Transformers I (3.15) PDF
Document Details
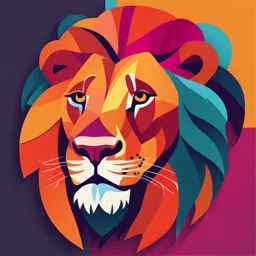
Uploaded by FaultlessMarsh8570
Tags
Summary
This document covers various aspects of transformer construction, operation, and types. It describes learning objectives related to transformers, including their construction principles, operating principles, and operation under no load. Concepts like primary and secondary currents, voltage relations, turns ratio, and power relationships are explained. The document also details hollow-core and shell-core transformers, as well as transformer windings.
Full Transcript
Transformers I (3.15) Learning Objectives 3.15.1.1 Describe various construction principles of transformers (Level 2). 3.15.1.2 Describe general operating principles of transformers (Level 2). 3.15.3.2 Describe transformer operation under no load (Level 2). 3.15.4.3 Describe the purpose of polarity...
Transformers I (3.15) Learning Objectives 3.15.1.1 Describe various construction principles of transformers (Level 2). 3.15.1.2 Describe general operating principles of transformers (Level 2). 3.15.3.2 Describe transformer operation under no load (Level 2). 3.15.4.3 Describe the purpose of polarity markings on transformer schematic diagrams (Level 2). 3.15.5.1 Describe methods for calculating transformer line voltages and currents (Level 2). 3.15.5.2 Describe methods for calculating transformer phase voltages and currents (Level 2). 3.15.7.1 Explain the terms primary and secondary current in relation to transformer operation (Level 2). 3.15.7.2 Explain voltage in relation to windings in transformer operation (Level 2). 3.15.7.3 Explain the turns ratio and how it applies to voltage and current output in a transformer (Level 2). 3.15.7.4 Explain the power relationship between primary and secondary windings in a transformer (Level 2). 2024-02-15 B-03b Electrical Fundamentals CASA Part 66 - Training Materials Only Page 170 of 284 Components of a Transformer Transformer Construction Principles A conventional transformer is a device composed of two or more coils wound on a former or core. The coils are linked by magnetic lines of force which transfer energy from one circuit to another. Transformers come in all shapes and sizes. Very large, high-voltage, high-current transformers are used for power distribution in towns and cities. In contrast, miniature transformers are used in electronic equipment. Aviation Australia Basic transformer In its most basic form, a transformer consists of: A primary coil or winding – receives energy from AC source. A secondary coil or winding – receives energy from primary winding and delivers it to load. A core that supports the coils or windings – provides a path for the magnetic lines of flux. Two coils of wire (called windings) are wound on some type of core material. In some cases, the coils are wound on a cylindrical or rectangular cardboard form. In effect, the core material is air and the transformer is called an air-core transformer. Transformers used at low frequencies, such as 60 Hz and 400 Hz, require a core of low-reluctance magnetic material, usually iron. This type of transformer is called an iron-core transformer. Most power transformers are of the iron-core type. 2024-02-15 B-03b Electrical Fundamentals CASA Part 66 - Training Materials Only Page 171 of 284 Aviation Australia A basic transformer schematic diagram 2024-02-15 B-03b Electrical Fundamentals CASA Part 66 - Training Materials Only Page 172 of 284 Core Characteristics The composition of a transformer core depends on such factors as voltage, current and frequency. Size limitations and construction costs are also factors to be considered. Commonly used core materials are air, soft iron and steel. Each of these materials is suitable for particular applications and unsuitable for others. Air-core transformers are generally used when the voltage source has a high frequency (above 20 kHz). Iron-core transformers usually used when the source frequency is low (below 20 kHz). Soft-iron-core transformers are very useful where transformers must be physically small, yet efficient. The iron-core transformer provides better power transfer than the air-core transformer. A transformer whose core is constructed of laminated sheets of steel dissipates heat readily, providing for the efficient transfer of power. Most transformers you will encounter in equipment contain laminated-steel cores. Aviation Australia Transformer core with sheet steel laminations These steel laminations are insulated with a non-conducting material such as varnish and then formed into a core. It takes about 50 of these laminations to make a core an inch thick. The purpose of the laminations is to reduce certain losses which will be discussed later in this chapter. An important point to remember is that the most efficient transformer core is one that offers the best path for the most lines of flux with the least loss in magnetic and electrical energy. 2024-02-15 B-03b Electrical Fundamentals CASA Part 66 - Training Materials Only Page 173 of 284 Transformer Types Hollow-Core Transformers Two main shapes of cores are used in laminated-steel-core transformers. One is the hollow-core, so named because the core is shaped with a hollow square through the centre. The core is made up of many laminations of steel and the transformer windings are wrapped around both sides of the core. Aviation Australia A hollow-core transformer 2024-02-15 B-03b Electrical Fundamentals CASA Part 66 - Training Materials Only Page 174 of 284 Shell-Core Transformers The most popular and efficient transformer core is the shell core, in which each layer of the core consists of E and I shaped sections of metal. These sections are butted together to form the laminations. The laminations are insulated from each other and then pressed together to form the core. Aviation Australia A shell-core transformer 2024-02-15 B-03b Electrical Fundamentals CASA Part 66 - Training Materials Only Page 175 of 284 Transformer Windings As stated previously, the transformer consists of two coils called windings which are wrapped around a core. The transformer operates when a source of AC voltage is connected to one of the windings and a load device is connected to the other. The winding that is connected to the source is called the primary winding. The winding that is connected to the load is called the secondary winding. Note: In this chapter, the terms primary winding and primary are used interchangeably; the terms secondary winding and secondary are also used interchangeably. Aviation Australia Transformer windings In the transformer shown in the cutaway view, above right, you will see that the primary consists of many turns of relatively small wire. The primary is wound in layers directly on a rectangular cardboard form. The wire is coated with varnish so that each turn of the winding is insulated from every other turn. In a transformer designed for high-voltage applications, sheets of insulating material, such as paper, are placed between the layers of windings to provide additional insulation. When the primary winding is completely wound, it is wrapped in insulating paper or cloth. The secondary winding is then wound on top of the primary winding. After the secondary winding is complete, it too is covered with insulating paper. Next, the E- and Ishaped sections of the iron core are inserted into and around the windings. The leads from the windings are normally brought out through a hole in the enclosure of the transformer. Sometimes, terminals may be provided on the enclosure for connections to the windings. 2024-02-15 B-03b Electrical Fundamentals CASA Part 66 - Training Materials Only Page 176 of 284 A transformer also includes four leads, two from the primary and two from the secondary. These leads are to be connected to the source and load respectively. Transformer Symbols The image shows typical schematic symbols for transformers. The symbol for an air-core transformer is shown in (A). Parts (B) and (C) show iron-core transformers. The bars between the coils are used to indicate an iron core. Frequently, additional connections are made to the transformer windings at points other than the ends of the windings. These additional connections are called taps. When a tap is connected to the centre of the winding, it is called a centre tap. The schematic shows a centre-tapped iron-core transformer. Aviation Australia Transformer schematic symbols The amount of induced voltage depends on the impedance of each inductor and the amount of magnetic coupling between the two windings. The amount of magnetic coupling between the primary and secondary windings is set by the type of core material and the relative position of the windings to each other. 2024-02-15 B-03b Electrical Fundamentals CASA Part 66 - Training Materials Only Page 177 of 284 Transformer Operation Transformers and Alternating Current A transformer is a device that transfers electrical energy from one circuit to another by electromagnetic induction (transformer action). The electrical energy is always transferred without a change in frequency, but may involve changes in magnitudes of voltage and current. Because a transformer works on the principle of electromagnetic induction, it must be used with an input source voltage that varies in amplitude. There are many types of power that fit this description; for ease of explanation and understanding, transformer action will be explained using an AC voltage as the input source. One important advantage is that when AC is used, the voltage and current levels can be increased or decreased by means of a transformer. As you know, the amount of power used by the load of an electrical circuit is equal to the current in the load times the voltage across the load, or P = EI. If, for example, the load in an electrical circuit requires an input of 2 A at 10 V (20 W) and the source is capable of delivering only 1 A at 20 V, the circuit could not normally be used with this particular source. However, if a transformer is connected between the source and the load, the voltage can be decreased (stepped down) to 10 V and the current increased (stepped up) to 2 A. Notice in the above case that the power remains the same. That is, 20 V times 1 A equals the same power as 10 V times 2 A. Up to this point the chapter has presented the basics of the transformer, including transformer action, the transformer's physical characteristics and how the transformer is constructed. Now you have the necessary knowledge to proceed into the theory of transformer operation. + PRIMARY COIL + LOAD _ SECONDARY COIL _ © Aviation Australia Basic transformer with alternating current input 2024-02-15 B-03b Electrical Fundamentals CASA Part 66 - Training Materials Only Page 178 of 284 No-Load Condition You have learned that a transformer is capable of supplying voltages which are usually higher or lower than the source voltage. This is accomplished through mutual induction, which takes place when the changing magnetic field produced by the primary voltage cuts the secondary winding. A no-load condition is said to exist when a voltage is applied to the primary, but no load is connected to the secondary. Because of the open switch, there is no current flowing in the secondary winding. Aviation Australia Transformer under no-load condition With the switch open and an AC voltage applied to the primary, there is, however, a very small amount of current, called excitation current, flowing in the primary. Essentially, what the excitation current does is 'excite' the coil of the primary to create a magnetic field. The amount of excitation current is determined by three factors: The amount of voltage applied (Ea) The resistance (R) of the primary coil's wire and core losses The XL, which depends on the frequency of the excitation current. These last two factors are controlled by transformer design. This very small amount of excitation current serves two functions: Most of the excitation energy is used to maintain the magnetic field of the primary. A small amount of energy is used to overcome the resistance of the wire and core losses, which are dissipated in the form of heat (power loss). Excitation current will flow in the primary winding at all times to maintain this magnetic field, but no transfer of energy will take place as long as the secondary circuit is open. 2024-02-15 B-03b Electrical Fundamentals CASA Part 66 - Training Materials Only Page 179 of 284 When there is no load on the secondary winding of the transformer, the primary winding draws very little even though it may be left connected to its supply source. This is because it is highly inductive, and it therefore has a high inductive reactance. The alternating current in the primary winding has a continually varying magnetic field that induces a back-EMF in each turn of the winding. 2024-02-15 B-03b Electrical Fundamentals CASA Part 66 - Training Materials Only Page 180 of 284 Counter-EMF Production of Counter-EMF When an alternating current flows through a primary winding, a magnetic field is established around the winding. As the lines of flux expand outward, relative motion is present and a counter-EMF is induced in the winding. This is the same counter-EMF you learned about in the chapter on inductors. Flux leaves the primary at the north pole and enters the primary at the south pole. The counter-EMF induced in the primary has a polarity that opposes the applied voltage, thus opposing the flow of current in the primary. It is the counter-EMF that limits excitation current to a very low value. Aviation Australia Production of counter-EMF Inducing a Voltage in the Secondary Windings As the excitation current flows through the primary, magnetic lines of force are generated. While current is increasing in the primary, magnetic lines of force are expanding outward from the primary and cut the secondary. As you remember, a voltage is induced into a coil when magnetic lines cut across it. Therefore, the voltage across the primary causes a voltage to be induced across the secondary. 2024-02-15 B-03b Electrical Fundamentals CASA Part 66 - Training Materials Only Page 181 of 284 Primary and Secondary Phase Relationship A transformer off load (no load connected to the secondary) acts as an inductor. In inductive circuits voltage leads current (CIVIL) so voltage will lead the current by 90°. Aviation Australia Voltage leads the current in an inductive circuit The opposition to current flow in an inductor is the self-induced voltage (Back EMF) which is induced due to the magnetic field. The magnetic field is caused by the amount of current in the wire of the coil winding. The flux produced by this current is directly proportional to the current and by default will proscribe a waveform in phase with current. The induced voltage (BEMF) is directly proportional to the rate of change of flux and therefore is also at 90° to the current, making the BEMF at 180° to the applied voltage. Aviation Australia 2024-02-15 Graphical representation of voltage sine wave leading current sine wave indicating an inductive load B-03b Electrical Fundamentals CASA Part 66 - Training Materials Only Page 182 of 284 As it is the same magnetic field that generates the BEMF and the voltage in the secondary, if both primary and secondary are wound in the same direction the polarity of the secondary will be the same as the BEMF and 180° to the applied voltage. Aviation Australia Transformer – primary and secondary wound in the same direction producing 180 degree phase shift Aviation Australia Alignment of like wound coils with bar core cut in half To show what a like wound coil looks like in a hollow core transformer we take the bar core cut in half and rotate them notice that the centremost terminals are still closest together at the bottom of the figure. Aviation Australia Magnetic circuit completed and phase relationship shown 2024-02-15 B-03b Electrical Fundamentals CASA Part 66 - Training Materials Only Page 183 of 284 Complete the magnetic circuit then reapply the input and output sine waves to show phase relationship. Most transformer uses do not require a specific phase relationship to the output. For those systems that do the method of indicating this is a dot by the input and output windings. Aviation Australia On schematics a dot is used to indicate input/output phase relationships With the winding wound in the same direction around the core and you require the opposite phase then just swap the terminals over. This then has the appearance of the coil being wound in the opposite direction as the perspective has changed. Aviation Australia Right hand winding is reversed causing phase relationship to be the same 2024-02-15 B-03b Electrical Fundamentals CASA Part 66 - Training Materials Only Page 184 of 284 Coefficient of Coupling The coefficient of coupling of a transformer depends on the portion of the total flux lines that cuts both primary and secondary windings. Ideally, all the flux lines generated by the primary should cut the secondary, and all the lines of the flux generated by the secondary should cut the primary. The coefficient of coupling is then one (unity), and maximum energy is transferred from the primary to the secondary. Practical power transformers use high-permeability silicon steel cores and close spacing between the windings to provide a high coefficient of coupling. Lines of flux generated by one winding which do not link with the other winding are called leakage flux. Aviation Australia Coefficient of coupling Since leakage flux generated by the primary does not cut the secondary, it cannot induce a voltage into the secondary. The voltage induced into the secondary is therefore less than it would be if the leakage flux did not exist. Since the effect of leakage flux is to lower the voltage induced into the secondary, the effect can be duplicated by assuming an inductor is connected in series with the primary. This series leakage inductance is assumed to drop part of the applied voltage, leaving less voltage across the primary. 2024-02-15 B-03b Electrical Fundamentals CASA Part 66 - Training Materials Only Page 185 of 284 Turns and Voltage Ratios The total voltage induced into the secondary winding of a transformer is determined mainly by the ratio of the number of turns in the primary to the number of turns in the secondary, and by the amount of voltage applied to the primary. Suppose we have a transformer whose primary consists of 10 turns of wire and whose secondary consists of a single turn of wire. You know that as lines of flux generated by the primary expand and collapse, they cut both the 10 turns of the primary and the single turn of the secondary. Aviation Australia Turns and voltage ratios Since the length of the wire in the secondary is approximately the same as the length of the wire in each turn in the primary, the EMF induced into the secondary will be the same as the EMF induced into each turn in the primary. This means if the voltage applied to the primary winding is 10 V, the counter-EMF in the primary is almost 10 V. Thus, each turn in the primary will have an induced counter-EMF of approximately one tenth of the total applied voltage, or 1 V. Since the same flux lines cut the turns in both the secondary and the primary, each turn will have an EMF of 1 V induced into it. For example, in a transformer that has only one turn in the secondary, the EMF across the secondary is 1 V. In a transformer that has a 10-turn primary and a two-turn secondary, since the flux induces 1 V per turn, the total voltage across the secondary is 2 V. Notice that the volts per turn are the same for both primary and secondary windings. Since the counter-EMF in the primary is equal (or almost equal) to the applied voltage, a proportion may be set up to express the value of the voltage induced in terms of the voltage applied to the primary and the number of turns in each winding. 2024-02-15 B-03b Electrical Fundamentals CASA Part 66 - Training Materials Only Page 186 of 284 This proportion also shows the relationship between the number of turns in each winding and the voltage across each winding. Notice the equation shows that the ratio of secondary voltage to primary voltage is equal to the ratio of secondary turns to primary turns. © Aviation Australia Voltage and turns ratio calculation Note: The ratio of the voltage (5:1) is equal to the turn ratio (e.g. 10:2, 200:40, 400:80). Sometimes, instead of specific values, you are given a turns or voltage ratio. In this case, you may assume any value for one of the voltages (or turns) and compute the other value from the ratio. For example, if a turn ratio is given as 6:1, you can assume a number of turns for the primary and compute the secondary number of turns (e.g. 60:10, 36:6, 30:5). A transformer in which the voltage across the secondary is less than the voltage across the primary is called a step-down transformer. The ratio of a four-to-one step-down transformer is written as 4:1. A transformer that has fewer turns in the primary than in the secondary will produce a greater voltage across the secondary than the voltage applied to the primary. A transformer in which the voltage across the secondary is greater than the voltage applied to the primary is called a step-up transformer. The ratio of a one-to-four step-up transformer should be written as 1:4. Notice in the two ratios that the value of the primary winding is always stated first. The voltage ratio of a transformer is the ratio of the amount of voltage in the primary winding (VP) to the amount of voltage in the secondary winding (VS). 2024-02-15 B-03b Electrical Fundamentals CASA Part 66 - Training Materials Only Page 187 of 284 Suppose a transformer has a primary voltage of 30 V and a secondary voltage of 90 V. The voltage ratio would be: VS V oltage Ratio = VP 90V V oltage Ratio = 30V 3 V oltage Ratio = or 3 1 The amount of voltage induced into the secondary winding is directly proportional to the ratio of the number of turns of wire in the primary winding to the number of turns of wire in the secondary winding. Therefore, the voltage ratio of a transformer is equal to the turn ratio: NS = NP VS VP The turn ratio of the above transformer is also 3:1. If the primary and secondary windings are made from a different type and/or a different gauge of wire, then the voltage ratio will not equal the turn ratio. 2024-02-15 B-03b Electrical Fundamentals CASA Part 66 - Training Materials Only Page 188 of 284 Effect of a Load on Transformer Operation When a load device is connected across the secondary winding of a transformer, current flows through the secondary and the load. The magnetic field produced by the current in the secondary interacts with the magnetic field produced by the current in the primary. This interaction results from the mutual inductance between the primary and secondary windings. © Aviation Australia Effect of a load on transformer operation 2024-02-15 B-03b Electrical Fundamentals CASA Part 66 - Training Materials Only Page 189 of 284 Mutual Flux The total flux in the core of the transformer is common to both the primary and secondary windings. It is also the means by which energy is transferred from the primary winding to the secondary winding. Since this flux links both windings, it is called mutual flux. The inductance which produces this flux is also common to both windings and is called mutual inductance. Flux is produced by the currents in the primary and secondary windings of a transformer when source current is flowing in the primary winding. When a load resistance is connected to the secondary winding, the voltage induced into the secondary winding causes current to flow in it. This current produces a flux field about the secondary in opposition to the flux field about the primary (Lenz's law). Thus, the flux about the secondary cancels some of the flux about the primary. With less flux surrounding the primary, the CEMF is reduced and more current is drawn from the source. The additional current in the primary generates more lines of flux, nearly re-establishing the original number of total flux lines. Aviation Australia Mutual flux 2024-02-15 B-03b Electrical Fundamentals CASA Part 66 - Training Materials Only Page 190 of 284 Turns and Current Ratios The number of flux lines developed in a core is proportional to the magnetising force (in ampereturns) of the primary and secondary windings. The ampere-turn (I × N) is a measure of magnetomotive force; it is defined as the magnetomotive force developed by 1 A of current flowing in a coil of one turn. The flux in the core of a transformer surrounds both the primary and secondary windings. Since the flux is the same for both windings, the ampere-turns in both the primary and secondary windings must be the same. Aviation Australia Turns and current ratio The current ratio is the inverse of the turns ratio and the voltage ratio. This means a transformer with fewer turns in the secondary than in the primary steps down the voltage, but steps up the current. Example: A transformer has a 6:1 voltage ratio. If the current in the primary is 200 mA, the current in the secondary is 1.2 A. In this example the voltage across the secondary is one sixth of the voltage across the primary and the current in the secondary is six times the current in the primary. 2024-02-15 B-03b Electrical Fundamentals CASA Part 66 - Training Materials Only Page 191 of 284 © Aviation Australia Turns ratio Primary and Secondary Winding Power As explained, the turn ratio of a transformer affects current as well as voltage. If voltage is doubled in the secondary, current is halved in the secondary. Conversely, if voltage is halved in the secondary, current is doubled in the secondary. In this manner, all the power delivered to the primary by the source is also delivered to the load by the secondary (minus whatever power is consumed by the transformer in the form of losses). © Aviation Australia Power relationship between primary and secondary windings 2024-02-15 B-03b Electrical Fundamentals CASA Part 66 - Training Materials Only Page 192 of 284 In a transformer with a turn ratio of 20:1, if the input to the primary is 0.1 A at 300 V, the power in the primary is P = V × I = 30 W. If the transformer has no losses, 30 W is delivered to the secondary. The secondary steps down the voltage to 15 V and steps up the current to 2 A. Thus, the power delivered to the load by the secondary is P = V × I = 15 V × 2 A = 30 W. Aviation Australia Transformer primary and secondary power We can calculate the power ratio in an ideal transformer by transposing the ratio between voltage and current as follows: VS VP = IP IS We can recognise the formula for the apparent power in the primary (APP). That is, apparent power in the primary equals the voltage across the primary (VP) times the current flow through the primary (IP). The formula for apparent power in the secondary (APS) is also shown in the above expression. If we substitute AP into the above expression, we can show that for an ideal transformer, apparent power in the primary equals apparent power in the secondary. As a formula, AP P = AP S 2024-02-15 B-03b Electrical Fundamentals CASA Part 66 - Training Materials Only Page 193 of 284 Where: PS = Power delivered to the load by the secondary PP = power delivered to the primary by the source PL = power losses in the transformer. The reason for this is that when the number of turns in the secondary is decreased, the opposition to the flow of the current is also decreased. Hence, more current will flow in the secondary. If the turns ratio of the transformer is increased to 1:2, the number of turns in the secondary is twice the number of turns in the primary. This means the opposition to current is doubled. Thus, voltage is doubled, but current is halved due to the increased opposition to current in the secondary. The important thing to remember is that, with the exception of the power consumed within the transformer, all power delivered to the primary by the source will be delivered to the load. The form of the power may change, but the power in the secondary almost equals the power in the primary. 2024-02-15 B-03b Electrical Fundamentals CASA Part 66 - Training Materials Only Page 194 of 284 Transformers II (3.15) Learning Objectives 3.15.2 Explain the causes of efficiency losses in transformers and methods for minimising losses (Level 2). 3.15.3.1 Describe transformer operation under load (Level 2). 3.15.4.1 Describe power transfer within a transformer (Level 2). 3.15.4.2 Describe transformer efficiency and how to calculate it (Level 2). 3.15.8 Describe auto-transformers (Level 2). 2024-02-15 B-03b Electrical Fundamentals CASA Part 66 - Training Materials Only Page 195 of 284 Transformer Losses Power Transformers Practical power transformers, although highly efficient, are not perfect devices. Small power transformers used in electrical equipment have an 80% to 90% efficiency range, while large, electrical utility distribution transformers may have efficiencies exceeding 98%. The total power loss in a transformer is a combination of three types of losses. One loss is due to the DC resistance in the primary and secondary windings. This loss is called copper loss or I2R loss. The two other losses are due to eddy currents and to hysteresis in the core of the transformer. Copper loss, eddy-current loss and hysteresis loss result in undesirable conversion of electrical energy into heat energy. Aviation Australia Power utility distribution transformers have very high efficiency Copper Losses Copper loss or I2R loss is the power lost due to the resistance of the wire used in the primary and secondary coils. These losses are usually given off as heat. We can minimise these losses if we lower the resistance of the wire used in the construction of the primary and secondary windings. This is accomplished by increasing the diameter of the wire. Weight and overall physical dimensions must also be considered when reducing copper losses. 2024-02-15 B-03b Electrical Fundamentals CASA Part 66 - Training Materials Only Page 196 of 284 Hysteresis Losses Reversing the magnetism of the transformer's core will release energy in the form of heat. Hysteresis loss is the loss of this heat energy and is proportional to the area and the materials used in the construction of the core, as well as to the frequency of the applied current. Air-core transformers have no hysteresis losses. Hysteresis losses can also be minimised by reducing the area of the core and by using supermalloy and permalloy materials (silicon-iron, alloys) in the construction of the core. Eddy Current Losses The changing magnetic field of a transformer induces an EMF into the core which sets up currents that circulate within the core. These circulating currents are known as eddy currents. If the core were made from solid iron, these eddy currents would combine together to form a very large current, causing very large losses in the form of heat. The induced eddy currents in the core also set up an opposing flux within the core. This results in more current flowing in the primary to try to maintain the core’s magnetic field, further increasing losses. To minimise the loss resulting from eddy currents, transformer cores are laminated. Since the thin, insulated laminations do not provide an easy path for current, eddy-current losses are greatly reduced. Aviation Australia Laminated cores and eddy current losses 2024-02-15 B-03b Electrical Fundamentals CASA Part 66 - Training Materials Only Page 197 of 284 Transformer Efficiency Transformer Efficiency Calculations To compute the efficiency of a transformer, the input power and the output power must be known. The input power is equal to the product of the voltage applied to the primary and the current in the primary. The output power is equal to the product of the voltage across the secondary and the current in the secondary. The difference between the input power and the output power represents a power loss. You can calculate the percentage of efficiency of a transformer by using the standard efficiency formula shown below: Ef f iciency (in%) = P out × 100 P in Where: Pout = total output power delivered to the load Pin = total input power. If input power to a transformer is 650 W and output power is 610 W, what is the efficiency? Solution: Ef f iciency (in%) = P out × 100 P in 610 Ef f iciency (in%) = × 100 650 Ef f iciency (in%) = 93.8% Power loss can also be calculated by subtracting Pout from Pin (VA or W). Power loss in the above transformer is 40 W – wasted due to heat losses. 2024-02-15 B-03b Electrical Fundamentals CASA Part 66 - Training Materials Only Page 198 of 284 Impedance Matching Maximum Power Transfer In order to understand the requirement for impedance matching and how it is accomplished, we must first study power transfer between parts of a circuit. This transfer could be between different stages of an amplifier or from an amplifier to a loudspeaker. Under ideal conditions, 100% of the power produced by a source is used by the load, but the fact that every source of energy has an internal resistance or impedance makes this impossible. The idea is to make the maximum power available at the load. Suppose we have a 24 V source with an internal impedance of 6 Ω, connected to a 2 Ω load. Aviation Australia Max power transfer #1 Now calculate the power in the load and source. Total circuit resistance: 6 + 2 = 8 Ω Circuit current: V I = 24 = R = 3 A 8 Power in the source: P = I 2 R = 3 2 × 6 = 9 × 6 = 54 Power in the load: P = I 2024-02-15 2 R = 3 2 × 2 = 9 × 2 = 18 B-03b Electrical Fundamentals CASA Part 66 - Training Materials Only Page 199 of 284 In this example, the source is consuming three times the power of the load, meaning the source will be glowing with the heat produced and will most likely be damaged. In the diagram below you see the same 24 V 6 Ω source connected to a 6 Ω Load. Aviation Australia Maximum power transfer question #2 With the load increased to 6 Ω, calculate the power in the load and source. Total circuit resistance: 6 + 6=12 Ω Circuit current: V I = 24 = R = 2 A 12 Power in the source: P = I 2 R = 2 2 × 6 = 4 × 6 = 24 Power in the load: P = I 2 R = 2 2 × 6 = 4 × 6 = 24 In this example, the source is consuming the same amount of power as the load, so the source is still producing a large amount of heat. The same applies to a 24 V 6 Ω source connected to an 18 Ω Load. 2024-02-15 B-03b Electrical Fundamentals CASA Part 66 - Training Materials Only Page 200 of 284 Aviation Australia Max power transfer question #3 Again, calculate the power in the load and source if the same 24-V, 6-Ω source is connected to an 18Ω load. Total circuit resistance: 6 + 18 = 24 Ω Circuit current: V 24 I = = R = 1 A 24 Power in the source: P = I 2 R = 1 2 × 6 = 1 × 6 = 6 Power in the load: P = I 2 R = 1 2 × 18 = 1 × 18 = 18 In this example, the load is consuming the same amount of power as in the first example, and is three times that of the source, 6 W. 2024-02-15 B-03b Electrical Fundamentals CASA Part 66 - Training Materials Only Page 201 of 284 Aviation Australia Maximum power transfer graph summary To Summarise If you require minimum heat generated in the source (as in when the source is a battery), then region 3 (Rload should be less than Rsource). If you require maximum power transfer (such as when linking an antenna to a radio), then use region 2 (Rload should be equal to Rsource). Area 1 should never be used as Rload should never be less than Rsource as this would damage the source. Power supplies require a way to connect a source and a load of dissimilar impedance in such a manner that the connection matches both impedances without losing power. Aviation Australia Impedance matching 2024-02-15 B-03b Electrical Fundamentals CASA Part 66 - Training Materials Only Page 202 of 284 The method of connecting dissimilar impedances is to use a transformer; it is just a matter of calculating the turns ratio, which is: ( NP ) 2 = NS ZP ZS This means: T 2 = ZP ZS The proof is shown below. Aviation Australia Max power transfer question #4 If we have a power supply delivering power to a load, and the voltage is 200 V and the load draws 8 A, then the resistance is: V R = 200 = I = 25 Ω 8 Now, if this is an AC power delivered through a transformer and the load connected uses the same power as before, we have the following circuit as an example. Aviation Australia 2024-02-15 Max power transfer question #4 - the power supply is now connected to the load through a transformer B-03b Electrical Fundamentals CASA Part 66 - Training Materials Only Page 203 of 284 The transformer steps the voltage down from 200 V to 50 V, so the current must be stepped up by a factor of 4. T = VP 200 = VS = 4 : 1 50 so 1 T o calculate I Sec T = 1 : 4 = 8 : I Sec ⟹ I Sec = 32 We now a have a voltage of 50 V and a current of 32 A, therefore: V R Sec = 50 = I = 1.5625 Ω 32 From the first circuit, we have a voltage of 200 V and a resistance of 25 Ω, and in the second we have a voltage of 50 V and a rersistance of 1.5626 Ω. This produces a voltage transformation ratio of 4:1. To calculate the impedance transformation ratio the impedance values of each side of the transformer is compared in a ratio. If we assume that the total impedance is equal to the resistance values calculated earlier then R Pri = Z Pri and R Sec = Z Sec. I mpedance Ratio = Z P ri : Z Sec ⟹ 25 : 1.5625 = 16 : 1 As the impedance ratio is 16:1, the impedance transformation ratio (16) is equal to the turns ratio squared (42). Note: We are ignoring transformer losses and assuming 100% efficiency. Transformer Ratings When a transformer is to be used in a circuit, more than just the turn ratio must be considered. The voltage, current and power-handling capabilities of the primary and secondary windings must also be considered. The maximum voltage that can safely be applied to any winding is determined by the type and thickness of the insulation used. When a better (and thicker) insulation is used between the windings, a higher maximum voltage can be applied to the windings. The maximum current that can be carried by a transformer winding is determined by the diameter of the wire used for the winding. If current is excessive in a winding, a higher-than-ordinary amount of power will be dissipated by the winding in the form of heat. This heat may be sufficiently high to cause the insulation around the wire to break down. If this happens, the transformer may be permanently damaged. 2024-02-15 B-03b Electrical Fundamentals CASA Part 66 - Training Materials Only Page 204 of 284 The power-handling capacity of a transformer depends on its ability to dissipate heat. If the heat can safely be removed, the power-handling capacity of the transformer can be increased. This is sometimes accomplished by immersing the transformer in oil or by the use of cooling fins. The power-handling capacity of a transformer is measured in either the volt-amperes or watts. Two common power generator frequencies (60 Hz and 400 Hz) have been mentioned, but the effect of varying frequency has not been discussed. If the frequency applied to a transformer is increased, the inductive reactance of the windings is increased, causing a greater AC voltage drop across the windings and a lesser voltage drop across the load. However, an increase in the frequency applied to a transformer should not damage it. But, if the frequency applied to the transformer is decreased, the reactance of the windings is decreased and the current through the transformer winding is increased. If the decrease in frequency is enough, the resulting increase in current will damage the transformer. For this reason, a transformer may be used at frequencies above its normal operating frequency, but not below that frequency. Aviation Australia Transformer power and frequency ratings 2024-02-15 B-03b Electrical Fundamentals CASA Part 66 - Training Materials Only Page 205 of 284 Auto-Transformers Auto-Transformer Configuration It is not necessary in a transformer for the primary and secondary to be separate and distinct windings. In what is known as an auto-transformer, a single coil of wire is 'tapped' to produce what is electrically a primary and secondary winding. The voltage across the secondary winding has the same relationship to the voltage across the primary that it would have if they were two distinct windings. Aviation Australia Adjustable auto-transformer schematic Auto-transformers may also have an adjustable tap which will provide a variable-output voltage. These auto-transformers are usually referred to by their brand name, Variac. The movable tap in the secondary is used to select a value of output voltage, either higher or lower than Ep, within the range of the transformer. That is, when the tap is at point A, Es is less than Ep; when the tap is at point B, Es is greater than Ep. If a voltage of 200 V is applied between points B and C, then a secondary voltage of 100 V would be available from A and B. 300 V will be available from points A and C. This is because the primary field resulting from the supply of current through B and C creates not only a back EMF of close to 200 V in the turns between B and C, but also an EMF of 100 V in the turns between A and B. These two EMFs are of the same phase because they are induced in one winding by the same field. They can therefore be added together to give a secondary voltage of 300 V between A and C. Alternately the 100 V induced between A and B can be taken as a secondary. 2024-02-15 B-03b Electrical Fundamentals CASA Part 66 - Training Materials Only Page 206 of 284 Aviation Australia Auto-transformer turns ratio 2024-02-15 B-03b Electrical Fundamentals CASA Part 66 - Training Materials Only Page 207 of 284 Filters (3.16) Learning Objectives 3.16.1 Define the operation and typical uses of low pass filters (Level 1). 3.16.2 Define the operation and typical uses of high pass filters (Level 1). 3.16.3 Define the operation and typical uses of band pass filters (Level 1). 3.16.4 Define the operation and typical uses of band stop filters (Level 1). 3.16.5 Identify the basic characteristics of low pass, high pass, band pass and band stop filters (S). 3.16.6 Define the properties that affect the resonant frequency of a circuit (S). 3.16.7 Identify the purpose of a tuned LCR circuit (S). 2024-02-15 B-03b Electrical Fundamentals CASA Part 66 - Training Materials Only Page 208 of 284 Filter Characteristics Filters Filters are devices that prevent unwanted quantities from passing through a system. A typical example is the car oil filter, which prevents impurities passing into the engine. An electrical filter is similar to the oil filter, but in this case the electrical filter prevents certain frequencies from passing through to the next stage of the circuit. Filters allow you to choose only the desired frequency or band of frequencies and eliminate the unwanted frequencies. The many uses of filters include channel selection in communications, reduction of interference by rejecting unwanted frequencies, and prevention of spurious oscillations. Most electronic equipment contains at least one filter. Filters are classified according to their frequency response characteristics. There are four basic types of filters: Low pass High pass Band pass Band stop. The term band refers to a range of frequencies. Usually, filters pass or reject a band of frequencies rather than a single frequency. Aviation Australia Four basic types of filters characteristics 2024-02-15 B-03b Electrical Fundamentals CASA Part 66 - Training Materials Only Page 209 of 284 The area under the curve is the allowed (passed) band of frequencies. For accurate sound reproduction, a good set of speakers will include: A tweeter A mid-range speaker A woofer. Sub-woofer A low-pass filter, as its name implies, passes low frequencies but rejects high frequencies. The dividing line between the low and high frequencies is referred to as the cut-off frequency and is denoted as fCO.. Below the cut-off frequency, signals pass essentially unaffected, but frequencies above the cut-off frequency are greatly attenuated or reduced. A high-pass filter passes all frequencies that are higher than a given cut-off frequency and rejects frequencies that are lower than the cut-off. Output from the amplifier is fed to the filter card, where the filter splits audio into: High frequencies for tweeters Medium frequencies for mid-range speakers Low frequencies for woofers. Therefore, only the correct range of frequencies is sent to each speaker. 2024-02-15 B-03b Electrical Fundamentals CASA Part 66 - Training Materials Only Page 210 of 284 Aviation Australia Frequency response of various filters The capacitor in the tweeter line likes to pass high frequency, while the inductor in the woofer line likes to pass low frequency. The capacitor and inductor in the mid-range line likes to pass middle frequency. Aviation Australia Filter circuit for speakers 2024-02-15 B-03b Electrical Fundamentals CASA Part 66 - Training Materials Only Page 211 of 284 Typical Use of Filters on Aircraft – Vibration Sensor Filters are used to select frequencies. It is essential to selectively monitor aircraft engine vibration but reject taxi rumble or air turbulence. Vibration sensor (a) 2024-02-15 B-03b Electrical Fundamentals CASA Part 66 - Training Materials Only Page 212 of 284 Aviation Australia Vibration sensor (b) 2024-02-15 B-03b Electrical Fundamentals CASA Part 66 - Training Materials Only Page 213 of 284 Basic Filter Operation Filter Operation The diagrams below show a low pass filter with a cut-off frequency of 1 kHz. Applying a 10 V peak signal at different frequencies, such as 100 Hz, 1 kHz and 10 kHz, will result in differences. Observe the change in the output. In the top diagram, the filter has a 100 Hz signal applied at 10 V peak. The filter allows the entire signal to pass to the output. In reality, some loss of signal will occur due to the way the components are configured within the filter. This will become clearer later on when we look at filter circuits. For now, these losses can be ignored for the purpose of explaining the filter operation. In the centre diagram, a 1 kHz signal is applied to the filter, again at 10 V peak. Notice that the applied signal is at the same frequency as the cut-off frequency (fco), that is, 1 kHz. The output from the filter is still at 1 kHz since filters do not change the frequency, but the amplitude of the signal has been reduced to 7.07 V peak. Some attenuation has taken place within the filter. Refer back to the previous graph associated with a low pass filter, the output voltage starts to reduce before the cut-off frequency is reached. In the bottom diagram, the frequency of the applied signal has been increased to 10 kHz and the input amplitude remains the same at 10 V peak, but this time filter has reduced the amplitude of the output to 1 V peak. 2024-02-15 B-03b Electrical Fundamentals CASA Part 66 - Training Materials Only Page 214 of 284 Aviation Australia Low pass filter frequency responses 2024-02-15 B-03b Electrical Fundamentals CASA Part 66 - Training Materials Only Page 215 of 284 Practical Filters In the shaded area of the ideal curves, frequencies are passed. In the unshaded area, frequencies are rejected. The ideal filters are so selective that the output voltage stops completely (low pass) or starts exactly (high pass) at the cut-off frequency. The difference between those signals that will be passed and those that will be rejected is sharp and definite. In practice, such steep and highly selective curves are impossible to achieve. While the ideal can be approached with special components and techniques, most filters introduce gradual attenuation, or loss, with frequency. For example, the practical or true response curve of the low-pass filter is illustrated below. At high frequencies, above fCO, the output voltage decreases gradually as the frequency increases. Hence, attenuation gradually increases at a nearly constant rate, with frequency. Aviation Australia Low-pass filter frequency response The practical response curve of the high-pass filter in the following figure shows that at low frequencies, before the cut-off, output voltage increases gradually as frequency increases. Attenuation gradually decreases, so the output voltage increases at a nearly constant rate with frequency. 2024-02-15 B-03b Electrical Fundamentals CASA Part 66 - Training Materials Only Page 216 of 284 Aviation Australia High-pass filter frequency response RC Low-Pass Filter There are two basic configurations for a low-pass filter: RC or RL. The RC low-pass filter uses a series resistor and a shunt capacitor. Aviation Australia Circuit for an RC low-pass filter In the case of a voltage divider across an AC source, the output is always less than the input; therefore, the filter is also an attenuator. Because inductors and capacitors are frequency sensitive, the output voltage varies with frequency. The inductive reactance (XL ) is proportional to frequency, whereas the capacitive reactance is inversely proportional to frequency. If the capacitive reactance (XC ) is high at low frequencies (compared to the resistance), most of the input voltage appears across the capacitor. However, as the frequency increases, XC decreases. More and more voltage appears across the resistor, while less appears across the capacitor. 2024-02-15 B-03b Electrical Fundamentals CASA Part 66 - Training Materials Only Page 217 of 284 RL Low-Pass Filter Suppose we have an RL low-pass filter that uses a series inductor and a shunt resistor. The inductive reactance (XL ) in the circuit varies proportionately with frequency. At low frequencies, XL is very low (compared to the resistor), so most of the input voltage appears across the resistor. However, as frequency increases, XL increases. More and more voltage appears across the inductor, while less appears across the resistor. This circuit also rolls off the higher frequencies. Aviation Australia Circuit for an RL low-pass filter Summary of Low-Pass Filters In general, an RC low-pass filter will do exactly the same job as an RL low-pass filter with the same cut-off frequency. The roll-off rates will also be the same. However, RC low-pass filters are usually easier to use and less expensive than RL low-pass filters because capacitors come in a wider range of values, are generally smaller than inductors and are cheaper to produce. Aviation Australia Physical filter electronic components 2024-02-15 B-03b Electrical Fundamentals CASA Part 66 - Training Materials Only Page 218 of 284 High-Pass Filter Operation Introduction to High-Pass Filter Operation A high-pass filter is a frequency-selective circuit that passes all frequencies above the cut-off frequency with little or no attenuation, while it rejects those signals below the cut-off frequency. Such filters are easily constructed with various combinations of resistance, capacitance and inductance. Aviation Australia Frequency response of a high-pass filter RC High-Pass Filter Suppose we have an RC high-pass filter with a series capacitor and a resistor that form a voltage divider across the generator. The filter output is taken from across the resistor. Aviation Australia Circuit for an RC high-pass filter 2024-02-15 B-03b Electrical Fundamentals CASA Part 66 - Training Materials Only Page 219 of 284 At frequencies below the cut-off frequency, the capacitive reactance (XC ) is very high and most of the generator voltage will be across the capacitor. Very little voltage will appear across the output resistor. However, as the frequency increases, XC decreases. Less voltage is dropped across the capacitor and more and more voltage appears across the resistor, allowing the higher frequencies to pass. RL High-Pass Filter Suppose we have an RL high-pass filter with a series resistor and an inductor that form a voltage divider across the generator. Output voltage is taken from across the inductor. Aviation Australia Circuit for a RL high-pass filter At frequencies below the cut-off frequency, the inductive reactance (XL ) is very low and most of the generator voltage will be across the resistor. Very little voltage will appear across the output inductor. However, as the frequency increases, XL increases. Less voltage is dropped across the resistor and more and more voltage appears across the inductor, allowing the higher frequencies to pass. The output of an RC high-pass filter, at the cut-off frequency (fCO), is 70.7% or 3 dB down from the maximum applied voltage. Performance of RC and RL high-pass filters is typically identical. Above the cut-off frequency, high-pass filters pass signals with little attenuation. 2024-02-15 B-03b Electrical Fundamentals CASA Part 66 - Training Materials Only Page 220 of 284 Summary of High-Pass Filters The performance of RC and RL high-pass filters is generally identical. At frequencies above the cutoff frequency, both RC and RL high-pass filters pass signals with little attenuation. At the cut-off frequency, the attenuation will be 3 dB. At frequencies below the cut-off frequency, the attenuation increases at a rate of 6 dB per octave or 20 dB per decade, which is the same for RC and RL low-pass filters. Aviation Australia High-pass characteristic curve (top right) RC and RL low- and high-pass filters are made with various combinations of inductors, capacitors and resistors. In each case, the filter is really a voltage divider made of two components. One component is a resistor and the other is a frequency - varying component such as an inductor or a capacitor. 2024-02-15 B-03b Electrical Fundamentals CASA Part 66 - Training Materials Only Page 221 of 284 Aviation Australia Summary of circuits and frequency responses - 1 Aviation Australia Summary of circuits and frequency responses - 2 2024-02-15 B-03b Electrical Fundamentals CASA Part 66 - Training Materials Only Page 222 of 284 Because the output voltage from each filter is tapped from a voltage divider, the output voltage will be less than the input voltage. As the supply frequency changes, the circuit reactance changes, and consequently the voltage division ratio changes. This causes the output voltage to vary. By selecting the appropriate values of resistance and capacitance for the voltage divider, filters can be designed so that they pass or eliminate the desired frequencies. 2024-02-15 B-03b Electrical Fundamentals CASA Part 66 - Training Materials Only Page 223 of 284 Series and Parallel Resonance Series Resonance As you have seen previously, inductive and capacitive reactances in an LCR circuit vary with frequency. An increase in the frequency causes inductive reactance (XL) to increase and capacitive reactance (XC ) to decrease. A decrease in the frequency causes the inductive reactance to decrease and the capacitive reactance to increase. The condition in which the inductive reactance equals the capacitive reactance is called resonance. For every combination of L and C, there is only one frequency (in both series and parallel circuits) that causes XL to exactly equal XC. This frequency is known as the resonant frequency. When the resonant frequency is fed to a series or parallel circuit, XL becomes equal to XC and the circuit is said to be resonant to that frequency and is totally resistive. The circuit is now called a resonant circuit; resonant circuits are tuned circuits. To describe the principles of series resonance we will use the representative series resonant circuit. Aviation Australia Series LCR circuit 2024-02-15 B-03b Electrical Fundamentals CASA Part 66 - Training Materials Only Page 224 of 284 Circuit Operation Let us now look at the curves which show how XL and XC vary with frequency in a series resonant circuit. The resonant frequency (fr) is the frequency where the magnitude of XL equals the magnitude of XC. Aviation Australia Impedance response for both L and C components It can be seen that below the resonant frequency (fr ), XC is larger than XL, so the voltage across the capacitor is larger than the voltage across the inductor and the series LCR circuit will act capacitively. Above the resonant frequency (fr), XL is larger than XC, so voltage across the inductor is larger than the voltage across the capacitor and the series LCR circuit will act inductively. 2024-02-15 B-03b Electrical Fundamentals CASA Part 66 - Training Materials Only Page 225 of 284 Parallel Resonance The resonant frequency (fr) of a parallel resonant circuit is calculated with the same formula used for series resonant circuits: 1 fR = 2π√ LC An ideal parallel resonant LC circuit is illustrated below. You will notice that the source voltage is applied across each component. Aviation Australia Parallel LC circuit (tank circuit) 2024-02-15 B-03b Electrical Fundamentals CASA Part 66 - Training Materials Only Page 226 of 284 Tuned Circuits Each LCR circuit responds to resonant frequency differently than it does to any other frequency. Because of this, an LCR circuit has the ability to separate frequencies. For example, suppose the TV or radio station you want to see or hear is broadcasting at the resonant frequency. The LC 'tuner' in your set can divide the frequencies, picking out the resonant frequency and rejecting the other frequencies. Thus, the tuner selects the station you want and rejects all other stations. If you decide to select another station, you can change the frequency by tuning the resonant circuit to the desired frequency. 1. In a series resonant circuit, at resonance, the impedance is resistive and a low value (usually the value of the resistance of the wire in the coil). 2. In a parallel resonant circuit (tank circuit), at resonance, the impedance is resistive and a high value (depending on the values of L and C chosen, it can be almost infinite). If you remember these two facts about tuned circuits, the world of filters is simple. Filters are used to select frequencies 2024-02-15 B-03b Electrical Fundamentals CASA Part 66 - Training Materials Only Page 227 of 284 Resonant Circuits as Filters Resonant circuits can be made to serve as filters. Series LC circuits (resonant) offer: Minimum opposition to current flow at frequencies at or near resonant frequency Maximum opposition to current flow at all other frequencies. Parallel LC circuits (resonant) offer: Maximum opposition to current flow at frequencies at or near resonant frequency Minimum opposition to current flow at all other frequencies. Using these two concepts, band-pass and band-stop filters can be constructed. The band-pass filter and the band-stop filter are two common types of filters that use resonant circuits. Aviation Australia Band-pass and band-stop responses 2024-02-15 B-03b Electrical Fundamentals CASA Part 66 - Training Materials Only Page 228 of 284 Band-Pass Filter Introduction to Band-Pass Filter Band-pass and band-stop filters use resonant circuits that you have seen in previous topics. If you have a good understanding of resonant circuits, the operation of band-stop and band-pass filters will be easy for you to grasp. These filters are designed to either reject or pass a narrow range of frequencies and due to this characteristic are widely used in both communication and navigation equipment. A band-pass filter is a circuit that allows a selected range of frequencies to pass, while frequencies above and below this range are greatly attenuated. The two basic configurations for a band-pass filter use either a series resonant LC network or a parallel resonant LC network. Aviation Australia Band-stop characteristic curve (bottom right) 2024-02-15 B-03b Electrical Fundamentals CASA Part 66 - Training Materials Only Page 229 of 284 Simple Band-Pass Filter In the circuit of figure view (A), the series LC circuit acts as a band-pass filter. It passes currents with frequencies at or near its resonant frequency, and opposes the passage of all currents with frequencies outside this band. Aviation Australia Simple series band-pass (A) View (B) is the parallel-LC circuit. If the parallel LC circuit is tuned to the same frequency as the series LC circuit, it will provide a path for all currents having frequencies outside the limits of the frequency band passed by the series-resonant circuit. You may remember from resonant circuits, series LC resonant circuits offer minimum impedance at resonance, thus passing maximum current. Conversely, parallel LC resonant circuits offer maximum impedance at resonance, thus passing minimum current. Aviation Australia Simple parallel band-pass filter (B) The simplest type of band-pass filter is formed by connecting the two LC circuits as shown in view (C). The upper and lower frequency limits of the filter action are filter cut-off points. 2024-02-15 B-03b Electrical Fundamentals CASA Part 66 - Training Materials Only Page 230 of 284 Aviation Australia Combination series-parallel band-pass filter (C) Series LC resonant circuits offer minimum impedance at resonance, thus passing maximum current. Conversely, parallel LC resonant circuits offer maximum impedance at resonance, thus passing minimum current. Should any frequencies be delivered to the circuit that are not within the selected bandwidth, not only will the series LC network block them, but the parallel LC network will shunt them away from the load. Aviation Australia Frequency response of a band-pass filter 2024-02-15 B-03b Electrical Fundamentals CASA Part 66 - Training Materials Only Page 231 of 284 Band-Stop Filter Introduction to Band-Stop Filter A band-stop filter is a circuit that rejects or greatly attenuates signals over a narrow frequency range. It is also known as a notch filter or band elimination filter. As with the band pass filter there are two basic configurations for a band stop filter. These configurations use either a series resonant LC network or a parallel resonant LC network. Aviation Australia Band-stop characteristic curve (bottom right) 2024-02-15 B-03b Electrical Fundamentals CASA Part 66 - Training Materials Only Page 232 of 284 Simple Band Stop Filters A band-stop filter circuit is used to block the passage of current for a narrow band of frequencies, while allowing current to flow at all frequencies above or below this band. Since the purpose of the band-stop filter is directly opposite that of a band-pass filter, the relative positions of the resonant circuits in the filter are interchanged. The parallel LC circuit shown on the following page view (A), act as a band-reject filter, blocking the passage of currents with frequencies at or near resonant frequency and passing all currents with frequencies outside this band. If a series LC circuit shown in view (B), is tuned to the same frequency as the parallel circuit, it can act as a bypass for the band of rejected frequencies. Then, the simplest type of band-reject filter is obtained by connecting the two circuits as shown in view (C). Aviation Australia Simple series (A) and parallel band-stop filters (B) © Aviation Australia Combination series-parallel band-stop filter (C) 2024-02-15 B-03b Electrical Fundamentals CASA Part 66 - Training Materials Only Page 233 of 284 As remembered from resonant circuits (at resonance): Series LC circuits offer minimum impedance, thus passing maximum current. Parallel LC circuits offer maximum impedance, thus passing minimum current. For frequencies within the selected bandwidth: Blocked by parallel LC network, and Passed by series LC network (all signals shunted away from load). For frequencies not within the selected bandwidth: Aviation Australia Frequency response of a band-stop filter 2024-02-15 B-03b Electrical Fundamentals CASA Part 66 - Training Materials Only Page 234 of 284 AC Generators (3.17) Learning Objectives 3.17.1 Describe the rotation of loop in a magnetic field and the waveform produced by an AC generator (Level 2). 3.17.2.1 Explain the operation and construction of a revolving armature type AC generator and it's relative disadvantages (Level 2). 3.17.2.2 Explain the operation and construction of a revolving field type AC generator (Level 2). 3.17.3 Describe constructional features and typical uses of single phase, two-phase and three-phase alternators (Level 2). 3.17.4 Differentiate between three-phase star and delta connections and their relative advantages (Level 2). 3.17.5 Describe the operation and construction of permanent magnet generators (Level 2). 3.17.6.1 Explain the purpose of a constant speed drive unit (S). 3.17.6.2 Describe the construction of an integrated drive generator (S). 2024-02-15 B-03b Electrical Fundamentals CASA Part 66 - Training Materials Only Page 235 of 284 AC Generator Theory The AC Generator Most of the electrical power used aboard aircraft is AC. As a result, the AC generator is the most important means of producing electrical power. AC generators, generally called alternators, vary greatly in size depending on the load to which they supply power. For example, the alternators in use at hydroelectric plants, such as Wivenhoe Dam (west of Brisbane), are tremendous in size, generating around 240 MW at very high voltage levels. Another example is the alternator in a typical automobile, which is very small by comparison. It weighs only a few pounds and produces between 100 and 200 W of power, usually at a potential of 12 V. Example of a small automotive alternator Many of the terms and principles covered in this topic will be familiar to you. They are the same as those covered in the topic on DC generators. You are encouraged to refer back as needed, and to refer to any other source that will help you master this topic. Regardless of size, all electrical generators, whether DC or AC, depend on the principle of magnetic induction. An EMF is induced in a coil as a result of a coil cutting through a magnetic field or a magnetic field cutting through a coil. 2024-02-15 B-03b Electrical Fundamentals CASA Part 66 - Training Materials Only Page 236 of 284 As long as there is relative motion between a conductor and a magnetic field, a voltage will be induced in the conductor. The part of a generator that produces the magnetic field is called the field. The part in which the voltage is induced is called the armature. For relative motion to take place between the conductor and the magnetic field, all generators must have two mechanical parts: a rotor and a stator. The rotor is the part that rotates; the stator is the part that remains stationary. In a DC generator, the armature is always the rotor. In alternators, the armature may be either the rotor or the stator. Three-phase alternator rotation and waveform produced The following sections discuss the different types of alternators and the relevance of the waveforms produced. 2024-02-15 B-03b Electrical Fundamentals CASA Part 66 - Training Materials Only Page 237 of 284 Alternator Types There are two types of alternators: 1. Revolving armature type – the rotor is the armature and the stator is the field. 2. Revolving field type – the rotor is the field and the stator is the armature; used almost exclusively in aircraft. Alternator types 2024-02-15 B-03b Electrical Fundamentals CASA Part 66 - Training Materials Only Page 238 of 284 Revolving-Armature Alternator The revolving-armature alternator is similar in construction to the DC generator in that the armature rotates in a stationary magnetic field. Rotating armature alternator In the DC generator, the EMF generated in the armature windings is converted from AC to DC by means of the commutator. In the alternator, the generated AC is brought to the load unchanged by means of slip rings. The rotating armature is found only in alternators of low power rating and is generally not used to supply electric power in large quantities. Note: The AC output is via slip rings. Disadvantages of the Rotating-Armature Configuration The revolving armature must be very strongly constructed to withstand centrifugal loads. A rotating-armature alternator requires slip rings and brushes to connect the armature output voltage and current to the load. The brushes and slip rings must be large enough to pass the entire load current. They are difficult to insulate against the relatively high alternator AC output voltage, resulting in arc-over and short circuits. 2024-02-15 B-03b Electrical Fundamentals CASA Part 66 - Training Materials Only Page 239 of 284 Rotating-Field Alternators High-voltage alternators (115-V AC) are usually of the rotating-field type. Rotating-field alternators are better suited for higher power applications because their brushes and slip rings are only required to carry field current (at relatively low values of DC voltage and current). The revolving-field type alternator has a stationary armature winding (stator) and a light-weight rotating field winding (rotor). The armature is connected directly to the load without sliding contacts in the load circuit. Large cross-section (low resistance) conductors can be used in the armature because it is not subject to centrifugal loads. Rotating field alternator 2024-02-15 B-03b Electrical Fundamentals CASA Part 66 - Training Materials Only Page 240 of 284 Permanent Magnet Generators Permanent Magnet Generators (PMGs) are also called engine-dedicated alternators or permanent magnet alternators. A PMG consists of a high-energy rare-earth permanent magnet rotor that rotates within a steel stator core wound with high-temperature insulated copper windings. Typically, it provides an AC output with a frequency and power proportional to the speed of rotation. Permanent magnetic generators As there is no requirement for power to be supplied to the field, there is no requirement for brushes or slip rings. Depending on the conditioning electronics downstream, PMGs can be designed to operate in either voltage mode (open circuit) or current mode (closed circuit). They are crucial components for providing power to the ignition exciter, FADECs (Full Authority Digital Engine Control) or other accessories on gas turbine engines. 2024-02-15 B-03b Electrical Fundamentals CASA Part 66 - Training Materials Only Page 241 of 284 Brushless Alternators The AC alternators used in large jet-powered aircraft are of the brushless type and are usually air cooled. Since the brushless alternators have no current flow between brushes or slip rings, they are very efficient at high altitudes, where brush arcing is often a problem. As discussed earlier, alternator brushes are used to carry current to the rotating electromagnet. However, in a brushless alternator, current is induced into the field coil through an exciter. A brushless alternator consists of three separate fields: a permanent magnetic field, an exciter field and a main output field. Schematic of a brushless generator The permanent magnets furnish the magnetic flux to start the generator, producing an output before field current flows. The magnetism produced by these magnets induces voltage into an armature that carries the current to a generator control unit, or GCU. Here, the AC is rectified and sent to the exciter field winding. The exciter field then induces voltage into the exciter output winding. The output from the exciter is rectified by six silicon diodes, and the resulting DC flows through the output field winding. From here, voltage is induced into the main output coils. The permanent magnet, exciter output winding, six diodes and output field winding are all mounted on the generator shaft and rotate as a unit. The three-phase output stator windings are wound in slots that are in the laminated frame of the alternator housing. The main output stator winding ends of a brushless alternator are connected in the form of a Y, and in the case of the diagram above, the neutral winding is brought to the outside of the housing along with the three-phase windings. 2024-02-15 B-03b Electrical Fundamentals CASA Part 66 - Training Materials Only Page 242 of 284 The GCU actually monitors and regulates the main generator's output by controlling the amount of current that flows into the exciter field. For example, if additional output is needed, the GCU increases the amount of current flowing to the exciter field winding, which in turn increases the exciter output. A higher exciter output increases the current flowing through the main generator field winding, thereby increasing alternator output. Since brushless alternators utilise a permanent magnet, there is no need to flash the field. In addition, the use of a permanent magnet eliminates the need to carry current to a rotating assembly through brushes. Sinusoidal Sine Wave The sinusoidal sine wave shows the value of induced EMF at each instant of time during a 360° rotation of the loop. A sinusoidal sine wave is a representation of induced EMF for a single coil rotated through a uniform magnetic field at a constant speed. Alternating current (AC), unlike direct current (DC), flows first in one direction and then in the opposite direction. DC amperage is constant. The most common AC waveform is a sine (or sinusoidal) waveform. When a conductor is cutting lines of flux quickly, it produces a greater force to drive electrons, and hence a greater potential difference. This is represented by the sine wave peaking when the wires are moving directly across (perpendicular to) the face of the magnetic field. Aviation Australia Sinusoidal wave form Each cycle of the sine wave consists of two identically shaped variations in voltage. The variations that occur during the time considered the positive alternation (above the horizontal line) indicate current movement in one direction. The direction of current movement is determined by the generated terminal voltage polarities. 2024-02-15 B-03b Electrical Fundamentals CASA Part 66 - Training Materials Only Page 243 of 284 The variations that occur during the time considered the negative alternation (below the horizontal line) indicate current movement in the opposite direction because the generated voltage terminal polarities have reversed. The distance from zero to the maximum value of each alternation is the amplitude. The amplitude of the positive alternation and the amplitude of the negative alternation are the same. A sine wave is a symmetrical waveform that varies equally around a fixed level and can be a representation of either voltage or current. The sine wave is an alternating (swings both positive and negative) waveform and is most commonly identified as the AC waveform. It bears a direct relationship to circular rotation. With AC, electrons flow first in one direction, and then in the other. Both current and voltage vary continuously. The graphic representation for AC is a sine wave, which can represent current or voltage. Two axes are used to depict a sine wave. The vertical axis represents the magnitude and direction of current or voltage. The horizontal axis represents time or angle of rotation in degrees. Aviation Australia Graph of AC signal When the waveform is above the time axis, current is said to be flowing in a positive direction. When the waveform is below the time axis, current is said to be flowing in a negative direction. A complete cycle occurs in 360°, half of which is positive and half negative. As the armature rotates through the magnetic field, at the initial position of 0°, the armature conductors are moving parallel to the magnetic field. They are not cutting through any magnetic lines of flux. Therefore, no voltage is induced. As the armature rotates from 0° to 90°, the conductors cut through more and more lines of flux. Induced voltage builds to a maximum in the positive direction. 2024-02-15 B-03b Electrical Fundamentals CASA Part 66 - Training Materials Only Page 244 of 284 Graphs showing 270 degrees of rotation As the generator continues to rotate from 90° to 180°, the armature cuts fewer and fewer lines of flux. The induced voltage decreases from a maximum positive value to zero. The armature continues to rotate from 180° to 270°. The conductors cut more and more lines of flux, but in the opposite direction. The voltage is induced in the negative direction, building up to a maximum at 270°. 2024-02-15 B-03b Electrical Fundamentals CASA Part 66 - Training Materials Only Page 245 of 284 Alternator Phase Types Single-Phase Alternators A generator that produces a single, continuously alternating voltage is known as a single-phase alternator. The stator (armature) windings are connected in series. The individual voltages, therefore, add together to produce a single-phase AC voltage. Aviation Australia Single phase output from a generator The definition of phase as you learned it while studying AC circuits may be less useful here. Remember, 'out of phase' meant 'out of time'. Now, it may be easier to think of the word phase as meaning voltage, as in single voltage. The need for a modified definition will be easier to see as we go along. Phase is often replaced with Ø in mathematical circuit analysis. Thus, for example, 3-Phase can be represented as 3-Ø. Single-phase alternators are found in many applications. They are most often used when the loads being driven are relatively light. The reason for this will be more apparent as we get into multiphase alternators (also called polyphase). Power that is used in homes, shops and ships to operate portable tools and small appliances is singlephase power. Single-phase power alternators always generate single-phase power. However, all single-phase power does not come from single-phase alternators. 2024-02-15 B-03b Electrical Fundamentals CASA Part 66 - Training Materials Only Page 246 of 284 Two-Phase Alternators Two-phase alternators have two or more single-phase windings spaced symmetrically around the stator so that the AC voltage induced in one is 90° out of phase with the other. These windings are electrically separate from each other so that when one winding is cutting the maximum number of flux lines, the other is cutting no flux lines. A two-phase alternator is designed to produce two completely separate voltages. Each voltage, by itself, may be considered a single-phase voltage. Each is generated completely independent of the other. Certain advantages are gained. Aviation Australia Two-phase output In a simplified two-pole, two-phase alternator, the windings of the two phases are physically at right angles (90°) to each other. You would expect the outputs of each phase to be 90° apart, which they are. The graph shows the two phases 90° apart, with A leading B. There will always be 90° between the phases of a two-phase alternator. This is by design. The two-phase alternator works via the same principle as a single-phase alternator. Each output is a single-phase voltage, just as if the other did not exist. The rotor is identical to that used in the single-phase alternator. The stator consists of two single-phase windings completely separated from each other. Each singlephase winding is made up of two coils connected in series so their voltages add. 2024-02-15 B-03b Electrical Fundamentals CASA Part 66 - Training Materials Only Page 247 of 284 In the left-hand schematic, the rotor poles are opposite the windings of Phase A. Therefore, the voltage induced in Phase A is maximum, and the voltage induced in Phase B is zero. As the rotor continues rotating counterclockwise, it moves away from the A windings and approaches the B windings. As a result, the voltage induced in Phase A decreases from its maximum value, and the voltage induced in Phase B increases from zero. In the right-hand schematic, the rotor poles are opposite the windings of Phase B. Now the voltage induced in Phase B is maximum, whereas the voltage induced in Phase A has dropped to zero. Notice that a 90° rotation of the rotor corresponds to one quarter of a cycle. The waveform picture shows the voltages induced in phase A and B for one cycle. The two voltages are 90° out of phase. The two outputs, A and B, are independent of each other. Two-Phase Three-Wire Alternator Now, look at the smaller schematic diagram in bottom left corner. Aviation Australia Two-phase three-wire output Only three connections have been brought out from the stator. Electrically, this is the same as the large diagram above. Instead of being connected at the output terminals, the B1-A2 connection was made internally when the stator was wired. A two-phase alternator connected in this manner is called a two-phase, three-wire alternator. 2024-02-15 B-03b Electrical Fundamentals CASA Part 66 - Training Materials Only Page 248 of 284 The large schematic shows four separate wires brought out from the A and B stator windings. This is the same as in previous alternator. Notice, however, that the dotted wire now connects one end of B1 to one end of A2. The effect of making this connection is to provide a new output voltage. This sine-wave voltage, C in the picture, is larger than either A or B. It is the result of adding the instantaneous values of phase A and phase B. For this reason it appears exactly half way between A and B. Therefore, C must lag A by 45° and lead B by 45°, as shown in the small vector diagram. The three-wire connection makes possible three different load connections: A and B (across each phase), and C (across both phases). The output at C is always 1.414 times the voltage of either phase. These multiple outputs are additional advantages of the two-phase alternator over the single-phase type. The two-phase alternator is seldom seen in actual use. Three-Phase Alternators A three-phase or polyphase circuit is used in most aircraft alternators. The three-phase alternator, as the name implies, has three single-phase windings spaced such that the voltage induced in any one phase is displaced by 120° from the other two. Three-phase output A schematic diagram of a three-phase stator showing all the coils becomes complex, and it is difficult to see what is actually happening. 2024-02-15 B-03b Electrical Fundamentals CASA Part 66 - Training Materials Only Page 249 of 284 View A of the simplified schematic above shows all the windings of each phase lumped together as one winding. The rotor is omitted for simplicity. The voltage waveforms generated across each phase appear on a graph as phase-displaced 120° from each other. The three-phase alternator is made up of three single-phase alternators whose generated voltages are out of phase by 120°. The three phases are independent of each other. 3-Ø Star and Delta Connections Rather than having six leads coming out of the three-phase alternator, the same leads from each phase may be connected together to form a star connection or more commonly referred to as a wye (Y) connection. It is called a wye connection because, without the neutral, the windings appear as the letter Y, sometimes, sideways or upside-down. I LINE = I PHASE A A A A 260V 100A AV = 450V 100A 260V 100A C E LINE = 1.73 x E PHASE AV = 450V 100A B B 260V 100A AV = C WYE-Connected Winding Values C B 450V 100A C N Aviation Australia Star or Y connection The neutral connection is brought out to a terminal when a single-phase load must be supplied. Single-phase voltage is available from neutral to A, neutral to B, and neutral to C. In a three-phase, Y-connected alternator, the total voltage, or line voltage, across any two of the three line leads is the vector sum of the individual phase voltages. Each line voltage is 1.73 times one of the phase voltages. Because the windings form only one path for current flow between phases, the line and phase currents are the same (equal). A three-phase stator can also be connected so that the phases are connected end-to-end; it is now delta-connected (because it looks like the Greek letter delta, Δ). 2024-02-15 B-03b Electrical Fundamentals CASA Part 66 - Training Materials Only Page 250 of 284 In the delta connection, line voltages are equal to phase voltages, but each line current is equal to 1.73 times the phase current. Aviation Australia Delta connection Both the wye and the delta connections are used in alternators. 2024-02-15 B-03b Electrical Fundamentals CASA Part 66 - Training Materials Only Page 251 of 284 Formula for Calculating Power in 3-Ø Circuits To calculate power consumed in a 3-Ø circuit, use: P = √ 3 × V × I × Cosineθ where V and I are assumed to be line values and cos θ is the power factor. To calculate power in kilo volt-amps (kVA; Apparent Power): P ower (kV A) = I Line × V Line × 1.732 1000 To calculate power in kilowatts (kW; True Power): P ower (kW ) = I Line × V Line × 1.732 × pf 1000 Remember that line values are as connected from phase to phase – one line. AC generators are typically power rated in kVA. To calculate the power rating of the following AC generator: Aviation Australia WYE connection example 200 × (115 × 1.732) × 1.732 P ower (kV A) = 1000 P ower (kV A) = 69 kV A 2024-02-15 B-03b Electrical Fundamentals CASA Part 66 - Training Materials Only Page 252 of 284 Phase Sequence When the rotor rotates, if the voltages in each winding reach their positive peak values in order of A, B, C, then the phase rotation is ABC. If Phases B and C are transposed, then the phase rotation becomes ACB. This causes three-phase motors to rotate in the reverse direction. Aviation Australia Phase sequence of a three-phase signal When connected to a 3-Ø load, the phase sequence is very important, particularly with rotating machinery (AC motors), as direction of rotation can be affected. 2024-02-15 B-03b Electrical Fundamentals CASA Part 66 - Training Materials Only Page 253 of 284 Advantages and Applications of Three-Phase Connections Star Delta Similar ends connected Dissimilar ends connected For balanced or unbalanced loads More suited to balanced loads V line = √3 V phase V line = V phase I line = I phase I line = √3 I phase Two values of voltage available One common voltage available Common connection available for earthing No common earthing point V line leads V phase by 30° I line leads I phase by 30° Suited to long-distance power transmissions Suited to locally operated machinery Alternator Frequency Control The output frequency of alternator voltage depends on the speed of rotation of the rotor and the number of poles. The faster the rotational speed, the higher the frequency. The lower the rotational speed, the lower the frequency. The more poles there are on the rotor, the higher the frequency is for a given speed. Factors determining alternator AC frequency 2024-02-15 B-03b Electrical Fundamentals CASA Part 66 - Training Materials Only Page 254 of 284 When a rotor has rotated through an angle such that two adjacent rotor poles (a north and a south pole) have passed one winding, the voltage induced in that winding has varied through one complete cycle. For a given frequency, the more pairs of poles there are, the lower the speed of rotation. A two-pole generator must rotate at four times the speed of an eight-pole generator to produce the same frequency of generated voltage. The frequency of any AC generator in hertz (Hz), which is the number of cycles per second, is related to the number of poles and the speed of rotation, as expressed by the equation: NP f = 120 P is the number of poles N is the speed of rotation in revolutions per minute (rpm) 120 is a constant to allow for the conversion of minutes to seconds and from poles to pairs of poles. Example The output frequency of an alternator with eight poles driven at 6000 rpm is 400 Hz. A six-pole alternator must be driven at 8000 rpm to have a 400 Hz output. 2024-02-15 B-03b Electrical Fundamentals CASA Part 66 - Training Materials Only Page 255 of 284 AC Generator Aircraft Connections Constant Speed Drive To provide a constant frequency as engine speed varies and maintain a uniform frequency between multiple generators, most AC generators are connected to a Constant Speed Drive unit, or CSD. Although CSDs come in a variety of shapes and sizes, their principle of operation is essentially the same. The drive unit consists of an engine-driven axial-piston variable-displacement hydraulic pump that supplies fluid to an axial-piston hydraulic motor. The motor then drives the generator. The displacement of the pump is controlled by a governor which senses the rotational speed of the AC generator. The governor action holds the output speed of the generator constant and maintains an AC frequency at 400 Hz, plus or minus established tolerances. The term CSD is most commonly applied to hydraulic transmissions found on the accessory drives of gas turbine engines, such as aircraft jet engines. On modern aircraft, the CSD is often combined with a generator into a single unit known as an integrated drive generator (IDG). Image by Daderot CSD for Boeing 727 2024-02-15 B-03b Electrical Fundamentals CASA Part 66 - Training Materials Only Page 256 of 284 Integrated Drive Generator Some modern jet aircraft produce AC with a generator called an Integrated Drive Generator, or IDG. An IDG differs from a CSD in that it contains both the CSD and the AC generator in the same housing. This is an example of a modern integrated drive generator (IDG). The term generator is still used even though IDGs are actually brushless alternators. Example of an IDG 2024-02-15 B-03b Electrical Fundamentals CASA Part 66 - Training Materials Only Page 257 of 284 AC Motors (3.18) Learning Objectives 3.18.1.1 Describe the construction, operation and characteristics of AC synchronous motors (Level 2). 3.18.1.2 Describe the construction, operation and characteristics of AC induction motors (Level 2). 3.18.1.3 Describe the construction, operation and characteristics of AC motors both single and polyphase (Level 2). 3.18.2.1 Describe methods of speed control (Level 2). 3.18.2.2 Describe methods of controlling direction of rotation (Level 2). 3.18.3.1 Describe methods of producing a rotating field: capacitor (Level 2). 3.18.3.2 Describe methods of producing a rotating field for an inductor (Level 2). 3.18.3.2 Describe methods of producing a rotating field: shaded or split pole (Level 2). 2024-02-15 B-03b Electrical Fundamentals CASA Part 66 - Training Materials Only Page 258 of 284 AC Motor Theory I Advantages of AC Motors There are advantages to the use of AC motors besides the wide availability of AC power. In general, AC motors cost less than DC motors. Most types of AC motors do not use brushes and commutators. This eliminates many problems of maintenance and wear. It also eliminates the problem of dangerous sparking. An AC motor is particularly well suited for constant-speed applications because its speed is determined by the frequency of the AC voltage applied to the motor terminals. Industry builds AC motors in different sizes, shapes and ratings for many different types of jobs. These motors are designed for use with either polyphase or single-phase power systems. Induction motors, single-phase or polyphase, whose rotors are energised by induction, are the most commonly used AC motors. Synchronous motors, for the purposes of this subject, may be considered polyphase motors of constant speed whose rotors are energised with DC voltage. Exploded view of an AC induction motor 2024-02-15 B-03b Electrical Fundamentals CASA Part 66 - Training Materials Only Page 259 of 284 Three-Phase Rotating Fields The three-phase induction motor also operates on the principle of a rotating magnetic field. The stator's windings can be connected to a three-phase AC input and have a resultant magnetic field that rotates. The upper and lower left figures in the image show the individual windings for each phase. The lower right figure shows how the three phases are tied together in a Y-connected stator. Aviation Australia Three-phase windings The dot in each diagram indicates the common point of the Y-connection. The individual phase windings are equally spaced around the stator. This places the windings 120° apart. Use the left-hand rule for determining the electromagnetic polarity of the poles at any given instant. In applying the rule to the coils in the image, consider that current flows towards the terminals for positive voltages, and away from the terminals for negative voltages. 2024-02-15 B-03b Electrical Fundamentals CASA Part 66 - Training Materials Only Page 260 of 284 Three-Phase Rotation Analysis Three-phase rotation The results of this analysis are shown for voltage points 1 through 7. At point 1, the magnetic field in coils 1-1A is at a maximum with polarities as shown. At the same time, negative voltages are being felt in the 2-2A and 3-3A windings. These create weaker magnetic fields, which tend to aid the 1-1A field. At point 2, maximum negative voltage is being felt in the 3-3A windings. This creates a strong magnetic field which, in turn, is aided by the weaker fields in 1-1A and 2-2A. At each point of the rotation, it can be seen that the resultant magnetic field is rotating in a clockwise direction. When the three-phase voltage completes one full cycle (point 7), the magnetic field has rotated through 360°. 2024-02-15 B-03b Electrical Fundamentals CASA Part 66 - Training Materials Only Page 261 of 284 Rotor Movement To explain rotor movement (using the diagram above), let us assume we can mount a bar magnet in the centre of the stator so that it is free to rotate. Let us also assume that the bar magnet is aligned so that its south pole is opposite the north pole of the stator field. You can see that this alignment is natural. Unlike poles attract, and the two fields are aligned so that they are attracting. Rotating from point 1 through point 7, the stator field rotates clockwise. The bar magnet, free to move, will follow the stator field because the attraction between the two fields continues to exist. A shaft running through the pivot point of the bar magnet would rotate at the same speed as the rotating field. This speed is known as synchronous speed. The shaft represents the shaft of an operating motor to which the load is attached. Rotor rotation This explanation is an oversimplification to show how a rotating field can cause mechanical rotation of a shaft. Such an arrangement using a permanent magnet would work, but it is not used due to limitations associated with a permanent magnet rotor. Practical motors use other methods, as we shall see in the next paragraphs. 2024-02-15 B-03b Electrical Fundamentals CASA Part 66 - Training Materials Only Page 262 of 284 Speed of AC Motors The magnetic field inside an AC motor rotates at a speed related to the frequency of the current supply. This field rotation speed is called the synchronous speed (Ns), and the rotational speed of the motor shaft is related to it. f × 120 NS = P In the above equation, Ns is the synchronous speed in rpm, f is the frequency in Hz and P is the number of poles per phase. The per-phase element of this last parameter is crucial. A three-phase motor with one pair of poles per phase has six poles, but rotates at the same speed as a single-phase motor with one pair of poles (i.e. two poles). Failure to appreciate this fact will cause speed calculation values to be three times too small. Synchronous Motors Some AC motors operate almost exactly at the synchronous speed; these are called synchronous motors. Asynchronous Motors Asynchronous motors operate at something less than the synchronous speed. The percentage difference between the full-load speed and the synchronous speed is called slip. Normal slip is around 5%, though it can be much higher. The difference between synchronous motors and asynchronous motors is one of fundamental design, not build quality. 2024-02-15 B-03b Electrical Fundamentals CASA Part 66 - Training Materials Only Page 263 of 284 AC Motor Speed Control Induction motors are practically fixed-speed devices. There are only two practical methods to change the rotation speed of AC induction motors: Use a frequency converter. Use a motor with separate windings for different speeds. In some applications, motors with dual-speed windings are used. For applications in which accurate speed control is needed, you need a frequency converter. Variable speed motor A frequency converter can run a three-phase AC motor at a wide speed range quite well (the performance of the motor is usually reduced outside its optimal operation speed). A frequency converter does not work with AC induction motors that are run from a single-phase power source because the operation of the required motor phase conversion capacitor is very frequency sensitive – it works as expected only at normal mains frequency. 2024-02-15 B-03b Electrical Fundamentals CASA Part 66 - Training Materials Only Page 264 of 284 Direction of Rotation Direction of Rotation in Three-Phase Motors The direction of rotation depends upon the direction of the rotating field. If the direction is reversed, then the rotor will follow in the reverse direction. This can be achieved by reversing any two of the phase terminals. Reversing a three-phase motor Reversing a Split-Phase Motor With the split-phase motor, a switch can select Phase B to lag A, or the B stator winding can be switched to carry or lead Phase A and thus cause the motor to follow the leading current. This option is only available on some single-phase motors due to the physical location (90°) of the windings. Many motors’ start and run windings are physically different so therefore cannot be reversed. Reversing a split phase motor 2024-02-15 B-03b Electrical Fundamentals CASA Part 66 - Training Materials Only Page 265 of 284 Induction Motors The Induction Motor The induction motor is the most commonly used type of AC motor. Its simple, rugged construction is relatively inexpensive to manufacture. The induction motor has a rotor that is not connected to an external source of voltage. The induction motor derives its name from the fact that AC voltages are induced in the rotor circuit by the rotating magnetic field of the stator. In many ways, induction in this motor is similar to the induction between the primary and secondary windings of a transformer. Large motors and permanently mounted motors that drive loads at fairly constant speed are often induction motors. Examples are found in washing machines, refrigerator compressors, bench grinders and table saws. Induction motors are probably the simplest and most rugged of all electric motors. There are only two main components: the stator and the rotor. Stator windings 2024-02-15 B-03b Electrical Fundamentals CASA Part 66 - Training Materials Only Page 266 of 284 Induction Motor Stator The stator contains a pattern of copper coils arranged in windings. As alternating current is passed through the windings, a moving magnetic field is formed near the stator. This induces a current in the rotor, creating its own magnetic field. The interaction of these fields produces a torque on the rotor. Note that there is no direct electrical connection between the stator and the rotor. Induction Motor Rotor The induction rotor is made of a laminated cylinder with slots in its surface. The windings in these slots are one of two types. The most common is the squirrel-cage winding. This entire winding is made up of heavy copper bars connected together at each end by a metal ring made of copper or brass. No insulation is required between the core and the bars. This is because of the very low voltages generated in the rotor bars. The size of the air gap between the rotor bars and stator windings necessary to obtain the maximum field strength is small. The other type of winding contains actual coils placed in the rotor slots. The rotor is then called a wound rotor. Induction motor rotor Regardless of the type of rotor used, the basic principle is the same. The rotating magnetic field generated in the stator induces a magnetic field in the rotor. The two fields interact and cause the rotor to turn. 2024-02-15 B-03b Electrical Fundamentals CASA Part 66 - Training Materials Only Page 267 of 284 Squirrel-Cage Rotor The squirrel-cage rotor is constructed of a number of conducting bars running parallel to the axis of the motor and two conducting rings on the ends. Typically, the conductors may be copper or aluminium. The assembly resembles a squirrel cage, thus giving this type of motor its name. The rotor b