Boiler Notes 20-21 PDF
Document Details
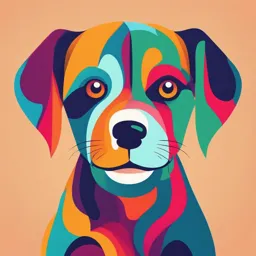
Uploaded by OutstandingMood6123
V.P.M.'s Maharshi Parashuram College of Engineering, Thane, Maharashtra
2021
Tags
Summary
These notes provide an overview of boiler unit operations, including different boiler types, design, working principles, and instrumentation. They cover key components like steam drums, superheaters, and economizers, along with control systems for steam temperature and pressure.
Full Transcript
Unit IV Unit Operations Boilers A boiler is a device used to generate steam at desired pressure and temperature by burning fuel to water to change it to steam. There are two main categories of boilers, and each can further be subdivided to several types: Fire-tube boiler - Hot gas in severa...
Unit IV Unit Operations Boilers A boiler is a device used to generate steam at desired pressure and temperature by burning fuel to water to change it to steam. There are two main categories of boilers, and each can further be subdivided to several types: Fire-tube boiler - Hot gas in several tubes is used to heat the surrounding water. Water-tube boiler - Water in the tubes is heated by the surrounding hot gas. Boilers are widely used in domestic and industrial applications such as: Thermal power plants Industrial processes Heating Sanitation Sterilizing equipment Water tube boiler design and working In a typical Water tube boiler design as shown in the figure, it consists of two drums the steam drum and the water or mud drum. They are connected with number of tubes called as down comers (which bring down the cold water from steam drum to mud drum) and risers which carry steam from mud drum to steam drum. The temperature of the steam (being in contact with water) cannot be increased beyond its saturation point and hence it is separated from water and separately heated in super heaters (a series of heat exchangers). The feed water is fed by feed water pump and valve. This supply of water is taken from dm (demineralisation) plant to avoid scaling. Water tube boiler parts and their functions There are many pressure parts and non pressure parts in a water tube boiler we only discuss main water tube boiler parts and function. Steam drum Steam drum is a collection vessel for steam & water. Here water & steam is separated. It has steam separators. Steam goes from top side to superheater & water goes from the bottom through down comer Mud drum, then to furnace bottom ring headers (bottom of furnace water wall). Super heater If the temperature of the steam is above its saturation temperature then it is called superheated steam. The super heater (heat exchanger) is used to increase the temperature of the steam. These are bundles of high strength tube which can bear temperature 600C Depending upon the material of tubes Economizer Economizer (heat exchanger) is the boiler accessory used to recover the heat of flue gas that leaving the boiler by heating feed water. The efficiency of a boiler can be increased with an economizer. Air Heater Air supplied to a boiler for combustion is pre heated with the help of air heater by recovering the heat of waste flue gas that leaves the economizer. Boiler Fans For combustion of fuel in the boiler furnace air is drawn from the atmosphere and pushed through the ducts with forced draught fan to furnace where air reacts with fuel and become flue gas, the flue gas is then extracted from the furnace with the help of Induced draught fan. The fan used in large water tube boilers are FD fans, ID fans, Primary air fans, Secondary air fans and Gas recirculation fans. Boiler Instrumentation involves control of the following parameters: 1) Boiler Drum level control 2) Combustion Control 3) Steam Temperature control 4) Steam Pressure Control 1) Boiler Drum level control It must be designed to maintain mass balance so that the drum level remains within limits of its safe and efficient operation. There are 3 schemes for the feed water control I Single element control A single element control only uses the drum level signal as the control process variable. After calculating the level deviation from the set point, the output of the controller is then passed to the boiler feed water valve, which then controls the level of feed water flow into the boiler drum. Single Element Control recommended on small boilers with a relatively large water volume and steady loads. This scheme is ineffective control option because of the swelling and shrinking effect*. *Swelling and Shrinking effect As steam demand increases, there is an initial lowering of the drum pressure resulting in an artificial rise in drum level as the steam bubbles expand and swell the drum water level. This phenomenon sends a false control signal to reduce feed water flow, when in fact the feed water flow should be increasing to maintain mass balance. Conversely, on a loss of steam demand, there is an initial rising of steam drum pressure which acts to lower the drum level by compressing the steam bubbles and shrinking the drum water level. This sends a false signal to increase feed water flow when in fact it should be decreasing to maintain mass balance. II Two element control The term 'two-element' is derived from measurement of two variables: steam flow and drum level that influence on the feed water valve position. It is sometimes referred as a combination 'feed-forward feedback' system because the steam flow demand is fed forward and the drum level signal becomes the feedback for controlling/manipulating feed water to boiler drum. The two-element drum level control shown in following figure. Steam flow is measured by the steam flow transmitter (FT-1), its signal is fed to the feed water flow computer (FC-1) after processing through the square root extractor (FY-1). As in the single-element level control, the drum level is measured by the level transmitter (LT- 1) and its signal is transmitted to the drum level controller (LC1). In the drum level controller, the process signal is compared to the drum level set-point, where a required corrective output signal to maintain the drum level is produced. This corrective signal is sent to the feed water flow computer. The feed water flow computer combines the signal from the two variables, and produces an output signal to the feed water control valve (FCV- 1). Auto/Manual transfer of the feed water control valve is accomplished via FK-1. Two Element Control isl recommended on small to medium boilers with moderate changes in steam demand. III Three Element Control The term 'three-element' is derived from measurement of three variables: steam flow, drum level and feed water flow that influence on the feed water valve position. Figure below shows the control scheme for three-element drum level control. To the left of the dotted line, the instrumentation is the same as that for the two-element drum level control, with one exception: the output of the feed water flow computer now becomes the set-point of the feed water flow controller (FIC-2). Equipment required to complete our three-element drum level control scheme includes an additional flow device (FE-2) and differential pressure transmitter (FT-2)The area to the left of the dotted line in following figure functions the same as that of a two element drum level control. We can pick up the operation for this scheme where the output signal of the feed water flow computer (the combination of steam flow and drum level) enters the feed water controller (FIC-2). This in effect becomes the set-point to this controller. Feed water flow Is measured by the transmitter (FT- 2). The output signal of the feed water flow transmitter is linearized by the square root extractor, (FY-2). This signal is the process variable to the feed water controller and is compared to the output of the feed water flow computer (set-point). The feed water flow controller produces the necessary corrective signal to maintain feed water flow at its set-point by the adjustment of the feedwater control valve (FCV-1). 2) Combustion Control Objective of combustion control is to adjust the heat input to the boiler in terms of fuel and air supplied in relation to output or steam demand. Steam Pressure is taken as an indicator of boiler load (it decreases when the steam demand increases) There are 3 types of combustion control schemes. 1) Series 2) Parallel 3) Series-Parallel Series Combustion control A change in the steam Pressure causes a change in the air flow rate which in turn changes the fuel flow rate. In the following diagram fuel flow becomes the secondary variable , however, it may be interchanged with fuel becoming the primary variable. This scheme is used for boilers with constant steam load and with fuels having constant efficiency Steam Pressure Air Flow Fuel Flow SERIES Parallel Combustion Scheme This is the most commonly used scheme for boilers of any size using fuels of constant calorific value. The steam flow simultaneously adjusts both the fuel as well as air flow rates Steam Pressure Air Flow Fuel Flow Series-Parallel combustion control If a boiler uses solid fuels (Coal firing scheme) the feed forward signal from the steam pressure controller is also given to combustion air control. Steam pressure variations are used to adjust the fuel flow. However, as steam flow is directly related to the heat released of the fuel, it can not be used to control the air flow rate. Steam Steam Flow Pressure Fuel Flow Air Flow 3) Steam Temperature Control To control the temperature of steam, cold water is directly injected in the steam with the help of attemperator device. It can be mixed at any one of the following 3 locations i) At the outlet of Boiler Drum ii) Between the successive stages of Superheaters iii) After the last stage of superheaters The second option is widely used and is shown in the figure above. Steam temperature is measured and after comparing it with the set point, the TRC generates actuating signal for the desuperheater water flow valve. 4) Steam Pressure Control The actual steam flow at any point is not necessarily a true indication of demand. According to Shinskey, the true load on a boiler can be approximated by where h is the differential developed by a flow element and p is the steam pressure. Figure 8.6s describes a boiler- pressure control system using this type of feedforward model. The pressure controller adjusts the ratio of firing rate to estimated load. In the firing rate control system shown in Figure 8.6s, the loops 101 and 102 measure the pressure and flow of the generated steam, respectively. The firing rate demand signal is generated in a feedback manner by the pressure controller PIC-101. In order to speed up the response of this loop to load changes, a feedforward trim is added. This trim is based on steam flow, because this flow is the first to respond to load changes. Therefore, as soon as the demand for steam changes, FY-102 will trim the firing demand signal, without waiting for the steam pressure to change. Feedback, Feed Forward and cascade control demonstrated in 3 element feed Water Control The term “3-element control” refers to the number of process variables (PVs) that are measured to effect control of the boiler feedwater control valve. These measured PVs are: ▪ liquid level in the boiler drum, ▪ flow of feedwater to the boiler drum, and ▪ flow of steam leaving the boiler drum. If the boiler drum liquid level is low, the level controller will call for an increase in feedwater flow. But consider that if at this moment, the feedwater supply pressure were to drop. The level controller could be opening the valve, yet the falling supply pressure could actually cause a decreased flow through the valve and into the drum. Thus, it is not enough for the level controller to directly open or close the valve. Rather, it must decide whether it needs more or less feed flow to the boiler drum. The level controller transmits its target flow as a set point to a flow controller. The flow controller then decides how much to open or close the valve as supply pressure swings to meet the set point target. This is a “2-element” (boiler liquid level to feedwater flow rate) cascade control strategy. The flow controller will immediately sense any variations in the supply conditions which produce a change in feedwater flow. The flow controller will adjust the boiler feedwater valve position to restore the flow to its set point before the boiler drum liquid level is even affected. The level controller is the primary controller (sometimes referred to as the master controller) in this cascade, adjusting the set point of the flow controller, which is the secondary controller (sometimes identified as the slave controller). The third element in a “3-element control” system is the flow of steam leaving the steam drum. The variation in demand from the steam header is the most common disturbance to the boiler level control system in an industrial steam system. By measuring the steam flow, the magnitude of demand changes can be used as a feed forward signal to the level control system. The feed forward signal can be added into the output of the level controller to adjust the flow control loop set point, or can be added into the output of the flow control loop to directly manipulate the boiler feedwater control valve. The majority of boiler level control systems add the feed forward signal into the level controller output to the secondary (feedwater flow) controller set point. This approach eliminates the need for characterizing the feed forward signal to match the control valve characteristic. Safety interlocks for boilers 1. Purge Interlock: Prevents fuel from being admitted to unfired furnace until furnace has been thoroughly purged. 2. Low Air Flow Interlock: Fuel is shut off upon loss of air flow and / or combustion air fan. 3. Low fuel supply Interlock: Fuel is shut off upon loss of fuel supply otherwise unstable flame condition results. 4. Loss of flame Interlock: All fuel is shut off upon loss of flame. 5. Fan Interlock: Stop of F.D. fan upon loss of I.D. fan