Chapter 2.1 Pneumatic Power System PDF
Document Details
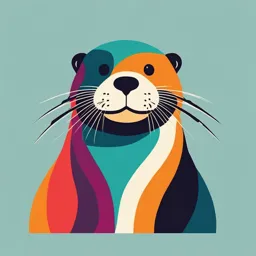
Uploaded by WiseCreativity
Singapore Polytechnic
Tags
Summary
This document describes pneumatic power systems in aircraft, including their functions, components, and advantages over hydraulic systems. It covers different types of pneumatic power sources and their use in various aircraft applications. This document is intended for training purposes.
Full Transcript
MM3531 Aircraft Systems Chapter 2: Pneumatic Power System For Training Purpose Only Official (Closed), Non-Sensitive Hydraulic Power Objective List the functions of pneumatic systems in the aircraft and its...
MM3531 Aircraft Systems Chapter 2: Pneumatic Power System For Training Purpose Only Official (Closed), Non-Sensitive Hydraulic Power Objective List the functions of pneumatic systems in the aircraft and its comparison with hydraulic systems. List and describe the different sources of input such as air bottles, ground supply and compressor. Describe with the aid of diagram, the working principle/functions of the various components in a typical high pressure pneumatic system, showing the distribution and the interface with other systems. Page 2 For Training Purpose Only Official (Closed), Non-Sensitive Hydraulic Power Pneumatic System Introduction There are aircraft equipped with high pneumatic pressure system over the use of hydraulic system or use only in emergency situation where the hydraulic is still the main source to operate the system. Brakes. Opening and closing of doors. Driving hydraulic pumps, alternators, starters, water injection pumps. Operating emergency devices. Both pneumatic and hydraulic systems are similar in their operation and transmit power in a confined space. The difference between air and hydraulic fluid one is compressible and the other is incompressible. Page 3 For Training Purpose Only Official (Closed), Non-Sensitive Hydraulic Power High Pressure Pneumatic System Pneumatic power source An emergency bottle is charged with compressed air, carbon dioxide or nitrogen at a certain pressure and the charging can be performed by a ground-operated compressor through a charging valve and the air is trapped inside by a shut off valve. The disadvantage of using an emergency bottle as the only source of supply of air (carbon dioxide, nitrogen or compressed air) is that it cannot be recharged in flight after use hence this arrangement is mainly used for emergency operation system such as emergency extension of landing gear or brakes in the event of hydraulic system failure. Ground charging Emergency system such as extension Emergency system station of arresting hook or main landing gear air bottles door actuators Page 4 For Training Purpose Only Official (Closed), Non-Sensitive Hydraulic Power High Pressure Pneumatic System Pneumatic power source Pneumatic power can also be supplied by bleed air from aircraft engine or adding air compressor to recharge the bottle after it is used during flight. Air drawn from engine Engine 1 compressor stage bleed air Usage by various Air bottles pneumatic sub-system such as actuator The compressor Air is drawn from which is coupled 2 with the engine the atmosphere by compressor gear box Page 5 For Training Purpose Only Official (Closed), Non-Sensitive Hydraulic Power High Pressure Pneumatic System Pneumatic Components The pneumatic system is considered is lighter in weight as compared to hydraulic system mainly because pneumatic system does not utilize reservoir, hand pump, accumulators, regulators, or engine-driven or electrically driven power pumps for building normal pressure. However there are still some similar components that exists in both the systems. Page 6 For Training Purpose Only Official (Closed), Non-Sensitive Hydraulic Power High Pressure Pneumatic System Pneumatic components Air Compressors The air compressors are installed on aircraft to recharge the air bottles whenever pressure is used for operating a unit. Several types of compressors are used for this purpose. Some have one or two stages of compression depending on the maximum desired operating pressure. Single Stage Reciprocating Compressor Page 7 For Training Purpose Only Official (Closed), Non-Sensitive Hydraulic Power High Pressure Pneumatic System Pneumatic components 2 Stage Air Compressors During compression of air, heat is generated as pressure is increased hence the intercooler is used to remove the heat which in turn reduce the power required to drive the compressor. Page 8 For Training Purpose Only Official (Closed), Non-Sensitive Hydraulic Power Pneumatic System Pneumatic components Moisture Separator and Chemical Drier They are used in pneumatic system to remove any moisture caused by the compressor. This is important because moisture will cause freezing and corrosion which can hinder the operation of components such as a check valve or control valve. Chemical driers are incorporated at various locations in a pneumatic system. Their purpose is to absorb any moisture that may collect in the lines and other parts of the system. Page 9 For Training Purpose Only Official (Closed), Non-Sensitive Hydraulic Power High Pressure Pneumatic System Page 10 For Training Purpose Only Official (Closed), Non-Sensitive Hydraulic Power High Pressure Pneumatic System Page 11 For Training Purpose Only Official (Closed), Non-Sensitive Hydraulic Power Pneumatic System Advantages of compressed air over electric or hydraulic. Air is available in an unlimited supply. The components used in pneumatic system are reasonably, simple and lightweight. Pneumatic system does not require return line (as compared to hydraulic system) which leads to weight saving. The system is relatively free from temperature problems. There is no fire hazard and low risk of an explosion occurring. Page 12 For Training Purpose Only Official (Closed), Non-Sensitive Hydraulic Power Recap List the functions of pneumatic systems in the aircraft and its comparison with hydraulic systems. List and describe the different sources of input such as air bottles, ground supply and compressor. Describe with the aid of diagram, the working principle/functions of the various components in a typical high pressure pneumatic system, showing the distribution and the interface with other systems. Page 13 For Training Purpose Only