Chapter 4 Section 10.docx
Document Details
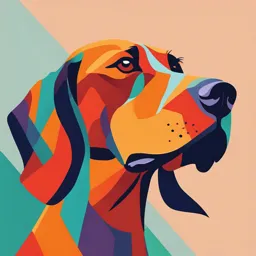
Uploaded by [email protected]
Tags
Full Transcript
Hello and welcome back to our journey through the Fundamentals of Flight. In our previous module, we unlocked the secrets of advanced aerodynamics, shedding light on the principles that govern pressure, temperature, and the mysterious force of lift that keeps our aircraft in the sky. Today, we\'ll s...
Hello and welcome back to our journey through the Fundamentals of Flight. In our previous module, we unlocked the secrets of advanced aerodynamics, shedding light on the principles that govern pressure, temperature, and the mysterious force of lift that keeps our aircraft in the sky. Today, we\'ll set our sights on something both profound and practical: the elements of an efficient airfoil. Aspiring pilots and aeronautical engineers, imagine the airfoil as the heart of an aircraft's wing. It\'s not merely a shape; it\'s a testament to human ingenuity, sculpted by laws of physics and refined through trial, error, and technological innovation. The efficiency of an airfoil can determine the lifeline of aircraft performance --- from the humblest gliders to the mightiest jet fighters. Understanding this will be your key to mastering flight dynamics and design. \[Slide: Definition of Airfoil\] An airfoil, my fellow aviation aficionados, is a shape designed to generate lift as air flows over and under it. Every airfoil is an amalgamation of science and art --- where every curve, thickness, and angle is a deliberate choice subjected to the ruthless jury of aerodynamics. \[Slide: Lift Generation by Airfoil\] At its core, lift generation hinges on differences in air pressure. The airfoil's shape is tailored to create lower pressure on its upper surface and higher pressure beneath, compelling the wing --- and thereby the aircraft --- upwards. \[Slide: Airfoil Shape and Contour\] Let\'s dive into the elements that make an airfoil efficient. The shape and contour are like the airfoil\'s signature --- unique, optimized for its role. A fighter jet\'s airfoil differs vastly from that of a cargo plane, as each is optimized for different flight conditions. \[Slide: Airfoil Thickness and Camber\] Thickness and camber, or the curvature of the airfoil, demand a delicate balance. Too thick, and drag will slow you down. Too slim, and you may not generate enough lift. Camber affects how air accelerates over the wing --- crucial for managing lift across various angles of attack. \[Slide: Leading and Trailing Edges\] Leading and trailing edges are the airfoil\'s frontlines. A sharp leading edge slices through the air with minimal resistance, while a tapered trailing edge ensures a smooth escape for airflow, minimizing turbulence and drag. \[Slide: Angle of Attack\] Speaking of angles of attack, your aircraft's attitude is not just about posture --- it's a pivotal player in lift dynamics. Increase the angle, and you\'ll hike up the lift, but push too far, and the airflow separates from the wing, causing a stall. \[Slide: Materials and Construction\] Materials and construction methods introduce a realm where physics meets pragmatism. Today\'s materials have to be light yet sturdy, able to weather the assault of high-speed winds and the relentless pull of gravity. \[Slide: Computational Fluid Dynamics (CFD)\] Now, let\'s acknowledge a revolutionary ally in airfoil design --- computational fluid dynamics or CFD. These advanced simulations allow us to foresee how airfoils perform long before they taste the wind. Think of CFD as a digital wind tunnel, a crucible where airfoil designs are forged. \[Slide: Summary of Key Elements\] In summary, an efficient airfoil is a symphony of shape, contour, angle, and material. When harmonized, they can coax the maximum lift with minimal drag out of the ether that an aircraft calls home. As we prepare to land today\'s session, remember that these elements are not standalone marvels but interdependent pieces of a grander puzzle. Only by understanding how they interact can we truly master the art of designing airfoils that transcend mere functionality and achieve aerodynamic excellence. Next up, you will delve into reading materials that further explore optimizing airfoil shape for even greater aerodynamic efficiency. Immerse yourself in the principles of lift production that directly influence airfoil shape design. Each page you turn will bring you closer to understanding the subtle dance between airfoil efficiency and the forces of flight. Thank you for your dedicated attention. We\'re not just learning to fly; we\'re soaring into the world of advanced aerodynamics and aircraft performance. Until next time, keep your eyes on the skies and your mind in the clouds. Hello, aspiring pilots and aviation enthusiasts! In our previous module, we took an in-depth dive into the core principles of aerodynamics, discussing how airflow, pressure, and airfoil shapes work together to keep aircraft aloft. Today, we soar into a new chapter in our journey, focusing on optimizing the airfoil shape for improved aerodynamic efficiency. By the end of this lesson, you will understand how to finesse airfoil designs to enhance aircraft performance. Airfoil shape optimization is both an art and a science. An airfoil, in its simplest terms, is the cross-sectional shape of a wing or blade. But why is its shape so critical? Because an aircraft\'s lift, drag, maneuverability, and fuel efficiency all hinge on the contours of its airfoils. Our goal here isn\'t just to create wings that lift; it\'s to tailor them precisely for specific flight conditions and performance criteria. Let's talk factors. The airfoil's shape can drastically alter how air flows over the wing. For instance, the thickness, camber, and leading-edge radius all come into play, each influencing how smoothly air moves over the surface, which in turn affects lift and drag. And it's not just about the form -- the material used, the texture of the surface, and even the temperature can impact performance. Picture air moving over a wing. It's not just a gentle stream; it\'s a dynamic dance of physics. The geometry of an airfoil manipulates this dance, channeling airflow to create low pressure on the top and high pressure beneath. It\'s a delicate interplay, demanding precision because even minute changes can have significant outcomes. Enter computational fluid dynamics, or CFD. This powerful tool models airfoil flows without the need for wind tunnel tests on every tweak. Engineers feed airfoil geometries into simulations to iterate designs quickly, seeing in virtual space how alterations affect performance. It\'s an indispensable method in modern aeronautics, allowing for efficient optimization before a design ever leaves the ground. Of course, computational power isn\'t infallible. That\'s why testing and simulations in controlled environments, like wind tunnels, are pivotal. Experimentation validates theories and hones designs, moving from the digital realm to the tactile world where actual airflows reign supreme. Let's take the supercritical airfoil as a stellar example. Introduced in the 1960s, its unique shape allows planes to fly close to the speed of sound with less drag, drastically improving efficiency over traditional airfoil designs. It's just one instance of how optimization has revolutionized flight. Before we conclude, let\'s crystallize a few best practices. Always start with a clear mission profile -- know the aircraft\'s intended use. Understand the trade-offs; for instance, an airfoil optimized for speed may sacrifice lift. Iterate and validate, using both CFD and wind tunnel tests, and remain open to new materials and technologies that can open doors to unprecedented aerodynamic efficiency. As we loop back to the hangar for today, remember: the shape of an airfoil isn\'t just a component of design; it\'s the wingbeats of innovation in aviation. Next time, we'll dive into a Reading on Lift Production Principles, where you'll study the mechanics behind lift and how different airfoil designs can harness this force with greater finesse. Make sure to glide through those materials to gain a fuller understanding of the connection between design and performance. Thank you for joining me in this lesson. Lift your knowledge, optimize your learning, and keep your ambitions sky-high until our next session. Fly safely! Lift is the fundamental force that allows an aircraft to ascend and remain in the air, defying the pull of gravity. It is generated primarily by the airfoil, a component of the aircraft\'s wings that is designed to exploit the principles of aerodynamics. In order to understand how airfoil shape design is influenced by lift production principles, we need to explore the underlying mechanics of how lift is created. The shape of an airfoil is crafted to have a curved upper surface and a flatter lower surface. This design causes air to travel faster over the top than beneath it. According to Bernoulli\'s principle, faster-moving fluid has lower pressure. Consequently, the pressure difference between the upper and lower surfaces of the wing creates an upward force -- lift. Several factors must be considered to optimize lift production when designing an airfoil: 1\. \*\*Angle of Attack\*\*: The angle between the chord line of the airfoil and the oncoming air is known as the angle of attack (AoA). Increasing the AoA to a certain point increases lift because it enhances the pressure differential. However, beyond a critical angle, the airflow separates from the upper surface of the airfoil, causing a stall, which drastically reduces lift. 2\. \*\*Camber\*\*: The curvature of the airfoil is referred to as camber. A higher camber typically increases lift by augmenting the pressure differential but can also increase drag. The design must balance lift and drag to achieve the desired performance. 3\. \*\*Aspect Ratio\*\*: This is the ratio of the wingspan to the average wing chord (width). Wings with a higher aspect ratio, which are longer and narrower, tend to produce more lift and less drag than wings with a lower aspect ratio. This is particularly important for aircraft designed for efficiency at high altitudes or for gliding. 4\. \*\*Thickness\*\*: The thickness of the airfoil affects both lift and drag. A thicker airfoil can generate more lift, but also more drag. Therefore, the thickness is usually varied along the span of the wing to optimize performance for different flight conditions. 5\. \*\*Leading and Trailing Edges\*\*: The shape of the leading edge affects how the air splits and reattaches to the airfoil, while the shape of the trailing edge influences the wake. Both must be designed to maintain smooth airflow and to control the boundary layer to maximize lift and minimize drag. 6\. \*\*Wingtips\*\*: Wingtip design can also play a significant role in lift efficiency. Features like winglets can help reduce vortex formation at the wingtips, decreasing induced drag and improving lift-to-drag ratio. When incorporating these principles into airfoil shape design, it\'s essential to consider the intended use of the aircraft. For example, an airfoil for a high-speed jet will be significantly different from one designed for a light, slow-moving glider. Through computational fluid dynamics (CFD) and wind tunnel testing, designers can simulate and analyze airflow over an airfoil, allowing them to fine-tune the shape for optimal lift production. The resulting design is a careful balance of all these factors, tailored to the specific requirements of the aircraft\'s performance envelope. In conclusion, the principles of lift production are central to the design of an efficient airfoil. By understanding and applying these principles, aerospace engineers and designers can create airfoil shapes that enhance the lifting capability of an aircraft while maintaining or improving overall aerodynamic efficiency.