CAB6- SCM Lecture Notes PDF
Document Details
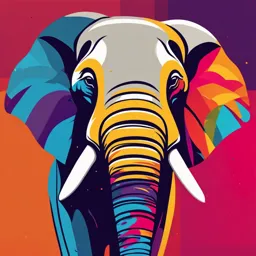
Uploaded by ChasteRhodonite
Hanze University of Applied Sciences Groningen
Tags
Summary
These lecture notes cover various aspects of Supply Chain Management (SCM), focusing on topics like order management concepts, customer service principles, and inventory types. The document also touches upon the importance of logistics in SCM.
Full Transcript
CAB6- SCM Mass lecture Notes Week 1: Order Management Concept: - Phase 1: Influence and order o Organization attempts to change the manner by which its customers place orders - Phase 2: Execute the order o Order receipt ▪ Electronically v...
CAB6- SCM Mass lecture Notes Week 1: Order Management Concept: - Phase 1: Influence and order o Organization attempts to change the manner by which its customers place orders - Phase 2: Execute the order o Order receipt ▪ Electronically vs. manually o Order fulfilment ▪ Inventory policy; number & location of warehouses o Order shipments ▪ Transport mode choice Customer service- anything that touches the customer - Including: all activities that influence information flow, product flow and cash flow between the organization and its customers - It is a philosophy/performance measures/an activity Customer relationship management (CRM)- the concept to align the supplier’s resources with its customers in a manner that increases both customer satisfaction and supplier profits - Maximize the efficiencies of the shipping organization’s logistics network Four steps to implement CRM: - Step 1: segment the customer base by profitability - Step 2: identify the product/service package for each customer segment o Determine what each customer segment values in its relationship with the supplier based on feedback from customers and sales representatives - Step 3: develop and execute the best processes o Deliver on customer expectations - Step 4: measure performance and continuously improve Customer service: - Marketing objective: allocate resources to the marketing mix to maximize long- term profitability of the firm - Logistics objective: minimize total costs, given customer service objective, where: o Total costs= transportation costs + warehousing costs + order processing & information costs + lot quantity costs + inventory carrying costs The 4 elements of customer service: 1. Time (length of lead time) 2. Dependability (consistent lead time, safe delivery, correct orders) 3. Communication (pre-transaction, transaction and post-transaction) 4. Convenience (flexible logistics service level) Stockout- occurs when desired quantities of finished goods are not available when or where a customer needs them - As a result, one of 4 possible events can occur: 1. The buyer waits until the product is available 2. The buyer back-orders the product 3. The seller loses current revenue 4. The seller loses a buyer and future revenue Logistics operations responsiveness (LOR)- examines how well a seller can respond to a buyer’s needs - Response can take two forms: 1. How well a seller can customize its service offerings to the unique requirements of the buyer 2. How quickly a seller can respond to a sudden change in a buyer’s demand pattern Week 2: Index- combines two or more metrics into one singular indicator Metric- involves a calculation or a combination of measurements, often in the form of a ratio - Ex. inventory turnover etc. Measure- requires no calculations and with simple dimensions - Ex. units of inventory Good performance measures/indicators: 1. Quantitative and easy to understand 2. Is visible and only measures what is important 3. Facilitates trust 4. Defined and mutually understood Performance categories: - Time o Ex. on-time delivery, order cycle time etc. - Quality o Ex. overall customer satisfaction, complete order, damage-free etc. - Cost o Ex. days sales outstanding, administrative, total delivered costs etc. - Other/supporting o Ex. minimum order quantity, change order timing, availability of information - Others: o Reliability o Responsiveness o Agility o Costs o Asset management Logistics Quantification Pyramid: 1. How logistics cost and service re perceived by channel members 2. Focuses on how a seller’s cost influences a customer’s profit and on how a seller’s service impacts a customer’s revenue. 3. Example: Transportation cost tradeoffs between less expensive (slower & less reliable) and more expensive (faster & more reliable) transportation 4. Product availability, order cycle time, post-sale logistics support Week 3: Goal of logistics- achieve the acceptable level of customer service at minimum total cost Types of inventory and rationales: 1. Procurement (purchase discounts), production (long production run), and transportation (freight rate discounts) 2. Demand- and supply-side uncertainties 3. Inventory costs associated with goods in motion during transportation time period. 4. Inventory costs associated with goods in process during manufacture or assembly of a complex product. 5. Seasonality in raw materials supply (e.g. production, transportation), in demand for finished product, or in both 6. Inventory hold in anticipation that an unusual event (e.g. strikes, significant price increase, extreme weather) Major types of inventory costs: - Inventory carrying costs - Ordering and set up cost - Expected stockout cost - In-transit inventory carrying cost Carrying cost vs. ordering cost - Ordering cost and carrying cost respond in opposite ways to changes in the number of orders or size of individual orders 1. Dependent demand vs. independent demand- Independent demand is unrelated to the demand for other items, while dependent demand is directly related to, or derives from, the demand for another inventory item or product. 2. Pull vs. Push. The “pull” approach relies on customer orders to move product through a logistics system, while the “push” approach uses inventory replenishment techniques in anticipation of demand to move products. 3. System-wide vs. Single-facility solutions. A system-wide approach plans and executes inventory decisions across multiple nodes in the logistics system. A single-facility approach does so for shipments and receipts between a single shipping and receiving point. fixed order quantity EOQ model, inventory is reordered when the amount on hand reaches the reorder point. The reorder point quantity depends on the time it takes to get the new order and on the demand for the item during this lead time. Just-in-time management- getting the right quantity of goods at the right place at the right time Three elements of JIT: Inventory Classification techniques: ABC Analysis ABC classification technique assigns inventory items to one of three groups according to the relative impact or value of the items that make up the group. A items are considered to be the most important, B items lesser importance, and C items least important. Pareto’s Law (The “80–20” Rule) Pareto’s Law “80–20” rule suggests that a relatively small percentage of inventory might account for a large percentage of the overall impact or value. Quadrant Model Quadrant model classifies finished goods inventories using value and risk to the firm as the criteria. Value is measured as the value contribution to profit; risk is the negative impact of not having the product available when it is needed. Summary: Week 4: Role of production operations in SCM: Economies of scale: - High volume production with lower cost per unit of output - Suitable in situations where production processes have high fixed costs and equipment Economies of scope: - Low volume production with flexible capabilities of producing a wide variety of products - Important in markets characterized by changing customer demand Logistics vs. SCM: - Logistics focuses on moving and storing goods, while SCM management focuses on the whole networks of the partners and logistics is more internally focussed while SCM management focuses on both internally and externally FMCG- fast moving consumer goods Production Tradeoffs: Centralized vs. Regional: - Centralized production facilities provide operating cost and inventory efficiencies - Regional production facilities allow companies to be closer to customers and more responsive Large vs. Small: - Larger facilities with excess capacity provide the flexibility to respond to demand spikes - Smaller facilities that are better utilized and more cost efficient Product-focused vs. Process-focused: - Product focused facilities performing many processes on a single product type that are more responsive - Process focused facilities concentrating on a few functions across multiple product types are more efficient at it limited scope of activities Production costs vs. Other supply chain costs Production Strategy Challenges: Mass production: (push) - Limitation on producer’s responsiveness - Potential for the bullwhip effect o Is caused by consumers when a little bit of demand changes o If we see other ppl buying more packages (like toilet paper in lockdown), then others subconsciously start to buy more and stores alert suppliers to produce more - Made to stock Lean manufacturing: (pull) - Difficult to achieve economies of scale - Require technological capabilities to achieve the supply chain visibility and synchronization - Increased risk of disruption - Assembled to order Flexible manufacturing: (pull) - High capital investment - System complexity - Require skilled technician - Require disciplined & high level of planning Adaptive manufacturing: (pull) - Require seamless transfer of knowledge and real-time information Smart manufacturing: (pull) - Require capabilities of a network with messaging standards - Require analytical toolkit - Require flexible automation Assembly process: Make-to-Stock (MTS) Make-to-Order (MTO) − Assemble-to-Order (ATO) − Build-to-Order (BTO) − Engineer-to-Order (ETO) Comparison MTO options: Production process layout- involves that arrangement of machines, storage areas, and other resources within the four walls of a manufacturing or an assembly facility Week 5: Demand management: - Estimate and manage customer demand and use this information to make operating decisions - To further ability of firms throughout the supply chain to collaborate on activities related to the flow of products, services, information and capital Supply-Demand Balancing Methods: - External balancing methods: o Change the way the customer orders ▪ Price ▪ Lead time - Internal balancing methods o Manage gap using internal processes ▪ Inventory ▪ Production flexibility Demand forecasting: 1. Independent demand o The demand for the primary item, known as base demand 2. Dependent demand o The demand directly influenced by demand for independent item Random fluctuation- a development that cannot be anticipated and is usually the cause to hold safety stock to avoid stockouts Trend fluctuation- gradual increase or decrease in demand over time for an organization Seasonal fluctuation- seasonal patterns that will normally repeat themselves during a year for most organizations Types of forecast error measures: - Cumulative sum of forecast errors (CFE): calculates the total forecast error for a set of data, taking into consideration both negative and positive errors - Mean squared error (MSE): squares each period error so the negative and positive errors do not cancel each other out - Mean absolute deviation (MAD): takes absolute value of each error, so the negative and positive signs are removed - MAPE - TRACK Signal: tracking signal can be used to measure forecast error, especially good at identifying if a “bias” exists in the forecast errors Common forecasting techniques: - Simple moving average: o Makes forecasts based on recent demand history and allows for removal of random effects - Weighted moving average: o Assigns weight to each previous period with higher weights usually given to more recent demand - Exponential smoothing: Week 6: Principle supply chain information requirements: 1. Meet quality standards o Accuracy o Accessibility o Relevancy o Timelines o Reliability 2. Support multidirectional flows o Internal and external information sharing o Suppliers (logistics providers, financial institutions, government agencies) 3. Provide decision support o Strategic decisions o Tactical planning o Rules based decision making o Execution and transaction processing System Capabilities: 1. Cross-chain visibility 2. Agility 3. Velocity 4. Synchronization 5. Adaptability 6. Segmentation 7. Optimization SCM planning applications: - Helps organizations shift from autonomous planning activities to synchronized planning processes that use real-time data for collaboration across departments, suppliers and customers SCM execution applications: - Warehouse management systems - Order management systems - Distributed order management - Transportation management systems - Global trade management - Manufacturing execution systems SCM facilitating tools: