CH#4 The Eight Wastes.pptx
Document Details
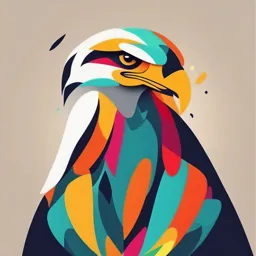
Uploaded by ThumbUpPyrite
University of Business and Technology
Full Transcript
Supply Chain Capstone Project Chapter#4: The Eight Wastes 1 Topics A. The Eight Wastes B. Inventory Waste C. Transportation Waste D. Motion Waste E. Waiting Waste F. Overproduction Waste G. Overprocessing Waste H. Defect or Error Waste I. Behavioral Waste 2 A. The Eight Wastes Waste: is anything tha...
Supply Chain Capstone Project Chapter#4: The Eight Wastes 1 Topics A. The Eight Wastes B. Inventory Waste C. Transportation Waste D. Motion Waste E. Waiting Waste F. Overproduction Waste G. Overprocessing Waste H. Defect or Error Waste I. Behavioral Waste 2 A. The Eight Wastes Waste: is anything that does not add value to a process. Typically, when a product is being stored, inspected, delayed, or waiting in line, it does not add value and it is 100 percent waste. 3 A. The Eight Wastes The most common way to describe these non-value-added activities is by using the concept of the eight wastes. These wastes are applicable to any process, whether it is manufacturing, administration, or transportation. 4 1. 2. 3. 4. 5. 6. 7. 8. A. The Eight Wastes Inventory Waste Transportation or Movement Waste Motion Waste Waiting Waste Overproduction Waste Overprocessing Waste Defect or Error Waste Behavioral Waste (Underutilized Employees) 5 Topics A. The Eight Wastes B. Inventory Waste C. Transportation Waste D. Motion Waste E. Waiting Waste F. Overproduction Waste G. Overprocessing Waste H. Defect or Error Waste I. Behavioral Waste 6 B. Inventory Waste Inventory: is a buffer between suppliers, manufacturers, and customers. It is needed to compensate for: 1. Lead times (e.g., in transportation, manufacturing, etc.) 2. Variability in the system, such as forecast errors, late deliveries, setup times, rework, quality problems, and downtime. 7 B. Inventory Waste Inventory might also refer to information, such as customer orders that is important as it directly impacts the cycle time. Inventory waste is both the most visible and is actually an end result of the other wastes. 8 B. Inventory Waste There are four types of inventory: 1. Raw materials —Typically purchased materials and components. Work-in-process (WIP) —The transformation process has started but has 2. not yet been completed. 3. Finished goods —Finished, saleable products. 4. Materials, Repairs, and Operations (MRO) —Inventory for equipment spare parts and supplies. 9 B. Inventory Waste All of these types of inventory cost money to maintain. This is called holding or carrying costs. These costs can range from 15% to 30% of include cost of damage. the value of a product and capital, taxes, storage, insurance, handling, labor, and 10 B. Inventory Waste Businesses need some inventory and typically have to balance the tradeoff between the cost of service. carrying inventory and customer 11 Topics A. The Eight Wastes B. Inventory Waste C. Transportation Waste D. Motion Waste E. Waiting Waste F. Overproduction Waste G. Overprocessing Waste H. Defect or Error Waste I. Behavioral Waste 12 C. Transportation Waste This type of waste include transporting or moving materials, people, tools, or information. When material is received, it should only be touched once to put it away and another time to pull it for consumption. However, it rarely happens. 13 C. Transportation Waste Material may be moved from one place to another on the floor, put on a storage rack, pulled to remove some material, then returned to a different rack, All of etc. this excess movement is wasteful. 14 C. Transportation Waste Companies are not only paying a forklift driver to move the material, but each time it is moved. Each time material is moved, inventory accuracy may be affected and damage may occur. When material is returned to a different spot, there is the risk of losing it and accidentally ordering more. 15 C. Transportation Waste The “foundation” concepts of layout and visual workplace are so important. When looking at layout, companies must think of “flow.” This is important whether for a manufacturing facility, office, or warehouse. 16 Topics A. The Eight Wastes B. Inventory Waste C. Transportation Waste D. Motion Waste E. Waiting Waste F. Overproduction Waste G. Overprocessing Waste H. Defect or Error Waste I. Behavioral Waste 17 D. Motion Waste The concept of motion waste is described by the idea of having things you use more often closer to you and things you use less often further away and higher up. Any motion that does not add value to the product or service is wasteful. Point-of-use storage: means having just enough material or information nearby, which can be replenished when needed from further away. 18 D. Motion Waste Ergonomics: is the science of how humans interact with equipment and the workplace. In terms of motion, you don’t just want to consider efficiency, but safety as well. 19 Topics A. The Eight Wastes B. Inventory Waste C. Transportation Waste D. Motion Waste E. Waiting Waste F. Overproduction Waste G. Overprocessing Waste H. Defect or Error Waste I. Behavioral Waste 20 E. Waiting Waste Waiting Waste: is time spent waiting on materials, supplies, information, and people that are needed to finish a task. This waste can be found whether in the shop floor, in a warehouse, or in an office. 21 E. Waiting Waste In most processes, a great deal of a product’s or service’s lead time is spent on waiting. This can be a result of long setup times, large batch sizes, and downtime. In an office environment, time can be spent waiting on equipment to start up, computer breakdown, signatures, employees on different work schedules. 22 E. Waiting Waste In many warehouses or distribution centers, products can sit “waiting” between different steps in the process (e.g., receiving, putting away, replenishing, picking, packing, and shipping). 23 Topics A. The Eight Wastes B. Inventory Waste C. Transportation Waste D. Motion Waste E. Waiting Waste F. Overproduction Waste G. Overprocessing Waste H. Defect or Error Waste I. Behavioral Waste 24 F. Overproduction Waste Overproduction: is manufacturing, ordering, or processing something before it is actually needed. This typically results in an excess of major waste. This can result in longer lead times, higher storage costs, and potentially a greater amount of of larger batch size. defects (which may be harder to detect) because 25 F. Overproduction Waste Overproduction inhibits (prevent) the smooth flow of In the office materials. environment, it may involve preparing or printing paperwork earlier in batches. The warehouse may suffer from pulling orders earlier than needed or ordering supplies and packaging materials in large batch sizes. 26 Topics A. The Eight Wastes B. Inventory Waste C. Transportation Waste D. Motion Waste E. Waiting Waste F. Overproduction Waste G. Overprocessing Waste H. Defect or Error Waste I. Behavioral Waste 27 G. Overprocessing Waste Overprocessing: happens when too much time or effort is put into processing material or information that is not viewed as adding value to the customer. This can also include using equipment that may be more expensive, complicated, or more precise than is actually needed to perform the operation. 28 G. Overprocessing Waste It may occur when there are unclear customer specifications, a product or service is continually refined beyond what the customer wants or needs, or a lengthy approval process is involved. In the office, overprocessing can include sending the same information in multiple formats (fax and e-mail), repeating the same information on different forms, reentering data, and unnecessary information on a form. 29 Topics A. The Eight Wastes B. Inventory Waste C. Transportation Waste D. Motion Waste E. Waiting Waste F. Overproduction Waste G. Overprocessing Waste H. Defect or Error Waste I. Behavioral Waste 30 G. Defect or Error Waste In manufacturing, the waste of defects primarily refers to repairing, reworking, or scrapping materials. The further along that a defect gets, the more costly it is to the company as they may need to rework it into the system, scrap it and make it all over again, and in the worst case, have it returned from the customer. 31 G. Defect or Error Waste In the office and warehouse, this can be errors such as those made during data entry, receiving, and picking and shipping the wrong product (or the right product, but to the wrong customer). This can be the result of a lack of standardized work and a lack of a visual workplace, poor lighting, and lack of training. 32 G. Defect or Error Waste There are many causes for this type of defect: o o o o o Poor processes Too much variations Supply issues Insufficient or improper training Tools and equipment not properly calibrated or precise o Excessive or unnecessary handling o Inventory levels that are too high 33 Topics A. The Eight Wastes B. Inventory Waste C. Transportation Waste D. Motion Waste E. Waiting Waste F. Overproduction Waste G. Overprocessing Waste H. Defect or Error Waste I. Behavioral Waste 34 I. Behavioral Waste Companies need employee creativity and participation to eliminate the other seven wastes. However, in some companies, there is a culture of not wanting to question things, or not taking risk. It’s like when hearing someone say,“This is how I was shown how to do it,” or “We’ve been doing things this way for years.” 35 I. Behavioral Waste If you’re going to have a successful Lean journey,this type of behavior is unacceptable and must be changed. You must fully utilize and leverage employee knowledge and skills, and offer proper training and opportunities for advancement to guarantee success 36 THE END 37