BIOTECH 2B03 Lab 8.docx
Document Details
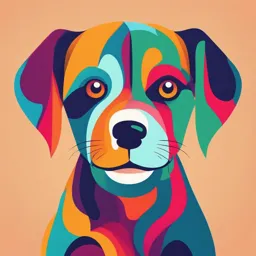
Uploaded by EarnestLake
Full Transcript
Experiment 8 – Synthesis of Biodiesel Introduction The United States is the largest single consumer of fossil fuels in the world. Each year, the U.S. consumes 125 billion gallons of gasoline and 60 billion gallons of diesel fuel (1-4). Currently the US consumes ~390 billion gallons of motor gasoline...
Experiment 8 – Synthesis of Biodiesel Introduction The United States is the largest single consumer of fossil fuels in the world. Each year, the U.S. consumes 125 billion gallons of gasoline and 60 billion gallons of diesel fuel (1-4). Currently the US consumes ~390 billion gallons of motor gasoline, and 868 billion gallons of petroleum fuel daily (5). With our current energy consumption and the possibility of a world-wide decline in oil production in the near future, the desire to find alternative feedstocks for our energy needs is increasing. Vegetable oil is one such renewable, alternative feedstock. The use of vegetable oil, particularly used vegetable oil, has many green advantages: the product biodiesel is used to supplement our energy supply which reduces our reliance on non-renewable petroleum fuels; a significant waste reduction is achieved when this process is carried out with used vegetable oils (waste vegetable oil from restaurants amounts to about 3 billion gallons annually); the by-product glycerin can also be used as an alternative feedstock; and since vegetable oils are renewable, their combustion does not lead to a net increase in atmospheric CO2 levels. This fuel source is commonly known as biodiesel and can be synthesized on an individual vehicle level or on an industrial scale. The methods behind biodiesel synthesis have been known for decades. In recent years, however, there has been significant interest in the production of biodiesel from food industry waste oils. Every year, fast food restaurants in the U.S. produce over 3 billion gallons of used cooking oil. Since many gallons of this used oil inevitably end up in landfills and sewers, the production of biodiesel from waste oil has the potential to significantly reduce environmental impact. Biodiesel is classified as a non-toxic material by the EPA and degrades readily in the environment. In this experiment we will synthesize biodiesel fuel from vegetable oil. Structurally, biodiesel is any small alkyl ester (e.g. methyl, ethyl, etc.) derived from vegetable oil; in this lab we will prepare the fatty acid methyl esters. Oils (called triglycerides or triacylglycerols) have a glycerine backbone joined by ester linkages to three fatty acid chains. Different oils and fats differ by the composition of the fatty acids. The most common fatty acids have 12, 14, 16, 18, or 20 carbons, and may have one or more double bonds (unsaturations). In general, it can be seen that animal fats tend to be higher in saturated fats compared to vegetable oils. Naturally occurring unsaturated fatty acids have the cis-(Z) configuration. The triglyceride structural formula below is typical of olive oil. It consists of two fatty acid chains of oleic acid and one of palmitic acid attached to glycerol (the vertical carbon chain). The reaction to form biodiesel from a triglyceride is known as a transesterification reaction. Transesterification is the process of transforming one type of ester into another type of ester. The reaction is catalyzed by the presence of the strong base, NaOH. In the first step of the reaction, the NaOH reacts with methanol in an acid base reaction. The products of this first step of the reaction are a very strong base, sodium methoxide, and water. In the second step, the sodium methoxide breaks the glycerine section from the fatty acid section in a base-catalysed nucleophilic addition-elimination reaction at the carbonyl carbon of the triglyceride. The separation of the glycerine portion leads to the formation of three fatty acid methyl esters (FAMEs), the biodiesel, and glycerol. The NaOH is regenerated as a product in the reaction. The biodiesel and glycerol are immiscible and will separate to form two layers. An excess of methanol is used to drive the reaction to completion, and this ends up with the catalyst in the glycerol layer when the reaction is complete. The separation of the biodiesel and glycerol layer is fortuitous in that we can easily separate and isolate our biodiesel product from the remaining product mixture. The glycerol by-product can be converted to glycerine soap through a saponification reaction if excess NaOH is used. Glycerine can also be burned as a fuel, and has many uses in the manufacture of cosmetics, food products, and pharmaceuticals; another idea recently published involves the use of a copper chromite catalyst to transform glycerine into propene glycol, a more environmentally friendly antifreeze. Biodiesel is a fuel with properties similar to petroleum-based diesel fuel. This means that it produces energy through combustion with oxygen (as does regular diesel). During combustion, each carbon contained in biodiesel is converted to carbon dioxide. As each carbon is oxidized to carbon dioxide it will release about 850 kJ per mole. The more carbons, the more energy produced upon combustion. Vegetable oil itself is also a fuel and can undergo combustion with oxygen. If this is so why do we need to convert the vegetable oil (triglycerides) to the methyl esters—why not just burn vegetable oil? The reason is due to the viscosity of the triglycerides. Viscosity is the internal friction or stickiness of a liquid. A viscous material is ‘thicker‘ and does not flow quickly. The viscosity of biodiesel is considerably lower than the oil from which it is made. While the structure of the fatty acid moiety does not change tremendously, the cleavage of the long chain from the glycerine backbone plays an important role in explaining this change. The viscosity of vegetable oil will present a problem in that its stickier nature will prevent it from flowing easily through the fuel pump systems of an engine. Since viscosity is generally inversely proportional to temperature, at lower temperatures the viscosity problem is enhanced. Unlike the triglycerides, methyl esters (biodiesel) are less viscous and will easily flow through the fuel system of an engine. However, when biodiesel is cooled to 0ºC, rather than freezing, it gels; so there is some controversy over the type and percentage of biodiesel that can be used in a standard diesel engine due to issues with gelling of the fuel. The introduction of solutes to biodiesel has an effect similar to freezing point depression and could, therefore be used to deal with this problem. References http://faculty.northseattle.edu/tfurutani/che238_2006/biodiesel.pdf http://greenchem.uoregon.edu/PDFs/GEMsID87.pdf https://teach.lanecc.edu/thompsonj/CH243/biodiesel%20lab.pdf http://www.rsc.org/Education/EiC/issues/2007July/ExperimentingWithBiodiesel.asp Michael Koscho, University of Oregon Preparation Questions What is the chemical name for an oil molecule? Most oils and fats contain palmitic and stearic acid as building blocks. Give the structure for both these compounds. Describe the role of sodium hydroxide in this reaction? Suggest ways to reduce gelling of biodiesel at low temperatures? How would you test this? What solute could you test in lab? (If available, you can test its effect in lab.) Reagents Vegetable oil e.g., canola, olive, soybean, peanut etc.; new or used Methanol 99% Finely ground anhydrous sodium hydroxide Procedure NaOH is corrosive and can cause severe burns on skin and eyes. Methanol is highly flammable and toxic by inhalation and in contact with skin. Sodium methoxide is flammable and also toxic by inhalation and in contact with skin. As a result, goggles and gloves should be worn at all times during the experiment to protect from the harmful effects of the anhydrous NaOH, the methanol, and the sodium methoxide. The hood should also be used to maintain harmful odours in a restricted area during the use of methanol and the synthesis of the sodium methoxide. Add 0.2 g of finely ground NaOH to 10 mL of absolute methanol in a 250 mL Erlenmeyer flask. Stir vigorously on a magnetic stir-plate in a well-ventilated location (hood) until all of the NaOH is dissolved. At this point the flask now contains sodium methoxide. Caution: heat is generated, and the resulting methanol/sodium methoxide solution is caustic. Add 50 mL vegetable oil to a second 250 mL flask (if using a solid triglyceride, use 50 g and heat to liquefy) Warm up vegetable oil to about 50°C. Warming the oil up is not necessary but increases the reaction rate. After the NaOH has dissolved (be sure the solution is well mixed – should appear cloudy), pour the vegetable oil into the methanol solution while continually stirring. The mixture will appear cloudy at first and then clear within a few minutes as the reaction nears completion; let the reaction continue. Cover with watch glass to condense any methanol vapours, returning them to the reaction mixture, and turn up stirrer to position 7 or 8. Stir vigorously for about 30 minutes (since the two layers have large differences in polarity and resist mixing, the system must be stirred vigorously to encourage intimate contact between the reagents). Transfer the contents of the flask into 15 mL plastic centrifuge tubes. The mixture will separate into two different layers. The glycerol will sink to the bottom, and the methyl ester (biodiesel) will float to the top. Allow the mixture to sit for about 15 minutes, and then place it in a centrifuge and spin for another 5 minutes to speed the separation (don‘t forget to counterbalance the centrifuge). If the layers have not separated continue to centrifuge for another 5 minutes. (Often, the bottom layer will have solidified, especially if waste cooking oil is used.) Using a transfer pipette, carefully draw off the top layer of biodiesel. Make sure not to get glycerol (bottom darker layer) in the biodiesel. Pour the biodiesel into a pre-weighed container. Calculate the mass of biodiesel synthesized. Calculate the yield and % yield. Note: For the production of fuel-quality biodiesel, the biodiesel layer would now need to be washed (to remove any glycerine soap by-products) and dried. Measure the mass of exactly 10.0ml of biodiesel to calculate its density. Compare the viscosities of the original vegetable oil and the biodiesel; viscosity can be approximated by measuring the time it takes for a known amount of the liquid to flow out of a pipette. Compare the temperature at which 10ml samples of the vegetable oil, biodiesel and biodiesel with solutes gel. Pure biodiesel gels around 0°C, so an ice-salt bath is needed to observe gel formation in mixtures. Cloudiness in the liquid is a good indication of the onset of gel formation. Report Note: A condensed lab report is required for this lab that has the following components: Title page, Results and observations, Calculations, Post laboratory questions. You may hand in one report for per lab group. Make sure to reproduce one formal set of ‘Results/Observations’ in word-processed form. Also, include scans of all individual ‘Original Data’ with your name on the top of each scan you submit. Write a summary of your experiment and results. Post Laboratory Questions Write out a complete curved arrow mechanism for the formation of one biodiesel molecule from vegetable oil (i.e., show one transesterification). How many molecules of biodiesel are produced for each molecule of oil? Report the mass of biodiesel obtained. Calculate the theoretical and percent yields. To do this you will need an “average” molecular weight for the vegetable oil. Determine what this number is and justify your answer. Would the yield differ if you used new versus used vegetable oil, or if you used different types of vegetable oil. Explain your answer. What physical characteristics differ between vegetable oil and biodiesel and how do they affect its use as a fuel? What are the differences between petroleum diesel and biodiesel with respect to their use as fuels? Why is only a catalytic amount of NaOH used in the biodiesel reaction? What would happen if a full equivalent of NaOH were added? One argument for using biodiesel is that the net amount of CO2 released into the atmosphere is claimed to be zero (or near zero). How can this be, given that the combustion of biodiesel released CO2? 74