital action may be adjusted by moving the control switch from left to right to any position between the two symbols. Be advised, orbital action is not recommended for cutting metal or for making precise cuts where the blade must be kept perpendicular to the material that you are cutting. In addition, orbital action will not operate if the blade is installed “upside-down (with the teeth facing upward). The Milwaukee sawzall is also equipped with a variable speed trigger control which can be operated at any speed from zero strokes per minute to full speed. The speed of the blade is based on the pressure applied to the trigger. Vent Saws There are several different brands and models of vent saws carried on PBCFR apparatus. Although these may vary slightly, the basic operating principles are the same. Refer to the owner’s manual for specific details on the particular saw carried on your unit. Every shift during the morning equipment check the fuel and bar chain oil reservoir levels should be checked. Prior to starting the saw, the fluid levels should be topped off as needed. 127 The procedures for starting the vent saw are as follows: It is recommended that the chain brake be engaged before starting the saw. Pushing the chain brake forward will engage it, which stops the rotation of the chain. Pulling the handle back disengages the brake and allows the chain to rotate. Next, if the saw is equipped with an “ON/OFF” switch place it in the “ON” position and then pull the choke button out. Some models may be equipped with a “Master Control Lever” for the choke, as pictured below. In this case, slide the lever down to the “Full Choke” position for cold starts. The “Half Choke” position is for warm starts. After the choke is engaged, press the “Decompression Valve” Stop button in (also known as the “Compression Release” button). Run This will allow for a smooth motion when attempting to start the Half Choke saw. The next step is to depress the safety and squeeze the Full Choke throttle at the same time. Pull the starter cord using short pulls until the engine turns over and the saw almost starts. Now return the choke to the normal operating position and push the decompression valve button in once again. While squeezing the safety and throttle, pull the starter cord again and the saw should start. Note: Each time the engine turns over you must press the “Decompression Valve” to release the compression inside the combustion chamber. If you do not depress this button, the starter cord will recoil with excessive tension, making it difficult to start, and potentially leading to injury. 128 To shut the saw off, press the “STOP” button or slide the master control lever up to the “STOP” position. Prior to use, it is important to check the tension of the chain. If the chain is too tight it may not rotate freely around the bar. If the chain is too loose it may come off the bar, potentially causing injury to the saw operator and/or damage to the saw itself. When the chain is properly adjusted it should hang with approximately ⅛” slack on the underside of the bar. ALWAYS shut the saw off prior to checking or making any adjustments to the chain tension! To adjust the tension of the chain, slightly loosen the two nuts that hold the bar in place. Next use a screwdriver to turn the tensioning screw. This will slowly move the bar inward or outward as needed. Once the proper tension is achieved, tighten the nuts so that the bar is held securely in place. Many of the vent saws carried on PBCFR apparatus are equipped with a multi-function tool which is stowed in the handle of the saw. The tool has a screwdriver at one end, and two different wrench sizes on the opposite end. The wrench sizes are designed for the following purposes: One side is used for adjusting the chain tension, while the other is used to change the spark plug. On some saws the size of the chain is marked directly on the bar. If the bar is not marked you can determine the correct chain size by measuring the distance from the center of the bar up against the casing to the tip of the bar. Round up to the nearest 2-inch measurement if needed. Sizes generally run 16, 18 and 20 inches. Some apparatus are equipped with a depth gauge on the vent saw. To adjust the cutting depth simply loosen the knob and slide it forward or backward along the slot in the bar. Once the desired depth is attained, tighten the knob to lock the gauge in place. Always confirm that the chain brake is locked and/or the saw is not running prior to adjusting the depth. 129 K-12 Saws Another type of saw carried on PBCFR apparatus is the K-12. Depending on the blade, this saw is capable of cutting a variety of materials including metal, concrete, and wood. It is useful for many applications including forcible entry and ventilation. This section will review general information regarding this type of saw. Remember that different models exist on our apparatus and each saw may vary slightly. It is important that you refer to the owner’s manual for specific details of each particular saw. Every shift during the morning equipment check the fuel level should be checked and topped off as needed prior to starting the saw. If you have a battery operated saw, ensure that the batteries are fully charged at the start of each shift. The procedures for starting the K-12 saw are as follows: If your saw is equipped with a “STOP” switch, slide it to the left so the “STOP” is not engaged. Pull the “CHOKE” button out and press the “Decompression Valve” button in, (also known as the “Compression Release” button). This will allow for a smooth motion when attempting to start the saw. The next step is to depress the safety and squeeze the throttle at the same time. Use short pulls to pull the starter cord until the engine turns over. Once the engine turns over, push the “CHOKE” button in and press the Decompression Valve button in again. It’s important to note that each time the engine turns over you must press the “Decompression Valve” in to release the compression inside the combustion chamber. If you do not depress this button, the starter cord will recoil with excessive tension, making it difficult to start, and potentially leading to injury. Pull the starter cord while depressing the safety and squeezing the throttle once again, and the saw should start. 130 To shut the saw off, slide the “STOP” lever to the right. Warning: Some newer saws run at high idle with the blade spinning when they first start up. You may need to engage the trigger to lower the RPMs to idle speed prior to use. Blade Types PBCFR carries a variety of blades for the K12 saw. It’s important to familiarize yourself with the specifics for each type of blade as well as what they are used for. The standard size blade for use with the K12 saw is either 12” or 14”. The blade measurement reflects the diameter of the blade, and does not represent the cutting depth. As a matter of fact, a 14” blade has a cutting depth of only 5”, and a 12” blade has a cutting depth of only 4”. 14” Diteq Blade The outer edge of this blade consists of vacuum bonded diamond segments. It is best suited for cutting a variety of material including: bulletproof glass, PVC, plastic, metal roofs, steel studs, railroad rails, rebar and other steel products. This blade is not a good for cutting wood. Although this blade may appear to be bi-directional, it does have a specific rotational direction. As pictured here, it is designed to rotate in the counter-clockwise direction. Use the multi-colored pattern on the blade as a guide to ensure that the blade is installed in the correct direction. 14” Dynablade Carbide Chip Blade The dynablade carbide chip blade is suited for cutting through multi-layered tar and gravel, wood shingles, corrugated aluminium, roofing materials, wood decking, light metal, tree roots, tires, plastic, and auto body parts. This blade should not be used to cut concrete or steel. Be aware that this is a very aggressive blade. Watch for flying particles and as with any saw, always wear eye protection and proper PPE. This blade is designed for intermittent cutting use. Avoid prolonged cutting without sufficient cooling of the blade. 12” Blazer Blade (Wood Blade) This 12” blade is primarily designed to cut wood, but it also useful on tar & gravel roofs, 131 light metal studding, shingle roofs, corrugated roofing, light sheet metal, railroad ties, plastic material. It is preferred over the Dynablade Carbide Chip blade for cutting typical plywood sheathed roofs. It cuts through the material much faster, and the depth of the cut from this 12” diameter blade will not cut completely through a 2” x 4” member if you accidentally cut too deep across the supporting members. Take note that this, and all wood blades, are directional. As pictured here, the blade should rotate counter clockwise. Tornado Blade The Tornado Blade is designed for cutting light and medim gauge steel, metal guard rails, auto bodies, aluminum, burglar bars, steel doors, iron pipes, reinforced and non reinforced concrete. The grooves in the blade are useful for removing tear out when cutting. Composite Blades Composite blades (aka discs) are designed for cutting metal and/or concrete. Refer to the label on the blade for specific use. Be aware that these blades wear down with use, decreasing the diameter and potential effectiveness over time. When cutting concrete, a small amount of water applied to the blade will help keep the dust to a minimum, protecting personnel and the victim. Blade Storage Do not store composite blades in the same compartment as fuel cans. Gasoline vapors can break down the makeup of the blade, causing it to fail during use. Regardless of the type of blade, always inspect it before and after each use. 132 Changing the Blade on a K-12 Saw Changing the blade on the K-12 saw is a fairly simple process. Needless to say, the first step is to ensure that the saw is OFF. Never attempt to change the blade with the saw running! To begin you will need a few hand tools: Adjustable wrench, medium size flat head screwdriver, vice grips, rag, and gloves. Changing the blade requires you to remove the bolt which is seated in the center of the blade and to remove the flange washer which is held in place by this center bolt. The center bolt works like any other traditional bolt – “Lefty Loosey - Righty Tighty”. So to remove it, you will need to turn it counter-clockwise. As you turn the center bolt the entire blade will spin with it. This is why you need the vice grips and rag, or a flat head screwdriver. Depending on the blade type, you will need these additional tools, or a gloved hand, to hold the blade in place when removing the center bolt and flange washer. Once the bolt is loose enough you can remove it, the flange washer and the blade all by hand. When putting a new blade on the saw, always confirm that the rotation direction of the blade corresponds with the rotation of the saw. Seat the blade in place on the saw, put the flange washer and center bolt in place, and tighten the bolt by hand. Hold the blade in place with one of the above mentioned methods and secure the bolt with a wrench. Do not overtighten the bolt when re-installing any K-12 saw blade. Once the blade is in place, always confirm that it is secure prior to firing up the saw. The fuel mixture for all PBCFR vent saws and K-12 saws are as follows: Use Non-ethanol Gasoline (Rec 90) Use 2-cycle engine oil Mix at a 50:1 ratio of fuel to oil Never fuel the saw in the same area that you will be cutting! Sparks from the saw may ignite any accidental fuel spillage, creating a potentially dangerous situation! 133 Battery Operated Cut Off Saw Some units, special operations in particular, are now equipped with a battery operated DeWalt FlexVolt 9” Cut Off saw. This saw runs off of a 60V battery pack and is designed specifically for cutting concrete or metal, depending on which blade you use. The blade size is 9”, so the cutting depth is limited to 3 ¼”. This saw can achieve up to 6500 RPMs and has a load manager light to indicate when the saw is working at maximum capacity. The blade guard can be adjusted as needed to give you full use of the saw blade depth if needed. One of the most unique features about this saw is that it has a quick connect fitting where you can attach a garden hose to the back of the saw. This allows water to flow down on both sides of the blade which helps control dust and keep the blade cool while cutting. The amount of water flow is controlled by the water regulator valve which is located just in front of the quick connect. The battery compartment is water tight, so you don’t have to worry about getting water inside that area as long as you properly latch the compartment after installing the battery. A wrench for changing the blade is stowed inside the battery compartment. Before changing the blade, always ensure that the trigger is in the locked position. As a secondary precaution, you may also remove the battery while changing the blade. The procedures for changing the blade are the same as the K-12 saw, however the Cut Off saw also has an additional feature, a blade lock button. Depress the blade lock button prior to unscrewing the center bolt. This will keep the blade from spinning as you loosen the bolt. 134 2-Stroke vs. 4-Stroke Small Engines I’m sure you’ve heard the terms 2-stroke engine and 4-stroke engine before, but what does that mean, and how can you tell the difference between the two? The technical difference between the two is how many revolutions it takes for the engine to complete a single cycle of combustion. But from a Driver Operator perspective, there are a few basic things that we need to know. First, there is an easy way to identify which is a 2-stroke engine vs. a 4-stroke engine. 2-stroke engines are commonly smaller than 4-stroke engines. The general rule of thumb is as follows: If you can carry it with 2 hands it is a 2-stroke engine, if it takes 4 hands to carry (2 people) it is a 4-stroke engine. Examples of 2-stroke engines include: Vent saw, and K-12 saw. Examples of 4-stroke engines include: RamFan, Generator, Hurst Generator. Another very important difference between the two is the fuel and oil that you use in each. 2-stroke engines require you to pre-mix the fuel and oil as discussed earlier in this chapter. The guidelines for 4-stroke small engines carried on PBCFR apparatus are as follows: Crankcase oil - SAE 30 Use Non-ethanol gasoline (Rec 90), and allow 1" of tank space for expansion. Any time you use the unit, run the fuel out of it by turning the fuel lever to the OFF position while the engine is running. The fuel lever shall be kept in the OFF position when the tool is not in use. Ventilation Fans The gasoline powered RamFan is useful for performing positive pressure ventilation and is equipped with a 4-stroke Honda engine. These fans are very powerful and are capable of moving approximately 13,000 cfm of air. The downside is that since they are gasoline powered they also emit exhaust fumes. To combat this, many units are equipped with a flexible exhaust tube that attaches to the side of the fan and can be used to divert the dangerous Carbon Monoxide (CO) exhaust gasses away from the doorway or opening. Be forewarned, the exhaust tube is made of metal and gets extremely HOT during use. It is essential that you wear fire gloves when handling it after the fan has been running. Failure to do so will result in burns. Starting Procedure: Oil and fuel levels should be checked during the daily morning equipment check. 135 Turn the “ON/OFF” switch to the “ON” position. Next, slide the fuel lever to the “ON” position and slide the choke lever to the “CHOKE” position. This should put the two levers in opposite positions as shown in the photo to the right. Pull the starting rope until the engine turns over. Return the choke lever to the right or “OFF” position. Pull the starting rope again and the engine should start. Keep the choke in the “OFF” position while the engine is running. The throttle is located above the starting rope and is adjusted by moving it left or right. When you turn the fan off, move the fuel lever to the “OFF” position and run the fuel out of the line. The fuel lever should then be kept in the “OFF” position when the fan is stowed on the apparatus. The gas powered Ramfan has a pair of silver adjustment tabs that can be used to tilt the unit up or down. If the adjustment is inoperable a piece of cribbing works well as a prop to tilt the unit upward. Position and tilt the fan so the maximum amount of air flows through the center of the opening. Although this is not a seal in the true sense, there should be no indication of backflow or leakage around the edges of the opening. The air should be flowing inward at all areas of the opening as shown above. 136 Electric Ventilation Fan Many PBCFR engines are also equipped with the Super Vac electric powered ventilation fan. These fans are also capable of flowing up to 13,000 cfm, depending on the model. They can be used both indoors and outdoors as there are no gaseous fumes produced. To operate the fan simply plug it in, move the On/Off Switch to the “ON” position, and rotate the dial clockwise to increase the air flow. Hydraulic Rescue Tools There are a variety of hydraulic rescue tools that are used throughout PBCFR. While some features on the power units may differ from tool to tool, the basic premise and operation is fairly standard for them all. The best way to become familiar with any tool carried on the apparatus is to get your hands on it and put it to use. Whether this is done during the daily morning truck check out or during a training session, it is up to you as the DO to know the equipment. All PBCFR hydraulic tool power units are 4-stroke engines that use regular unleaded gasoline. 137 Starting procedures will vary depending on the unit that you have on your apparatus. The fuel, oil, and hydraulic fluid levels should be checked during the morning equipment check, prior to starting the unit. Starting Procedure: Always ensure that the lines are de-pressurized by placing the control lever(s) in the “DUMP” or “NEUTRAL” position prior to starting the power unit. If the unit is equipped with an “ON/OFF” switch, turn it to the “ON” position. Slide the fuel lever to the “ON” position. Place the choke lever in the “CHOKE” position. Pull the starting rope until the engine turns over. Once the engine turns over, move the choke to the “OFF” position and pull the starting rope again. The engine should start. Keep the choke in the “OFF” position while the engine is running. On some units the choke is built into the throttle lever as pictured to the right. To place these units in the “CHOKE” position, pull the lever out and up as shown here. Be aware that this lever is spring loaded. To move it to the “RUN” position, lower the lever while keeping it extended out. If you release the lever in the center position between “CHOKE” and “RUN”, it will retract to the “STOP” position and the engine will shut off. The engine speed is controlled by the throttle. On some units the throttle is marked with a “turtle” and a “rabbit” symbol to indicate standard and high speed respectively. When the tools are in operation the throttle should be placed in the high speed position. When turning the power unit off, move the fuel lever to the “OFF” position while the engine is running. The engine will continue to run for a brief period until all the fuel in the line has been used up. The fuel lever should be kept in the “OFF” position when the unit is stowed on the apparatus and any time it is not in use. The hydraulic fluid level is checked by un-screwing the cap located on the reservoir and inspecting the dipstick. Some units have a sight glass instead of a dipstick so you can view the fluid level at a glance. On power units equipped with a sight glass, the fluid level should be filled about halfway up the sight glass. On units without a dipstick or a sight glass the hydraulic fluid should be maintained approximately one inch from the top of the tank. 138 When operating several pieces of rescue equipment with one power unit, or working on an extended extrication, it may be necessary to refill the hydraulic fluid. Also, if you find that the tools are not opening or closing to their full potential, it may be that the hydraulic fluid is low. Always keep a spare bottle of hydraulic fluid on the apparatus for these circumstances. ** Only use approved hydraulic fluid as specified for each individual unit. If you are unsure of which fluid to use, contact the Central Shop for assistance. ** HURST units are capable of performing at an angle of up to 20°. However, in order to guarantee maximum safety and performance, they should be operated on level ground whenever possible. Some power unit models are not designed to idle for extended periods of time without having the hydraulic tools connected to them. For this reason, when doing your morning truck check, or at any time, do not run the power unit for more than 15 minutes without having the tools attached to it. Although they are being phased out, some apparatus may still have the hoses and hydraulic tools with the twin line connections that have both male and female “quick-coupler” couplings. Although these couplings are not as easy to use as the “mono-couplings”, they do allow you to set the tools up “in series” if necessary as shown below. Most of the hydraulic tools, hoses, and power units on PBCFR apparatus are now equipped with the “mono-couplings”. These couplings make for fast, easy connections when assembling the hydraulic tools for use. To make the connection, simply turn the female side of the union clockwise until it locks into place. Although these hoses can be coupled while under pressure, the factory recommendation is that you dump the pressure, or depressurize the tool, prior to connecting or disconnecting the hose couplings. Each mono-coupling should have a dust cap attached to it. When not in use, 139 place the dust caps on the couplings to avoid any dust or debris from getting into the fittings. As stated above, there are several different styles of hydraulic tool power units carried on PBCFR apparatus. Some power units will only allow one tool at a time to be operated while others have a “simo” mode or simultaneous mode which allows you to operate more than one tool at a time, independent of each other. In “simo” mode you will not lose pressure from one tool to the other. Another model of power unit carried by PBCFR has a “turbo” mode, which steals power from one tool to ramp up the power on another. To complicate things further, some apparatus are outfitted with 5000 psi tools and power units, while others have 10,000 psi sets. Be advised, you CANNOT mix and match these tools. They use different types of hydraulic fluid. On top of all this, some apparatus now carry Genesis tools and power units while others are outfitted with Hurst equipment. Regardless of the make, model, or style of power unit, always place it in “Dump” or “Neutral” and depressurize the equipment prior to turning the power unit off. With so many different models, there is no substitute for getting your hands on the equipment and knowing how to operate it. It is up to you as the DO to take the initiative to be familiar with whatever equipment is carried on your apparatus. More information and resource materials can be found on the internet and some materials are available on Target Solutions in the File Center in the Driver Operator folder. Some apparatus carry a variety of interchangeable tips for the spreaders and rams. These accessories can easily be changed out by removing the retaining pin on the tip of the tool. 140 SCBA Cylinders Each air pack on the apparatus must be checked daily, as do the spare SCBA cylinders. Part of this daily check includes visually inspecting the bottle for damage, proper pressure, and hydrostatic test date. Additionally, the cylinders should be capped and stored face down to avoid contamination. PBCFR utilizes composite SCBA cylinders, meaning they are aluminum cylinders wrapped in layers of resin and fiberglass. SCBA cylinders shall be changed out when they are less than 90% full (for 4500 psi cylinders this is 4050 psi). All composite SCBA cylinders must be hydrostatically tested every 5 years, and the Hydrostatic maximum service life is 15 years from the date of Test Date manufacture. After 15 years of use, the cylinder is permanently removed from service. Per PBCFR policy, any air cylinder with a hydrostatic test date that shall expire within 3 months, or is within 3 months of its 15 year service life, shall be Manufactured Date tagged and sent to the SCBA Shop. SCBA’s currently carried on PBCFR apparatus are equipped with a Heads Up Display (HUD) and PASS device. These air packs require 6 AA batteries for operation. Operational personnel are authorized to replace the batteries on the SCBA if needed. Replacement batteries must be Duracell or Energizer, which are available through the county warehouse. WARNING: Batteries must only be changed in an area known to be nonflammable. Changing the batteries in a flammable atmosphere may cause an ignition which could result in serious injury or death. Before changing the batteries, always be sure that the cylinder valve is off and the PASS device is completely inactive. Never remove or replace the batteries with the system pressurized or damage may occur to the electronic components. 141 Always replace all six batteries at the same time. The battery holder is marked on the inside with the orientation of the batteries. Use a large Phillips or flat head screwdriver to loosen the screw and remove the cover. Remove the old batteries and replace all 6 batteries with new ones, ensuring that the orientation of each battery is correct. The battery cover must be installed so that it is water tight. Before replacing the cover, check the cover gasket for tears or cuts and ensure that it is clean and free from debris. If damage is found, remove the air pack from service, tag it, and contact the SCBA Shop for repair. All equipment requiring repair shall be cleaned and decontaminated by operations personnel prior to being sent to the SCBA Shop for repair. After replacing the batteries, ALWAYS perform a regular operational inspection and air pack check before placing the pack back in service. ***Refer to policy #FR-O-301 Vehicle Equipment Inspection and Check Out for more information. You can also find the Scott Operating and Maintenance Manual on the PBCFR Intranet or call the SCBA Shop if needed at (561) 616-6967.*** Portable Extinguishers There are three types of extinguishers carried onboard PBCFR apparatus. They are Carbon Dioxide (CO2), ABC Dry Chemical, and Portable Water Can (PWC) extinguishers. These extinguishers must be inspected annually and should have a valid inspection tag that is dated. The gauges should be within the green range on the water can and dry chemical extinguishers. CO2 extinguishers that do not possess an inspection tag shall be weighed in accordance to the label affixed on the extinguisher to determine if it is usable. CO2 extinguishers shall be hydrostatically tested every 5 years. Dry Chemical Extinguishers shall be hydrostatically tested every 12 years. 142 Water can extinguishers shall be hydrostatically tested every 5 years. Adding one ounce of foam to the water can gives it the properties of a wetting agent and helps reduce the surface tension of the water. The Portable Water Can Extinguisher (PWC) should be refilled and pressurized by the DO after each use. Specific instructions on how to refill and batch mix foam in the PWC to create a wetting agent are found in chapter 5 of this manual (Foam Operations). Generators The 3500 watt generator is an alternative means of providing 120 volt AC power to the scene. Like the Ramfan, this unit is equipped with a 4-stroke Honda engine that uses regular unleaded gasoline. Starting Procedure: Oil and fuel levels should be checked during the morning equipment check. Turn the “ON/OFF” switch to the “ON” position. Next, slide the fuel lever to the “ON” position and slide the choke lever to the “CHOKE” position. This should put the two levers in opposite positions as shown in the photo below. Pull the starting rope until the engine turns over. Return the choke lever to the “OFF” position. Pull the starting rope again and the engine should start. Keep the choke in the “OFF” position while the engine is running. There is no throttle to adjust on the generator. The engine speed is fixed on these units. When turning the generator off, unplug all appliances first. Then move the fuel lever to the “OFF” position while the engine is running. The engine will continue to run for a brief period until all of the fuel in the line has been used up. The fuel lever should be kept in the “OFF” position when the unit is stowed on the apparatus and any time it is not in use. Although models vary, the generator is capable of supplying power to twist-lock and 143 standard duplex receptacles. The receptacle panel is located on the front of the generator and is equipped with a main breaker. The main breaker should be kept in the “OFF” position until the generator is ready for use. After the generator is started, it will run at idle speed until something is plugged into it and the breaker is moved to the “ON” position. This will cause the RPMs to increase to the normal operating speed. The generator is equipped with a “Volt Selector” toggle switch. This switch should always be kept in the “120V ONLY” position. Extension cords and adaptors used by PBCFR are rated for 120 volts and will only fit into the outlets marked as such. Any time that anything is plugged into the generator the Ground Fault Circuit Interrupter (GFCI) must be connected in-line with the device. This will provide protection from electric shock for personnel and the equipment. GFCI Honda “Suitcase” Style Generator Some PBCFR apparatus are equipped with the Honda 2200 watt “suitcase” style generator. These units are capable of providing 120 volt AC power to the scene in a more compact package. Like the 3500 watt generator, these units are equipped with a 4-stroke Honda engine that uses regular unleaded gasoline. Although they provide less power than the 3500, they are much lighter, easy to maneuver, and are designed to be carried by one person. There are a few different models outfitted on our apparatus, but the starting procedure is the same for them all. Oil and fuel levels should be checked during the morning equipment check. On these generators, you must remove the maintenance cover to access the oil dipstick as shown in the diagram below. 144 Starting Procedure: Always ensure that all adaptors and devices are unplugged from the generator and that the Eco Throttle is in the “OFF” position prior to starting the unit. Begin by rotating the fuel filler vent cap to the “ON” position. Move the choke lever to the “CHOKE” position and turn the Engine Switch to the “ON” position. Pull the starter cord until the engine turns over. Return the choke lever to the “OFF” position. Pull the starter cord again and the engine should start. Keep the choke in the “OFF” position while the engine is running. Depending on the model, the generator will be equipped with either a built in GFCI or a Circuit Protector. Both are designed to trip and stop the power going to the receptacles if there is a short circuit or a significant overload of the generator. Confirm that this is reset and in the normal operating position prior to plugging any equipment into the generator. Because of this built in feature, it is not necessary to connect the in-line GFCI adaptor when using these generators. 145 During normal operation the green Output Indicator light will be illuminated, indicating that the receptacles have power going to them. If the red Overload Alarm lights up or the circuit protector trips, the device you are running may require more power than the generator can provide. Another cause of this may be a short circuit, or an internal fault. The power to the receptacles will be stopped until the problem has been rectified. If the device you are running requires more power, you may need to use a 3500 watt generator instead. The Oil Alert indicator is designed to prevent engine damage caused by an insufficient amount of oil in the crankcase. A red light will illuminate before the oil level falls below a safe limit. If this occurs, the oil alert system will automatically stop the engine. If this happens, or if you see the red Oil Alert indicator light illuminate during use, check the engine oil level immediately. Eco Throttle: The Honda 2200 series generators are also equipped with an ECO Throttle switch. When placed in the “ON” position this automatically raises or lowers the engine speed based on the electrical load for lower noise and improved fuel consumption. The ECO Throttle switch should be in the “OFF” position when starting the engine. Once the engine is running, plug in the appliance and then move the ECO Throttle switch to the “ON” position. If the appliance is not running with enough power move the ECO Throttle switch back to the “OFF” position. When turning the generator off, unplug all appliances and devices first. If your generator is equipped with a “FUEL OFF” position on the Engine Switch, move the switch to this positon. The engine will continue to run for a brief period until all the fuel in the line has been used up. When the engine has stopped running, move the Engine Switch to the “OFF” position. If the Engine Switch does not have a “FUEL OFF” position, simply move it to the “OFF” position to stop the engine. When the engine has cooled, turn the fuel filler vent cover to the “OFF” position. Do not lay the generator on its side when moving, storing, or operating it as this may 146 cause oil to leak and damage the generator engine. Heed all warnings posted on the generator at all times. For more information, refer to the owner’s manual on Target Solutions in the File Center in the Driver Operator folder. When operating any small engine, use caution refilling the fuel when the engine is hot. The exhaust area can get extremely hot and any accidental fuel spillage may ignite. This may cause a potentially dangerous situation and/or damage to the equipment. **Never refill any small engine with fuel while it is running.** Deck Gun/Ground Monitor The Deck Gun/Ground Monitor is a master stream device that is capable of flowing high flow GPM rates. When mounted on the apparatus it is called a Deck Gun. When used in conjunction with the base and placed on the ground, it is referred to as a Ground Monitor. The maximum recommended flow for either configuration is 1250 GPM. At this flow rate the nozzle reaction can be as high as 630 pounds! Use caution at all times during operation. Whether it is mounted on the truck or mounted on the ground, you can use either a fog or solid bore nozzle. 147