Drilling Chapter 5 (Drilling) PPT PDF
Document Details
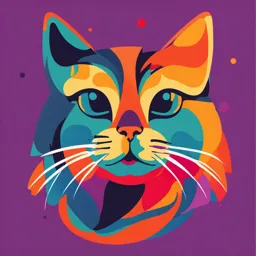
Uploaded by AwestruckArtNouveau
Joseph EL-GHOLAM
Tags
Summary
This document is a presentation on "Drilling" that describes and explains various machine types used in metal machining, such as portable, sensitive, upright, radial, gang, multiple spindle, automatic, and deep hole drilling machines. Each machine type is thoroughly explained with its capabilities and operational features.
Full Transcript
Drilling 19-Oct-20 Theory of Metal Machining/Prepared by Joseph EL-GHOLAM 1 Drilling Drilling, is a machining operation used to create a round hole in a workpart Drilling is usually performed with a rotating cylindrical tool that has two cu...
Drilling 19-Oct-20 Theory of Metal Machining/Prepared by Joseph EL-GHOLAM 1 Drilling Drilling, is a machining operation used to create a round hole in a workpart Drilling is usually performed with a rotating cylindrical tool that has two cutting edges on its working end called a drill or drill bit The rotating drill feeds into the stationary workpart to form a hole whose diameter is equal to the drill diameter Drilling is customarily performed on a drill press, although other machine tools also perform this operation 19-Oct-20 Theory of Metal Machining/Prepared by Joseph EL-GHOLAM 2 Drilling Machines Drilling machine is one of the most important and versatile machine tools in a workshop Drilling machines are classified based on their constructional features, or the type of work they can handle Portable drilling machine Sensitive drilling machine Upright drilling machine Radial drilling machine Gang drilling machine Multiple spindle drilling machine Automatic drilling machine Deep hole drilling machine 19-Oct-20 Theory of Metal Machining/Prepared by Joseph EL-GHOLAM 3 Portable Drilling Machine A portable drilling machine is a small compact unit and used for drilling holes in workpieces in any position, which cannot be drilled in a standard drilling machine These drilling machines operate at fairly high speeds and accommodate drills up to 12 mm in diameter A magnetic drilling machine is a portable drilling machine with a magnetic base (either electromagnetic or permanent magnet) They operate with different speeds and can drill a hole up to 35 mm 19-Oct-20 Theory of Metal Machining/Prepared by Joseph EL-GHOLAM 4 Sensitive Drilling Machine It is a small machine used for drilling small holes in light job In this drilling machine the workpiece is mounted on the table and drill is fed into the work by purely hand control High rotating speed of the drill and hand feed are the major features of sensitive drilling machine A sensitive drilling machine consists of a horizontal table, a vertical column, a head supporting the motor and driving mechanism, and a vertical spindle Drills of diameter from 1.5 to 15.5 mm can be rotated in the spindle of sensitive drilling machine 19-Oct-20 Theory of Metal Machining/Prepared by Joseph EL-GHOLAM 5 Upright Drilling Machine The upright drilling machine is larger and heavier than a sensitive drilling machine It is designed for handling medium sized workpieces and is supplied with power feed arrangement In this machine a large number of spindle speeds and feeds may be available for drilling different types of work Upright drilling machines are available in various sizes and with various drilling capacities (ranging up to 75 mm diameter drills) The table of the machine also has different types of adjustments 19-Oct-20 Theory of Metal Machining/Prepared by Joseph EL-GHOLAM 6 Upright Drilling Machine 19-Oct-20 Theory of Metal Machining/Prepared by Joseph EL-GHOLAM 7 Radial Drilling Machine The radial drilling machine consists of a heavy, round vertical column supporting a horizontal arm that carries the drill head Arm can be raised or lowered on the column and can also be swung around to any position over the work and can be locked in any position The drill head containing mechanism for rotating and feeding the drill is mounted on a radial arm and can be moved horizontally on the guide-ways and clamped at any desired position 19-Oct-20 Theory of Metal Machining/Prepared by Joseph EL-GHOLAM 8 Radial Drilling Machine The maximum size of hole that the machine can drill is not more than 50 mm Powerful drive motors are geared directly into the head of the machine and a wide range of power feeds are available as well as sensitive and geared manual feeds The radial drilling machine is used primarily for drilling medium to large and heavy workpieces 19-Oct-20 Theory of Metal Machining/Prepared by Joseph EL-GHOLAM 9 Plain Radial Drilling Machine Vertical movement of the arm on the column Horizontal movement of the drill head along the arm Circular movement of the arm in horizontal plane about the vertical column. 19-Oct-20 Theory of Metal Machining/Prepared by Joseph EL-GHOLAM 10 Semi Universal Radial Drilling Machine Vertical movement of the arm on the column Horizontal movement of the drill head along the arm Circular movement of the arm in horizontal plane about the vertical column Drill head can be swung about a horizontal axis perpendicular to the arm 19-Oct-20 Theory of Metal Machining/Prepared by Joseph EL-GHOLAM 11 Universal Radial Drilling Machine Vertical movement of the arm on the column Horizontal movement of the drill head along the arm Circular movement of the arm in horizontal plane about the vertical column Drill head can be swung about a horizontal axis perpendicular to the arm Additional rotatory movement of the arm holding the drill head on a horizontal axis is also provided for enabling it to drill on a job at any angle 19-Oct-20 Theory of Metal Machining/Prepared by Joseph EL-GHOLAM 12 Gang Drilling Machine In gang drilling machine, a number of single spindle drilling machine columns are placed side by side on a common base and have a common worktable A series of operation may be performed on the job by shifting the work from one position to the other on the worktable This type of machine is mainly used for production work 19-Oct-20 Theory of Metal Machining/Prepared by Joseph EL-GHOLAM 13 Gang Drilling Machine 19-Oct-20 Theory of Metal Machining/Prepared by Joseph EL-GHOLAM 14 Multiple-Spindle Drilling Machine The multiple-spindle drilling machine is used to drill a number of holes in a job simultaneously and to reproduce the same pattern of holes in a number of identical pieces in a mass production work This machine has several spindles and all the spindles holding drills are fed into the work simultaneously Feeding motion is usually obtained by raising the worktable 19-Oct-20 Theory of Metal Machining/Prepared by Joseph EL-GHOLAM 15 Multiple-Spindle Drilling Machine The multiple-spindle drilling machine is used to drill a number of holes in a job simultaneously and to reproduce the same pattern of holes in a number of identical pieces in a mass production work This machine has several spindles and all the spindles holding drills are fed into the work simultaneously Feeding motion is usually obtained by raising the worktable 19-Oct-20 Theory of Metal Machining/Prepared by Joseph EL-GHOLAM 16 Deep Hole Drilling Machine A deep hole drilling machine is a metal-cutting machine tool, designed to produce very deep, precision holes into virtually any metal using specific tools such as BTA and gundrills Deep hole drilling machines are ideal for a variety of sizes of deep holes, and are necessary for holes that are approximately 20:1 depth- to-diameter or greater in ratio 19-Oct-20 Theory of Metal Machining/Prepared by Joseph EL-GHOLAM 17 BTA Deep Hole Drilling Machine BTA drilling is a deep hole drilling process that uses a specialized drilling tool on a long drill tube to produce deep holes in metal, from holes with a diameter from 20 mm up to 250 mm, up to depth-to-diameter ratios of 400:1 BTA drilling is the most effective method of drilling deep holes, as it is a cleaner, more reliable and capable process than conventional twist drills, and can achieve larger diameters and higher feed rates than the alternative gundrilling 19-Oct-20 Theory of Metal Machining/Prepared by Joseph EL-GHOLAM 18 Gundrilling Deep Hole Drilling Machine Gundrilling machines are capable of precision holes from 1 – 50 mm in diameter and can maintain accuracy in extreme depth-to- diameter ratios Gundrilling uses internal coolant, and chips exit through a groove in the tool for a clean and accurate drilling process 19-Oct-20 Theory of Metal Machining/Prepared by Joseph EL-GHOLAM 19 Deep Hole Drilling Machine 19-Oct-20 Theory of Metal Machining/Prepared by Joseph EL-GHOLAM 20 Deep Hole Drilling Machine 19-Oct-20 Theory of Metal Machining/Prepared by Joseph EL-GHOLAM 21 Construction of Drilling Machine The head containing electric motor which transmits the rotation to the spindle with the drill fixed in the chuck via V-pulleys and V- belt A pinion engages a rack fixed onto the sleeve to provide vertical up and down motion of the spindle and hence the drill so that the same can be fed into the workpiece or withdrawn from it while drilling Spindle speed or the drill speed is changed with the help of V-belt and V-step-pulleys Larger drilling machines are having gear boxes for the said purpose 19-Oct-20 Theory of Metal Machining/Prepared by Joseph EL-GHOLAM 22 Construction of Drilling Machine Adjustable work piece table is supported on the column of the drilling machine and can be moved both vertically and horizontally Tables are generally having T-slots so that the vise or the workpiece can be securely held on it Base table is a heavy casting and it supports the drill press structure Column is a vertical round or box section which rests on the base and supports the head and the table The round column may have rack teeth cut on it so that the table can be raised or lowered depending upon the workpiece requirements 19-Oct-20 Theory of Metal Machining/Prepared by Joseph EL-GHOLAM 23 Specifications of a Drilling Machine A heavy-duty drilling machine is specified by following parameters: Drilling capacity Taper in spindle (Morse No.) Distance between spindle and column (maximum and minimum), in case of radial drilling machine Transverse of spindle Minimum distance between spindle and table Minimum distance between spindle and base plate Working surface of table (i.e., diameter) Range of spindle speeds Range of power feed per revolution Motor speed Motor power 19-Oct-20 Theory of Metal Machining/Prepared by Joseph EL-GHOLAM 24 Specifications of a Drilling Machine 19-Oct-20 Theory of Metal Machining/Prepared by Joseph EL-GHOLAM 25 Accessories and Attachments of Drilling Machine Tool-holding devices used to hold or drive cutting tool like the chuck, drill sleeve, drill socket, drill drift, and boring heads. Work-holding devices used to clamp or hold work piece, like the vise, blocks, plates, jigs, and clamps 19-Oct-20 Theory of Metal Machining/Prepared by Joseph EL-GHOLAM 26 Drill Chucks Most common devices used for holding straight-shank cutting tools Key chuck type Keyless chuck type Most contain three jaws that move simultaneously when outer sleeve turned, and they hold straight shank of cutting tool securely 19-Oct-20 Theory of Metal Machining/Prepared by Joseph EL-GHOLAM 27 Drill Sleeves Used to adapt drill shank to machine spindle if taper on tool is smaller than taper in spindle 19-Oct-20 Theory of Metal Machining/Prepared by Joseph EL-GHOLAM 28 Drill Socket Used when hole in spindle of drill press too small for taper shank of drill Used often as extension sockets. 19-Oct-20 Theory of Metal Machining/Prepared by Joseph EL-GHOLAM 29 Drill Drift Used to remove tapered-shank drills or accessories from drill press spindle, always place rounded edge up so this edge will bear against round slot in spindle Use hammer to tap drill drift and loosen tapered drill shank Use board or piece of pressed- wood to protect table or vise 19-Oct-20 Theory of Metal Machining/Prepared by Joseph EL-GHOLAM 30 Boring Head Their use is not limited to drilling machines; they are used on boring machines, milling machines, punching machines This device allows the enlarging of a hole that has already been drilled (or cast) by means of a single-point tool or several such tools according to the type of the boring head With the boring head counter boring, counter sinking, spot facing, and internal grooving can be executed 19-Oct-20 Theory of Metal Machining/Prepared by Joseph EL-GHOLAM 31 Drill Vise Vise is one of the important devices used for holding workpieces on a drilling machine table The work is clamped in a vise between a fixed jaw and a movable jaw Parallel blocks are placed below the work so that the drill may completely pass through the work without damaging the table Different types of vises are used for holding different types of work and for performing different operations. 19-Oct-20 Theory of Metal Machining/Prepared by Joseph EL-GHOLAM 32 Plain Vise 19-Oct-20 Theory of Metal Machining/Prepared by Joseph EL-GHOLAM 33 Swivel Vise 19-Oct-20 Theory of Metal Machining/Prepared by Joseph EL-GHOLAM 34 Tilting Vise 19-Oct-20 Theory of Metal Machining/Prepared by Joseph EL-GHOLAM 35 Universal Vise 19-Oct-20 Theory of Metal Machining/Prepared by Joseph EL-GHOLAM 36 Universal Vise 19-Oct-20 Theory of Metal Machining/Prepared by Joseph EL-GHOLAM 37 Cross Slide Vise 19-Oct-20 Theory of Metal Machining/Prepared by Joseph EL-GHOLAM 38 Cross Slide Vise 19-Oct-20 Theory of Metal Machining/Prepared by Joseph EL-GHOLAM 39 T-Bolts and Clamps The workpieces can be held directly on the machine table by means of ‘T’ – bolts and clamps The top of the machine table has ‘T’ – slots into which ‘T’ – bolts may be fitted The clamps are made of mild steel ‘T’ – bolts pass through a central hole on the clamp The clamp is made to rest horizontally on the work surface by placing a suitable step block at the other end of the work 19-Oct-20 Theory of Metal Machining/Prepared by Joseph EL-GHOLAM 40 T-Bolts and Clamps 19-Oct-20 Theory of Metal Machining/Prepared by Joseph EL-GHOLAM 41 T-Bolts and Clamps 19-Oct-20 Theory of Metal Machining/Prepared by Joseph EL-GHOLAM 42 T-Bolts and Clamps 19-Oct-20 Theory of Metal Machining/Prepared by Joseph EL-GHOLAM 43 T-Bolts and Clamps 19-Oct-20 Theory of Metal Machining/Prepared by Joseph EL-GHOLAM 44 T-Bolts and Clamps Step blocks: The step blocks are used in combination with ‘T’ – bolts and clamps for holding the work directly on the table The step block supports the other end of the clamp Workpieces of different heights are held by leveling the clamp on different steps of the step block 19-Oct-20 Theory of Metal Machining/Prepared by Joseph EL-GHOLAM 45 Step Blocks 19-Oct-20 Theory of Metal Machining/Prepared by Joseph EL-GHOLAM 46 Step Blocks 19-Oct-20 Theory of Metal Machining/Prepared by Joseph EL-GHOLAM 47 V-Block V–blocks are used for holding cylindrical workpieces The work may be supported on two or three V’-blocks according to the length of the work The work is held on the ‘V’ groove and is clamped by straps and bolts They are made of cast iron or steel and are accurately machined 19-Oct-20 Theory of Metal Machining/Prepared by Joseph EL-GHOLAM 48 V-Block 19-Oct-20 Theory of Metal Machining/Prepared by Joseph EL-GHOLAM 49 Angle Plate Angle plates have two faces at right angle to each other and are made of cast iron It resembles the English alphabet ‘L’ All the sides of a angle plate are machined accurately Slots and holes are provided on both the faces of the angle plate Work is clamped on one of its faces by means of bolts and nuts 19-Oct-20 Theory of Metal Machining/Prepared by Joseph EL-GHOLAM 50 Angle Plate 19-Oct-20 Theory of Metal Machining/Prepared by Joseph EL-GHOLAM 51 Drill Jigs Drill jigs are used in mass production process A jig is specially designed to hold the work securely and to guide the tool to any desired position Holes may be drilled at the same relative positions on each of the identical workpieces The work is clamped and removed easily The cost of making a drill jig is more but a low order of skill is sufficient to work with a drill jig 19-Oct-20 Theory of Metal Machining/Prepared by Joseph EL-GHOLAM 52 Plate Jig 19-Oct-20 Theory of Metal Machining/Prepared by Joseph EL-GHOLAM 53 Box Jig 19-Oct-20 Theory of Metal Machining/Prepared by Joseph EL-GHOLAM 54 Chanel Jig 19-Oct-20 Theory of Metal Machining/Prepared by Joseph EL-GHOLAM 55 Indexing Jig 19-Oct-20 Theory of Metal Machining/Prepared by Joseph EL-GHOLAM 56 Diameter Jig 19-Oct-20 Theory of Metal Machining/Prepared by Joseph EL-GHOLAM 57 Types of Drills A drill usually consists of two cutting edges set an angle with the axis The types of drills and tools related to drilling operations are as follow: Center drills Twist drills Gun drill Core drill bit Counterbore bit Spotfacing bit Countersink bit Ejector drill Indexable drill bit Spade bit Straight fluted bit Trepan bit Twist step drill bit Unibit Reamer Left hand bits Screw extractors taps 19-Oct-20 Theory of Metal Machining/Prepared by Joseph EL-GHOLAM 58 Center Drills Center drills consist of a pilot drill and a countersink They are used to create holes at the center of a piece of stock so it can be turned between centers on a lathe in metalworking applications 19-Oct-20 Theory of Metal Machining/Prepared by Joseph EL-GHOLAM 59 Center Drills Type A 19-Oct-20 Theory of Metal Machining/Prepared by Joseph EL-GHOLAM 60 Center Drills Type B 19-Oct-20 Theory of Metal Machining/Prepared by Joseph EL-GHOLAM 61 Center Drills Type R 19-Oct-20 Theory of Metal Machining/Prepared by Joseph EL-GHOLAM 62 Center Drills Type R 19-Oct-20 Theory of Metal Machining/Prepared by Joseph EL-GHOLAM 63 Twist Drills Twist drills usually have a taper shank, at the end which is fitted into the drilling machine having a tapered sleeve of matching taper Sometimes the shank is machined parallel, then a special collet chuck is fitted in the drilling machine, in which the drill is held The drill has two lips at the other end where the cutting takes place, when the drill rotates The angle between the two cutting lips is usually 118° The chips formed at the cutting edges are automatically guided upwards through the helical grooves cut into the body of the drill; these grooves are called flutes 19-Oct-20 Theory of Metal Machining/Prepared by Joseph EL-GHOLAM 64 Twist Drills Nomenclature 19-Oct-20 Theory of Metal Machining/Prepared by Joseph EL-GHOLAM 65 Twist Drills 0.5