Optical Fiber Communication Systems PDF
Document Details
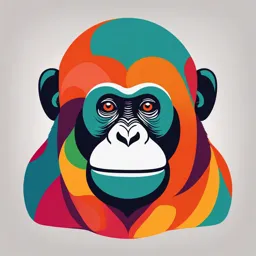
Uploaded by ImaginativePeachTree
STC/JHS
Tags
Summary
This document provides guidelines and procedures for optical fiber communication systems. It covers cable laying, including trenching, cable length calculations, and blowing of OFC cables. The text also includes procedures for cable protection, cable splicing, and duct integrity testing. The document includes diagrams of different cable bend radii, and the arrangement for laying the cable across other infrastructure.
Full Transcript
chapter 13 optical fiber Communication System Section I Guideline for use of OFC 2 48 fiber OFC with 6 Quad jelly filled quad Cable Laid All OFC should be laid...
chapter 13 optical fiber Communication System Section I Guideline for use of OFC 2 48 fiber OFC with 6 Quad jelly filled quad Cable Laid All OFC should be laid in HDPE pipe using blowing method IP MPLS network Shall be installed for both short haul and long haul Section III Cable pit near OFC room shall have depthof 1.25m Rlc pipes dia each will be provided Two ofOFC100mm and separately for quad Cable The pipes shall be laid up to 2 mar Length from the cable pit outside wettable away slope such that Cable in a way smoother entry of inside the cable pit is obtained section I Detailed survey and Finalization of the Route Plan OFC of Procedure for 5 km charts I 5 km charts should be prepared which covers a length scale of 5 Km of the route 10 am 1 km The Cable route shall be started foom Controloffice with 30 Mtr steel tape For OFI a minimum distance of 5.75 Mtr Should be maintained b w ONE masts and the Cable In yard minimum distance of Imtr foom ONE a must may be maintained with HDPE Pipe 1.2 km tapping provided for emergency control Ikman.to Cable Length for OFC system Route Length as per actual measurement plus contour allowance of 2.5 Entra Length for track 2 5 meters crossing including loop on each side 10 meters entra length on approdus crossing of the bridges and culverts on each side as per miment 5 meters Cable to be kept on either side ofsteel of major bridge 2.5 meters of Cables on short bridges At joint everyshall a loop of 10 meters on either side be kept In Cable but a loop of 10 meters in the Cable pit shall be kept section VI flow Diagram work Preparation of Material Tool Equipment Digging Trenching laying ofHDPE Duct sieved Earth filling Backfilling Protective Covers ifAny DIT Duct Intignity test Blowing of Cable completion Machine excavation Caterpillar Tractor can be used for laying Cable along cable route using adjustable ripper lowing typical preparation of Lemeterdepth Duct laying DIT shall becarried out when laying is completed in a block section 8 10km Paying out Cable OFC bend radius is the minimum bend radius under tension is during pulling 20timesans W yÉffabridgingsafetydonation ÉÉftÉhyfg the diameter the 30 times of OFC 1111 Radiusof Drum 30 X Diameter of OFC Laying of Cable by winch 1.1 times w Pulling Tension kg Bending Radius 30 times D Pulling speed Max 15 mtr min Blowing of OFC Cable 10 to 15 meter OFC Should be kept in next pit of Section I 9 This chapter or section covers the various Cable protection arrangements for the purposeof preventing damage to cable and protection to staff Protection of Cable Crossing Bridges Culverts i septate troughs should be provided for laying 6 quad cable and OFC For Smaller Currents bridges HDD should be adopted with DWC pipe protection and ensuring that cable is minimum 2 mtr below the bed of culverts bridges iil at culverts bridges using steel crossing GI major box troughs pipe pipe channels etc Measure against theft of steel Troughs i In order to prevent theft Steel of optic fibre Cable troughs with OFC should be filled by to ts specification Espasmysdspitia ill por emperative Less Iii Before Pouringng bitumen compound its temperature should be accurately measured to ensure that the Pouring temperature is not more mar 1404 Civ The bitumen Compound should be filled upto a height Approvimetly 60mm of Arrangement for laying of Fiber optic Cable across Girder Bridges Girder bridges up to span length of 12 meter through GI pipe Girder bridges of span length more than 12 meters through steel trough separate trough for 6 quad Cable should be used laying Protection arrangement the Cable Route on Purpose Bricks provide in Cable trenching to be placed after covering the Baffles b The Cable marker shall be provided at distance of normally 50 meters on cable route and my the wherever route places changes 4 Joint Indicator shall be provided at all joints d The Cable and markers provided shall marker faint be standard stone RCI type of WCPable Crossing Tracks and level Crossing Geate The cable shall be laid in RCC PWC ducts keeping dept Sa as soules In case of Cable crossing the he gates RCI DWI Ducts to be laid on the road and for a distance at least 2 meters foom either side of the road of Minimum depth at any track Crossing Shall not be less than 1.2 meters with RCC DWC duct In Case Cable crossing the track it may be ensured that it should not be bent less than In Ñ trenchless JEoad HDD platform Railways track etc should be adopted A minimum depth of 1.2 meter 120 am to be ensured 120 am for OFC 100 am for quad cable Cable should be taken in GI pipe in rocky areas Curberts Girder bridges and PSC girder bridges Note 5 meter Cable should be kept at the ends OFC Cable shall be taken through class B GI Breommdameter Also for tunnet Back Trenches filling of At least 120 mm foom the surface of the lastcable At 500 mm depth pvc warning tape shall be a provided continuously ruining in the trench In care of shortage of manpower video recording ofandcableback trench protection arragand laying depthoftrenches should be included in scope of filling of contract Section x̅ 10 ng valias of Two Techniques for fainting of OFC Mechanical splice Fusion splice Mechanical splice This aligns the anis the two fibres to be and of hold Joined physically them together Mechanical splicing may be used only for temporary splicing of fibres Fusion splicing This is done localized heating i e by by Applying electric are or flame at the interface between the butted pre aligned fibre end causing them to soften and fuse together now days only fusion splicing shall be adopted The following steps are involved for jointing of the Cables of Cable for 1 Preparation 2 the fainting Cable Stripping cutting 3 Prepration of Cable and joint closure for solicing H and clearing fibers and of stripping 5 organising fibres finishing joints 6 Sealing of joint closure 7 Placing joint in pit Preparation of Cable for jointing During the installation a minimum of 10meter of Cabal a at each end is coiled in the jointing pit to provide out at locations for jointing to be carried b The pit size shall be so as to ensure the length of wall on which faint is more ed is greater than clouser length plus twice minimum the bending radius of the cable C A pit length 11 meter is sufficient for most of the cable of and Clouser joind the Cable Stripping Cutting of The Cable is stripped of outer and inner sheath with each sheath the staggered it Apposimetely 10mm foom one above Stripping and cleaning of fibee Prior to splicing primary protective coating of each fibre shall be stripped off up to length mm fibre stripper of 50 by Uri cleaning of the fiber shall then be performed to obtain as close as possible to a perfect 90 face on the fibre Splicing of the Fibre Fusion splicing of fibre Follow general steps with full Automatic the microprocessor central splicing machine The clean bare fibre shall be dipped in the beaker of ethyl alcohol of dm ultrasonic cleaner and Ultrasonic cleaner Switched on for 5 10 seconds The bare fibre shall then be placed inside'v groove of the splicing machine by opening clamp I mm gap 1 available b w mayand electrodes end of the fibre being spliced and heat shrine protector insulted The machine shall Pre fuse set align both in and Y directions and finally fuse the fibre Mechanical splicing of the fibre two method Precision alignment of fibre in v1 groove and fibre ends are sealed with some inden matching fluid and adhesive Ultrasonic light Source for curing optical adhesive v Trt Note The end to end loss should not enceed Esa En WI RCC Cable Route Marker For OFC and Quad Cable route All sides above ground to be painted with RED enameled paint The Concrete Composition to be added as 12 4 For OFC faint All sides above ground to be painted with Greene enameled paint For QUAD joints All sides above ground to be painted withfellows enameled paint Duct Test DIT Integrity DIT is to be carried before OFC Cable blowing The purpose of DIT is to ascertain and ensure the the duct for Cable installations suitability of through jetting Important points for DIT Cable installation through jetting can be carried out successfully only under a pressure of10bar Possible reasons for failure of DIT Preserve test are Leakage at Couplers Puncture in Duct The DIT test consists of the h important following steps i Air blowing purpose is to ensure that there are no discontinuities in the duct ii shuttle diameter 80 of the duct inside diameter of a and of 150 mm length is passed through the duct iii sponge of a diameter two times the duct inside diameter and length of 100mm is blown through the duct vs Pressure is conducted at test 5 bar pressure 30 Minutes with manimum for permissible drop 0.5 bar of Air is ng introduced into duct and a check is made at the end of the 2 km Section of duet Shuttle Test A shuttle of a diameter 80 1 of duct inside diameter and 150 of duett Mmtentis passed through the If The shuttle should pass through the 2 km of duct length in a space of 3 minutes means Shutle 3 minute 2 km duet past aim I 1 Sponge Blowing Purpose of blowing sponge through the duct is to clean it A sponge of a diameter twice the inside diameter the duct and 100 mm in length is blown through of the duct The time Required for the sponge to pass through the 2km duct length in 3 minutes Presure Test The pressure test is conducted at 5 bar pressure over a 30 minutes period the pressure loss should not exceed 0.5 bar